Welcome! Here are the website rules, as well as some tips for using this forum.
Need to contact us? Visit https://heatinghelp.com/contact-us/.
Click here to Find a Contractor in your area.
Was it common for plaster to crack immediately?
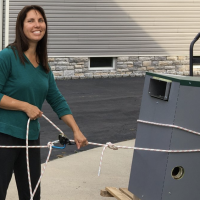
ethicalpaul
Member Posts: 7,794
I’ve seen this on several horsehair plaster/lath walls that I’ve restored in my 1915 house:
after I remove paneling and two layers of wallpaper, I see bare plaster (no paint) and sometimes cracks with ancient filler material on them (see picture). It seems to have happened more on the second floor.
to me this says the walls must have cracked (and had filler applied) during initial construction before the first wallpaper was applied.
was this common? Did the house settle/flex under tension immediately upon construction, causing these cracks and then hardly at all over the next 100 years?
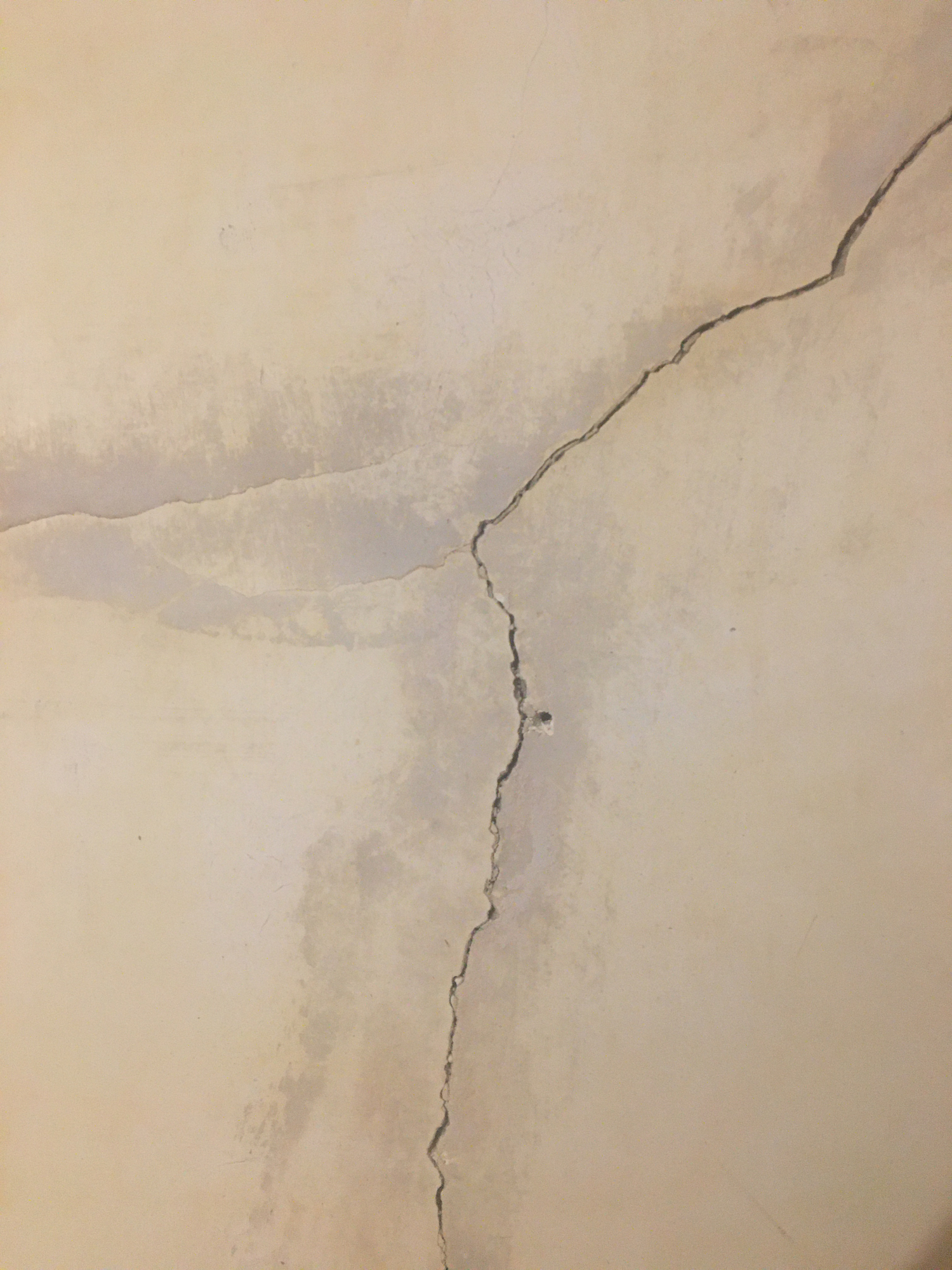
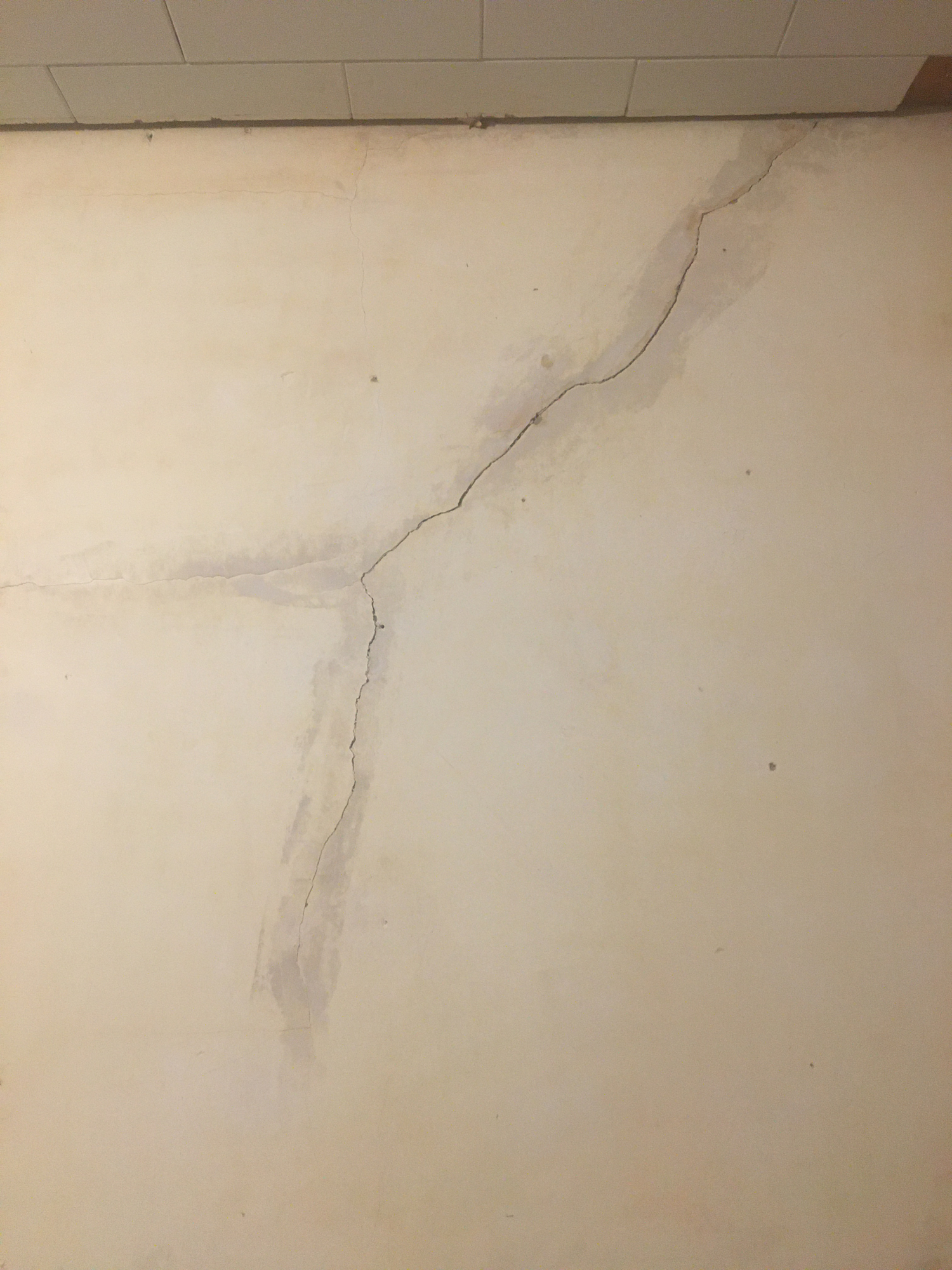
after I remove paneling and two layers of wallpaper, I see bare plaster (no paint) and sometimes cracks with ancient filler material on them (see picture). It seems to have happened more on the second floor.
