"Spin Weld" PVC Pipe & Fittings?
I'm pondering the best way to PVC to PVC weld a 4" x 2" reducing fitting and a 2" pipe stub (3" long) with a special .2mm stainless steel filter screen wire mesh entrapped within the socket connection.
The screen serves as a water filter resin bead containment barrier (keeps the beads in the 4" pipe side yet allow the treated water to pass to the 2" out port side)
In the conventional "primer + cement" application ..... trying to keep the primer and cement from reaching (clogging) the screen ...... is problematic! : (
Even if I try to protect the screen during priming and cementing with a removable paper disk ...... the primer is so invasive it always finds a way past any protection! The cement not so far behind in this respect as well.
I could just easily "sandwich" this screen in between a PVC union ...... but the cost per screen mounting (30 to 40 2" unions needed per unit) would become outrageous. Using the existing socket connection has no cost at all.
So now I'm thinking ..... don't chemically weld at all ..... spin weld!
I've spin welded PVC pipe ends together with perfection (see pic) .... but don't know if the tapered socket + un-tapered pipe will actually work for this method.
....... any thoughts on all this?
Thanks!
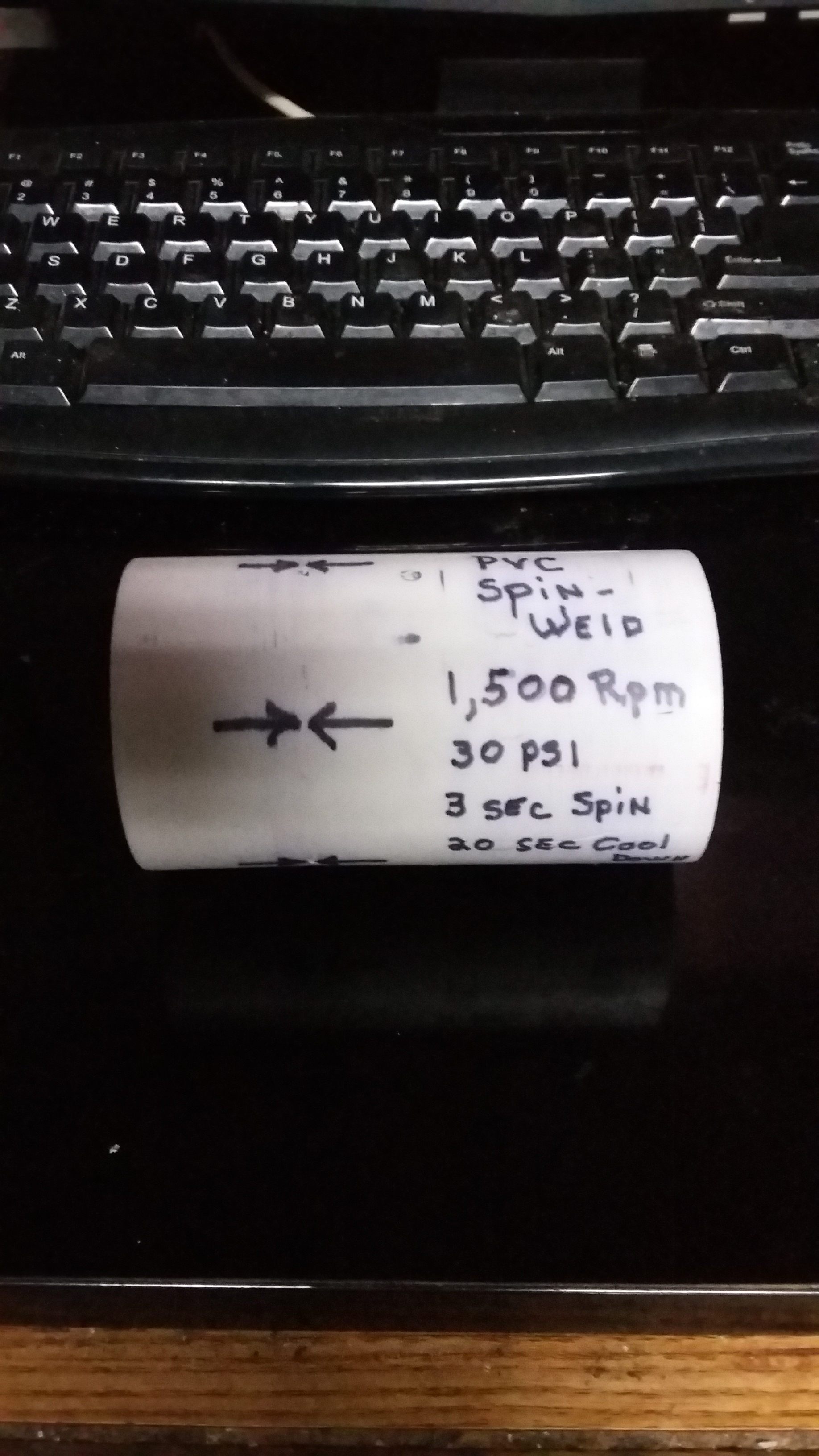
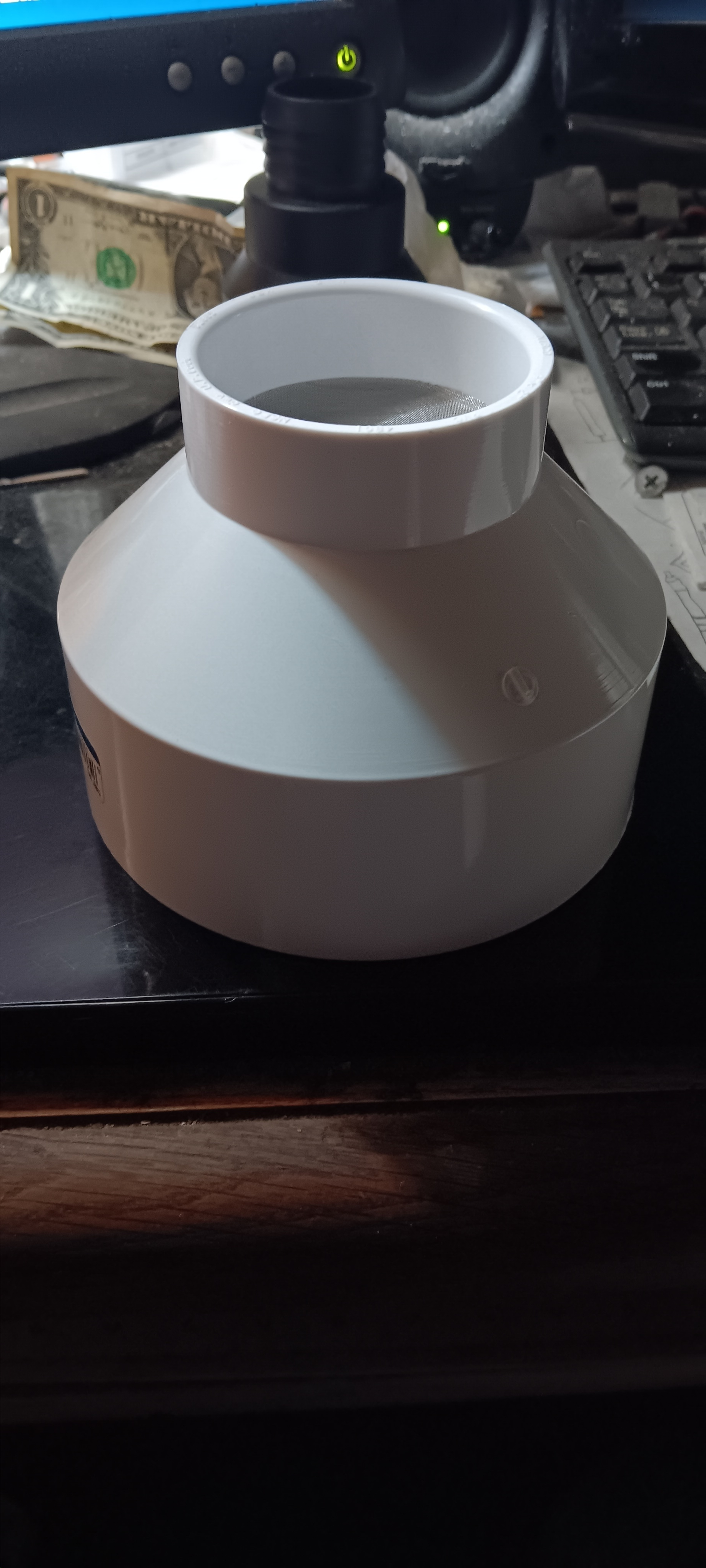
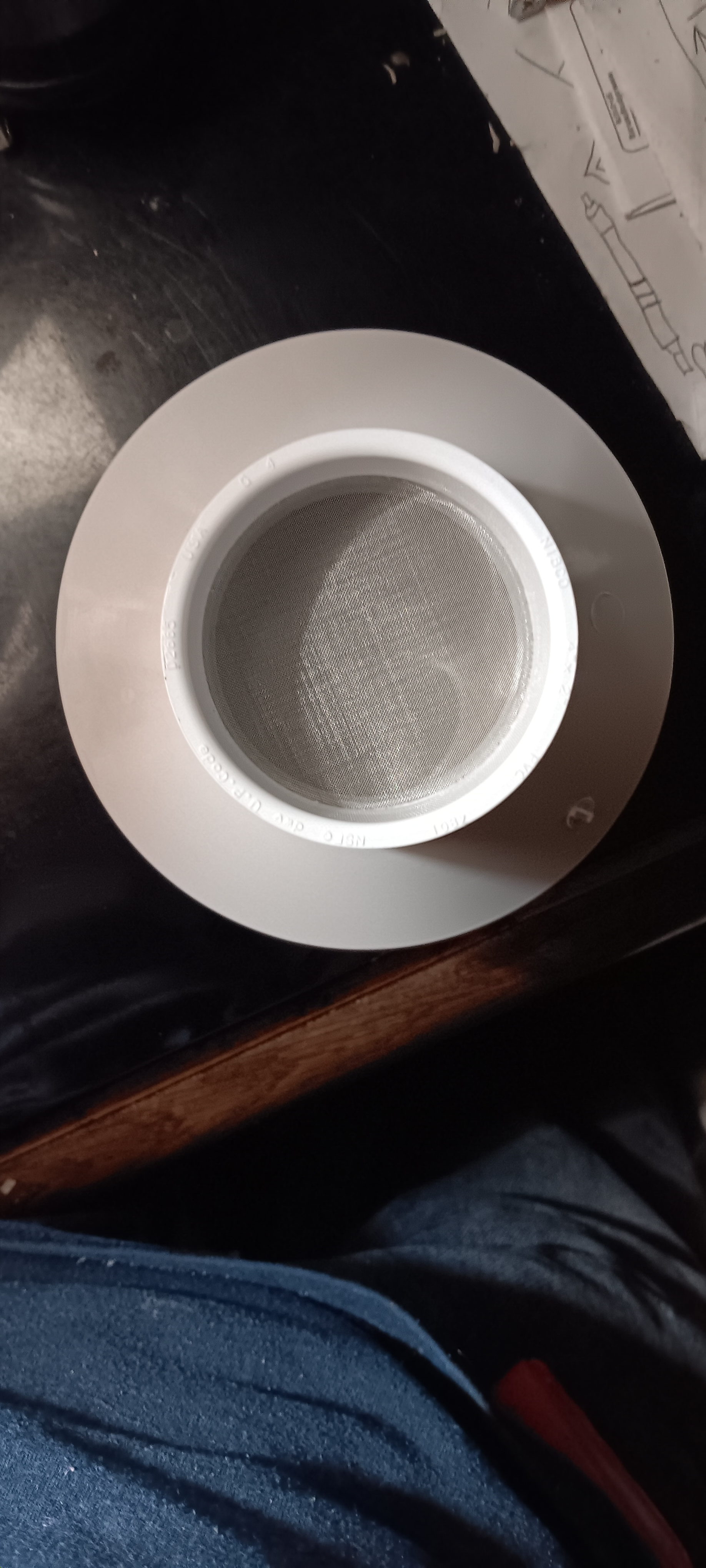
Comments
-
@RickDelta
The best thing to do is to keep it as simple as possible by using fittings and adapters related to each other to offer the best result possible. ie... no leaks, true plumb and level.0 -
Seems trial and error will be the saying of the day as you continue with this. Give it a try?0
-
I would just install a Y strainer rather then taking a chance
https://www.amazon.com/TOMEX-Y-Strainer-Sediment-Socket-Female/dp/B0CL5SX5TQ?source=ps-sl-shoppingads-lpcontext&ref_=fplfs&psc=1&smid=A3GTUGHQ8MD61X
1 -
...... @ $63.00 each x 40 = $2,520 I'll take a chance with the socket design!pecmsg said:I would just install a Y strainer rather then taking a chance
https://www.amazon.com/TOMEX-Y-Strainer-Sediment-Socket-Female/dp/B0CL5SX5TQ?source=ps-sl-shoppingads-lpcontext&ref_=fplfs&psc=1&smid=A3GTUGHQ8MD61X0 -
RickDelta said:
I would just install a Y strainer rather then taking a chance
...... @ $63.00 each x 40 = $2,520 I'll take a chance with the socket design!
https://www.amazon.com/TOMEX-Y-Strainer-Sediment-Socket-Female/dp/B0CL5SX5TQ?source=ps-sl-shoppingads-lpcontext&ref_=fplfs&psc=1&smid=A3GTUGHQ8MD61X1 -
-
