Cool 1950's Control

Anyway, right about now I'm wishing it was still there.
Anyone ever see this before? Seems like residential steam units have actually lost ground with respect to control in the 60 years since this was produced. Anyway, since I am still running the very model pictured here it is clear that these folks knew what they were doing when they manufactured it.
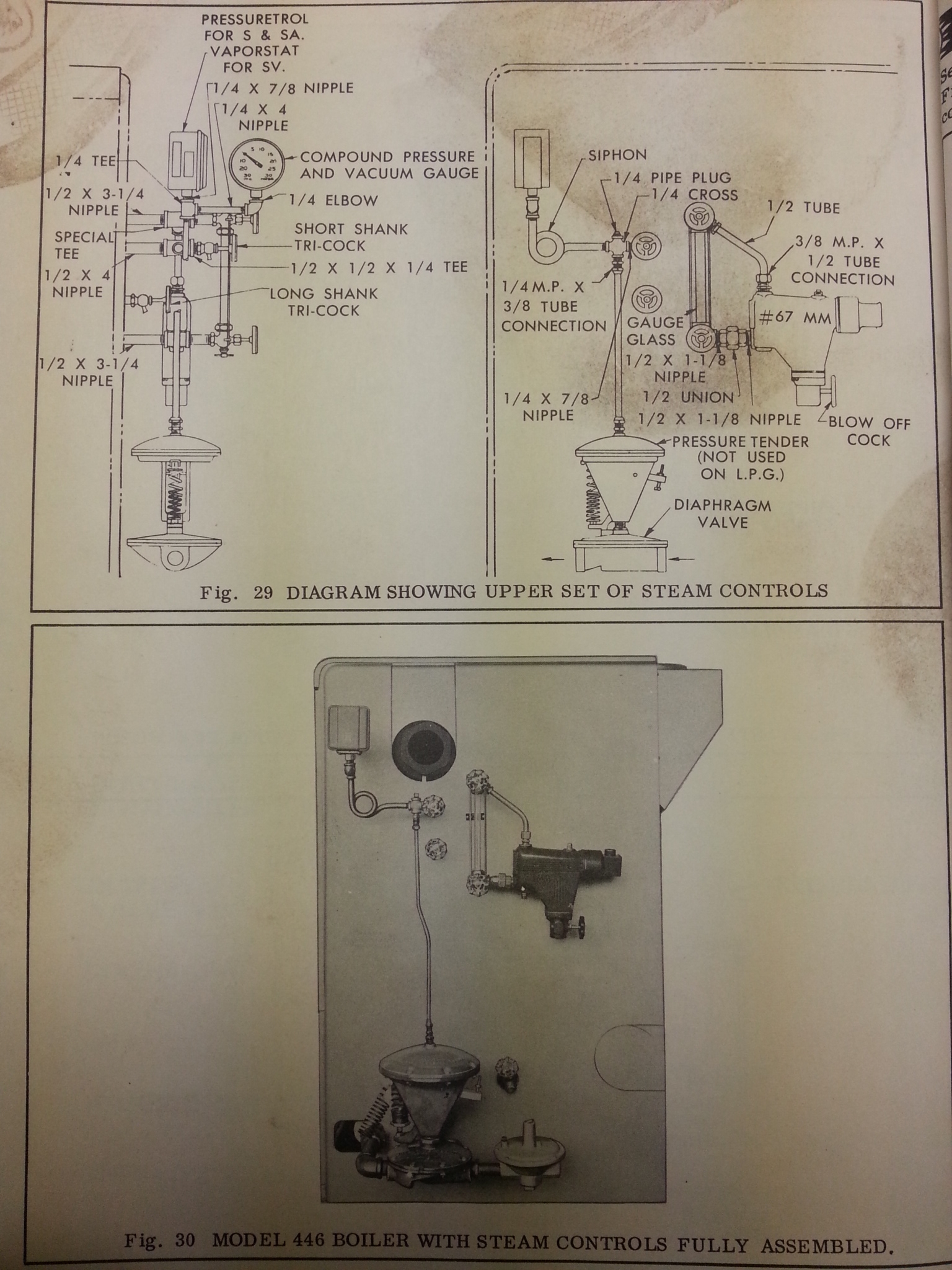
Comments
-
Amazing! I'll bet it took real skill to set that up right.0
-
Yes that is a Bryant gas actuated valve which could be a straight on/off valve or could be a throttling type control. The Bryant valves could actually have the diaphragm changed in the field. Way back when I was working for the gas company we carried the diaphragms in our trucks in a lubricated packet. They were leather and had to be kept lubricated. There was also a kit with three springs for determining different inputs based on steam pressure changes. When a call for heat was initiated it would fire on full fire and as the steam pressure increased depending on the springs it would throttle down in a sense operating as a high fire low fire burner. When these would fail we converted them to powerpile self generating systems, still giving the customer a system that worked with out a need for 120 volt/24 voltage.5
-
Great. Thanks for the info Tim. I notice the gauge pictured is compound and just happens to be shown in vacuum. Would that just have been a standard gauge back then or was this control possibly used where there was some vacuum also?Tim McElwain said:Yes that is a Bryant gas actuated valve which could be a straight on/off valve or could be a throttling type control. The Bryant valves could actually have the diaphragm changed in the field. Way back when I was working for the gas company we carried the diaphragms in our trucks in a lubricated packet. They were leather and had to be kept lubricated. There was also a kit with three springs for determining different inputs based on steam pressure changes. When a call for heat was initiated it would fire on full fire and as the steam pressure increased depending on the springs it would throttle down in a sense operating as a high fire low fire burner. When these would fail we converted them to powerpile self generating systems, still giving the customer a system that worked with out a need for 120 volt/24 voltage.