to me this says the walls must have cracked (and had filler applied) during initial construction before the first wallpaper was applied.
was this common? Did the house settle/flex under tension immediately upon construction, causing these cracks and then hardly at all over the next 100 years?
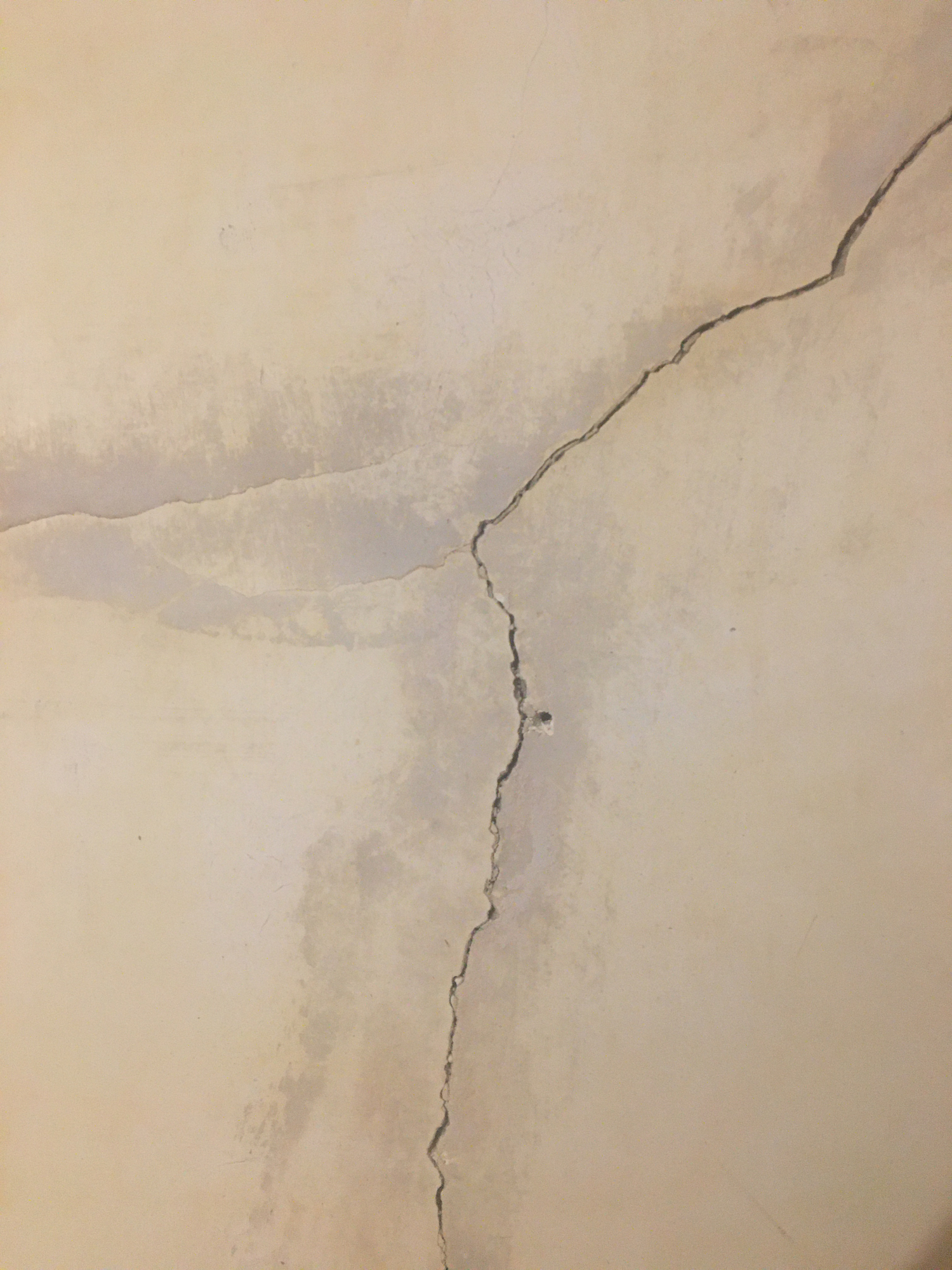
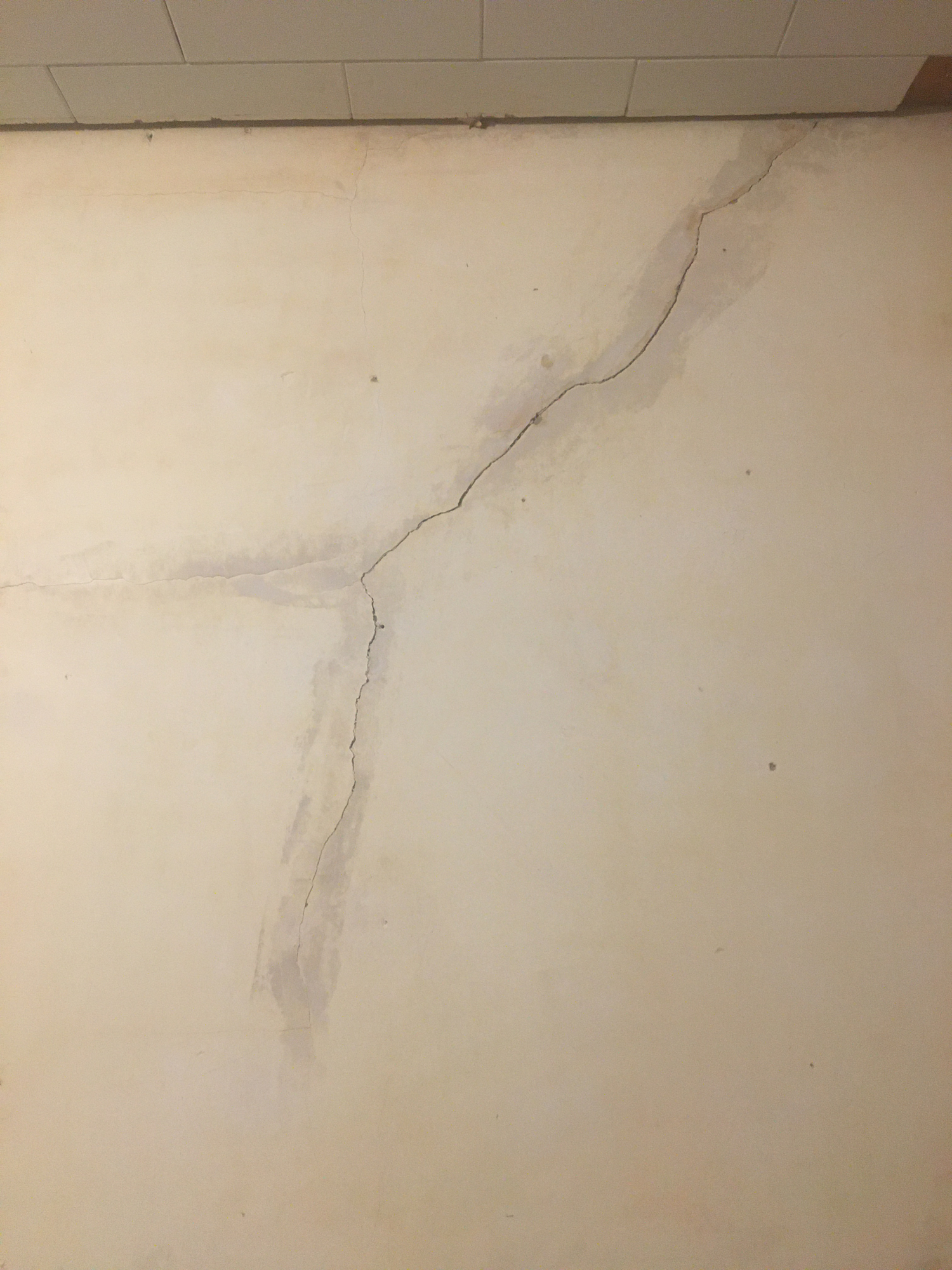
NJ Steam Homeowner.
