Welcome! Here are the website rules, as well as some tips for using this forum.
Need to contact us? Visit https://heatinghelp.com/contact-us/.
Click here to Find a Contractor in your area.
Best Of
Re: Equalizer disabled experiment video
Thanks Rusty!
Don't give me too much credit—that's the beauty of having a steam boiler in my house and working in a different industry, so when I get home I'm not sick of the topic 😅
Note that I don't think it doesn't have a function—it is a great drip from the header and there are edge cases where it will prevent the hartford loop from having an air bubble in it. I'm not sure when it got this name but apparently old books called it a "bleeder" or "drip".
What I hoped to show (and I think I have shown) is that it seems NOT to have any effect on the thing that the industry currently thinks is its most important function, to prevent the water from being pushed out of the boiler under normal operating conditions. Thanks again for your note.
Re: Honeywell supervent
The biggest issue here is that it's piped backwards. The pump needs to be on the downstream side of the Supervent/ expansion tank in order for the system to work properly. The odds are pretty slim that the Supervent needs any sort of service, but if it does, you can loosen that brass nut on the top and remove the guts without removing anything else.With that 4 way valve, the system pump is pumping away from the PONPC.
The boiler pump would be better on the return piping, but it should vent air as piped. It's a small, low pressure drop path from boiler, around 4 way and back to boiler. Looks like an 007 so it is not developing a lot of delta P.
It is piped in the hottest point in the system, that is the #1 mechanism for air removal, lowest pressure is second.
No harm in disassemble and inspection. If it has a lot of mineral scale, that too would indicate it is taking on fill water.
If there is a vent inside the boiler jacket, try screwing the cap closed.
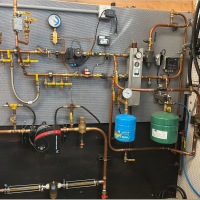
1
Re: Honeywell supervent
Had the same thought. Someone else had a similar problem. Most thought there was a leak and makeup water was loading the system with air. While it may be piped correctly, a steady flow of fresh water into the vent has got to make thinks worse, my opinion.
Re: Honeywell supervent
The biggest issue here is that it's piped backwards. The pump needs to be on the downstream side of the Supervent/ expansion tank in order for the system to work properly. The odds are pretty slim that the Supervent needs any sort of service, but if it does, you can loosen that brass nut on the top and remove the guts without removing anything else.

1
Re: The "equalizer" is mis-named. It does nothing to equalize anything.
This whole post reminds me of a book called Pumping Away, how that author had the audacity to take on an entire industry of all knowing boiler engineers about expansion tank placement.
How dare he!
Wait until the book banners in Florida get a of that wokeness
woke: a state of being aware
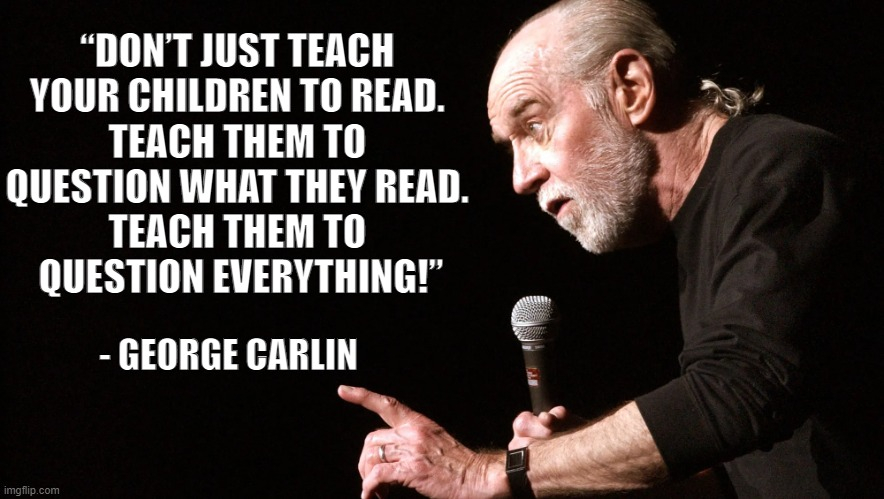
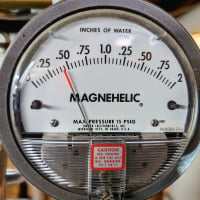
6
Re: A Liittle R & R for a few hours...
