What I Learned During the 1930s

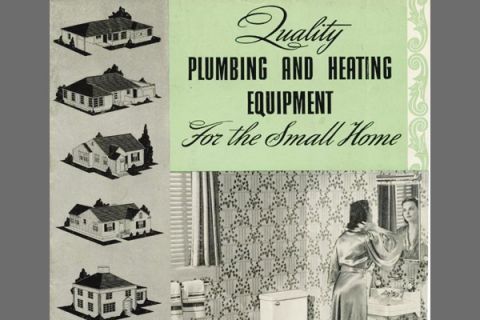
There were a lot of writers then who focused on the art of steam- and hot- water heating back in the 1930s. You can learn a lot by looking back over your shoulder.
Comments
-
Always great to read stories of old. Brings back the times when i started working in the trade in early 60's and many oldtimers were still around, Thanks for the reading Jerry B0
-
Rise of central AC makes a quality hot water system a hard sell.0
-
Cheap does matter. When my 1930 coal to oil to NG American Standard died I couldn't find anyone to replace it. It was hugely expensive to operate anyway. So, we went with a forced air furnace with central AC. It was cheap and there are plenty who can work on it and it cooled the house. Win, win, win.
Eventually, after learning from this site for years, I took a chance and replaced the boiler myself. It wasn't cheap. It was labor intensive. It was time consuming. But I needed something to do so all that didn't matter. It is a third the cost to operate than the old boiler and the heat is way better than the furnace.
1 -
-
"Rise of central AC makes a quality hot water system a hard sell."
This issue has become highly exaggerated, and it really works no different than a gravity system for generating heat. While there were limiting factors to gravity heat systems (mentioned above), there really are no limiting factors to gravity cooling (it's just air rising or falling in open space). It's a shame that some large old homes are being torn down because new owners feel that A/C ducts are required in every room.
Our c1918 6,500 sq. ft. home has 2 attic units that drop cold air from the ceilings of the second floor. Even before my improvements, those units dropped enough cold air down the 2 staircases to adequately cool the first floor. But I replaced both units, bumping up 1/2 ton on each, then replaced all of the lazy-man's flexible duct with proper metal duct to improve air flow, then added 1 extra vent at the top of the large staircase, and added 1 large return at the top of the closed door to the attic where the highest point of the heat rises to. I sense little to no difference on the first floor than if we had forced air ducts in every room. And I didn't have to resort to ugly mini-splits or loud SDHV systems.0 -
Many of the 1950s small ranch houses built in the early 50s around here had the heat on the inside walls and the returns on the outside walls. The returns were panned, and the supplies were ducted, and panning is cheaper than ducting. Didn't work out very well.
My grandfather bought a two family around 1915 which had coal fired hot air. I guess he didn't like it because he had it taken out. Two boilers, radiation and piping installed for less than $800. Both boilers were still running in 1979 when we sold it, both converted to oil0 -
My house has a graduated forced air system that was installed in about 1950 when it was converted from a floor furnace. All the supplies are in the middle of the house and all the returns at the perimeter. It is all rectangular duct all the way to re register boxes, it must have all been custom made in someone's shop, all the rectangular bends are curved. I don't think the difference between where they were panning and where they were building ducts was much of a consideration in layout.EBEBRATT-Ed said:Many of the 1950s small ranch houses built in the early 50s around here had the heat on the inside walls and the returns on the outside walls. The returns were panned, and the supplies were ducted, and panning is cheaper than ducting. Didn't work out very well.
My mom and grandma's houses were built in the mid 50's and both have mostly center supply and perimeter returns as well.0 -
Nice history lesson. It is interesting to see how technology evolves over time. I am not sure the boiler vs. furnace is as simple as cheaper upfront cost. That certainly is an important factor, particularly with the spec home market, but not sure it is the determinant on custom homes.
I think many factors come into play such as widespread adoption of central air and desire for less maintenance. When I built my log house, I looked at several heating options and elected to go with FA for a couple of reasons. The main reason was to facilitate central air and the secondary reason was less maintenance and no risk of damage from a flooded house due to a frozen pipe. I know at least two homes in my area that had $20,000+ repairs after having a heating pipe freeze and burst flooding their home while they were away. No hydronic system saves enough to cover than kind of home repair.
Also, the difference in both comfort and efficiency between a well-designed FA system and a well-designed hydronic system is relatively small today. Similarly, I see little difference in longevity. My house has three Lennox furnaces installed in 1999 and all three are going strong. One furnace has had zero repairs. One furnace had a control board die when it was two years old, but nothing since then. And the third furnace had to have the inducer motor replaced a few years ago. Other than that, no maintenance other than filter changes and no other repairs needed. I don’t know how long they will last, but all three still look and operate like new and I would not be surprised if they last another 20+ years.
