Welcome! Here are the website rules, as well as some tips for using this forum.
Need to contact us? Visit https://heatinghelp.com/contact-us/.
Click here to Find a Contractor in your area.
I couldn't find this one in the search box.

Double D
Member Posts: 447
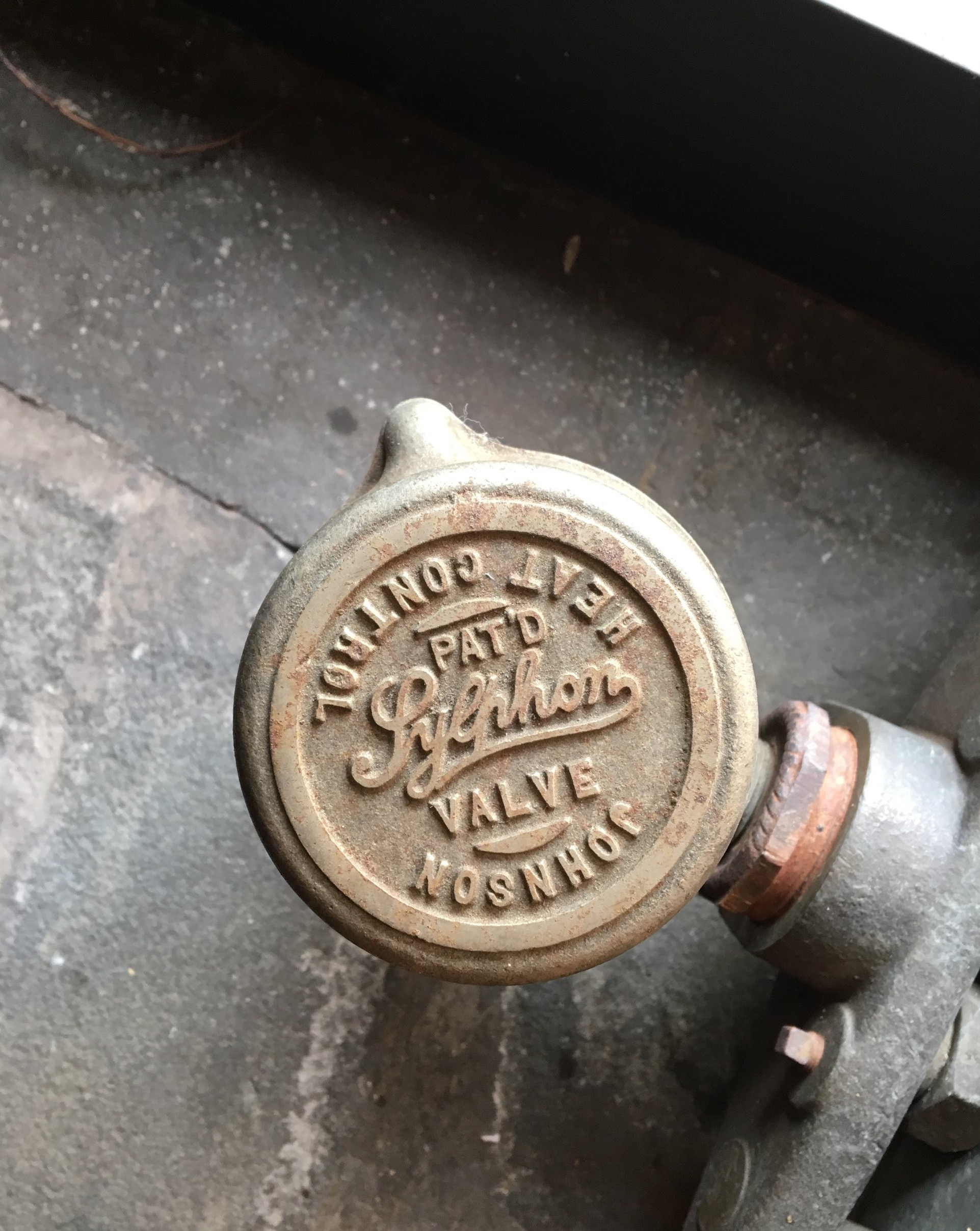
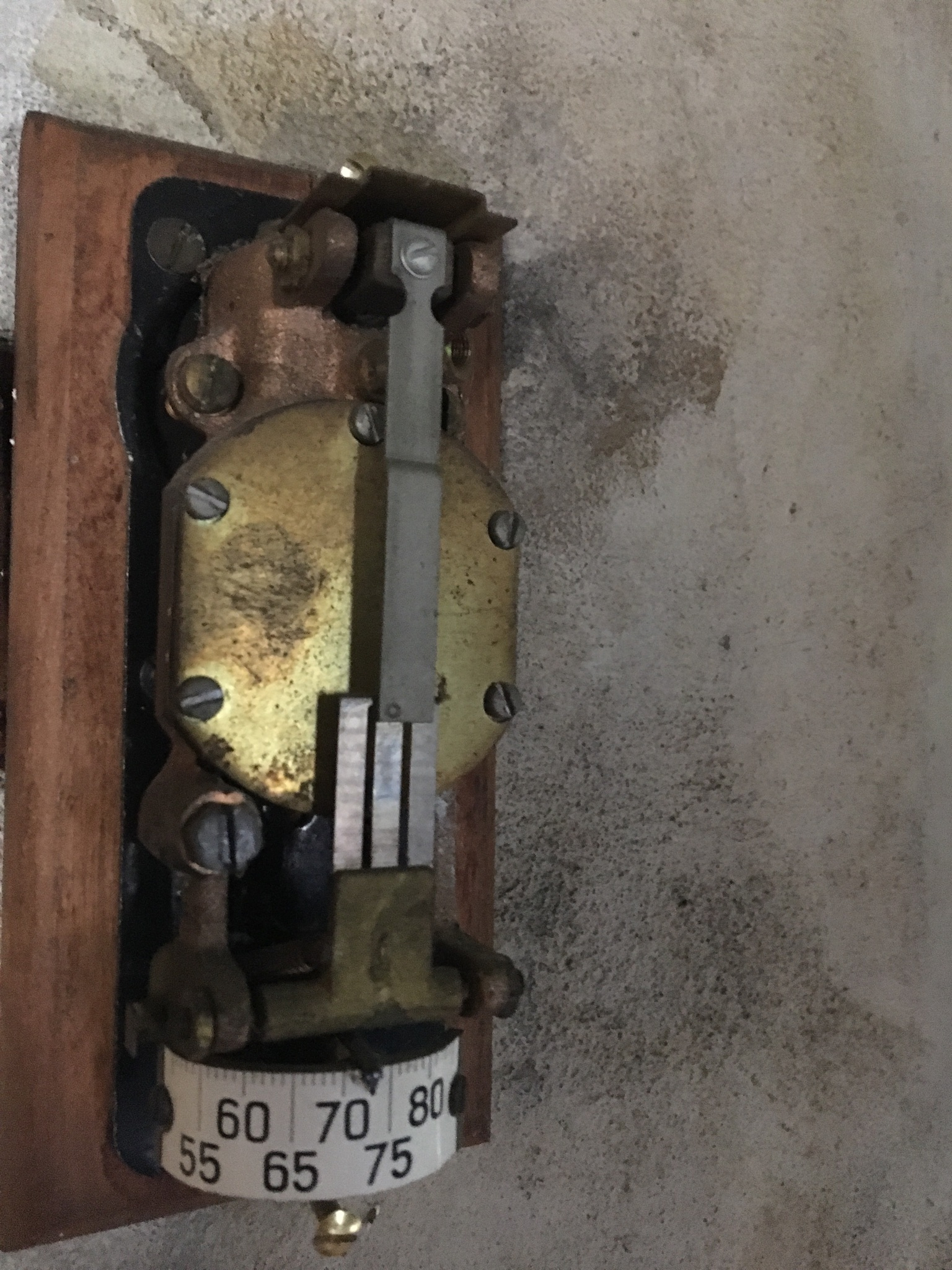
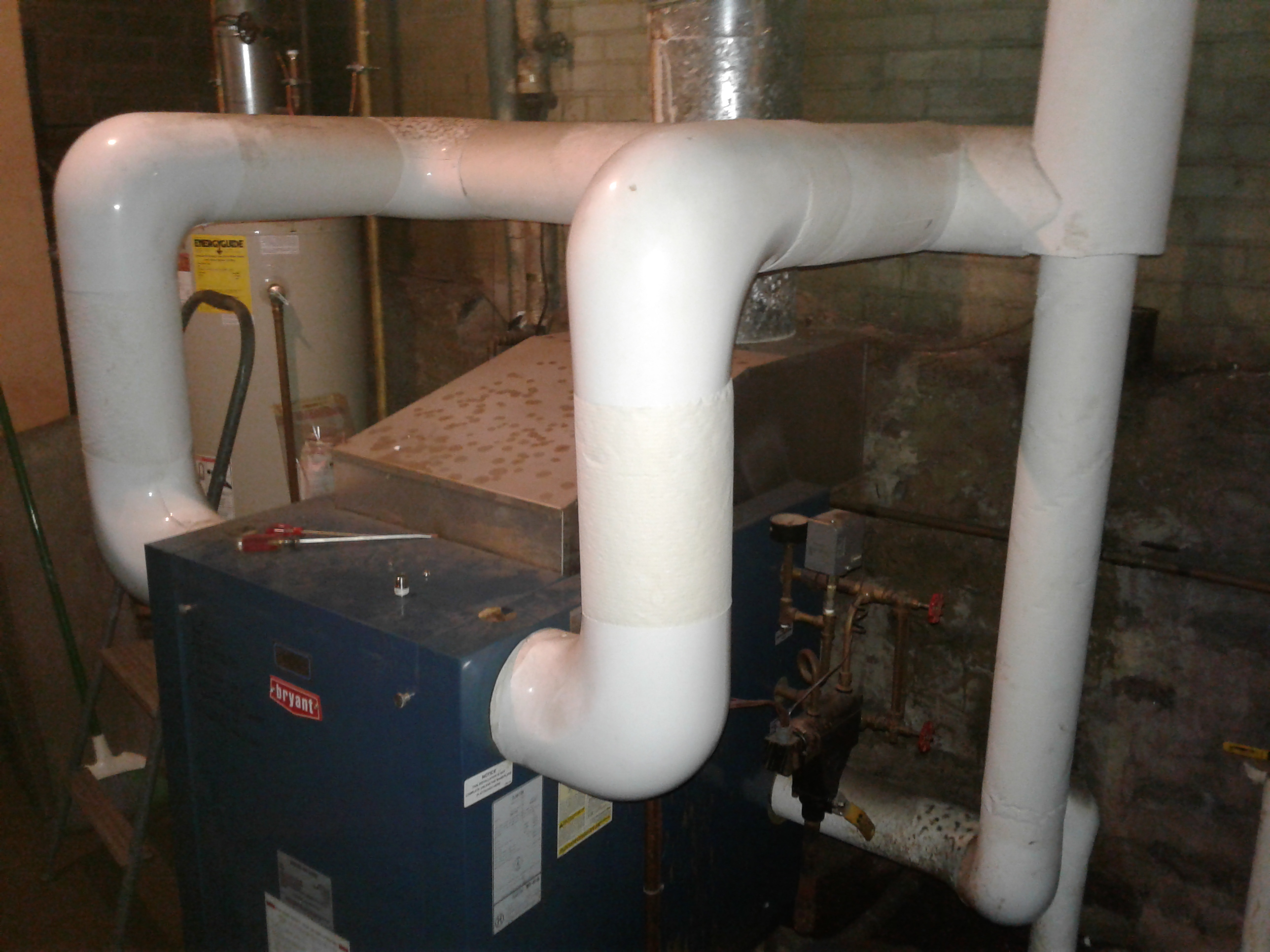
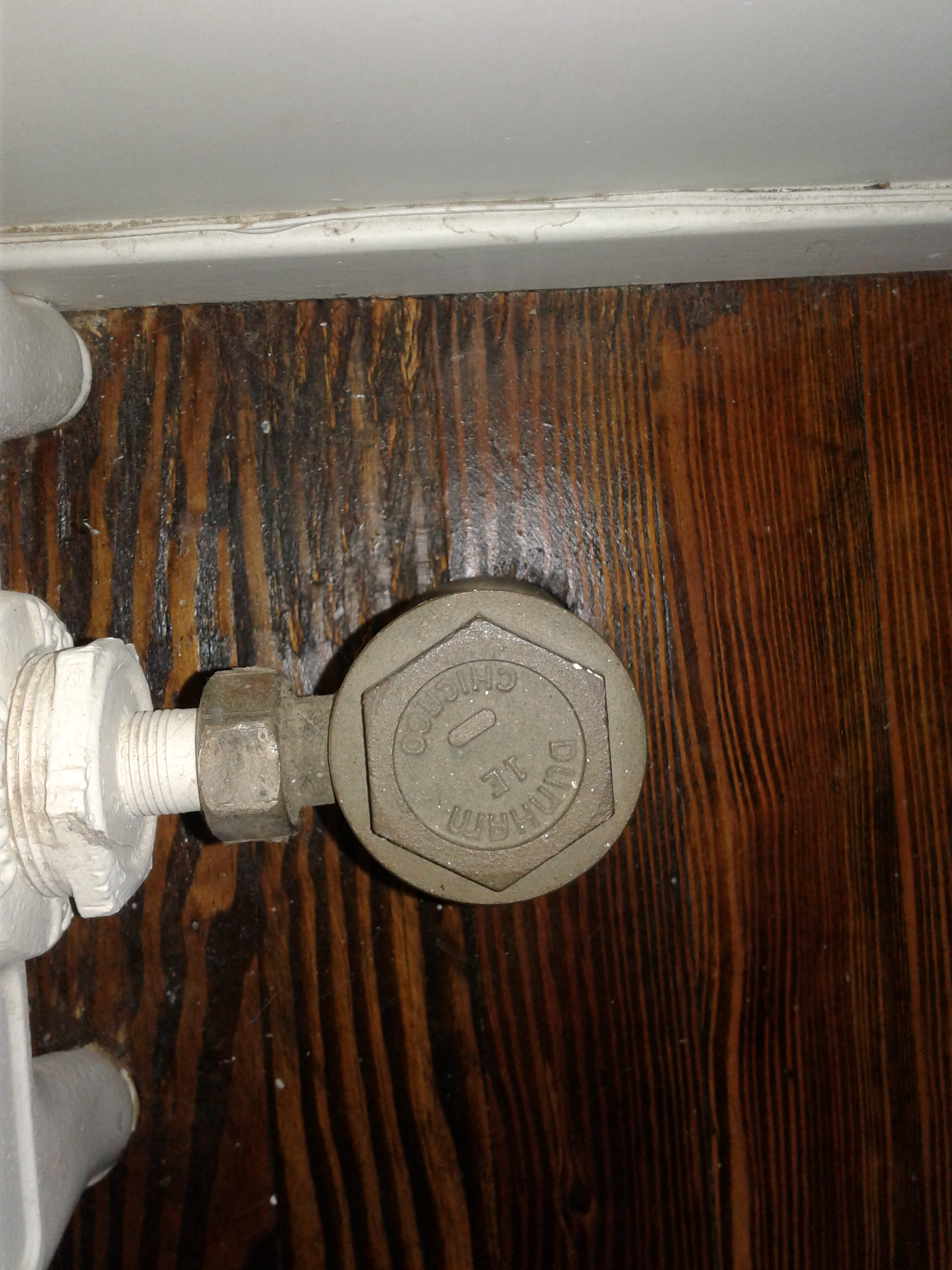
