Welcome! Here are the website rules, as well as some tips for using this forum.
Need to contact us? Visit https://heatinghelp.com/contact-us/.
Click here to Find a Contractor in your area.
Advice on how to approach 2 pipe steam system

Nap176
Member Posts: 6
Hey folks. Relatively new owner of a 2 pipe steam system and wondering as to best approach to increase efficiency of the system. In March 2020 (only cold month living in the house), i had what I believed to be an exorbitantly high nat gas bill - ~$300 - had the therm on 70 when it was averaging 51 degrees, using on avg 3ccf of gas a day. That seems high, but i've only lived with hydronic heat before. Again, not an expert.
This is what I know about the setup- the 2.4k sq ft home was built in 1880 ( SE Pennsylvania, very thick (~2ft) masonry walls/newer windows/minimal insulation but relatively airtight) and has a 2 pipe steam system (11 Warren Webster steam convectors - I believe - totaling ~310 EDR, which i estimated using the box measurements) tied into a ~25 yo 225k btu Columbia boiler. I am no expert, but the near boiler piping looks wonky - technical term
. Furthermore, when i popped off the convector covers the fins were caked in dirt/dust (which i have since vacuumed off) - I imagine that was a contributing factor to lack of output. All convectors seemed to get warm and boiler was responsive to call for heat. No clanging/banging in pipes.
My question is - what should i focus on first:
1) The convectors. I've cleaned off the accessible side of the coils, but for the life of me can't figure out how to remove the cover/box. I can't find any manuals online, but the boxes seem to share a brace/bolts with the coils at the very bottom, and then are screwed into the wall at the top. The boxes are probably covered in ~10 coats of paint. Is it worth it to try and remove the boxes/thoroughly clean the coils/strip the paint and reinstall? Last thing i'd want to do is start to remove them and mess up the fins.
2) The boiler. Some folks have said "if it ain't broke, don't fix it" others have said replace it and re-do the near boiler piping.
3) The piping is in good shape, but the main vent likely needs to be replaced.
Again, what should i prioritize/focus on from an ROI perspective? The system works, but trying to save some money on heating costs in the winter. Any pointers, no matter how high-level would be most appreciated.
Thanks all. The level of expertise on this board is incredibly impressive.
