Welcome! Here are the website rules, as well as some tips for using this forum.
Need to contact us? Visit https://heatinghelp.com/contact-us/.
Click here to Find a Contractor in your area.
Had some bad advice and need some new direction.

bauer0667
Member Posts: 4
Hi,
I have a 32'x41' older red iron building with 12" wide insulated wall panels ( with only about 2.5" fiberglass insulation) that lock together tongue and groove style. The building has 11ft high walls with some 4" Batt insulation and a tin roof. There are two 4'x9' pella windows and a commercial glass walkthrough door 3'x8'. A 14"x9" insulated garage door and a 9'x7' insulated garage door. The concrete floor is 6" thick with 2" pink foam board insulation and a vapor barrier under it. The rebar was ran and the pex was zip tied to it, so its about 3" from the surface. I did a heat loss calculator and got 35,615 BTU/Hr Loss ( I don't know if this is 100% right).
The floor has 4 circuits of 1/2" nibco oxygen barrier pex two circuits are at 150ft and two are at 360ft ( I now know I should have had more circuits, they shouldn't exceed 300ft and should have all been close to the same length hence the bad advice). The 150ft circuits run about 12" away from the edge of the concrete floor and around the parameter of the shop. The 360ft circuits run back and forth in the middle of the shop. All are 12" apart from each other.
I have a 105,000 btu propane crown cast iron boiler with a Bell and Gosset HV Series 102210 with a max GPM of 40 and 0-12ft head range.
Here is some questions I need some advice on:
Does the heat loss btu seem logical?
What size circulator pumps will I need?
What should be head loss be at?
I would really appreciate any advice on how to move forward. Below is the how we are thinking about setting up the boiler.
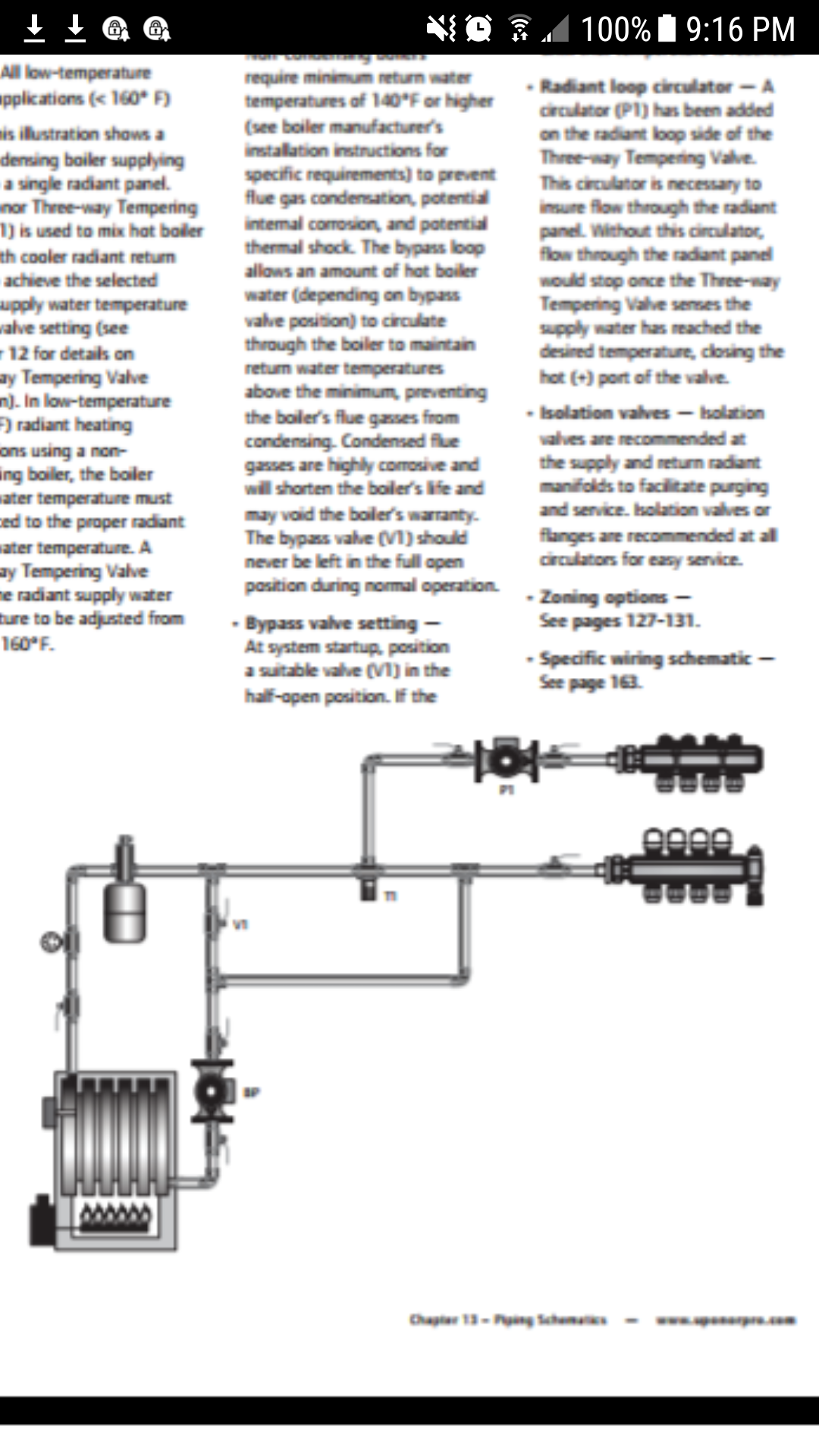
I have a 32'x41' older red iron building with 12" wide insulated wall panels ( with only about 2.5" fiberglass insulation) that lock together tongue and groove style. The building has 11ft high walls with some 4" Batt insulation and a tin roof. There are two 4'x9' pella windows and a commercial glass walkthrough door 3'x8'. A 14"x9" insulated garage door and a 9'x7' insulated garage door. The concrete floor is 6" thick with 2" pink foam board insulation and a vapor barrier under it. The rebar was ran and the pex was zip tied to it, so its about 3" from the surface. I did a heat loss calculator and got 35,615 BTU/Hr Loss ( I don't know if this is 100% right).
