Obnoxious Banging, Constant Bleeding, Info Overload

TL;DR - Hot water boiler system. Upper floor boiler loops always full of air, constant loud, percussive banging in pipes in the middle of the night. Bleed frequently but keep getting air. Unsure if noise is pipe expansion, or because of air.
Last spring I bought an older house in Alaska that has a hot water boiler system and slant-fin baseboard radiators for heating. I'm unfamiliar with this type of system so it has been a real task to learn how it all works and to do small maintenance tasks. I've figured a lot of stuff out, but there has been a major issue that I can't figure out. Well two, really.
First, system details.
House built: 1967
Floors: 3 (basement, main, loft)
Boiler Manufacturer: Lennox/Dunkirk
Boiler Model: PWB-5D
Boiler Loops: 4
Boiler Location: Basement
Vertical Distance from Boiler to Main Level loops: 9'6"
Vertical Distance from Boiler to Loft Level loop:17'6"
Linear feet of loops shown below and on attached PDF.
Basement: 1 Loop
Main Floor: 2 loops - Main loop (living room, kitchen, bathroom), Master Bed loop (abandoned, unknown reason)
Loft: - 1 Loop
EDIT: *There are not bleeders in the loops, bleeding has to be done near the boiler where the loops return*
I'll include a ton of pictures and other helpful info below.
Issue #1: Constant Banging
I am constantly woken up in the middle of the night due to bursts of very loud, percussive, very annoying banging sounds coming from the walls. At first I thought it was just noise from the expansion and contraction of the copper pipes against the joists and studs they passed through, but then it started getting worse. After lots of googling and youtube videos, I bled all 4 loops and noticed the problem wasn't AS bad. But it was short lived. After a few days it will be just as bad again. The following scenario is when it is worst: If I set the thermostat on the main floor to around 60 or 65, the heat isn't being called constantly. When there is a call for heat, the sound is AWFUL. Listen to the audio, and take look at the waveform below. It starts out as high frequency banging, then slowly tapers off. Then it does it again on the next cycle.
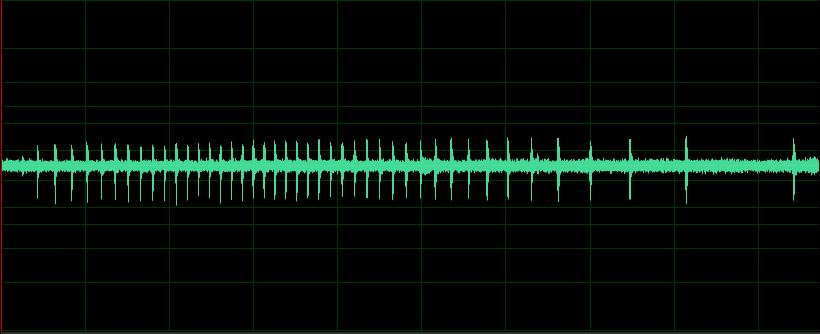
Link to audio clip: Banging Sounds
If, however, we just leave the thermostat cranked all the time, so the loop is always open and circulating, the banging isn't as frequent, or as intense. I HAVE to solve this problem soon, as we have an Airbnb and this can't keep disturbing guests.
Issue #2: Air In Loops
I discovered a while back when turning on the loft thermostat, that when activating the loft loop, there will be a long pause and then a bunch of very audible gurgling sounds, followed by the sound of flowing water.
Link to sound recording of loft loop gurgling: Loft Loop Gurgling
Bleeding the system takes care of this for a day or two, but then the air comes right back. I have noticed air when bleeding both the main floor loop, and the loft loop, but especially the loft loop (obviously).
There are no known major leaks that I am aware of. Where's the water going? Where's the air coming from?
Bonus Issue: Tridicator stuck on 30 PSI. I have no idea what my actual pressure is, ever.
I have considered using a leak sealing product, but am unsure of how to get it into the system. When I drain the boiler and replace the tridicator, can I just dump it in that hole? Should I replace the tridicator and do some pressure tests first, before assuming there's a leak?
I have reached the limit of things I can troubleshoot without some more expertise, which is why I came here.
Details Dump Below:
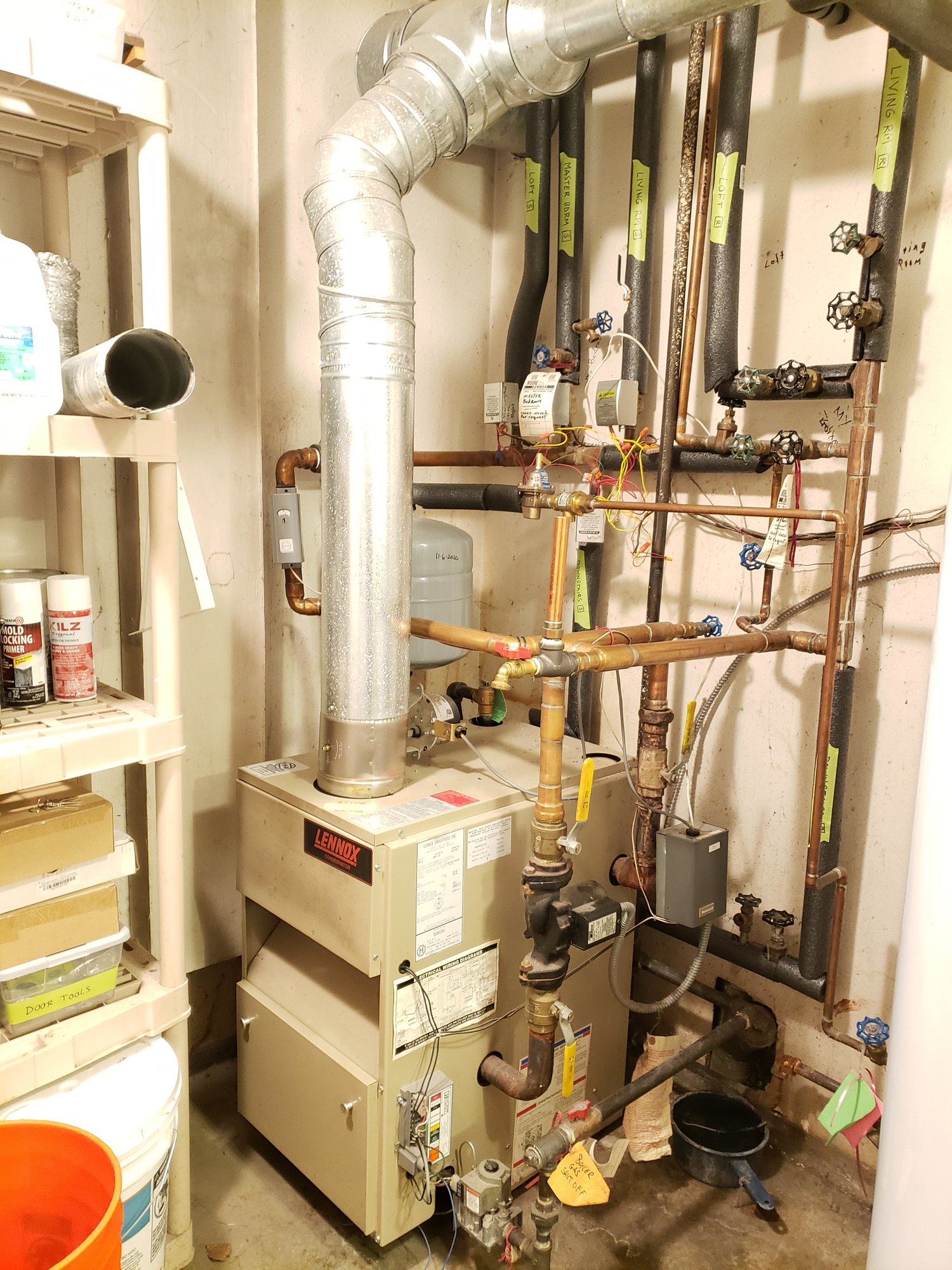
Boiler System. I forgot to take a picture of the expansion tank, but I banged on the sides and it sounds fine.