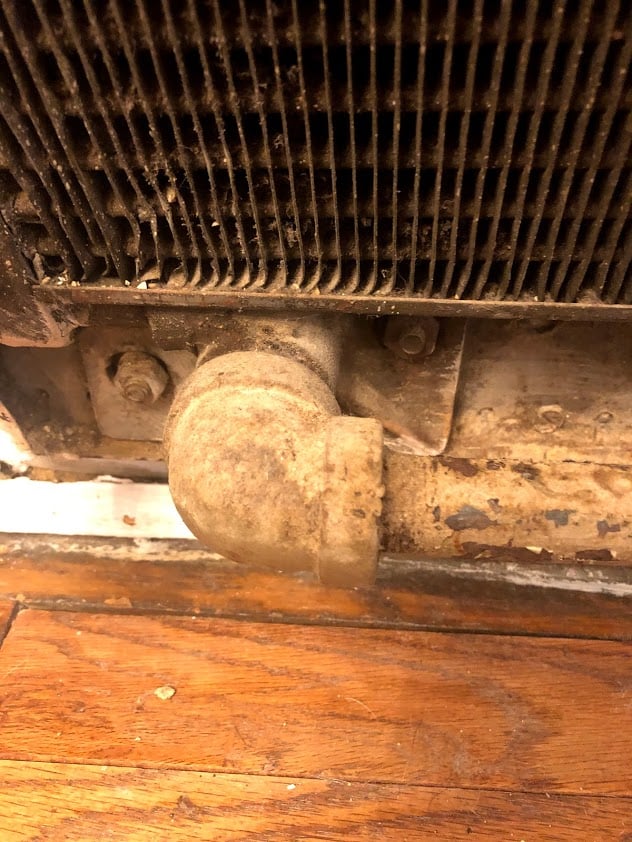
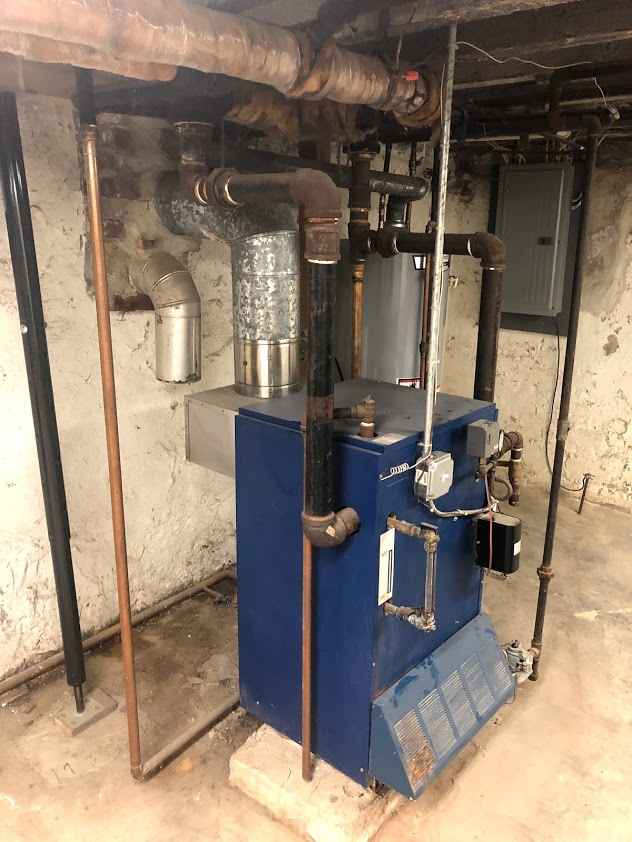
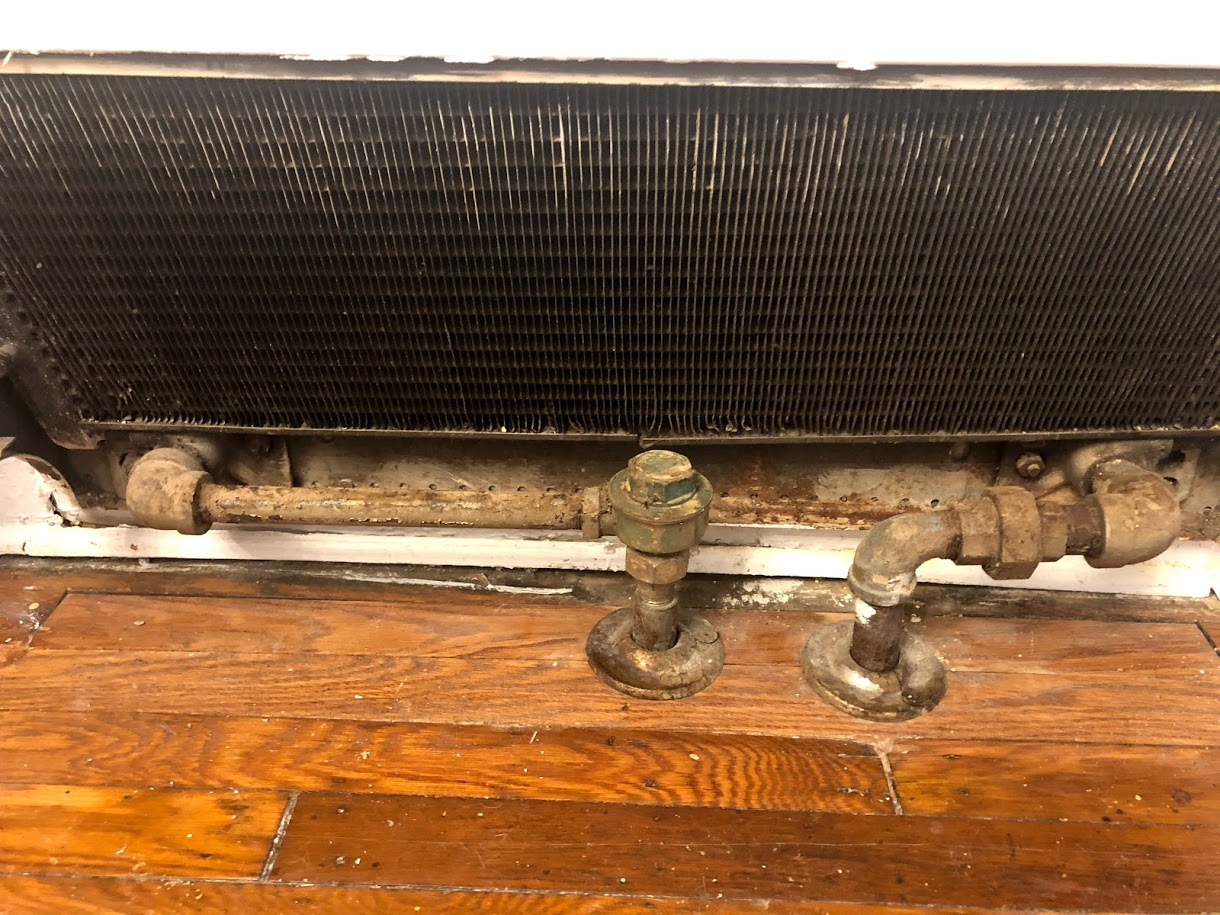
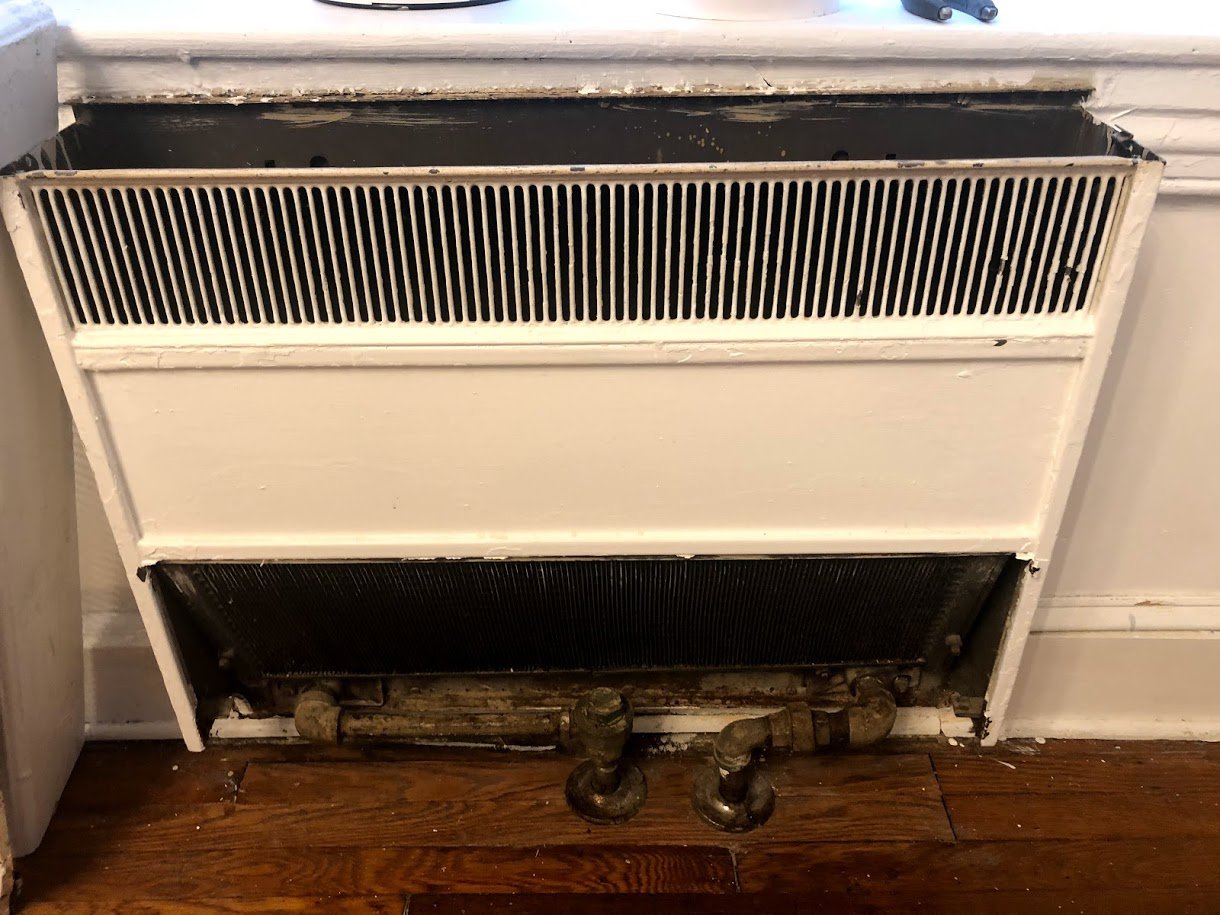
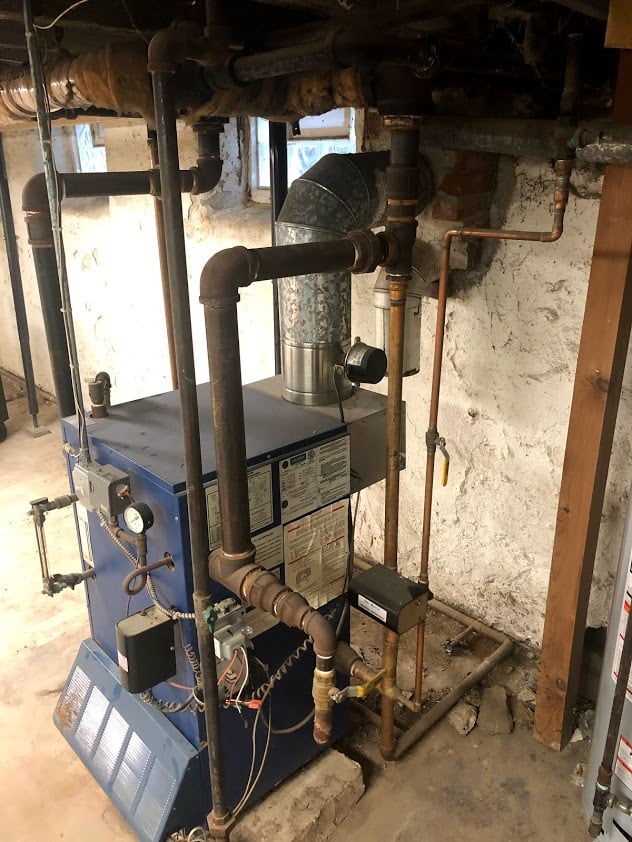
This is what I know about the setup- the 2.4k sq ft home was built in 1880 ( SE Pennsylvania, very thick (~2ft) masonry walls/newer windows/minimal insulation but relatively airtight) and has a 2 pipe steam system (11 Warren Webster steam convectors - I believe - totaling ~310 EDR, which i estimated using the box measurements) tied into a ~25 yo 225k btu Columbia boiler. I am no expert, but the near boiler piping looks wonky - technical term

My question is - what should i focus on first:
1) The convectors. I've cleaned off the accessible side of the coils, but for the life of me can't figure out how to remove the cover/box. I can't find any manuals online, but the boxes seem to share a brace/bolts with the coils at the very bottom, and then are screwed into the wall at the top. The boxes are probably covered in ~10 coats of paint. Is it worth it to try and remove the boxes/thoroughly clean the coils/strip the paint and reinstall? Last thing i'd want to do is start to remove them and mess up the fins.
