Question - Load calcs for existing large buildings
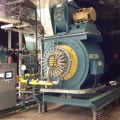
When it comes to very large buildings, how do you go about accomplishing that? Are their companies you can hire to do it? Is it costly? Is it possible to find original design info for the building anywhere?
I've been to a few Carrier system design classes. They suggested using "check figures" to estimate loads and in a worst case scenario it could be accurate enough select equipment. I need to find some load calc classes to attend.
I may have a project coming up for a large-ish building. It currently has three 2 million btu Aerco Benchmark condensing boilers that need to be replaced. I have not had a project of this size before where I might be part of the design. I work on and service equipment of this size and much larger every day, but never participated in load calcs. Any advice appreciated.
Comments
-
The principles are basically the same for a large building as they are for a small one... except... in a larger building, you have to account much more cleverly for occupancy and exposure. Occupancy -- how many people, what kind of machinery, even what kind of lighting -- makes a much bigger difference in a large building. To a first approximation, heat loss increases with the surface area of the building, which increases somewhere between linearly and the square of the size, but occupancy increase somewhere between the square and cube of the size. Exposure is much more important in bigger buildings -- but affects control and system balance more than heat loss.
And yes, there are professionals on whom one can call. Architects and some Mechanical Engineers should be qualified to do the job -- and shouldn't quote on it or accept the work if they aren't. Not to say that some don't. Sorry. They aren't cheap. On the other hand, they should also stand behind their work...Br. Jamie, osb
Building superintendent/caretaker, 7200 sq. ft. historic house museum with dependencies in New England1 -
-
@Mike Sheppard,
If your replacing the boilers just do a "Block Load" of the building not usually that hard. Yes, having the original prints will help.
I would look at the age of the building for a clue. If the Aerco's are original to the building replacing them with the same size would be safe. If it's an old building all bets are off. Usually with two boilers the correct way is to size each boiler at 80% of the load. Gives you some redundancy and one boiler during the worst weather will keep the place from freezing. So doing a load is best becucase you don't know how they figured. redundancy. People and lighting have no affect on a heat loss.....you have to heat the place when empty and with the lights off.
When I had to do one I did it the old long hand method.
If you get an engineer farmalier with the buildings construction they will square foot it and be pretty accurate.
Don't forget any make-up air coming in through any ac or ventilating system1 -
We do these calculations often. We use the IBR "whole house" method. Google earth is very valuable for measuring buildings and sometimes windows as well.
With these tools you can get pretty close. If you need to be very precise, you could spend a day measuring with a helper. Then spend a day making calculations. Not saying we haven't done it, just not necessary on every job. I can tell you that when we do our own load calculations on commercial jobs, we often downsize equipment significantly.
We have worked on several large apartment buildings in the last few years with "full flow" make-up air handlers. These make-up units were designed to replace the heated air the bathroom and kitchen fans exhausted. I can tell you that the make up load can be significant, especially with one hundred percent outside air.2 -
@STEVEusaPASTEVEusaPA said:Can you get your hands on the original construction/mechanical blueprints? Someone may have done all the work already.
I am going to try. The building was built in 1965. If they don't have physical copies on-site is there any way of finding them in an archive or something?
@EBEBRATT-EdEBEBRATT-Ed said:@Mike Sheppard,
I would look at the age of the building for a clue. If the Aerco's are original to the building replacing them with the same size would be safe. If it's an old building all bets are off. Usually with two boilers the correct way is to size each boiler at 80% of the load. Gives you some redundancy and one boiler during the worst weather will keep the place from freezing. So doing a load is best becucase you don't know how they figured. redundancy. People and lighting have no affect on a heat loss.....you have to heat the place when empty and with the lights off.
Don't forget any make-up air coming in through any ac or ventilating system
The Aercos aren't original. They are the second set of boilers. The originals were two Kewanee firebox boilers, which happen to still be in the boiler room. They never removed them. The building was built in 1965.
What is your opinion on sizing boilers in large residential applications like this? Everything I've read read says size the boilers to add up to 100% of the load. Do people prefer sizing each boiler at 80% in large applications like this?