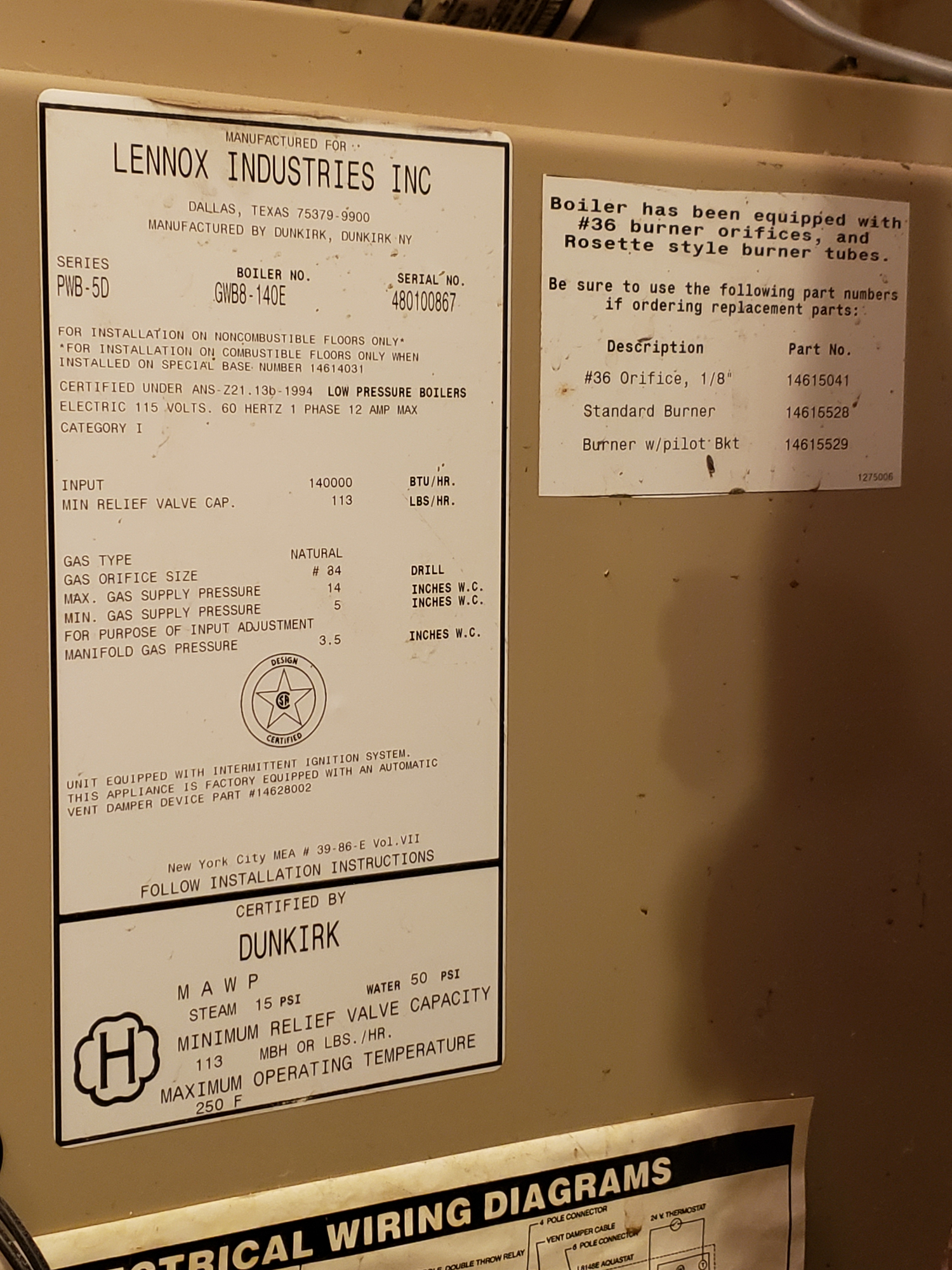
Boiler Label
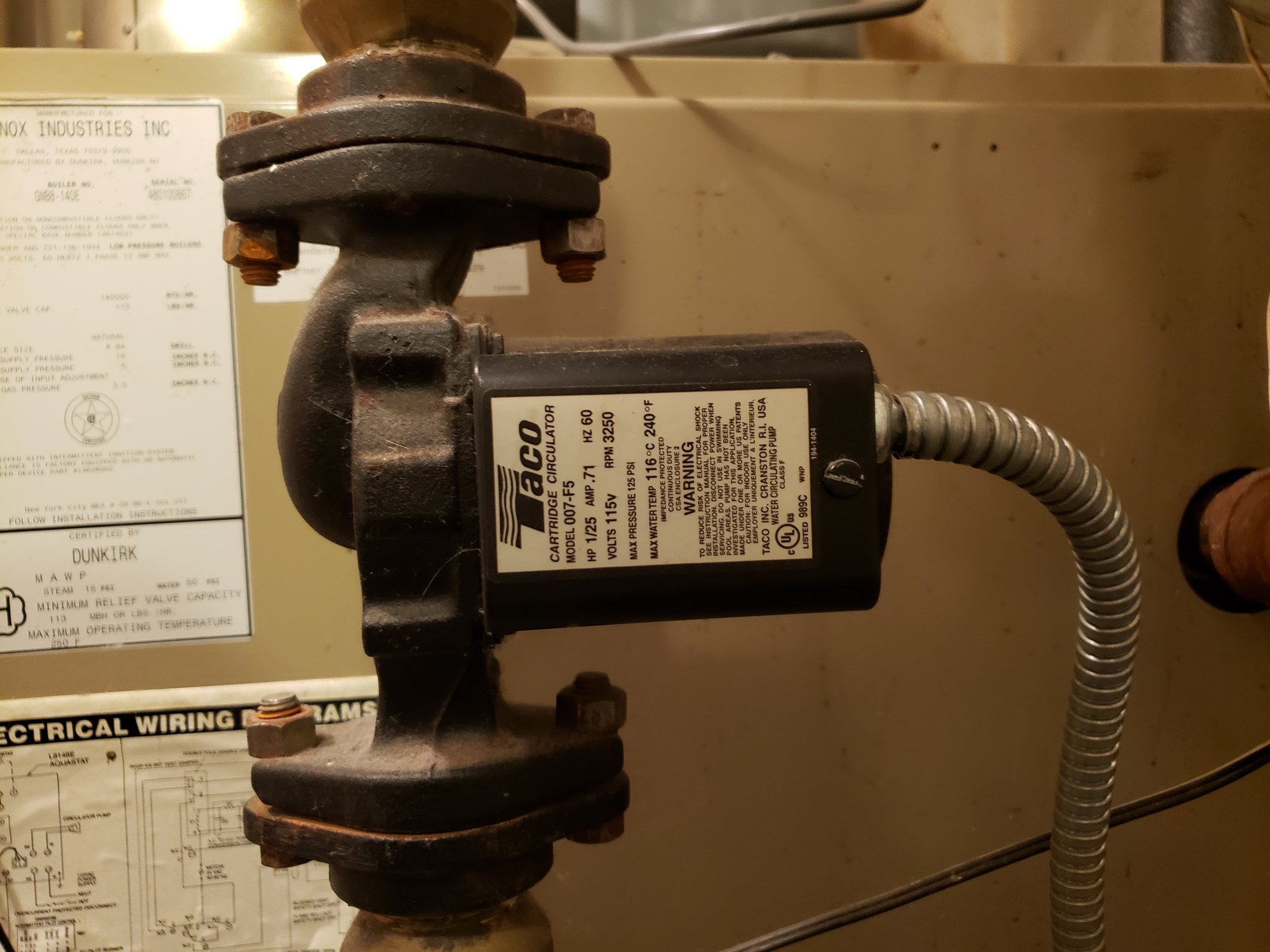
Pump
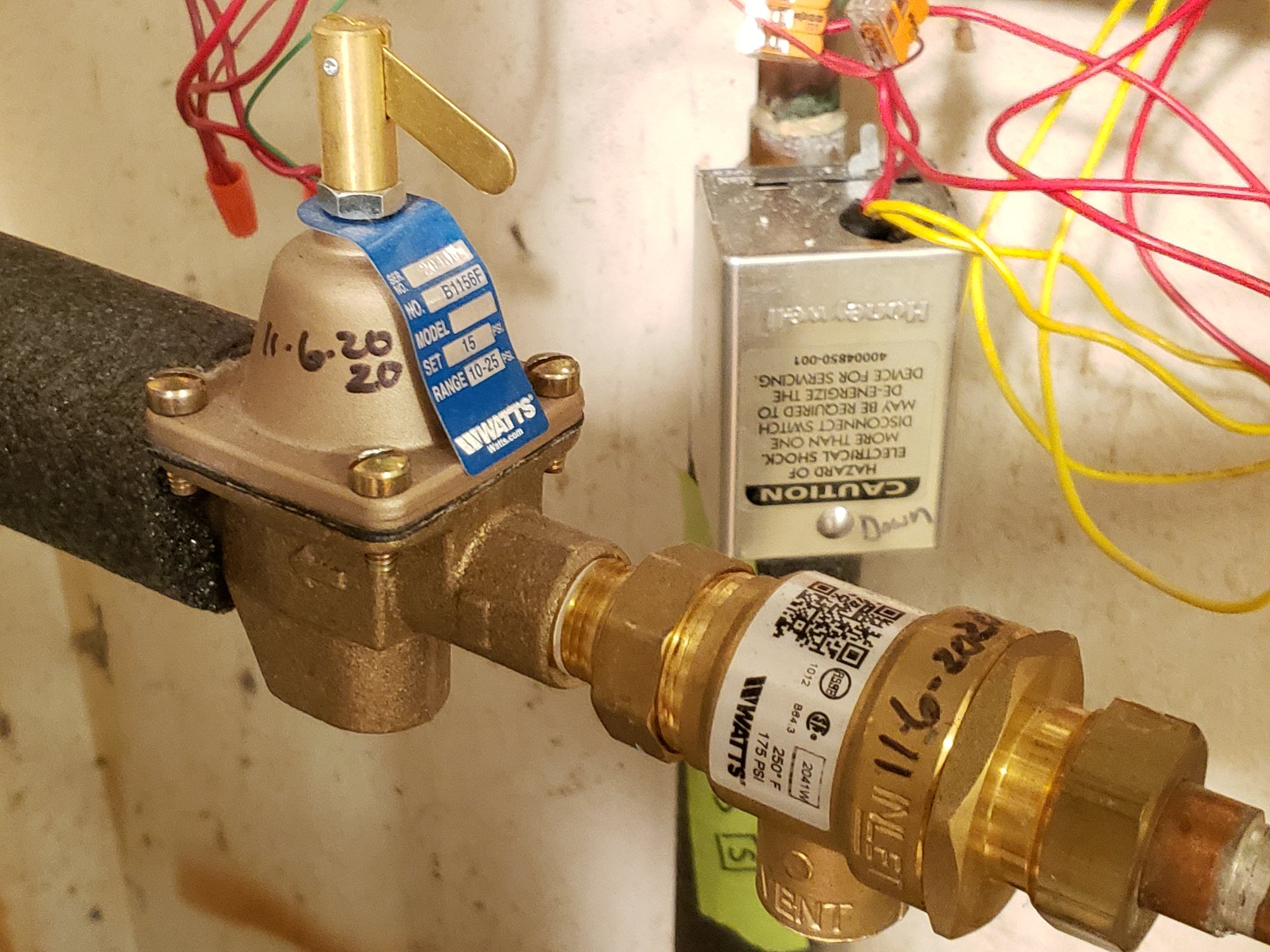