Free NJ and remote steam advice:
https://heatinghelp.com/find-a-contractor/detail/new-jersey-steam-help/
See my sight glass boiler videos:
https://bit.ly/3sZW1el
0
Comments
-
-
You are lucky, when I tried to remove wall paper, often the plaster would come off with it.
Sometimes the freeze/thaw during the winter would work on the plaster.
Maybe not being painted/sealed helped it crack.
Wall paper could have been put on years later.
Or the 2nd floor was not heated at all, initially.
Did some rewiring in a store building about that age. The entire ceiling, 24' X 60' or so, was wall papered. Cracked only where the roof leaked.
My arms ached just thinking about doing that job 100 years ago.
Just plastering the ceiling.....and then doing the paper....14' ceiling...
1 -
Older house used much wetter wood than what’s used today so there was a lot of movement of the floors and walls over the first few years.
I’ve also found that while the old framing is dimensionally larger than post WWII nominal size, builders tended to over-span the framing leading to more floor bounce and cracking.
I sistered all of the second floor joist when renovating my old house. Much less movement and weird house creaking now.I wasn’t able to sister the first floor framing due to the hydronic lines and certain sections of the house have a good amount of bounce even when dog runs around.2 -
That filler looks to me to be more recent, if that's traces of it I see on the edges of the crack.
That's a fairly typical settling crack, and likely did happen in the first 25 to 30 years. Now if the wallpaper is older than that I'd be wrong of course! But if the crack was found and the wallpaper over it wasn't wrinkled, the crack came first.
A comment on older house framing. It's a little different, as @PC7060 says. Most of the timbers would have been rough sawn (after about 1800), and they would normally be full size -- that is to say, when it says it's a 2 x 4, it's a 2 x 4. Perhaps more to the point -- it was much tighter grain would, and thus a great deal stronger. Not, however, significantly stiffer. In the walls, 24 inch spacing was normal -- which, considering the extra dimension of the wood, is actually stronger than modern dimension lumber on 16 inch spacing.
The problem comes in the floors. It is not, strictly, correct to say that the older builders "over-spanned" the floors. They didn't. A true dimension 2 x 6 has a section modulus of 72. A modern 2 x 8 has very nearly the same section modulus --and it is the section modulus which determines the strength of a beam to carry a load. However, the old boys weren't as worried about deflection (which is what cracks plaster ceilings!). A modern 2 x 8 is about quarter again as stiff as an old true 2 x 6 (a modern 2 x 6, however, is only half as stiff as a true 2 x 6!). Modern standards call for a maximum deflection under live load of 1/360th of the span. Pre World War II standards called for a maximum deflection of 1/240.
All else equal, it is that difference in permitted deflection, combined with the modern dimension system, which dictates much deeper joists for a given span than older construction, and can be very misleading to modern carpenters (I've heard more than one say something to the effect of "how can that possibly stay up?!"). It also means that if you are planning to replace an older joist (or rafter, for that matter) with modern timber, you would be very wise to check the correct size -- it will be deeper by one or two or even more sizes than the old timber you are replacing.