Make-up air is something I will have to find out. Most of these places use gas fired RTUs for the hallways which introduce make-up air, but they also heat the air already. I'm assuming that could lower the load on the boilers. Most of these places only have heat emitters in the living spaces.
@ScottSecorScottSecor said:We do these calculations often. We use the IBR "whole house" method. Google earth is very valuable for measuring buildings and sometimes windows as well.
Would you happen to have a link to information on the IBR method? How would you size the boilers percentage-wise? Two boilers each sized for 50%? or higher?
@Jamie Hall thank you for the info. I have a lot of learning to do. I've taken several week-long design classes but we never really got into doing actual heat loads. We learned about design of the systems already knowing the heat load, and touched a little bit on the different types of loads that add to a heat load, such as solar loads, transmission, people, lights etc. I need to find a good class that can tie all of this together where we perform actual load calculations. I will also look into what it would cost to have a professional perform it. May be worth it if we can downsize the boilers and cost.Never stop learning.0 -
Mike, we used to do it with the IBR pencil and paper method years ago. Switched to the Slant Fin CD years ago and still use that and the current Slant Fin online software. We have used Siggy's software in the past as well for layout and heat loss calcs. We also use other software when required, but these are my preferred methods, especially if we only need a rough estimate.
As far as Google Earth, if you download the software there is a "ruler" at the top of the page that allows you to calculate the length and width of the building, etc. In my experience, the ruler is typically within a few percent of actual size.
With regard to percentages of load for boiler sizing it depends on the type of building, budget and other factors. With buildings such as hospitals (that we've never designed) they will typically have at least one hundred percent redundancy. With Senior Public Housing apartments, they typically have between fifty and one percent redundancy. With private office buildings and apartment buildings, we typically see twenty to fifty percent redundancy. These same rules apply to dhw production and heating circulator pump sizing.
We use the Taco HSS software for design and layout most of the time.
https://www.slantfin.com/slantfin-heat-loss-calculator/
http://www.tacocomfort.com/products/design_tools/hydronic_system_solution/index.html#
https://www.hydronicpros.com/
https://www.hydronicpros.com/1 -
@Mike_Sheppard , back to your sizing/redundancy question, depends on many additional factors (below assumes hot water, not steam).
1. If it's a project on a real tight budget and we are confident on the actual heat loss (know all of the 'r' values, window values, etc), know the required water temps on design day, etc we will size two boilers for fifty percent of the actual load.
2. For projects with a reasonable budget, we will size the equipment with some redundancy. This is especially true if the boilers are condensing with high turn-down ratios. Often we'll spec two, three of four boilers that will total up to 150% of the load. This allows for one boiler to be down and no noticeable difference with regard to temperature.
3. For high end projects, they prefer or even require 100% redundancy. In simple terms, let's assume load on design day is five million BTU, they demand we spec and install ten million BTU.
Often we are faced with type 1 projects. Only one time since I've been doing designs have we got that dreaded complaint, "The system you installed is not keeping up!" This was a large greenhouse with radiant slab and overhead high temperature unit heaters. The (two) one million btu boilers were actually condensing when the sun set on cold December days, despite primary secondary piping. We ended up installing a (third) one million btu boiler at cost and it solved the problem of the massive start up load. Boilers lasted over twenty years before the greenhouse was demolished for new apartments. Ironically, this was the last greenhouse we worked on...1 -
What we've done for many years is look at the historic fuel usage of the building. We take the average monthly temps and the average daily usage of the coldest months we can find on the gas bills and deduct the average daily usage of the summer months. This gives us the average usage per day at a given outdoor temp. Asking what temperatures are maintained in the building and looking at the building construction should allow you to get a pretty accurate guess of the building balance point ( internal heat gains equal heat loss, or when heat begins being needed). Take this temperature (usually between about 55 and 65F) deduct the monthly average temp in the winter to give you the number of degrees the heating system is heating the building. Divide teh daily usage calculated above by the number of degrees and you get the number of btu's /day. Divide that by 24 to get btus per hour per degree. Multiple that by ( the building balance point minus the design temp) to get the raw btu/hr input on the coldest day. However, that number is usually too low because the heat loss due to infiltration is directly related to temperature.. We usually add about 15% to compensate for the extra heat loss.