The floor has 4 circuits of 1/2" nibco oxygen barrier pex two circuits are at 150ft and two are at 360ft ( I now know I should have had more circuits, they shouldn't exceed 300ft and should have all been close to the same length hence the bad advice). The 150ft circuits run about 12" away from the edge of the concrete floor and around the parameter of the shop. The 360ft circuits run back and forth in the middle of the shop. All are 12" apart from each other.
I have a 105,000 btu propane crown cast iron boiler with a Bell and Gosset HV Series 102210 with a max GPM of 40 and 0-12ft head range.
Here is some questions I need some advice on:
Does the heat loss btu seem logical?
What size circulator pumps will I need?
What should be head loss be at?
I would really appreciate any advice on how to move forward. Below is the how we are thinking about setting up the boiler.
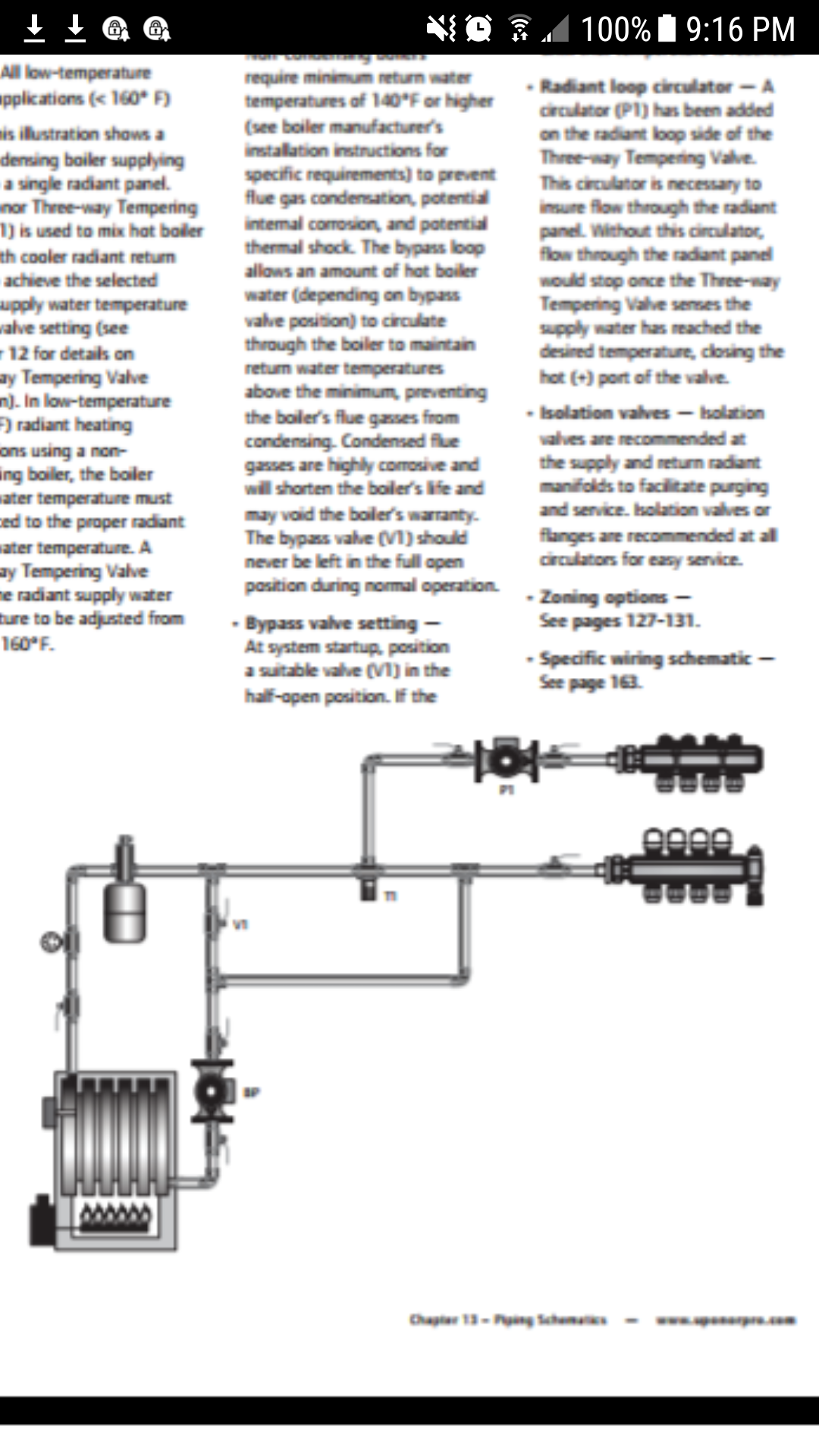
0
Comments
-
Well, without knowing design temperatures it's a little hard to say. But as a wild guess, the heat loss isn't too far off, although it's possibly low.
