How best to throttle down condensate feed pump flow?

A technical question: after watching a video about steam boilers (posted on the wall earlier: https://forum.heatinghelp.com/discussion/163167/steam-boiler-the-inside-story), the video talks about 'modulating' condensate return into the boiler as to not collapse steaming bubbles with adding too much condensate return too quickly. Video shows what happens with steam under slower and then faster condensate return rate - makes sense 100% - and suggests best practice being to 'modulate' condensate return to match the steaming rate.
When our feed pump comes on, it quickly reduces the built up 2-3-4 oz op pressure down to 0. If the boiler is in low fire mode, pressure will drop and it can trigger high fire. This quickly builds pressure up to 8 oz, then the low fire again kicks in and settles around 3-4 oz until the next time float switch calls for water.
So, on our WM LGB 7 condensate return/feed tank we now have 2 isolation valves, regular ball valves. I throttled them both down to about 1/3 or 1/2 closed to slow down the rate the condensate pumps into the boiler when the float switch calls for it. (Throttling down only one creates quite a loud hum, both of them throttled down some makes it virtually silent.) This has the desired effect of slowed down pumping rate, and naturally, the pump motor is running a bit longer. This has in fact stopped the steam collapsing and the pressure in the boiler holds steady at about 3-4 oz after the pump shuts off. So, problem is solved, low fire stays low, and in high demand and high fire, op pressure also stays at 3-4 oz. Steam bubbles are not collapsing. Yay!
