Sweating copper, 2 scenarios, rookie alert
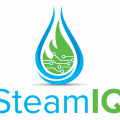
I have sweated plenty of copper, mostly 1/2" & 3/4" variety. I use a MAPP torch, Nokorode flux, and Silvabrite 100 solder. I sand the fittings with emory cloth and the inside with a stainless brush. Recently I've become much more careful about cleanliness and touching the pipe after I clean it.
Most of the time things go great. But most of those times I'm sweating things like air lines for my garage and am using new tube and new fittings, everything is clean and dry, and the position is horizontal etc.
I am redoing a bathroom and I live in an old house. The entire thing is plumbed in copper up to 4" drains. Since the bathroom is gutted I shut off the water to the risers and then bled the pipes back down to the basement. So there should be no water in the pipes. I need to sweat to these stubs coming out of the floor/wall area. Access isn't great but I've had worse. I'm nervous based on past experiences about sweating vertically. Any tips? lower left corner is where the risers come up

My biggest issue over the years is water getting to the joints. I swear I will stuff half a damn loaf of bread in the tube and still get a bad joint. It frustrates me. I have had the same tub of Nokorode for 15 years. I thought maybe it was contaminated so I recently bought a new jar. And new solder.
Situation 2:
The other thing I need to do is unsweat a 3" copper toilet drain. I have a 6" piece of new copper to install and bought a new brass deep seal closet flange ring. I would like to sweat in the copper riser while I have everything exposed and before subfloor goes in. My assumption is that a MAPP torch may not be hot enough? I do have an oxy acetylene rig with a rosebud lol...might be a little heavy carrying up the stairs.
From what I read using lead bearing solder is the way to go. Cut pipe, slip on closet ring. Hammer pipe to ring to flare it. Solder with bearing solder which I just procured a 1 lb roll of 50/50 Kester. I assume I could flux with Nokorode?

I've never done this before so would appreciate advice as well.
Mainly I've been dealing with subpar joists and getting those back up to snuff. This entire house is just one big puzzle. I was particularly pleased with how I manage to get my shower drain plumbed and drew out the locations of the holes in the blocking in CAD. It's bad when you have a pseudo machinist doing home construction projects and he brings his Mitutoyo calipers to the job site lol

SteamIQ
Comments
-
The easiest thing may be to transition to pex and PVC.Bob Boan
You can choose to do what you want, but you cannot choose the consequences.0 -
Some of that wood looks like the place I care for. In which case, it has a dismayingly low char/ignition temperature. I use one of the fancy electric rigs for 1/2 inch and 3/4 inch -- Pipemaster Pro (try Amazon) when I absolutely have to work near the stuff. If you do decide to use a torch, like on the bigger stuff, be really really careful. Use an asbestos or other flame deflector. Make sure the flame or hot gas can't get into any out of the way nooks and crannies. Have a bucket of water and rags handy. And whatever else -- do not leave the area until you are completely certain that everything is cool!
I don't mean to sound paranoid... but I am!Br. Jamie, osb
Building superintendent/caretaker, 7200 sq. ft. historic house museum with dependencies in New England0 -
For the water lines or toilet? Or both?Ironman said:The easiest thing may be to transition to pex and PVC.
My gut tells me that the copper toilet deal is the best repair and than a Fernco isn't the best idea. Would certainly be easier. What are your thoughts on that?
I did cut out the copper shower drain because I had to add in blocking between beams and the previous configuration did not allow that. For that drain I transitioned from copper to PVC using a Fernco.
I guess that I'm essentially doing the same thing with toilet.
I don't have any PEX tools, not opposed to getting the right tool but this is probably the sum total of the job, running a line for the toilet supply, H&C for vanity and for shower. Sweating in that part doesn't make me nervous, it's the dang vertical connection to the existing pipe. I used a sharkbite recently in a fit of frustration trying to solder into wet pipes and I have to say it worked awesome. But it was in the basement and visible. These pipes are going to be buried between tile floor and a mortar ceiling so it would be a huge pain to repair
Peter Owens
SteamIQ0 -
I hear you Jamie. I'm nervous about fire as well and I respect the old timbers. It is very very dry I can attest to that. My usual routine is to fill up a spray bottle with water. I put some heavy gauge aluminum plate behind the joint to keep the flame off.Jamie Hall said:Some of that wood looks like the place I care for. In which case, it has a dismayingly low char/ignition temperature. I use one of the fancy electric rigs for 1/2 inch and 3/4 inch -- Pipemaster Pro (try Amazon) when I absolutely have to work near the stuff. If you do decide to use a torch, like on the bigger stuff, be really really careful. Use an asbestos or other flame deflector. Make sure the flame or hot gas can't get into any out of the way nooks and crannies. Have a bucket of water and rags handy. And whatever else -- do not leave the area until you are completely certain that everything is cool!