1926 1000EDR Mouat 2 pipe vapor system,1957 Bryant Boiler 463,000 BTU input, Natural vacuum operation with single solenoid vent, Custom PLC control0 -
here is the patent if your interested. Its in Dan's museum section.
https://heatinghelp.com/heating-museum/bryant-pressure-tender/gwgillplumbingandheating.com
Serving Cleveland's eastern suburbs from Cleveland Heights down to Cuyahoga Falls.3 -
Thanks for this Gerry. Very interesting.gerry gill said:here is the patent if your interested. Its in Dan's museum section.
https://heatinghelp.com/heating-museum/bryant-pressure-tender/1926 1000EDR Mouat 2 pipe vapor system,1957 Bryant Boiler 463,000 BTU input, Natural vacuum operation with single solenoid vent, Custom PLC control0 -
What is the safety on this to keep it from trying to fire with the pilot not lit? Was there just a conventional milivolt valve ahead of it either powered with a thermopile or a 24 v with a thermocouple switch?0
-
Digging way back into the gray area of my brain I remember these control systems. The one shown is not actually a "gas actuated control" but instead is a modulating gas valve that controls the gas input using steam pressure. When these devices were used there was a back-up gas valve that was controlled by the thermostat and the 24 volt safety devices in series with that gas valve. I do not know who made the Bryant valve but I have seen this same type valve made by "Detroit Lubricator" and "General Controls". The Detroit valve was usually for residential boilers and I have seen and serviced quite a few of the General Controls on large residential and commercial boilers with pipe sizes through 4". Most of these modulators were on boilers for schools and a few were even used on high pressure boilers up to about 500 HP or around about 21,000,000 BTU input. As to the "gas actuated controls" the difference between them and the one shown is that the gas pressure opened and closed the gas valve, with control tubing running through the safety pilot, pressure controls, low water cut off, and thermostat controlled solenoid valve. The gas pressure was directed to the underside of the diaphram to open the gas valve and to the top of the diaphram to close the gas valve. In the case of a power failure there may be a solenoid by-pass tube to run around that solenoid for manual boiler operation. I only saw these gas actuated devices on residential boilers2
-
> @mattmia2 said:
> What is the safety on this to keep it from trying to fire with the pilot not lit? Was there just a conventional milivolt valve ahead of it either powered with a thermopile or a 24 v with a thermocouple switch?
On my model 446 I still run the original standing pilot with bi-metal strip safety in series with the 24V controls.1926 1000EDR Mouat 2 pipe vapor system,1957 Bryant Boiler 463,000 BTU input, Natural vacuum operation with single solenoid vent, Custom PLC control1 -
We are warned not to ever attempt to downfire our oversized boilers, and yet this mechanism did just that on a minute-by-minute basis, right?
Did the combustion just go to hell and back during these adjustments? And there was no way to see it in the many decades before combustion analyzers so no one cared?NJ Steam Homeowner.
Free NJ and remote steam advice: https://heatinghelp.com/find-a-contractor/detail/new-jersey-steam-help/
See my sight glass boiler videos: https://bit.ly/3sZW1el1 -
The only ones that know that are the ones that designed it.ethicalpaul said:We are warned not to ever attempt to downfire our oversized boilers, and yet this mechanism did just that on a minute-by-minute basis, right?
Did the combustion just go to hell and back during these adjustments? And there was no way to see it in the many decades before combustion analyzers so no one cared?
You can downfire your boiler if you want, but it will take a lot of time and experimenting all while understanding what is happening and why. If a company engineers a boiler they can see how it responds etc and design it so it can work under many conditions.
If you just go and downfire your atmospheric boiler, no one has any idea what it's going to do. It's not a simple "Yeah just turn this knob and this will happen". No one knows.
In general, I do not believe combustion goes to hell and back. Your excess O2 goes up the more you downfire meaning efficiency drops. To know how much takes testing. I'm sure you also need to make sure the pressure is high enough that the burner won't blow out from a breeze, and that it will light properly repeatedly at that pressure etc.
