Welcome! Here are the website rules, as well as some tips for using this forum.
Need to contact us? Visit https://heatinghelp.com/contact-us/.
Click here to Find a Contractor in your area.
Brewery boiler issues
Options

sraburne
Member Posts: 16
I currently posted concerns about brewery low pressure steam boiler having vacuum issues causing overfilling and learning about operating pressures. I did install a vacuum breaker which took care of the vacuum and overfilling and i also increased the operating pressure from 8 PSI to 10 PSI it increase the steam pressure. Thank you for all the help on these issues. I ordered Mr Wohlfarth book Brewing with steam.
Within minutes of going through the book I got a little nervous.
The enclosed picture shows
Steam header is welded and the steam supply is not in the correct location.
The pipe off of the steam traps, the condensate has to be lifted and i am 80% sure their is no check valves.
This system was installed by a boiler company, not me I just volunteered with pay, to work on it.
My question is will the header being welded or the condensate pipe having no check valves becoming an issues, safety or production. I need to inform them about.
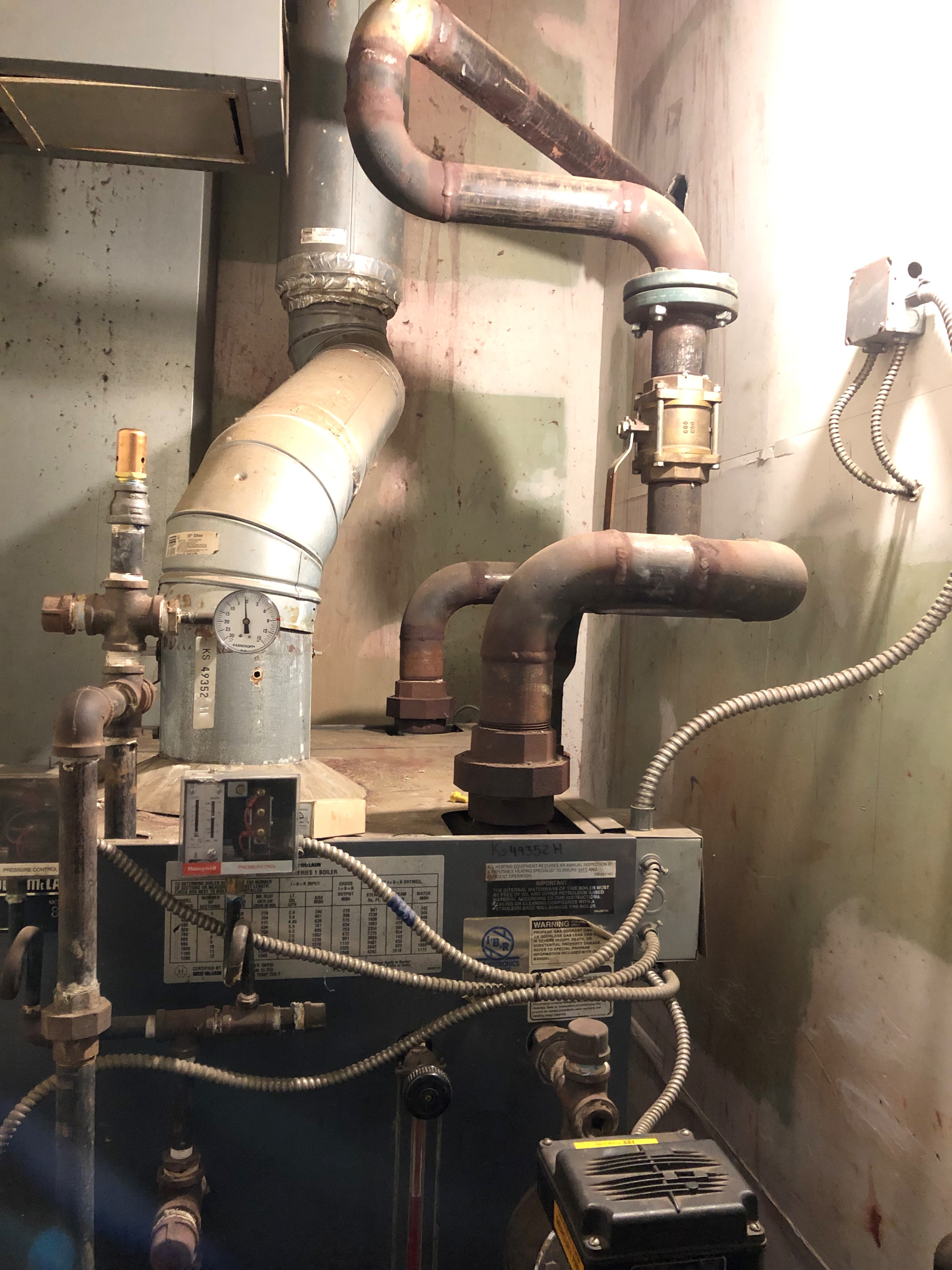
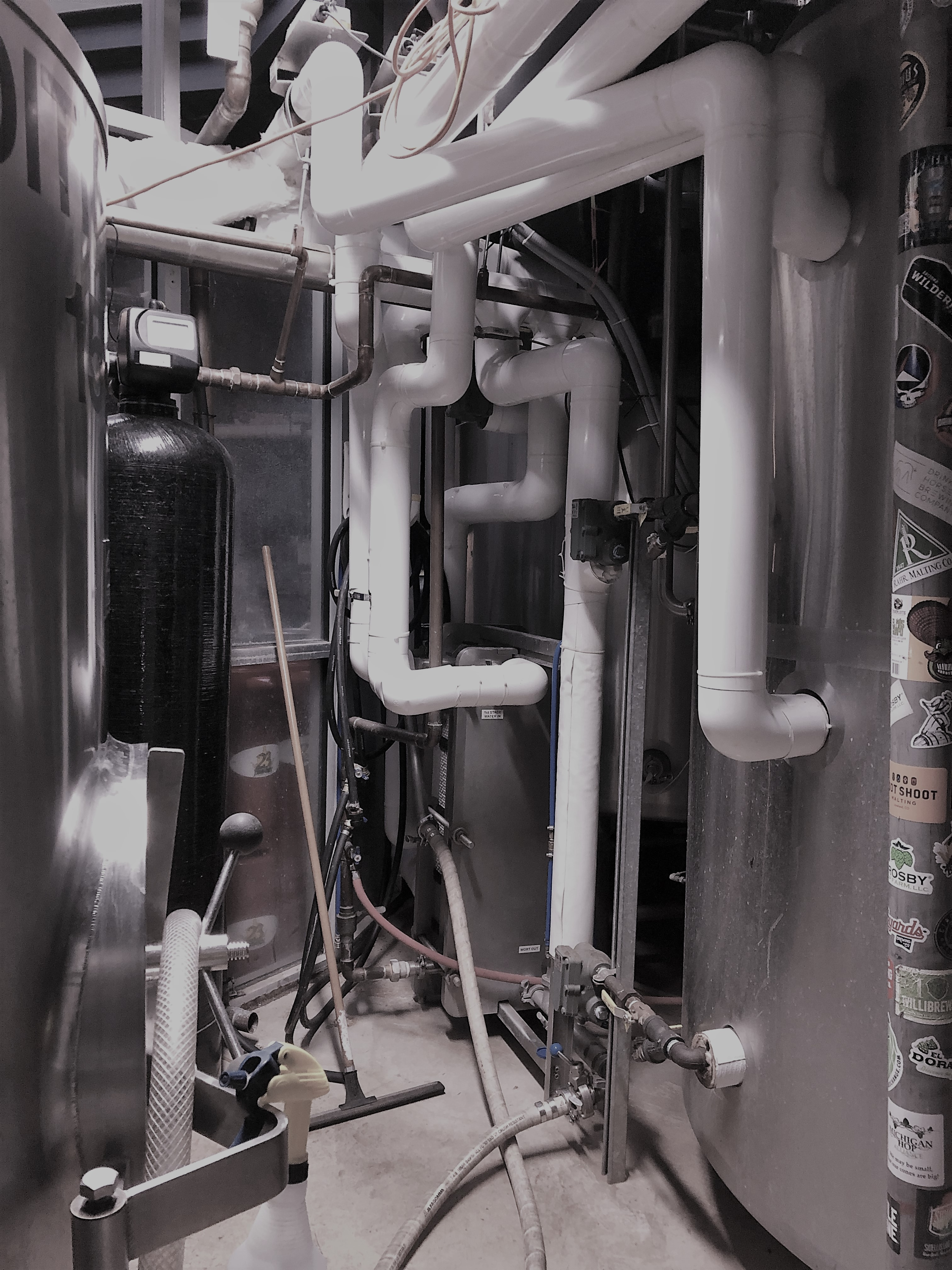
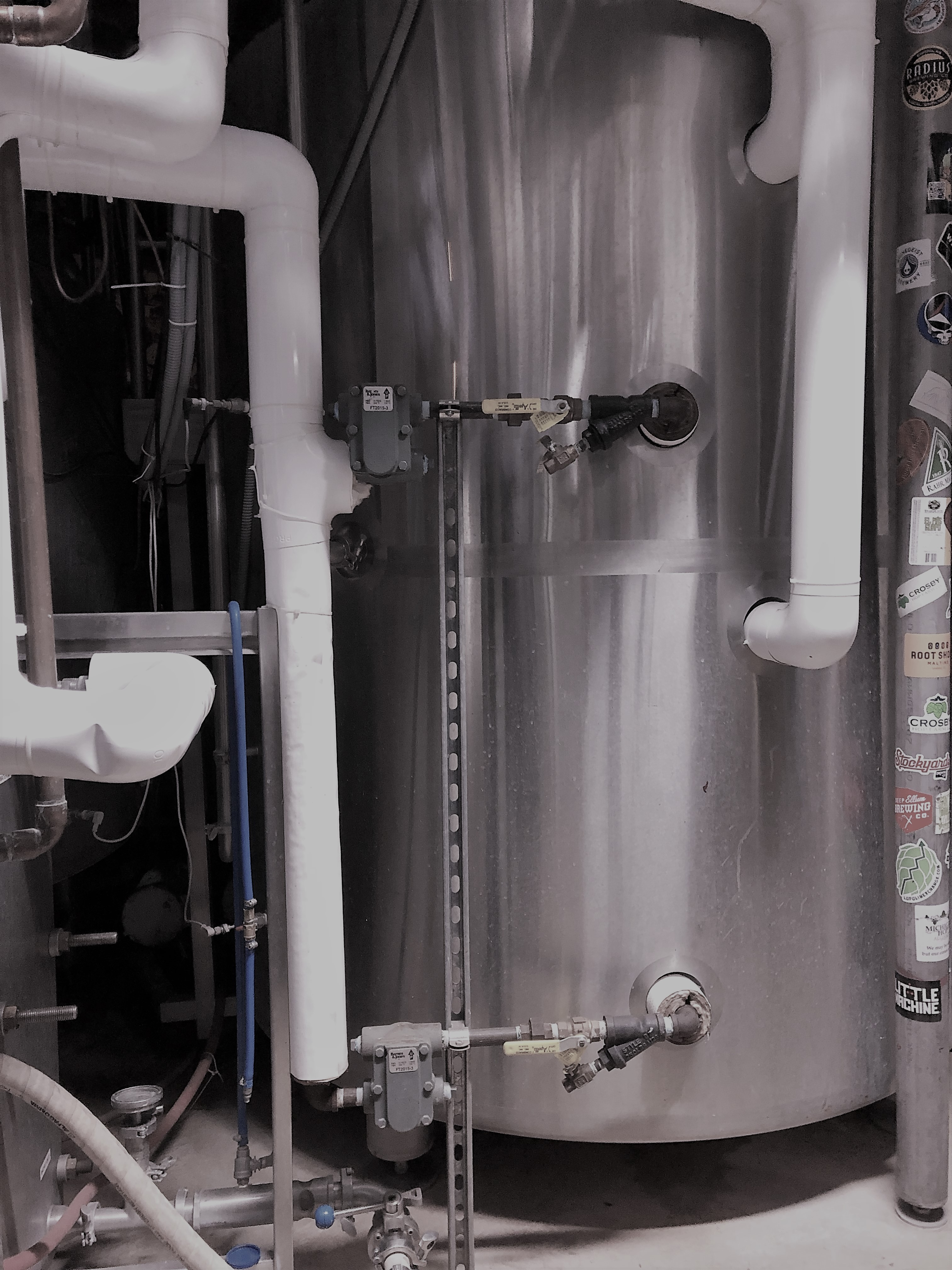
0
Comments
-
Got to admit I'm not really keen about that welded header. Do I assume from what I can see that it is solidly welded? If so, it may be putting quite a bit of stress on the boiler block -- and itself -- while the boiler is warming up (and static stress, if it isn't exactly the same length as the openings in the boiler). I'd be happier if you had flanged joints connecting the riser stubs to the risers rather than unions; the flanged joints would give just enough laterally to reduce the stress.
But hopefully others, more experienced than I, will also comment.Br. Jamie, osb
Building superintendent/caretaker, 7200 sq. ft. historic house museum with dependencies in New England0 -
Thanks Jamie
I appreciate the input, I am trying to keep an open mind about this system, but the more I read about it The more nervous I get .
The boiler this one replaced blow up, I was told.
Happy new year0 -
