Replace 3 way mixing valve with variable speed pump in snowmelt loop
I am looking at design options for a small snowmelt system. This is an add-on to an existing modulating condensing boiler, hydronic air, indirect water heater system. The snowmelt part of this system will be on a separate closed loop, glycol, heat exchanger, etc.
EDIT: The snowmelt will not be idled. It will be run, when needed, to melt snow.
What I am focused on right now is the temperature control of the glycol loop.
Here is part of a diagram from Caleffi for reference:
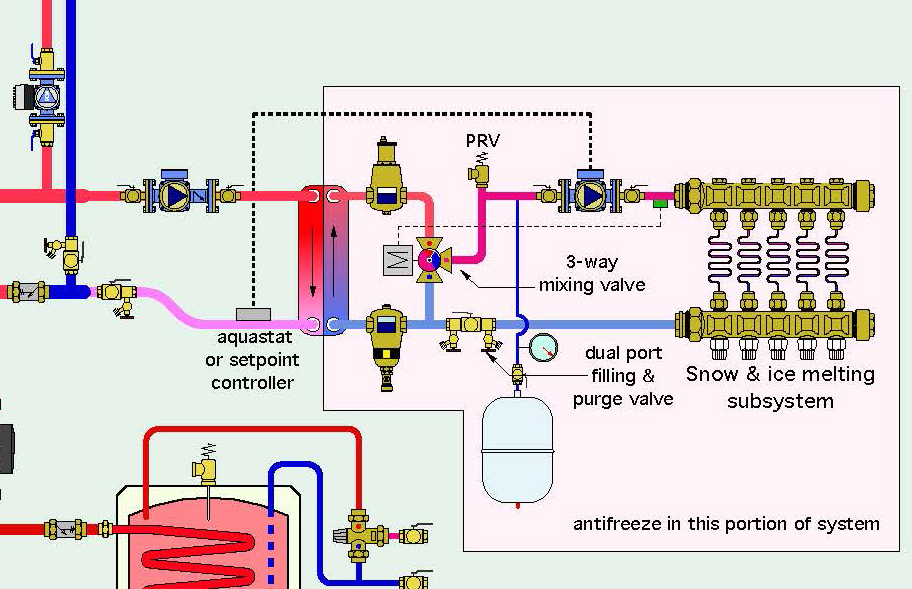
As shown in the diagram, a 3 way mixing valve is used to control the fluid temperature in the snowmelt loop. Because of the cost and complexity of these mixing valves, I was wondering if it would be simpler to get rid of the mixing valve and use a variable speed pump to adjust the temperature instead. It would look like this:
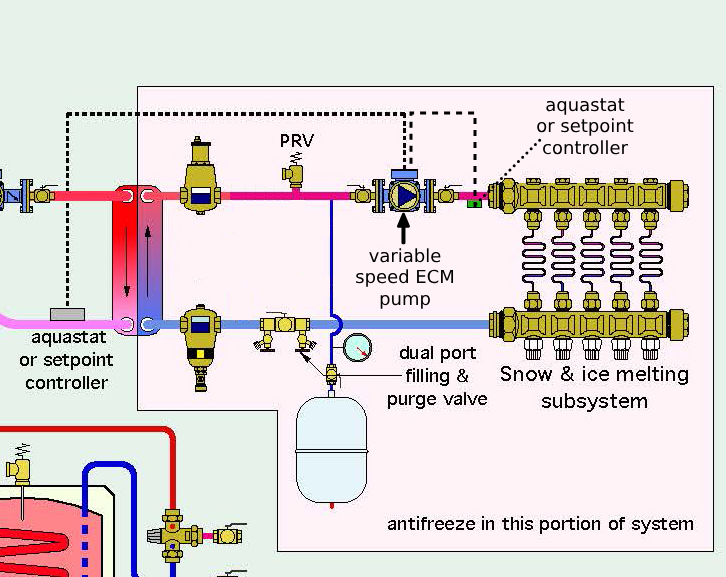
I have some questions about this alternate arrangement:
1) Would this work?
2) If this works, are there any pros or cons of this method?
3) If this works, why are mixing valves typically used instead?
Here are some guesses I have for answers, but they are just that -- guesses. Would appreciate feedback from those with more knowledge than myself.
1) ?
2) Pros:
- Simpler
- Less expensive
Cons:
- If the flow is slowed, to reduce how much heat goes into the snowmelt system, it might result in less even heating. In other words, the heat might get sucked out part way along the pex and there might not be any left after a certain point. The earlier parts of the path would get overheated and the further parts underheated. Whereas, with the mixing valve approach, the flow can stay fast. The water can be tempered down, yet still allow some of that heat to get to the end of the pex loops. It would be spreading out the conduction over a longer span of the pex than it would be with the variable speed pump approach.
3) - Historically, there weren't variable speed pumps, so finer control was available through the mixing valve option.
- Uneven heating, as explained above.
Thanks for any feedback on this.
David
Comments
-
-
Do you mean the existing pump used for the hydronic air loop, or do you mean set up a separate injection loop section between the main loop and the glycol loop?ratio said:I think I would control the temp via the pump on the boiler side.
The main problem I would have with lowering the temp in the main loop is it would affect the hydronic air temperature too. So whereas I might be able to get the snowmelt up to temp and back off on the temperature, doing so by changing the temp in my main loop would get me cold air at the registers. That probably wouldn't keep up with the house heat demand on a cold day.
Thanks,
David0 -
Do you have enough boiler output to run the snowmelt and house heat at the same time? How large is the snowmelt? What size boiler?
No need for any mixing device on the snowmelt with a mod con, just run the boiler at 100- 110, or so
When the snowmelt runs you will get cold return to the boiler, dragging down the supply temperature, so until the snowmelt starts to warm you may not have enough boiler BTU?Bob "hot rod" Rohr
trainer for Caleffi NA
Living the hydronic dream0 -
I would throttle the pump that feeds boiler water to the HX based on the supply temp of the snow melt side.0
-
Thanks for the reply, @hot_rod.
The boiler was sized to allow for some future additions like this when it was installed. This snowmelt is a relatively small patch -- about 200 or so square feet. The boiler output is about 170K BTU (Buderus GB142-60).hot_rod said:Do you have enough boiler output to run the snowmelt and house heat at the same time? How large is the snowmelt? What size boiler?
