Boiler Running Full Tilt, Cold House
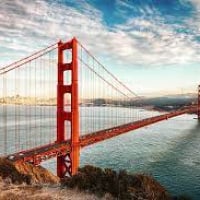
This Lochinvar has been running at 100% modulation for days after heating without any problem for years. It has not been de-rated in the programming; CO2 is 8.5%, flue temperature is 71F. Technical support at Lochinvar thinks that the HX is occluded, but I think we would see a higher stack temperature. I have my own theory. What do you think?
Two btu per sq ft for degree difference for a slab
Comments
-
it isn't pushing enough air through the gas valve one way or another. air leak, blower running slow or damaged or clogged, something else clogged or iced. if it were a gas supply issue the mixture would be off. it is burning right just not enough volume. hx filled mostly with condensate?
0 -
has it been taking on fill water that could have scaled it up?
What type of heat emitters?
Is it primary secondary or a LLH? The display shows pump 1 and 3 activated?
Bob "hot rod" Rohr
trainer for Caleffi NA
Living the hydronic dream0 -
-
Combustion is good must be underfired. I would think the flue temp would be higher if the HX was the issue.
Doesn't the flue temp follow the water outlet temp?
0 -
-
-
it doesn't have any way to actually measure the air or gas flowing through the boiler, it just either know what voltage it sent to the fan motor or maybe has a tachometer lead on the fan motor and calculates the firing rate from that.
@EBEBRATT-Ed the flue temp is a function of the return water temp. the hx is arranged so the flue gases hit the return water last so it can approach the return water temp
0 -
If the boiler is firing at 100% then its adding all the Btu that it can produce to the heating medium. All those BTU's are going somewhere. No matter how bad your combustion is. If he is leaking water he is just heating feed water that is just draining.
And I don't think he has a dirty he exchanger as it still in the condensing mode.
@mattmia2 I doubt the software is lying, that was saying sarcastically. The hall sensor in the ECM motor communicates with the CPU to tell how fast the ECM is running. the speed of the ECM motor dictates the BTUS delivered into the system. If the motor is calling for 100% RPM then its asking for the maximum BTU input.
0 -
Have you verified actual fluid and flue temps? Have you placed it in service mode and manually adjusted the fan speed to verify it's hitting both ends (high fire is usually around 8900 RPM)? Have you turned off the feeder to verify it's not just pouring everything right back out under the slab?
0 -
I chatted with the folks at the Sermeta booth at AHR this week. As @pedmec mentioned the fan speed regulates the firing rate of the burner.
My specific question was if the burner could run at it's lowest firing rate for long periods without any issues. As that question came up here recently. Yes, as long as the gas valve is adjusted to the fan speed. The correct valve/fan assembly, and adjusted accurately. Combustion trimming is be a must.
He did mention the burners for the USA market tend to be the version that looks like a mesh or steel wool wrap. The burners in Europe are laser slotted stainless tubes. This has to do with NG gas quality and blends in Europe.
Bob "hot rod" Rohr
trainer for Caleffi NA
Living the hydronic dream0 -
Take a look at the picture and you will see the water feed turned off. That was the first thing I did and the water pressure stuck at 15psi for as long as I was there.
@GroundUp The fluid temperature shown on the screen is fairly accurate by feeling the pipes. The stack temperature was verified by my combustion analyzer. I did not verify the fan speed, but I heard it ramp up after ignition and it seemed to follow the displayed percentages.
It's been raining heavily here and I thought a high water table might be sucking heat out of the slab, but I still have other things to test before settling on that. I'll go back soon and clock the gas meter. Maybe pull the lid off the HX to see if anything looks amiss.
8.33 lbs./gal. x 60 min./hr. x 20°ΔT = 10,000 BTU's/hour
Two btu per sq ft for degree difference for a slab2 -
That only tells you how fast the fan is turning, not how much air it is moving or how much air is moving through the gas valve. In my UFT the fan pushes through the gas valve so if there is a leak between the fan and the gas valve it won't get the flow it claims. About half of the potential problems here are engine manifold vacuum leak 101.
Could you get enough flow through a bad diaphragm in a pressure switch to significantly affect the firing rate but still close the switch?
Could the inlet be restricted enough to reduce the airflow significantly but still make the pressure switch happy? What happens if you disconnect the inlet piping?
1 -
I had a customer with a similar condition. Early munchkin serving a completely uninsulated slab section on S.F. hillside. Pre thermal camera. After much theorizing and measurement I found the smoking gun. Being on a hill there was little question about what way heated water would flow if that was the loss case. After six small holes were drilled in the joint of the driveway below the structure the heat flow was identified. It would have been easier with a thermal camera. Running flat out for 24 hrs will have a loss signature somewhere. The volume of dripping condensate is proof positive of BTU development.