I don't mean to sound paranoid... but I am!
After I'm done and the joint is cool I spray water over the entire area and soak the wood.
Appreciate the words of cautionPeter Owens
SteamIQ0 -
Keep a spray bottle and perhaps even a bucket of water near by when soldering. I always do, just because the water is off and you really never know.
For water in pipes, I always take the torch and heat the pipe a few feet from where my joint is and slowly work my way back to the joint, this drives any water out of the pipe. Do this immediately before fluxing the joint.Single pipe 392sqft system with an EG-40 rated for 325sqft and it's silent and balanced at all times.
1 -
Nu-Calgon Thermo-Trap comes in a quart spray bottle. I use to protect AC valves while brazing 15% solder for lineset. (Red hot copper to make it flow). I use it for plumbing soldering around wood. Thick and clings to things. Wash away with Water.
There are "No Hub" Fernco type couplings for DWV that are specifically sized for copper to PVC.....great connection.
Fernco are a little big for the copper side.0 -
I bought some Ferncos from supplyhouse that were specific sized to go from copper to PVC. Just installed one last night on my shower drain. The fit was perfect.
I don't know why but I'm somehow leary of the Fernco on the toilet. Maybe it's my preconceived notion that I should have 100% copper. It would surely be way easier. I just want to make sure it's done right even if it means doing more work. I also really don't want a leak especially since I don't know how I would test it once I sweated the joint.
The last time I had an issue was on the run in the basement to these risers for H&C water. It was the weekend of AFC championship game and my wife had invited a bunch of people over. So like an idiot I decide an hour before the game is the perfect time to sweat in some new ball valves because I was concerned the old valves weren't sealing. Shut the water off at the main, drain as best I can. Torch empty pipe to drive off water. Stuff bread in pipe. sweat in new valves (opened).ChrisJ said:Keep a spray bottle and perhaps even a bucket of water near by when soldering. I always do, just because the water is off and you really never know.
For water in pipes, I always take the torch and heat the pipe a few feet from where my joint is and slowly work my way back to the joint, this drives any water out of the pipe. Do this immediately before fluxing the joint.
Turn on water, leaks. Cut it out do it again. 30 minutes to game time. Leaks again, get frustrated. Try one more time, only one leaks, then I see the other weeping. Say $%^ it and go to Home Depot and buy 2 Sharkbites. Job done lolPeter Owens
SteamIQ0 -
I'd have no problem using the correct Fernco: we bury them in concrete and directly in the earth.Sailah said:
For the water lines or toilet? Or both?Ironman said:The easiest thing may be to transition to pex and PVC.
My gut tells me that the copper toilet deal is the best repair and than a Fernco isn't the best idea. Would certainly be easier. What are your thoughts on that?
I did cut out the copper shower drain because I had to add in blocking between beams and the previous configuration did not allow that. For that drain I transitioned from copper to PVC using a Fernco.
I guess that I'm essentially doing the same thing with toilet.
I don't have any PEX tools, not opposed to getting the right tool but this is probably the sum total of the job, running a line for the toilet supply, H&C for vanity and for shower. Sweating in that part doesn't make me nervous, it's the dang vertical connection to the existing pipe. I used a sharkbite recently in a fit of frustration trying to solder into wet pipes and I have to say it worked awesome. But it was in the basement and visible. These pipes are going to be buried between tile floor and a mortar ceiling so it would be a huge pain to repair
As far as the Sharkbite goes, I'm like you: I'd don't like the idea of concealing it even though it's approved to do so.
ProPress fittings would be your best option for the potable stuff. Ferguson and Hajoca supply will rent the tool per day around here. Check some of your local suppliers.