The main boiler loop supply is set to 140 degrees for the hydronic air. If I turn that down to 110, I'll get cold feeling air at the registers and I'm not sure if it would keep up with the thermostats on a cold day.hot_rod said:No need for any mixing device on the snowmelt with a mod con, just run the boiler at 100- 110, or so
When the snowmelt runs you will get cold return to the boiler, dragging down the supply temperature, so until the snowmelt starts to warm you may not have enough boiler BTU?
I also left out an important part of this -- the snowmelt won't be idled (added to original post now). It will only be run when needed to melt snow.
0 -
The only problem with that is that it will affect the temp going to the hydronic air handler (because of how I want to control the snowmelt eventually). I want to keep the hydronic air at 140, and allow a separate temperature for the snowmelt loop.ratio said:I would throttle the pump that feeds boiler water to the HX based on the supply temp of the snow melt side.
I hope to have a simple mode where the snowmelt loop runs at a fixed temperature (governed by a sensor in front of the snowmelt pump). I also hope to add more advanced controls that will get the snowmelt surface up to temp and then back off to keep it at the setpoint (instead of cycling off and on).
I want the separation of temperatures in the two loops so that the hydronic air can do its thing and the snowmelt can do its thing, independently.
I guess I can see what you are suggesting though. The pump shown in the original diagram, to the left of the heat exchanger, could be a variable speed pump.
So you are saying that pump could be slowed down to adjust the temperature to the right of the heat exchanger, but the pump in the snowmelt loop would still be able to go full speed?
I've seen injection type designs where this is done, but they have a separate loop between the main loop and the heat exchanger. I'm not sure why that separate loop is set up the way it is.
Okay, looking at this again, I guess they are using closely spaced Tees instead of the hydraulic separator in the Caleffi diagram (and like I have in my system). I was thinking it was an extra-extra loop when I first looked at it. They also don't have a heat exchanger, because they probably have glycol in the whole system.
Let me know if I am understanding you correctly.
You are suggesting that I need a pump on the boiler side of the heat exchanger anyway. Make that a variable speed pump and control it faster or slower to affect what temperature comes out the glycol side of the heat exchanger. I would still have the pump on the glycol side of the heat exchanger. That could be operated at a fixed speed to keep the fluid moving through the pex loops for the snowmelt. So I'd have tempered water, but still full speed flow to the snowmelt.
I guess my question then would be why do people use mixing valves more than injection systems like this? I read something about flow balancing being a factor in the injection design, but I don't know exactly what they meant.
Thanks,
David
0 -
You could go to injection mixing rather than a mixing valve, but that's much more expensive than a simple mixing valve and requires an additional circulator. Simply slowing down the flow to the snowmelt would raise the supply temperature, if anything. A typical 3 way thermostatic mixing valve is by far the cheapest and simplest option here0
-
Yup, that's it.davidd said:You are suggesting that I need a pump on the boiler side of the heat exchanger anyway. Make that a variable speed pump and control it faster or slower to affect what temperature comes out the glycol side of the heat exchanger. I would still have the pump on the glycol side of the heat exchanger. That could be operated at a fixed speed to keep the fluid moving through the pex loops for the snowmelt. So I'd have tempered water, but still full speed flow to the snowmelt.
I guess my question then would be why do people use mixing valves more than injection systems like this? I read something about flow balancing being a factor in the injection design, but I don't know exactly what they meant.
I heard here somewhere that injection mixing doesn't work very well, and I have no actual experience—but I do live a block away from a Holiday Inn Express and if I ever get a round tuit that's how I would repipe the radiant floor at my church to decouple it from the hydro air and convectors. YMMV.0 -
I was working through this in response to the reply from @ratio. I would need a circulator on both sides of the heat exchanger anyway. I was originally thinking the circulator for my hydronic air handler could be used to move water through that loop, but it dawned on me that won't work. If I have the water go through the heat exchanger before the hydronic coil, I'll get cold air blowing out of our registers when the snowmelt and air are running at the same time. If I have the water go through the air handler before the heat exchanger, I'll send lower temp water to the snowmelt, which will take longer for it to come up to temp.GroundUp said:You could go to injection mixing rather than a mixing valve, but that's much more expensive than a simple mixing valve and requires an additional circulator. Simply slowing down the flow to the snowmelt would raise the supply temperature, if anything. A typical 3 way thermostatic mixing valve is by far the cheapest and simplest option here
If I need a pump on both sides of the heat exchanger anyway, then I am not seeing how it would be less expensive to use the mixing valve. Can you help me with understanding that?0 -
ratio said:
Yup, that's it.davidd said:You are suggesting that I need a pump on the boiler side of the heat exchanger anyway. Make that a variable speed pump and control it faster or slower to affect what temperature comes out the glycol side of the heat exchanger. I would still have the pump on the glycol side of the heat exchanger. That could be operated at a fixed speed to keep the fluid moving through the pex loops for the snowmelt. So I'd have tempered water, but still full speed flow to the snowmelt.
davidd said:I guess my question then would be why do people use mixing valves more than injection systems like this? I read something about flow balancing being a factor in the injection design, but I don't know exactly what they meant.
Thanks for sticking with me while I worked through what you were suggesting. I appreciate it. In fact, her is a token of my appreciation!ratio said:I heard here somewhere that injection mixing doesn't work very well, and I have no actual experience—but I do live a block away from a Holiday Inn Express and if I ever get a round tuit that's how I would repipe the radiant floor at my church to decouple it from the hydro air and convectors. YMMV.
That's what I read too (that injection mixing doesn't work very well). I may have also read injection mixing designs work better for very large system, rather than residential. I just don't know *why* the injection mixing doesn't work well, or how to make it work better vs worse. I gave up on that idea when I read that it might be problematic. But I'm willing to take another look at it.
Maybe someone else here knows why variable speed injection mixing is problematic?
@ratio, how is the radiant floor plumbed in with your hydronic air system now?
0 -
What the injection mixing could do is watch the boiler return and modulate accordingly, so you always have adequate swt for the heat.A thermostatic mix valve would not have that function, but you could limit the gpm to the melt, which would limit its output.