Now there is another factor in very old houses -- say 1810 to 1820 or earlier. The floorboards were thick -- typically an inch, often more -- and wide. But, perhaps more important, the tops of the joists were likely to be uneven even if they were sawn and not adzed, and it was normal for a floorboard to not be in contact with one or more joists when it was unloaded. Now when you step on it, it will deflect down to touch the joist underneath it -- and this can be a bit disconcerting until one gets used to it.
I might add that if you are really planning to work on old houses, it's not a bad idea at all to find a sawyer with a good mill in your area who can cut the wood you want to the dimensions you want. Makes life much simpler.
Oh and one other thing -- don't worry about seasoning. Air-dried wood, either hard or soft, which has been ricked for at least a year is dryer and more dimensionally stable than any of the kiln dried modern lumber one can buy.
None of this applies to post World War II construction, by the way. I've seen some pretty horrible stuff in that time frame up to the present...Br. Jamie, osb
Building superintendent/caretaker, 7200 sq. ft. historic house museum with dependencies in New England3 -
And yet one more thing on the framing -- if you happen to be working on a post and beam structure, that's a completely different matter. They aren't hard to work on --but they do require one to think a bit differently!Br. Jamie, osb
Building superintendent/caretaker, 7200 sq. ft. historic house museum with dependencies in New England1 -
Jamie Hall said:That filler looks to me to be more recent, if that's traces of it I see on the edges of the crack. That's a fairly typical settling crack, and likely did happen in the first 25 to 30 years. Now if the wallpaper is older than that I'd be wrong of course! But if the crack was found and the wallpaper over it wasn't wrinkled, the crack came first. A comment on older house framing. It's a little different, as @PC7060 says. Most of the timbers would have been rough sawn (after about 1800), and they would normally be full size -- that is to say, when it says it's a 2 x 4, it's a 2 x 4. Perhaps more to the point -- it was much tighter grain would, and thus a great deal stronger. Not, however, significantly stiffer. In the walls, 24 inch spacing was normal -- which, considering the extra dimension of the wood, is actually stronger than modern dimension lumber on 16 inch spacing. The problem comes in the floors. It is not, strictly, correct to say that the older builders "over-spanned" the floors. They didn't. A true dimension 2 x 6 has a section modulus of 72. A modern 2 x 8 has very nearly the same section modulus --and it is the section modulus which determines the strength of a beam to carry a load. However, the old boys weren't as worried about deflection (which is what cracks plaster ceilings!). A modern 2 x 8 is about quarter again as stiff as an old true 2 x 6 (a modern 2 x 6, however, is only half as stiff as a true 2 x 6!). Modern standards call for a maximum deflection under live load of 1/360th of the span. Pre World War II standards called for a maximum deflection of 1/240. All else equal, it is that difference in permitted deflection, combined with the modern dimension system, which dictates much deeper joists for a given span than older construction, and can be very misleading to modern carpenters (I've heard more than one say something to the effect of "how can that possibly stay up?!"). It also means that if you are planning to replace an older joist (or rafter, for that matter) with modern timber, you would be very wise to check the correct size -- it will be deeper by one or two or even more sizes than the old timber you are replacing. Now there is another factor in very old houses -- say 1810 to 1820 or earlier. The floorboards were thick -- typically an inch, often more -- and wide. But, perhaps more important, the tops of the joists were likely to be uneven even if they were sawn and not adzed, and it was normal for a floorboard to not be in contact with one or more joists when it was unloaded. Now when you step on it, it will deflect down to touch the joist underneath it -- and this can be a bit disconcerting until one gets used to it. I might add that if you are really planning to work on old houses, it's not a bad idea at all to find a sawyer with a good mill in your area who can cut the wood you want to the dimensions you want. Makes life much simpler. Oh and one other thing -- don't worry about seasoning. Air-dried wood, either hard or soft, which has been ricked for at least a year is dryer and more dimensionally stable than any of the kiln dried modern lumber one can buy. None of this applies to post World War II construction, by the way. I've seen some pretty horrible stuff in that time frame up to the present...