Pressure thingy on the inlet and an unknown thingy on the right of it
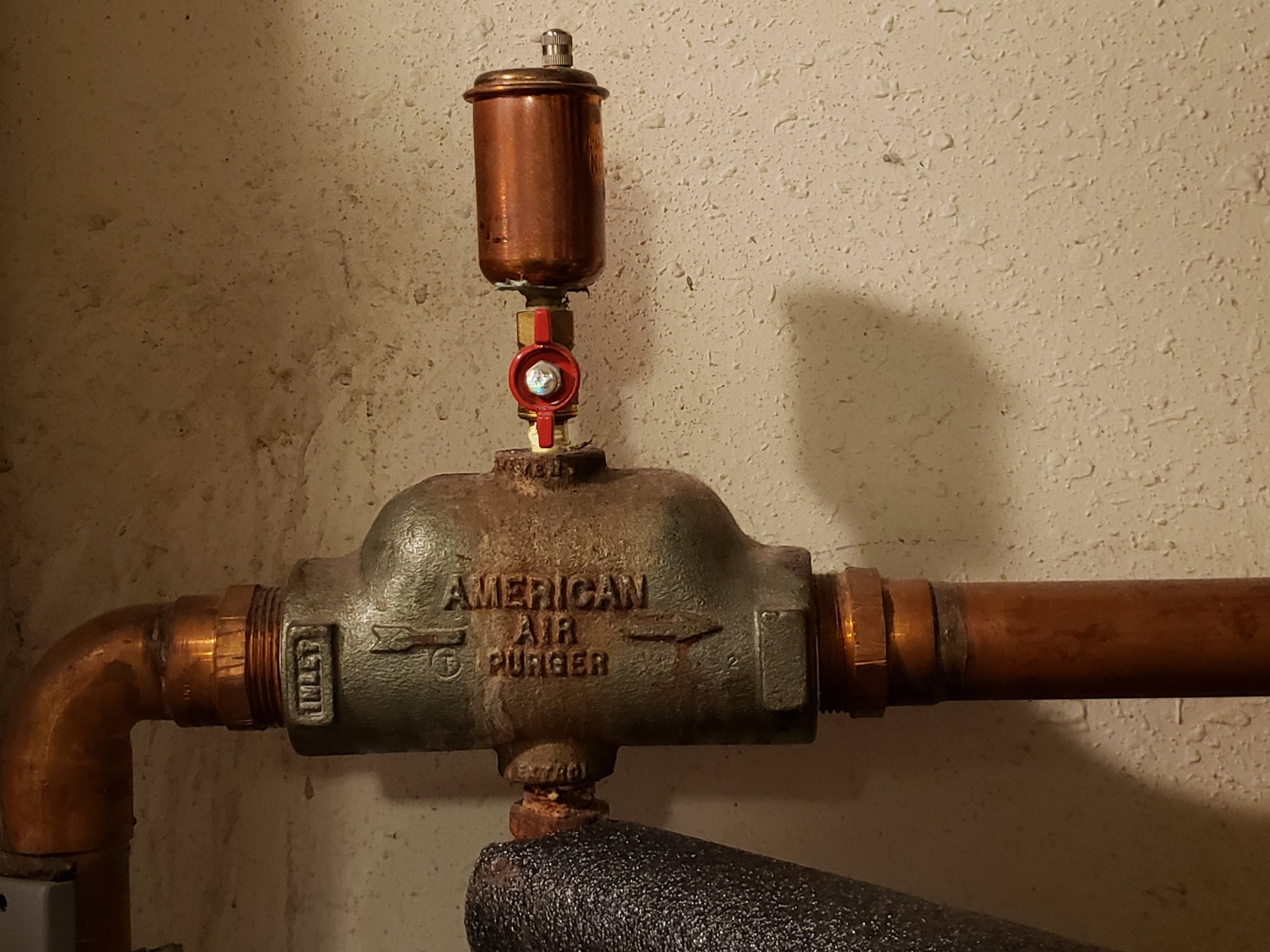
Air Separator
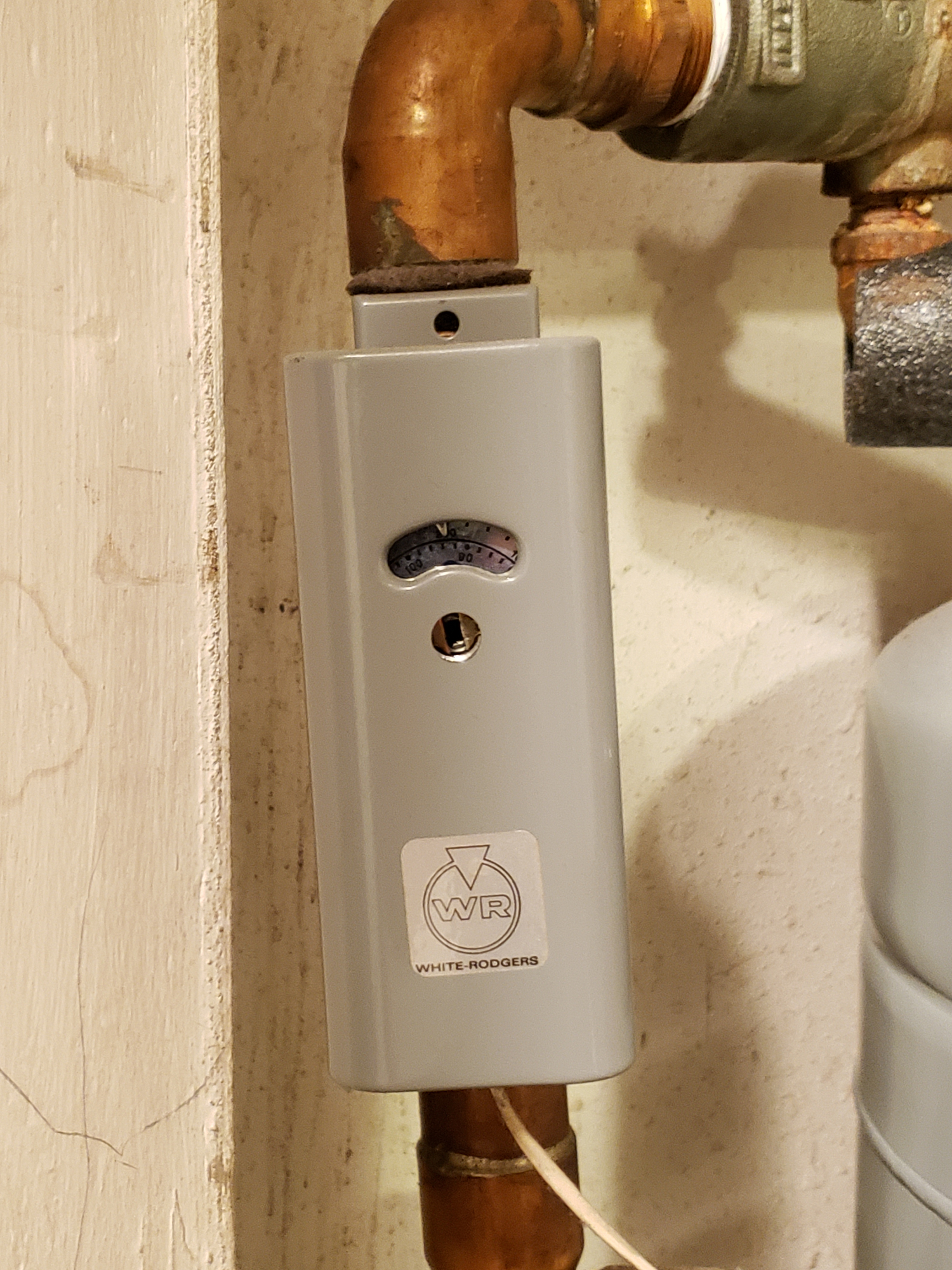
