Welcome! Here are the website rules, as well as some tips for using this forum.
Need to contact us? Visit https://heatinghelp.com/contact-us/.
Click here to Find a Contractor in your area.
A total basket case
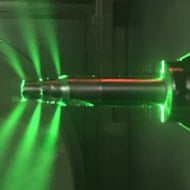
Lard
Member Posts: 115
I have inherited a mess of a one-pipe steam system in a 1920’s church. The water use is insane...if that even describes it. The boiler is intact (it passed the flood test with flying colors) so the major leaks only exist in the buried wet returns.
The boiler is a a hopelessly oversized Weil McClain 1180 with a Gordon Piatt gas gun. A model 780 is even a bit oversized based on my EDR calculation of 2135 sq. ft. The NBP is a mess with takeoffs between risers (ugh...). Some bonehead added a receiver tank and two F&T traps at the tank from the old wet returns. When water makes it (rare, due to the insane leakage) these hammer like mad due to a 2 1/2 ft rise in the returns to get to the tank. There is a float valve for makeup in the feed tank that did not have a meter, but now it has a logging meter installed as of last october. See the pictures and cry. The water dept has contacted the church in previous years due to excess consumption! Supposedly some boiler sections were replaced a few years ago (duh...) and the contractor said nothing of the visibly leaking returns or surging/wet steam.
This thing is essentially a one-pass boiler at this point.
The plan is to abandon the wet returns and put in two condensate receivers at the exposed ends of the mains. I believe each main end will need a false water line to bring several drips together before a properly sized F&T trap. I would love to go back to gravity, but replacing the buried lines would require sawing through the slab in a finished part of the basement to excavate/replace the returns. There are low radiators and indirect stacks in the basement ceiling so there is no room for dry returns without creating head bangers.
The boiler is a a hopelessly oversized Weil McClain 1180 with a Gordon Piatt gas gun. A model 780 is even a bit oversized based on my EDR calculation of 2135 sq. ft. The NBP is a mess with takeoffs between risers (ugh...). Some bonehead added a receiver tank and two F&T traps at the tank from the old wet returns. When water makes it (rare, due to the insane leakage) these hammer like mad due to a 2 1/2 ft rise in the returns to get to the tank. There is a float valve for makeup in the feed tank that did not have a meter, but now it has a logging meter installed as of last october. See the pictures and cry. The water dept has contacted the church in previous years due to excess consumption! Supposedly some boiler sections were replaced a few years ago (duh...) and the contractor said nothing of the visibly leaking returns or surging/wet steam.
This thing is essentially a one-pass boiler at this point.
The plan is to abandon the wet returns and put in two condensate receivers at the exposed ends of the mains. I believe each main end will need a false water line to bring several drips together before a properly sized F&T trap. I would love to go back to gravity, but replacing the buried lines would require sawing through the slab in a finished part of the basement to excavate/replace the returns. There are low radiators and indirect stacks in the basement ceiling so there is no room for dry returns without creating head bangers.
0
Comments
-
-
> @JUGHNE said:
> Any chance of running a new wet return above the floor against a wall and boxing it in? A doorway would be an issue, but could be cut down into the floor at that location (s).
I had the same thought early on.
There would be three finished rooms and two doorways to cut through. At that point the old path may as well be excavated since the can of worms would be open.
I also thought that the cuts under doorways would be crud traps with no good way to clean them out.0 -
If you can follow that excellent suggestion, and go with gravity, you could do away with all the unreliable pumps, and switches.
That would cut out a lot of reliability problems in the future. Probably, the two new wet returns could be of modest size, (1& 1/2” or less?) and copper, until they meet up before the boiler. They will need some tee’s and valves at both ends, to enable a pressure flush in the future. God gave us marvelous gravity, so why not use it especially here?
You could follow the walls, and maybe not even have to box it in.
Otherwise you will need a condensate feed tank in place of what’s there now, triggered by the LWCO.—NBC1 -
More exactly, boiler feed tank/pumps. As @nicholas bonham-carter said, these must be controlled by a low water sensor -- I wouldn't call this one a low water cutoff; on that monster you want two of those, too! -- which will trigger the feed pumps. Since you will have two tanks, you have a slight problem with which tank feeds... so...
