Expansion tank/ Re Piping questions

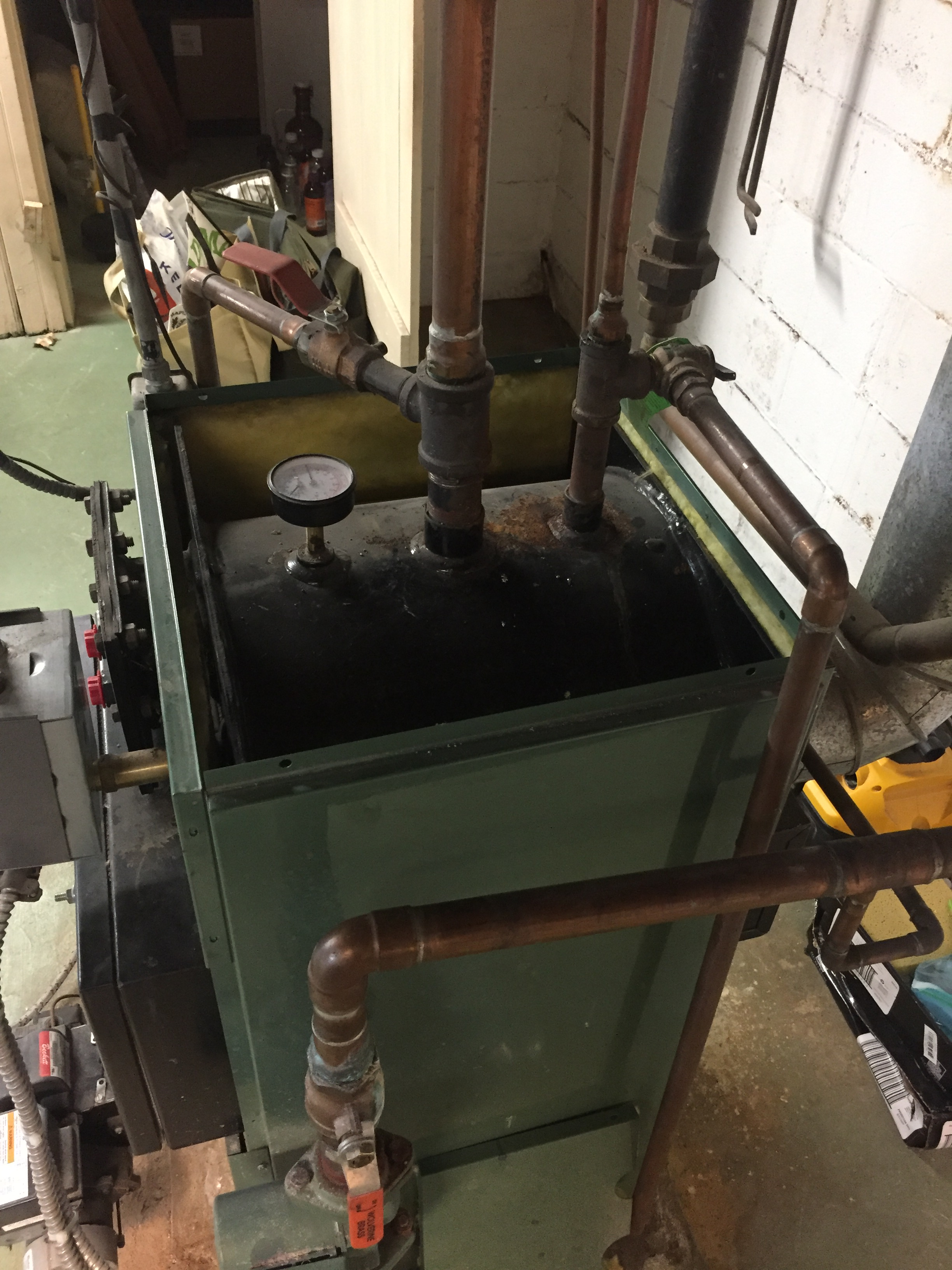
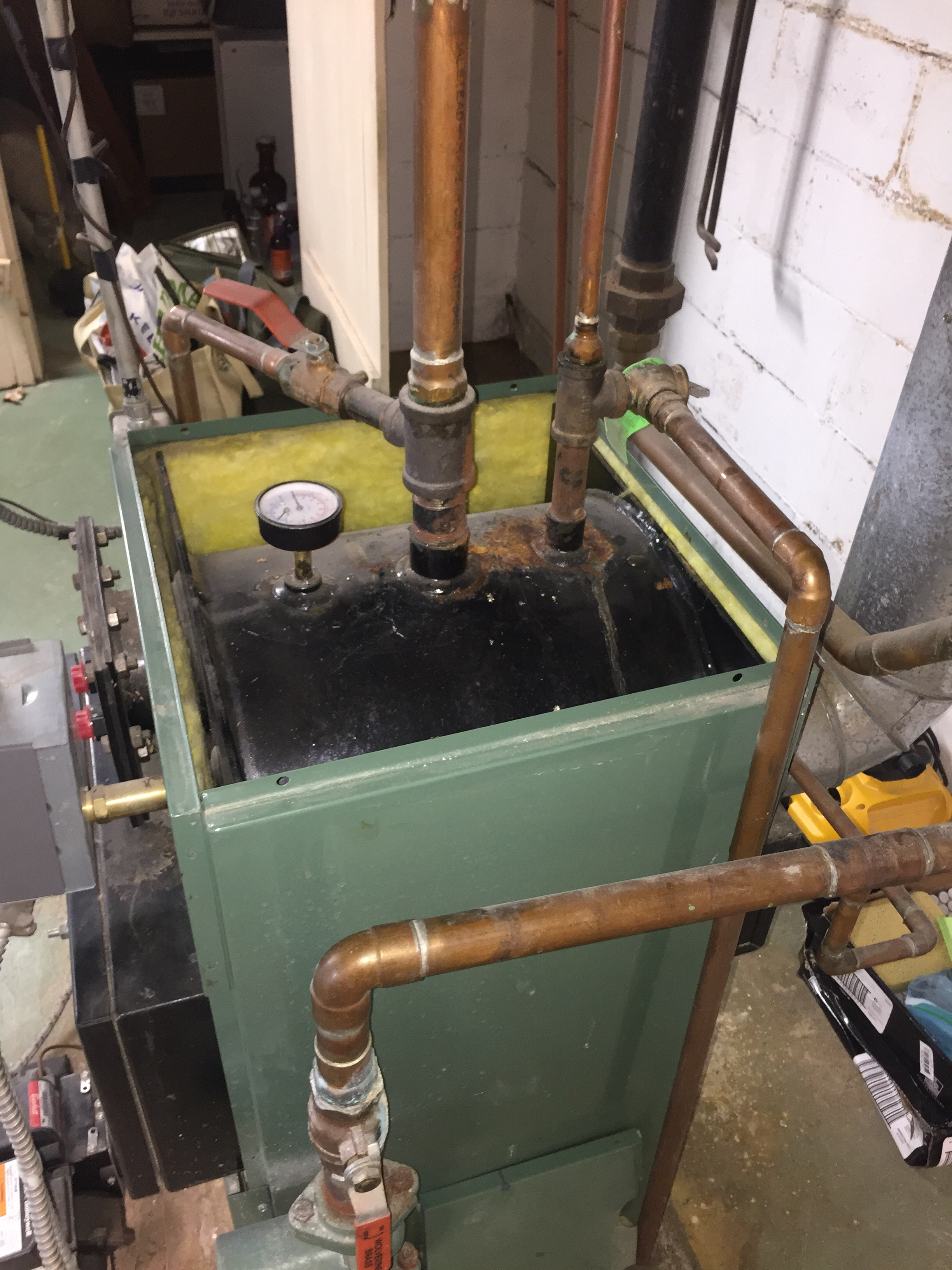
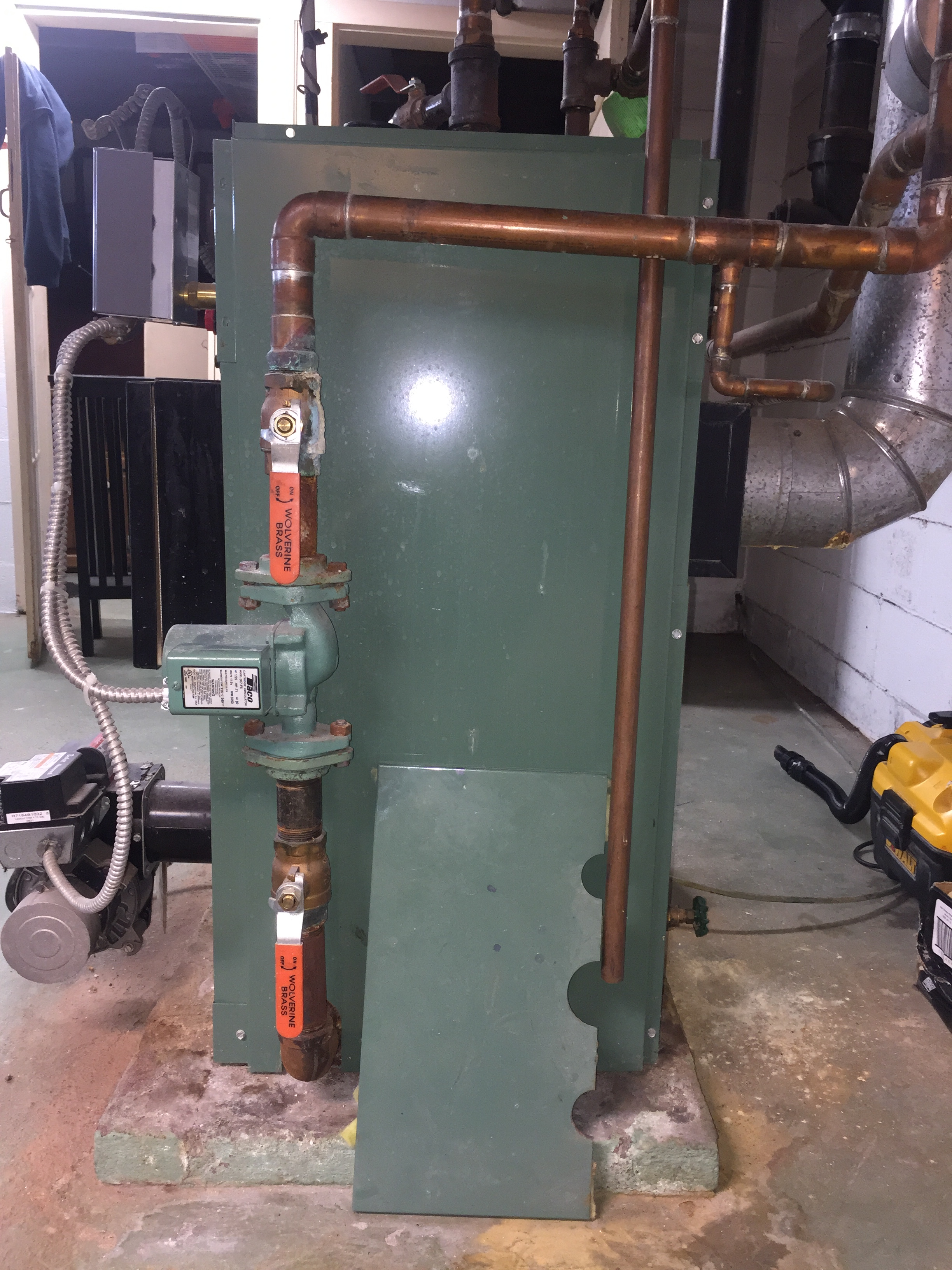
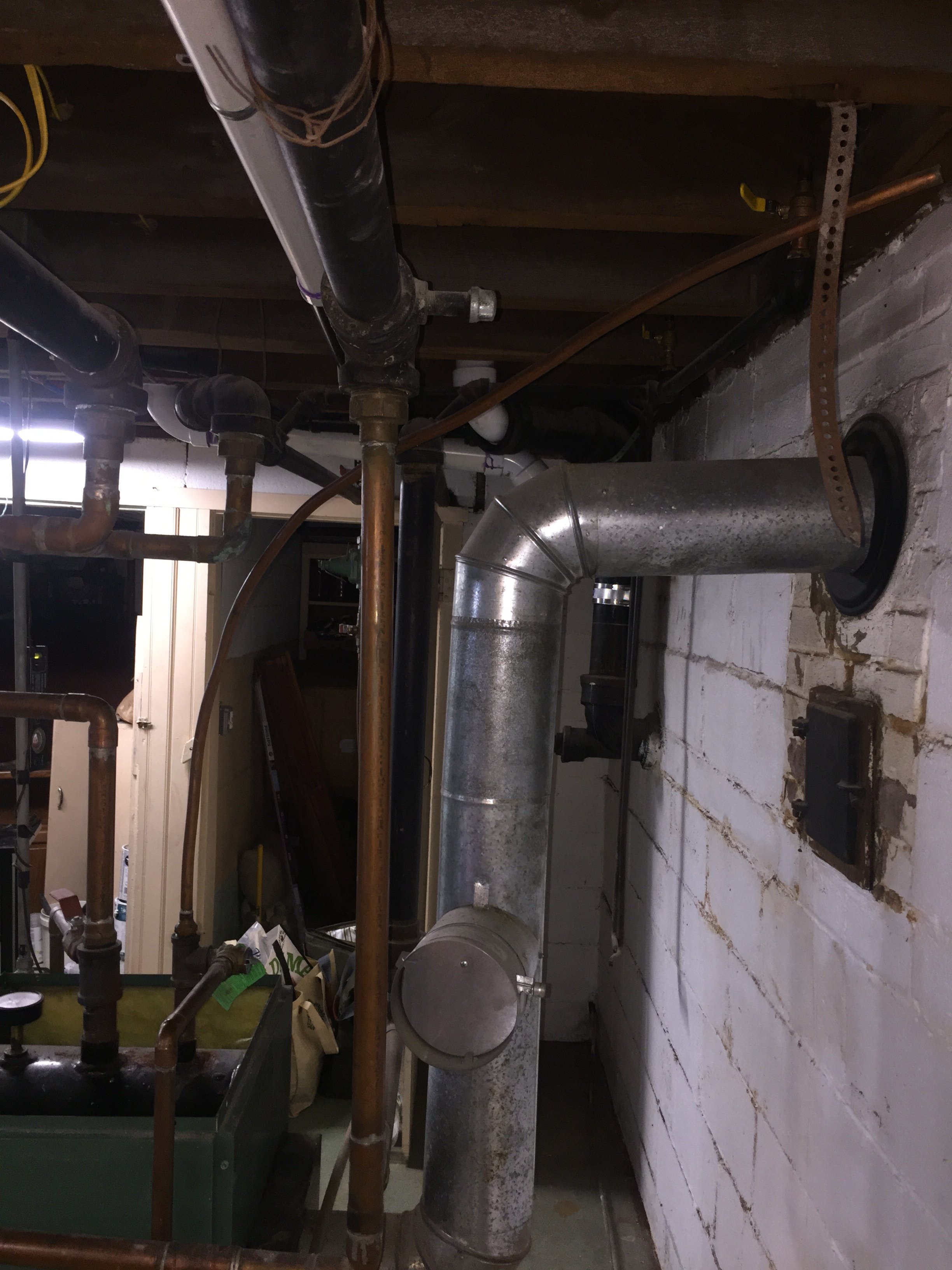
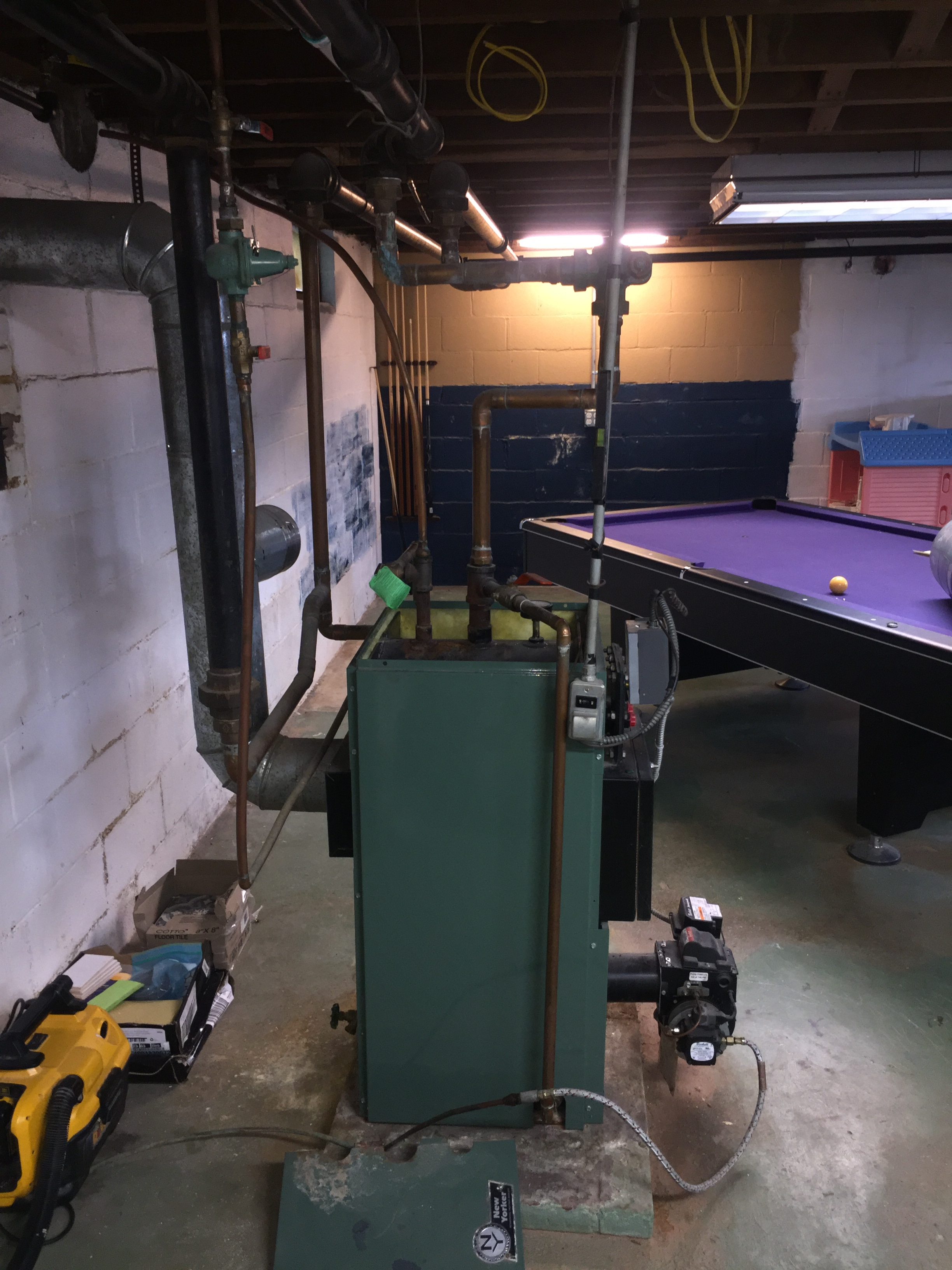
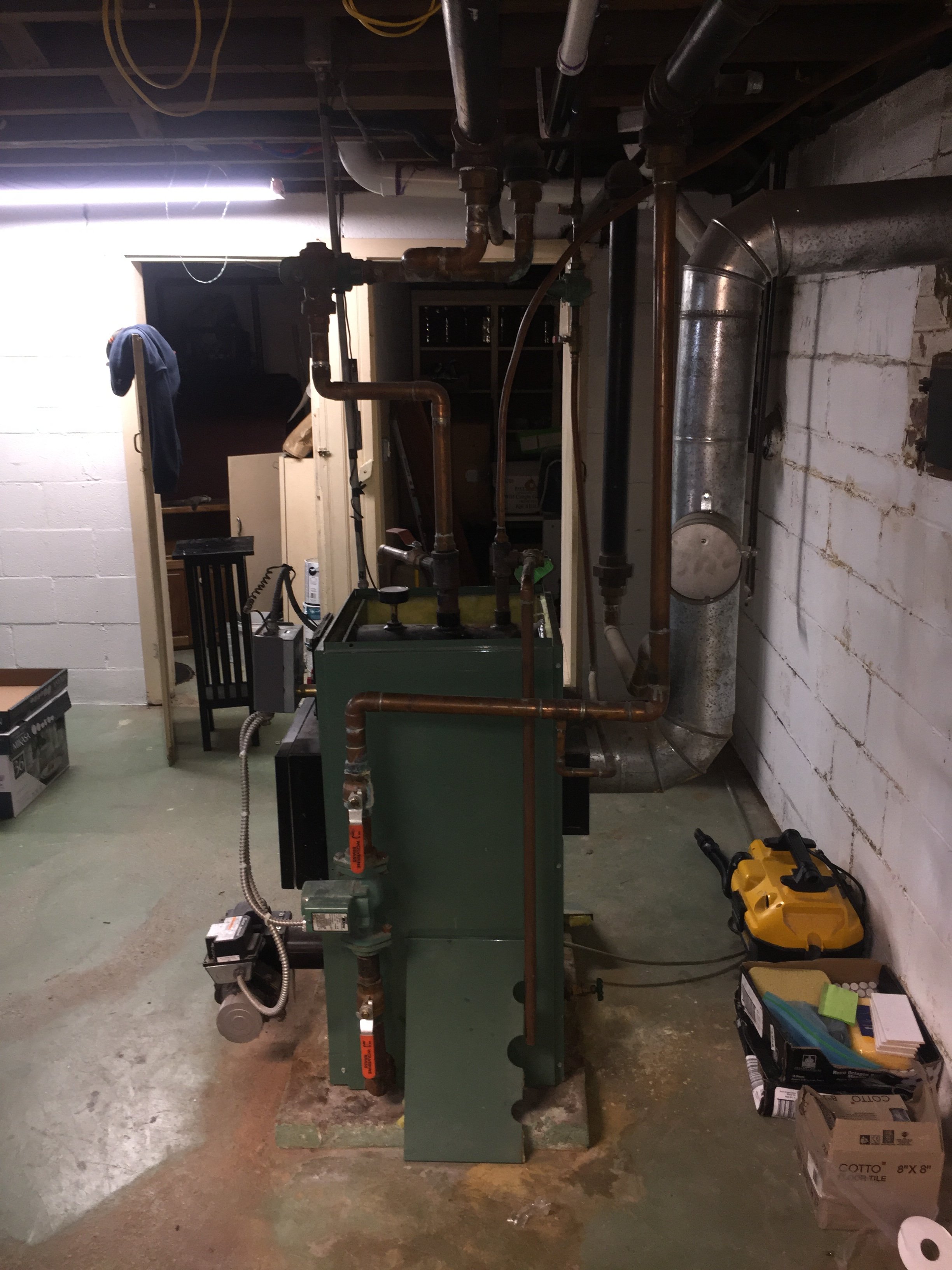
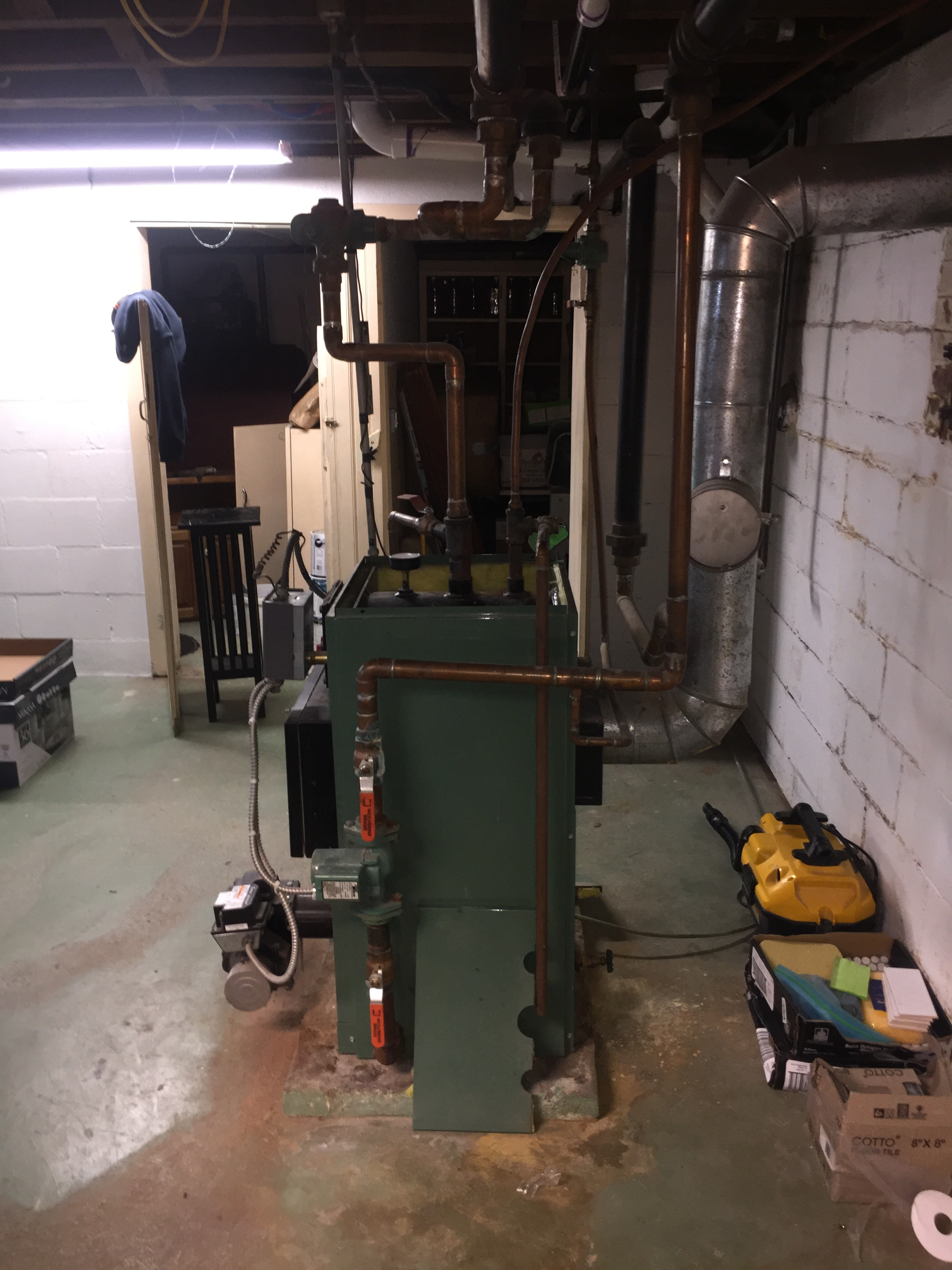
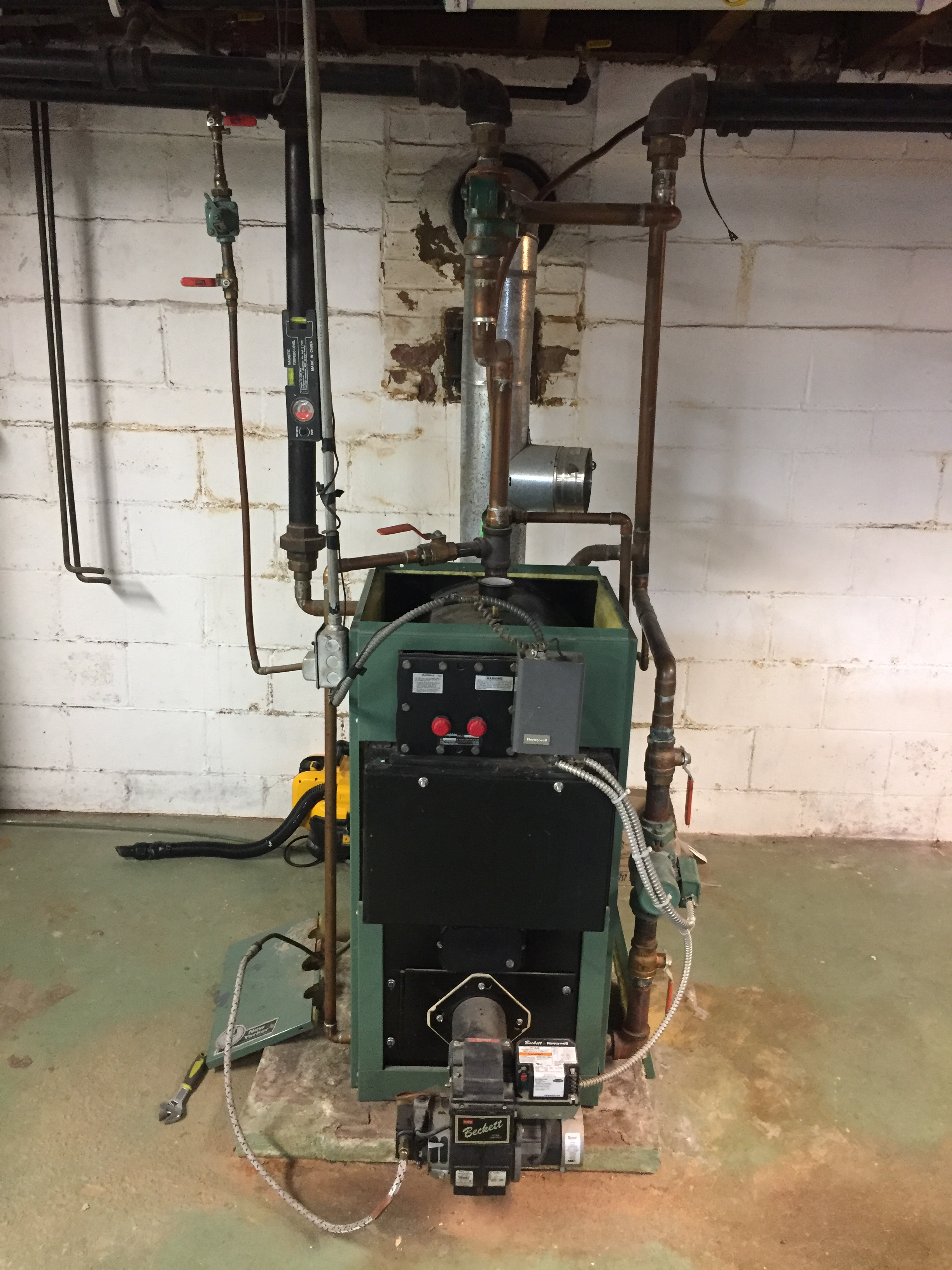
Comments
-
The cheapest, easiest thing you could do that would work, but not best practice, would be to come off the top of your tee where the relief valve is located, put a ball valve (take handle off and leave open), check the charge of the bladder tank to match the boiler's operating pressure, and screw the bladder tank onto the valve. You will be cursed by the person who bangs their head into it.