Is it under any pressure? You could prime and glue only the very ends of the fitting and only insert the pipe a 1/4 to 1/2 way?
Miss Hall's School service mechanic, greenhouse manager, teacher, dog walker and designated driver
0 -
The cost for that many Y strainers would be way to costly for this application.hot_rod said:That looks like an awfully fine mesh? Prone to easily plugging and no easy way to service. That is where a Y strainer is handy, easy to disassemble and clean. Or change mesh size.
I never need access to clean this filter. After service life of the resin beads I dispose of the entire assembly.0 -
I know you want us to tell you that you've come up with a brilliant idea, but ...
Is spin welding an approved method for joining street-pressure PVC in your jurisdiction?
If you used a 2"x4" reducing bushing instead of the reducing coupling, and the bushing was threaded on the 2" side, you could put a male threaded adapter on the 2" pipe and screw the whole thing together. The bushing plus the adapter costs less than the coupling.
If you're at street pressure you need fittings rated for potable water, which may be hard to find in 4".0 -
"Is spin welding an approved method for joining street-pressure PVC in your jurisdiction?"DCContrarian said:I know you want us to tell you that you've come up with a brilliant idea, but ...
Is spin welding an approved method for joining street-pressure PVC in your jurisdiction?
If you used a 2"x4" reducing bushing instead of the reducing coupling, and the bushing was threaded on the 2" side, you could put a male threaded adapter on the 2" pipe and screw the whole thing together. The bushing plus the adapter costs less than the coupling.
If you're at street pressure you need fittings rated for potable water, which may be hard to find in 4".
They "heat weld" the blue PVC water mains here I know.
The spin weld "butt" end methode is extremely strong. When I smash it with a hammer the pipe breaks ....... but the joint remains intact.
Your idea of using a threaded bushing sounds perfect! I will have to see if they make such a thing.
..... but I do believe a threaded connection derates (weakens) its use in a pressure environment.
0 -
Sorry but that’s not gonna cover your **** when there’s damages0
-
What can possibly go wrong?0
-
Thinking:RickDelta said:
"Is spin welding an approved method for joining street-pressure PVC in your jurisdiction?"DCContrarian said:I know you want us to tell you that you've come up with a brilliant idea, but ...
Is spin welding an approved method for joining street-pressure PVC in your jurisdiction?
