Welcome! Here are the website rules, as well as some tips for using this forum.
Need to contact us? Visit https://heatinghelp.com/contact-us/.
Click here to Find a Contractor in your area.
How to interpret Combustion Analysis Results - Noritz CB199-dv
Options
Amodedude1
Member Posts: 20
Just fired up a brand new Noritz CB199-DV (Natural Gas) and ran a combustion analysis and I'm trying to see if the unit is running within specifications or if I need to make adjustments but I am having trouble finding the OEM specifications for anything other than CO2 and gas pressure. Also, I'm not sure exactly how to interpret my results. Obviously, this is my first time ever doing a combustion analysis and this is my own boiler so I want to make sure I get it running right. Do the results indicate an adjustment is necessary on the gas valve or if it is running Lean or Rich?
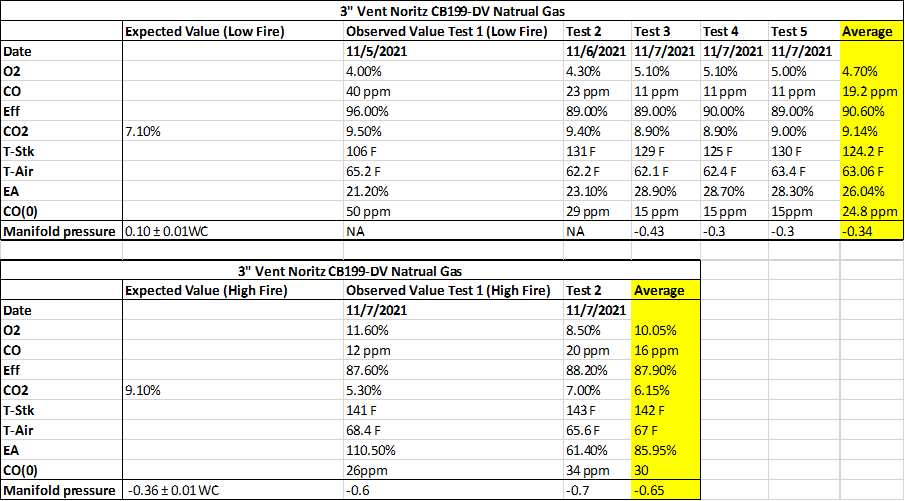
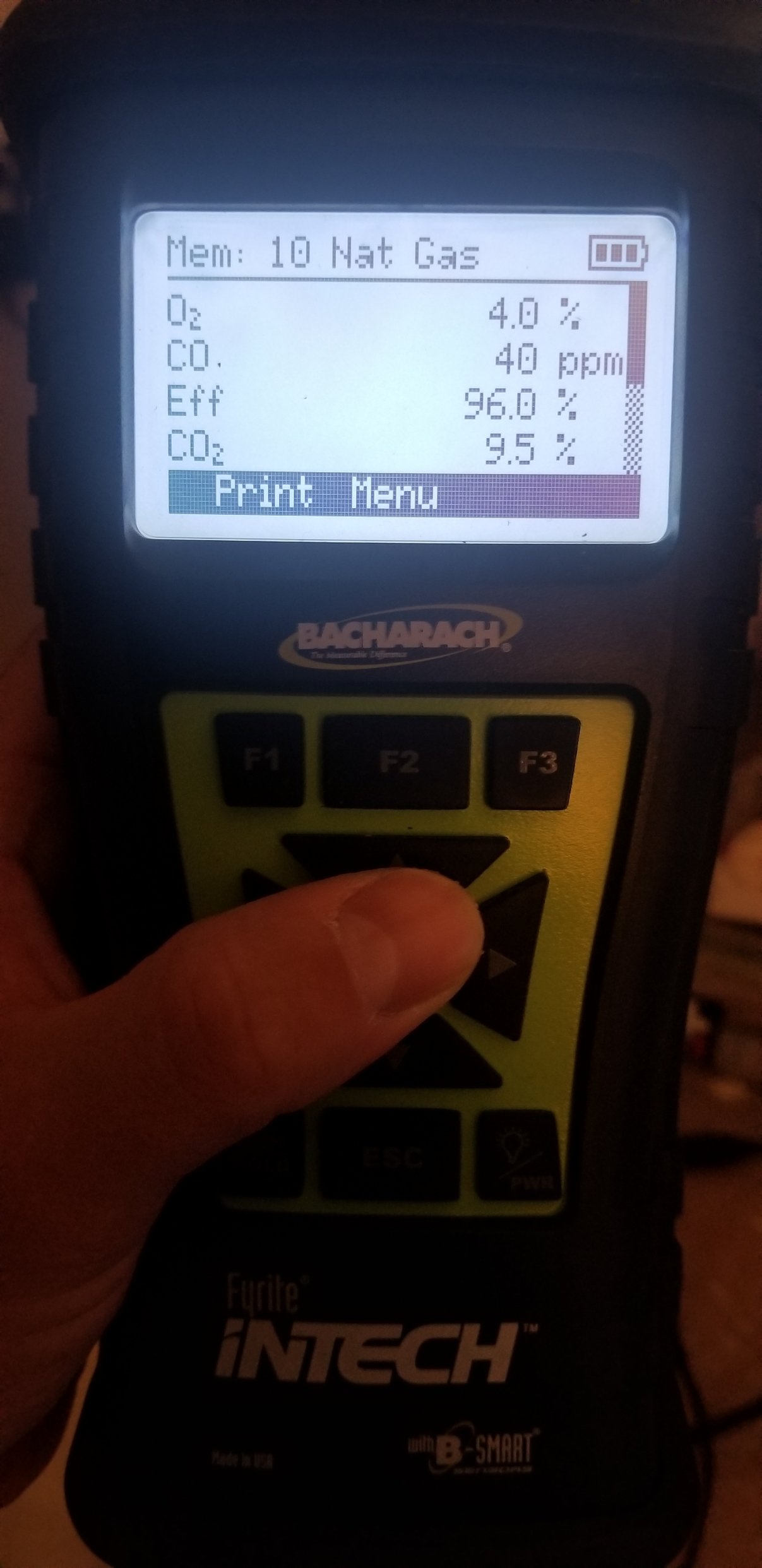
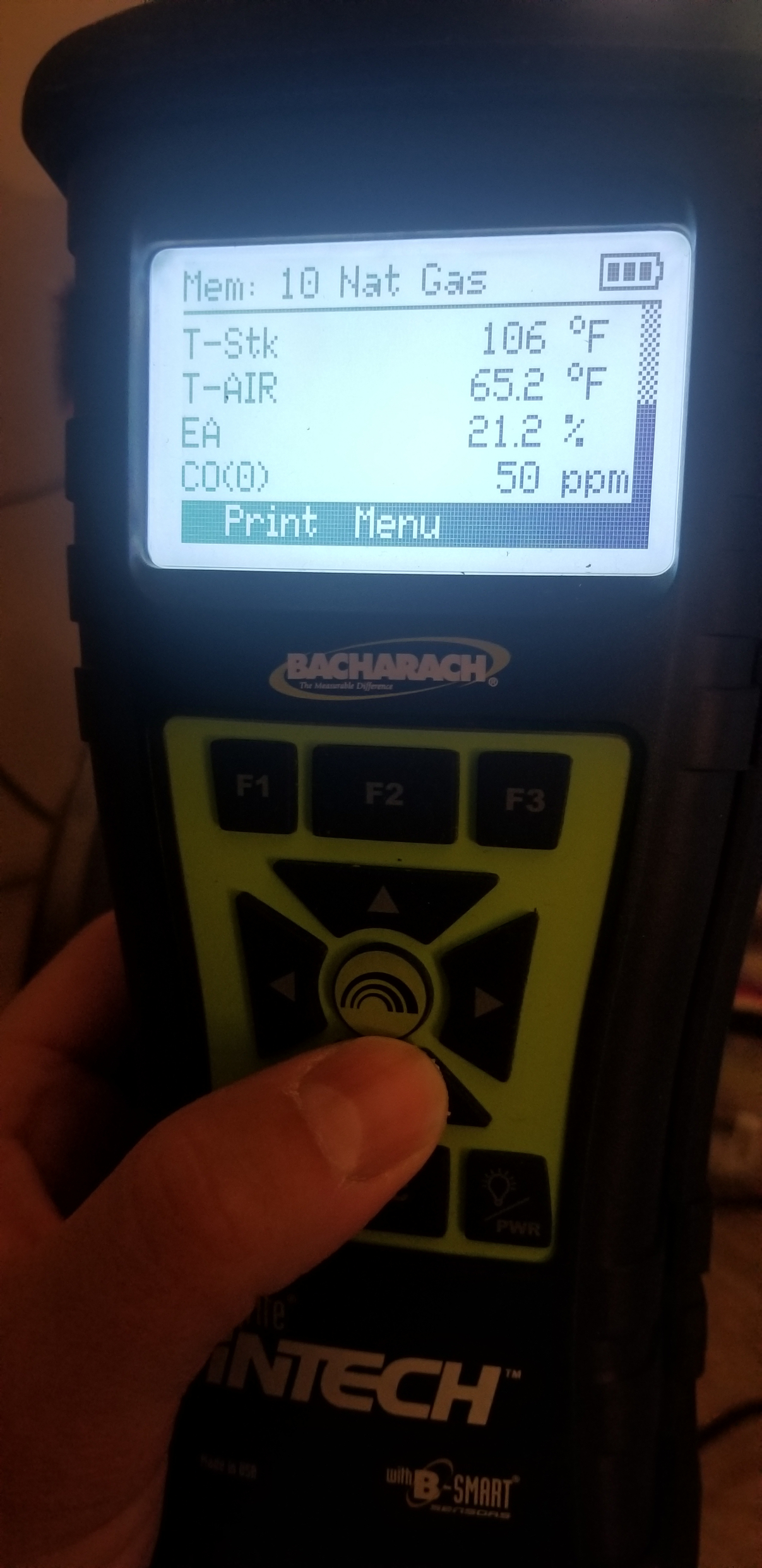
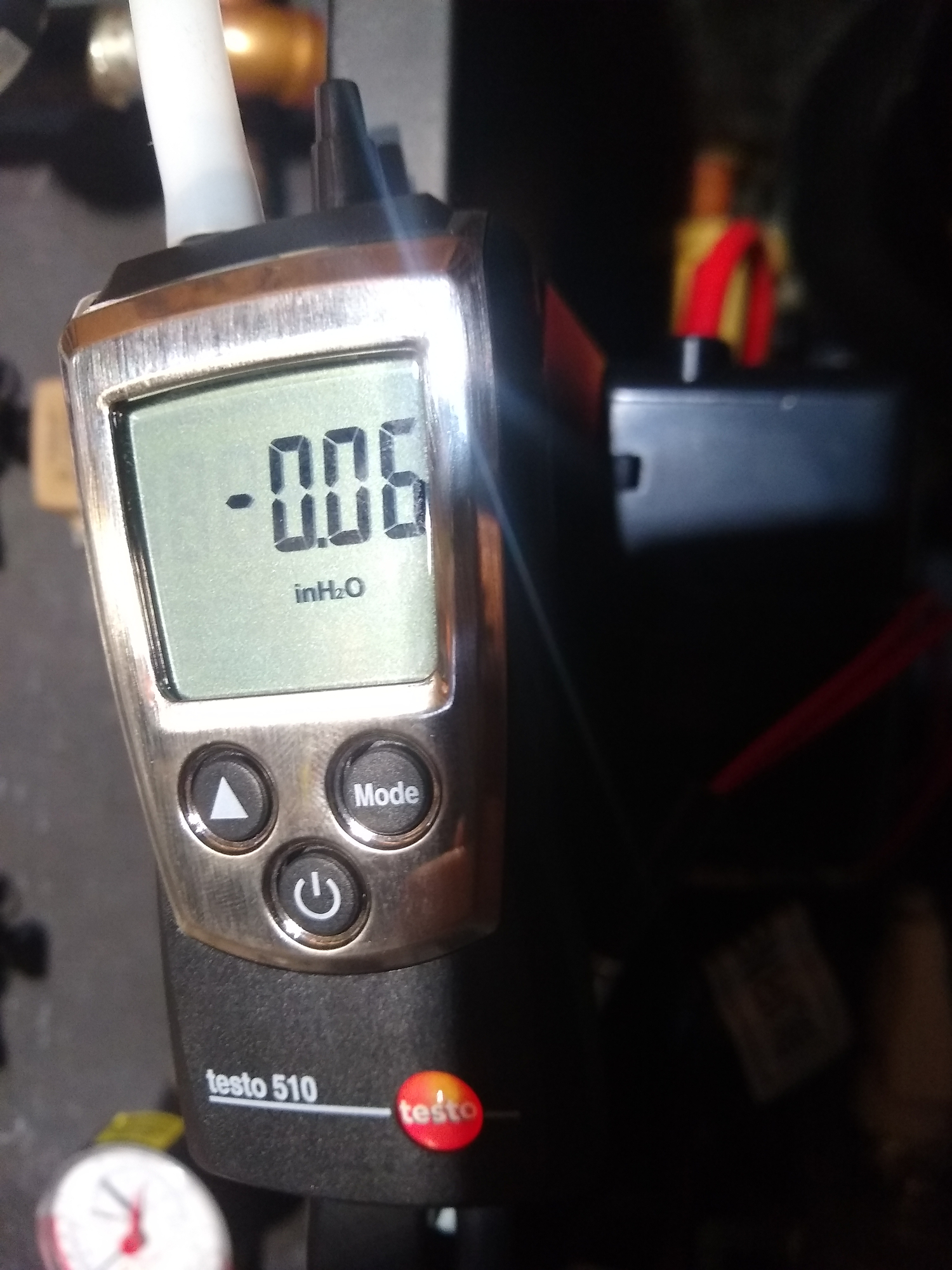
Natural Gas supply pressure was tested at right around 7.5"w.c.
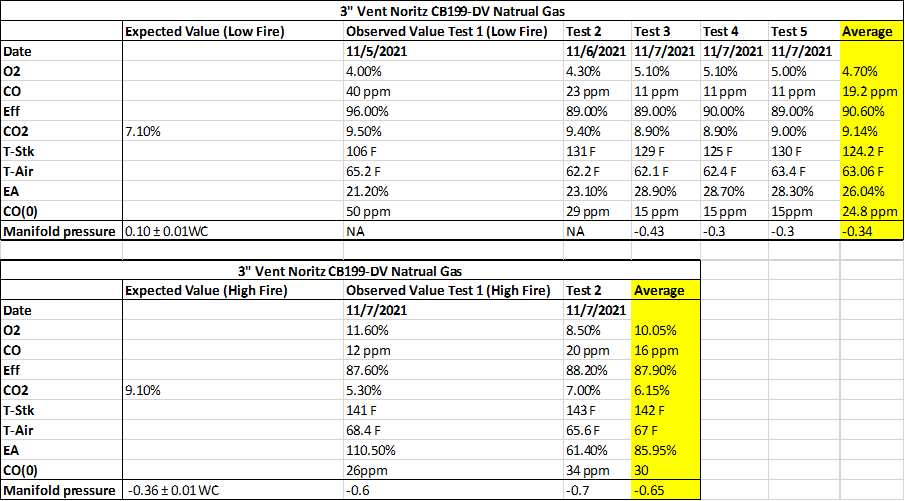
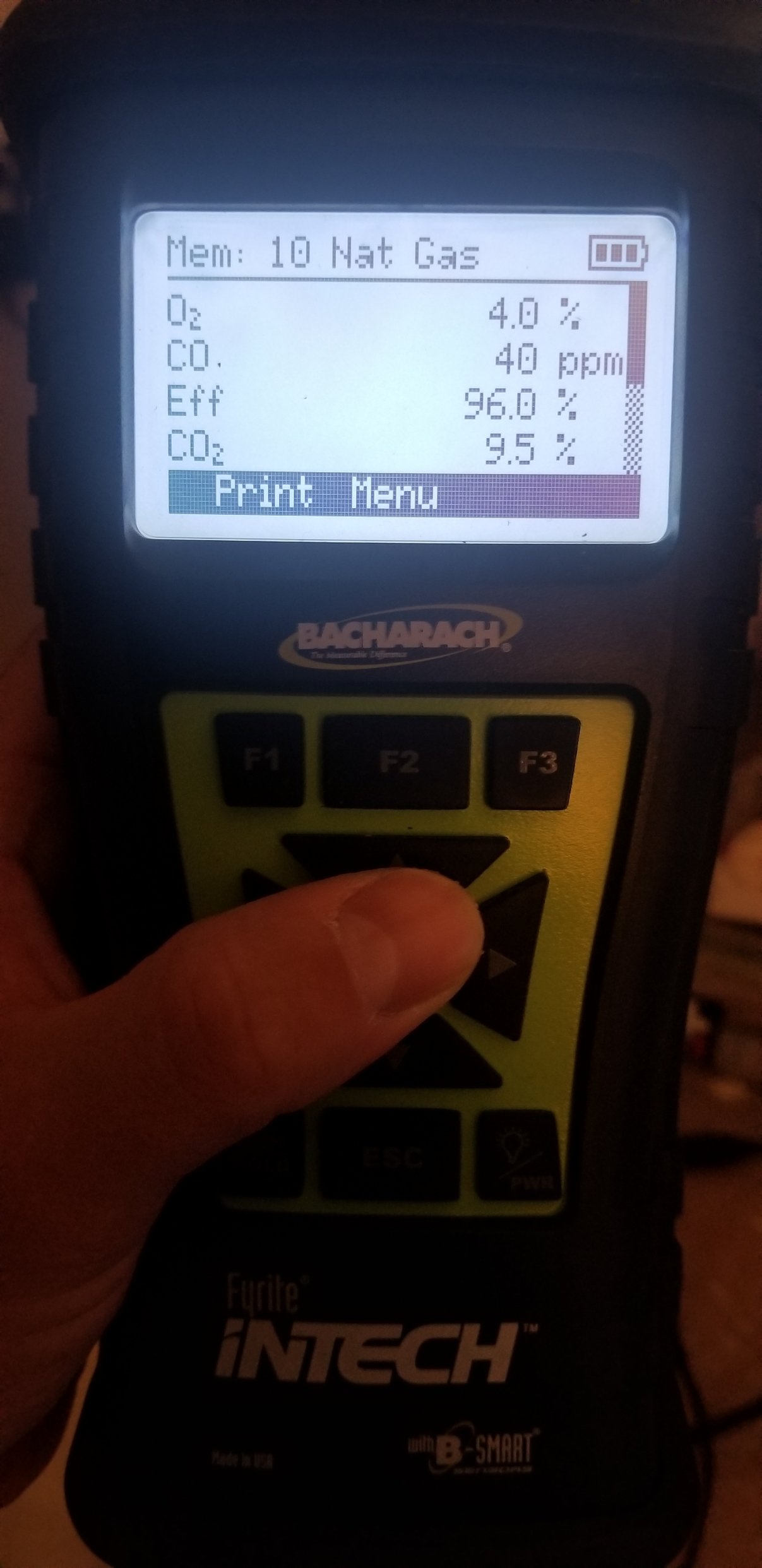
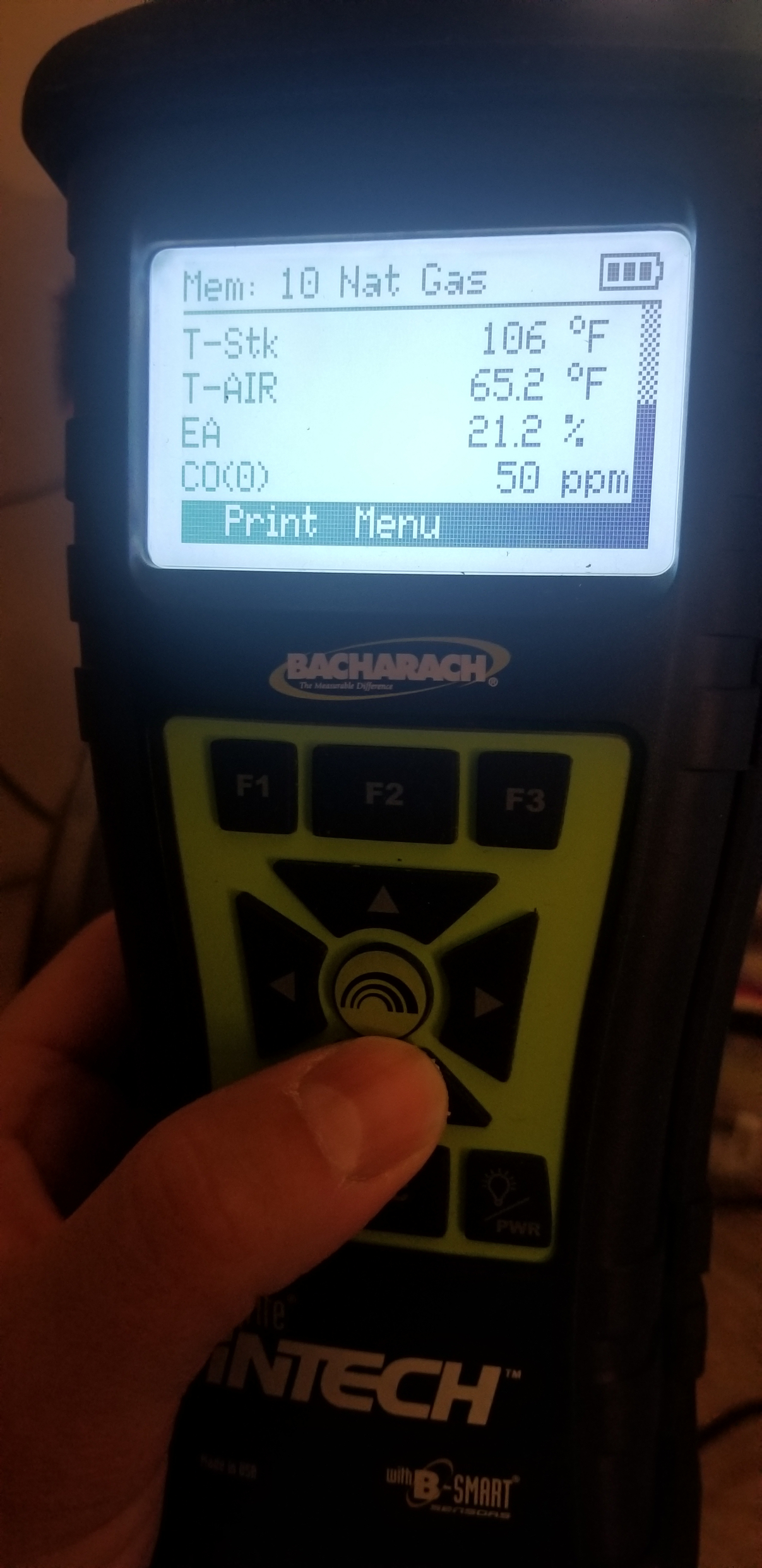
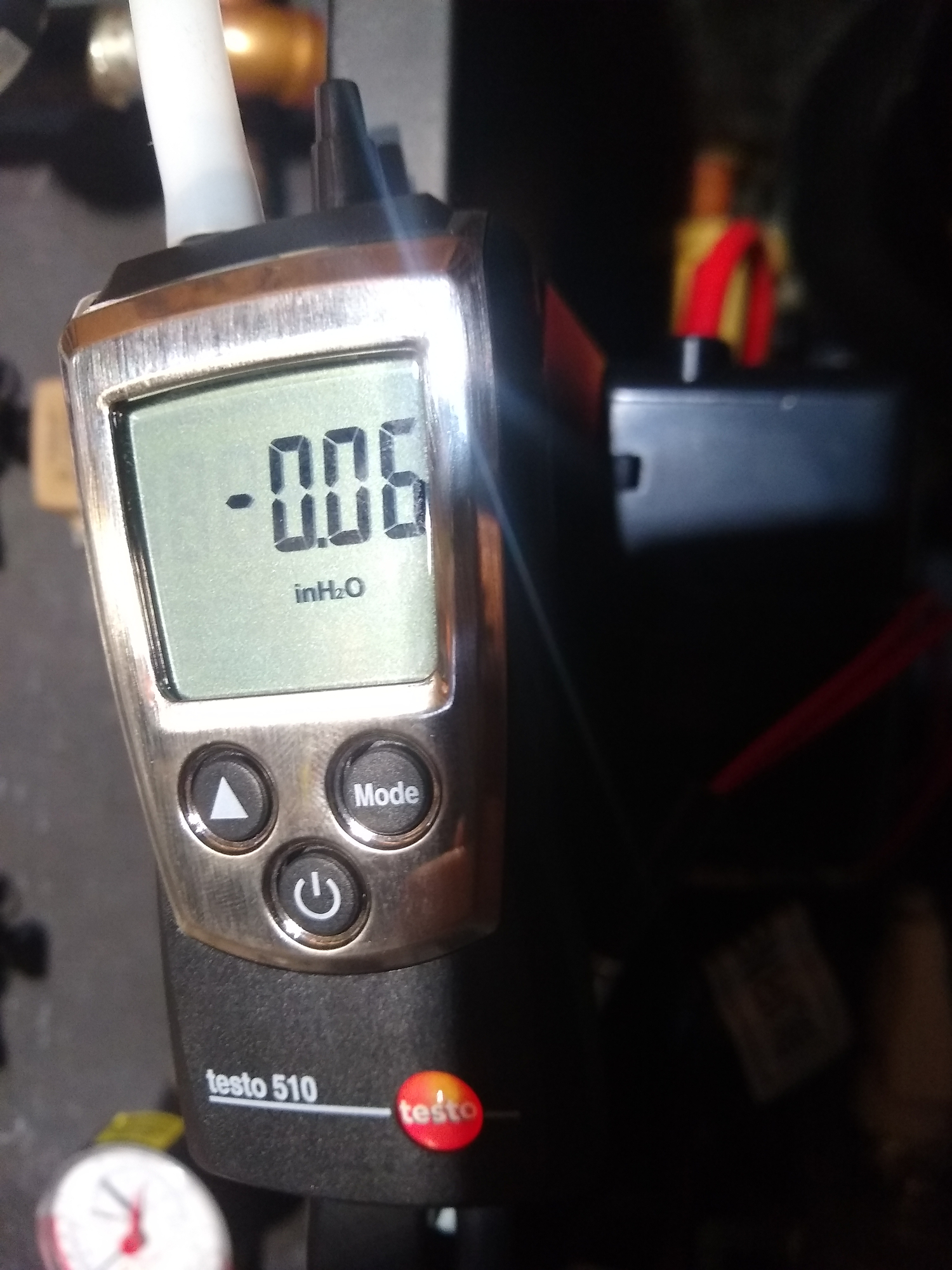
Natural Gas supply pressure was tested at right around 7.5"w.c.
0
Comments
-
Here is some of the documentation I found on the CB199 from the installation and service manuals.