2) The boiler. Some folks have said "if it ain't broke, don't fix it" others have said replace it and re-do the near boiler piping.
3) The piping is in good shape, but the main vent likely needs to be replaced.
Again, what should i prioritize/focus on from an ROI perspective? The system works, but trying to save some money on heating costs in the winter. Any pointers, no matter how high-level would be most appreciated.
Thanks all. The level of expertise on this board is incredibly impressive.
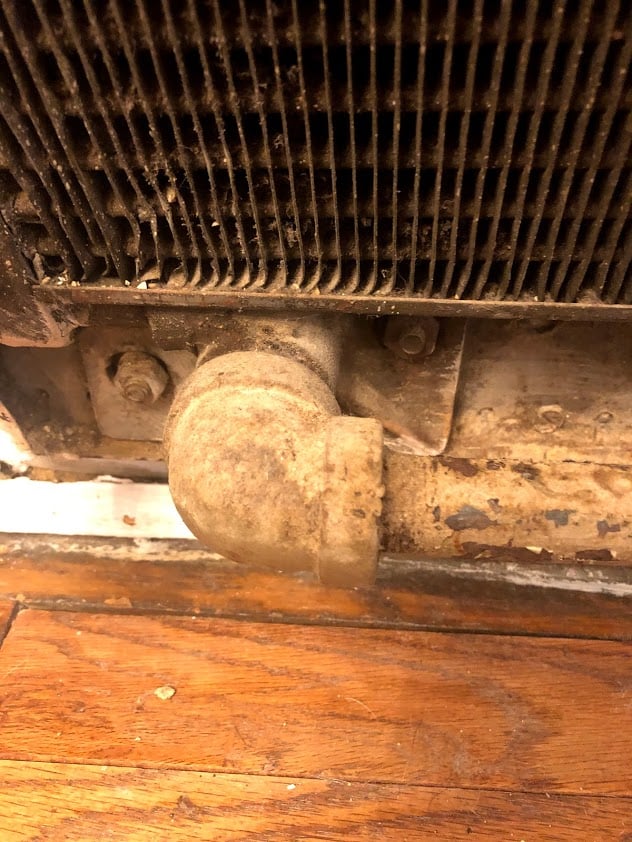
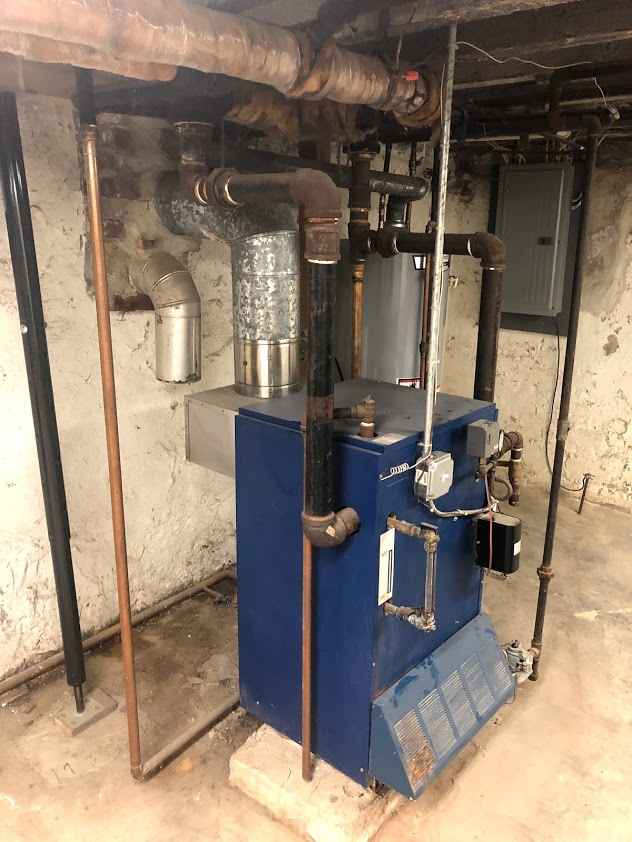
