Welcome! Here are the website rules, as well as some tips for using this forum.
Need to contact us? Visit https://heatinghelp.com/contact-us/.
Click here to Find a Contractor in your area.
rusted coil plate bolts removal
Options

mikedo
Member Posts: 274
peerless wbv -04 -150 wpco the coil plate bolts are very rusted im assuming they are similar to burnham weil mclain and deadhead in the casting besides drilling them out does anyone know a better way of removing them
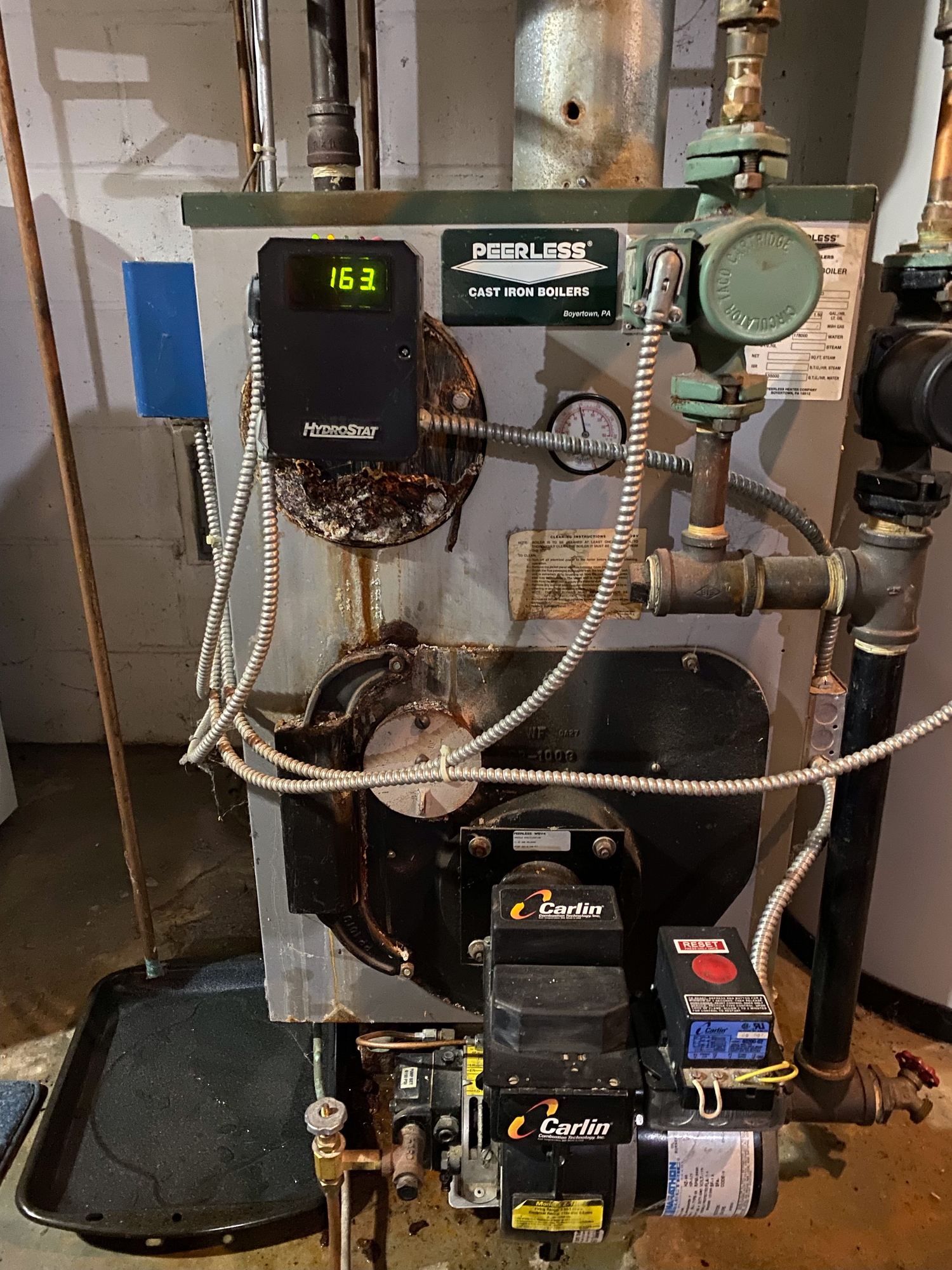
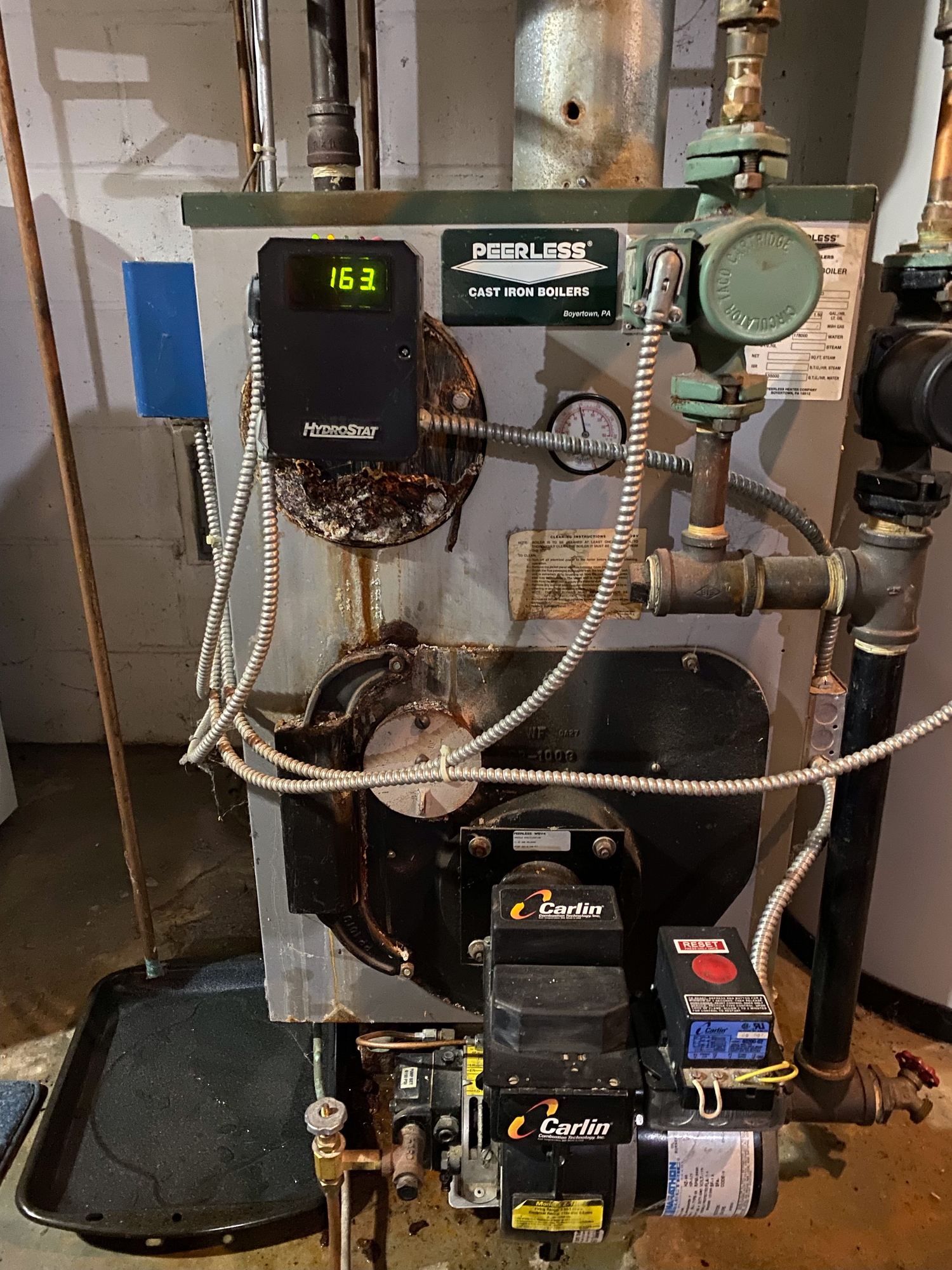
0
Comments
-
-
-
thanks for help never heard of drill bits that run in reverse. im plannig on get my **** kicked there it if wasnt a good friend of mine i would not touch it. maybe someday the manufacturers will come up with a better design its only been a problem for 70 years.0
-
@mikedo "left hand drill bits" they are wormed the opposite direction of typical drill bits so that if you drill into screws with standard threads, the bit should impart enough force on the fastener to unscrew it. You drill a pilot hole with the left hand bits and if you're lucky it'll unscrew the fastener by itself, if that doesn't work, you step up to screw extractors using the pilot hole you've created with the previous bit.