Clamp-on high limit
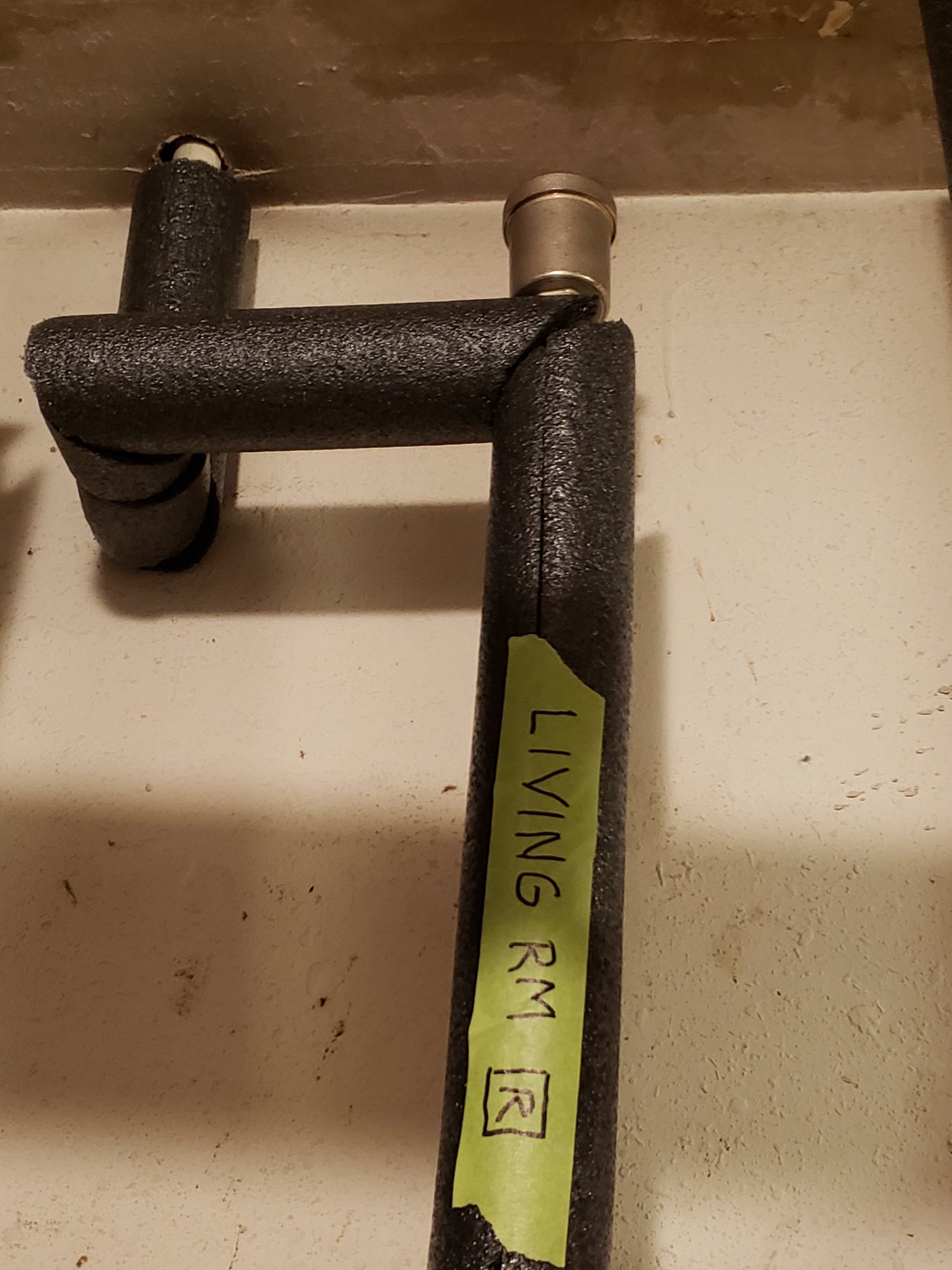
Some kind of air vent thingy
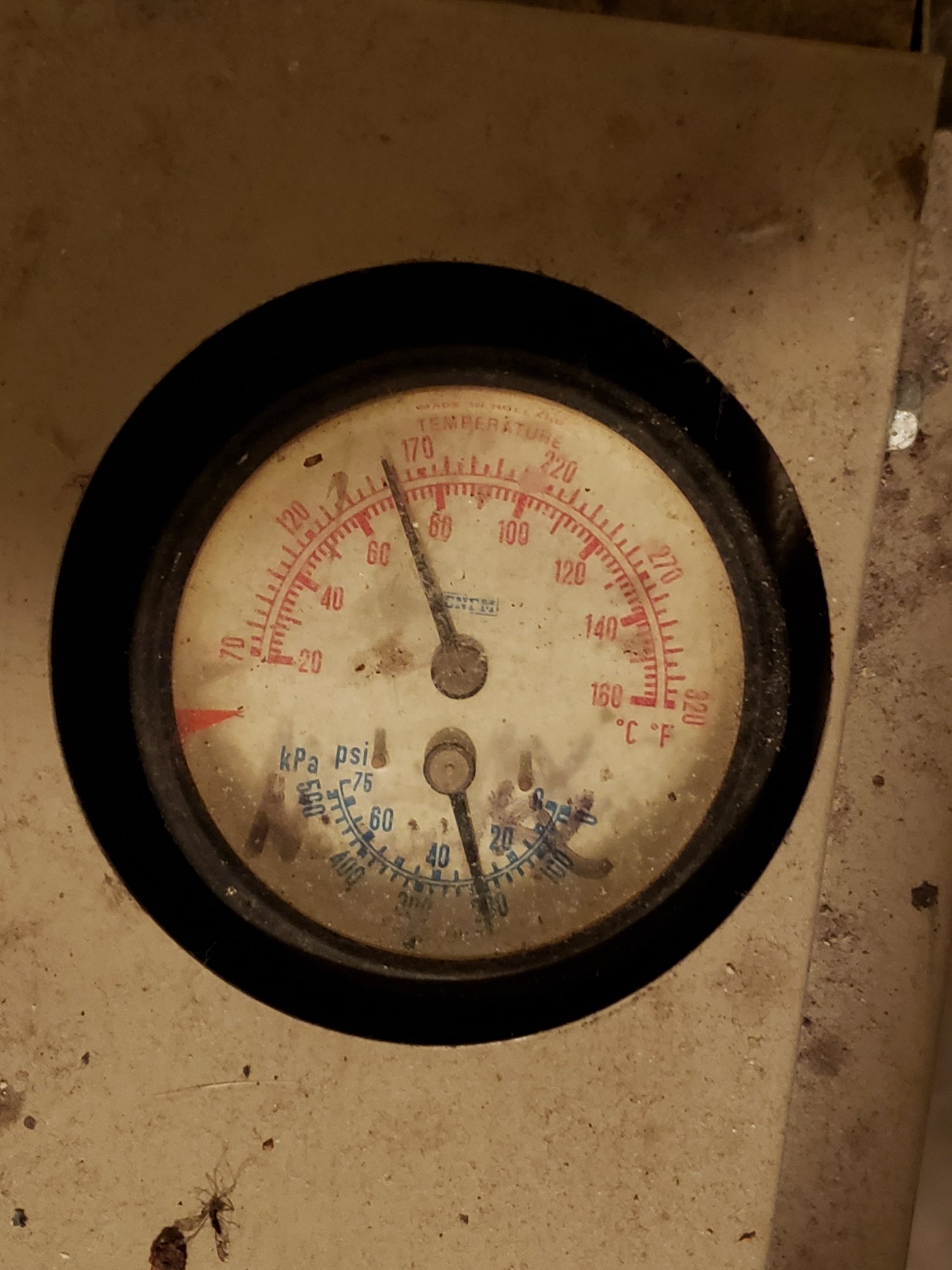
Tridicator, forever stuck on 30psi