Injection mix would require two pumps and the control to operate them
Some of the snowmelt controls have the injection mixing function also
As you mentioned the injection mix, via variable speed would handle this bestBob "hot rod" Rohr
trainer for Caleffi NA
Living the hydronic dream0 -
Regarding watching the boiler return temperature... With the modulating boiler, it is always going to try to keep me getting 140 out. What am I missing there? If the boiler return temperature drops down, the boiler should ramp up to keep the supply out at 140, right?hot_rod said:What the injection mixing could do is watch the boiler return and modulate accordingly, so you always have adequate swt for the heat.
A thermostatic mix valve would not have that function, but you could limit the gpm to the melt, which would limit its output.
Injection mix would require two pumps and the control to operate them
Some of the snowmelt controls have the injection mixing function also
As you mentioned the injection mix, via variable speed would handle this best
I'm hoping to set up a simple mode for things to operate, with aquastats or something similar. I can't justify the high cost of the pro controls from the big names, for more advanced efficiencies, but I work in IT, so I should be able to program something to provide the advanced mode. I plan to have a switch for each mode of operation (simple/advanced). That way, if the advanced mode breaks, I still have simple mode to fall back on.
I'm not seeing how the injection mixing requires a separate pump, in my case. I think I need to use a different pump than the hydronic air pump I have now anyway. Running the heat exchanger and the hydro coil in series is going to make one or the other cold. By having a separate pump for each, I would prevent that. This is separate from the concept of how to control temperature to the snowmelt pex runs.
I've read that injection mixing can be problematic. Any idea why it might be difficult to make work properly?
Thanks again for your help. You've helped me in the past, and it is greatly appreciated.0 -
Injection pumping is basically a heating loop (that requires its own pump) & an injection 'loop' (supply & return) (that requires its own pump) fed from a boiler loop (that requires its own pump). Usually the injection point is closely spaced tees in the heating loop, but in your case it's going to be the HX.
My radiant floor went in in the 50's, it's 1 or 1¼" threaded pipe on ≈30" centers. It was originally controlled by starting the circ based on return water temp (I think), with a boiler bypass line & a globe valve throttling the supply water. Currently I start the pump based on a slab sensor I drilled up to near the surface (I hope!) from underneath & use the same globe valve to set the supply temp to around 80°. It works, but my end goal is to separate the loop completely, run the loop circ on ∆T & inject to control the temp. I think with that setup, I can do a reset on the slab, that is, inject more BTUs when it's colder than when it's warmer. It takes a week for the slab to noticably cool.
0 -
You need to add some more data to get the correct answer.
Boiler is 170K actual output? Tied to a primary loop capable of 17 gpm?
What is the size of the air handler, btu/hr or gpm is 140F adequate for supply? If the coil runs a 20∆ you have 120F in the primary loop to the snowmelt zone. On cold start you may see 30F returning from the SIM, so you need enough injection gpm and temperature to get that up to 90F or so. But the loop needs to still be maintained high enough to heat.
Then define a number of btu/hr that you want to send to the melt zones? 100- 125 btu/ sq ft for reasonably fast recovery for a slab that is not idled. GPM required? Figure a 120- 130F SWT for the SIM, 25 ∆.
Adjust for the glycol % in the SIM loop 40- 45% depending on the brand of glycol should be adequate.
With some additional info you can then add all the numbers into the mixed temperature formula, see what temperature the snowmelt will pull the primary loop down to. If you want to maintain the fan coil at 140F you may need to run the boiler temperature a bit higher so you don't drop too low for the coil to give you adequate temperature output.
At days end it comes down to your expectation from the SIM and what it will take to get there. Class 1 would be a minimum, if you are spending the time and money to melt snow.
Some Uponor and ASHRAE info.Bob "hot rod" Rohr
trainer for Caleffi NA
Living the hydronic dream0 -
Thanks @hot_rod . That will take some time for me to digest.hot_rod said:You need to add some more data to get the correct answer.
Boiler is 170K actual output? Tied to a primary loop capable of 17 gpm?
What is the size of the air handler, btu/hr or gpm is 140F adequate for supply? If the coil runs a 20∆ you have 120F in the primary loop to the snowmelt zone. On cold start you may see 30F returning from the SIM, so you need enough injection gpm and temperature to get that up to 90F or so. But the loop needs to still be maintained high enough to heat.
Then define a number of btu/hr that you want to send to the melt zones? 100- 125 btu/ sq ft for reasonably fast recovery for a slab that is not idled. GPM required? Figure a 120- 130F SWT for the SIM, 25 ∆.
Adjust for the glycol % in the SIM loop 40- 45% depending on the brand of glycol should be adequate.
With some additional info you can then add all the numbers into the mixed temperature formula, see what temperature the snowmelt will pull the primary loop down to. If you want to maintain the fan coil at 140F you may need to run the boiler temperature a bit higher so you don't drop too low for the coil to give you adequate temperature output.
At days end it comes down to your expectation from the SIM and what it will take to get there. Class 1 would be a minimum, if you are spending the time and money to melt snow.
Some Uponor and ASHRAE info.
To answer some of your questions...
The boiler's own loop, according to buderus, shouldn't go higher than 20 gpm. It ships with a grundfos UPS15-58, which has a max of about 17 gpm (with no head). I believe there is about 4 feet of head through the boiler, and that I end up with about 14 gpm as a result. It has a hydraulic separator/low loss header. The btu output rating is 176,300 BTU DOE, and 168,000 BTU Net IBR.
Their is a DHW priority loop on the same side of the hydraulic separator as the boiler, but that can be ignored for the sake of this discussion.
On the other side of the hydraulic separator is my air handler loop. It has a 30+ year old taco pump in the air handler (reused from old Lennox CompleteHeat that I had before the Buderus boiler). I have reason to believe it is pushing about 9.5 gpm.
The air handler is rated for 105,000 BTU with 140 degree water.
You said, "If the coil runs a 20∆ you have 120F in the primary loop to the snowmelt zone. On cold start you may see 30F returning from the SIM, so you need enough injection gpm and temperature to get that up to 90F or so. But the loop needs to still be maintained high enough to heat."