0 -
I think you’re underfired, maybe @captainco can weigh in about an oriface change.
Your CO2 numbers seem backwards, low fire vs. high fire.There was an error rendering this rich post.
2 -
You are too rich on low fire and too lean on high fire. CO is under 100, which is good.
I have never been under the hood of a Noritz. Do you have the adjustment instructions?
Your condition usually involves adjusting an offset screw which can be a challenging adjustment
"If you can't explain it simply, you don't understand it well enough"
Albert Einstein2 -
Was the outdoor air temp warmer for the first test and colder on the latter?"If you can't explain it simply, you don't understand it well enough"
Albert Einstein0 -
I totally agree about it seeming backwards between high and low fire. I'm not sure why that is. The way I was switching between high-fire and low-fire was to set the dip switches according to the service manual. I'll try and take pics of the DIP switches when I try to do this again. However, I'm pretty sure it was high fire mode because the fan spooled up pretty significantly (i.e. - seemed to get faster and was louder).
Dip Switch Settings From Service Manual:
High Fire: 6 ON, 7 OFF
Low Fire: 6 OFF, 7 ON
Also, I the ambient air shouldn't have been so significantly different for the tests done today. All the tests done today 11/7 were done within an hour of one another. The biggest issue I had with the high fire test was that I couldn't get the boiler to stay on in high fire mode with a heating demand call for longer than about a minute. The water temperature was being satisfied in under 1 min even after I bumped the setpoint up to 180deg. Then the burner would go out so I don't think the test had enough time to steady out for high fire.
Next time I'm going to see if going into "Installer Mode" has any effect on this (i.e. - If I can keep the boiler on longer) or try to do the high fire test first instead of doing low fire first like I did here.
Lastly, and probably my biggest issue here is, I can't figure out how to get to the cap off for the offset screw to make any adjustments.