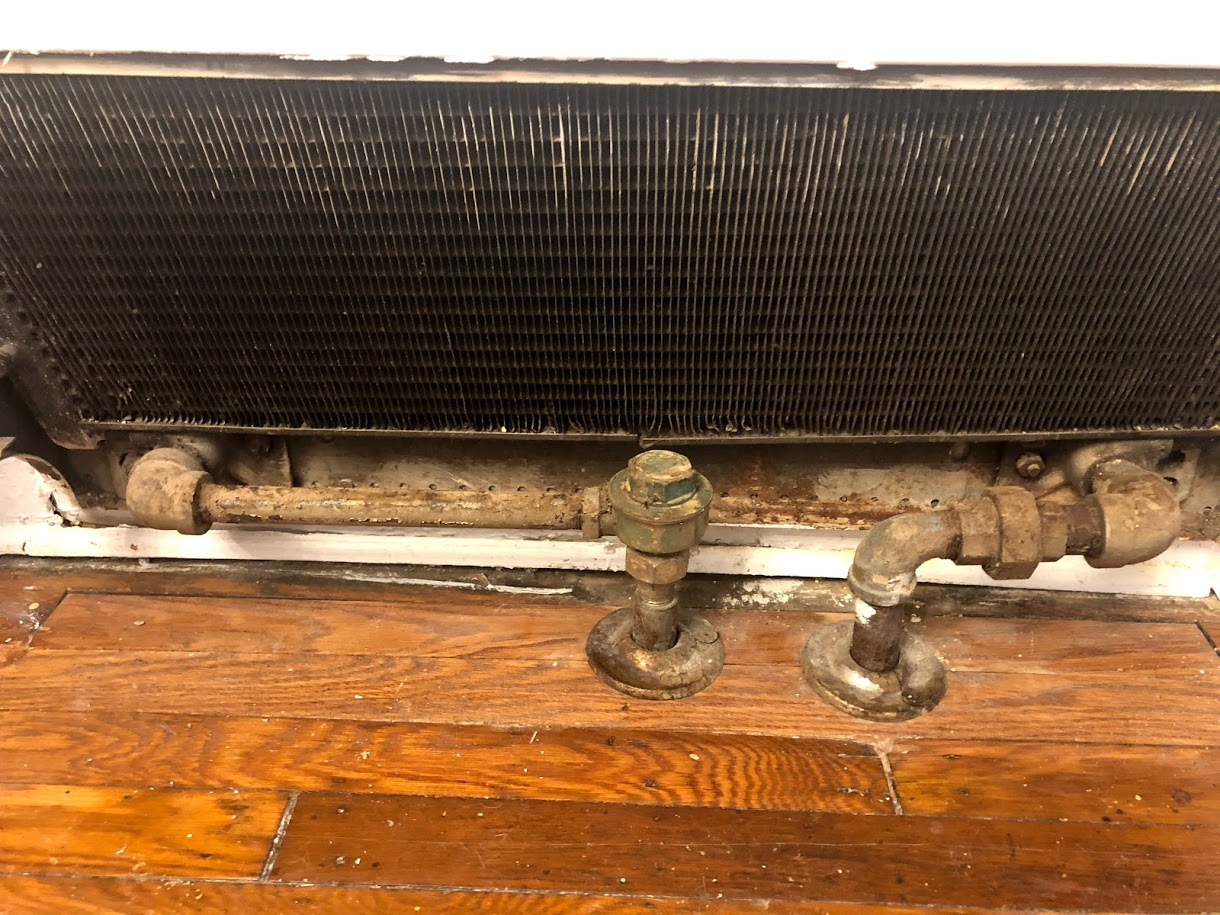
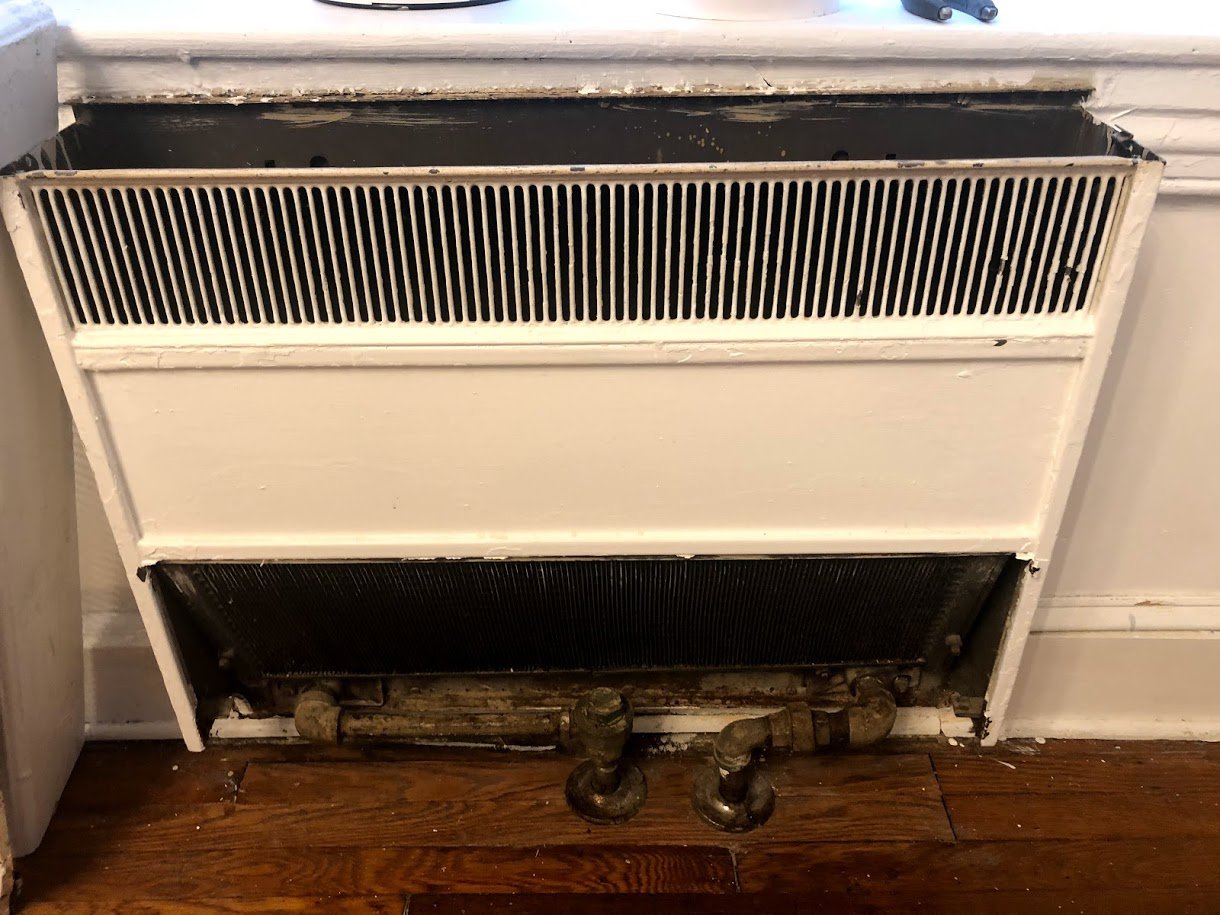
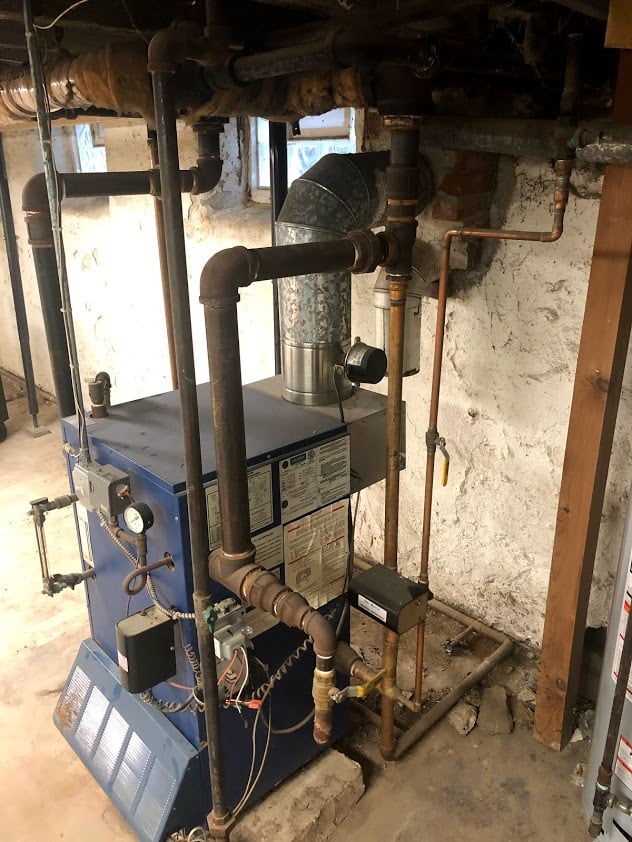
0
Comments
-
-
Yes, mains tied together (attaching photo, let me know if that is helpful). Main vent is in the opposite corner from boiler - tried to get closest pic i could.
