Welcome! Here are the website rules, as well as some tips for using this forum.
Need to contact us? Visit https://heatinghelp.com/contact-us/.
Click here to Find a Contractor in your area.
12" Threaded Pipe
Options

Mkowal5220
Member Posts: 9
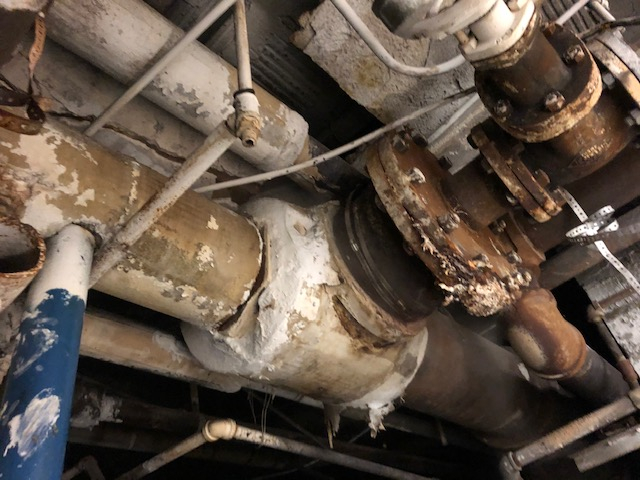
I (the estimator) have been quoting and repairing steam leaks in 100 plus year old buildings for years now. Of course we flange and weld our repairs but it always amazes me how those old timers would have threaded that 12" pipe (8 and 10 also), our guys struggle with 3 and 4".
Does anyone have any idea how they were able to do this? I cant find anything online that talks about how they did it.
1
Comments
-
That's a very good question. One that I have asked many times.
I've also wondered how they screwed it all together and not have it leak.
It is my understanding that they used a type single bit that was rolled around the pipe, cutting the threads.
Nowadays, a CNC machine at a machine shop would do the threading.
0 -
when the dead men put those systems in they were not afraid to work, When i started 45 yr ago i asked an old time steam man in NYC how it was done when he started in the 20's and explained to me about chain falls scaffolds, jacks and cribbing.0
-
So they threaded it with a milling machine with an auto feeder that matched the thread pitch that probably also rotated the pipe?0
-
55 years ago I worked in the Brooklyn museum in New York City.
I was a young mechanic at the time we had to remove a 12" nipple and cap from a T at the end of a steam main just outside of a concrete wall and install a short nipple (not available for purchase) The short nipple was needed to install a transmission piece to weld an adapter to a 12 x 8" fitting so a new extension to the steam main could be installed.
My boss had to rent a stock and die and a donkey with a bench vise from a pipe yard in Virginia.
He also had to buy a 1/2 length of 12" pipe. The cost for the rental and pipe was $1700.
It four of us to make a 48" nipple 6 hours. The wrench we used was a giant chain wrench which was rented also, luckily we did not have to use a hold back wrench.
Let me tell you those steam fitters were men of iron.
JakeSteam: The Perfect Fluid for Heating and Some of the Problems
by Jacob (Jake) Myron1 -
Wouldn't it have made more sense to cut the nipple and weld a flange to it in place?0
-
About 30 years ago, I visited a high school in Erie, Pa. where I was sent to answer questions the contractor had about a couple of H B Smith boilers. The 16" steam header and all the piping in the boiler room from 12" down was threaded as was all the OS&Y valves and fittings. What a sight it was. According to the head fitter who looked as old as dirt, said that those pipes were threaded by hand with a ratchet threader. Then the fittings and valves were put together with pipe tongs using a pipe dope similar to "litharge and glycerin". Then the threads were set by someone using a 4-6 lb hand sledge pounding on the inside of the pipe. I am not positive if that is how it is actually done but that is what that guy said.
By the way, there is a Hadley landis style heavy duty 13" large capacity threading machine for sale on E'BAY for only $39,500.00 . Imagine taking that to a piping job. They do not say how much it weighs but it would definitely strain a muscle or two.
I forgot to add 1 thing; there is a company in the south side of Pittsburgh, Pa called B M Kramer that has a HUGE pipe machine that can thread very large pipe sizes. They stock just about everything for piping.0 -
You sure don't want to get a leak in a 16" steam header the first time you fire it up I'm guessing, what a pain!
NJ Steam Homeowner.
Free NJ and remote steam advice: https://heatinghelp.com/find-a-contractor/detail/new-jersey-steam-help/
See my sight glass boiler videos: https://bit.ly/3sZW1el0 -
They used the same type of threaders we have available today like the Ridgid 141 that does 2 1/2-4' and the 161 that goes up to 6"
They also made larger sizes which went up to at least 12". Can't remember if it went bigger but I have and old brochure around here somewhere from Toledo threaders if I find it I will post it.
They also had bigger machines to use in a shop.
I was told the put strings up for all the pipes and measured off the strings then made up a lot of the pipe and fittings and cut threads at the shop.2 -
-
I've used chain tongues on the six-inch threaded pipe a very long time ago.
Still have no exact info as to how that twelve-inch pipe was threaded back in the day. At least nothing specific like the excellent picture that @EBEBRATT-Ed posted above. Is that really a machine that would have been used?0 -
-
No, that was not me as a first year apprentice LOL
If any one has seen or used the Ridgid 141 or 161 threader thay had those back in the day. Toledo made them as well, I think Ridgid came along later.
