Welcome! Here are the website rules, as well as some tips for using this forum.
Need to contact us? Visit https://heatinghelp.com/contact-us/.
Click here to Find a Contractor in your area.
Hole develops in a low-loss header.
Options
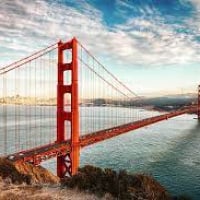
Alan (California Radiant) Forbes
Member Posts: 4,498
Jan. 2016 installation of a Vitodens to replace a Munchkin (hole in the HX); also installed a Viessmann low-loss header (LLH). I get a call this weekend that the LLH spouted a leak of red water; the owner stuck a toothpick in the hole to stop the flow. Viessmann tech. support wants me to test the water.
The tubing is barrier Mr. PEX.
Has anyone experienced this?
The tubing is barrier Mr. PEX.
Has anyone experienced this?
8.33 lbs./gal. x 60 min./hr. x 20°ΔT = 10,000 BTU's/hour
Two btu per sq ft for degree difference for a slab
Two btu per sq ft for degree difference for a slab
0
Comments
-
Looks like the hole is below the weld? If so, rule that out. Be interesting to take a bandsaw and cut the unit in half to see if the metal has been attacked in other areas.
That seems like a short period of time for metal of that thickness to pin hole. If the water was that aggressive I'd think the expansion tank would also show signs of deterioration, maybe?
Any leaks in the system that may be causing frequent fill water to enter? Is it connected to a fill valve?Bob "hot rod" Rohr
trainer for Caleffi NA
Living the hydronic dream1 -
I agree that this sounds like a water quality issue. Was the system flushed and tested when the munchy was replaced?
"If you can't explain it simply, you don't understand it well enough"
Albert Einstein0 -
Sounds like a water chemistry issue. It's possible that it's a manufacturing defect, water testing will tell.0
-
Good call on the x-tank, hr. No leaks in the system that I know of. All the heating is above grade and you would see the leak, but I should check the exposed area below the lower floor. Yes, it's connected to a fill valve.
Zman: We power flushed the loops when the new boiler was installed.
Paul: Yes, we will have the water tested.8.33 lbs./gal. x 60 min./hr. x 20°ΔT = 10,000 BTU's/hour
Two btu per sq ft for degree difference for a slab0 -
Looking at the water in the catch basin makes me think 02 is getting in.0
-
So, further research shows that the tubing has no oxygen barrier. A foolish mistake on my part and I will pay dearly : ) Actually, I'm not smiling at all.
I saw the red tubing and I thought "oxygen barrier". And the system was installed in 2006 by a high end radiant installer and I though surely, they must use barrier tubing. Wrong, wrong, wrong. I have learned my lesson.
There's no room for a heat exchanger and pumps; thinking of a brass or stainless steel hydraulic separator, but don't know if they are available.
Looking for a little help here. Thanks in advance.
8.33 lbs./gal. x 60 min./hr. x 20°ΔT = 10,000 BTU's/hour
Two btu per sq ft for degree difference for a slab0 -
Hydronic conditioner chemical regiment. It will require a yearly test and booster O2 scavengers may be needed.
Run the SWT as low as possible to minimize O2 ingress.Bob "hot rod" Rohr
trainer for Caleffi NA
Living the hydronic dream0 -
Is there an adjacent closet somewhere maybe? Or you could get creative with piping over piping( without covering crucial components)0
-
Instead of a LLH, pipe in a FPHX that's oversized and a SS pump for system. I've used this method numerous times when confronting non-barrier tubing, even on early Viessmann systems, where the installer should have known. Then add conditioning chemicals to system side. I strap the LLH sensor to supply pipe on system side.0
-
Anything that is metal has to be removed, anything, the SS circ is a good idea.
0 -
Here is the Vitodens installation manual, clearly stating not to use non barrier tubing directly with the with the boiler.
Jeffrey Campbell0 -
Alan already clearly said he made a mistake, thought the tubing was O2 barrier.Steve Minnich0
-
I don’t understand how @Alan (California Radiant) Forbes made the mistake. Didn’t the previous installer put the tubing in?2
-
yes, he said " system was installed in 2006 by a high end radiant installer and I though surely, they must use barrier tubing. Wrong, wrong,..."Danny Scully said:I don’t understand how @Alan (California Radiant) Forbes made the mistake. Didn’t the previous installer put the tubing in?
he didn't install the tubing, he assumed they did it right0 -
-
Would installing a Flexcon fiberglass / plastic buffer tank help
Plus adding chemicals and then using SS or brass pumps? Plus running as low as possible water temps.0 -
How about doing it the old fashioned way...Primary/ secondary piping.To learn more about this professional, click here to visit their ad in Find A Contractor.0
-
Here you go.
Install this, power flush and hit the snot out of it w/ Fernox.
https://www.ebay.com/itm/Low-Loss-Header/172494694589?hash=item28297c28bd:g:FYcAAOSwjVVVzBX70 -
the SS LLH will still allow contaminated water to circulate within the boiler.0
-
Don't feel bad, @Alan (California Radiant) Forbes -- if we didn't make mistakes or faulty assumptions now and then we wouldn't be human, and we are. I've made my share...
That said, I I'd really try to figure out a way to put a positive barrier -- a heat exchanger -- between the poor little boiler and the rest of the system...Br. Jamie, osb
Building superintendent/caretaker, 7200 sq. ft. historic house museum with dependencies in New England0 -
Alan, can you fabricate a floor mount support/hanger for a HX and pump, perhaps right in front of shown tubing location. If not the floor, higher up on the wall?0
-
I would think the boiler's heat exchanger is rated for non-barrier tubing...isn't it stainless steel. You'll need to upgrade pumps and accessories, of course.To learn more about this professional, click here to visit their ad in Find A Contractor.1
-
I like kcopp's solution with the SS LLH and some kind of conditioner or O2 scavenger. There will be a primary pump that needs to be replaced as well.
I appreciate all the other comments and suggestions, especially Jamie's who showed me empathy when I needed it. Thanks!8.33 lbs./gal. x 60 min./hr. x 20°ΔT = 10,000 BTU's/hour
Two btu per sq ft for degree difference for a slab0
Categories
- All Categories
- 87K THE MAIN WALL
- 3.2K A-C, Heat Pumps & Refrigeration
- 57 Biomass
- 425 Carbon Monoxide Awareness
- 114 Chimneys & Flues
- 2.1K Domestic Hot Water
- 5.7K Gas Heating
- 106 Geothermal
- 160 Indoor-Air Quality
- 3.6K Oil Heating
- 70 Pipe Deterioration
- 981 Plumbing
- 6.3K Radiant Heating
- 388 Solar
- 15.4K Strictly Steam
- 3.4K Thermostats and Controls
- 54 Water Quality
- 47 Industry Classes
- 48 Job Opportunities
- 18 Recall Announcements