Welcome! Here are the website rules, as well as some tips for using this forum.
Need to contact us? Visit https://heatinghelp.com/contact-us/.
Click here to Find a Contractor in your area.
Best Of
Re: The case of the high gas costs, this Friday's case
Good morning the customer indeed replaced the normally open vent valve with a normally closed one. They look so similar. The vent valve was used to vent any gas leaking through the first gas valve. It amazes me that there is a certain amount of gas leakage permitted with a gas valve. I have enclosed the allowable leakage chart for a Honeywell V48 valve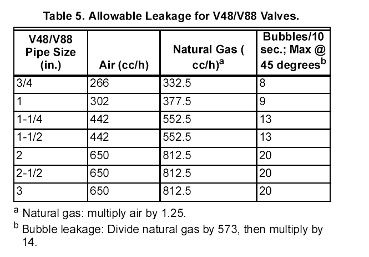
Here is the link to this weeks case, The Case of the High Gas Costs https://youtube.com/watch?v=3GfQKxglZso
I also posted another video. It was an article I wrote for Mechanical Business Magazine Its called Troubleshooting Hydronics https://youtube.com/watch?v=YIMBJ78cWyI
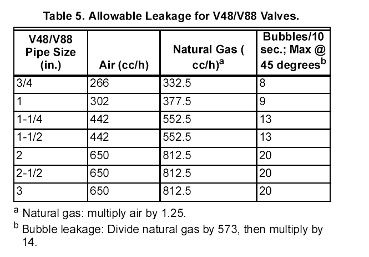
Here is the link to this weeks case, The Case of the High Gas Costs https://youtube.com/watch?v=3GfQKxglZso
I also posted another video. It was an article I wrote for Mechanical Business Magazine Its called Troubleshooting Hydronics https://youtube.com/watch?v=YIMBJ78cWyI
Re: Snowmelt
Same design but with R-10 edge and underslab and the downward loss drops to 4 btu/sqft.
Snow Melt Design Sheet Project Name
Date
Location
Tag
Inputs Outputs
Length 100 Area,sqft 1200.00
Width 12 Btu/sqft 156.20
Design Temperature 0 Total Melting Load,btu/h 187439.81
Wind Speed, mph 5
Altitude Sea level Downward loss,btu/h/sqft 3.85
Snow Fall Per hour,inches 4 Edge Loss, btu/h/sqft 1.93
Area Free Ratio Snow Free=1