When I tried loosening up on the "Cap Screw" (which I'm assuming is as the caption says, a "CAP" with the actual adjustment screw underneath? I'm turning ant-clockwise (lefty-loosely) to remove but it's not seeming like it wants to budge with any reasonable amount of pressure and I'm worried about breaking it...0 -
Here is a link to the service, install, and owners manuals:
https://support.noritz.com/tankless-water-heaters-residential-combination-boilers-cb199-dv-ng
https://www.noritzparts.com/category/noritz-cb199-dv-ng-oem-repair-parts0 -
@Amodedude1
I agree with @Zman
" You are too rich on low fire and too lean on high fire. CO is under 100, which is good.
I have never been under the hood of a Noritz. Do you have the adjustment instructions?
Your condition usually involves adjusting an offset screw which can be a challenging adjustment"
Small adjustment you pretty close.
Your manifold gas pressure looks a wisker low on both lo & hi fire don't know if that is adjustable.
If it is I would play with that before the offset0 -
Yes, I'm pretty sure it is adjustable. Bare with me here, but I'm thinking the manifold adjustment is the small screw on the top right hand side with a - ... + marking on the top right hand side of the picture? The service manual is very vague about gas valve adjustments.
Might be time for me to get in touch with Noritz to see if they have any more details about the gas valve adjustments. You can see the markings from my Alen key where I tried to loosen the cap screw from the offset adjustment. It did not want to budge and gave me a bad feeling something might break if I had whaled on it any further so I stopped. I was probably doing something wrong.
@EBEBRATT-Ed Copy that, I'm assuming the top right adjustment port is most likely the manifold pressure adjuster. I'll try adjusting that before messing with my offset.
0 -
-
That looks like the same valve used in the HTP UFT Series. Dip switch setting are same as well. The top cap unthreads normally CCW. Gas valve adjustment is very sensitive. As @Zman said, make small changes (1/16-1/8 turn) and wait for changes to settle out.This video illustrates the process for the UFT series.2
-
The cap takes a Torks wrench, not an Allen.Bob Boan
You can choose to do what you want, but you cannot choose the consequences.0 -
I’m wondering if the gas line is of sufficient size? If not, that would cause it to run too lean as it ramps up to high fire.
I’d leave the gas valve adjustment alone until you confirm that you’re getting sufficient gas inlet pressure all the way from low to high fire.Bob Boan
You can choose to do what you want, but you cannot choose the consequences.1 -
@PC7060 You are right, its most likely the exact same single orifice gas valve used on the HTP equipment and it appears to be the same valve as what is shown in the YouTube video. It's a Time Engineering ET72S.J0209 gas valve.
I finally figured out how to get access to the offset adjustment. Indeed the 4mm hex *is* just a CAP. The Cap covers the adjustment screw which is also a 4mm hex. The issue was that it looked like there was either some kind of sealant applied onto the threads of the CAP from the factory OR the threads had galled up over time since 2016 when the unit was built which prevented it from coming off easily. Once off, you can see the offset adjustment screw underneath the CAP.
Before messing with anything I re-took the INLET static gas pressure and also did a dynamic pressure in low fire mode only. The static test was with the boiler not running. Dynamic was with the boiler running.
STATIC Inlet Pressure: 8.45"w.c.
DYNAMIC Inlet Pressure: varied from 8.39"w.c. to 8.46"w.c.
I think this is okay. For the record, Gas supply line is 1 1/4" coming into the house. That steps down to 1" before entering the gas meter. After the gas meter it is 1" for about 6ft at which point it Tee's into a 3/4" leg for the final 4 ft run to the Combi-boiler. On the other side of the tee, beyond the boiler, there is only a Gas range and oven. Those are the ONLY 3 gas appliances in the house and were not running during any of the tests. Black Iron pipe all the way through to the boiler and no flex or pressure regulators.
The last picture shows my manometer hooked up and ready to read manifold "outlet" pressures.
The good news is that I was able to perform my tests in LOW FIRE and everything seemed to be okay after an adjustment of about one half 1/2 turn C.C.W direction on the offset adjustment screw in the (-) minus direction. I made adjustments very slowly in about 1/8 turn increments until getting to the -0.10" w.c. (+/- 0.01) specification on my manometer. As I turned C.C.W. the CO2 readings went down and I was able to get the CO2 readings as close as possible to what is in the service manual for low fire. The closest I could seem to get was 8.0% CO2. Any more than this and my manometer readings would go beyond (more negative) than -0.11"w.c. spec. The new CO2 reading seems better than the about 9% I was getting previously in low fire.
Once flipping the DIP switches into HIGH Fire, things started to get weird. I started to get some very strange modulating pulsating noises or humming noises as soon as I flipped the switches into HIGH FIRE. See the video. I only let it run like that for a few seconds because it sounds very bad! Any ideas?https://youtu.be/AioPPuq4leg
EDIT: This is known as a "foghorn" /"fog-horning" noise. Looks like its way too lean in HIGH fire. Now I don't get how to adjust this. If it's too rich in low fire and too lean in high fire??? I can put it back to original settings but super confused at this point. Could it be a bad gas valve?
0 -
Put your manometer on the inlet pressure side of the valve and check the variance in high mode. There is a range of allowable change (see manual) and you will want to see if the pressure is fluctuating in rhythm to the sounds. If the inlet pressure is fluctuating or dropping out of tolerance I recommend to contact the gas company to have the meter looked at.I defer to @Ironman or one of the other pros for additional advice as my experience is limited.1
-
I have not worked on that model gas valve.
On similar valves, you would first set it to high fire using the screw to the right. You would then go to low fire and adjust the offset screw if needed.