I think what I would do is to have two condensate receiver tanks, as you have planned. Each would have a float which operate what amounts to a condensate return pump for that tank -- but it wouldn't go to the boiler. They -- the two of them -- would go to a third tank at the boiler, and it would be a true boiler feed tank, controlled, as I said above, by a low water sensor. This tank -- not the condensate receivers -- would also have a float, which would control makeup water if required -- and an overflow to a drain, in the hopefully unlikely event that it threatens to overflow.
It sounds more complicated than it really is, and I'll readily grant that it adds another pump and some complexity in control. On the other hand, even with that monster boiler the condensate return pumps don't have to be that big, and better yet the piping can be copper, and relatively small in diameter even with that monster at full song, you are still on the order of only 2 gallons per minute for the whole system -- 1 inch copper with suitable pumps should be quite adequate, and better yet -- you can install it pretty much where you want it.Br. Jamie, osb
Building superintendent/caretaker, 7200 sq. ft. historic house museum with dependencies in New England0 -
> @nicholas bonham-carter said:
> If you can follow that excellent suggestion, and go with gravity, you could do away with all the unreliable pumps, and switches.
> That would cut out a lot of reliability problems in the future. Probably, the two new wet returns could be of modest size, (1& 1/2” or less?) and copper, until they meet up before the boiler. They will need some tee’s and valves at both ends, to enable a pressure flush in the future. God gave us marvelous gravity, so why not use it especially here?
> You could follow the walls, and maybe not even have to box it in.
> Otherwise you will need a condensate feed tank in place of what’s there now, triggered by the LWCO.—NBC
If gravity can be done I would definitely prefer it. The rooms to run through are well above the water line so copper is out. Next time I am there I will investigate a path while avoiding doors to keep it a dry return (the possible kicker is a curved wall).
The other return does not have this option at all. It is either hack up the concrete floor or pump overhead. If gravity can be attained on the other line it would be worth tearing up the floor for this shorter one (but that would not go over well).
There is already a feed tank/pump controlled by the LWCO so any remote receiver can just barf into that tank as it currenly stands. Eliminating said tank would be wonderful but I am limited by the layout of this basement0 -
> @Jamie Hall said:
> More exactly, boiler feed tank/pumps. As @nicholas bonham-carter said, these must be controlled by a low water sensor -- I wouldn't call this one a low water cutoff; on that monster you want two of those, too! -- which will trigger the feed pumps. Since you will have two tanks, you have a slight problem with which tank feeds... so...
>
> I think what I would do is to have two condensate receiver tanks, as you have planned. Each would have a float which operate what amounts to a condensate return pump for that tank -- but it wouldn't go to the boiler. They -- the two of them -- would go to a third tank at the boiler, and it would be a true boiler feed tank, controlled, as I said above, by a low water sensor. This tank -- not the condensate receivers -- would also have a float, which would control makeup water if required -- and an overflow to a drain, in the hopefully unlikely event that it threatens to overflow.
>
> It sounds more complicated than it really is, and I'll readily grant that it adds another pump and some complexity in control. On the other hand, even with that monster boiler the condensate return pumps don't have to be that big, and better yet the piping can be copper, and relatively small in diameter even with that monster at full song, you are still on the order of only 2 gallons per minute for the whole system -- 1 inch copper with suitable pumps should be quite adequate, and better yet -- you can install it pretty much where you want it.
Precisely what I had planned, as the feed tank already exists (controlled by a level switch). You are right, It is not complicated. I work with hydraulics, pneumatics, electrical every day and this condensate concept is simple compared to most of those systems. I am just weighing options here.
I had already planned for 2 gpm but even then the radiation is split between two mains so that is overkill. I believe the connected radiation is a total of 1.06 gpm condensate. The smallest (6 gallon) will work in this case if I did my math correctly. I was planning to use 1” for the pumped return due to the 130’ length. 3/4 black iron was borderline with frictional head.0 -
Buried wet returns don't need to be buried deeply. Six inches is fine, unless your AHJ requires more depth. This would minimize excavation.
Keep in mind that the condensate transfer pumps and the extra traps they need will require maintenance over the years. This is another reason we like gravity return.All Steamed Up, Inc.
Towson, MD, USA
Steam, Vapor & Hot-Water Heating Specialists
Oil & Gas Burner Service
Consulting0 -
> @Steamhead said:
> Buried wet returns don't need to be buried deeply. Six inches is fine, unless your AHJ requires more depth. This would minimize excavation.
>
> Keep in mind that the condensate transfer pumps and the extra traps they need will require maintenance over the years. This is another reason we like gravity return.
