Welcome! Here are the website rules, as well as some tips for using this forum.
Need to contact us? Visit https://heatinghelp.com/contact-us/.
Click here to Find a Contractor in your area.
Flow rates through existing slab radiant system

offshell
Member Posts: 7
I purchased a home last January and have already spent a bit of money trying to get some of the heating options sorted out. One of the systems was a an outdoor boiler/indoor electric boiler system. I had the wood boiler disconnected for this season since I'll be traveling. While that was done, I had them replace the 12 port manifold with a newer one with flow rate adjustment and add an outdoor reset and slab sensor.
After the new manifold went in, the flow rates have been consistently running around .15 GPM over the 12 loops wide open. The circulating pump is a 1/25 HP Grundfos 15-58FC but it makes no real difference between the medium and high settings. There's an 60kbtu Seisco SH-18 running at the moment and its putting out 120F water and the return is showing around 70F.
Since the pump looked easy enough to swap out, I tried putting a larger 1/6 HP Steibel Eltron CP3S26-110BFC on it this past weekend only to have the end result show the exact same flow rate of around .15 GPM irrelevant of the low/med/high setting on the much larger pump.
I don't technically know what the length or even locations of the 12 zones are within my house other than two of them being labelled for the garage. There was a lot of gunk in the system after the wood boiler was disconnected so it was flushed for quite a while. I've also taken the clean out plates off the boiler and tried to clean them as well as I could as well. Nothing seems to make a difference.
Is the flow rate of .15 GPM with the delta temp a concern? Why wouldn't the larger pump make any difference in the flow rate? When I release all the pressure from the system, and then add the pump (either one of them) back in and then raise the pressure back up to around 15PSI, the initial start of the pump causes a slightly higher flow rate, then by the time the air is out of the system again it seems to have fallen back to the .15 GPM. If I close down all but one of the lines, I can get up to about .8GPM from the larger pump and maybe .8 or .7GPM from the smaller pump equally on any one specific line. Open two lines and it drops to .5 or less etc and then down to .15 with all lines open.
Any suggestions or advice?
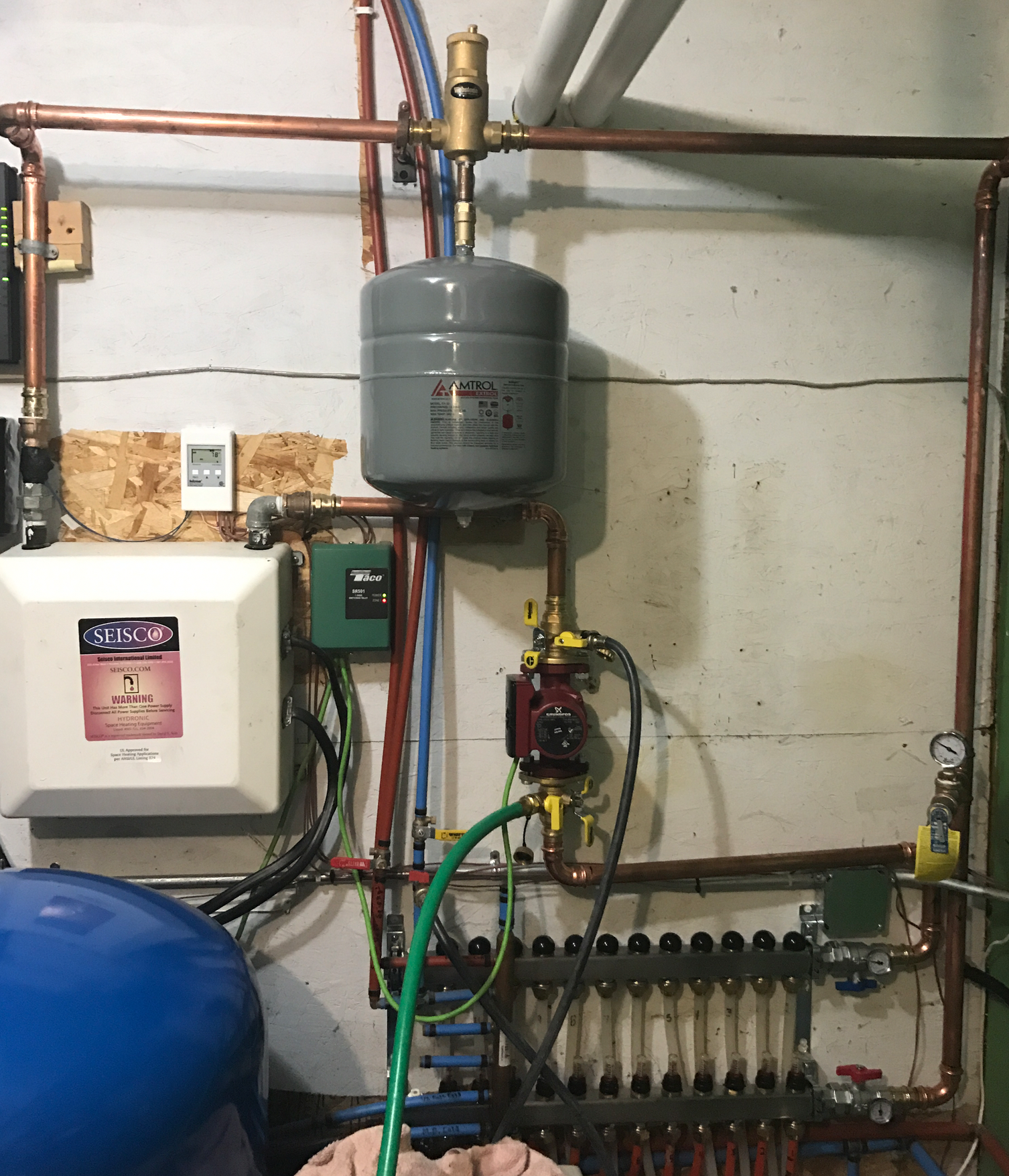
After the new manifold went in, the flow rates have been consistently running around .15 GPM over the 12 loops wide open. The circulating pump is a 1/25 HP Grundfos 15-58FC but it makes no real difference between the medium and high settings. There's an 60kbtu Seisco SH-18 running at the moment and its putting out 120F water and the return is showing around 70F.