So are you thinking the return water from the hydronic coil will go into the supply port of the glycol heat exchanger? That is what I was thinking at first too, but now I am thinking I should have it plumbed so that both the hydronic coil and the heat exchanger see 140 degree water. With a variable speed pump going to the heat exchanger, it could slow down the delivery of the 140 degree water to the heat exchanger, such that the glycol loop on the other side would see lower temperatures, when the snowmelt surface is up to temp (and not needing as much heat input).
Is the question whether the boiler's own loop (14 net gpm, set to 140 degree water, when on space heating mode) has enough heat capacity to keep up with the air handler and the snowmelt at the same time? My thought (which might be ignorant) was that the air handler is only taking out 105K btu, so there is roughly 65k capacity remaining (if we use 170k as the capacity of the boiler).
I think one problem with me looking at it this way is the btus/sq ft often used are for once the snowmelt gets up to temp. From a cold start, it can be much higher. That may be what you are pointing out. It seems it would really be a matter of how fast you want to get up to temp. My left over 65k btu could get sucked up easily with enough gpm going through the heat exchanger on the supply side.
With the above in mind, having a variable speed pump delivering water to the heat exchanger might allow me to reduce the risk of taking out too much heat too fast, when bringing the snowmelt up to temp. Off the top of my head, if the system monitors the supply into the hydronic coil, and that starts dipping down below 140, then it could back off on the speed of the pump delivering water to the heat exchanger. This type of dynamic adjustment would always have the snowmelt getting up to speed as fast as it can, without sacrificing heat at the air registers. Does that sound reasonable?
A few things to note:
- As for my expectations of the snowmelt, they are pretty low. "Ability not to need to shovel snow, with an allowance for walking on snow." is how the requirement would read. I am fine with it taking its time to do the melting. Less concerned with snow than I am with ice. Ice usually happens when it is warmer (which means less time for the system to come up to speed). Although some types of snow might be slippery, those usually happen when it is warmer too. It is Minnesota. We are used to walking on/through snow.
I may be adding some other snowmelt areas in the future. This first one will be a good test case to see how it works. I already planned to have the next area be able to be run at a different time than this first one, because it would be larger and I didn't think I'd have enough boiler capacity to run both concurrently. I wasn't even sure I'd have enough capacity for the 2nd area and my hydronic air running concurrently. After this discussion of bringing things up to temp, I am inclined to split that future 2nd area into 2 or 3 zones. That way I can run one zone at a time, if needed, and just cycle through the zones to complete the snow removal.
I already planned to have at least 2 zones in this first area. There is a higher area that may require more btus/different runtime, or I may want it to run by itself (more chance for ice there). I also plan to have a French drain on the edge of the snowmelt. I may have a 3rd zone next to it, to ensure water can flow into it and doesn't start freezing as it leaves the snowmelt area. I may find out that isn't needed. If so, I simply won't run that zone. I'd rather spend the money on some extra pex, and not use it, than have it back up from ice.
- My snowmelt won't be a slab. It will be in sand, under pavers. This may make it slower to respond than concrete, especially before the snow starts melting. Once it starts melting, the conduction of heat through the sand should increase, in theory. But pavers, with the inherent gaps between them, aren't going to conduct much, laterally. And the total mass being heated is more than it would be with pex a couple inches below the surface in a concrete system.
- The reason 140 degrees is important for the hydronic air system is because lowering it too much can make it feel drafty by the registers, since they are seeing a lower temperature than the coil. It will still heat the house with a lower temp. I don't know how cold out it would have to be, at a given temp, before it wouldn't be able to keep up. We haven't experienced that yet, to the best of my knowledge, at 140 supply temp.
Having said that, the drafty feeling by the registers might not be critical. I don't know if there are many registers where someone hangs out for any length of time, other than the cats and dogs (and man, do they love sitting by the registers). The main thing is that the rooms are able to keep up with the thermostat.
Secondly, the drafty nature is a function of fan speed in the air handler. If I reduce air speed along with a reduction in supply temp to the hydronic coil, that could help to keep the register temps from getting too low. It has been on my to-do list for years, to automate this. I purchased a special board that I hope to use to control the boiler temp. The original blower motor was replaced a few years ago with an ECM blower motor than I should be able to control with 0-10 volts DC. I have it wired for fixed speeds right now (one speed for AC and one for heat).
If I can control the boiler temp and blower speed, I can reduce cycling the boiler. I could have the boiler and the blower back off as the room temp approaches the thermostat set point. In an ideal case, it would run continuously, never crossing the setpoint, but hovering just under it. I have semi-smart thermostats, so I should be able to get a read on their settings and what temp they are seeing in my (to be) control system.
All that is to say that, with some additional automation, I might be able to get by on less than 140 degree water to the hydronic coil, and more of my boiler capacity could go to other heating loads, like the snowmelt.
Thanks again for the detailed reply. The back and forth helps me in considering things that are second nature to the professionals. Hopefully the exchange will help others who might come across this post in the search for answers to similar questions too.
David
0 -
My best guess, at this point, is that a normal/typical variable speed injection mixing system, with the closely spaced Tees, is more challenging than what we are proposing. Because the water is truly being mixed, in the closely spaced Tees arrangement, there is more math around the pressures/hydraulics, and possibly unwanted heat migration when inactive, than there is when a heat exchanger is used instead of the closely spaced Tees.ratio said:Injection pumping is basically a heating loop (that requires its own pump) & an injection 'loop' (supply & return) (that requires its own pump) fed from a boiler loop (that requires its own pump). Usually the injection point is closely spaced tees in the heating loop, but in your case it's going to be the HX.
My radiant floor went in in the 50's, it's 1 or 1¼" threaded pipe on ≈30" centers. It was originally controlled by starting the circ based on return water temp (I think), with a boiler bypass line & a globe valve throttling the supply water. Currently I start the pump based on a slab sensor I drilled up to near the surface (I hope!) from underneath & use the same globe valve to set the supply temp to around 80°. It works, but my end goal is to separate the loop completely, run the loop circ on ∆T & inject to control the temp. I think with that setup, I can do a reset on the slab, that is, inject more BTUs when it's colder than when it's warmer. It takes a week for the slab to noticably cool.