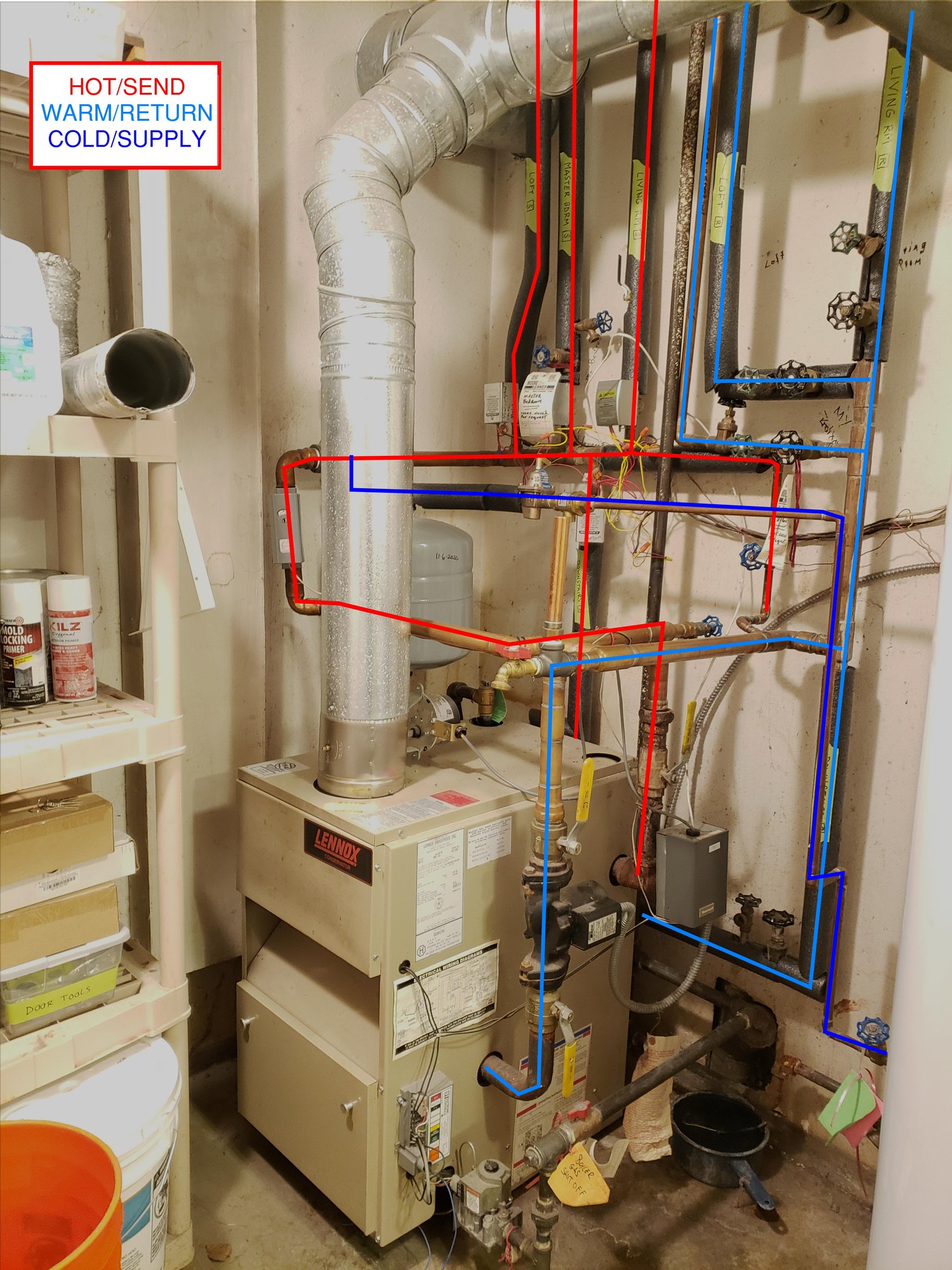
Diagram of how I understand this thing flows
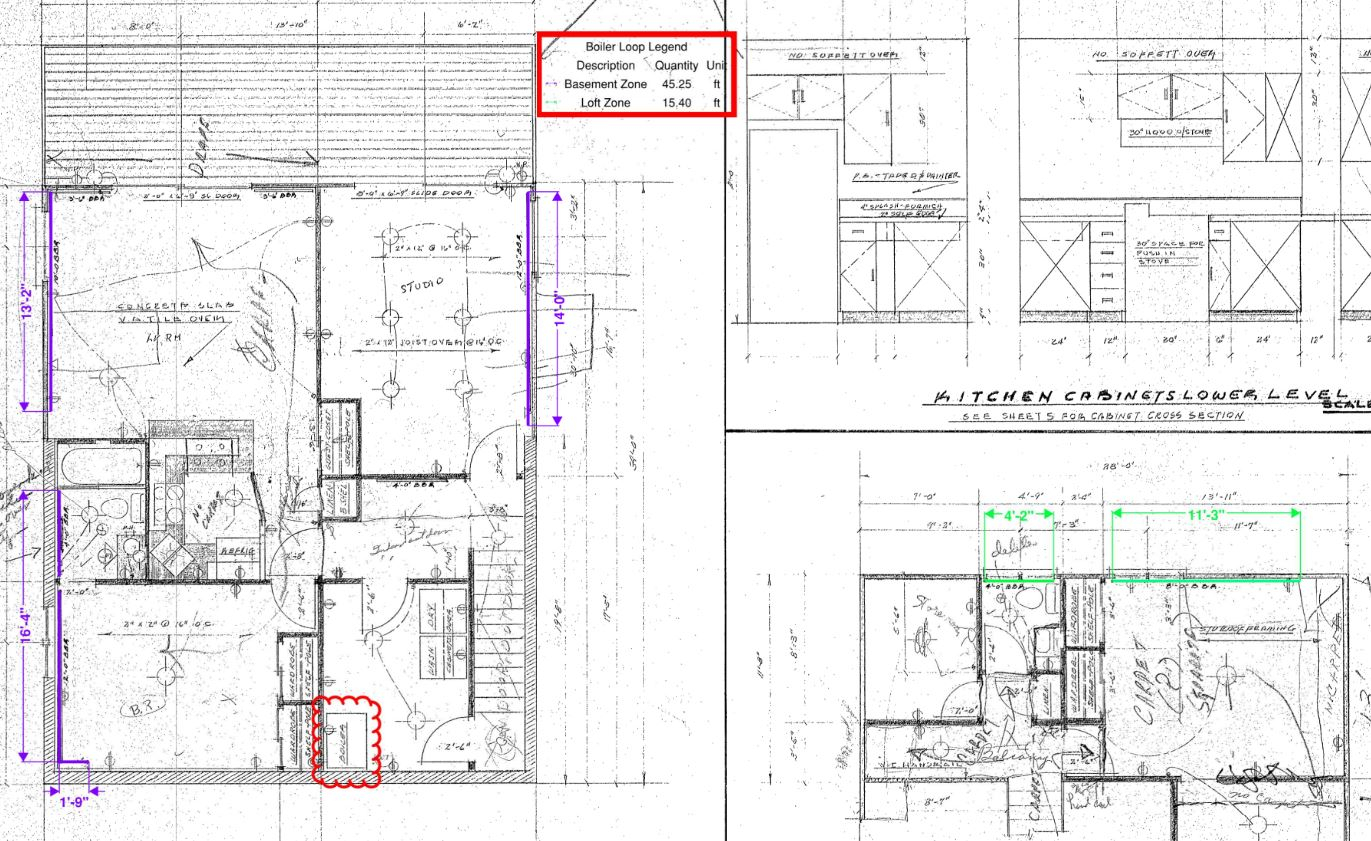
Basement Loop. See attached PDF.