Better would be to re-do the near boiler piping so you have the supply coming out the top, then a spirovent. Attach the exp tank onto the bottom of the spirovent, with a webstone expansion tank valve in between-pipe your make up water into it.
Then you put your isolation valves and circulator, pumping away from the expansion tank.
Dan's book 'Pumping Away' shows a wonderful example of how this is piped, with appropriate valves and drain so you can basically purge all air out of the system from the basement, unless you have column radiatiors, it which case you'll still have to bleed each radiator.
I also see it appears you have a pretty interesting bypass piped into the boiler.
And you oil line scares me...There was an error rendering this rich post.
0 -
I've never seen a horizontal tube New Yorker.
Pretty cool.0 -
Yea all are column radiators except for one I replaced in a bathroom. Should it still be piped the way you suggested ? This would mean removing circulator pump where it is at and connecting that to the boiler where the pump was, and installing that one or preferably a new one above on the supply coming out of the top of the boiler? The bypass piped into the boiler, what should be done? I assume you mean the pipe on left that comes from tee through ball valve and down to the bottom. Is this an issue? Also what should be done with the oil line. It comes from a oil tank and is routed along floor against wall the that happens that you see. It is gravity fed. Is there away to bring it over head and put a pump or what would be the correct procedure for dealing with that. Thanks for the info I appreciate your time, I might buy that book to read up on it, is there an illustration of that method you mentioned? I familiar with the setup except for the isolation valves. I could put it where easiest, I might be selling this house soon anyway, but I would rather do it correctly. Thanks again any more information is greatly appreciated.0
-
I hope you have not sent that old expansion tank to the scrap pile!! You can still use it by simply extending the pipe length to the new location of the steel compression tank.
BUY the books pumping away and classic hydronics and then fix it with pipe and what ever fittings you need.0 -
its outside I just want to do the best thing for the system and im an electrician so my knowledge of this type of thing and system and how it really works is limited.0
-
the old tank is laying outside it what i meant0
-
Bring it back in and hang it back up and follow the instructions in Dans books and the B+G literature if it does not have an airtrol valve in it already.