0 -
At your air vent does it look like there is a steam trap on the small 1/2 or 3/4" piping. You may have a cross over vent.
You would do well to buy the book "We Got Steam Heat" and then the "Lost Art of Steam Heating". Quite available and great reading....money well spent.
In the meantime have you noticed the pressure gauge moving as you heat and also what is the pressuretrol set at?
Picture with the cover off would be good.0 -
Wonky is definitely a good term. However, for the moment if the system is operating without banging, while you could probably gain a small amount of efficiency by repiping, it's probably not cost effective.
The very first thing to do, though, is really quite simple: get a technician in there who really knows what he or she is doing to thoroughly clean the boiler fire side, and set and adjust the burners. This takes time, and isn't free, but it will ensure that you are getting the heat you are paying for.
That said. If your calculation of the total EDR of those convectors is reasonably correct, your boiler is almost 3 times bigger than it needs to be (310 EDR can output only about 75,000 BTUh). That works out to about 30 BTUh per square foot -- which is a remarkably poor way to size a heating system, but the number is at least in the ballpark. This suggests that while the convectors are likely sized reasonably, the boiler isn't.
As noted above, if it's reasonably quiet and the boiler doesn't short cycle too badly, it may not be cost effective to do anything about it -- but that oversize boiler is costing you money in fuel.Br. Jamie, osb
Building superintendent/caretaker, 7200 sq. ft. historic house museum with dependencies in New England1 -
As @Jamie Hall took the word out of my mouth
"That said. If your calculation of the total EDR of those convectors is reasonably correct, your boiler is almost 3 times bigger than it needs to be (310 EDR can output only about 75,000 BTUh). That works out to about 30 BTUh per square foot -- which is a remarkably poor way to size a heating system, but the number is at least in the ballpark. This suggests that while the convectors are likely sized reasonably, the boiler isn't.
As noted above, if it's reasonably quiet and the boiler doesn't short cycle too badly, it may not be cost effective to do anything about it -- but that oversize boiler is costing you money in fuel."
I would recheck the calculated edr. If the boiler is really 2 or 3x larger than you need I would budget for a new boiler and fix the boiler piping at the same time.
In the meantime I would clean the convectors, make sure all the traps are working properly and make sure the venting is up to snuff.
The fact that it works with no banging and the piping looks like it has "sort of a header" is a good sign
Try "find a contractor" on this site0 -
Thanks all. This is immensely helpful. I have not noticed the pressure gauge move during heating and the pressuretrol is set at 0.5 psi. I calc'ed the EDR using page 266 for the closest match for Warren Webster 3.5" depth convectors. I just assumed I was missing something, given the massive mismatch between the convector heating capacity and the BTU rating of the boiler.0
-
Two things pop out:
1- Looks like Beavis and Butt-head piped that boiler. It needs a 3-inch drop header to run properly, otherwise wet steam will reduce the system's efficiency. Have it repiped.
2- The main vent is pathetically small for this system. You should have at least one Gorton #2 vent and maybe two. Also make sure the crossover traps are working properly. In many cases, we upgrade them using Barnes and Jones' "Big Mouth Crossover Traps". All this lets air leave the system quickly and quietly, so the steam can distribute faster.
Vapor systems like your Webster were the Cadillac of heating in their day, and are still some of the best out there.
What part of Southeast PA are you in?All Steamed Up, Inc.
Towson, MD, USA
Steam, Vapor & Hot-Water Heating Specialists
Oil & Gas Burner Service
Consulting1 -
@Steamhead , that made me laugh, thank you. Understood and I really appreciate the feedback. From my limited understanding of these systems, this was a very impressive system back in its day. I think the house went thru a period in the 70-80's where it was a low-budget rental (and that seems to be the era of shoddy work in this house that I am currently reversing). I am in Northwest Philadelphia (Mt Airy).0
-
I noticed that you have un-insulated piping running through a wall in the basement. to save a small amount of fuel it is best to insulate all the un-insulated piping.
Insulating the piping is a non invasive method of increasing efficiency. It acts like a high paying bond that will pay a dividend for ever.
In old houses like yours and one like I used to own the envelope of the house is not insulated well and can be extremely costly to upgrade.
If the house has a wooden exterior or shingle an upgrade to the house can be done without opening the interior walls.
Remove the old exterior covering, install 2" thick foam insulation and wrap the house in Tyveck.
Or fill the interior cavity of the walls of the house with blown in insulation or pressurized foam.
Check the attic for insulation make sure you have at least 12" of insulation in the attic.
Getting back to the heating plant, typically a boiler is sized to 1.33
the size needed to heat the house. That is without an internal coil to make hot water. The extra .33 btuh is for the piping pickup factor.
Cleaning the fire side of the boiler may increase the boilers efficiency and should be done for safety purposes as you do not know if that has ever been done.