My question - aside from throttling down with ball valves, is there any other valve better suited to do this with - like some kind of flow check valve - or should I even worry about it? Or, is there a way to reduce the pumping rate of the motor aside from perhaps lowering voltage to the motor with some kind of a modulating resistor on the 110 line? The motor is your standard one coming from Hoffman, model 609.
Reason I ask: I'm quite sure that the 33 gpm pumping rate will after a while eat-away at the ball of the valve, eventually rendering the valve useless if trying to use it isolate boiler from the tank and vice versa when servicing. Am I overthinking this?
Long question - thanks for reading!
Valves about 1/3 to 1/2 way closed:
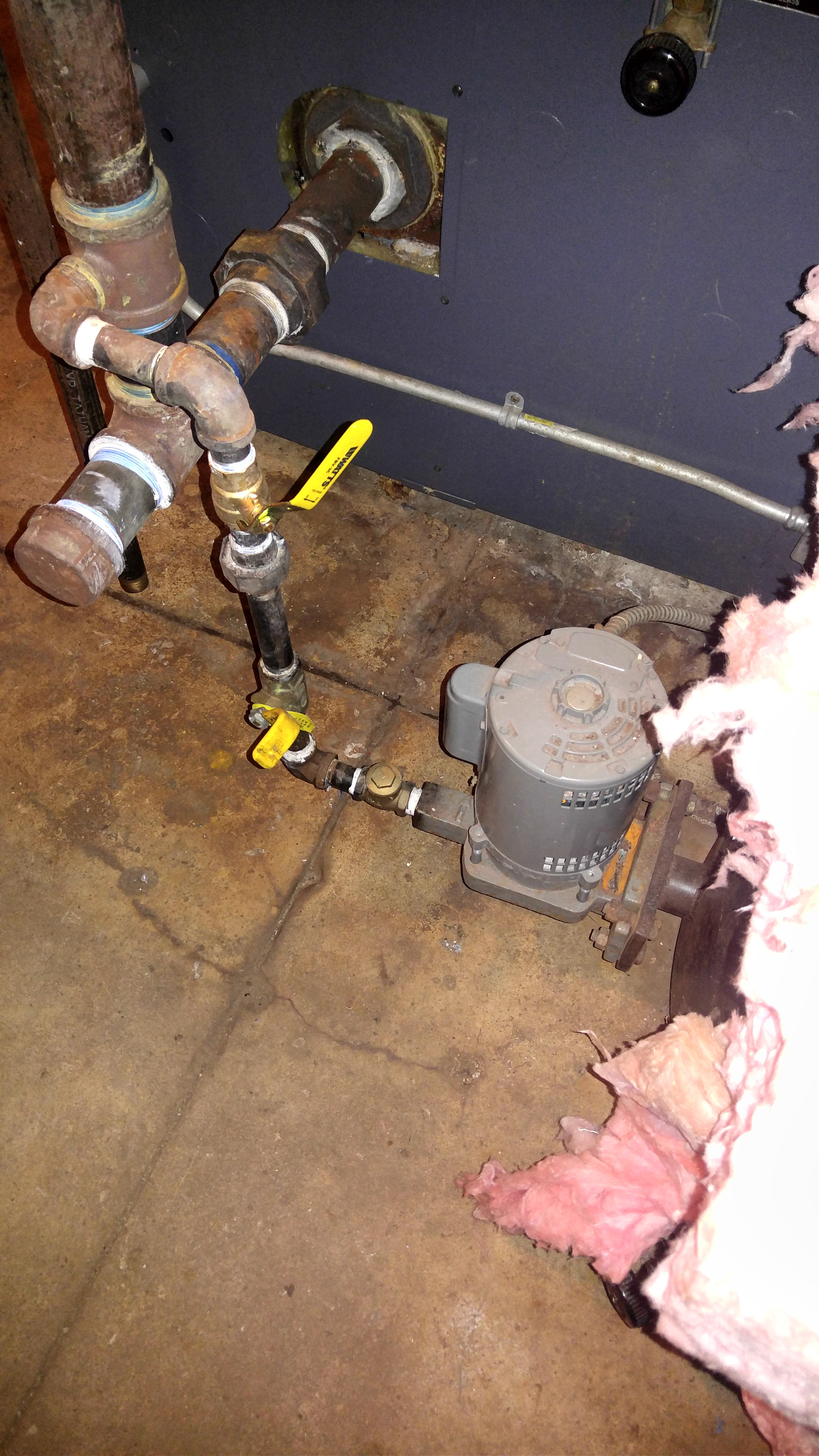
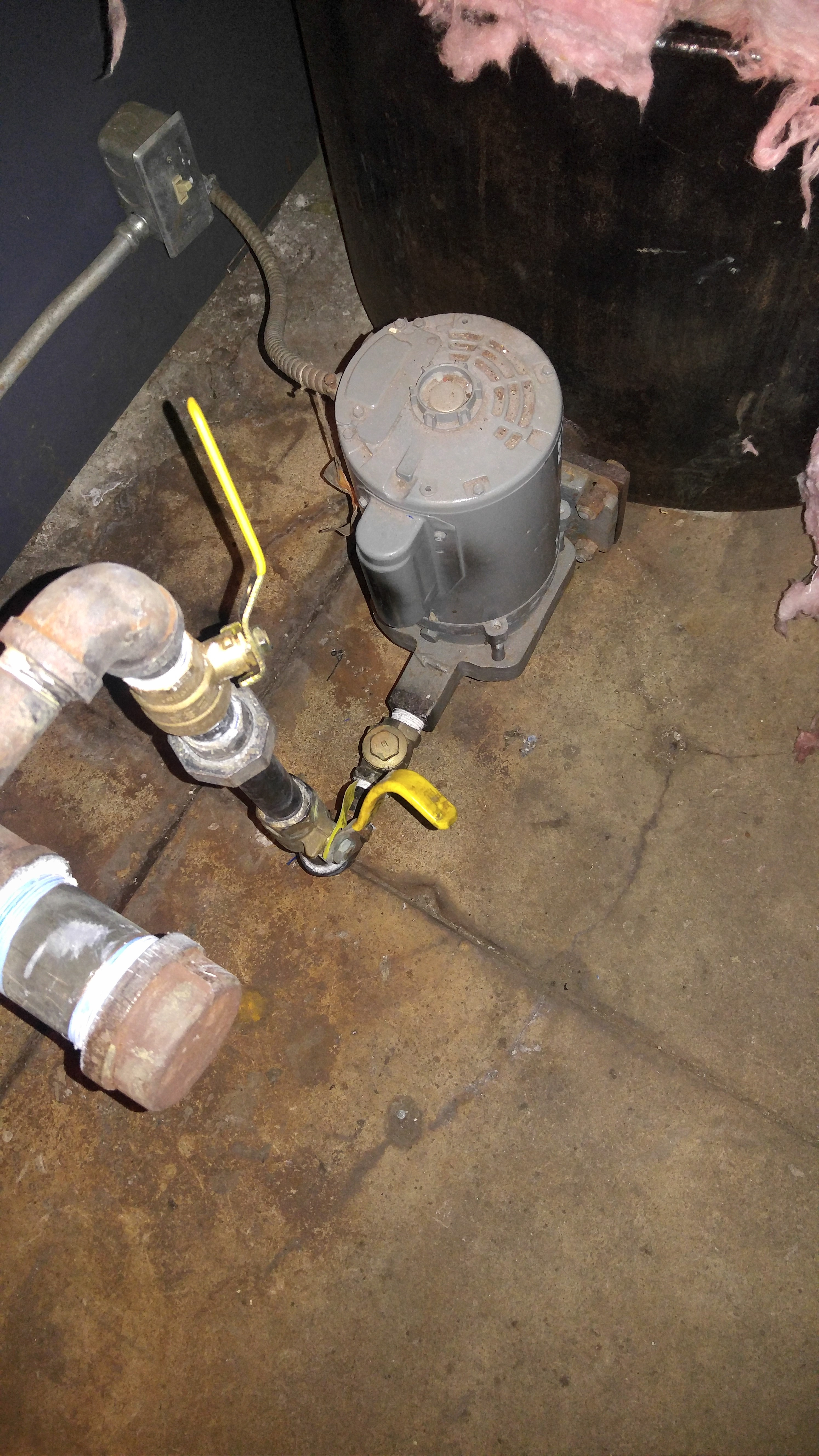
Comments
-
I just rebuilt a cond pump feed into a boiler.
I inserted a 3/4" brass gas stop.
These are the type that need a wrench to turn. The internal passage is reduced a lot even when fully open. Just having that resistance seemed to be enough for my job.
These are sometimes referred to as "square head balancing cock" or gas IB? stops.
I believe there is a specific device for the purpose but none are close to me.
I improvise a lot for a 42 YO boiler repair. This was a take out...used.
Anything installed will wear from the water turbulence, IMO