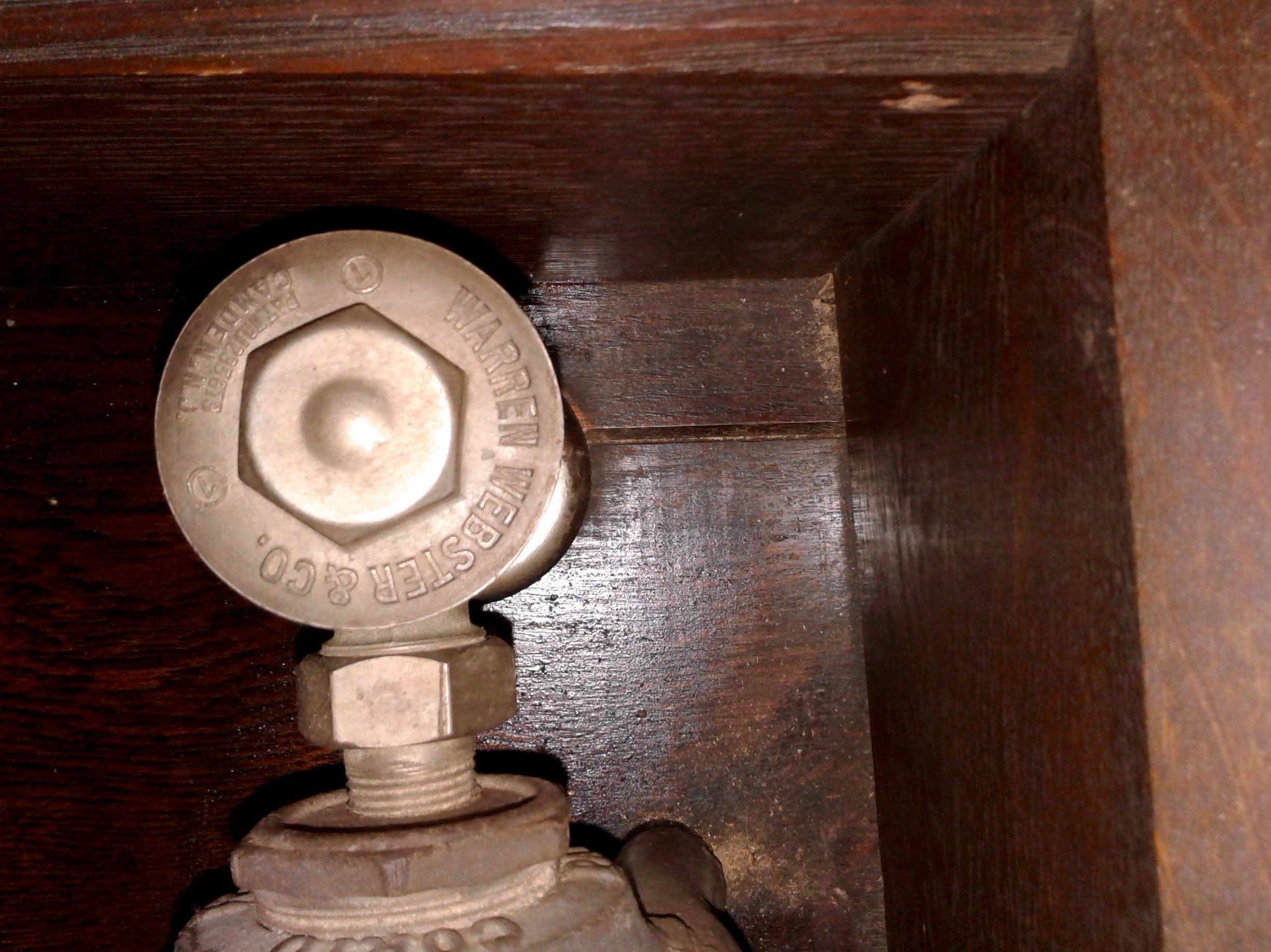
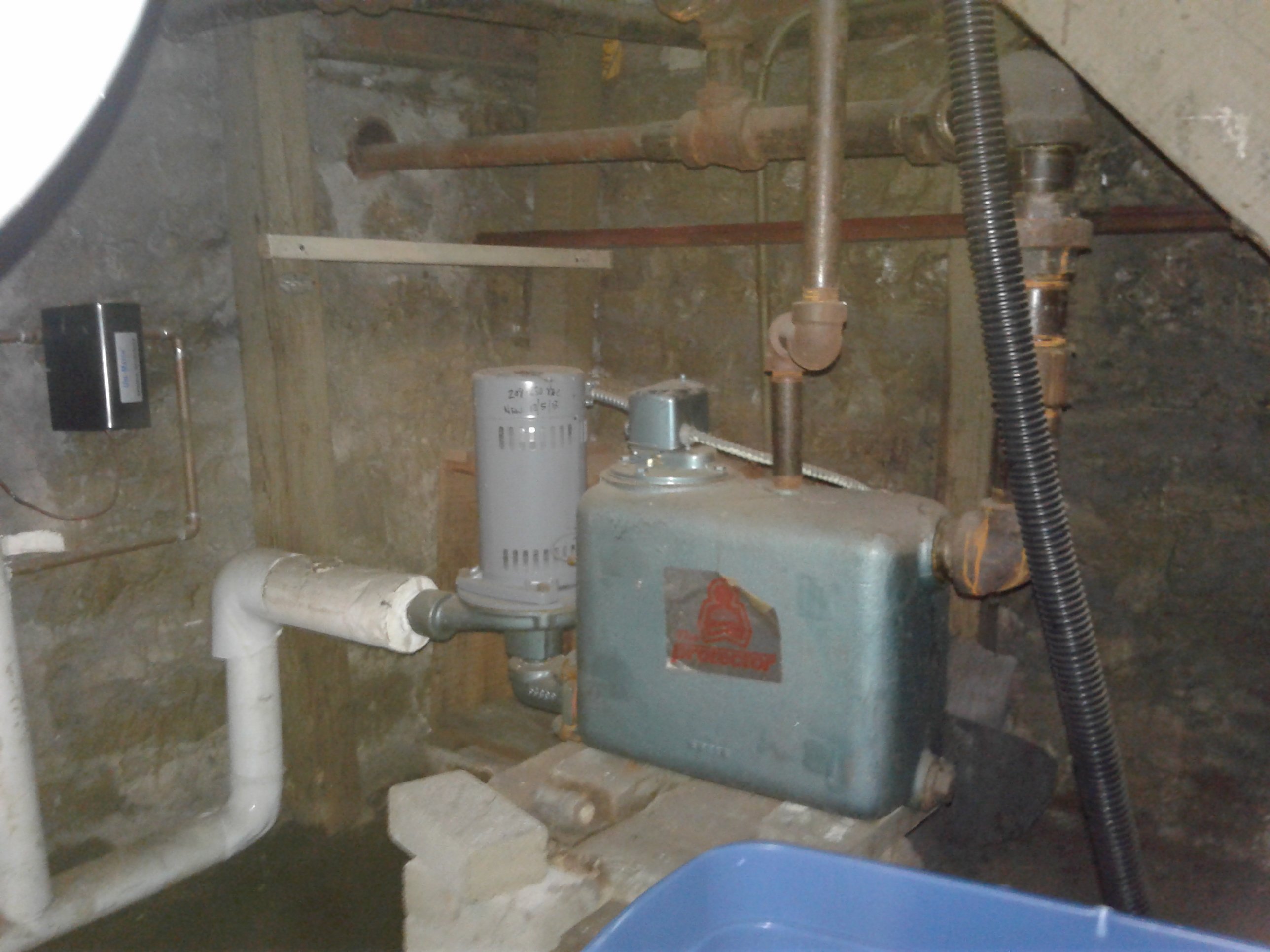
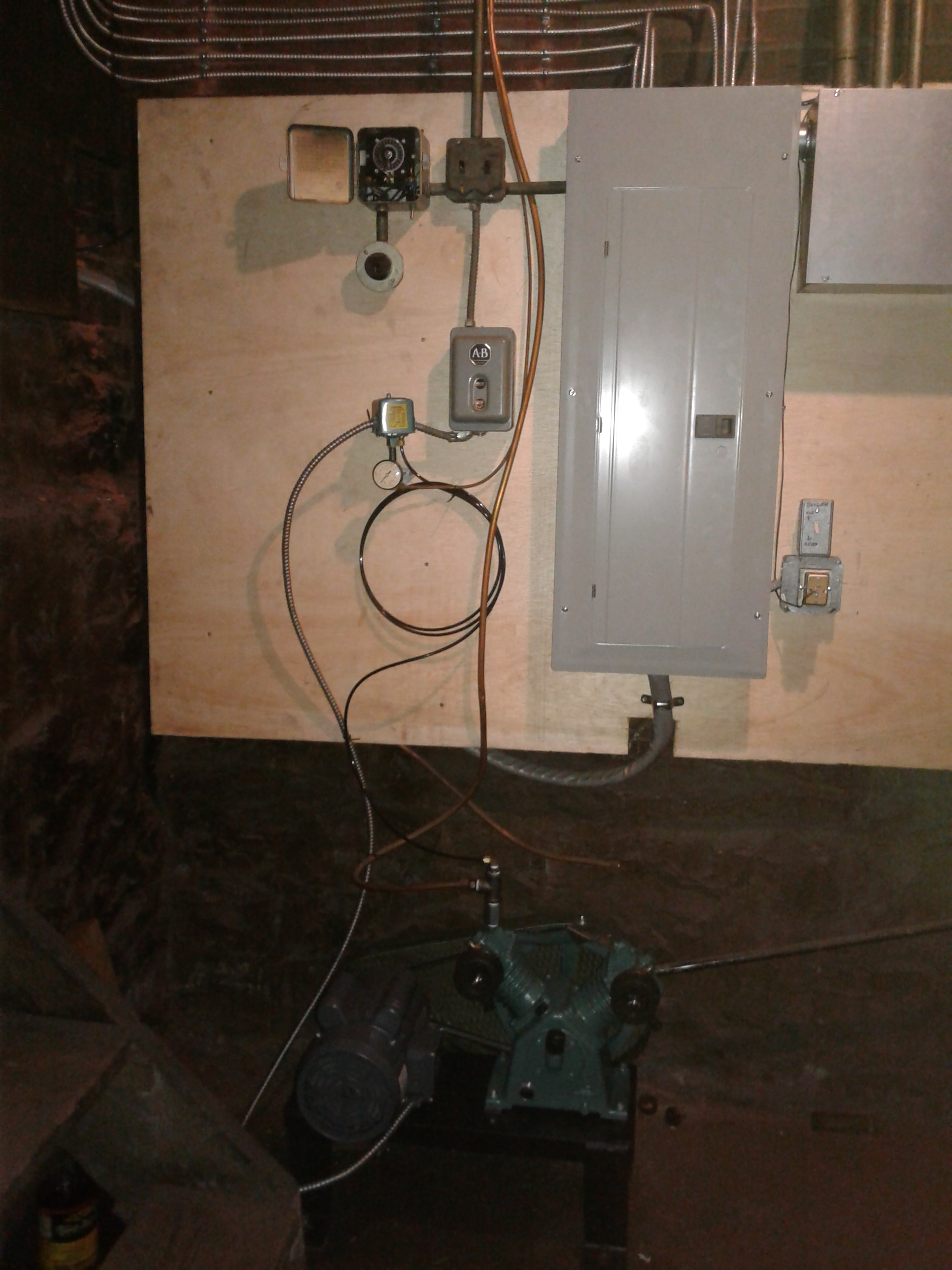
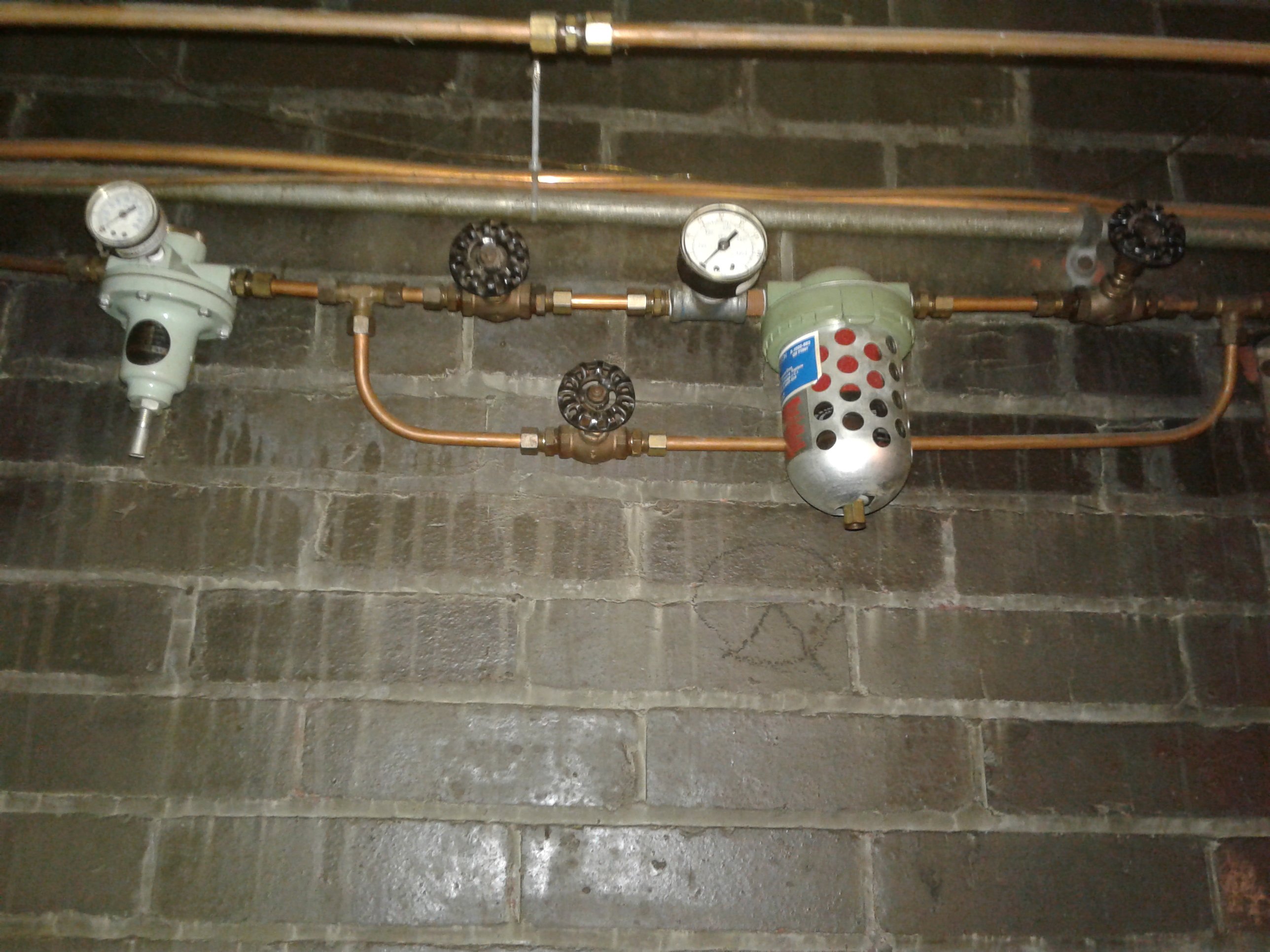
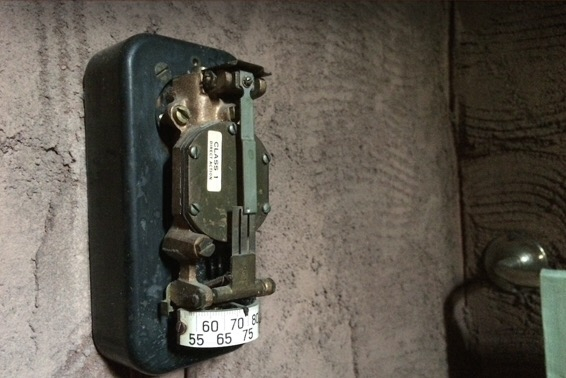
I went out on a call to start up a steam system for a new owner. I was able to get him heat but as you can see there are some system issues. (The pressuretrol needs to go) My question is there anyone out there familiar