Before you go crazy with vent valve replacement which is easy to do, when the heating season starts see how long it takes for the radiators to get hot. Typically steam should be in all the rads in 20 minutes and the rads should get very hot in 25 to 30 minutes.
The test should be performed from a cold boiler start. I am not in favor of installing supper vent valves in small houses.
My recommendation is one Gorton # 1 vent valve if you have only one vent valve in the system.
Based on the steam pressure you are operating at you may never know if you have a blown steam trap as all the steam is used up in the cast iron radiators in the building. If it gets real cold like down into the single digits you might find out some of the traps are bad.
The near boiler piping is a bit shoddy and should be changed when a new boiler is installed, but what concerns me is the lack of a Hartford Loop. That should be corrected asap because that can become a insurance problem. Because you have wet returns in the basement a failed wet return can empty the boiler of water. Even if you have low water cutoffs a mishap can occur and the fuel supply may not shut off and that can cook the boiler and or start a fire.
Jake
Steam: The Perfect Fluid for Heating and Some of the Problems
by Jacob (Jake) Myron0 -
Haven't read @dopey27177 's full commentary, but...
One thing: if your house has plaster and lathe walls, do not, repeat do NOT, use any form of foam in place insulation. No reputable insulation contractor will guarantee that he or she won't damage the plaster walls -- perhaps irrevocably -- for very good reason.
Further, you might find that getting at the walls from outside is more of a can of worms than you want to tackle. One of the older houses I care for has outside walls which include, reading from the inside space: 1/2 inch plaster on lathe; true 4 inch air space, 1 inch true sheathing lumber (the stuff is 1 inch true by 12 inches true, hard pine, cut nails), 1/4 inch asphaltic weather board, narrow clapboards (also cut nails), 1/8 inch asphaltic moisture barrier, and exterior shingles (put on in 1933 -- relatively modern). All in excellent condition. Needless to say, demolition and replacement would pay for a lot of fuel...Br. Jamie, osb
Building superintendent/caretaker, 7200 sq. ft. historic house museum with dependencies in New England1 -
Appreciate the feedback, both of you. I am definitely going to tackle the air-sealing/insulation conversation. The home is a twin, so my one party wall is a non-issue. The other wall has incredibly thick masonry walls with an air gap and ~1/2 inch plaster on lathe. The homes on my block all were built in the same era (1880-1890) and all are classic Germantown stone walls (for those familiar with the area). Suffice it to say, the juice might not be worth the squeeze for wall insulation.
The area of focus for me will be the mansard roof - it's original slate sides and terne metal top. I know for a fact it is totally uninsulated (replaced knob and tube on the third floor in the ceiling couple months past) and i think a lot of my heat loss is happening thru the roof. Just want to make sure I am giving proper thought to ventilation needs before i go crazy.0 -
Do the roof. Make sure you have good vapour barriers -- the last thing you want is moisture from the house in an uninsulated space! But get as much insulation in there as you can.
If it were mine, I'd leave the outside walls alone. Just leave 'em be as they are. You'll never get insulation in from the outside -- and while you might be able to blow dense pack in from the inside, first place it would probably hang up on the plaster keys and not fill the space properly, and second place repairing the plaster and any wall finishes is going to be large dollars (I personally charge more for plaster work than anything else I do -- or have done!). Not worth it.Br. Jamie, osb
Building superintendent/caretaker, 7200 sq. ft. historic house museum with dependencies in New England0 -
I'd focus on any airsealing you can do with that kind of construction. I found a ~15"x24" hole behind a kitchen cabinet that they cut to put in a vent stack then just put a cabinet in front of it. Sealing around window frames, weight pockets, plumbing/heating, electrical outlets, around the sill if you can, block the wall cavities if it is balloon frame so it doesn't pull air from the basement and anywhere else it can up and out the roof.1
-
Appreciate the input, both of you. I am definitely going to focus on airsealing first, and then try and figure out what is the best way to insulate/ventilate the mansard roof. It's original slate/terne metal so want to be respectful of the historicity and the architecture (so many homes in my area they just tarred over it in the 70's/80's....goodness gracious.1
Categories
- All Categories
- 87K THE MAIN WALL
- 3.2K A-C, Heat Pumps & Refrigeration
- 58 Biomass
- 427 Carbon Monoxide Awareness
- 113 Chimneys & Flues
- 2.1K Domestic Hot Water
- 5.7K Gas Heating
- 109 Geothermal
- 161 Indoor-Air Quality
- 3.6K Oil Heating
- 70 Pipe Deterioration
- 995 Plumbing
- 6.3K Radiant Heating
- 391 Solar
- 15.4K Strictly Steam
- 3.4K Thermostats and Controls
- 55 Water Quality
- 44 Industry Classes
- 48 Job Opportunities
- 18 Recall Announcements