What does "SPOILER" mean, Erin? Mad DogIt's just a feature that comes with the forum software and is mostly used in forums where they discuss movies and TV shows. It's used to hide/reveal parts of posts that can contain spoilers about the endings to shows, etc.
Re: Embassy Onxy
I tried to send pics via phone but not working. However, the resting PSI is 15.
I had "former" plumber's tech come and do service on unit, replacing ignition rods and flame sensor (annual stuff) and he tried to sell me on a gas valve; he's worked on unit for the past three years (usually it's the owner's son). I was miffed by this (he always seems to find something the unit needs-I never trusted him) and right after he left, the "harmonics" started. I immediately called the rep at Embassy here in Melville to get his opinion of the new development. He informed me that if the gas value was a problem it wouldn't be a slow process but it would go bad without warning. He indicated to me that the unit probably need a gas valve adjustment. This is when I called the new plumber. The new plumber didn't find anything wrong and of course when he came....no harmonics. It still makes the noise so when the rep comes tomorrow I will deal with that issue, but the water "dripping" concerned me which I hadn't noticed when the new guy came.
I will have him look at the expansion tank and discuss the backflow prevention valve vent and the high pressure safety valve (which seems to me that this is what it might be).
I appreciate your diagnostic impromptu and will give an update in case anyone else might experience the kinds of issues.
Thanks!
I had "former" plumber's tech come and do service on unit, replacing ignition rods and flame sensor (annual stuff) and he tried to sell me on a gas valve; he's worked on unit for the past three years (usually it's the owner's son). I was miffed by this (he always seems to find something the unit needs-I never trusted him) and right after he left, the "harmonics" started. I immediately called the rep at Embassy here in Melville to get his opinion of the new development. He informed me that if the gas value was a problem it wouldn't be a slow process but it would go bad without warning. He indicated to me that the unit probably need a gas valve adjustment. This is when I called the new plumber. The new plumber didn't find anything wrong and of course when he came....no harmonics. It still makes the noise so when the rep comes tomorrow I will deal with that issue, but the water "dripping" concerned me which I hadn't noticed when the new guy came.
I will have him look at the expansion tank and discuss the backflow prevention valve vent and the high pressure safety valve (which seems to me that this is what it might be).
I appreciate your diagnostic impromptu and will give an update in case anyone else might experience the kinds of issues.
Thanks!
GB 142, flameout at startup.
I’d like to address what seems to be a not uncommon issue with this boiler. I had the issue of watching at startup a gentle blue flame would be blown out by what I observed through the site glass as a wind. It would cycle through properly but code 6A, repeat and eventually lock out. I tried lots of different ideas suggested by this site and reading the manual.
I admit the boiler needed cleaning which I paid for but got an unsatisfactory job. I did it my self several times after learning the proper way. This did not cure the issue but was necessary anyway.
Holding my hand over the snorkel loosely at startup would get it to ignite. This act cut down the “wind” allowing it to ignite. Once I removed my hand it would stay lit but you could see the wind return.
It seemed to me I needed to find where the extra air was comming from. I wrapped the top of the chamber to seal that gasket with tape. It would not ignite. Next the bottom plate. Same result. I removed the tape each time so I was only dealing with one variable at a time. I lit the boiler using my hand to cover the snorkel again. Next I gently pushed on the fan motor. This totally changed the flame and calmed the air down. I took the assembly apart as far as I could given my tools at hand. What I realized was, there is a rubber bushing between the motor and fan housing that had dry rotted and the source if the extra air. I replaced the fan/motor assembly and it was good as new.