Bob Boan
You can choose to do what you want, but you cannot choose the consequences.0 -
The issue is, like anything else soldering is an art and over time you learn things with practice, like how hot to get it, when to stop heating etc. Get it too hot and the solder thins out too much or you burn your flux.Sailah said:I bought some Ferncos from supplyhouse that were specific sized to go from copper to PVC. Just installed one last night on my shower drain. The fit was perfect.
I don't know why but I'm somehow leary of the Fernco on the toilet. Maybe it's my preconceived notion that I should have 100% copper. It would surely be way easier. I just want to make sure it's done right even if it means doing more work. I also really don't want a leak especially since I don't know how I would test it once I sweated the joint.
The last time I had an issue was on the run in the basement to these risers for H&C water. It was the weekend of AFC championship game and my wife had invited a bunch of people over. So like an idiot I decide an hour before the game is the perfect time to sweat in some new ball valves because I was concerned the old valves weren't sealing. Shut the water off at the main, drain as best I can. Torch empty pipe to drive off water. Stuff bread in pipe. sweat in new valves (opened).ChrisJ said:Keep a spray bottle and perhaps even a bucket of water near by when soldering. I always do, just because the water is off and you really never know.
For water in pipes, I always take the torch and heat the pipe a few feet from where my joint is and slowly work my way back to the joint, this drives any water out of the pipe. Do this immediately before fluxing the joint.
Turn on water, leaks. Cut it out do it again. 30 minutes to game time. Leaks again, get frustrated. Try one more time, only one leaks, then I see the other weeping. Say $%^ it and go to Home Depot and buy 2 Sharkbites. Job done lol
I doubt there's anyone that solders pipe that hasn't been where you were at least one time in their life. After the first leak you're frustrated, now you're rushing and annoyed so you make mistakes, that leaks, now it's even worse etc.
Kinda like my 5" hole that ended up 5 1/2" in the wall over the weekend.Cut perfectly round, but, too big.
Single pipe 392sqft system with an EG-40 rated for 325sqft and it's silent and balanced at all times.
1 -
Interesting about the Fernco. So in my situation you'd cut the branch as it comes from the soil stack and put the fernco there and then everything else is PVC? Man I just bought all the supplies for the darn brass job lol.Ironman said:
I'd have no problem using the correct Fernco: we bury them in concrete and directly in the earth.
As far as the Sharkbite goes, I'm like you: I'd don't like the idea of concealing it even though it's approved to do so.
ProPress fittings would be your best option for the potable stuff. Ferguson and Hajoca supply will rent the tool per day around here. Check some of your local suppliers.
Re ProPress, I just called my local FW Webb branch and they rent the pro press tool. I like that idea a lot thanks would never have considered it.
I really enjoy sweating the copper pipe it's just this one area I don't have a lot of room for mistakes and if a fancy rental tool makes the job a simple one I'm all for it. I hope I have enough room for the tool to swing in there I'll need to check tonight.
Thanks I come in here asking for help sweating copper and now I'm renting fancy tools and using a rubber seal on the poop tube
Peter Owens
SteamIQ1 -
The trick to sweating a vertical pipe up hill is not to use too much heat and keep the heat up high on the fitting The solder will flow towards the heat so if your heat isn't above the solder the solder will run down the pipe and make a mess. You can solder the whole fitting at once or step your way around the fitting by pulling the torch away and then reapplying heat
Practice on some scrap with some 1/2" fittings.
Everyone here will think I am nuts but I stay away from turbo torch style tips especially in a tight spot.
Nokorode is the best flux in my opinion. Keep a spray bottle handy0 -
I don't think you're nuts, but I'm a bit baffled by this comment.EBEBRATT-Ed said:The trick to sweating a vertical pipe up hill is not to use too much heat and keep the heat up high on the fitting The solder will flow towards the heat so if your heat isn't above the solder the solder will run down the pipe and make a mess. You can solder the whole fitting at once or step your way around the fitting by pulling the torch away and then reapplying heat
Practice on some scrap with some 1/2" fittings.
Everyone here will think I am nuts but I stay away from turbo torch style tips especially in a tight spot.
Nokorode is the best flux in my opinion. Keep a spray bottle handy
Turbo torch swirl tips produce a hotter, but smaller flame. I find the smaller flame much more suitable for tight spots.
Single pipe 392sqft system with an EG-40 rated for 325sqft and it's silent and balanced at all times.
