Welcome! Here are the website rules, as well as some tips for using this forum.
Need to contact us? Visit https://heatinghelp.com/contact-us/.
Click here to Find a Contractor in your area.
Best Of
Re: Boiler Cleaning - TSP vs Washing Soda?
I'm late to this thread, having just discovered it while searching for something else. Here's a caution I learned some time ago:
A chiller manufacturer's representative warned me once to avoid TSP for cleaning the cast iron heat exchanger and the condenser water tube heat exchanger passages (mixed metals) because of the very high pH when mixed to a solution that will be effective. (About 1%)
Sodium carbonate (washing soda) was suggested instead because it has a lower pH. It also rinses with no residue to manually remove.
I don't know if TSP will cause boiler problems, but thought it wise to post here.
The Numbers-
TSP has a very high pH, at 12.5 for a 1% solution. Washing soda is lower. Unfortunately, I can't find the washing soda pH chart. If I remember correctly, pure sodium carbonate mixed to 1% was 10.5pH.
The pH scale isn't linear, it's logarithmic, so a one point change is substantial.
Sorta Off Topic, But Interesting-
Interestingly, the TDS sheets for many latex paint & primer products say to avoid TSP for pre-paint washing. Some tech supports say it's because of the very high pH, some say because of the hard-to-remove residue that is left behind.
Hope This Helps Someone Someday!
Paul
A chiller manufacturer's representative warned me once to avoid TSP for cleaning the cast iron heat exchanger and the condenser water tube heat exchanger passages (mixed metals) because of the very high pH when mixed to a solution that will be effective. (About 1%)
Sodium carbonate (washing soda) was suggested instead because it has a lower pH. It also rinses with no residue to manually remove.
I don't know if TSP will cause boiler problems, but thought it wise to post here.
The Numbers-
TSP has a very high pH, at 12.5 for a 1% solution. Washing soda is lower. Unfortunately, I can't find the washing soda pH chart. If I remember correctly, pure sodium carbonate mixed to 1% was 10.5pH.
The pH scale isn't linear, it's logarithmic, so a one point change is substantial.
Sorta Off Topic, But Interesting-
Interestingly, the TDS sheets for many latex paint & primer products say to avoid TSP for pre-paint washing. Some tech supports say it's because of the very high pH, some say because of the hard-to-remove residue that is left behind.
Hope This Helps Someone Someday!
Paul

1
Re: Thinning Copper
I've seen it 100 times around Philly. USN electrical school; civilian HVAC&R and Oil and Gas burner training notwithstanding. Mostly worked larger commercial systems. (But see the problem mostly in [older] home-sized systems/buildings with some newer technology installed.) Spent nearly 20 years investigating property insurance claims cause-of-loss, and successfully argued many claims as an expert for both property owners and insurers.
The contributing factors vary, depending on the system, but the underlying problem is always the same. (One caveat is extremely acid (low pH below 5) water, or alkaline (high pH above 8) which would be a rarity, with untreated well water in a system. By all means however, if in doubt, check and rule out pH.
Here I want to interject, the second picture of the copper cut is not full or consistent wall thickness. That piece too has begun to thin, it's just hard to see. I will not explain all the scenarios here, or tell-tale signs, as they are many, and again, vary. I'd need Dan Hollahan to help me write a book.
Three main contributing factors most often cause this problem, and one common denominator has always accompanied, or can be the sole cause. IE: partial or full loss of earth ground. I was in NH at Viega with Lou Abruzzese formerly lead tech at United Refrigeration, to present technology to address this problem.
Problem, one word: ELECTROLYSIS. I would lie to forensically investigate your system and show you. (Moreover, the property owner may have insurance coverage for the damage.) Piecing-in plastic repair sections may aggravate the problem and send it elsewhere in the building. Significant damage or not, it will progress and/or re-emerge if not corrected, and it doesn't happen overnight. It is showing up so much because of newer technology such as VFDs and even ECMs. Pump Manufacturers deny a problem in fractional horsepower systems, but AEGIS RIngs were developed to address damage to multi-horsepower motors. I've witnessed and corrected it in systems with small variable speed circulators, and the problem even linked to variable speed combustion fans in gas boilers. It is a phenomenon engineering has touched on (as with AEGIS Rings) but not fully understood or embraced.