2 -
-
I've seen this one, too, in Massachusetts. And if you start crunching numbers, it's quite astonishing how much heat that flowing groundwater can take away… without even raising its temperature all that much.
Br. Jamie, osb
Building superintendent/caretaker, 7200 sq. ft. historic house museum with dependencies in New England0 -
@Alan (California Radiant) Forbes Have you looked at the water meter? A constant well placed domestic leak might be able to sap off BTU’s. Is that an 80k? I know those Eichler’s need all BTU’s a small boiler can offer to bring the structure to 70f on a cold day. It’s hard to see signs of a leak in the rain if it doesn’t come through the top of the slab. Check any French drain outlets. Can you thermal camera to follow the heat?
0 -
I just went back to the job this morning. The domestic water meter is as steady as a rock.
I clocked the gas meter at 65 seconds to use ½ a cubic foot of gas with the boiler running at 100% with no other gas appliance being used other than the water heater pilot light. Tell me if I'm wrong, but my calculations show that 27,700 BTU were used by an 80,000 BTU boiler running at 100%. This is new territory for me as I've never had this happen. My first guess would be a bad gas valve.
8.33 lbs./gal. x 60 min./hr. x 20°ΔT = 10,000 BTU's/hour
Two btu per sq ft for degree difference for a slab1 -
-
if the gas valve were bad the combustion would be off(as far as i can tell). It is doing exactly what it is supposed to do but there is less air moving through it than what is supposed to be.
also check the pressure both at the meter and the appliance. if the gas pressure is low or high at the meter then your calculations cloking the meter will be off. the meter measures volume. the density of the gas varies greatly with pressure.
but my bet is on airflow it either leaking or restricted through the appliance.
htp had a problem with a flapper that would break off and restrict air flow.
i will note that it is much easier for me to think about this sitting around for hours than having a few minutes standing in front of the thing.
1 -
measuring the draft at various points in the combustion path might tell you what is going on but that is a little beyond my understanding.
0 -
Stupid question, but have you tried shutting down for 5 minutes and restarting? Or going into Service Mode and try to manually adjust the firing rate? Can fan RPM be shown in the display?
Could incoming gas pressure be low? Even at a low input, I'd expect a higher flue temperature than 71°. I would lean towards the board or sensor(s) if gas pressure is good.
0 -
-
because the fan motor is spinning at 100%. it is not moving 100% air/fuel mixture through the combustion chamber or likely 100% air through the gas valve. it appears that the airflow is about 40%.
0 -
-
-
-
I never checked the gas pressure because I thought it would have locked out if the pressure got too low. Personally, I think the gas pressure on the inlet side will check out fine and if I have time today, I'll go and get a reading.
I also want to remove the makeup air pipe and check the shutter that hr pointed out.
I'm with @mattmia2 so far.
8.33 lbs./gal. x 60 min./hr. x 20°ΔT = 10,000 BTU's/hour
Two btu per sq ft for degree difference for a slab0 -
if the pressure at the meter is too high it would cause the index to under read and your clocking would calculate out to under firing. i don't think that is what is happening because of the other symptoms but the pressure at the meter needs to be correct for the clocking to be accurate.
0 -
i suppose you could measure the exhaust with an anemometer and work out from the diameter of the pipe the flow rate and work out what that should be at full firing by figuring the amount of air it takes to burn that amount of gas.
0 -
Fan speed is not necessarily air movement. Gas volume in the burner mixture is the result of actual air volume movement. The mixture can be of rich or lean but proper air volume is the only thing that will open the gas valve regulator enough to get proper mixture for the 80k burn. Under clocked gas volume consumption with a good burn and full fan rpm would make me look at the fan for integrity and debris or any means of air flow restriction. hot _ rod mentioned the air shutter. verify that. I’ve had condensate back ups that restrict ( with very light gurgling sounds). Lochinvar had a waterlogged condensate trap ball that falls to partially block the trap. I’ve had roofers pull the intake 180 fittings off and shove the piping down that then holds water in the rain and causes intermittent capacity problems. You are close. I’m sure you’ll get it with the next investigation. I do wish there were published air pressure ranges for different points to verify against.
1 -
-
@mattmia2 You have said as much. Correct logic must be repeated. Draft readings on power burners are different from 80k fire tube mod cons. Obviously the physics are consistent. I think flue variations, manufactures designs, air density, might make any ranges so wide to be inconclusive. Figuring it out is the task. I know I’ve needed to relearn/ remember things. I had on tap 20 years ago. It’s always so obvious once it’s found. I find it fun. Some find it trying. If it was always easy everyone would do it.
