Where and How to Tie in Time Delay Relay
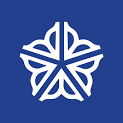
This first post is just the problem, I'll have a lengthy background in a reply.
I have a Smith HB250 Boiler with the following control devices:
- CG400-1090 Cycle Guard Low Water Cutoff
- RIBTU1S Relay
- Mechanical Low Water Cutoff (McDonnell & Miller 67? - No label on it) - definitely the same form factor - came with boiler perhaps?
- Spill Switch
- Rollout Switch
- Dwyer Photohelic (primary pressure control)
- Vaporstat (backup control)
- Thermostat (Netatmo) - for control purposes a simple two-wire thermostat powered by AAA batteries (no C-wire) - it also operates as a wifi-relay to activate the boiler on call from radiators.
- If I'm missing any other safety features, it is probably there in the series, I'll confirm if relevant.
All of these controls are working properly (at least I assume the spill and rollout switches are working 😲) Most of the time (outside of the coldest days), my boiler operates on pressure as individual radiators call for heat - which leads to me just pressurizing the mains while the radiator is already full of steam, I'd like to install a time delay relay.
I tried purchasing two time-delay relays and placing them in series between the Photohelic and Spill switch - apologies as I am not going to use the right words to explain the circuit:
- 1st: ICM203 - this didn't work. I assumed that this was because the circuit needed to always be energized.
- 2nd: Littlefuse SPDT 0.1 to 10 min Delay on Break Time Delay (24v) - this didn't work in the circuit either. But I did confirm the relay does indeed work from the boiler transformer. Notably, the boiler doesn't fire at all when it is connected. I wired the Littlefuse like this:
Here's the wiring diagram of my boiler: any ideas on where I can put the time delay?
Comments
-
For background, the first post was long enough!
I have a 2,000sf 1920 two-pipe boiler system with an EDR of 745 and a Smith HB250-S-6 Boiler. At a nominal input of 205,000 BTUs, it is only slightly larger than my demand, but unlike many new boilers, it is sized (mostly) appropriately.
What I've done over the last 6 years or so is add smart valves and TRV to my system that open and close on the temperature in the room. This has had various pressure problems. You can click on my post history to see them, but I've gotten them worked out. Now that my Photohelic is installed and I'm not relying on the uncalibrated products from Honeywell, the system is working very well. I am satisfied with the operation (I eventually turned down the Photohelic to 14 inches). This weekend, in single-digit temps, the boiler kept my house at temperature without 100% run time and without activating the pressure switch a lot (it wants to sit at 9-11 inches when fully open).
You can also zoom in and see how poorly my new Vaporstat is calibrated. In this picture, the Vaporstat was cut before the Photohelic.
So, each of my radiators can call for heat. This leads to maximum comfort as every room stays warm but burns more gas as the rooms cool at different rates, and it seems like once one radiator is done heating up, another is calling. This system (European Netatmo for those who care) is working as designed, and I can't operate it off this (comfort) mode as the room with my thermostat loses heat significantly less than other rooms, and my house would be too cold if that room controlled the temperature of my whole house.
Ideally, I'd change my settings so three radiators would have to call instead of having just one call for heat to turn on the boiler. Unfortunately, the built-in software doesn't allow for that, and I don't want to delve too deep into computer programming only to have something break and need troubleshooting when I'm away, and my wife is freezing at home.
So, as an alternative, I'd like to add a time delay relay to reduce my fuel consumption - right now, I am pressurizing my pipes while the radiator is already full of steam. With a time delay, This should result in more radiators needing heat when the boiler fires. Hence the above post.
0 -
what is the EDR on this 200,000 boiler.
0 -
Ha, I had it originally and deleted it - 745 EDR - that said, sizing doesn't appear to be the problem.
0 -
-
I'm not sure I follow what you mean by primary control as there are two:
- Pressure: I don't want to raise the Phothelic set point - I get water hammer when I get up to 2psi or so and of course more pressure doesn't do anything.
- Thermostat: I am stuck with the thermostat controls I have for the operation I desire - I can't set it to start based on delta T unfortunately..
0 -
Where is the Dwyer Photohelic (primary pressure control) on the boiler wiring diagram? Is this a simple open/close set of contacts that turn the burner on and off based on steam pressure?
Your boiler's original LWCO appears to be of the probe type. The mechanical one was added after the fact, maybe to comply with a local code.