with this compressed air operating system. Most but not all of the rooms have thermostats on the walls controlling rad valves. The thermostats appear to be controlling the amount of pressure to the valve on the supply side based on room temperature.The rest of the rads are just standard 2 pipe with both Webster and Dunham 1E traps.
0
Comments
-
Search under "pneumatic controls"
Should be maybe 1/4" copper tubing between each tstat and steam control valve.
Many systems are "fail safe" in that without any air pressure the control valves would fully open.
Truly old Johnson tstats.....1940-50's??0 -
It was a high end system in it's day. Modulating control, possibly with centrally controlled night set back. There's plenty of this still in service, parts shouldn't be too hard to source (although $$$). You should be able to rehab it cheaper than "updating" it to modern controls, which will entail replacing the actuators or using solenoid valves to give on/off control.-1
-
What type of building/use is this?
What regulates the rads without tstats?0 -
The building is a residential mansion. There is a standard round Honeywell thermostat on the wall which cycles the boiler. There is nothing else controlling the rads other than a trap on the return side.0
-
With no air pressure does everything heat (actually overheat)?0
-
Yes, everything heats/ overheats. Rads that did not heat had their supply valves off. Once I opened the valves, those rads heated.0
-
If you apply about 18 PSI to the system and turn the tstats down then the supply valves should close.
There may be a small tap at tstat or valve to test the air pressure it is controlling to valve.
The only tstats I am familiar with are Powers (1960's). They will regulate the air pressure with room temp to modulate the steam valve very accurately. Just breathing on the sensor will raise the delivered air pressure turning down the flow.
All these components need clean dry air.
Your water separator in the picture looks original and might have given up long ago.
If much water has gotten into the air lines, then the tstats and valves may be locked up.