Wow, that sounds like quite the system. Is that pipe in concrete?
A week to cool! That's wild. I imagine it takes quite a bit to get it up to temp too then?
How many square feet and how big is the boiler? Fixed temp or modulating boiler?0 -
The injection mixing itself would require a variable speed circulator and control in addition to the two circulators already required to move fluid. Last time I saw a VS circ and control package, it was about $800. A regular Honeywell AM series mixing valve is nearly bulletproof and is around $100. 100<800, hence why the mixing valve approach is much less costly and also much simpler and more reliable.davidd said:
I was working through this in response to the reply from @ratio. I would need a circulator on both sides of the heat exchanger anyway. I was originally thinking the circulator for my hydronic air handler could be used to move water through that loop, but it dawned on me that won't work. If I have the water go through the heat exchanger before the hydronic coil, I'll get cold air blowing out of our registers when the snowmelt and air are running at the same time. If I have the water go through the air handler before the heat exchanger, I'll send lower temp water to the snowmelt, which will take longer for it to come up to temp.GroundUp said:You could go to injection mixing rather than a mixing valve, but that's much more expensive than a simple mixing valve and requires an additional circulator. Simply slowing down the flow to the snowmelt would raise the supply temperature, if anything. A typical 3 way thermostatic mixing valve is by far the cheapest and simplest option here
If I need a pump on both sides of the heat exchanger anyway, then I am not seeing how it would be less expensive to use the mixing valve. Can you help me with understanding that?0 -
Better yet if you have a hydraulic separator. Now your loads are parallel instead of series in a P/S loop.
If you want to glycol the entire system, just connect the SIM directly to the sep.
Or separate the SIM with a plate HX and glycol just that portion. It will need an air sep and expansion tank also, and a glycol fill tank. I prefer this to glycol in the entire system.
If you add a 132 Quicksetter on the SIM pump discharge, just adjust that to take as much as the boiler can keep up with.
Sounds like you don't know how many btu the air handler needs to provide? That would be the heatload of the home at design condition. The AH is rated for 105,000 but do you need 105,000, or is 60 or 80,000 enough to heat the home.
You could add a balance valve on the AH also, adjust it to just the amount of flow you need on a cold design day, the rest is available for SIM.
Looks like you have adequate boiler capacity, the goal, I think, would be give the snow melt all it can take and still warm the home.
No need for a mix valve or injection mix, as both would require you run the boiler much higher, maybe 150 or 160 for the mix stations to work properly. You lose boiler efficiency when return to boiler is above 130.Bob "hot rod" Rohr
trainer for Caleffi NA
Living the hydronic dream0 -
Yeah, that's what I want -- water for the hydro air and DHW and glycol for the cold radiant loads (snowmelt and in floor heat, with bare ground under it, hence the need for glycol, as a later addition).hot_rod said:Better yet if you have a hydraulic separator. Now your loads are parallel instead of series in a P/S loop.
If you want to glycol the entire system, just connect the SIM directly to the sep.
Or separate the SIM with a plate HX and glycol just that portion. It will need an air sep and expansion tank also, and a glycol fill tank. I prefer this to glycol in the entire system.
I'm not visualizing what this would look like. Are you saying to throttle the flow going into the snowmelt glycol runs with a separate balancing valve between the pump (the pump on the snowmelt side of the heat exchanger) and the manifold (which will also have balancing valves)?hot_rod said:
If you add a 132 Quicksetter on the SIM pump discharge, just adjust that to take as much as the boiler can keep up with.
That's correct. I did some math a number of years ago, but I'm not sure if I still have that somewhere. I know it provides more than enough. It cycles on and off, as needed, to satisfy the thermostats (3 air zones, but only 2 are in use).hot_rod said:
Sounds like you don't know how many btu the air handler needs to provide? That would be the heatload of the home at design condition. The AH is rated for 105,000 but do you need 105,000, or is 60 or 80,000 enough to heat the home.
That's an idea. I am guessing that would have the same effect as lowering the supply temperature to the hydro coil though. There would be less heat delivered, but the same airflow, so the registers might feel like they are blowing cold air. However, as I said before, that might not be critical.hot_rod said:
You could add a balance valve on the AH also, adjust it to just the amount of flow you need on a cold design day, the rest is available for SIM.
Yep. I think that's probably what I can shoot for. I hadn't thought about the extra load to bring the snowmelt up to temp, and that the heat going to the snowmelt during that phase might need to be held back a bit (so the house would have enough heat). Thanks for pointing that out.hot_rod said:
Looks like you have adequate boiler capacity, the goal, I think, would be give the snow melt all it can take and still warm the home.
Is it still considered injection mixing if I am pushing water at a heat exchanger with a variable speed pump and controlling how fast it receives the heat? And is there any reason why I'd need to run the boiler at a higher temperature for that type of design? I haven't considered the traditional injection mixing (with closely spaced Tees), because I want to have the heat exchanger anyway to separate the water from the glycol.hot_rod said:
No need for a mix valve or injection mix, as both would require you run the boiler much higher, maybe 150 or 160 for the mix stations to work properly. You lose boiler efficiency when return to boiler is above 130.
I think I'd rather have some variable control over the energy going into the heat exchanger, because I'll have different heat loads over time on the glycol side of the heat exchanger. The under floor heat (future state) will require far less input than the snowmelt areas. I'm pondering whether I want all these types of radiant loads getting heat from the same heat exchanger, and adjusting how much heat gets to the heat exchanger with a variable speed pump on the input side of the heat exchanger. My other option is to have one heat exchanger for the snowmelts and a different one for the under floor heat areas. That means needing another pump, another pressure tank, and all the other goodies.
If I put everything on one heat exchanger, when the higher temperature is being sent to the heat exchanger, the thermostat for the under floor heat will simply cycle the zone off and on more than it otherwise would. When the snowmelt isn't active, I'd lower the temperature to the underfloor heath (by slowing the flow to the heat exchanger), and it would ideally hover just under the thermostat setting for the floor rather than cycling the whole thing off and on. Eventually, I might even be able to programatically lower the temperature coming out of the boiler -- either when the hydro isn't running, or because I am also able to (at that time) adjust the hydro blower speed down to match the lower temp going to they hydro coil. That, I think, would be optimal as far as efficient use of natural gas, because I'd get more condensing in the boiler.