The made sizes up to 12" as I recall, maybe larger. I used to have a very old brochure from Toledo but I think I tossed it as it was mostly destroyed
But i do remember 1 thing. The 8" threader was heavy maybe 150-200 lbs but the brochure said "Can easily be put on the pipe by one man".
Difficult to imagine them threading pipe before electricity was widely available and they must have hauled pipe and fittings to the jobs in a horse and wagon
probably used water power to drive some machines0 -
We have a Ferg fab facility here in Front Royal, VA
Threading up to 12", & roll grooving up to 36"
https://m.ferguson.com/content/branch-solutions/pipe-fabrication
1 -
When I see stuff like that on a job site, I marvel at the ingenuity of the people who did it. Their knuckles must have dragged on the ground.Ray Wohlfarth
Boiler Lessons0 -
I don't think it was their knuckles that were dragging on the ground...RayWohlfarth said:When I see stuff like that on a job site, I marvel at the ingenuity of the people who did it. Their knuckles must have dragged on the ground.
Can you imagine anyone threading 12" pipe today?
0 -
53 years ago I just out of high school and my father thought I needed a better job. He arranged for an interview as a "Boiler Maker apprentice". The first question the master asked, was to pick up a 64" compound wrench and bring it over to him and explain it's use. That was not a problem at all for me it only weighed 125 lbs. I was quite familiar with the wrench because I grew up on big farm in VT and we did irrigation and refrigeration (orchards). I was hired on the spot and my pay was doubled. All the fitting and nipples had the weight stamped or embossed on them so we knew how much we were lifting. We would use "Beaver" dies and huge band saws like the one pictured above to cut and thread. The near boiler piping was tuff, but handling the 1200 lbs. sections in a tight basement was by far the worse part of the job. But, I loved my job and I'm still doing it today at 73. Although our boilers today weigh in at 75 lbs... Kids today have no idea what work is.7
-
My Grandpa "Buttsy" who taught me, and whose business I purchased, always told the story of how his boss at the time, moved his family 55 miles away to do the plumbing and heating modernization to the Federal Building in Huron SD from 1933-35. There was a fair amount of 3/8"-12", the largest being used for roof drain leaders. Anyway they took their pipe to the railyard roundhouse and had the threads cut by the boilermakers on their big turning lathe (I'd have loved to see that!). As a side note: Grandpa hired those same boiler makers to come down after hours and "drill" overhead holes with a star bit and 2# hammer for 5/8" lead expansion anchors (approximately 1.5" O.D. holes) for a pint of whiskey/night to hang that pipe. He said their arms were as big as your thigh. All the Potable water lines were/are threaded brass, with the exposed pipe assembled with strap wrenches and rosin, disassembled and shipped to Sioux City Iowa to be chrome plated, returned and reassembled. You all know 12" cast 90's weigh in at over 220 #'s and were lifted with rope slings and block and tackle. I still have one of the 5' chain tong wrenches they used, for tightening that 12" they added a cheater pipe. For pipe pitch they used a water filled hose with a gauge glass in each end.
5 -
0
-
I checked out a steamer in a USPO building that had the same chrome plated brass plumbing. It was a one pipe system from that era. May have been WPA projects.
From when they had more time (cheap labor) than money.
And only about 80 miles west of Sioux City.0 -
When I still had hair I worked at Eatons pipe shop. They did not believe in welding steam pipe because they wanted to be able to retrieve the flanges when the pipe rotted or they were renovating for some job. The threader they had was circa 1896 and the whole shop ran off one 20 horse dc motor with flat belts and pulleys in the ceiling. The threader could go up to 10 inch and it used one chaser die to cut the threads, to cut pipe you could drop a cutter die and cut the pipe at whatever you needed. The first job I did with old Stan was a chilled water bypass six inch pipe, threaded elbows and flanges. We used chain wrenches and red lead dope, I remember I was doing chins on the wrench handle and I still couldn't get that joint tight. My job ( it seemed like) every Friday afternoon was to take a cutting torch cut a kirf at the base of the flange on old pipe and take a bull head chisel and hammer the pipe inward so I could get the threaded flange off. The boss of the shop who had been there for 42 years bragged to me one time, when I said I was fed up pounding pipe to rescue flanges, he told me he didn't think they had bought a new flange for 60 years. The whole store all two blocks of it, was high pressure 125 psi steam it was an education from the early 20 th century. They used water elevators ,when they used dray horses the horses stalls were on the second floor of the shipping building, the water main was cast iron factory flanged cast iron 24 inch diameter, quite the place.2
-
-
Categories
- All Categories
- 87K THE MAIN WALL
- 3.2K A-C, Heat Pumps & Refrigeration
- 58 Biomass
- 426 Carbon Monoxide Awareness
- 113 Chimneys & Flues
- 2.1K Domestic Hot Water
- 5.7K Gas Heating
- 109 Geothermal
- 161 Indoor-Air Quality
- 3.6K Oil Heating
- 70 Pipe Deterioration
- 994 Plumbing
- 6.3K Radiant Heating
- 389 Solar
- 15.4K Strictly Steam
- 3.4K Thermostats and Controls
- 54 Water Quality
- 44 Industry Classes
- 48 Job Opportunities
- 18 Recall Announcements