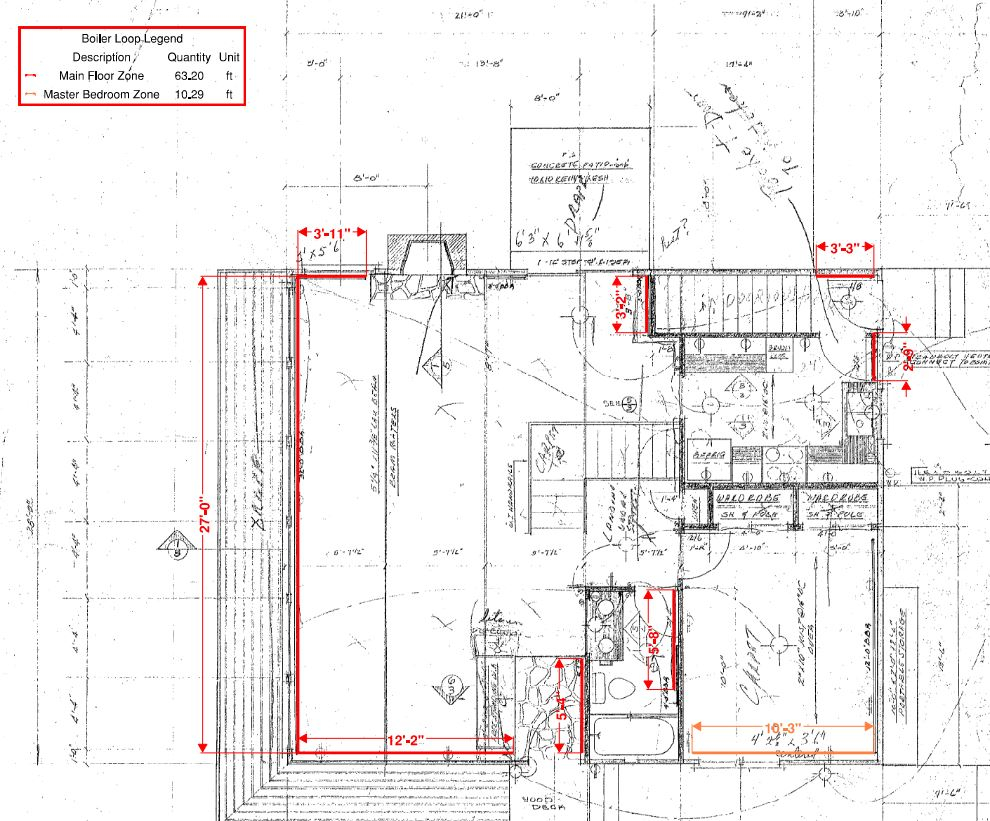
Main Level Loops. See attached PDF.
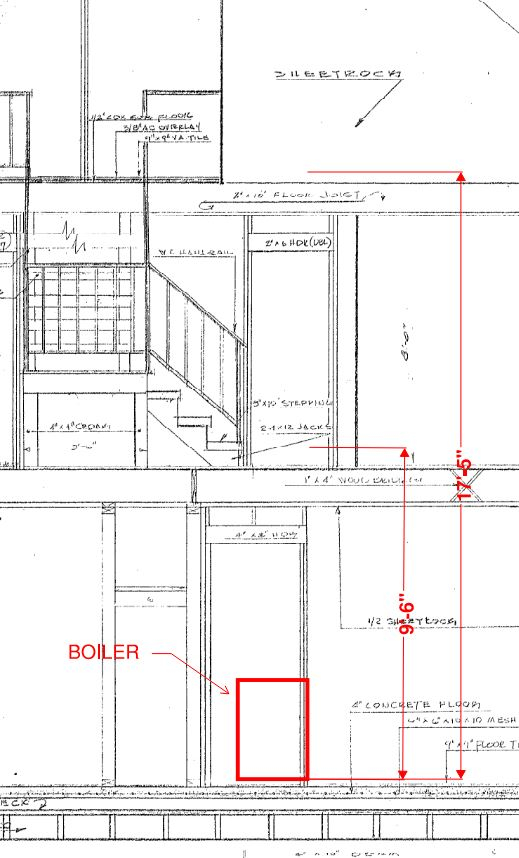
Vertical rise. See attached PDF.
If there is any more information I can provide, please let me know.
Out of all this I'm hoping to cover 3 things:
1. Is there something about the layout of this system that is terrible, and/or contributing to these issues?
2. Should I add a leak sealer, and if so, how do I get it in without a pump?
3. I guess it's just 2 things.
Thanks!
Comments
-
If you open a bleeder on one of the upper floor radiators with the pumps off, do you get air or a nice solid stream of water. I'm thinking that your tridicator -- a useless gauge anyway -- is lying to you and that your system pressure is low. I'd get a reliable pressure gauge on there -- you can get the gauge from Amazon, and some fittings to hook it up to a hose bibb from a hardware store -- and see what you really have.
Then I wonder about the expansion tank. This is a little more difficult, really, but there is a Schrader valve (like a car tire) on the end opposite the water inlet. Can you measure the air pressure there? Just like measureing a car --even the same gauge.Br. Jamie, osb
Building superintendent/caretaker, 7200 sq. ft. historic house museum with dependencies in New England0 -
Seems like you’re boiling and flashing. Verify pressure with a simple “hose thread” pressure gauge (I like a 30 pound gauge for this, not a crazy 100 or higher psi gauge)
circulator may be dead, need to verify flow. I like the “swoosh” test—-quickly shut off a valve and listen for the change in velocity. The valves (either one) before or after the pump will do just fine. No swoosh means no flow (very generally speaking)
strap on high limit——not sure what’s up with that, seems hoaky. The boiler doesn’t have its own main control?
leak sealer—-not really, fix or replace
may need some heating guy to figure stuff out0 -
That banging sounds like expansion noise from the pipes especially since it is only while heating or cooling, not when the pipes are up to boiler temp.