It is better to keep the ball valve at the boiler connection in working order for pump service, so I would not throttle that one at all.-1 -
Relief may be kinder. A controlled circuit feeding some of pump output back.0
-
The ball valves will take a lot of wear. They aren't bullet proof, but they will take a good bit of wear. Whatever you do, don't try to throttle that motor by reducing the voltage. That doesn't work on induction motors and can damage -- or ruin -- the motor.Br. Jamie, osb
Building superintendent/caretaker, 7200 sq. ft. historic house museum with dependencies in New England-1 -
Thanks Jamie - I was just reading about that not being an option as it can burn out the motor. I think I'll stick with throttling down the valve for now.Jamie Hall said:The ball valves will take a lot of wear. They aren't bullet proof, but they will take a good bit of wear. Whatever you do, don't try to throttle that motor by reducing the voltage. That doesn't work on induction motors and can damage -- or ruin -- the motor.
Should I be worried about the motor working harder?0 -
No. It's rated for it.MilanD said:
Thanks Jamie - I was just reading about that not being an option as it can burn out the motor. I think I'll stick with throttling down the valve for now.Jamie Hall said:The ball valves will take a lot of wear. They aren't bullet proof, but they will take a good bit of wear. Whatever you do, don't try to throttle that motor by reducing the voltage. That doesn't work on induction motors and can damage -- or ruin -- the motor.