If the condensate has to rise up then check valves should be installed on the trap outlet pipes.
With regard to welded pipe headers. Many on this site are against welded headers. But the largest pipe that can PRACTICALLY be screwed together these days is 4" and it is common for many contractors to weld anything 2 1/2" and up. Boilers that need 5", 6" 8" 10" 12" or larger
headers are welded more often than not.
That being said, the risers come up out of the boiler and the horizontal branches that run over to the header should be longer if possible to build some flexability into the header. Yes welded pipe can flex. Burnham recommends 18" minimum on the horizontal.
It is possible that the header can cause stress on the boiler and cause boiler failure if expansion and contraction are disregarded.
Do this: Take a pc of 2" black pipe 2' long and stand it on the floor vertically. Put moderate hand pressure on it.....it won't move.
Now take the same pipe with a 2" 90 on each end. Cut 2 18' pieces and screw them into the 90s facing in the same direction (like the letter C)
stand this mess up with the end of the bottom 18" pc up on a block of wood or something. Push down on the end of the top 18" pc. You can move it 1/4" with no problem and it's not because of screwed fittings.0 -
We did a Weil-McLain 488 with a Powerflame gas set using 6” cast iron fittings for the header and two 5” by 5’ boiler risers.
DL Mechanical LLC Heating, Cooling and Plumbing 732-266-5386
NJ Master HVACR Lic# 4630
Specializing in Steam Heating, Serving the residents of New Jersey
https://heatinghelp.com/find-a-contractor/detail/dl-mechanical-llc
https://m.facebook.com/DL-Mechanical-LLC-315309995326627/?ref=content_filter
I cannot force people to spend money, I can only suggest how to spend it wisely.......0 -
@sraburne Thanks for buying the book. The piping should not affect the safety and only the efficiency. The idea of the takeoff to the system between the last boiler tapping and the equalizing pipe is to dry the steam. The way it is piped will allow wet steam which will lower the efficiency of the system. @Dave0176 did a nice job of piping and the steam should be much drier because of using drop headers and the proper location of the takeoff to the system.