You will want to check your gas pressure at high and low fire."If you can't explain it simply, you don't understand it well enough"
Albert Einstein1 -
As @Ironman mentioned earlier, undersized supply lines can cause this type of problem so I used the numbers you provided to check the sizing.My local code authority uses IFGC Table 402.4(2) with length based on the longest run.At a run of 10’ at 3/4” the rated CFM is 360. At 20’, the CFM is 247.Typical BTU per CFM is a bit more than 1,000 so the 200K BTU boiler is well within limits for the line.0
-
@PC7060 The exact measurements for length of gas pipe coming out of the gas meter are 9ft 1" black Iron, then a tee, then 8ft of 3/4". I was off on my estimates but I think that should still fall well within the numbers for BTU/CFM.
I'll get a measure of the dynamic inlet pressures for high fire tomorrow. For now, I'll leave you with a video of what it is that I'm doing for my adjustments. Calling it quits for tonight. Also, just want to re-iterate that the readings from my first post were from before ever touching a single adjustment screw on the gas valve or anything else. They didn't seem right from the start according to the literature which prompted me to start futzing with adjustments in the first place.
Video:https://www.youtube.com/watch?v=LgjS8p15Nos
0 -
Video is interesting, you can really hear the oscillating noise as you adjust the valve in high mode. As a FYSA, the procedures for the HTP fuel valve setup indicate adjusting the valve in low fire only. I think that when you turn the valve down to keep the system from foghorning it is inhibiting hire fire. My reason for this assertion is the low CO level shown on your video in high fire.On my system the CO scales up from around 6 PPM in low fire to 60 PPM in high fire.
I know this doesn’t help pinpoint the solution but though it was worth mentioning.Not sure if someone have already mentions this but have you verified your intake and exhaust lines are clear?0 -
Really appreciate all the help from everyone here. @Ironman and @PC7060, I ran the inlet pressure tests and also did one last combustion test in each mode just as a sanity check. This time, I shut off water demand, turned the boiler off, and restarted with the new DIP switch settings each time rather than flipping while running the boiler. The results seem pretty much the same. Outlet manifold pressure did not change whatsoever in each mode. However, the inlet pressure DID fluctuate slightly while running. The static (boiler off) pressure was very stable. Inlet pressure only fluctuated while running. Each reading was saved after the boiler had run for several minutes and values had stabilized.
LOW FIRE
_____________________________________________________
Inlet Pressure STATIC: 7.60"w.c.
Inlet Pressure DYNAMIC: 7.55"w.c. to 7.64"w.c. (varied)
O2: 5.7%
CO: 13ppm
CO2: 8.6%
Eff: 98.6%
T-Stk: 90deg F
T-Air: 64.9degF
Manifold Outlet Pressure: -0.05"w.c.
HIGH FIRE
_____________________________________________________
Inlet Pressure STATIC: 7.60"w.c.
Inlet Pressure DYNAMIC: 7.38"w.c. to 7.50"w.c. (varied)
O2: 8.1%
CO: 08ppm
CO2: 7.2%
Eff: 92.3%
T-Stk: 112deg F
T-Air: 65.4degF
Manifold Outlet Pressure: -0.05"w.c.
NORMAL FIRE
----------------------------------------------
Inlet Pressure STATIC: 7.67"w.c.
Inlet Pressure DYNAMIC: 7.41"w.c. to 7.59"w.c. (varied)
O2: 5.0%
CO: 09ppm
CO2: 9.0%
Eff: 95.8%
T-Stk: 106deg F
T-Air: 66.2degF
Manifold Outlet Pressure: -0.05"w.c.
A few thigs that stick out to me are that the manifold outlet pressure never changes no matter the mode. Also, normal fire values seems to fall somewhere in-between the low and high values except for O2. Lastly, the inlet pressure measured at the gas valve did seem to fluctuate +/- about 10-15"w.c. The ambient temps did increase slightly probably from the boiler running for around 20min during the tests.0 -
@Amodedude1 - thanks for the test information. The inlet pressure change seems well within spec. The high mode still seems off to me given how low the CO is but that just my thought (and could be your sensor).Is the system foghorning in high mode?
How does it perform during actual radiant heat operation?
What is the supply and return water temp during high mode? BTW, what type of radiant heat do you have?0 -
Is the system foghorning in high mode?- No more fog horn in any fire mode for both DHW and Heat. I left the offset adjustment the way it was per the combustion readings above. It might be slightly out of spec but I'm gonna call it good here since this seems to be the best I can get without a foghorn in high fire. Again, I can get low fire to be almost perfect but once it goes into high fire, it will foghorn so I had to scale back in lowfire to prevent the foghorn.
How does it perform during actual radiant heat operation? - It seems to be working great. I have Uponor Pex-a radiant floor heat. only one loop right now but 3 more future loops. Current loop is right around 160ft long under hardwood floor. It keeps the floor nice and warm. DHW is perfectly hot and consistent.
What is the supply and return water temp during high mode? - Delta between inlet and outlet on the radiant is about 20degF. Outlet at the manifold is 130degF return is 110degF (going off memory im not Infront of boiler right now).
and could be your sensor - agreed, it could be. I just find it unlikely because the NIST card from Bacharach says it was calibrated 10/20/2021 and just purchased from Supply House .com but it's certainly possible.
Since the boiler seems to be working fine I'm thinking I'll just leave as is for now unless anyone has any suggestions. I may purchase a new gas valve and replace just out of curiosity. Also, I did check that the vent was clear and it is. I have 3" vent on both intake and exhaust which is (approximately) 12 ft long for both.
0 -
All sounds good then. Are you using ODR to control SWT? The lower you can get the operating temperature the more efficient your boiler will operate.Agree it unlikely the new analyzer would have bad CO.0
-
-
-
And good job getting the system setup!0
-
UPDATE: This has been bothering me for a while that I wasn't able to dial in the system perfectly. Recently, my AGM module failed. It started jamming up on it's own and progressively got worse. Each time it jammed, it would throw an ERROR 67. I ended up replacing the old AGM with a new one (Noritz Part #:NPF303) and in the process decided to give the adjustments one last shot.