1 -
-
Looks a touch lean but pretty close to me
0 -
@GroundUp Maybe you see something I don’t. Is 8.5% CO2 way off? It’s a bit lean maybe. I guess we all have different criteria for descriptors. For me way off is reserved for it won’t light or is making carbon or is outside the specified range.
The screen stating 100% tells me the tach is likely reading in spec. for full fire or we would see a fan speed error. This is what has me wondering. Is that screen message the result of the signal or the feed back. A 100% output single with a fan loaded fan that only move 40% is possible but it would likely code out. It is not coding. If the fan impeller is damaged it could spin at the correct rpm without being able to move the air. I’m not clear on how tightly programmers are monitoring fan signal vs feed back and when.
27k BTU ( the clocked gas consumption) isn’t chump change. The house should see some warming over a 24 hr period with 55F days. Maybe they are seeing the 20 whatever thousand/hr. There’s still an obvious problem. If this clocked consumption is accurate, it’s a burn rate issue. Why is the main question. For the inquisitor like me, why has the boiler not coded out with a 100% signaled burn rate while only consuming 40%? I know air flow is the best reason. A bad impeller is all I can come up with if the tach feed back is only loosely looked at. Maybe the control doesn’t check for much. The fan can be loaded ( spinning much slower with traction) or slipping ( unloaded ) at high rpm with no code. That seems odd to me.
0 -
I don't think the boiler knows the flow on the hydronic side, the flow on the combustion side or the flow of the gas. If it were serving a snowmelt load or a cold radiant slab a swt of 77 and a delta t of 10 at 100% firing would be normal with a flow of about 15 gpm. The only thing that would look suspect from the sensors the control has is that the flue temp would likely be a little higher but it would be really hard in software to define the cutoff between normal and abnormal and not cause false errors or lockouts.
I'm not sure where the pressure switches are in the combustion path but it seems almost inevitable that there are some places that it could be restricted without the switches seeing something abnormal. It is possible that the fan is caked with something that is reducing its output too.
Assuming this is the right Nobel, it looks like the fan has 2 power leads and 4 control leads.
0 -
@mattmia2 I'm clear that the boiler knows nothing. It calculates a firing rate. It sends a fan speed signal, normally a type of PWM , the fan tries to spin up to speed, the tach sends back the actual. That’s all there is to firing rate barring a possible variable Venturi. Don’t think that applies. Either coding doesn’t care about a discrepancy or it does. There’s an allowable range. It’s hard to believe the control can request 100% fan speed and anything could limit output to 40% due to an air restriction, all the while with an 8.5% co2 burn and no code. That’ a case I want to know about. Yup maybe a caked impeller or broken or ? I would think the tachometer feed back would show any of those cases as out of range but maybe there are gray area case or condition and this is it.
0 -
How does the motor work, is it servo controlled to get the right speed or is the tach just feedback? If something like the shutter that @hot_rod showed is stuck partially open it will restrict the flow but it will also change the load on the fan motor so either the speed will change a lot or a control(either on the main board or built in to the motor) will change how much power it is developing to turn at the correct speed.
0 -
I need to find that exact model to say with any conviction. It’s not a combi. The shutters I’m familiar with are weighted doors that close off a high speed Venturi gas jet while low CFM is drawn through it. The fan programing must be tailored to how and when the shutter opens for high speed mixtures. The shutter could be caught in a mid position and the fan speed is still in range but the boiler is just limited to what the stuck shutter and small jet can produce while the control thinks it’s burning 80 k nicely. Maybe the 8.5% co2 is involving only part of the main jet and that makes it a bit lean with the fan at 100% pushing through the stuck shutter. If the shutter fully opened the main jet would com on line in full and we’d see 9.5% and full 80k burn
0
Categories
- All Categories
- 87K THE MAIN WALL
- 3.2K A-C, Heat Pumps & Refrigeration
- 58 Biomass
- 426 Carbon Monoxide Awareness
- 116 Chimneys & Flues
- 2.1K Domestic Hot Water
- 5.7K Gas Heating
- 109 Geothermal
- 160 Indoor-Air Quality
- 3.6K Oil Heating
- 70 Pipe Deterioration
- 993 Plumbing
- 6.3K Radiant Heating
- 389 Solar
- 15.4K Strictly Steam
- 3.4K Thermostats and Controls
- 54 Water Quality
- 44 Industry Classes
- 48 Job Opportunities
- 18 Recall Announcements