I'm sure it can be done.
But I'm also sure it's outside of my ability.Single pipe 392sqft system with an EG-40 rated for 325sqft and it's silent and balanced at all times.
1 -
Now that digital control is so much easier today I think downfiring or modulation at the residential level is a waste of money and the source of needless worry. Have it tuned on one speed somewhere near max as the manufacturer intended. All that is needed is a control that produces a few more cycles and limits straight run times so that the system never sees any pressure. 2 cycles per hour +/- gets this done easily with any size boiler. Astounding really that no simple control for this has been developed by now.
I've been working on it. I ran the following control this year and was quite happy with it:
One temp switch at the feed pipe of the last rad in the system to get steam on cold start. Run every burn until that sensor sees steam plus an adjustable delay off amount. This way all degrees of cold start get to the same partial fill level on the first burn of a call. Start all new burns within the same call after that when that same sensor opens back up plus an adjustable delay on amount. Cycles then adjust themselves to conditions. Burn times/wait times change on their own with the demand. When steam is condensing faster in colder weather burn times take a little longer to satisfy that sensor and wait times are a little shorter because steam is condensed faster and that sensor opens up a little sooner. Net burn time to total time adjusts itself. Between those two timers you can find a nice place that extends calls, has zero pressure and evens out the heat while surely covering design day. I bobbled around 2 to 2.5 cycles per hour all winter. I haven't touched anything since before Christmas.
I run it with a PLC because wiring and adjusting is a ton easier. Could be hardwired though with actual delay off/on timer. Very happy with it. Real simple.
1926 1000EDR Mouat 2 pipe vapor system,1957 Bryant Boiler 463,000 BTU input, Natural vacuum operation with single solenoid vent, Custom PLC control2 -
These modulating gas valves worked on power burners like the Power Flame, Metler, Auburn, and almost any industrial old style burner since most of these gas valves had a linkage kit to control the combustion air and additional controls to control the overfire draft. However, I could never get these devices to work properly on any of the atmospheric sectional boilers that we called "underfired units". On this type unit, when you reduced the gas input pressure you would also reduce the primary air through the burner venturi and the flame would get lazy and have a tendency to cause the flame to soot the boiler sections. At the lower input, the excess secondary air would not clean-up the now " dirty flame" and sooting of the boiler sections would was guaranteed. I saw this attempt to reduce the boiler's input used on a large boiler in an elementary school. The boiler's input was 5,000,000 BTU of nat gas and what a job it was to clean that unit. After the second cleaning of the sections the boiler was returned to it's original design and everything went back to normal. I tried to explain to the "engineer" at the company why this attempt at lowering the input would not work but he knew more than I did.1
-
I found remnants of one on a B-Line gas boiler (division of Bryant). What was significant was that, in this instance, a 1/4” gas line ran from the manifold to a diaphragm actuator that controlled the secondary air on an otherwise atmospheric boiler. The base was sealed and there were dampers at the back of the base. Primary air was not modulating through protruding traditional air shutters on each venturi.
As originally equipped, when the steam came up the gas went down and so did the secondary air. Full modulation. Even though there was a draft hood on the outlet.
That 1929 B-Line provided the highest efficiency number my UEI combustion analyzer ever showed on a steam boiler. It finally leaked at the water line (at the age of 82) and Gerry Gill replaced it with a nice peerless. Fuel consumption per degree day stayed virtually the same. One of those instances where the 80 year old was more than competitive with new stuff.
On Bryant’s boilers of that time (say 1930) like the “No-Toil” that could be equipped with the Bryant heat tender, the burner area was pretty conventional but the draft hood was a convoluted affair with a wavy iron impediment to the flue gas flow. I forget now what it was called but it was intended to control excess air. It would be adjusted based on the number of sections if I recall correctly. That Bryant No-Toil was the same vintage as the B-Line above and had nearly as excellent combustion analyzer derived efficiency numbers. We’re talking around 84.5% to 85%.
If I can find my old photos of either boilers and the printouts I’ll post them.Terry T
steam; proportioned minitube; trapless; jet pump return; vac vent. New Yorker CGS30C
3
Categories
- All Categories
- 87K THE MAIN WALL
- 3.2K A-C, Heat Pumps & Refrigeration
- 58 Biomass
- 426 Carbon Monoxide Awareness
- 116 Chimneys & Flues
- 2.1K Domestic Hot Water
- 5.7K Gas Heating
- 109 Geothermal
- 160 Indoor-Air Quality
- 3.6K Oil Heating
- 70 Pipe Deterioration
- 994 Plumbing
- 6.3K Radiant Heating
- 389 Solar
- 15.4K Strictly Steam
- 3.4K Thermostats and Controls
- 54 Water Quality
- 44 Industry Classes
- 48 Job Opportunities
- 18 Recall Announcements