Just to let you know I did check to make sure the boiler had the correct set up as far as resistance and air/gas ratio was concerned. That all checked out.
I hope this helps someone else down the road. I spent many hours cleaning it and diagnosing it. Good luck. Be safe.
I admit the boiler needed cleaning which I paid for but got an unsatisfactory job. I did it my self several times after learning the proper way. This did not cure the issue but was necessary anyway.
Holding my hand over the snorkel loosely at startup would get it to ignite. This act cut down the “wind” allowing it to ignite. Once I removed my hand it would stay lit but you could see the wind return.
It seemed to me I needed to find where the extra air was comming from. I wrapped the top of the chamber to seal that gasket with tape. It would not ignite. Next the bottom plate. Same result. I removed the tape each time so I was only dealing with one variable at a time. I lit the boiler using my hand to cover the snorkel again. Next I gently pushed on the fan motor. This totally changed the flame and calmed the air down. I took the assembly apart as far as I could given my tools at hand. What I realized was, there is a rubber bushing between the motor and fan housing that had dry rotted and the source if the extra air. I replaced the fan/motor assembly and it was good as new.
Just to let you know I did check to make sure the boiler had the correct set up as far as resistance and air/gas ratio was concerned. That all checked out.
I hope this helps someone else down the road. I spent many hours cleaning it and diagnosing it. Good luck. Be safe.

3
Differential pressure bypass vs balancing valve (vs maybe a dP pump)
Hi All
I am designing a manifold system for low temp radiant loops. The current design includes 8 loops, which would cover the whole house (upper floors, not basement, approx 1800sq ft). However, the plan is not to install all loops at once. I have two loops installed (done during renovations) and ready to be hooked up. I designed the manifold to accommodate the whole house so that in the future, the existing radiators could be taken offline and replaced with radiant loops.
All loops will have individual balancing valves.
Because the system will be sized for the whole output, but only running a few loops initially, I want to include a a differential bypass between the supply and return. It seems to me, that a balancing valve could accomplish the same thing, just not automated. The advantage of the balancing valve is no moving parts (theoretically more reliable), cheaper initial cost and more compact (easier to integrate into my design). The downside is that I would have to adjust it manually each time I added a loop. I am ok with this and maybe even prefer it as it would be one less thing to diagnose if issues come up.
Alternatively, I could install a dP pump. My hangup here is that I am not using zone valves, so it seems like a waste. The plan is to balance the system using balancing valves and maintain a constant temp throughout the home. Once the flow is set, it should not need adjustment until another loop is added.
Am I missing any details about what a DPV offers over a balancing valve? Do they truly accomplish the same thing?
I am designing a manifold system for low temp radiant loops. The current design includes 8 loops, which would cover the whole house (upper floors, not basement, approx 1800sq ft). However, the plan is not to install all loops at once. I have two loops installed (done during renovations) and ready to be hooked up. I designed the manifold to accommodate the whole house so that in the future, the existing radiators could be taken offline and replaced with radiant loops.
All loops will have individual balancing valves.
Because the system will be sized for the whole output, but only running a few loops initially, I want to include a a differential bypass between the supply and return. It seems to me, that a balancing valve could accomplish the same thing, just not automated. The advantage of the balancing valve is no moving parts (theoretically more reliable), cheaper initial cost and more compact (easier to integrate into my design). The downside is that I would have to adjust it manually each time I added a loop. I am ok with this and maybe even prefer it as it would be one less thing to diagnose if issues come up.
Alternatively, I could install a dP pump. My hangup here is that I am not using zone valves, so it seems like a waste. The plan is to balance the system using balancing valves and maintain a constant temp throughout the home. Once the flow is set, it should not need adjustment until another loop is added.
Am I missing any details about what a DPV offers over a balancing valve? Do they truly accomplish the same thing?