Total Load,btu/h 194378.87
Snow Melt Panel Assembly
Layer 1 Material Concrete
Layer 1 Thickness, inches 0 Supply Water Temperature 106.53
Layer 2 Material Concrete Flow,gpm 16.61
Layer 2 Thickness, inches 0 Loop Length 24.00
Tube Layer material Concrete Flow Per Loop 0.17
Tube Layer Thickness, inches 9 Pressure Loss,ft/hd 0.01
Tube Depth In Layer 3 Velosity,fps 0.15
Underslab Insulation 2" R-10
Edge Insulation 2" R-10 Total Tube Required 2400
Slab Long Axis Orientation N S
Dominant Wind Direction N S
Tube Size 3/4" HePex
Tube Spacing 6 Model Conditions vs. Design
Number Of Loops 100 Outdoor Temperature 10
Wind Speed, mph 5
Glycol % 40 Snow Fall Per Hour, inches 6
Design Temperature Differential 25 Area Free Ratio Snow Free=1
Operation Mode Idle/On Btu/sqft Required 188.78
Film Temperature 33 Btu/sqft Available 156.20
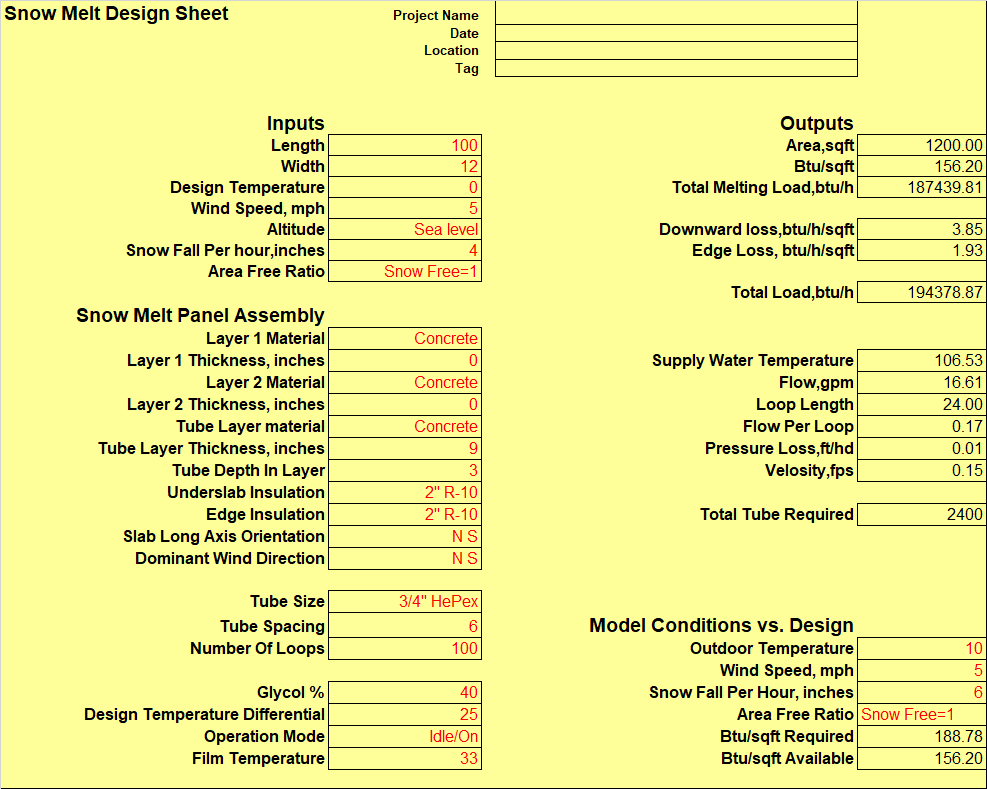
Snow Melt Design Sheet Project Name
Date
Location
Tag
Inputs Outputs
Length 100 Area,sqft 1200.00
Width 12 Btu/sqft 156.20
Design Temperature 0 Total Melting Load,btu/h 187439.81
Wind Speed, mph 5
Altitude Sea level Downward loss,btu/h/sqft 3.85
Snow Fall Per hour,inches 4 Edge Loss, btu/h/sqft 1.93
Area Free Ratio Snow Free=1
Total Load,btu/h 194378.87
Snow Melt Panel Assembly
Layer 1 Material Concrete
Layer 1 Thickness, inches 0 Supply Water Temperature 106.53
Layer 2 Material Concrete Flow,gpm 16.61
Layer 2 Thickness, inches 0 Loop Length 24.00
Tube Layer material Concrete Flow Per Loop 0.17
Tube Layer Thickness, inches 9 Pressure Loss,ft/hd 0.01
Tube Depth In Layer 3 Velosity,fps 0.15
Underslab Insulation 2" R-10
Edge Insulation 2" R-10 Total Tube Required 2400
Slab Long Axis Orientation N S