The header may be a bit low. I like using at least 24" above the boiler as a min.
I have a brewery here where they lift the condensate and i do not like that. They work great when the steam is on 24/7 but as soon as you shut off the boiler, you lose your lift. I like to gather the condensate from the vessels in a small condensate tank. From there it can be piped back to the boiler feed unit.
You may want to consider an air vent on the steam trap for the vessel as air may not be able to get out.
To be sure the boiler is safe, have it checked twice a year and test the low water cutoff regularly. That is the leading mechanical cause of boiler accidents.
@Jamie Hall was right about the welded header. A threaded header allows the expansion and contraction of the pipe. The pipe expands at a great rate than the cast iron boiler.
Ray Wohlfarth
Boiler Lessons0 -
Hi All
I am back on this same steam boiler. I have installed vacuum breakers on the steam header before the zone valve ( their are 4 jackets each with its own zone valve) also I installed vacuum breaker at the boiler 24" above the water line. The issues of the boiler overfilling has been resolved. Thanks for your help.
The brewery asked he to increase the operating pressure setting from 9PSI to 10.5PSI.
I told him the pressure relief will trip at 15PSI. I have my manual high pressure set at 12PSI.
He has been using it the past month at this setting. During my last visited he told me, that he has had to reset the manual safely multiple times, but mostly in the morning when he arrives.
what I am seeing is when all the zones temperate are satisfied and the zone valves close. Their is no were for steam to give up its energy and boiler pressure increases and trips the high pressure safety. The boiler burner dose turn off at the set pressure . I don't think the relief valves is blowing off.
I was think if i had a bypass valve piped from the steam header to the feed water condensate tank, throw a steam trap. This valve would open when 4 zone valve were closed.
Know that i read this I my be over thinking this. Maybe just lower the pressure setting be to 9 PSI.
Thank you for your time,
Steve Raburne
0 -
Hello @sraburne,
Why not just shut the boiler down when all 4 zones are satisfied ? If a zone (any zone) calls for steam start the boiler up again. Why waste fuel making pressure that just causes nuisance tripping of the manual safely high pressure switch ?
What is going on (or not going on) in the morning when he arrives that would cause the high pressure nuisance tripping ? Does the system use less zones in the morning ?
National - U.S. Gas Boiler 45+ Years Old
Steam 300 SQ. FT. - EDR 347
One Pipe System0 -
@sraburne Im glad its working better. For a brewery, I typically set the manual limit control to 15 psi and try running the boiler around 11 psi. As far as the boiler tripping, I think it may be because the boiler will continue to make steam even after the burner is off. This could cause the pressure to rise. Try these settings and see how it goes. I would also verify the manual reset limit shuts off at the set pressure. It may be tripping at a lower pressure. Good luckRay Wohlfarth
Boiler Lessons0 -
One thing that you may want to consider would be to tie in a small zone valve off the steam header that would open when the boiler is shut down to dump the steam into a device such as the condensate tank or something else that could utilize that steam. Instead of just wasting the steam, it would be put to good use.0
Categories
- All Categories
- 87K THE MAIN WALL
- 3.2K A-C, Heat Pumps & Refrigeration
- 58 Biomass
- 426 Carbon Monoxide Awareness
- 113 Chimneys & Flues
- 2.1K Domestic Hot Water
- 5.7K Gas Heating
- 109 Geothermal
- 161 Indoor-Air Quality
- 3.6K Oil Heating
- 70 Pipe Deterioration
- 994 Plumbing
- 6.3K Radiant Heating
- 391 Solar
- 15.4K Strictly Steam
- 3.4K Thermostats and Controls
- 55 Water Quality
- 44 Industry Classes
- 48 Job Opportunities
- 18 Recall Announcements