Since the pump looked easy enough to swap out, I tried putting a larger 1/6 HP Steibel Eltron CP3S26-110BFC on it this past weekend only to have the end result show the exact same flow rate of around .15 GPM irrelevant of the low/med/high setting on the much larger pump.
I don't technically know what the length or even locations of the 12 zones are within my house other than two of them being labelled for the garage. There was a lot of gunk in the system after the wood boiler was disconnected so it was flushed for quite a while. I've also taken the clean out plates off the boiler and tried to clean them as well as I could as well. Nothing seems to make a difference.
Is the flow rate of .15 GPM with the delta temp a concern? Why wouldn't the larger pump make any difference in the flow rate? When I release all the pressure from the system, and then add the pump (either one of them) back in and then raise the pressure back up to around 15PSI, the initial start of the pump causes a slightly higher flow rate, then by the time the air is out of the system again it seems to have fallen back to the .15 GPM. If I close down all but one of the lines, I can get up to about .8GPM from the larger pump and maybe .8 or .7GPM from the smaller pump equally on any one specific line. Open two lines and it drops to .5 or less etc and then down to .15 with all lines open.
Any suggestions or advice?
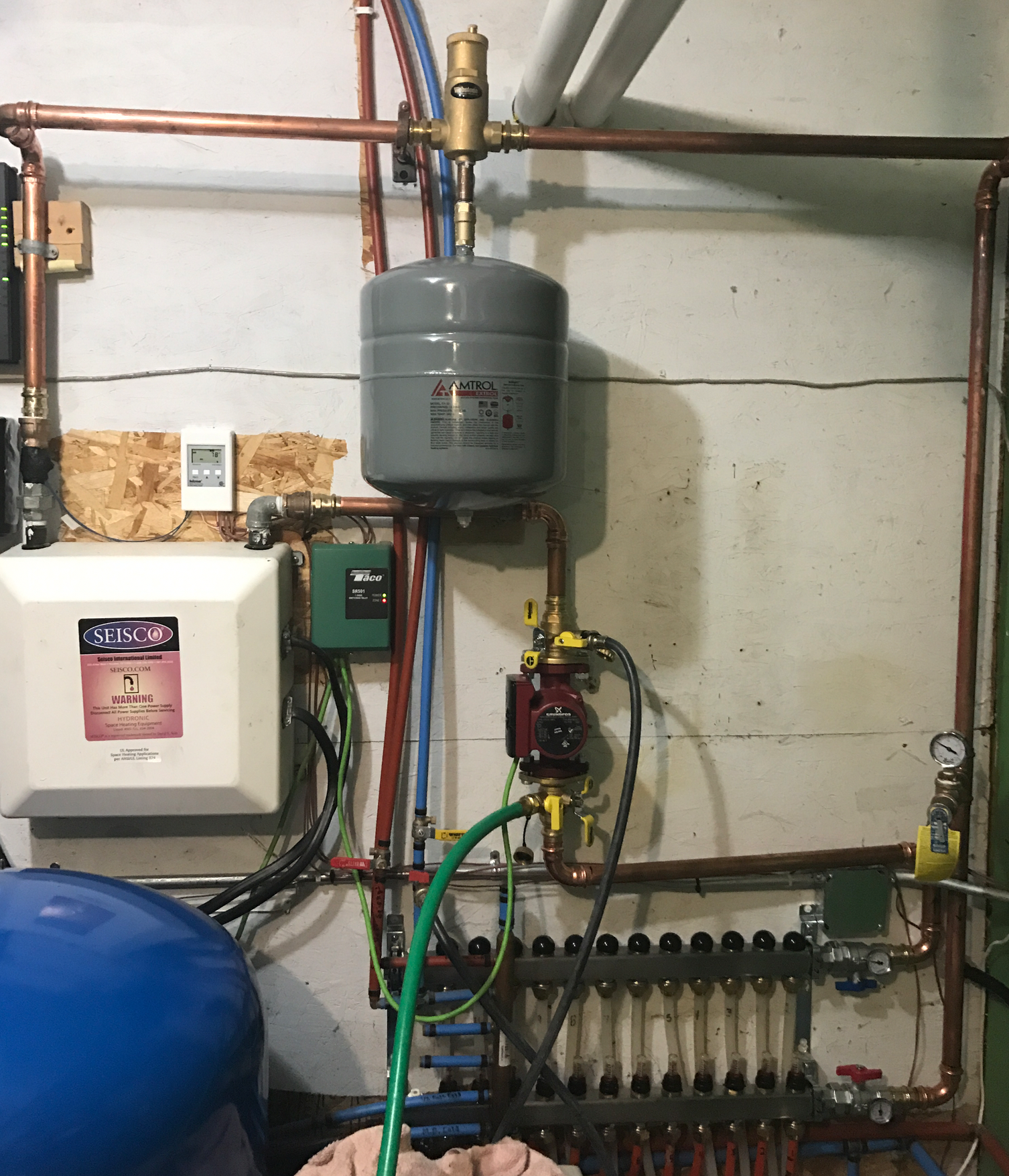
0
Comments
-
Are you sure all air is purged? Is the circulator pumping in the right direction? I can't tell from your pic which way it's pumping.Bob Boan
You can choose to do what you want, but you cannot choose the consequences.0 -
It's pumping up into the boiler from the return then up over and down into the supply. I guess I'm not 100% sure if it's all purged. I've never connected directly to the manifold to try to purge air. Probably worth trying.0
-
I see you have handy dandy taps on both sides of the pump. Can you put a pressure gauge on each tap temporarily, and see what the pressure difference across the pump is for your various conditions? That will tell you where the pump is operating on its curve.
Something is out of whack here...Br. Jamie, osb
Building superintendent/caretaker, 7200 sq. ft. historic house museum with dependencies in New England0 -
You have to isolate and purge EACH loop individually.Bob Boan
You can choose to do what you want, but you cannot choose the consequences.0 -
If you are certain that you have flow, and the system is circulating, could be the indicators are not workingBob "hot rod" Rohr
trainer for Caleffi NA
Living the hydronic dream0 -