Dominant Wind Direction N S
Tube Size 3/4" HePex
Tube Spacing 6 Model Conditions vs. Design
Number Of Loops 100 Outdoor Temperature 10
Wind Speed, mph 5
Glycol % 40 Snow Fall Per Hour, inches 6
Design Temperature Differential 25 Area Free Ratio Snow Free=1
Operation Mode Idle/On Btu/sqft Required 188.78
Film Temperature 33 Btu/sqft Available 156.20
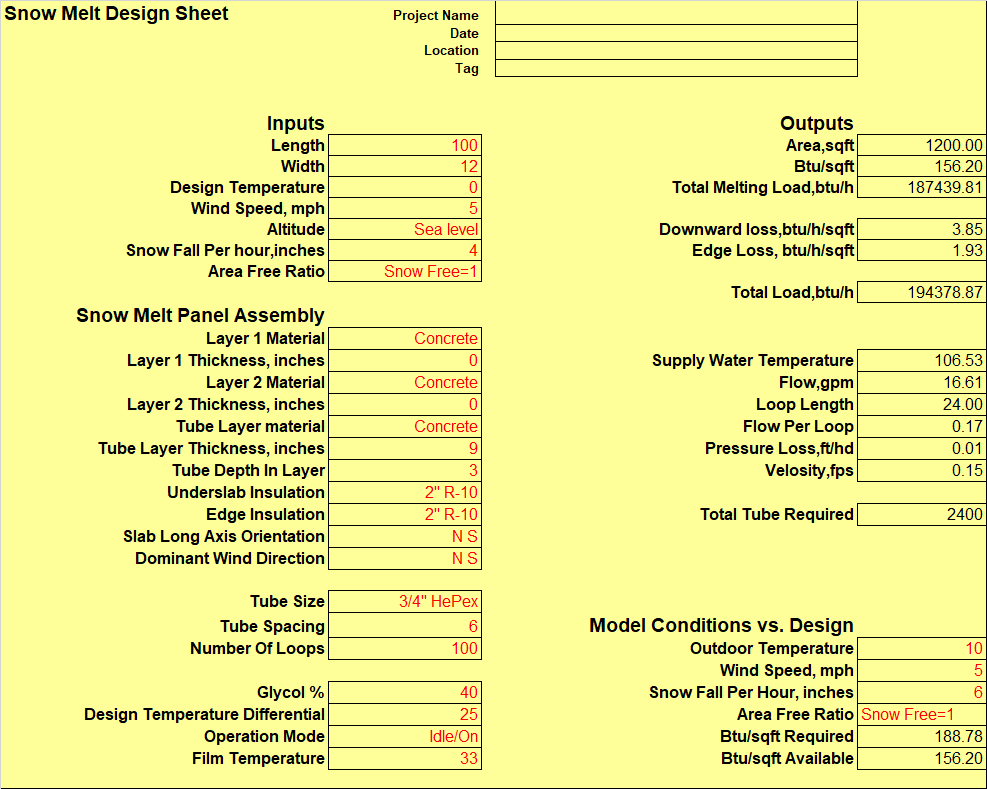

1
Re: Snowmelt
Here is the design info using the ASHRAE design methodology. It calculates about 61 btu/sqft of downward loss with no insulation.
Snow Melt Design Sheet Project Name
Date
Location
Tag
Inputs Outputs
Length 100 Area,sqft 1200.00
Width 12 Btu/sqft 156.20
Design Temperature 0 Total Melting Load,btu/h 187439.81
Wind Speed, mph 5
Altitude Sea level Downward loss,btu/h/sqft 61.44
Snow Fall Per hour,inches 4 Edge Loss, btu/h/sqft 190.58
Area Free Ratio Snow Free=1
Total Load,btu/h 489863.82
Snow Melt Panel Assembly
Layer 1 Material Concrete
Layer 1 Thickness, inches 0 Supply Water Temperature 106.53
Layer 2 Material Concrete Flow,gpm 41.87
Layer 2 Thickness, inches 0 Loop Length 24.00
Tube Layer material Concrete Flow Per Loop 0.42
Tube Layer Thickness, inches 9 Pressure Loss,ft/hd 0.05
Tube Depth In Layer 3 Velosity,fps 0.38
Underslab Insulation None
Edge Insulation None Total Tube Required 2400
Slab Long Axis Orientation N S
Dominant Wind Direction N S
Tube Size 3/4" HePex
Tube Spacing 6 Model Conditions vs. Design
Number Of Loops 100 Outdoor Temperature 10
Wind Speed, mph 5
Glycol % 40 Snow Fall Per Hour, inches 6
Design Temperature Differential 25 Area Free Ratio Snow Free=1
Operation Mode Idle/On Btu/sqft Required 188.78
Film Temperature 33 Btu/sqft Available 156.20