The ICM 203 should work just fine if connected this way.
In this configuration, the gas valve will operate as soon as there is 24VAC applied to the valve. When power to the valve is terminated, there will be a delay in the restarting of the gas valve according the the selected time on the dial. for example if you select 10 minutes, then the delay after the power is terminates will start and if you power the gas valve within the 10 minute delay, the gas valve will not open until the internal clock of the ICM 205 reaches 10 minutes.
Example 1: Call for heat (24 V. power) to the gas valve terminates at 12:00. The call for heat is reestablished at 12:03. The gas valve will not power up until 12:10. this is because the internal timer has not yet expired.
Example 2: Call for heat (24 V. power) to the gas valve terminates at 12:00. The call for heat is reestablished at 12:13. The gas valve will power up until 12:13. This is because the internal clock has expires at 12:10 and the power to the gas valve will open the valve at the time power is reestablished.
Is this the delay you are looking for?
Edward Young Retired
After you make that expensive repair and you still have the same problem, What will you check next?
1 -
@EdTheHeaterMan Thanks! I'll try this later.
The Dwyer is indeed wired simple, in series between the Vaporstat and Spill switch - it is operating appropriately.
As to the mechanical cut-off, it apparently did come with the boiler - the manual shows it in a bunch of pictures but makes no reference to the model. I think all it really does is serve as a cutoff when I drain the boiler.
https://archive.org/details/manualzilla-id-6979130
0 -
@EdTheHeaterMan to the edits you made. I believe your example is what I am looking for.
Ideally, once the pressure switch is hit, the boiler doesn't restart for 10 minutes.
Now what I'm worried about is what happens when I get close to the design temperature like this past weekend - this will also trigger when the Cycleguard does its test. I just hope that the boiler can heat through these longer arbitrary cutoffs. I think I will just have to test it out.
0 -
FYI: I made some edits to my earlier post.
So the euro-thermostat can get a signal from the radiators in the rooms and signal the thermostat to call for heat. Interesting.
Your concept to time delay the gas valve in order for more of the radiators to call for heat before relighting is an interesting idea. I can see how that will work and there may be some savings in that design. Similar to purging heat from a system after the call for heat is over, so you don't leave unused heat in a water boiler. By waiting 10 minutes before restarting the gas valve, you are removing one of the causes of short cycling, (oversized boiler in relationship to the few radiators that are calling for heat) and also giving that longer run cycle for the boiler to reach the cutoff pressure.
Let us know how this works our for you. I can see an @ethicalpaul video of this in the future. As long as the Netatmo system isn't too expensive.
Edward Young Retired
After you make that expensive repair and you still have the same problem, What will you check next?
2 -
The Netatmo system is mostly great - the biggest thing it is missing is little sensors you can place elsewhere in the room. There's a larger problem with the frequency it operates on - it's why all kinds of heating devices are sold in Europe but not the US.
7 years ago when I stated, there weren't US legal alternatives. They are just starting to come on the market but you have to be an automation expert to use them.
0 -
It is only 10 minutes, and that is not a lot of time for a steam boiler. Worst case scenerio is 20 minutes if the call for heat reestablishes and then the gas valve fires up for a few seconds, then the CycleGard opens the circuit and you need to wait another 10 minutes. The recovery will just take a few more minutes. I think it will be an acceptable amount of off cycle.
If not, you can always reduce the time to 8 minutes.
Edward Young Retired
After you make that expensive repair and you still have the same problem, What will you check next?
0 -
If you are referring to the CycleGard delay after a Low Water interruption, that is not an issue, That CycleGard time delay and the additional time delay will take place at the same time. They are both "delay after" controls
Edward Young Retired
After you make that expensive repair and you still have the same problem, What will you check next?
0 -
@EdTheHeaterMan thanks for the thoughts, and I’m glad you corroborate what I’m thinking.
One final question, it seems like you like the idea of 10 minutes between starts, is that the right length or would it be something shorter? I was thinking 3 to 5 minutes, but I only have experience with one Boiler in years in the trade.0 -
@KarlW Is this in your own building? Or is this for a customer?
In my own home I would start at 10 minutes. If there is a problem I could go an reduce the timer.
In a customers building, I would start at 4 minutes for the first week, then go back and change it to 5 minutes, then the following week go the 6 minutes…. When you get to the maximum 10 minutes of the timer, and no tenant complains, then you are good to go.