2 -
@ChrisJ , I just prefer the old "prestolite tips" maybe because I am old and so are they. I hate the turbo torch screeching and the fact that you can't throttling them without the tip burning red. Sometimes in a tight spot you can't maneuver fast so less heat is better IMHO.
But on larger tubing or brazing or outside in the wind out comes the turbo0 -
Well I think I've formulated a plan. In my buying spree a month ago I had already ordered a Fernco for the toilet line, and in the same order I ordered the brass closet flange. Nothing like hedging your bets I suppose.
I'll work on getting that plumbed in.
For the water lines I decided why not let an opportunity allow for playing with fun tools. I ordered the pro press fittings in all sorts of configurations and will rent the tool from Webb this weekend. Will be fun trying to figure it all out. I checked and I should have enough stickout from below to fit the tool between the joists.
Thanks I'll post some pics next summer when I've finally made some progress.Peter Owens
SteamIQ1 -
Drop down to a #2 tip.EBEBRATT-Ed said:@ChrisJ , I just prefer the old "prestolite tips" maybe because I am old and so are they. I hate the turbo torch screeching and the fact that you can't throttling them without the tip burning red. Sometimes in a tight spot you can't maneuver fast so less heat is better IMHO.
But on larger tubing or brazing or outside in the wind out comes the turbo
No problems.
The loud howling lets you know it's working.
All joking aside, I think ear protection is important with turbo torch tips.Single pipe 392sqft system with an EG-40 rated for 325sqft and it's silent and balanced at all times.
0 -
Sailah said:
Well I think I've formulated a plan. In my buying spree a month ago I had already ordered a Fernco for the toilet line, and in the same order I ordered the brass closet flange. Nothing like hedging your bets I suppose.
I'll work on getting that plumbed in.
For the water lines I decided why not let an opportunity allow for playing with fun tools. I ordered the pro press fittings in all sorts of configurations and will rent the tool from Webb this weekend. Will be fun trying to figure it all out. I checked and I should have enough stickout from below to fit the tool between the joists.
Thanks I'll post some pics next summer when I've finally made some progress.
Single pipe 392sqft system with an EG-40 rated for 325sqft and it's silent and balanced at all times.
0 -
Sweating 2 in and over you should tin them first....use 50 50 solder sticks.. Had some tight quarter soldering over the years, I actually had to hire a fire department detail...It was mostly in the city areas....like the north end in Boston0
-
Have to be honest, how do you tin them and them still get the fitting to fit over the pipe?j a said:Sweating 2 in and over you should tin them first....use 50 50 solder sticks.. Had some tight quarter soldering over the years, I actually had to hire a fire department detail...It was mostly in the city areas....like the north end in Boston
Single pipe 392sqft system with an EG-40 rated for 325sqft and it's silent and balanced at all times.
0 -
Hey feel free to come on over this weekend and sweat the joints for meChrisJ said:. in my mind I could foresee disaster trying to do all that work and water coming through our dining room plaster ceiling if I made a mistake.
I'm man enough to admit in this area I don't have the requisite skills. I would feel bad having a plumber come over and sweat 2 things.
I sweated about 125' of 3/4" copper a few months ago plumbing my barn for my big 80gal compressor. That sweating I like. Nice clean copper. Old copper with bad consequences just makes me nervous.
Peter Owens
SteamIQ1 -
I'm right down the street if you want to dust off the old solder sticks. Then @ChrisJ won't feel so hurt.j a said:Sweating 2 in and over you should tin them first....use 50 50 solder sticks.. Had some tight quarter soldering over the years, I actually had to hire a fire department detail...It was mostly in the city areas....like the north end in Boston
Peter Owens
SteamIQ1 -
Sailah said:
Hey feel free to come on over this weekend and sweat the joints for meChrisJ said:. in my mind I could foresee disaster trying to do all that work and water coming through our dining room plaster ceiling if I made a mistake.
I'm man enough to admit in this area I don't have the requisite skills. I would feel bad having a plumber come over and sweat 2 things.
I sweated about 125' of 3/4" copper a few months ago plumbing my barn for my big 80gal compressor. That sweating I like. Nice clean copper. Old copper with bad consequences just makes me nervous.
This coming weekend I need to be in the attic again vacuuming up 150 years worth of dust and garbage and trying to hang an air handler.