Thanks for the quick responses. I just hooked up to the manifold fill ports and started moving port by port through the process of purging and it seems like theres a ton of air in the system otherwise I have a different issue. Line 1 has been running so far by itself for maybe 10 minutes and is still throwing air bubbles into the bucket. Whats the usual time frame for a single line that might have a ton of air in it?0
-
Very well could be... especially if the wood boiler gunked up the piping.
0 -
better hoses make a difference too. Dropped the garden hose for the hoses from my washer and it doesn't still gets the air in the line but isn't sucking air at the attachment point.0
-
Ok, purged air from each line individually. After that I was able to start it back up and saw slightly better flow rates with the smaller 15-58FC pump. Might have to try the larger pump again. Will try to get back to it tomorrow. Thanks for all the help. I'll try picking up some other pressure gauges as well to try some of the other suggestions.0
-
-
That's what I was doing last night. I hooked up a hose to the supply and another to the return on the manifold. Closed the main manifold valves then shut off all 12 ports on top and bottom then opened one and turned on the fill valve, ran it for 10 minutes or so then closed it up and moved to the next one down the line. The flow was a bit better between .15 and .30 this morning so this evening I spent a bit of time running the lines a bit more and then put the larger pump back on. Right now all of the lines are around .3 to .5 GPM which is a decent increase for me so far but will have to see if it changes over night.
Last night I didn't have a hose long enough to get to the drain so I picked up a new hose and a cheap pressure gauge to drop in before the pump so when I have a chance this week I'm going to try running a lot more water through every line to see if there's any more air to clean out.0 -
I had a job a couple years back w a similar issue. problem ended up being the manifolds. Same issue... changed them out to get the indicators and the manifolds were incredibly restrictive. I swapped those out for the simple copper versions. Problem solved.0
-
That would be pretty annoying. There was a copper manifold on there previously so I was trying to upgrade ha. The one on there is an Uponor 12 port http://www.supplyhouse.com/Uponor-Wirsbo-A2701202-12-Loop-1-Stainless-Steel-Radiant-Heat-Manifold-Assembly-w-Flow-Meter0
Categories
- All Categories
- 87K THE MAIN WALL
- 3.2K A-C, Heat Pumps & Refrigeration
- 58 Biomass
- 426 Carbon Monoxide Awareness
- 116 Chimneys & Flues
- 2.1K Domestic Hot Water
- 5.7K Gas Heating
- 109 Geothermal
- 160 Indoor-Air Quality
- 3.6K Oil Heating
- 70 Pipe Deterioration
- 994 Plumbing
- 6.3K Radiant Heating
- 389 Solar
- 15.4K Strictly Steam
- 3.4K Thermostats and Controls
- 54 Water Quality
- 44 Industry Classes
- 48 Job Opportunities
- 18 Recall Announcements