I think the differences between systems are not nearly as great as many like to believe when you compare similarly well-designed and competently installed systems. It seems most comparisons are done with well-designed hydronic systems and poorly designed furnaces. No question a lousy furnace installation is going to be much less comfortable and efficient than a good hydronic installation. However, a good modern furnace installation is very good. Most who visit my house have no idea it has FA heat as the temp is always uniform and there is no noticeable noise nor detectable drafts. I only hear my furnace fire up if I am home alone and don’t have a TV or radio on. Even normal conversation completely masks the sound of the furnace.0 -
A WWII Kid, we had a second level non-insulated apartment with a single wood-fired parlor heater. Recall my mother complaining of having to move our ice-skinned galvanized washtub from the kitchen table onto the heater to prep my daily bath.
Folks bought a house with a coal-fired steam "snowman" in 1944. 11+ cords of wood later and never warm Dad installed a Winkler Stoker and life got better.
Moving on since through FHA & FHW systems, here in rural northern New England my vote goes to our current delta-t managed gravity assisted hot water system. Life is good.
Noting your reference to kerosene, grew up with penny-pinching Yankees who used kerosene as a coolant in their old A's & T's & Chevvies. Cheaper than anti-freeze or alcohol when unavailable. Just make sure there weren't any leaks ..... exciting!0 -
Great story! Thanks for the memories.Retired and loving it.0
-
@mattmia2
The curved fittings were called "railroad fittings" sometimes made with aluminum duct.
Usually, the furnace ducts ran down the middle of the house. Using panning to get to the returns on the outside walls meant less ductwork total as they never panned the supplies kept the cost down1 -
I wonder if the center supplies with perimeter returns were a carry over from the gravity air furnaces.
With the returns under the windows for the cold air to get captured and go to the furnace and then the hot air supplies on the inside it seemed like the best for gravity air flow.
I have seen some perimeter return ducting drop down under the basement floor and then thru concrete tunnels end up under the monster "octopus" furnace.
It seems the more vertical and less horizontal air flow for hot air would create more natural draft.
Could it be that it worked well enough then and so logic was applied that it would be even better with blower motors??
Today those huge out of the wall decorative supplies that were fed with 12" or so pipe make for good return air grills.
HO usually likes the looks of them and then they get floor supplies cut into the perimeter in what we consider the "correct" method.0 -
Nice history lesson0
-
My friend Bern Nagengast, who is ASHRAE's historian, shared these pics of the first copper tee with the holes for solder with me. I tell about them in the tale. The link to the U.S. patent is under the second pic. Thanks, Bern!
Retired and loving it.1 -
I have some old fittings that I got from a coworker that bought a house that came with a garage full of parts from the previous owner that was a plumber that are the cast type. I seem to recall some had the hole in the side. They weren't quite the same as this but they are this style.
This makes me wonder how they make modern copper fittings. Are they cast then formed or are they somehow pressed out of a slug of copper or what.0 -
-
-
My only surprise was that they get their raw copper in sheet rather than ingot form. Generally, ingots are the least expensive way to obtain raw materials that will be again melted. It is always fun to watch manufacturing processes and see the ingenuity in the machines and processes and understand why we can get such products relatively inexpensively.0
-
That video looks dated. They may be doing things differently now.Retired and loving it.0
-
those plates are the form the copper is in after refining. they dissolve it and electroplate it in to plates to purify it.Voyager said:My only surprise was that they get their raw copper in sheet rather than ingot form. Generally, ingots are the least expensive way to obtain raw materials that will be again melted. It is always fun to watch manufacturing processes and see the ingenuity in the machines and processes and understand why we can get such products relatively inexpensively.
@DanHolohan I could see how you could press 2 port fittings but i couldn't see how to press a side port. I think that is the British or Australian how its made, i have never seen that on the us version.0 -
I believe the machine extrudes it. These things work under very high pressure.Retired and loving it.0
-
It is in the video. they fill it with water in a press and the water pressure forces the copper in to the side branch of the die. (there must be a ton of engineering in keeping everything the right thickness in that process)DanHolohan said:I believe the machine extrudes it. These things work under very high pressure.
0
Categories
- All Categories
- 87K THE MAIN WALL
- 3.2K A-C, Heat Pumps & Refrigeration
- 58 Biomass
- 426 Carbon Monoxide Awareness
- 113 Chimneys & Flues
- 2.1K Domestic Hot Water
- 5.7K Gas Heating
- 109 Geothermal
- 161 Indoor-Air Quality
- 3.6K Oil Heating
- 70 Pipe Deterioration
- 994 Plumbing
- 6.3K Radiant Heating
- 391 Solar
- 15.4K Strictly Steam
- 3.4K Thermostats and Controls
- 55 Water Quality
- 44 Industry Classes
- 48 Job Opportunities
- 18 Recall Announcements