Welcome! Here are the website rules, as well as some tips for using this forum.
Need to contact us? Visit https://heatinghelp.com/contact-us/.
Click here to Find a Contractor in your area.
A False Water Line is a True Solution to Water Line Issues

Gordo
Member Posts: 857
When newer (and smaller) gas or oil fired steam boilers replace their (larger) coal fired antecedents, the water level usually changes to a lower level, exposing previously flooded "wet" returns to the delightful joys of steam powered water hammer.
The false water line is an old trick to re-flood those wonderful wet returns to keep the steam out. This particular job had a boiler feed tank involved that we just can't rid of for...rea$ons.
So, in addition, a loop seal is twined up with a false water line to keep the steam out of the boiler feed tank, too.
Look, Ma! No traps!
https://www.youtube.com/watch?v=jxMlTp8QcIA
The false water line is an old trick to re-flood those wonderful wet returns to keep the steam out. This particular job had a boiler feed tank involved that we just can't rid of for...rea$ons.
So, in addition, a loop seal is twined up with a false water line to keep the steam out of the boiler feed tank, too.
Look, Ma! No traps!
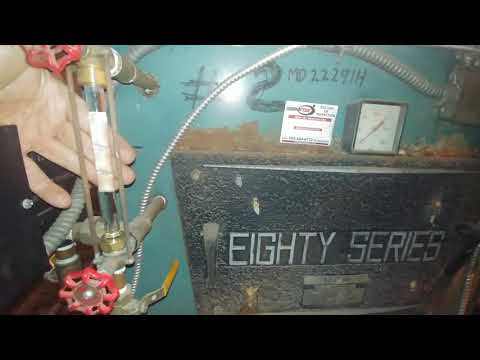
All Steamed Up, Inc.
"Reducing our country's energy consumption, one system at a time"
Steam, Vapor & Hot-Water Heating Specialists
Oil & Gas Burner Service
Baltimore, MD (USA) and consulting anywhere.
https://heatinghelp.com/find-a-contractor/detail/all-steamed-up-inc
"Reducing our country's energy consumption, one system at a time"
Steam, Vapor & Hot-Water Heating Specialists
Oil & Gas Burner Service
Baltimore, MD (USA) and consulting anywhere.
https://heatinghelp.com/find-a-contractor/detail/all-steamed-up-inc
4
Comments
-
This was our first big job- you can see more by clicking on the link in our Find a Contractor ad below.All Steamed Up, Inc.
Towson, MD, USA
Steam, Vapor & Hot-Water Heating Specialists
Oil & Gas Burner Service
Consulting0 -
-
-
We recently had to install a false waterline in conjunction with a new boiler job in a Church. It was a bit of a head scratcher at first. One side of the building had traps and vents on the radiators, the other side had no traps and vents on the radiators. It finally dawned on us that one side of the building was designed to have wet returns, and the other side dry. The last guys to install a boiler didn't grasp this concept very well, and that lead to adding radiator vents where they shouldn't be, and finally construction of an incorrect false waterline:
They made it too high however, making both returns wet, and they didn't equalize it in any case. Of course it banged and heated very poorly. The returns that should have been dry lost their main venting when they became wet, which further exasperated things...
So we tore it all out and set about making things right, with the false waterline at the correct height to keep the one return wet, and the other dry.
The photo is somewhat misleading as the boiler room is recessed from the main basement level. The lower return on the left is actually the higher, dry return. It rises up once it exits the boiler room.
We also built a trap test station off the false waterline. After testing we found that 90% of the traps were faulty (no surprise) and we got those all changed out.
We then removed the vents from the dry return radiators, added main venting, and a vaporstat to keep the pressure nice and low.
All better.New England SteamWorks
Service, Installation, & Restoration of Steam Heating Systems
newenglandsteamworks.com2 -
New England steamworks, Nice work, but while I am a fan of black steel pipe, am I seeing the same for potable water feed?
Lance0 -
Yes, but potable would be a misnomer. It is isolated with a backflow preventer. This particular jurisdiction was going full-bureaucratic-hell with a Hot Works permit, so we just said: "screw it". And then we did, in fact, screw it together...
Problem solved.New England SteamWorks
Service, Installation, & Restoration of Steam Heating Systems
newenglandsteamworks.com2 -
@New England SteamWorks Really digging the installed trap testing station! Well done!All Steamed Up, Inc.