Should I be worried about the motor working harder?Br. Jamie, osb
Building superintendent/caretaker, 7200 sq. ft. historic house museum with dependencies in New England0 -
Thanks! That's great!Jamie Hall said:
No. It's rated for it.MilanD said:
Thanks Jamie - I was just reading about that not being an option as it can burn out the motor. I think I'll stick with throttling down the valve for now.Jamie Hall said:The ball valves will take a lot of wear. They aren't bullet proof, but they will take a good bit of wear. Whatever you do, don't try to throttle that motor by reducing the voltage. That doesn't work on induction motors and can damage -- or ruin -- the motor.
Should I be worried about the motor working harder?0 -
The motor will be working less hard with the valve throttled than it will with the valve wide open. Put an amprobe on the motor and check it if you want to. The less water it pumps the less amps it will draw.
In the past a square head gas cock was recommended for balancing or throttling pump flow. A "circuit setter" balancing valve would be better but cost $$. Ball valves will work and are cheap$$$
The first part where you talk about "modulating condensate return" they are probably referring to industrial jobs where they run the feed pumps continuously and put a modulating control valve in the pump discharge line to each boiler. This valve is controlled by a modulating feed water level control (mounted on the boiler) that matches feed water into the boiler based on the steaming rate. It feeds the boiler feed water all the time when it is operating. Not on-off like smaller jobs2 -
This is 3/4" type L hard copper over 40 years that was part of a HW recirc return line. It was just downstream of a ball valve that has been throttled for maybe only 10 years.
The valve still works but apparently the turbulence of water washed away the pipe solder joint. This is all of the copper left inside the socket of the valve. No pieces had to be dug out.
There is a sharpie mark on the pinhole that developed and became obvious. The solder joint was not leaking.
This will not be a problem with your pump line, but seemed to be a good place for show and tell.1 -
Thank you everyone. I thought I read somewhere, a few years ago, maybe it was the pump manual itself, that pump needs to be throttled down for flow control.
@EBEBRATT-Ed : did not know amps will fall with throttled down valve on the output side. Somehow I thought it would be the opposite - kind of like the hot air furnace blower motor which draws more amps when airflow is obstructed (like a dirty filter). But I guess this is only on the start up. Interesting indeed! Thanks for that info!
As to "modulating", it was exactly what you said - big commercial boilers. But it got me thinking that slowing down condensate intake will allow our boiler to maintain steaming output (as in not drop op pressure, and it did!). Probably why I read pump should be throttled.
@JUGHNE
Attached is the picture of the nipple I took off from that equaliser, seen in the pic with the valves with a cap on it. That is downstream from the feeder, in line with lower return on the boiler. I took it off to wand the boiler and when I cleaned it to reinstall, it looked like this. I replaced it with sch. 80 pipe, for good measure. I was quite certain this was from turbulance. I wonder if throttling down the flow will have a positive effect on it, but also how it'll affect the 3/4" lines after the valves. I suppose time will tell. Turbulence inside pipes can indeed create havoc. This nipple was in there for 5 months. Thanks for sharing that pic.0
Categories
- All Categories
- 86.8K THE MAIN WALL
- 3.1K A-C, Heat Pumps & Refrigeration
- 57 Biomass
- 425 Carbon Monoxide Awareness
- 109 Chimneys & Flues
- 2.1K Domestic Hot Water
- 5.6K Gas Heating
- 105 Geothermal
- 160 Indoor-Air Quality
- 3.6K Oil Heating
- 70 Pipe Deterioration
- 966 Plumbing
- 6.3K Radiant Heating
- 385 Solar
- 15.3K Strictly Steam
- 3.4K Thermostats and Controls
- 54 Water Quality
- 44 Industry Classes
- 47 Job Opportunities
- 18 Recall Announcements