If you used a 2"x4" reducing bushing instead of the reducing coupling, and the bushing was threaded on the 2" side, you could put a male threaded adapter on the 2" pipe and screw the whole thing together. The bushing plus the adapter costs less than the coupling.
If you're at street pressure you need fittings rated for potable water, which may be hard to find in 4".
They "heat weld" the blue PVC water mains here I know.
The spin weld "butt" end methode is extremely strong. When I smash it with a hammer the pipe breaks ....... but the joint remains intact.
Your idea of using a threaded bushing sounds perfect! I will have to see if they make such a thing.
..... but I do believe a threaded connection derates (weakens) its use in a pressure environment.
....... Prime and cement the "threads" !!
This would eliminate the primer and cement migration towards the filter screen and restore the joints pressure rating to standard pipe working PSI.
0 -
I had not heard of spin weld before. Does the pipe, used in water mains around there, have a specific end to maintain alignmentBob "hot rod" Rohr
trainer for Caleffi NA
Living the hydronic dream0 -
https://www.homedepot.com/p/DURA-4-in-x-2-in-Schedule-40-PVC-Reducer-Bushing-SPGxFPT-438-420/203225044RickDelta said:
Your idea of using a threaded bushing sounds perfect! I will have to see if they make such a thing.
..... but I do believe a threaded connection derates (weakens) its use in a pressure environment.
Rated for potable water too.0 -
-
DCContrarian said:
Your idea of using a threaded bushing sounds perfect! I will have to see if they make such a thing. ..... but I do believe a threaded connection derates (weakens) its use in a pressure environment.
https://www.homedepot.com/p/DURA-4-in-x-2-in-Schedule-40-PVC-Reducer-Bushing-SPGxFPT-438-420/203225044 Rated for potable water too.
Think of a 2" pvc union ...... I could simply insert the screen in between the o- ring.
That would be ideal ...... but is cost prohibited.
.... just like I did with incerting a fender washer in this union at the end of a circulator.
0 -
There's going to be a lip at the bottom of the threading, same size as the lip on the coupling in the original post.RickDelta said:
That won't work! How do you "sandwich " the screen in-between the two mating surfaces?
If that lip isn't big enough, here's an idea for making a bigger one: get a piece of 2" PVC and a 2" threading die. Thread the end of the PVC pipe, then cut 1/4" off the end. Use a nipple wrench to screw it down into the fitting until it bottoms out. Put in the screen, then screw in the rest of the pipe.
0 -
Hi @RickDelta , The screen you're looking at is pretty fine and could have a problem with blowing out if the flow rate got too high. Is there a way to put a grid behind the fine mesh? Maybe something like 1/4" welded wire mesh, but made of stainless??? Or, will the flow rate always be low?
Yours, Larry1 -
The manufacture of the screen mesh offers several high pressure reinforcement options ..... exactly as you had suggested.Larry Weingarten said:Hi @RickDelta , The screen you're looking at is pretty fine and could have a problem with blowing out if the flow rate got too high. Is there a way to put a grid behind the fine mesh? Maybe something like 1/4" welded wire mesh, but made of stainless??? Or, will the flow rate always be low?
Yours, Larry
0 -
I think I found the perfect solution.
Works with either chemical or spin welding.
High pressure safe without added reinforcement.
Simply lay screen disk over end of the 2" PVC pipe and heat press (embed) the stainless steel screen into the pipe end (aprox. 5 sec).
Destructive testing (hitting with a hammer) punctures the screen ....... but the embedded mesh/seal remains intact!
The tiny micro ridge formed in the PVC end is easily removed during the edge chamfering.
During the pipe to fitting assembly, the screen edges are further entrapped tighty against the internal end stops within the socket itself.
0 -
@RickDelta My thought on this is to use a wye strainer as what @pecmsg says above. Go shopping for one that fits your needs and budget and modify it as necessary.0
-
Intplm. said:
@RickDelta My thought on this is to use a wye strainer as what @pecmsg says above. Go shopping for one that fits your needs and budget and modify it as necessary.