Working in your basement sounds a lot better so can we swap?Single pipe 392sqft system with an EG-40 rated for 325sqft and it's silent and balanced at all times.
0 -
I took 8 years off my life vacuuming up concrete dust from demolishing the mud wall shower.
I'm glad my daughter is only 8 (this is her bathroom) and she adores her daddy. If she were 16 and acting like I did when I was 16 I'd probably be telling her to go outside and use the darn hose.Peter Owens
SteamIQ1 -
@ChrisJ , tinning, clean flux and solder the tubing wipe it with a rag while hot, don't get burnt. Picture un sweating and old joint, pulling the fitting off and wipe the tubing so you can put a new fitting on and sweat it-1
-
ChrisJ said:
Have to be honest, how do you tin them and them still get the fitting to fit over the pipe?j a said:Sweating 2 in and over you should tin them first....use 50 50 solder sticks.. Had some tight quarter soldering over the years, I actually had to hire a fire department detail...It was mostly in the city areas....like the north end in Boston
Have to be honest....as well...Its a standard procedure and works well....ChrisJ said:
Have to be honest, how do you tin them and them still get the fitting to fit over the pipe?j a said:Sweating 2 in and over you should tin them first....use 50 50 solder sticks.. Had some tight quarter soldering over the years, I actually had to hire a fire department detail...It was mostly in the city areas....like the north end in Boston
0 -
Practice, practice, practice. Use the right torch tip. Manufacturer's have all kinds of good information for that.
If something nearby can burn, cover it with something wet or can't burn. Preferably both. I use 16 gauge plates on top or in front of wet rags in the tightest places. I use only the plates when I'm not in defcon 1.Steve Minnich0 -
Well I want to thank everyone for the encouragement.
I had bought a bunch of propress fittings in anticipation of the big day. Well that day was yesterday, and today. And I had forgotten to rent the tool. I actually enjoy sweating pipe and it was bothering me that I had gotten beaten down by a couple bad experiences.
I basically piped everything as I wanted it, got the shower roughed in, stubs for vanity, toilet. Put valves on and crossed my fingers.
No leaks!
The vertical section I was so nervous about went well.
I was meticulous about cleaning everything well, not touching the pipe after cleaning, wiping off excess flux etc. I can't say I'll ever make a living doing it but I was well pleased at the results. And managed to not set anything on fire which is always a plus.
I also had a good experience with the Ferncos and got all the drains done in PVC including the toilet. I have the shower vent left to connect but that will require going into the attic for another day.
Thanks
Peter Owens
SteamIQ2 -
Congratulations! Anticipation is always (OR USUALLY) the worse part of most jobs.0
-
-
on my past life I was a remodeling and new construction plumber, that toilet line-- I'd have to see how much free room was below that pipe before attempting to un-sweat that and sweat in a new joint. Most definitely not beginner stuff
Yes 50-50, silly to use anything esle on dwv.
Any yes to the spray bottle, I've kinda winced at some guys over the years spraying areas when it wasn't dangerous or even tight space, but when it comes to being within a couple inches of old wood, you need to be able to wet the wood and spray out the occasional flare up or wood that is starting to smoke.
Vertical soldering, yes it just takes practice. Not too much heat, you need to spread the heat around more so. Too little heat you're gonna be temped to 'blob' on the solder, too much heat you fry the flux.
I recall doing some "off the wall, never do that again stuff" in my late teens at a hospital remodel. I literally batted out a fire with my bare hand, I thought my heart was gonna jump out of my throat. Hard to explain, the fire was 'above' my solder joint and it was hard to reach.
0
Categories
- All Categories
- 87K THE MAIN WALL
- 3.2K A-C, Heat Pumps & Refrigeration
- 57 Biomass
- 425 Carbon Monoxide Awareness
- 116 Chimneys & Flues
- 2.1K Domestic Hot Water
- 5.7K Gas Heating
- 109 Geothermal
- 160 Indoor-Air Quality
- 3.6K Oil Heating
- 70 Pipe Deterioration
- 986 Plumbing
- 6.3K Radiant Heating
- 389 Solar
- 15.4K Strictly Steam
- 3.4K Thermostats and Controls
- 54 Water Quality
- 44 Industry Classes
- 48 Job Opportunities
- 18 Recall Announcements