I just saw your attachment. Putting it inline here:
I'd be aiming for the lower option (with the heat exchanger). What is the "E" in that one?
Thanks again!
David0 -
Ah, okay. So you are talking about thermostatic mixing valve instead of a 3 way valve that has a motor on top and a control system. For some reason, I was thinking the all-in-one thermostatic mixing valves weren't appropriate for this type of thing. I guess, with that style, there wouldn't be a way to send more heat to get the snowmelt up to temp and less heat once it does get up to temp.GroundUp said:
The injection mixing itself would require a variable speed circulator and control in addition to the two circulators already required to move fluid. Last time I saw a VS circ and control package, it was about $800. A regular Honeywell AM series mixing valve is nearly bulletproof and is around $100. 100<800, hence why the mixing valve approach is much less costly and also much simpler and more reliable.</p>davidd said:
I was working through this in response to the reply from @ratio. I would need a circulator on both sides of the heat exchanger anyway. I was originally thinking the circulator for my hydronic air handler could be used to move water through that loop, but it dawned on me that won't work. If I have the water go through the heat exchanger before the hydronic coil, I'll get cold air blowing out of our registers when the snowmelt and air are running at the same time. If I have the water go through the air handler before the heat exchanger, I'll send lower temp water to the snowmelt, which will take longer for it to come up to temp.GroundUp said:You could go to injection mixing rather than a mixing valve, but that's much more expensive than a simple mixing valve and requires an additional circulator. Simply slowing down the flow to the snowmelt would raise the supply temperature, if anything. A typical 3 way thermostatic mixing valve is by far the cheapest and simplest option here
If I need a pump on both sides of the heat exchanger anyway, then I am not seeing how it would be less expensive to use the mixing valve. Can you help me with understanding that?
Regarding the pricing for the variable speed circulator, I wouldn't be buying an advanced control for it. I'd be trying to figure out how to make it work with relatively simple controls (in a suboptimal way) for a "simple mode". I'd also use custom controls, that I'd create and program, for an "advanced mode". So my situation is a little different than some who might not have a desire to build their own controls. The reason for both methods is so I'd still have a fallback if the advanced controls failed or needed to be worked on.
Thanks,
David
0 -
I suppose there are different definitions for injection mixing. Typically you inject a high temperature to mix with the colder return to get a desired output. To do that, obviously you need a temperature above 140 to blend with cold return to get 140. 140 blended with 30 degree will not get you 140. I sent the formula a few posts up if you want to know exactly
since you don’t have any exact loads numbers for any of the loads the math gets wonky
So by sending 140 directly from the boiler to the sim its not injecting in my mind. But call it what you want
Im trying to keep the boiler in a best efficiency mode. Its kind of silly to buy a mod con and run it at 160 just to do injection mixing?
From the boiler directly to the HX is the path of least resistance
A balance valve regulates flow, heat output by reducing flow instead of temperature. A balance valve is considered a fine tuning device
Unless you have money to burn and you want extra complexity, I don’t see any reason for variable speed pumping?
send as much flow and temperature to the SIM to get the job done and shut it off. It will coast for a few hours after you stop flow.
Its not a comfort issue where you might modulate flow or temperature to maintain a consistent radiant floor temperature for example. You are heating the great outdoors
I think with pavers in sand you will want 130- 140 swt
E is for expansion tankBob "hot rod" Rohr
trainer for Caleffi NA
Living the hydronic dream0 -
Yup, encased in concrete. I imagine the slab varies from 4 to 8+ inches, if my experiences with similar vintage slabs are any indication.davidd said:Wow, that sounds like quite the system. Is that pipe in concrete?
A week to cool! That's wild. I imagine it takes quite a bit to get it up to temp too then?
Yeah, it's not exactly quick responding. I know it takes a week to cool because a few years ago our insurance inspector 'tested' the high limit by turning it down until it tripped, but he forgot to turn it back up so it tripped again. It was 8-9 days before I started getting complaints!How many square feet and how big is the boiler? Fixed temp or modulating boiler?
it's around 5000 feet², fed from a 5 section Peerless 211A (net I.B.R 584k) that also feeds two 10 ton air handlers & various convectors.
0 -
Yeah, it's not exactly quick responding. I know it takes a week to cool because a few years ago our insurance inspector 'tested' the high limit by turning it down until it tripped, but he forgot to turn it back up so it tripped again. It was 8-9 days before I started getting complaints!ratio said:
Yup, encased in concrete. I imagine the slab varies from 4 to 8+ inches, if my experiences with similar vintage slabs are any indication.davidd said:Wow, that sounds like quite the system. Is that pipe in concrete?
A week to cool! That's wild. I imagine it takes quite a bit to get it up to temp too then?
How many square feet and how big is the boiler? Fixed temp or modulating boiler?
it's around 5000 feet², fed from a 5 section Peerless 211A (net I.B.R 584k) that also feeds two 10 ton air handlers & various convectors.
And 8-9 days before they stopped complaining?
So does that boiler have a way of operating where it heats water, but doesn't run steam? And then you are taking from the water and feeding it to a heat exchanger, with the radiant loads on the other side of the exchanger? If so, then you want to eventually split it out so the floor and the other 2 types of loads are on different heat exchangers?
If it has one heat exchanger now, does your floor zone cycle off and on, because it is receiving hotter water (that the other loads need) than it needs?
The reason I am asking, besides curiosity, is because if the above is true, then you are trying to solve for a problem I will have to solve for if I go down this path of using a variable speed pump on the boiler side of the heat exchanger to vary the temperature on the glycol side. In my situation, future state, I will have multiple snowmelt zones and a couple underfloor heat zones. The underfloor heat will want lower temps than the snowmelt. With simple controls, it would mean the floor heat zones cycling their zone valves off and on. With more advanced controls, I can vary the speed of the pump pushing water to the shared heat exchanger when the snowmelt is inactive, lowering the temps the foot heat zones see, and reducing cycling those zone valves.