The pipes need to be free to move wherever they go through framing without sticking and slipping and popping/ticking. They also need to be free to slide on the carriers in the baseboard cover. It could have been trapped in the framing when it was built or during remodeling or the carriers could be broken or missing in the cover. You could try turning the aquastat down a bit, 60 f to 180f is a big delta t and the copper will expand a lot in that transition. I wouldn't go below 150 f without measuring the return water temps. It may also have trouble heating the house at that temp on colder days.
As for the air, you will need to verify the gauge before you can work on that. Where does the relief valve discharge? Can you verify that it is not discharging? You may just have at that you have not removed especially if the pressure is too low.0 -
Unfortunately I don't have bleeders in the baseboard, so I can't check that. Whenever I bleed it, I do it using the valves on the return lines next to the boiler.
I know the discharge valve works because I accidentally shut off a valve while bleeding before I set the inlet water pressure thingy back to reduced pressure, so it puked water out the relief valve.
I haven't checked the pressure of the expansion tank, but I can. I at least know it's not waterlogged.
The clamp on high limit switch is a local code requirement. The main one is on the boiler outlet pipe, the gray box, but the clamp on one is a runaway prevention.
As far as temperature swing goes, when we have a cold streak, it already can't keep the main floor above 62. I noticed that despite the thermostat being cranked all the way up, the flame was still shutting off, rather than running constantly. I had a technician come out and he showed me that my main limit switch has a 25 degree swing, meaning the water temp will have to drop 25 degrees before it was fire up again. The seems ineffective to me, AND likely to cause a lot more temperature swings in the pipes.
I will track down a pressure hose bib pressure gauge. Does it matter where I connect it?
I was thinking of these two options, but I wasn't sure if it would be affected by the adjacent pump.
0 -
The pressure will be different on each side of the circulator but either location will tell you if it is way too low or too high.
If it isn't keeping up but the the burner is cycling it sounds like you have air somewhere that is affecting circulation. That air scoop and the circulator being located where it is pumping in to the boiler means it will do a lot poorer job of removing air than more modern setups.
It sounds like you may need to find where the pipe is trapped and add something like some plastic shims or cut away some building materials to help it move more quietly. the easiest places to get to will be where the piping enters the room to connect to the baseboard through walls or floors but it could easily be where it works its way through the building too. The element should be sitting on plastic glides that are centered on the carriers inside the baseboard cover. Any or all of these places could be making your noise.0 -
Here’s what I would do if it were mine -Find/fix leaks - the air is coming from somewhere and it’s most likely from makeup water.Install an air separator and lose the air scoop.Pump away from the expansion tank (point of no pressure change)
Verify system pressure like it was mentioned above.Verify that the tank isn’t ruptured. It’s possible that it is and the leak, if you have one, may hide the symptoms of a failed tank.Steve Minnich4 -
Went to Home Deport and got a pressure gauge and installed it as shown below. I am running about 10.5 PSI, which is low, right? My make-up water thingy has a pressure of 15 psi, so why isn't it adding water? I was able to bring the pressure up to 15 by slowly letting some make-up water in the manual way. We'll see how long it takes for the pressure to drop back to 10.
I still need to check the pressure of the expansion tank.
Also, on the air vent things, I assume the little nub on top needs to be loose? How loose?
What is the best way to figure out where my pipes run? Can I use a thermal camera to trace them through floors and walls? If I can narrow down the source of the sound, I'm not beyond ripping open a wall or a floor to make it stop.
0 -
the cap should be loose enough that you can jiggle it on the threads. It just needs to be loose enough that the seal inside isn't clamped on to the outlet of the automatic vent. Since the system gauge doesn't work someone might have misadjusted the pressure reducing valve. you might need to readjust it to 12 psi or so.0
-
Those are adjustable? I thought they were pre-set at a certain PSI and that was that. I has a tag on it that says Set to 15psi. Also, what should my system pressure be, based on the vertical rise of the loft loop?0
-
Your pressure looks OK. 12-15 PSI is normal for a two story home. That is the normal pressure for the fill valve to keep the boiler pressure at. It is also what the air pressure in the expansion tank should measure at. To check the air pressure in the tank it has to be removed from the boiler, or at least isolated from the boiler and the water pressure drained off.0
-
That air purger installed at an ell is virtually useless. It would take some repiping to get the near boiler piping to a better condition.
Connecting the expansion tank where you have that hose bib and test gauge would help a lot and be super simple, no piping changes. A wash machine hose and one 1/2 hose adapter would allow you to try it out. and see if it makes air removal easier. But without a good purger the system is a bit handicapped.
Ideally that purger would be converted to a boat anchor and a microbubble air separator put in it's place
Rapid and wide temperature swings will cause copper tube to expand and make all sorts of noise, not sure how much of that could be minimized. An outdoor reset control would minimize the high temperature operation and minimize expansion type noises.
Looks like an auto vent on living room return? it could be sucking air in since you are pumping at the PONPC, if it's a Taco 007n it may not have enough fizz to pull a negative there, but I'd screw down the cap on any vents like that on return piping. What have you to lose.Bob "hot rod" Rohr
trainer for Caleffi NA
Living the hydronic dream1 -
Start with repiping the boiler that would be my approach since it is piped wrong.0
-
Do you have a link to one you would suggest> I don't know anything about these devices.hot_rod said:Ideally that purger would be converted to a boat anchor and a microbubble air separator put in it's place
0 -
You have a number of things going on. If the boiler shuts down and rooms are still cold, you are not moving enough heat to those zones. On a cold day the boiler, ideally should run non stop. If some rooms are too warm and others cold, you can close down the dampers on the Slantfin in the hot rooms and do a bit of balancing.
So either your flow is to low, or there is not enough fin tube baseboard in some rooms. That boiler output is around 120,000 btu/ hr. If you figure 500 btu/ ft output for that Slantfin, you need 240 feet of Slantfin to cover the load on a design day. Assuming the load is 120,000? A heat load would be needed to confirm that.
Regardless, you need 240' to move what the boiler can supply. How many feet do you have?
If you are close on SlantFin footage, you can either increase supply temperature a bit, although more expansion noise. Or if you have a multi speed circulator, turn it up one speed. Once you hear water rushing through the pipes, you are flowing too fast.
It could really use a boiler repipe to correct all the issues, not sure how deep you want to get into this?
The suggestion I made to move the expansion tank to the return side of the pump, no other changes was to maybe get you thru this season, and regroup. Tighten down the caps on all those air vents, they could be allowing air in. If it comes back after bleeding, somewhere, somehow air is getting in. Unless it is all expansion noise causing the complaint.
A more involved option is to install a better air purger, and either move the pump up on the supply, or move the expansion tank to the return. Any microbubbles that are circulating decrease the heat output from the Slantfin some. Need to have a solid stream of turbulent water for best heat transfer to the tube.
A hydronic pro would probably start with a sawzall and cut all the piping out and rebuild
from the boiler up
Even after that much rebuild the piping in the walls could still cause some noise if it is too tightly fastened, inadequate expansion room, etc.Bob "hot rod" Rohr
trainer for Caleffi NA
Living the hydronic dream0 -
Thanks for all the input, Bob.
I already know the reason (or at least one of the reasons) the boiler doesn't cycle enough and deliver enough heat. The limit switch has a 25 degree swing. So after the water heats up to the upper limit, the burner shuts off and won't come back on until the water temperature has dropped by 25 degrees. Seems ridiculous. Can I change out that device?
As far as temporarily moving the expansion tank to get through the season goes, what does moving the expansion tank accomplish? I'm certainly open to it.
A full re-pipe might be a project for next fall. I'll have to learn to solder before then.
At this point I'm fairly certain that pipe expansion/contraction is the source of the banging sound. I know I'm still getting air in somehow, but that's not as big of a worry as dealing with the noise.
Currently debating between renting or just buying a thermal camera so I can trace and document my loops in the floor and walls. After I know where they're at, it will be time to rip open the floor and wall in the troubled area.