Do this: (and it can be quite tedious and detailed, or as simple as a new building electrical system earth grounding rod.) Check every ground connection in the building electrical system. At the very least, Ground Your System! as a stand alone. IE: drive a grounding rod next to your heating equipment if you must, ensure grounding including necessary shunts throughout and protect your system. Again, you may be sending the problem elsewhere in the building, but your stuff is protected.
This really needs a book written on the subject and real-life solutions/mitigation. Dan, help!
If I were there, I could demonstrate the effect and solution, but cannot address every system and every possibility here. This took me decades of empirical research in the field to fully grasp the depth and breadth of this insidious unseen, often slowly developing long term problem. I would love to inspect your Grundfos 10-16 ECM pump internals, some system components, and perform analysis on your copper piping.
Three examples: 1. Ever seen a hole pit right through the side of a water heater relief valve? 2. A law faucet at one sink rot down right in place? Same effect. In any case, you are basically electroplating the sewer, or something somewhere where transient currents can find ground. 3. Have inexplicable nuisance flame failures on that furnace you can't seem to solve? 99.9% you have a grounding problem.
Ground! Ground! Ground! Ground the World, so to speak. Then Ground some more.
This is me - Never developed the page:
https://www.facebook.com/DrGrounding
The contributing factors vary, depending on the system, but the underlying problem is always the same. (One caveat is extremely acid (low pH below 5) water, or alkaline (high pH above 8) which would be a rarity, with untreated well water in a system. By all means however, if in doubt, check and rule out pH.
Here I want to interject, the second picture of the copper cut is not full or consistent wall thickness. That piece too has begun to thin, it's just hard to see. I will not explain all the scenarios here, or tell-tale signs, as they are many, and again, vary. I'd need Dan Hollahan to help me write a book.
Three main contributing factors most often cause this problem, and one common denominator has always accompanied, or can be the sole cause. IE: partial or full loss of earth ground. I was in NH at Viega with Lou Abruzzese formerly lead tech at United Refrigeration, to present technology to address this problem.
Problem, one word: ELECTROLYSIS. I would lie to forensically investigate your system and show you. (Moreover, the property owner may have insurance coverage for the damage.) Piecing-in plastic repair sections may aggravate the problem and send it elsewhere in the building. Significant damage or not, it will progress and/or re-emerge if not corrected, and it doesn't happen overnight. It is showing up so much because of newer technology such as VFDs and even ECMs. Pump Manufacturers deny a problem in fractional horsepower systems, but AEGIS RIngs were developed to address damage to multi-horsepower motors. I've witnessed and corrected it in systems with small variable speed circulators, and the problem even linked to variable speed combustion fans in gas boilers. It is a phenomenon engineering has touched on (as with AEGIS Rings) but not fully understood or embraced.
Do this: (and it can be quite tedious and detailed, or as simple as a new building electrical system earth grounding rod.) Check every ground connection in the building electrical system. At the very least, Ground Your System! as a stand alone. IE: drive a grounding rod next to your heating equipment if you must, ensure grounding including necessary shunts throughout and protect your system. Again, you may be sending the problem elsewhere in the building, but your stuff is protected.
This really needs a book written on the subject and real-life solutions/mitigation. Dan, help!
If I were there, I could demonstrate the effect and solution, but cannot address every system and every possibility here. This took me decades of empirical research in the field to fully grasp the depth and breadth of this insidious unseen, often slowly developing long term problem. I would love to inspect your Grundfos 10-16 ECM pump internals, some system components, and perform analysis on your copper piping.
Three examples: 1. Ever seen a hole pit right through the side of a water heater relief valve? 2. A law faucet at one sink rot down right in place? Same effect. In any case, you are basically electroplating the sewer, or something somewhere where transient currents can find ground. 3. Have inexplicable nuisance flame failures on that furnace you can't seem to solve? 99.9% you have a grounding problem.
Ground! Ground! Ground! Ground the World, so to speak. Then Ground some more.
This is me - Never developed the page:
https://www.facebook.com/DrGrounding
Re: How to fix this mono flow rad? (FIXED)
circ is fineHow do we know this? What are we calling "fine"?
Also, removing the tees and going full-flow through the radiator will make the rad heat to its full potential at every call for heat....unless there's some kind of ODR logic in place...which may or may not suit your purposes. Be ready for that. With the limited info we have here, it looks to me like there are too many elbows and too long of a run with small pipe to permit flow through that branch. You probably already know this but the TDH through the heat emitter branch can't exceed that of the piping between the supply and return tees, which tends to be not very much and is mostly determined by the Delta-P through the Venturi cone. Is my stream of conciousness helping yet? I find 1-pipe hydronic systems to be pretty darn interesting. I just wish they worked better.