Well, I finally figured out what was going on with the LOW Fire CO2 being higher than the HIGH Fire CO2 and it was a real Shake my Head moment. The problem was de to the fact that I didn't open up enough faucets to make the boiler fan go into HIGH FIRE mode!
Previously, I was doing all my test with just the kitchen sink faucet open on full HOT. Apparently this was not enough to dump all the BTUs the boiler was putting out. This time, I opened up BOTH the kitchen sink and the shower to full blast HOT and wouldn't you know it, the boiler obviously kicked into HIGH FIRE mode. The fan spooled up big-time compared to what you saw in the videos and the CO2 readings finally started to make sense! LOWFIRE CO2 less then HIGH FIRE CO2! Finally!!
I can't believe it was that simple but hopefully this helps someone out in the future. Make sure you open ALL YOUR FAUCETS, not just one otherwise your boiler may not actually kick into high fire regardless of if you have the DIP switches set to be locked in high fire or not. You need a place (or multiple places) to dump the heat. So the new readings are:
LOW FIRE (Service Manual Spec for CO2 = 7.1%)
_____________________________________________________
O2: 8.4%
CO: 18ppm
CO2: 7.1%
Eff: 99.6%
T-Stk: 64deg F
T-Air: 55degF
HIGH FIRE (Service Manual Spec for CO2 = 9.1%)
_____________________________________________________
O2: 5.3%
CO: 57ppm
CO2: 8.8%
Eff: 88.7%
T-Stk: 133deg F
T-Air: 55.5degF
NORMAL FIRE
----------------------------------------------
O2: 6.6%
CO: 18ppm
CO2: 8.1%
Eff: 94.3%
T-Stk: 109deg F
T-Air: 55.7degF
These numbers finally make a lot more sense to me and are close enough to what the service manual says to make me happy.
The only issue now is that I'm getting a little "fog horn"/howling noise every time the boiler fires up and it lasts about 2-3 seconds until the AGM/FAN Speeds adjust. I've been running it overnight and seems okay apart from the weird horn noise it makes on transition from OFF State-Low/High Fire. I'm not sure if there are any settings in installer mode that I could adjust to compensate for this. I found the following settings 17:FS (A.FH2, b.FH1, C.FL, & d.Ag) which control:
A.FH2 - 30 ~ 30 • Maximum Fan RPM compensation in DHW mode : ±30.
b.FH1 - 30 ~ 30 • Maximum Fan RPM compensation in Heating mode : ±30.
C.FL - 30 ~ 30 • Minimum Fan RPM compensation : ±30.
d.Ag - 50 ~ 50 • AGM Position compensation : ±50.
My factory default settings are:
A.FH2 - 00
b.FH1 - 00
C.FL - 01
d.Ag - 15
I'm thinking *maybe* the AGM Position compensation or Min Fan RPM compensation **might** be something I can try adjusting but then again, these are set at the factory and probably should not be messed with. Curious if anyone else has experience with these?
My goal now is to get rid of this startup howl/horn noise.1 -
Also, just for the sake of completeness, I did also replace the gas valve while I was in the process of replacing the AGM since I was originally suspecting that it was a gas valve issue (which most likely, it is not). I also found out some more info about it.
The "Time Engineering CO. LTD" ET72S-J0209 gas valve from Noritz (Part# NAC180 - CB - Gas Valve Assembly) is actually just a rebranded version of the Siemens VGU7 gas valve: https://sid.siemens.com/v/u/A6V102607060 -
I’ve been having some occasional foghorn issues on DHW calls but my biggest issues is a flame loss fault Erro 12 when CH ramps up to mid fire around 75k BTU (assuming 5gpm internal pump on high, 30F DT), The AGM steps just fine, but get to step 9 and when the inducer gets near the top of the step, burner shuts down. Flame signal looks steady the whole time 0.7-0.8. It will refire and repeat 5 or 6y times then go into lockout.
For now I’ve just kept the thermostat at the same temp and limit it to under 30F delta T. The problem is I just converted over another steam radiator and I’m about 8k BTU short at 140F water temps when it gets under 20F outside.
I put a SOX3 on there and tried making some adjustments to the F/A ratio, but none of the numbers line up with the charts above. Right not its running only 2.5-4% O2 CO2 8-10%. A little rich. But when I lean it out closer to spec, it gets too lean and flame drops out.
Oddly on a max call for DHW, it never drops out since it ramps up quickly. Only on a slow ramp it seems as it hits mid fire. I did play with the AGM and inducer offsets, but it didnt change anything that i could tell.
Question 1 - could a dirty HE be causing these issues?
Question 2 - what is the sequence of operation after step 9. I would think that was max firing rate, but its actually mid fire I suspect. Does it go to 0 again and ramp up a second time but with higher inducer speeds?1 -
Update. Talked to Noritz tech support. They are supposed to be sending me a flame sensor, sight windows and a new heat exchanger. I suspect the HE is partially plugged and causing what I’m seeing. I wonder if its an issue they had with that model year and they’ve made some updates. My boiler is a 2016 production model. I know the supplier that originally sold it had a lot of issues with them.2
Categories
- All Categories
- 87K THE MAIN WALL
- 3.2K A-C, Heat Pumps & Refrigeration
- 58 Biomass
- 427 Carbon Monoxide Awareness
- 113 Chimneys & Flues
- 2.1K Domestic Hot Water
- 5.7K Gas Heating
- 109 Geothermal
- 161 Indoor-Air Quality
- 3.6K Oil Heating
- 70 Pipe Deterioration
- 995 Plumbing
- 6.3K Radiant Heating
- 391 Solar
- 15.4K Strictly Steam
- 3.4K Thermostats and Controls
- 55 Water Quality
- 44 Industry Classes
- 48 Job Opportunities
- 18 Recall Announcements