"Reducing our country's energy consumption, one system at a time"
Steam, Vapor & Hot-Water Heating Specialists
Oil & Gas Burner Service
Baltimore, MD (USA) and consulting anywhere.
https://heatinghelp.com/find-a-contractor/detail/all-steamed-up-inc0 -
@Gordo; you may want to add a 2nd gas valve just for safety. The company I worked for recommended a 2nd gas valve on every job even when the "code" did not require one. They were very safety conscious. Nice job on the false water line. It is surprising to me as to how many contractors and system designers never heard of them. One last thing; a condensate feed tank was always installed when the company replaced an old coal unit with a new, smaller gas/oil unit due to reduced water capacity of the new units.1
-
-
@retiredguy : The second gas valve suggestion is an excellent idea! I think, however, in this case, the customer would only follow that suggestion if the boiler inspector insisted.
We have been fairly successful so far in doing "boilerfeedtank-ectomys" even on larger systems if there are wet returns (gets the water back to the boiler much faster than a dry return) and if lo-hi-lo firing is set up.
When we first walked into that boiler room back in July of 2005, there was, in addition to the boiler feed tank, 3 two inch F&T "master" traps, a condensate return pump in the flood-able (and often flooded) pit, and an extra 50 gallon piggy-back tank tied onto the boiler feed tank for good measure.
They were losing 10,000 gallons a year in leaks. Its down to less than 300gal/yr, partly due to blow-downs.
They were running both boilers at 7 psi. Now its running on one down-fired boiler, 4 oz/in2.
It took a long time, many years of bit by bit progress, to get to where it is now.All Steamed Up, Inc.
"Reducing our country's energy consumption, one system at a time"
Steam, Vapor & Hot-Water Heating Specialists
Oil & Gas Burner Service
Baltimore, MD (USA) and consulting anywhere.
https://heatinghelp.com/find-a-contractor/detail/all-steamed-up-inc1 -
-
Gordo..... we've been doing the same thing "boilerfeedtank-ectomys" and "condensate pump 'ecotomys". We used to keep the good used units, but they ended up stacking up so we got rid of most of them. Get the system vented properly, get the pressure set correctly and get the return properly configured and the water comes back plenty quick on most systems.To learn more about this professional, click here to visit their ad in Find A Contractor.1
-
Very cool stuff. It would be awesome to shadow you guys on some jobs.
I like the loop seal idea. I had a job earlier this year where they had the boiler replaced and feedwater tank installed, but didn't trap the system at all. The feedwater tank was tiny, held only a few gallons it seemed. Water line in the tank was about 6 inches off the floor. Around 1 psi there was enough steam pressure to blow steam out of the tank. They ran at 12 ounces but still had hammering when the steam reached the wet return on the floor.
I had proposed first removing the unneeded feedwater tank and converting back to gravity return. But that was shot down (the company I worked for at the time installed it...) Then I proposed a false water line tank, which was shot down (because the company I worked for at the time told them I didn't know what I was talking about and everything was working properly, except for the extreme banging and uneven heating of the building).
Now I'm wondering if I could have just gotten away with a false water line and loop seal like this. False water line would have taken care of the wet returns and loop seal would stop the steam from reaching the tank as long as there was enough room for the water to move up and down with the changes in steam pressure. And steam pressure was kept low as it should be of course.
Thank you for posting this video!Never stop learning.1 -
and everything was working properly, except for the extreme banging and uneven heating of the building).
Simple solutions are the best. But loopy loops don't look simple to those too impatient to figure out purpose of those loops. At first glance they're "plumbers' nightmare".
Now I'm wondering if I could have just gotten away with a false water line and loop seal like this. False water line would have taken care of the wet returns and loop seal would stop the steam from reaching the tank as long as there was enough room for the water to move up and down with the changes in steam pressure. And steam pressure was kept low as it should be of course.
0 -
@jumper I agree. I'd imagine the false waterline tank would look pretty "loopy" too lol.Never stop learning.0
Categories
- All Categories
- 87K THE MAIN WALL
- 3.2K A-C, Heat Pumps & Refrigeration
- 58 Biomass
- 427 Carbon Monoxide Awareness
- 113 Chimneys & Flues
- 2.1K Domestic Hot Water
- 5.7K Gas Heating
- 109 Geothermal
- 161 Indoor-Air Quality
- 3.6K Oil Heating
- 70 Pipe Deterioration
- 994 Plumbing
- 6.3K Radiant Heating
- 391 Solar
- 15.4K Strictly Steam
- 3.4K Thermostats and Controls
- 55 Water Quality
- 44 Industry Classes
- 48 Job Opportunities
- 18 Recall Announcements