Bottom line is the longer the off cycle the longe the on cycle will be. If the system is properly sized and all the radiators are open in the coldest days, you may never get to the high pressure cut off.
The greatest savings will happen during the milder days when you can have longer off cycles.
Edward Young Retired
After you make that expensive repair and you still have the same problem, What will you check next?
0 -
You could probably size the boiler close to the heat loss with that much zoning. the radiators are only consuming steam if the boiler is producing it. The radiators may still be hot when the boiler isn't firing but they aren't getting additional heat for more than a very short period after the boiler stops firing. It produces pressure because the radiators are consuming les steam than the boiler is producing, not that they "are full of steam".
That being said, i think that littlefuse time delay powers a timer circuit inside when it is energized by flowing some current through the load then closing its contacts when the timer expires. If the load is high impedance it won't work, it needs to control a relay coil or gas valve or something. If it is in the wrong place it could cause an ignition control to lock out because it is expecting flame to be proven in a certain timeframe.0 -
I’m not getting a new boiler, and as I approached my design temp over the weekend, my boiler had very long run times with the cycle guard being the main break. 745 EDR is 174,000 BTU - that assumes I accounted for all of my radiators. 205,000 BTU isn’t massively oversized.
Correct me if I’m wrong, this is a two pipe system. When my boiler fills with steam the trap closes and traps the steam in the radiator. With the steam trapped (either by the closed TRVs or the steam trap on open TRVs) the system pressurizes and shuts off at the pressure setting (14in H2O).
Here’s the key piece: for some time (I’m not sure how much, and it there are a lot of variables) the radiator is filled with steam before it condenses and the lower temp opens the steam trap(s) any and all steam applied during this time is largely (but admittedly not completely) useless. But heat continues to radiate in the room until the radiator cools down.
Burning fuel during those times is uneconomical, and in a system where I burn fuel everytime a radiator needs heat I need to minimize this so I don’t go broke.
This is the first season I’ve been operating this way and I’m afraid of what my December gas bill will look like.
To your time delay comment, I believe that’s exactly what happened and Ed has proposed and alternate spot to place it in the system so I am going to try that.
0 -
The steam condenses in the radiator and shrinks in volume something like 1700 times and pulls more steam in. if the radiators are condensing as much steam as the boiler is producing it builds no pressure, the pressure only builds if the boiler produces more steam than the system can condense.
0 -
oh, other people commented while i wandered away and finished reading the initial post…
0 -
are you comparing the output of the total radiation to the heat loss of the structure? i bet it is still way more than the heat loss even if the connected edr is close to the output of the boiler. with your zone valves if the boiler can't quite fill the whole system some zones will be satisfied and close then the zones that were starved of steam can heat. as long as the connected edr is greater than the heat loss a smaller boiler would work. i'm not saying you should change it, just pointing out that a significantly smaller boiler could probably work with the control system.
0 -
@EdTheHeaterMan the wiring worked! Thank you - I’ve set it for somewhere in the 5-6 minute mark and left instructions to wake me up if it gets to cold tonight.
In accordance with Murphy’s Law the coldest room in my house (due to heat loss) is my bedroom - an enclosed sleeping porch for those familiar with Midwestern-style century homes (Rochester, NY is in most ways the eastern-most Midwest city, absolutely so architecturally). We’ll see how it goes with longer cycles.
@mattmia2 I’m just trying to make sure my boiler isn’t burning gas nonstop. As to the sizing, I disagree - my boiler is sized pretty close. As the temperatures got down to single digits over the weekend you can see my boiler uptime hover at over 80% (Rochester NY’s design temp is 5-degrees and we actually had a low of 2 on Sunday) - it only dropped during my nightly setback. I could go smaller, but not much.
0 -
Hello KarlW,
Why didn't the ICM203 work, the one I have works fine with an open circuit. In your case I would have inserted it in series with the Dwyer Capsu-Photohelic relay contacts, although other places may work too. Looks like your Dwyer Capsu-Photohelic is set to open the circuit at 18 inches WC, then the delay of the ICM203 would start and not re-close the circuit until the delay expires (0.03 to 10 Minutes later). By then the pressure would have diminished and possibly the thermostat satisfied.