These current returns are at least 3’ deep for most of their run since there is an upper level to the basement between a low level dining hall and the boiler room. The hall (where the long return begins) is 1’ lower than the boiler room. This upper level is the thorn in this situation.0 -
-
Can you separate the lower level into a hot water loop from the boiler?—NBC0
-
> @Ironman said:
> The boiler should also have 3 risers, not two.
There are three risers. The third is hidden behind the flue. In fact it is nearly touching it.
> @nicholas bonham-carter said:
> Can you separate the lower level into a hot water loop from the boiler?—NBC
I have plans to do a loop (and eliminate the electric that was put in) since there is so much surplus boiler size. I would add baseboards around the basement. The current low radiation would remain steam though due to its massive size.
Currently there is 120 EDR worth of radiators hanging from the ceiling but all those do is heat the sanctuary above. They are below the main so they are two pipe. The other low radiation is two 237 EDR stacks of indirects (ARCO Vento) in the ceiling to heat the sanctuary. After doing my EDR calculation, I don’t want to switch these to water as that would cut 594 EDR from the steam radiation on an already comically oversized boiler.0 -
I was at the building today. The return along the floor would be along a curve instead of a straight run and would be a couple feet above the water line. A false water line would be a must due to the high elevation. Three separate drips come together right before the return enters its rusty grave.
This silly curved wall makes hiding an above floor pipe in the finished rooms much more difficult. There would be several very thick (one is 20+ inches) brick walls to punch through too.
I have not totally abandoned this option but doubt I can drum up much support for a big ugly pipe making wacky jogs every few feet along that wall. The congregation approves of the pump method because it is substantially less disruptive to the spaces affected. If it was unfinished space there would be no question other than to go to the way nature (and the dead folk) intended.
The other confirmed challenge is that the other return can not go along a wall. it enters the floor in a room with a large hallway perpendicular to the path between it and the boiler. It is pretty much “islanded” other than going underground or overhead. One of the ceiling radiators ties into this return too so an overhead dry return is out unless that radiator is nixed.
I took a few more photos (there are three risers, Yes, it is welded, Yes, the takeoffs are right above the center riser, No, the steam is not dry!)
I already have dropped the pressuretol to 0.5/1 diff from 2/2 diff and check the pigtails frequently since I am taming 1500MBH of fire. It short cycles on longer runs but things are much more even and quiet and the crumbled returns take much less hammering abuse.
A gaggle of big mouths is in order once these returns are figured out. Right now there are only two Gorton #2’s venting 120’ of 6” / 80’ of 4” main (it reduces to 4” at a level change/drip to finish out the last 80’). I believe the system only heats evenly right now because the venting is primarily happening through the holes in the returns.... if we go with condensate tanks/F&T traps, the traps alone will not be enough venting for this volume (traps peg out at 1.3cfm at 1oz per the awesome venting chart)
The other 3” main is only 70 feet long but the single Gorton #2 is also severely inadequate once the returns are tight. The two Gorton 2’s from the monster main will have a new home there (with some repurposed Hoffman 75 friends on an adjacent nipple)0 -
Since its a wet return, why not use some soft copper along the curving wall. To tame the beast and probably greatly counteract the bad header piping, I'd down fire that boiler substancially. A 3 to 1 downturn is pretty standard on those boilers and you pretty much never need to worry about condensation in the boiler.....its too hot. With the reduced firing rate the water may not even make it up to the header.To learn more about this professional, click here to visit their ad in Find A Contractor.2
-
> @The Steam Whisperer said:
> Since its a wet return, why not use some soft copper along the curving wall. To tame the beast and probably greatly counteract the bad header piping, I'd down fire that boiler substancially. A 3 to 1 downturn is pretty standard on those boilers and you pretty much never need to worry about condensation in the boiler.....its too hot. With the reduced firing rate the water may not even make it up to the header.
Good suggestion on the soft copper (the thought crossed my mind, I have wrassled the stuff in A/C linesets), but is it readily available in greater than 1” diameter as needed here? Also, is copper only acceptable under the boiler water line, or is it also acceptable as the wet portion of a false water line located well above the actual boiler water line?
The mere thought of a 50’ coil of 1 1/2” soft copper makes me giggle.