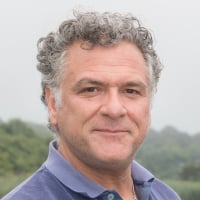
2
Re: How to fix this mono flow rad? (FIXED)
At seventy years old, I would be concerned about the internal condition of the monoflow tees. We have numerous residential and commercial customers that have similar systems with cast iron monoflow tees. On one job in particular that has or had numerous system leaks over time, the tees were in poor condition.
Many of these tees were plugged with rust and sediment (on the bull that feeds the radiator). In some instances the venturi (cone) was missing or in poor condition. On one very large system, the half inch steel pipe that fed the radiator above was clogged for a few feet. If your system has had a leaky boiler or some rotted pipes I would be very concerned that the monoflow tee is not doing what it was designed to do, namely divert water to the radiator.
Many of these tees were plugged with rust and sediment (on the bull that feeds the radiator). In some instances the venturi (cone) was missing or in poor condition. On one very large system, the half inch steel pipe that fed the radiator above was clogged for a few feet. If your system has had a leaky boiler or some rotted pipes I would be very concerned that the monoflow tee is not doing what it was designed to do, namely divert water to the radiator.
Re: Snowmelt
The edge loss is a big number also as it is exposed to ambient air temperature all the time.
At some point the earth under a non insulated slab warms and reduces the downward losses.
Not to say ignore underslab insulation, some of the early radiant design guides did not always show snowmelt slab insulation insulation.
A slab with that much mass, about 30 yard per slab at 9" = 120,000 lbs! and no insulation in a critical application like a fire station may need to be idled as the start up response will be very slow.
Hopefully the design is a high BTU/ sq ft? Appropiate for the class of melt as per ASHRAE
You would want a certified compaction test for that much slab and equipment weight also. Slabs fail due to improper site work often times.
It may require high load foam. Most foam board is 15- 25 psi.
Dow makes high load foam board up to 60 or 80 psi $$.
The insulation may cost as much as the slab
I doubt any engineer will sign off on operating costs, and that is where you will take the hit without insulation.
At some point the earth under a non insulated slab warms and reduces the downward losses.
Not to say ignore underslab insulation, some of the early radiant design guides did not always show snowmelt slab insulation insulation.
A slab with that much mass, about 30 yard per slab at 9" = 120,000 lbs! and no insulation in a critical application like a fire station may need to be idled as the start up response will be very slow.
Hopefully the design is a high BTU/ sq ft? Appropiate for the class of melt as per ASHRAE
You would want a certified compaction test for that much slab and equipment weight also. Slabs fail due to improper site work often times.
It may require high load foam. Most foam board is 15- 25 psi.
Dow makes high load foam board up to 60 or 80 psi $$.
The insulation may cost as much as the slab

I doubt any engineer will sign off on operating costs, and that is where you will take the hit without insulation.
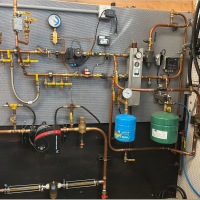
4
Re: I'm in hot water (pun intended) - Boiler reconditioning
All gone now, replaced by condos etc.

1
Re: Thinning Copper
Thermal balance valves work by watching and responding the temperature where they are installed, typically at the return of the recirc branch(s)
Suppose you have a building with uninsulated HW piping, common in older buildings everywhere. Suppose also that piping runs through cold spaces, unconditioned space, 55° crawlspaces, basement plenum spaces etc. The thermal balance valve will open to whatever flow rate is required to try and meet the return temperature setting. It could require .5 gpm, or 4 gpm to get the return temperature required by the setter.
It does not, cannot maintain a specific flow rate or velocity. With a 5 psid the 3/4 valve you mentioned will allow 4 gpm, which is in excess of 2 fps in 3/4 copper tube.
Thermal balance valves offer a unique temperature solution for a temperature problem. Great for retrofitting older recirc installations with problems.
The recirc pump needs to be sized to provide adequate flow and pressure differential to overcome the most hydraulically remote, and or highest temperature drop circuit, if a building has multiple recic loops.
In some cases high head, high flow recirc pumps are needed to get the job done.