That then requires about 22 BTUh per square foot, which isn't unreasonable for a concrete floor.
With a reasonable delta T -- 10 degrees -- that would take a little less than 10 gpm.
So -- a couple of thoughts. And I'm sure some of the radiant pros will chime in (steam is my particular area). First, I suspect the boiler is oversize. Second, I suspect the pump is oversize. Third, that boiler doesn't like to condense -- but the floor doesn't like to be hot, so you are going to have to do some interesting mixing and tempering to get the requirements of the two to match. And fourth, it will be easier to balance the system hydraulically if you hook the two 150 foot loops together in series to make on 300 foot loop.Br. Jamie, osb
Building superintendent/caretaker, 7200 sq. ft. historic house museum with dependencies in New England2 -
Agree with Jamie. Also, when you exceed 300' on a 1/2" loop, you get beyond the capacity of the smaller wet-rotor circs like a Grundfos ups15-58. I don't have the info in front of me at the moment, but I'll check it tonight on how much head a 360' loop has at the required gpm.
Another thing to consider (as Jamie said), is the CORRECT mixing system for a slab. Variable speed injection mixing is the best approach.
http://www.tekmarcontrols.com/images/_literature/356_c_01.pdf?lbisphpreq=1Bob Boan
You can choose to do what you want, but you cannot choose the consequences.0 -
You really don't have adequate return protection for the boiler. That function is critical in a high mass system like slab radiant as it can keep the boiler running cold for hours.
A bypass valve as shown is not a good method, it is a fixed position valve and cannot react to return temperature.
Your system is similar to 3-6 below.
You will need to get a manifold with balance valves to dial in those varying lengths.
You have the pieces, boiler is probably oversized if you load number is accurate. It just needs so massaging and a few additional components.
Bob "hot rod" Rohr
trainer for Caleffi NA
Living the hydronic dream0 -
You really don't have adequate return protection for the boiler. That function is critical in a high mass system like slab radiant as it can keep the boiler running cold for hours.
A bypass valve as shown is not a good method, it is a fixed position valve and cannot react to return temperature.
Your system is similar to 3-6 below.
You will need to get a manifold with balance valves to dial in those varying lengths.
You have the pieces, boiler is probably oversized if you load number is accurate. It just needs so massaging and a few additional components
___________________________________________________________________
Yes I ran into this problem already. However utilizing the close T's and having a primary and secondary pump should help bring the boiler temp up before returning into the boiler. The attachment shows this.
0 -
Nope, primary secondary will not provide absolute protection either. It will provide blending of temperatures based on various P or S flow rates and temperatures.
You need a temperature responsive device to have boiler return protection.Bob "hot rod" Rohr
trainer for Caleffi NA
Living the hydronic dream0
Categories
- All Categories
- 87K THE MAIN WALL
- 3.2K A-C, Heat Pumps & Refrigeration
- 58 Biomass
- 427 Carbon Monoxide Awareness
- 113 Chimneys & Flues
- 2.1K Domestic Hot Water
- 5.7K Gas Heating
- 109 Geothermal
- 161 Indoor-Air Quality
- 3.6K Oil Heating
- 70 Pipe Deterioration
- 995 Plumbing
- 6.3K Radiant Heating
- 391 Solar
- 15.4K Strictly Steam
- 3.4K Thermostats and Controls
- 55 Water Quality
- 44 Industry Classes
- 48 Job Opportunities
- 18 Recall Announcements