The above (adjusting the shared heat exchanger temperature depending on which loads are active) works, because my snowmelt will be relatively seldom used, and the underfloor heat used more often. In your case, you probably want all heat loads running at all times.
One alternative for me is to run 2 heat exchangers and 2 variable speed pumps into them, giving the snowmelt the temp it wants and the in floor heat the team it wants. If what I guessed about your arrangement is true, that is what you'd like to do as well (different temp to the hydro/panels vs the in floor heat).
In my case, my current thought is the added cost of a second closed glycol loop for my underfloor heat, and another pump to drive it, isn't worth it. The snowmelt system won't be used that much, so the minor additional wear and tear on the floor zone valves and temporary temperature swings of the floors are acceptable compromises.
David
0 -
It's a straight hot-water boiler. Just a different trim kit to make it steam or water.davidd said:So does that boiler have a way of operating where it heats water, but doesn't run steam? And then you are taking from the water and feeding it to a heat exchanger, with the radiant loads on the other side of the exchanger? If so, then you want to eventually split it out so the floor and the other 2 types of loads are on different heat exchangers?
I really need two different temperatures, cooler water for the radiant floor & hotter water for the convectors. The air handlers have (actually had, one needs work) 3 way valves so they can handle hotter supply water already, but the convectors need the water as hot as they can get it.
If it has one heat exchanger now, does your floor zone cycle off and on, because it is receiving hotter water (that the other loads need) than it needs?
No HX now, I manually balance the supply water to the floor loop with a valve & just turn the pump off when the temp starts to climb. I want that to be automatic and metered, & eventually just inject more BTUs when it's cold out than when it's warmer out.The reason I am asking, besides curiosity, is because if the above is true, then you are trying to solve for a problem I will have to solve for if I go down this path of using a variable speed pump on the boiler side of the heat exchanger to vary the temperature on the glycol side. In my situation, future state, I will have multiple snowmelt zones and a couple underfloor heat zones. The underfloor heat will want lower temps than the snowmelt. With simple controls, it would mean the floor heat zones cycling their zone valves off and on. With more advanced controls, I can vary the speed of the pump pushing water to the shared heat exchanger when the snowmelt is inactive, lowering the temps the foot heat zones see, and reducing cycling those zone valves.
I think you're over-thinking things. I don't think you're going to need glycol in the radiant floor, so just run it off a 3-way valve, tapped in to the boiler loop, like normal. The SIM loops will need glycol, so a HX for it. A SIM loop circ, maybe ΔP if you are going to control the various loops individually, an injection pump with a temp sensor on the outlet of the SIM side of the HX. The injection pump will only need to run when the SIM is operating, so a little bit of controls work.
The above (adjusting the shared heat exchanger temperature depending on which loads are active) works, because my snowmelt will be relatively seldom used, and the underfloor heat used more often. In your case, you probably want all heat loads running at all times.
One alternative for me is to run 2 heat exchangers and 2 variable speed pumps into them, giving the snowmelt the temp it wants and the in floor heat the team it wants. If what I guessed about your arrangement is true, that is what you'd like to do as well (different temp to the hydro/panels vs the in floor heat).
In my case, my current thought is the added cost of a second closed glycol loop for my underfloor heat, and another pump to drive it, isn't worth it. The snowmelt system won't be used that much, so the minor additional wear and tear on the floor zone valves and temporary temperature swings of the floors are acceptable compromises.
David1 -
Yep, that sounds like a good plan. I wasn't sure how the return water from a regular injection mixing arrangement would compare to the return glycol hitting the heat exchanger. I like the path of least resistance though.hot_rod said:Im trying to keep the boiler in a best efficiency mode. Its kind of silly to buy a mod con and run it at 160 just to do injection mixing?
From the boiler directly to the HX is the path of least resistance
My thought there is that I don't want to waste energy heating it more than it needs to be. If it needs to get to 35 degrees to melt snow, then I don't want to overshoot that to 40, 50, 60, etc. If I shut it off when it reaches 35, then it might get down to below freezing again before the snow is melted (either too much snow when it starts melting or the snow has continued to fall). My thought was that I could keep it at 35 degrees, by changing the heat into the heat exchanger, until the snow is gone, and then allow X minutes for drainage/evaporation. Some of that X minutes can be with the system turned off, because there will be some amount of coasting, like you said.hot_rod said:
I don’t see any reason for variable speed pumping?
send as much flow and temperature to the SIM to get the job done and shut it off. It will coast for a few hours after you stop flow.
Its not a comfort issue where you might modulate flow or temperature to maintain a consistent radiant floor temperature for example. You are heating the great outdoors
Thanks!
David
0 -
Ah, okay. So more about automation. Got it.ratio said:No HX now, I manually balance the supply water to the floor loop with a valve & just turn the pump off when the temp starts to climb. I want that to be automatic and metered, & eventually just inject more BTUs when it's cold out than when it's warmer out.
Unfortunately, for the 2 inside areas that are part of this discussion, I do need glycol. It is somewhat of a worse case scenario where one of the rooms has a high ceiling and one outside wall, and the other (which is 4 steps down from the first one, as the house is on a hill) has a vaulted ceiling with 3 outside walls. There is a chance I could get by without gycol for the first room mentioned, but not the second. That second flooring is above a crawl space that has ground as a floor and not much around the 3 outside "walls". The risk would be too high, even with a ton of insulation, that the cold could eventually freeze it. I would be worried that the end of the first flooring that butts up to the crawl space for the second flooring would be at risk of freezing too. The radiant will only be on as desired, not on all the time, so it won't be saving itself from freezing.ratio said:I think you're over-thinking things. I don't think you're going to need glycol in the radiant floor, so just run it off a 3-way valve, tapped in to the boiler loop, like normal. The SIM loops will need glycol, so a HX for it. A SIM loop circ, maybe ΔP if you are going to control the various loops individually, an injection pump with a temp sensor on the outlet of the SIM side of the HX. The injection pump will only need to run when the SIM is operating, so a little bit of controls work.
However, if I add underfloor heating to any other areas in the house, those can be run off the non-glycol side of the system. There is a ground level bathroom and hallway and a couple bedrooms that could be done. I may not want to spend the time and money for those, as they are adequately heated with hydro air.