On large hotels, hospitals with sprawling pipe layouts we often see pumps pumps like Grundfos Magnas used. They provided the needed flow and also modulate with the thermal balance valve operation.
Keep in mind the pressure drop across the thermal setter needs to be in the calculation. When closed down expect a very low Cv. the ThermoSetter is .35Cv at the low end. The thermosetters need flow always to be able to respond, so the .35 needs to be accounted for in the pump calc. Another reason to use a delta P pump and let it run 24/7
In the example below the pump spec is 17.5' to get the 1.5 gpm in an insulated pipe example. Well beyond that 15-16 dhw pump.
The graphs below show the considerable heat loss difference between insulated and un-insulated copper. flow rate has to compensate for this. Typically you run a 10∆ on a recirc loop, leave the tank at 120, return from farthest fixture at 110°
A dynamic balance valve like a PIC valve would be able to limit the flow to a specific gpm, in a branch requirement. They too are used in DHW balance, but do not adjust or respond to temperature, Caleffi offers one with a temperature gauge for dynamic recirc balancing..
My point being you need to do some math when you install thermal type balance valves and spec the pump. The head required may surprise you.
Suppose you have a building with uninsulated HW piping, common in older buildings everywhere. Suppose also that piping runs through cold spaces, unconditioned space, 55° crawlspaces, basement plenum spaces etc. The thermal balance valve will open to whatever flow rate is required to try and meet the return temperature setting. It could require .5 gpm, or 4 gpm to get the return temperature required by the setter.
It does not, cannot maintain a specific flow rate or velocity. With a 5 psid the 3/4 valve you mentioned will allow 4 gpm, which is in excess of 2 fps in 3/4 copper tube.
Thermal balance valves offer a unique temperature solution for a temperature problem. Great for retrofitting older recirc installations with problems.
The recirc pump needs to be sized to provide adequate flow and pressure differential to overcome the most hydraulically remote, and or highest temperature drop circuit, if a building has multiple recic loops.
In some cases high head, high flow recirc pumps are needed to get the job done.
On large hotels, hospitals with sprawling pipe layouts we often see pumps pumps like Grundfos Magnas used. They provided the needed flow and also modulate with the thermal balance valve operation.
Keep in mind the pressure drop across the thermal setter needs to be in the calculation. When closed down expect a very low Cv. the ThermoSetter is .35Cv at the low end. The thermosetters need flow always to be able to respond, so the .35 needs to be accounted for in the pump calc. Another reason to use a delta P pump and let it run 24/7
In the example below the pump spec is 17.5' to get the 1.5 gpm in an insulated pipe example. Well beyond that 15-16 dhw pump.
The graphs below show the considerable heat loss difference between insulated and un-insulated copper. flow rate has to compensate for this. Typically you run a 10∆ on a recirc loop, leave the tank at 120, return from farthest fixture at 110°
A dynamic balance valve like a PIC valve would be able to limit the flow to a specific gpm, in a branch requirement. They too are used in DHW balance, but do not adjust or respond to temperature, Caleffi offers one with a temperature gauge for dynamic recirc balancing..
My point being you need to do some math when you install thermal type balance valves and spec the pump. The head required may surprise you.
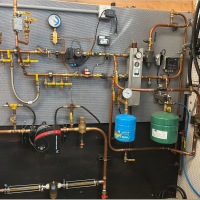
2
Re: Just to stir the pot...
Oddly enough, the one thing that is least likely to be affected by lowering the Hz, is an inverter heat pump. Their whole schtick is lowering the Hz. That's why you generally don't see and can't find their real efficiencies as they have to be tested and listed while locked at 60 Hz as that is the standard in the US. It's like rating a gas fired boiler's efficiency under the least efficient circumstances possible. And even then the inverters are putting out far more than you put in despite the claim "You can’t put in less and get more than was put in impossible unless just on paper "
1
Re: Please Fact-check Retired Plumber's Advice Re: TRVs & Lockshields
I'm with Hot Rod on these issues. While we certainly have installed many TRVs, they are rarely a quick and easy install. The benefits may or may not be worth the cost of the labor and materials. This is especialy true if the original designer was good at sizing the radiation.
One other thing to consider, is that we've noticed with older hot water systems (made up of mostly steel and iron), that metallic particles occasionally end up on-or-in the seat of the brand new valve.
One other thing to consider, is that we've noticed with older hot water systems (made up of mostly steel and iron), that metallic particles occasionally end up on-or-in the seat of the brand new valve.