The steel compression tank lets your boiler work with very low water pressure when its working and hot. You can use an air scoop for the steel compression tank or an Internal Air Separator fitting sized to the main piping size. I have the IAS and an airtrol valve on the steel compression tank I have hanging in the ceiling of my laundry room and I have no air bubbles to deal with or the need to bleed the baseboard radiators either.
That oil line needs to be fixed with a new oil line hung from the ceiling joists above the oil tank across the ceiling joists and down to the boiler. Have a plumber or an oil guy that will not overcharge you to come in and change the burner to a 2 pipe system will be easier as the deaerators have a "maximum" total length of 25 feet that they can be used on and a two pipe system pulls oil in and pushes the excess oil back to the tank and the oil is always filtered as a result of that so a two pipe system is better actually.
Two rolls of refrigerant grade soft copper, the oil tank fitting that has the two tapping's for the copper pipe to pass through and be locked in place with the compression fittings and the brass compression fittings for the soft copper copper will be all you need except for the burner connection fittings. You will need a cap for connection at the bottom of the tank to cover the fitting that is threaded into the shut off valve.
You need a new fuel shut off valve to bring it up to code too.
A good plumbing supply house will be able to help you with burner parts as long as you have all the information from the tag or tags on the burner.
read dans books before the cold weather comes so you can fix that boiler up. You need to put furnace insulation in the top of the boiler to hold the heat in the boiler too. You can by small quantities of it from Mcmaster Carr.
SO do you get involved with high voltage 4,000 Volt AC or greater?
0 -
I don't agree with any of this.leonz said:Bring it back in and hang it back up and follow the instructions in Dans books and the B+G literature if it does not have an airtrol valve in it already.
The steel compression tank lets your boiler work with very low water pressure when its working and hot. You can use an air scoop for the steel compression tank or an Internal Air Separator fitting sized to the main piping size. I have the IAS and an airtrol valve on the steel compression tank I have hanging in the ceiling of my laundry room and I have no air bubbles to deal with or the need to bleed the baseboard radiators either.
That oil line needs to be fixed with a new oil line hung from the ceiling joists above the oil tank across the ceiling joists and down to the boiler. Have a plumber or an oil guy that will not overcharge you to come in and change the burner to a 2 pipe system will be easier as the deaerators have a "maximum" total length of 25 feet that they can be used on and a two pipe system pulls oil in and pushes the excess oil back to the tank and the oil is always filtered as a result of that so a two pipe system is better actually.
Two rolls of refrigerant grade soft copper, the oil tank fitting that has the two tapping's for the copper pipe to pass through and be locked in place with the compression fittings and the brass compression fittings for the soft copper copper will be all you need except for the burner connection fittings. You will need a cap for connection at the bottom of the tank to cover the fitting that is threaded into the shut off valve.
You need a new fuel shut off valve to bring it up to code too.
A good plumbing supply house will be able to help you with burner parts as long as you have all the information from the tag or tags on the burner.
read dans books before the cold weather comes so you can fix that boiler up. You need to put furnace insulation in the top of the boiler to hold the heat in the boiler too. You can by small quantities of it from Mcmaster Carr.
SO do you get involved with high voltage 4,000 Volt AC or greater?
There was an error rendering this rich post.
2 -
-
-
Ok so conflicting information here. Anybody have some other input here as to what I should do. I did order that book going to check it out, but thinking about not putting that old tank back in and doing some re piping. As far as the oil line is there any conflict with how Leonz suggested it should be done, or is this the correct procedure. Not trying to be a **** to anyone here just trying to figure out the right thing to do as I do not have extensive or hardly any knowledge of this system. I appreciate any and all information, just trying to get it fixed up correctly to get heat soon.
Basically the only thing we would deal with is the Transformer before the building. The company I work for does all commerical work hospital school transit crap. Ive been stuck working nights on tranist for awhile waiting for some new projects to start up in the spring or hopefully sooner.0 -
An expansion tank could be mounted on the side of the boiler near the pump and tied into that 1/2" copper line. Now you are pumping away from the tank.
A vertical type air purger could be added to the line out of the top of the boiler. That would be two fairly simple upgrades to the piping, solving air elimination and proper pump to tank relationship.Bob "hot rod" Rohr
trainer for Caleffi NA
Living the hydronic dream2 -
==================================================================================================================================================================hot rod said:Horse and buggy technology, those old steel compression tanks. O2 ingress, lots of heat loss, large physical size compared to diaphragm tanks, so many reasons to abandon them when upgrading.
I have to disagree with you Bob, I wanted to have a steel compression tank reinstalled for my coal stoker boiler for many reasons. The old steel open to air vent tank my home had was simple and vented to atmosphere and only needed to be replenished with water when the water level was low in the tank and this was indicated by the tube gauge on the end of the open to air tank.
My new coal stoker boiler has a B+G 15 gallon steel compression tank with a one inch B+G air separator and a glass tube gauge with globe valves to check the water level. Yes Dan, they still leak through the packings; but I will fix that by installing ball valves and fittings to connect the glass tube gauge and globe valves to the ball valves next summer.
I have an B+G 1-1/4 inch tapping Internal air separator that has worked very well since it was installed and I have had no issues with the system as it runs from 4 PSI to 12 PSI when running the coal stoker on summer temperatures of 140 low 160 high with a 10 degree differential with 190 as the dump temperature using 10 degree differential for the L4006A.
One more issue was the automatic air vent which always leaked and I had to install a reducer in the air scoop and a pipe nipple and ball valve to allow me to replace it without draining the boiler.
I have a B+G Bulldog RB-122-A low water cut off as the primary control for the boiler as safety mechanism in the event of a water loss in the boiler.
I wanted an independent Low Water Cut Off as the hydrostat 3250 plus unit failed and nearly let the boiler boiler dry. The second unit I was sent also failed and the junk chinese gauge was inaccurate.
I was letting the boiler run on oil with the replacement control unit
to see if it was working properly and I just stood there and waited and watched.
Less than ten minutes into its running on oil the computer in hydrostat 3250 plus shut the low water shut down function that was programmed in to the triple aquastat; I muttered many unkind words about hydrolevel, keystoker and the dealer I bough the boiler from and turned it off.
I replaced it with a honeywell L8124L1011 triple aquastat as I could not fit a vertical triple aquastat in the same location due to the placement of the oil burner tube wherein I muttered a few more choice words about keystoker.
I eventually returned the defective units back to the stove dealer 2 years later and as I left as he gave me a not happy look nor do I care that he did either.
They being keystoker had 54 of these hydrostat 3250 plus units returned to them as defective when I called about getting a new one from my dealer and they being keystoker said they were not defective after they tested them.