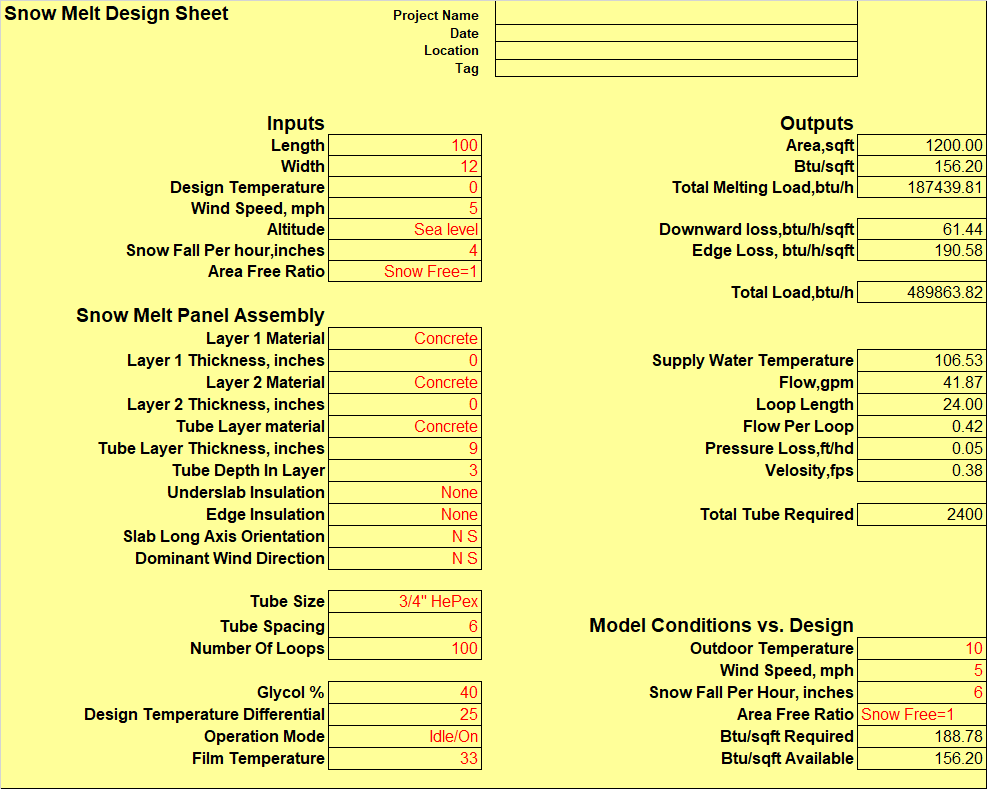
Snow Melt Design Sheet Project Name
Date
Location
Tag
Inputs Outputs
Length 100 Area,sqft 1200.00
Width 12 Btu/sqft 156.20
Design Temperature 0 Total Melting Load,btu/h 187439.81
Wind Speed, mph 5
Altitude Sea level Downward loss,btu/h/sqft 61.44
Snow Fall Per hour,inches 4 Edge Loss, btu/h/sqft 190.58
Area Free Ratio Snow Free=1
Total Load,btu/h 489863.82
Snow Melt Panel Assembly
Layer 1 Material Concrete
Layer 1 Thickness, inches 0 Supply Water Temperature 106.53
Layer 2 Material Concrete Flow,gpm 41.87
Layer 2 Thickness, inches 0 Loop Length 24.00
Tube Layer material Concrete Flow Per Loop 0.42
Tube Layer Thickness, inches 9 Pressure Loss,ft/hd 0.05
Tube Depth In Layer 3 Velosity,fps 0.38
Underslab Insulation None
Edge Insulation None Total Tube Required 2400
Slab Long Axis Orientation N S
Dominant Wind Direction N S
Tube Size 3/4" HePex
Tube Spacing 6 Model Conditions vs. Design
Number Of Loops 100 Outdoor Temperature 10
Wind Speed, mph 5
Glycol % 40 Snow Fall Per Hour, inches 6
Design Temperature Differential 25 Area Free Ratio Snow Free=1
Operation Mode Idle/On Btu/sqft Required 188.78
Film Temperature 33 Btu/sqft Available 156.20
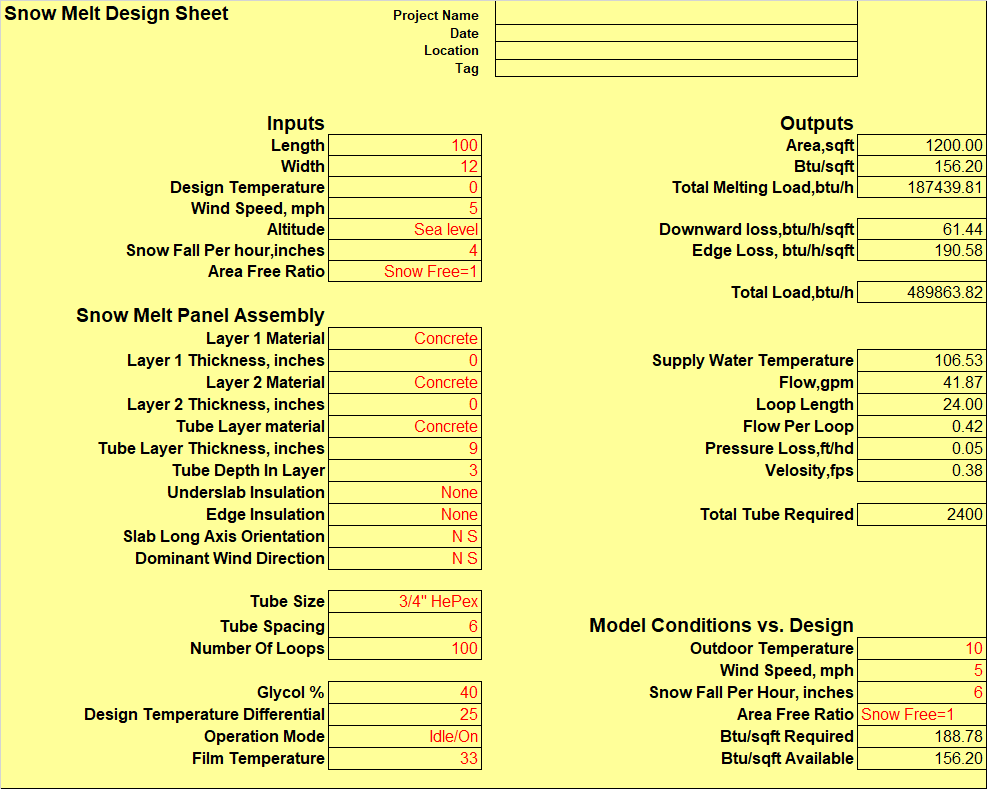

1
Re: Single line oil tank bushing help - top of tank
Thanks @EdTheHeaterMan. Your link includes compression fittings, they are ok to use instead of flared? Everything I see says to never use any compression fittings.The compression fittings are not to seal the oil line as a leak free fitting. the compression fittings are to hold the fuel line in place so the fuel line does not move up or down inside the tank.