Due to the open floor plan of the two rooms mentioned above, heating the air isn't efficient, and their floors are darn cold. There is a gas fireplace in the lower of the 2 rooms, so that is what is used to provide comfort. That doesn't do much to heat the floor, and sends a lot of heat up to a loft overlooking the room in question. A window is often opened in the loft, because it gets too warm up there with the fireplace going. The radiant underfloor heating will hopefully solve for some of these issues (more efficiency, better comfort).
As for equipment, I can get by with less equipment and controls, and it would most likely work fine. I'm going to add a bit more to it in order to optimize the energy usage. This may be more for the "fun" of it, than for net cost savings. However, having said that, I imagine some cost savings on the snow melt side of it could add up over time. Much of that depends on mother nature too. Last winter, in Minnesota, we had a lot of snow. This year, I haven't had to do any snow removal to speak of (KNOCK ON WOOD).
This isn't something that most people would want/need to do. It is more of the type of thing people who are into home automation might venture into. Software and devices exist that can provide the type of control the really expensive radiant controls allow for, yet with more flexibility than those systems and with less expense. Simplified controls might have better reliability, however, so I want to make the system work with standard controls and then override those with the more advanced solutions. If the advanced solutions go down, I can switch back to the standard controls.
David0 -
The universal hydronic formula may answer many of your questions.
as for snow melting and other design questions Q (quantity of heat)= 500 X flow X delta T
Assume you have a fixed flow to the SIM loops call it 4 gpm
500 X 4 X (100swt-30rwt ) = 140,000 btu/ hr delivered to the slab
Now assume you want to just supply 35° to the slab, for whatever reason
500 X 4 x (35swt -30rwt) = 10,000 btu/hr
As you see the delta T dictates how much heat you can move into the slab.
While technically you can melt snow at 35° swt, it may take days to get the job done. Sure 35 SWT will be more efficient operating SWT, but SIM and efficiency are not usually in the same sentence
Typically folks want to see the snow go away quickly, so concrete can take up to 150F according to the Uponor design manual.
Some customers feel they should be able to flick a switch and the snow instantly disappears. Like a garbage disposal.
At the flow rates and the boiler output you have to share, I doubt you will shock the slab by warming it too fast.
There comes a point when it makes more sense to have two separate boilers. A dedicated SIM boiler allow the heating loads to balance those different SWT better. Ant to eliminates that 30° concrete flywheel messing with heating loads.Bob "hot rod" Rohr
trainer for Caleffi NA
Living the hydronic dream1 -
I meant maintaining a surface temperature of 35 degrees, not a supply water temperature of 35 degrees.hot_rod said:
Now assume you want to just supply 35° to the slab, for whatever reason
500 X 4 x (35swt -30rwt) = 10,000 btu/hr
As you see the delta T dictates how much heat you can move into the slab.
While technically you can melt snow at 35° swt, it may take days to get the job done. Sure 35 SWT will be more efficient operating SWT, but SIM and efficiency are not usually in the same sentence
I can get it up to that temp as fast as the boiler will allow. But then I'd like to throttle back on the heat to the exchanger, such that the surface temp stays constant. That's my best guess at optimizing it for falling snow. For pre-existing snow, I guess some real world tests will reveal what is most efficient -- cooking it at max heat until the snow is melted, or the throttle back approach. I suspect going low and slow (like cooking pork) will provide some efficiencies on the condensing side.
Real world tests, in and of themselves, will be a challenge, since there are so many variables:- air temperature
- humidity
- wind speed
- starting ground temperature
- dew point
- snow amount
- length of snowfall
- "type" of snow
That would be fun, albeit a bit noisy.hot_rod said:
Some customers feel they should be able to flick a switch and the snow instantly disappears. Like a garbage disposal.
Maybe store some solar in a molten salt, underneath the snowmelt area, with an insulated top. When they flip the switch, with 2 feet of snow, the insulation slides away, the area splits down the middle, and the 2 sides are hydraulically raised, causing the snow to slip down onto the 1000 degree griddle below.
With a bigger area to melt, that's probably where I'd have to go. But with my modest needs (smaller area, not often used, no big rush to do the melting), I can't justify another system. It is definitely more challenging to have wildly disparate heat loads in one system. But life can be boring without challenges, right?hot_rod said:
There comes a point when it makes more sense to have two separate boilers. A dedicated SIM boiler allow the heating loads to balance those different SWT better. Ant to eliminates that 30° concrete flywheel messing with heating loads.
David
0 - air temperature
-
I like complicated. It's a personal failing of minedavidd said:
Ah, okay. So more about automation. Got it.ratio said:No HX now, I manually balance the supply water to the floor loop with a valve & just turn the pump off when the temp starts to climb. I want that to be automatic and metered, & eventually just inject more BTUs when it's cold out than when it's warmer out.
Unfortunately, for the 2 inside areas that are part of this discussion, I do need glycol. It is somewhat of a worse case scenario where one of the rooms has a high ceiling and one outside wall, and the other (which is 4 steps down from the first one, as the house is on a hill) has a vaulted ceiling with 3 outside walls. There is a chance I could get by without gycol for the first room mentioned, but not the second. That second flooring is above a crawl space that has ground as a floor and not much around the 3 outside "walls". The risk would be too high, even with a ton of insulation, that the cold could eventually freeze it. I would be worried that the end of the first flooring that butts up to the crawl space for the second flooring would be at risk of freezing too. The radiant will only be on as desired, not on all the time, so it won't be saving itself from freezing.
I see. I think you're going to end up with both expensive and complicated.0
Categories
- All Categories
- 87K THE MAIN WALL
- 3.2K A-C, Heat Pumps & Refrigeration
- 58 Biomass
- 426 Carbon Monoxide Awareness
- 113 Chimneys & Flues
- 2.1K Domestic Hot Water
- 5.7K Gas Heating
- 109 Geothermal
- 161 Indoor-Air Quality
- 3.6K Oil Heating
- 70 Pipe Deterioration
- 994 Plumbing
- 6.3K Radiant Heating
- 391 Solar
- 15.4K Strictly Steam
- 3.4K Thermostats and Controls
- 55 Water Quality
- 44 Industry Classes
- 48 Job Opportunities
- 18 Recall Announcements