I have no oil to burn nor do I need to burn oil as keeping a full tank of oil is only wasted money and the way the oil burner is set up the
fumes back up into the house through the burner flange mounting and through the oil burners combustion tube.
I am going to remove the oil burner and install the cover plate back on the oil burner mounting weldment which is on the dry side of the boiler this year.
If I had been able to afford the VanWert VA400 coal stoker boiler installation which was $6,000.00 at the time in 1981 I would still have it heating my home and making hot water.
The new Honeywell triple aquastat has worked flawlessly since I had the electrician wire it back in and the B+G low water cut off shuts the boiler down on each test cycle so I can sleep very well.
I have a spare triple aquaststat and a spare circulator as I only need one circulator to run my system now.
The old honeywell controls on my hand fed wood and coal boiler worked flawlessly from 1982 until 2015 when the new coal stoker was installed by the plumbers I hired. Choosing them was a very costly mistake.
If I had been able to afford the AHS coal gun coal stoker with the sled type coal stoker I would have purchased it but the dealer was a real (*&^%$%^&*(.
He knew nothing about coal stoker boilers and he acted like I was crazy asking to speak to someone about an AHS S130 coal stoker boiler. Needless to say he knew nothing about these coal stoker boilers even after he bought one and had it in his warehouse so he could become an authorised AHS dealer.
I would have been able to leave my old Buderus G205 Logana oil fired boiler installed in 1988 in place next to it and simply changed the flue pipes when I needed to burn oil.
My old plumber burned me about that old AVCO LYCOMING boiler as he said the boiler had a leak and the friend I gave the boiler to said it had no leaks so that experience cost me $5,000.00 that was an unnecessary expense.
SO even though its old technology, it still works and works well.
And I would bet that Dan still has his steel compression tank hanging in the ceiling above his boiler too as it just sits there and lets the air bubbles rise into the tank through the air separator and the airtrol valve and dissolve into the water in the steel compression tank.
Just because its old technology does not mean it will not work and work well; gravity hot water heating systems and steam heat prove that every day in the heating seasons.
My thoughts on a we day when I cannot get chores done.
-1 -
There's no conflicting information. There's all the professionals saying one thing, and a homeowner who loves steel expansion tanks (probably too much), and emotes here alot about them.
I wouldn't change from steel to compression, just to change if everything else was working, but @hot rod said it best (and is one of the leading hydronics experts around.
Here's a more detailed description along with my comments:
-----leonz said:Bring it back in and hang it back up and follow the instructions in Dans books and the B+G literature if it does not have an airtrol valve in it already.
You can't assume facts not in evidence. We don't know the condition of the tank. It's obviously pretty old. Why do all that work to put something back in service that is sub-par to what's available.
-----
-----leonz said:
The steel compression tank lets your boiler work with very low water pressure when its working and hot. You can use an air scoop for the steel compression tank or an Internal Air Separator fitting sized to the main piping size.
Air scoop, even piped correctly is a poor choice over newer air elimination.
The proper pressure needed is a matter of fact, and can't be less than what is needed based on the maximum height of the radiation, plus usually about 4 psi. If your system needs 12 psi, it needs 12 psi, regardless of the expansion tank used.
-----
-----leonz said:
I have the IAS and an airtrol valve on the steel compression tank I have hanging in the ceiling of my laundry room and I have no air bubbles to deal with or the need to bleed the baseboard radiators either.
The OP has column radiators. Using proper, modern air elimination, installed correctly is the best option. After initial purging, and bleeding of the radiators, and keeping the proper amount of pressure in the system, the amount of maintenance needed for air is minimal.
-----
-----leonz said:
That oil line needs to be fixed with a new oil line hung from the ceiling joists above the oil tank across the ceiling joists and down to the boiler. Have a plumber or an oil guy that will not overcharge you to come in and change the burner to a 2 pipe system will be easier as the deaerators have a "maximum" total length of 25 feet that they can be used on and a two pipe system pulls oil in and pushes the excess oil back to the tank and the oil is always filtered as a result of that so a two pipe system is better actually.
Why do you recommend hanging oil lines from the ceiling? You have no idea about the oil tank. Is it outside, inside, a gravity or lift.
Don't change the system to a 2 pipe (also requires a bypass plug in the fuel pump). It's well known and accepted practice not to use 2 pipe.
If your using 1 gph, your pump is pulling about 20 gph and sending 19 of it back to the tank.
A better solution is 2 filters at the tank (I like a General, then Spin-On), and treat the tank if there is a fuel quality issue.
-----
-----leonz said:
Two rolls of refrigerant grade soft copper, the oil tank fitting that has the two tapping's for the copper pipe to pass through and be locked in place with the compression fittings and the brass compression fittings for the soft copper copper will be all you need except for the burner connection fittings. You will need a cap for connection at the bottom of the tank to cover the fitting that is threaded into the shut off valve.
You need a new fuel shut off valve to bring it up to code too.
A good plumbing supply house will be able to help you with burner parts as long as you have all the information from the tag or tags on the burner.
Oil lines need to be coated now, and for gravity jobs you need an OSV. You also need a firomatic at the tank, and one at the burner by code. I wouldn't change the oil line from one at the bottom of the tank to one at the top without a reason.
I wouldn't rely on a supply house to tell you what you need, but would instead allow a competent professional to do the job properly and by code.
-----
-----leonz said:
read dans books before the cold weather comes so you can fix that boiler up. You need to put furnace insulation in the top of the boiler to hold the heat in the boiler too. You can by small quantities of it from Mcmaster Carr.
Dan's books have great information about piping-proper methods and theory and best practices, never saw one mention of furnace insulation.There was an error rendering this rich post.
0 -
Some boilers have no insulation on the steam jacket just as mine was and I had to put furnace insulation on it to keep from overheating the house as the boiler is on the same level and not in a basement.
I had to have my oil line hung from the ceiling joists after it entered the home and it would constantly air lock and it needs a two pipe set up to prevent it from air locking if an when the oil system gets used again.
His oil tank is in his basement and the single fuel line runs along the foundation wall to the boiler. I agree that he needs the fireomatic valves to bring it up to code.
I installed a RACOR 500FG fuel filter in my system as it was constantly plugging up with dead algae from the tank and by changing to the top set up in my case eliminated the oil from freezing and plugging up after I eliminated the old felt filter set up.
What always worked still works and that is why I went back to a steel compression tank as we have a single loop system that was originally 2 loops. Our system lost pressure several times and it had to be pressurized with a jet pump and more water as we lost our 292 foot deep well due to the well caving in all the way up to the steel casing which is 92 feet deep.0 -
No question that style tank can and do work, but the newer diaphragm tanks with micro bubble air removal add so much to the system, more than likely increasing efficiency of the heat emitters and boiler by scrubbing tiny microbubbles that develop every time the boiler heats from a cold start.