Coated stainless steel bolts would prevent the corrosion problem. Boiler makers for whatever reason cheap on on stupid things trying to undercut the competition. It's why we see iron instead of brass pigtails, those stupid plugs rather than drain valves beneath sight glasses, brass plated rather than solid brass friction washers inside sight glasses, no low PSI gauges in addition to the 0-30PSI ones required by code, pressuretrols instead of including vaprostats, etc.2 -
HB Smith was the only boiler MFG I know of that had a flange on the boiler casting and they used nuts and bolts on their coils in the old days. probably was too expensive to make and made too much sense so they stopped making them that way. The old 1100, 2000 and 2500 model boilers had them....maybe some others
Get some "Kroil Oil" which in MHO is the best penetrating oil, Lots of drills and taps. I have on occasion drilled them out larger and tapped them for 7/16" bolts. Use never seize on the bolts regardless of the bolts used3 -
I've had good results using penetrating oil, a heavy flat chisle, and a lump hammer. Use a wire brush, even a 3/4 copper fitting cleaning brush and scrape all the crud away first. Tap all around the flats of the bolts without damaging them. I believe they're 9/16 hex heads. A good socket or box wrench. Use short bursts of pressure so you hopefully won't snap the heads off.1
-
I've had success grinding the heads off of the bolts; after draining the boiler of course.
Remove the coil / plate and the remaining studs will protrude 3/8 or 1/2" from the block. Heat them red hot and let them cool, repeat.
I use a 6 or 8 " pipe wrench on the studs; I've never had to drill or tap.
Coil plate bolts need to be tightened after un-crating the boiler when new.1 -
This is a Burnham boiler before & after...0
-
Use a 6 point socket and breaker bar. An impact wrench is more likely to break a seized bolt than a breaker bar.
If they were installed from the factory with antiseize or they used brass or stainless bolts they wouldn't seize in the first place. If a bolt is stuck, heat it with a torch before you break it. use stainless and antisieze for the replacements.1 -
Is there a correct torque value when re-installing these bolts?0
-
Generally 20-25 ft lbs.Rickoo said:Is there a correct torque value when re-installing these bolts?
Anti-seize recommended
Criss-cross tightening at lower values first.. then to 20.
Tighten more only if you observe leaking..
Retorque after firing for a while, then double check a week down the road or whenever you remember.1 -
If you use a good penetrating oil numerous times a day and repeat for 2-4 days, this would yield the best results. Applying the penetrating only once or twice is not the answer. Then try sockets, wrenches, or a small impact wrench. Remember, too much muscle will break off the bolts or studs. If you have the time try the penetrating oil over many days.2
-
This method is just fine. On some older boilers I installed, there were instructions (that no one ever reads) instructing the installer or the homeowner to check the coil plate bolts in 6 months. You won't believe that the gasket shrinks enough over the first 6 months to the point where the bolts are only hand tight in some cases. A 1/2 turn with a wrench in 6 months, then another 1/4 turn in another 6 months will keep that gasket from ever leaking.mikedo said:thanks for help never heard of drill bits that run in reverse. im plannig on get my **** kicked there it if wasnt a good friend of mine i would not touch it. maybe someday the manufacturers will come up with a better design its only been a problem for 70 years.
25 Ft. lbs. is usually sufficient, but go back in 6 months and check that tightness again.Rickoo said:Is there a correct torque value when re-installing these bolts?
Edward Young Retired
After you make that expensive repair and you still have the same problem, What will you check next?
1 -
-
0
-
If they are bound up in that front plate rather than seized in the hx, use the breaker bar to work them back and forth both ways to break the part in the plate loose.0
-
EBEBRATT-Ed said:@MikeL_2 That is a good option
I try to avoid this type of repair during the winter months - don't want or need added pressure.0 -
Did it get replaced? I find it fascinating when guys fix such a corroded part.I'm not a plumber or hvac man and my thoughts in comments are purely for conversation.0
-
i didnt end up doing the work. the oil company that has been servicing it for over ten years did it i think 3 of the bolts broke but im not sure how they extracted them. the 2 guys told her she was lucky they got them out and were very nice. she had talked to the service manager about them never saying anything about it needing work all these years and they gave her a reduced price for that and some other work the boiler needed. i told her that i thought they were very fair about the whole thing.0
Categories
- All Categories
- 87K THE MAIN WALL
- 3.2K A-C, Heat Pumps & Refrigeration
- 58 Biomass
- 427 Carbon Monoxide Awareness
- 113 Chimneys & Flues
- 2.1K Domestic Hot Water
- 5.7K Gas Heating
- 109 Geothermal
- 161 Indoor-Air Quality
- 3.6K Oil Heating
- 70 Pipe Deterioration
- 994 Plumbing
- 6.3K Radiant Heating
- 391 Solar
- 15.4K Strictly Steam
- 3.4K Thermostats and Controls
- 55 Water Quality
- 44 Industry Classes
- 48 Job Opportunities
- 18 Recall Announcements