Then there is the detailed wood work most older homes show, but many modern builders don't even consider... Its sad how few people notice these things and then butcher them during 'renovations'.1 -
The Sears kit homes were pretty amazing. Now and then you see one which hasn't been modernized out of existence -- but not often. They are very well built.
One thing on using modern dimension lumber, if you must -- let it season as long as you can in the environment you are going to use it in.Br. Jamie, osb
Building superintendent/caretaker, 7200 sq. ft. historic house museum with dependencies in New England1 -
We stood up our outside walls with full span trusses in 1991.
5/8" SR on entire ceiling and outside walls.
(this madness was to avoid air infiltration of wall/ceiling joints...also easier to rock the big box with few cuts/waste...after the carpenters did this they apricated the "madness" and would do it more often except for electricians not cooperating ).
Then built interior walls later.
They stood for maybe 2 years before SR was applied to interior walls.
This was a pay as you go venture, electrical & PLBG & HVAC done in "spare" time.
Before rocking you could see light between jacks, cripples and king studs and also on corners where the wood had shrunk. (even though all these pieces were shot together with nail guns and appeared to be tight 2 years previous).
This was standard lumber of the day and considered dried. It all stayed straight.
Had we rocked right away the shrinkage would have taken place under the rock and perhaps caused nail pops or cracks.
We do have some truss upheaval in the winter time sometimes showing a line on the intersection of walls and ceiling. Come springtime the gaps close.
Some people have had interior walls lifted off the floor from truss upheaval.
IIUC, the more a truss is loaded with snow the bottom cord will bow up.
Temp diff makes a difference in deflection also.1 -
oh, maybe I had an incorrect notion then. I didn’t think of the idea that the plaster itself might have been the original wall appearance. Is that what I am understanding?That would make a lot more sense if that plaster were exposed for some years, then cracked, then cracks filled for that first wallpaper.
By the way, the magic tool for wallpaper removal is the steamer that is available anywhere. Possibly the best $50 I have ever spent.NJ Steam Homeowner.
Free NJ and remote steam advice: https://heatinghelp.com/find-a-contractor/detail/new-jersey-steam-help/
See my sight glass boiler videos: https://bit.ly/3sZW1el0 -
-
Very common in the 1800s for the plaster to be the finish @ethicalpaul , both on walls and ceilings, without even paint, never mind wallpaper. Even in some really high class places. And some of those finish plaster jobs were really beautiful work. If you think that finding people to do steam piping correctly is tough, try finding someone to do that class of plaster work. No, I've never seen wallpaper on a flat ceiling, but on sloping ceilings under the eaves, for instance, it's kind of normal.Br. Jamie, osb
Building superintendent/caretaker, 7200 sq. ft. historic house museum with dependencies in New England1 -
When I was 15 years old (65 years ago) I worked for two Russian brothers, cement and plaster contractors that did ornamental plaster work for churches and synagogues two summers . When I began as a helper my job was to load the plaster and quick lime to the storage area and slack the lime. Bring the lime to them and assist the mixing of plaster and lime. They proportioned the plaster and lime and I mixed.
The amount of mix was in proportion the the rate of their ability to put the plaster on the wall. I once mixed to much and they made me throw it away. I said that I can add some water to the plaster and remix it so they don't have to throw it out. They explained to me that re constituting the plaster is not good because it has already began to set an would crack or fall off the wall in several years.
When they did compete wall replacements over wood lathe after I removed all the plaster and undercoat from the wall it was my job the wet the lathe before they put the neat and brown coat on.
My instructions were wet the lathe and hang burlap on the wall then put the bottom of the burlap into deep pans filled with water. The burlap pulled water out of the pans by osmosis and allowed the wood lathe absorb the water. This was allowed to go on for one day. After they were satisfied with condition of the wood lathe they began the process of re-plastering. Each step that was done burlap was hung from the wall for one day, this was done let the neat and brown coat to cure slowly.