I have already suggested downfiring to the church council. My concern is that the burner is rated for one input only and is a Gordon Piatt (defunct). Likely a new gas gun would be in order to actually achieve that goal.1 -
The largest I think I've used may have been 1 1/4 inch. It probably fine as long as it under water. We use copper for our header drip, return piping and hartford loop on our smaller installs.
The gas gun may show an input range on the plate. I'd call the boiler manufacturer and look around for suppliers still selling GP parts for additional resources.
My own church had been running a 2,000,00 btu/hr input WEil Mclain LGB with all the standard bad piping typically used with these boilers. The burners all rotted out on one end due to previous leaks and we shut off that half of the boiler. 1,000,000 btu/hr is still a bit big for the system.To learn more about this professional, click here to visit their ad in Find A Contractor.0 -
> @The Steam Whisperer said:
> The largest I think I've used may have been 1 1/4 inch. It probably fine as long as it under water. We use copper for our header drip, return piping and hartford loop on our smaller installs.
>
> The gas gun may show an input range on the plate. I'd call the boiler manufacturer and look around for suppliers still selling GP parts for additional resources.
>
> My own church had been running a 2,000,00 btu/hr input WEil Mclain LGB with all the standard bad piping typically used with these boilers. The burners all rotted out on one end due to previous leaks and we shut off that half of the boiler. 1,000,000 btu/hr is still a bit big for the system.
1 1/4 copper would likely be OK for the ~1000 EDR dripping to this particular return since that is less than 1gpm. I will propose the idea after taking some measurements to put together a comprehensive estimate. Due to the snaking around the rooms it is probably around 150’. If smaller than 1 1/4 is acceptable for this load, that would be wonderful though there is less margin for crud buildup.
Unfortunately the gas gun shows only one input. Max 1527 MBH, Min 1527 MBH. Any downfiring on this would void the listing.0 -
1/1/4 inch is good to 1200 EDR according to the tables. I'd just use the soft for the curved wall section then rigid for the rest.To learn more about this professional, click here to visit their ad in Find A Contractor.0
-
> @The Steam Whisperer said:
> 1/1/4 inch is good to 1200 EDR according to the tables. I'd just use the soft for the curved wall section then rigid for the rest.
The curved wall goes through all three rooms all the way to the boiler room, 80’ or so. The rigid section would only be the other 50’ or so at the corner of the building.
80’ of soft 1 1/4 is about 1/3 the cost of a pump unit alone and keeps it simple and reliable. The feed tank still requires a trap (for now) but at least one pump would be gone. I like it!
I will be there tonight and will measure the exact distances. Not looking forward to knocking holes through those walls, but that’s why Hilti exists.0 -
Did a little more investigation last night.
I discovered some knucleheading on the main return (the return discussed before is more or less a drip from the south indirects and from an elevation change in the large main). Someone back in the 70’s or 80’s ran a separate 3” main to the radiators on the north side of the building and capped off their connections to the large original main. My guess is the end radiators were not heating so they did all this extra work to add a main when better main venting would have fixed it right.
There is a 1 1/2 return (the lower silver-painted pipe) from the end of this “new” main (the upper silver-painted pipe) that ties into the return from the original main (the large pipe at the back) well above the water line (8’). The “short circuit” creates some substantial water hammer in the 2 1/2” return and interferes with venting. This is all a welded mess inside of a wall but the obvious fix is to rip out the wall and get this connection below water.
I also discovered a very crusty hoffman 76 in the wall. Its float likely succumbed to the hammer the day it was installed. There is also a Gorton #2 but it is closing way before it should due to the “short”
I also finalized load calculations for each return last night. The southern return is draining 951 EDR and the end of main return is draining 1249 EDR.0 -
The vote is in. Pump it is (for the far return).
The layout of the building made the gravity solution prohibitive. Nobody liked the wall-hugging pipe idea much other than myself.
That said, I have questions. I have been working with Germans for almost 16 years so I may default to overcomplication...
False water line:
Please correct me if I am in error here. My plan is to pop the 2” wet return up 48” right before its current entry underground with a 2x3/4x2 reducing tee (3/4” is for cleanout/blowdown), add another tee at the top of that 48” vertical for the F&T trap, then a couple more feet of 2” vertical before reducing to 3/4” to the main for the equalizer. The trap will have a wye strainer w/blowdown, isolation gate valves, and a ball valve on the other discharge port for testing.
There will still be 4’ between this water line and the main. I quickly sketched it out on the closest thing laying around when my brain was processing this—an old computer cover in the scrap steel pile. see photo.