Really should not need to monitor water level with a glass tube on a modern hydronic system? A seaweed leak free system should not need any additional water added once it is filled, heated and purged via a micro bubble type air separator.
I doubt we will convince you there is a better way, but not many installers start out with plain steel tanks on new systems these days.Bob "hot rod" Rohr
trainer for Caleffi NA
Living the hydronic dream0 -
My diaphragm tank installed in 1995 is still the same one.
Maybe added air a couple times within that period.
Plain steel compression tanks I work on have to be drained maybe every 2-3 years. Not a big deal for me as I do service work. But a PIA to HO if they have to do it themselves.0 -
Did they balk at having you install an airtrol valve to solve that issue? Or did they open the water fill valve and leave it open too?0
-
If you are referring to the existing compression tanks I mentioned, the airtrol valve was in place already.
These are installs from the 1960's.
This system will eventually lose air thru a variety of places and the tank will become water logged.
Today the diaphragm tank system with proper air removal/eliminator which removes all air, rather than try to place and keep it captured in the compression tank gives less problems. IMO0 -
This would work great.hot rod said:An expansion tank could be mounted on the side of the boiler near the pump and tied into that 1/2" copper line. Now you are pumping away from the tank.
A vertical type air purger could be added to the line out of the top of the boiler. That would be two fairly simple upgrades to the piping, solving air elimination and proper pump to tank relationship."If you can't explain it simply, you don't understand it well enough"
Albert Einstein0 -
======================================================JUGHNE said:If you are referring to the existing compression tanks I mentioned, the airtrol valve was in place already.
These are installs from the 1960's.
This system will eventually lose air thru a variety of places and the tank will become water logged.
Today the diaphragm tank system with proper air removal/eliminator which removes all air, rather than try to place and keep it captured in the compression tank gives less problems. IMO
The 3 reasons I know of for a steel compression to become water logged in boilers are:
a. a leaking domestic coil from a cracked tube feeding potable water into the boiler displacing the air in the steel compression tank.
b. a leaking fill valve due to a poor seat in the valve or debris in the valve seat.
c. a new oil or gas boiler installed with a bladder compression tank automatic air vents and an automatic fill valve that will end up filling the steel compression if the new boilers water has not been shut off to the coal stoker.
A friend of mine in coal country had this happen when the oil boiler crapped out and a plumber replaced it with a new one using a bladder tank and an automatic air vent valve and air scoop.
The air blanket in the steel compression tank for the Axeman Anderson S260 coal stoker boiler was eventually bled out from the steel compression tank through the oil fired boiler and the air scoop and automatic air vent.
My friend found that he had no heat in the 2 family farm house as a result of this and he was able to track down the problems and fix them after I suggested he purchase the books "Classic Hydronics" and "Pumping Away".
He added new main shut off valves between the two boilers water circulation ciruits as well as adding shut off valves to the two domestic coil loops and water heater to separate them as well.
He had to do a number of repairs on the coal stoker which included replacing the ash slicer and replacing a worn out honeywell mechanical triple aquastat with hydrostat 3250 and install a new low water cut off, a new back flow preventer and replace the leaking original domestic coil and the mounting bolts for the domestic coil that had to be drilled out and tapped as well as welded to replace the old bolts and its gasket and he installed new circulators and a few new radiator air bleeder vents and its been running well ever since.
My thoughts as a layperson.
0 -
hot rod said:
An expansion tank could be mounted on the side of the boiler near the pump and tied into that 1/2" copper line. Now you are pumping away from the tank.
A vertical type air purger could be added to the line out of the top of the boiler. That would be two fairly simple upgrades to the piping, solving air elimination and proper pump to tank relationship.
Ok so Tie it into the half inch line that comes over from the fill valve assembly. Should I add air purger or isolating valves or vents there or just tie it in. Then In addition I should add A vertical type air purger to the line coming off the tee next to the pressure relief valve?
On the oil tank note. The oil tank is located in an adjacent room and the oil line is run in a L shape then comes along the wall and out where you see it so its just gravity fed. Should I have it re done a different way ?
I greatly appreciate all the information here.0 -
The tank can be mounted anywhere, even strapped up in the joist if that is easier. Get a roll of perforated metal "plumbers" tape to mount it. I have mounted the tanks on their side without any issues.
The connection would be easy into that 1/2" line from the fill valve. 1/2" copper or heat pex would work to connect it.
Check the air pressure when you remove the tank from the box or system. The air charge needs to be the same as the fill pressure, generally around 12- 15 psi.
The air purger needs to be in the copper supply line coming out the top of the boiler.
A few different manufacturers offer vertical versions, looks like an 1-1/4" pipe out of the boiler?
A press connection version would be a snap to install if you have access to a tool or hire a plumber to make these two corrections.Bob "hot rod" Rohr
trainer for Caleffi NA
Living the hydronic dream0 -
Ok just to clarify I will re route the half inch line coming from the fill valve to accomidate installation of the expansion tank if I need to. As long as its between the fill valve and the Tee it connects to. Do I need anything else on top of the expansion tank where it connects to the copper If not Im just going to put a copper tee there. Also something like this VJV125 Spirotherm
should be Should be installed Right after the copper comes out of the boiler top, the 1 1/4 supply line.
I have abrother in law who work for a refrigeration contractor and the company I work for does mechanical commercial installation also I think I could borrow a pro press tool from one or the other. I talked to my brother in law before but he said his knowledge of home systems is not the best. Ill try and find a press version see what the price might be , if not should this connection be soldered for that size or brazed or is the preference in this type of system?
Also I have a roll of the perforated plumbers tape for mounting or strapping of the tank. Also the tank says 12 psi im going to verify it then.
Thanks again much appreciated0 -
Here is one way to add the fixes.
After you tee into the 1/2, add the valve and remote mount that tank where it is easy to check and out of the way.
Bob "hot rod" Rohr
trainer for Caleffi NA
Living the hydronic dream0 -
alright nice I had not noticed that image on the last one.0
Categories
- All Categories
- 87K THE MAIN WALL
- 3.2K A-C, Heat Pumps & Refrigeration
- 57 Biomass
- 425 Carbon Monoxide Awareness
- 112 Chimneys & Flues
- 2.1K Domestic Hot Water
- 5.7K Gas Heating
- 106 Geothermal
- 160 Indoor-Air Quality
- 3.6K Oil Heating
- 70 Pipe Deterioration
- 979 Plumbing
- 6.3K Radiant Heating
- 387 Solar
- 15.4K Strictly Steam
- 3.4K Thermostats and Controls
- 54 Water Quality
- 44 Industry Classes
- 48 Job Opportunities
- 18 Recall Announcements