EX>
1000 therms used for the month (30 days)
Average Temperature 28F
Typical summer month usage 100 therms /month (30 days)
Heating usage for month;
1000 therms - 100 therms = 900 therms
heating usage per day
900 therms / 30 = 30 therms/day
heating usage per hour
[30 therms /day] / 24 hours/day = 1.25 therms/ hour or abotu 125,000 btu/hr
building is lightly insulated construction of the early 1960's
so it probably can stay warm down to about 60F outside, and then the heat needs to kick on.
Temperature difference for above month
60F - 28F = 32 F
Btus/ F load
[125,000 btu/hr] / 32F = 3906 btu/F
With design temperature of -5F and balance point of 60F,
Design change in temperature between in and out is
60F -0 [-5F) = 65 F
Raw heating usage
3906btu/f x 65F = 253,890 btu/hr
Additional for air infiltration increases:
253, 890 btu/r x 115% = 291,973 btu/hr
This is btu/hr input to the heating equipment
Figuring boiler efficiency can be very tricky as the published efficiency really can't be used. I use the efficiency curve for atmospherics found in Burnham's modular boiler literature of the National board curve ( same curve) to determine at what efficiency the boilers are firing at during this month.
Heating load
[291, 973 btu/hr] / 70%( boiler efficiency) = 417,104 input.
if the building is using setback, you will probably need to bump this number by 30 to 50% depending on how deep a setback and how often.
Ventilation loads are rather tricky. However, what is usually ignored is that if the ventilation system is operated according to occupancy in the building, the ventilation loads increase as the building occupancy increases, however, the internal gains from people also increase, reducing the space heating needs.
To learn more about this professional, click here to visit their ad in Find A Contractor.1 -
If the boilers are on there own gas meter there should be valuable info available there. Some gas companies log daily on commercial meters. Find the daily use on your design day and you have everything you need.
For clients that are planning way in advance, data loggers are awesome. You can log pulses on the meter. On/off cycles on burner motors, you name it. I am logging an 7.6 million BTU plant next winter to see how much additional load it can take for a future expansion.
Do be careful to look at the condition of all the building equipment. I logged a 6.4 million BTU boiler and determined that it only really used about 1.2 on design day. After a closer look, I discovered 800,000 BTU's of hydronic makeup air units that the tenant had not maintained and were not running. That was almost a big mistake."If you can't explain it simply, you don't understand it well enough"
Albert Einstein1 -
Never thought about using the gas usage information. Hopefully that is something I will be able to get from them. Thank you for the example @The Steam Whisperer (Formerly Boilerpro)
@Zman any specific data loggers you'd suggest? That is a great idea. Would be great to do this for customers with older boilers. I could apply this at many locations.Never stop learning.0 -
I use Hobo Loggers.
These are nice for single stage burners https://www.onsetcomp.com/products/data-loggers/ux90-004m
You just subtract the pre/post purge times in excel.
These state loggers will log pulse meters like gas and water meters https://www.onsetcomp.com/products/data-loggers/ux90-001m ,you can also use a CT switch https://www.onsetcomp.com/products/sensors/csv-a8 and a state logger to measure electrical current to anything.
Put one of these outside https://www.onsetcomp.com/products/data-loggers/ux100-003 and you will have real outside temps.
The Hobo software will graph the results. You can dump all of it into excel to work out the math.
"If you can't explain it simply, you don't understand it well enough"
Albert Einstein0
Categories
- All Categories
- 87K THE MAIN WALL
- 3.2K A-C, Heat Pumps & Refrigeration
- 57 Biomass
- 426 Carbon Monoxide Awareness
- 116 Chimneys & Flues
- 2.1K Domestic Hot Water
- 5.7K Gas Heating
- 109 Geothermal
- 160 Indoor-Air Quality
- 3.6K Oil Heating
- 70 Pipe Deterioration
- 991 Plumbing
- 6.3K Radiant Heating
- 389 Solar
- 15.4K Strictly Steam
- 3.4K Thermostats and Controls
- 54 Water Quality
- 44 Industry Classes
- 48 Job Opportunities
- 18 Recall Announcements