Trap sizing: The trap is to handle 236 lbs/hour, with a 1.5 factor applied this is 354 lbs/hour. The hoffman F0115h-4 is a decent match I believe. This is far closer than the two Armstrong 15-B6’s currently at the feed tank at~1600 lb/hour each. Some goofball years ago thought “If one alone exceeds the boiler output, two is better yet, right?!”
Pumped return throttling: what is the best valve style to use here?
Vacuum breaker: I plan to install a vacuum breaker at the ceiling in the boiler room. There is a 10’ drop to the feed tank so the chance of condensate flashing is high. What is the best bet here? There are a couple already installed on the gigantic scrap metal traps that will become available. It seems they are just a spring loaded ball but I have no specs on them. They do crack when I blow into them so the cracking pressure can’t be too high.
As for the other return, I plan to saw the rusted section out in the boiler room and connect a clear vinyl tube to the buried section to give it a static leak check over a prolonged period (once heating season is done). Hopefully it is still OK and has just been sending water to the long/older return that is obviously rotted/visibly leaking. Given some new information, my guess is that it was replaced in 1989 during a renovation so my fingers are crossed. It is a 20’ straight run of 2 1/2” underground. If needed, maybe I could just use it as a “conduit” for a smaller pipe since it is so oversized...0 -
Progress!
Over the summer, the returns were both redone completely.
The “south” return was the condensate pump installation which was not too bad. A 32” waterline was set up to seal the various drips into the old return, a trap was installed at the top, and an equalizer tapped into the main. 130’ of 1” type L copper was run for the run back to the feed tank. This side works wonderfully aside from some condensate backup into one of the ceiling radiators causing a spitting vent (two pipe, air vent, yet some goofball long ago put a trap on it). I am just going to gut or remove the trap as I believe the re-established waterline is locking things up with that trap/creating a vacuum.
Upon testing of the “North” return, it was found to hold absolutely NO water either. 3gpm for 15 minutes into it just disappeared...
This wet return was re-run with 1 1/2” type L copper with a short 8’ segment fed under the floor through the old 2 1/2” pipe. The same waterline/trap/equalizer setup used on the South return was also done for this line, minus the pump. It flows by gravity from the trap to the feed tank.
There was an “unknown since 1989” crawlspace to access most of the “north” return. I did have to tear up a room to access the area, but it was needing work anyhow. The crawlspace is full of dissolved gravel muck from the carbonic acid/70,000 gallon-per-year leak. It is similar in texture to agricultural lime.
Not a fun time under there...but I did figure out the original purpose of the cavity— it was the intake for an old abandoned/capped 6’x3’ brick ventilation shaft that still goes three stories up to the roof, with two small disconnected radiators positioned in the center that (presumably) induced a draft. Cool!
Also discovered was a high-tech pipe support system for the old return: they flopped it on cinder blocks (that later crumbled) rather than taking time to hang it properly. This obviously amplified the already-ridiculous water hammer!
All said and done, one hour of steaming during testing used less than a gallon of water (there are some old steam leaks to fix yet). With the old returns last year, it lost an average of 90 gallons per hour of steaming.. The water level is stable, zero hammer, and no more hot spring under the hallway. I did have to replace the shaft seal on the feed pump since it leaked as soon as it saw hot water for the first time in years.
The only revision to make is the vent on the condensate tank. I want to route it away from the shelving, vent it high at a tee, then drop back to the floor. It is copper at the moment since I had the scraps leftover to make up a temporary condensing stack/vent for testing. Venting is the next tuning step since it was previously vented through the porous returns.
1 -
Also, I am going to redo those awful dhw pipes that interfere with the equalizer pipe before things are started up. They have been hanging like that forever...0
Categories
- All Categories
- 87K THE MAIN WALL
- 3.2K A-C, Heat Pumps & Refrigeration
- 58 Biomass
- 427 Carbon Monoxide Awareness
- 113 Chimneys & Flues
- 2.1K Domestic Hot Water
- 5.7K Gas Heating
- 109 Geothermal
- 161 Indoor-Air Quality
- 3.6K Oil Heating
- 70 Pipe Deterioration
- 995 Plumbing
- 6.3K Radiant Heating
- 391 Solar
- 15.4K Strictly Steam
- 3.4K Thermostats and Controls
- 55 Water Quality
- 44 Industry Classes
- 48 Job Opportunities
- 18 Recall Announcements