To me the cracks on the wall may have occurred from a poor mix or over working of the under coating or applying the finish coat when the neat or brown coat was left to dry to long. When the plaster was put on the under coating it may have pulled the water out of the plaster and that could have caused the plaster to crack.
Anyway the wall looks like it started with some water damage.
PS if you are going to use wire lathe to replace some of the missing wood lathe make sure the wire lathe has plenty of nails in it when securing to the studs and putting your under coating on the wire lathe first, let it dry for a day before putting on the neat than the brown coat, let each coat dry for a day and make sure that the wall is even. When putting on the finish plaster coat try to keep the plaster coat at about 3/8 of inch thick, do not over work the plaster.
JakeSteam: The Perfect Fluid for Heating and Some of the Problems
by Jacob (Jake) Myron5 -
We wanted tradition 3 coat stucco on our new house.
We finally found a contractor who would do this, he and his boys were only 70 miles away. The father moved here from Mexico years ago. The live in the middle of cowboy country in central Nebr. The boys could switch from Spanish to perfect Midwest cowboy English in mid sentence. This was very impressive actually as many locals have trouble with basic correct English and condemn some one with ESL.
Anyway, the father said that there is some ingredient left out of Portland that gave the old time stucco great strength. He had me find what he called "glue" to mix into the stucco. It was some liquid bonding agent, we used gallons of it to add to the mix.
He was quick to dump out any mix that did not feel "right"....it is buried under my driveway.
After more than 25 years things still look pretty good.
Some years later I was visiting with a plasterer on a job.
It was remodeling a 1930's building with perfect plaster.
He had to patch holes the HVAC blasted ductwork thru and close up some small windows.
I told him this story and he said absolutely that is true.
He had worked on a historic church helping some guys who were doing restoration.
(He may have been the token Union mason put on the job)
They were from Europe and brought their own materials with them stating that American Portland and lime whatever, were inferior to theirs.
They refused to use it.0 -
If you ever do have to do some plastering, there is a chap in Brattleboro, VT who sells stuff on line -- and has good videos. https://plastermagic.com/ The web site is slow to load, but the product is good. Since the magician I had to do plaster restoration has moved back to Puerto Rico (he was an absolute magician with the stuff... sob...) I've managed to teach myself at least the basics... it's harder than it looks! And you don't want to see the early results... but I'm getting there.Br. Jamie, osb
Building superintendent/caretaker, 7200 sq. ft. historic house museum with dependencies in New England1 -
Nearly lost arts.0
-
Thanks all. I think I’ve seen the magician’s videos. Nothing like for me, I’m strictly patch and pray over here 😅
I like the look of the raw plaster but my wife would never go for it. It will be painted.
now that Jamie told me they used to use plaster as the finished surface I’m sure the wallpaper came years later. Thanks again!NJ Steam Homeowner.
Free NJ and remote steam advice: https://heatinghelp.com/find-a-contractor/detail/new-jersey-steam-help/
See my sight glass boiler videos: https://bit.ly/3sZW1el0 -
I recall a joke "The only plaster that doesn't crack is in a bag".
I've liked watching Youtube videos from Kirk Giordano plastering Inc. for years now.
He's really good at what he does and he makes it look really easy.https://youtu.be/GVj1uYAfMuQ
https://youtu.be/dzfhZmsGvRY
Single pipe 392sqft system with an EG-40 rated for 325sqft and it's silent and balanced at all times.
1
Categories
- All Categories
- 87K THE MAIN WALL
- 3.2K A-C, Heat Pumps & Refrigeration
- 58 Biomass
- 427 Carbon Monoxide Awareness
- 113 Chimneys & Flues
- 2.1K Domestic Hot Water
- 5.7K Gas Heating
- 109 Geothermal
- 161 Indoor-Air Quality
- 3.6K Oil Heating
- 70 Pipe Deterioration
- 995 Plumbing
- 6.3K Radiant Heating
- 391 Solar
- 15.4K Strictly Steam
- 3.4K Thermostats and Controls
- 55 Water Quality
- 44 Industry Classes
- 48 Job Opportunities
- 18 Recall Announcements