The best practice for that fitting is to remove about 48" of the plastic cover from the fuel line. Then slide the compression nut over the fuel line until you reach the plastic covering, followed by the compression ring, then followed by the compression fitting. Those fittings are designed without a stop for the copper to be able to slide thru. Once the fitting is 48” past the end of the tube, straighten the tubing and insert the tubing into the tank thru the ⅜” pipe tap opening. With the copper on the bottom of the tank, slide the compression fitting into the ⅜” threads and tighten the fitting. Next slide the compression ring and the compression nut on the fitting but do not tighten the compression nut.
Now with the fuel line on the bottom of the tank, raise the fuel line up about 2-½” to 3-½” off the tank floor. Now tighten the compression nut to hold the fuel line in place. Not too tight, just tight enough to hold the tubing in place. By using this method, you will have one piece of tubing with no fittings at the top that can leak air into the fuel line that can cause a break in the siphon line and cause air to create a no heat situation because the fuel pump loses its prime.
This is an old trick I learned over 45 years ago. The tube is seamless, one piece, with no fittings, from inside the bottom of the tank to the top of the tank and then back down to below the tank. Once you prime the fuel line, that will act as a siphon and you will have trouble free operation.
Re: Spokes and baseball cards
I was a Football Guy in the early 1970s, so I used Football cards in my spokes. The future delinquents of my Neighborhood used to steal Chrome Caps off the Tires of The Caddys and sell them to us for our bike tires...50 Cent each! What we REALLY loved to do is make ramps like Evil Knieval and Jump them...Got knocked out once...Wore my football Helmet and All the Pads after that. We had a GREAT childhood.. just be home for dinner.. Mad Dog 🐕
Re: What's buried here?
Could be an oil tank valve handle. I have seen gate valves on oil lines before. Have you opened up the pipe plug and put a 10' stick in that pipe to see if it goes to an oil tank?
Re: Just to stir the pot...
It was decades ago, I don’t even remember where it was, not Arthur Ave., though. Pretty sure it was called Mamas, and when you walked in there she was your Mama, heros as big as an aircraft carrier and so stuffed you couldn’t fold them in half. For some reason I’m recalling lots of Yankee memorabilia on the walls.
Then there was some old timer somewhere else in the Bx, in a storefront that looked abandoned, steamy windows, a wreck inside, you’d never know what it was from the outside. But every lunchtime he’d set up steam tables and made some of the best heros I’ve ever had - brisket with boiled potatoes and peppers, yeesh. I think he was an old Marine vet, had some old photos on the walls.
Then there was some old timer somewhere else in the Bx, in a storefront that looked abandoned, steamy windows, a wreck inside, you’d never know what it was from the outside. But every lunchtime he’d set up steam tables and made some of the best heros I’ve ever had - brisket with boiled potatoes and peppers, yeesh. I think he was an old Marine vet, had some old photos on the walls.
Re: Where is Bob Bona these Days??
Bob is solid. We went out for drinks a few times over the years and always had lots of laughs. If you speak to him, Matt, please tell him I said hello.
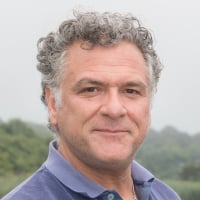
1