...... "Y" strainer @ $63.00 each x 40 = $2,520 I'll take a chance with the socket design!
The filter never needs to changed or cleaned!
The entire system including the pressure vessels are disposed of at the resin beads expiration.
There is a replaceable particulate filter before and after this TAC water filter assembly.
This entrapped socket filter design essentially costs nothing except for the 86 cent stainless steel mesh filter.
1 -
I don't see how that is any less prone to fouling from migration of the cement than just using a fitting.RickDelta said:I think a found the perfect solution.
Works with either chemical or spin welding.
High pressure safe without added reinforcement.
Simply lay screen disk over end of the 2" PVC pipe and heat press (embed) the stainless steel screen into the pipe end (aprox. 5 sec).
Destructive testing (hitting with a hammer) punctures the screen ....... but the embedded mesh/seal remains intact!
The tiny micro ridge formed in the PVC end is easily removed during the edge chamfering.
During the pipe to fitting assembly, the screen edges are further entrapped tighty against the internal end stops within the socket itself.
How about this amendment: use a threading die to thread the end of the 2" pipe and screw it together.
0 -
What is spin welding? Is that another name for friction welding?
Single pipe 392sqft system with an EG-40 rated for 325sqft and it's silent and balanced at all times.
0 -
I saw the picture, didn't know what I was looking at.
Single pipe 392sqft system with an EG-40 rated for 325sqft and it's silent and balanced at all times.
0 -
DCContrarian said:
I don't see how that is any less prone to fouling from migration of the cement than just using a fitting.RickDelta said:I think a found the perfect solution.
Works with either chemical or spin welding.
High pressure safe without added reinforcement.
Simply lay screen disk over end of the 2" PVC pipe and heat press (embed) the stainless steel screen into the pipe end (aprox. 5 sec).
Destructive testing (hitting with a hammer) punctures the screen ....... but the embedded mesh/seal remains intact!
The tiny micro ridge formed in the PVC end is easily removed during the edge chamfering.
During the pipe to fitting assembly, the screen edges are further entrapped tighty against the internal end stops within the socket itself.
How about this amendment: use a threading die to thread the end of the 2" pipe and screw it together.
The problem with a threaded filter screen solution is the rotational shear on the ultra fine screen mesh wires. It would tend to rip at the .2 mm filter spacing size and allow the resin beads to escape the 4"containment tank.
.... and a threaded pvc pipe it's working pressure degraded.
0 -
"@DDContrian"
"I don't see how that is any less prone to fouling from migration of the cement than just using a fitting."
...... by having the filter screen embedded onto the end of the pipe (as opposed to inside the socket) the filter sits backwards 90 degrees away from the primer and cement application.
..... also, the big white fuzzy ball applicator is to un-controllable (messy), I'll be using a more controlled application to apply primer and cement (foam stick).0 -
In-between the arrows is the spin weld joint!!ChrisJ said:I saw the picture, didn't know what I was looking at.
I also take a 2" schedule 80 PVC pipe and expand its diameter to 4" schedule 40 as a sewer lateral repair liner.
It then it becomes MO-PVC (Molecularly Oriented-PVC)
0 -
-
Doesn't the mesh interfere with the spin weld surfaces?Bob "hot rod" Rohr
trainer for Caleffi NA
Living the hydronic dream0 -
Categories
- All Categories
- 86.8K THE MAIN WALL
- 3.1K A-C, Heat Pumps & Refrigeration
- 57 Biomass
- 425 Carbon Monoxide Awareness
- 109 Chimneys & Flues
- 2.1K Domestic Hot Water
- 5.6K Gas Heating
- 105 Geothermal
- 160 Indoor-Air Quality
- 3.6K Oil Heating
- 70 Pipe Deterioration
- 966 Plumbing
- 6.3K Radiant Heating
- 385 Solar
- 15.3K Strictly Steam
- 3.4K Thermostats and Controls
- 54 Water Quality
- 44 Industry Classes
- 47 Job Opportunities
- 18 Recall Announcements