I'm sure I'm over simplifying it, but how hard could it be to re-pipe the boiler? Just chop some pipes, solder some new stuff in in a different layout.0 -
You can but that really shouldn't be an issue unless you are close to design conditions and if you are the boiler should not be reaching the upper limit very often. I think you have a lot of air in the system somewhere, you keep removing little bits of it but you aren't getting the bulk of it. Are you sure the circulator is actually moving water and it isn't just heating off of gravity flow?nathandclements said:Thanks for all the input, Bob.
I already know the reason (or at least one of the reasons) the boiler doesn't cycle enough and deliver enough heat. The limit switch has a 25 degree swing. So after the water heats up to the upper limit, the burner shuts off and won't come back on until the water temperature has dropped by 25 degrees. Seems ridiculous. Can I change out that device?
Knowing what it should be like after you are done is the hard part.nathandclements said:I'm sure I'm over simplifying it, but how hard could it be to re-pipe the boiler? Just chop some pipes, solder some new stuff in in a different layout.
0 -
What's the best way to test this? The pump makes noise like it's running. When I turn on the heat in the loft, the gurgling happens and then water sounds like it's moving through, so I assume it's working. If I'm bleeding the loop with full pressure make-up water, I don't know how there could still be trapped air in the that loop, aside from suspended air in the make-up water.mattmia2 said:Are you sure the circulator is actually moving water and it isn't just heating off of gravity flow?
0 -
The purge method is really to get enough air out to get circulation started, it is still dependent on good air elimination at the boiler to get rid of the final air. There may be air still trapped in some spots where the flow isn't enough to entrain it and pull it along.nathandclements said:If I'm bleeding the loop with full pressure make-up water, I don't know how there could still be trapped air in the that loop, aside from suspended air in the make-up water.
Is the abandoned loop still attached to the system? If it is you need to get the air our of there too or it could absorb in the water and come out of solution elsewhere.
The basic idea of the purge method is your near boiler piping and air elimination deaerates the water and the air remaining in other areas absorbs in to the deaerated water where it is removed at the boiler. if your air elimination isn't at the hottest and lowest pressure point and it is just an air scoop it may not be doing a very good job of getting the water ready to absorb air pockets out in the system.0 -
Maybe order a copy of “Pumping Away” from this site to get a grasp of how the expansion tank location effects air removal. It is the simplest thing to try my suggestion before you start ripping things apart. It will prove out the very common fix actually works as explained in the book.Bob "hot rod" Rohr
trainer for Caleffi NA
Living the hydronic dream0 -
Thanks for links, I've got some reading to do. Got a thermal camera on the way so I can trace the piping in the noisy area. I am 99% sure at this point that it's noise from heat expansion where the pipe is wedged against a joist. When it's banging, I can literally feel it in a certain area of the floor.
Also, as previously suggested, I closed both breather things and today I noticed my pressure was up to 14psi.0 -
I read the excerpt from Pumping away at the link (https://heatinghelp.com/systems-help-center/pumping-away-piping/).
Isn't my system already pretty much set-up the same way as in this diagram? I'm confused.
0 -
Not at all. Your circulator is pumping in to the boiler and the air scoop and the expansion tank.
In pumping away the circulator is after the air separator and expansion tank and the air separator is on the outlet of the boiler so the air separator is at the highest temperature and lowest pressure point in the system which makes that point the place in system where air is most likely to come out of solution.0 -
Maybe a drawing helps visualize the concept.
Your pump is flowing into the return of the boiler, thru the boiler and at the expansion tank. At the PONPC.
So, the tank could move to where that purge valve with gauge is located. Or move the pump up to where the air purger is.
The piping is a mess either way. Repiping all that near boiler would allow you to get the pump/ tank relationship correct and install a better air separator.
Your best first step is addressing any pipes that are rubbing, or fastened too tightly.
If it is air noise inside then piping, then correct the air removal function.Bob "hot rod" Rohr
trainer for Caleffi NA
Living the hydronic dream0 -
If you have air vents on the returns I would make sure the caps are closed tight. If you have air vents on the supplies close the ones you don't see on a regular basis.
Miss Hall's School service mechanic, greenhouse manager, teacher, dog walker and designated driver
0 -
hot_rod said:
Maybe a drawing helps visualize the concept.
Thanks guys, this makes more sense.mattmia2 said:In pumping away the circulator is after the air separator and expansion tank and the air separator is on the outlet of the boiler so the air separator is at the highest temperature and lowest pressure point in the system which makes that point the place in system where air is most likely to come out of solution.
In terms of moving my tank, I have two logistical questions.
1. It's heavy. How do I mount it elsewhere, like at the place where I put the gauge?
2. How do I disconnect it without making a mess? There's no service valves that allow me to isolate the tank, and when I take it off there will just be an open hole. I assume I'll need to find some sort of cap to close it off?0 -
When ever any service on the water side is completed, you need to drain the boiler to a floor drain or with a utility pump to the outdoors. Once the pressure is released you can decide of the repair need the boiler completely drained or just have the radiation water lowered to a point below the repair location. If the expansion tank is still heavy after the pressure is at 0 PSIg, then you have a problem with the expansion tank.nathandclements said:
Thanks guys, this makes more sense.
In terms of moving my tank, I have two logistical questions.
1. It's heavy. How do I mount it elsewhere, like at the place where I put the gauge?
2. How do I disconnect it without making a mess? There's no service valves that allow me to isolate the tank, and when I take it off there will just be an open hole. I assume I'll need to find some sort of cap to close it off?
I recall a customer that we needed to visit several times each winter. There was no heat in one or more of the several zones. We repaired the no heat problem by purging air from the problem loops. Just after learning about Pumping Away and attending a seminar by @DanHolohan, this customer needed a new boiler. We installed the new boiler in accordance with the Pumping away design using the more expensive Spirovent (only one available at that time). My installer, who also performed many of the no heat service calls over the years, was skeptical that this piping design would solve anything. The 6 or 7 zone system needed to be purged several times after previous repairs. This procedure took over 45 minutes in the past. with the new design my installer was surprised that the boiler and radiation was air free on the first purge of each zone. He was also was surprised at the amount of automatic venting that took place in the first 20 minutes of operation. He was even further surprised that the balance of the winter resulted in no additional service calls. He has been a believer of "pumping away" ever since.
You seem to have a similar problem as my customer of many years ago. However you do not need a new boiler. Not yet anyway. Your Lennox boiler has many years of service left as long as you stop adding fresh water constantly. Repipe the near boiler piping as indicated in this illustration. Once this is done, your air problems will be resolved.
Notice the hottest water (the supply pipe on the boiler) is located near the air vent. Also notice the lowest pressure water (the inlet side of the pump) is also near the air vent. This is important in getting air to leave the system. Your system is currently set up so the lowest pressure air in nowhere near the air scoop.
Here is a booklet I used when I was teaching a one day seminar on Hydronics for The EH-CC http://media.blueridgecompany.com/documents/ZoningMadeEasy.pdf. It was written by the same author, years before Pumping Away. Between these two books, you will be able to comletely understand your heating system.
As far as the noise from the expansion of the copper pipes in the floor and walls, that is another issue that may never be resolved. to avoid ripping up walls and floors, that noise may be mitigated by another concept called outdoor reset. This can be accomplished with some very simple control additions and adjustments
Repipe near boiler piping and outdoor reset. That is where I would start if you were my customer.
Edward Young Retired
After you make that expensive repair and you still have the same problem, What will you check next?
0 -
Questions about draining the boiler to move the expansion tank:
1. Do I need to/should I drain the radiation loops, or will their water stay-put as long as their zone valves are closed?
2. When refilling the boiler, do I just close the drain and turn the water supply back on? Is there a specific method or order of operations for refilling? What about air expulsion?0
Categories
- All Categories
- 87K THE MAIN WALL
- 3.2K A-C, Heat Pumps & Refrigeration
- 58 Biomass
- 426 Carbon Monoxide Awareness
- 117 Chimneys & Flues
- 2.1K Domestic Hot Water
- 5.7K Gas Heating
- 109 Geothermal
- 161 Indoor-Air Quality
- 3.6K Oil Heating
- 70 Pipe Deterioration
- 994 Plumbing
- 6.3K Radiant Heating
- 389 Solar
- 15.4K Strictly Steam
- 3.4K Thermostats and Controls
- 54 Water Quality
- 44 Industry Classes
- 48 Job Opportunities
- 18 Recall Announcements