I have a ICM203F, just to play with, and I have played with it. My EDR is larger than my boiler so I have no actual need for it in my system. Its an interesting timer (since the delay continues totally un-powered, I will re-verify this). Also I wanted to reverse engineer it, so far it looks like a TRIAC is the AC switch.
With Ed's placement of the ICM203 at the gas valve, if the thermostat or your "smart valves and TRV" system is calling for heat during the 'Off Delay' of the ICM203 the damper won't close. Benefit, less wear and tear on the Damper, disadvantage $$$ going up the chimney.
National - U.S. Gas Boiler 45+ Years Old
Steam 300 SQ. FT. - EDR 347
One Pipe System0 -
I originally installed the ICM 203 in series between the pressure switch and damper. I’m not sure why it didn’t work in series when I tried it either. The boiler didn’t turn on at all with it in. Putting it where Ed suggested did work.
The pressure take 1-2 mins to diminish, but even then the radiators are still warm, hence adding in the time delay.
0 -
Assuming the 2nd timer is a HRDB223 that should work to, however the way it is integrated into the existing circuit would be much more critical. Was the transformer that powered the HRDB223 the same as the transformer for the boiler's control circuit ?
EDIT: Looked into it deeper, my second opinion is it will not work for this application, see text below.
I would say this relay (the HRDB223) would not work for this application. The problem is the relay does not change state at the trigger event.
National - U.S. Gas Boiler 45+ Years Old
Steam 300 SQ. FT. - EDR 347
One Pipe System0 -
I ran the HRDB from the same transformer and I put in a jumper from the 2(+) to the C - I bridged it from the same point (between the Photohelic and Damper) and the boiler wouldn’t run with it in either.
0 -
If you have not, please re-read my last two posts I kept editing them after the initial post, I never refreshed the page so I did not know you had probably read them already.
I would have wired the HRDB223 this way to make the normal trigger operation correct (terminal 6). However there is two issues with using that device, no initial closure of the 'initiate switch' function and the relay is in the wrong state during the time delay interval as stated in a previous post.
Once triggered the timing of the ICM 203 is fine with no power connected to the unit.
I suspect the ICM 203 did not work in your original setup due to the load current of the Damper trigger circuit is below the 0.040 Amp (40 mA) minimum load specification (Holding Current). The gas valve current should be easily above that, so it worked there. For me I would want the Damper working correctly (issue explained above). If it is determined that the Damper trigger circuit current is too low an appropriate resistor could be added as a slight additional load.
National - U.S. Gas Boiler 45+ Years Old
Steam 300 SQ. FT. - EDR 347
One Pipe System0 -
When you say $$$ going up the chimney, is this just heat escaping? If it's just that, I can afford it somewhat as I have a dedicated overheated boiler room.
Otherwise, it worked last night (not as cold, hovering around 30 degrees) and kept my bedroom at temperature. Thanks @EdTheHeaterMan for your help!
One other problem is solved as I thought it would but I forgot to mention it in this post; Water Hammer:
Unlike most water hammer, this was easily locatable and would be only on the active radiators. With the boiler short cycling (as little as 60 seconds on, 60 seconds off) to only feed one or two radiators, after a few cycles I would get water hammer clearly banging on the inlet stem pipe to whatever radiator is on at that time. Nearly of my radiators inlets go to a top opening so there is a 2-3 foot stem coming out of the floor.
My theory is that with the steam trap closed in the radiator (or less likely the TRV closed), steam could no longer enter the radiator and was condensing in the stem - when the burner stopped due to pressure and no more steam was coming, this steam in the stem began to condense just in time as the burner restarted and steam came back up and the resulting crash creates water hammer.
There was no water hammer last night.
0 -
" When you say $$$ going up the chimney, is this just heat escaping? If it's just that, I can afford it somewhat as I have a dedicated overheated boiler room. "
Yes, heat you are paying for. For the cost of a 620 Ohm, 2 Watt resistor I think I would want my Damper to work as intended.
If your boiler duty cycle is reduced the boiler room should not be as hot. I would run the timer with the longest delay your comfort will tolerate. Same with the Dwyer pressure settings as low a pressure your comfort will tolerate.
National - U.S. Gas Boiler 45+ Years Old
Steam 300 SQ. FT. - EDR 347
One Pipe System1 -
So, a fun update over the weekend. I had the time delay set to 6 minutes or so and it worked for a couple of weeks. We had "normal" temperatures, lows in the teens, highs in the high 20s- low 30s. This is after the first week of design temperatures (single digits) and the second week of warm temperatures (40s-50s).
Two rooms in my house, my converted sleeping porch bedroom and my mother-in-law's attic apartment, which are among the rooms I want to be heated most, could not maintain temperature.
I'm quite sure it is because these areas have significantly higher heat loss than other rooms:
- As I mentioned above, each radiator can call for heat for heat independently when it is not satisfied.
- Each time one or two radiators call for heat, I only get a minute or two of steam before the pressure is satisfied (0.5 psi) and it shuts off.
- As more radiators call for heat (I have 11 radiators of my 16 radiators with smart TRVs) my system takes longer to reach pressure. When all radiators are fully open, my system stabilizes at about 0.25psi and doesn't shut off for pressure.
- At normal temperatures, the heat loss of most of my house is not even enough to get many of my valves to open simultaneously. The one minute of steam, 6 minutes off cannot heat my coldest rooms to temperature.
Long story short - looks like I should add some insulation to these rooms.
In the short term, I turned down the time delay to 3 minutes and it appears that this is better. In the medium term (by next season), I plan on implementing a weighted control system using smart valves and my new Hubitat smart home controller that turns on the boiler when "important" rooms need heat.
0 -
Might try more venting and more insulation on the piping to those radiators, add a main vent on the supply pipe, so it can move steam to the radiator more quickly. If i'm thinking about it right, it really shouldn't shut off on pressure until there is steam to the radiator if the riser is vented adequately.
0 -
A rather nice description of what happens with TRVs which can independently call for steam…
Yes, insulation would help. May I ask, though, have you managed to get the system as a whole so it is well balanced and adequately vented with all the TRVs open? Do those two cold rooms get adequate heat in that setting?
Not to put too fine a point on it, if the system isn't inherently properly balanced, TRVs are going to make a whole host of problems worse…
Br. Jamie, osb
Building superintendent/caretaker, 7200 sq. ft. historic house museum with dependencies in New England1 -
@mattmia2 the system is well insulated - properly encapsulated asbestos insulation, only wet return that I had to replace in full isn’t insulated.
Adding @Jamie Hall: my system is adequately vented and I am very pleased with it. When it got down to 2 degrees outside all of my radiators called for heat and stabilized at 7-9” of H2O (my 0.25psi above) - all radiators were heating with no cold ones*. At 2 degrees, I’m at about 45 minutes per hour on.
I’m sized about right, a 205,000 BTU boiler with an EDR that calls for around 182,000. I’m quite sure that I just wasn’t getting enough heat in a 1.5 minute on, 7 minute off cycle.*Except for a bathroom radiator that I need to diagnose - it doesn’t get hot under any circumstance, I suspect the TRV has a mechanical issue separate from my controls.
0 -
I was thinking more venting on the risers, the insulation was just to make it have to work less to get the steam there. Is the radiator fully hot when the pressuretrol cuts out? I suppose if those are the only 2 radiators calling for much of an hour 6 minutes off could be much longer than that on time or at least the steaming period of the on time. There is going to be some time that it fires to get back to boiling before it produces any new steam. If you extend the off time that may significantly increase the time before it starts making steam.
0 -
@mattmia2 the attic radiator does have a vent on the riser. It went from requiring about 30 minutes of boiler on time to heating (near) immediately, that was a change I made last year after my MiL pointed it out.
Both radiators get hot and at cold temps when all are calling and warm temps when not as much heat is needed they keep up. It is just that middle band where my high heat-loss rooms need more heat than the time delay allowed.
0
Categories
- All Categories
- 87.1K THE MAIN WALL
- 3.2K A-C, Heat Pumps & Refrigeration
- 58 Biomass
- 427 Carbon Monoxide Awareness
- 114 Chimneys & Flues
- 2.1K Domestic Hot Water
- 5.7K Gas Heating
- 110 Geothermal
- 161 Indoor-Air Quality
- 3.6K Oil Heating
- 70 Pipe Deterioration
- 999 Plumbing
- 6.3K Radiant Heating
- 391 Solar
- 15.4K Strictly Steam
- 3.4K Thermostats and Controls
- 55 Water Quality
- 45 Industry Classes
- 48 Job Opportunities
- 18 Recall Announcements