Air compressor looks fairly recent though. Probably water drain in bottom of tank. Oil level/change??
0 -
@JUGHNE Thank you so much for your input. The compressor is very recent but the old abandoned one is still connected to the piping with numerous small leaks. The tank is mounted on the wall just below the old compressor and motor. The valves on the left and right of the existing water separator are closed, there was nothing I could do to stop that from leaking. The bypass valve on the bottom is wide open. Before I started this post, I suggested to the owner to have the service man install a water separator/ filter at the outlet side of the new compressor. Debris from the new compressor is in the seat of the compressor relief valve preventing it from closing. Once he repairs or replaces his control, I will go back to repair the remaining leaks and check for or install a drain at the bottom of the tank. I have not checked to see what the pressure is at the thermostats or actuators but the compressor shuts off at 60PSIG. The existing controller is a Square D 9013FHG12M1X.
Just curious, is there any manual or literature out there on this system?0 -
Wow I have not seen those since I was young apprentice and had a full head of hair. The old Johnson Controls theremostats were used 15 Psi for the day pneumatic pressure and 20 Psig for the night pressure which would lower the temps by 10 degrees F. Those thermostats has a gauge port (see the slotted brass screw on the bottom left side of the thermostat) To calibrate the thermostat, you set them for the room temperature and test the outlet pressure on the branch line using a pressure gauge. It should read 7 1/2 pounds at room temperature. The adjustment screw in under the temperature reading of the thermostat. They were susceptable to water and can be replaced as well as the control valves on each rad. Good luck Thanks for the memories.Ray Wohlfarth
Boiler Lessons0 -
The air supply system is not rocket science....if you can figure out steam systems this should be a walk in the park.
IIWM, I would take care of the entire system if I had to service the controls. This would give you the advantage of being more familiar with the entire system.
For the old one I inherited, I looked in the Grainger book, they do a lot with air supplies. Good info in the book, don't know about the website.
Also, your air compressor looks to be designed for pneumatic controls. If you google that company they should have a lot of installation info. Relief valves usually have a pull ring on the top and fully opening it might blow out the junk, if not replace it. (just like a PRV, only it may open at plus 100PSI.
I added an air line filter and coalescing filter before the pressure regulator. These have clear sediment bowls with manual blow down drain valves.
The 60 PSI you see is feeding the pressure regulator which should put out a steady 18 or so.
If you can get the old compressor out of the piping system and just use storage tank that would eliminate some leaks and potential contamination. The cooler the air gets before going out to the system is better, the water drops out in the tank. (Initially I needed the coat hanger wire to unplug mine....nasty gunk)
Pneumatic systems can range from very simple to very complex.
You are looking at perhaps the simplest set up. Great learning experience. Very few want to learn about this. Somewhat like steam heat.....just tear it out and start over. But like steam it is usually repairable and you could perhaps carve out your own niche if there was more in the area.
National Energy Control Corp. necc-controls.com
handles parts. I have had the old brass Powers tstats rebuilt by them. Don't know about yours though.
You could call them 610-449-9800, Havertown PA
More pictures of the old AC/tank would be good.
0 -
I was just going to ask if the slotted screw on the left was for a gauge port. Thank you for your input @RayWohlfarth. Before I try doing anything at the thermostats and actuators I want to get past the numerous leaks. Now there's 2 that said this system operates at a lower pressure. At first I thought the contractor who installed the new compressor knew what he was working on but he's the one who set the pressure at 60lbs.0
-
I'll get more pictures when I go back. The gauge on the regulator at the wall also reads 60lbs. I did notice when the pressure gets to 20lbs you can hear a click at the old compressors pressure switch which is still connected. I did mention to the owner I would be disconnecting all connections to the old compressor.0
-
Put a gauge of your own on the outlet side somewhere. If the system itself, as opposed to the compressor outlet, is running at 60#, that's not too good. The pressure switch for the old compressor switching isn't surprising, as it should be tied in before the system regulator along with the new compressor.0
-
On the Powers tstats, the screw is recessed and when loosened you slip a hose over it for your gauge. You don't want to lose the screw.
Think of the air supply system as a pounds/ounces gas supply system with it's regulator.
You need that 60 PSI feeding your regulator that puts out the steady 15-18 PSI that feeds to the system. That is why there are permanently installed gauges before and after the regulator.
Ray mentioned the day/night system, 15 for day and 20 PSI for setback at night. That would require 2 separate regulators and a method to switch the system connection from one to the other.
Electric timer or manual like mine is. I didn't see any of that in your air system yet.0 -
There is a 24hr timer (top left of main panel) that is set to shut the compressor off between 8pm & 7am. The master BR is right above the compressor, I assume the previous owner had it turn off at night so they wouldn't hear it cycle while they sleep.0
-
Huh. Pneumatic heating valves generally (but not always!) fail to full open when air pressure is lost.
The air compressor can be relocated to anywhere convenient (garage, maybe?) as long as you can get an air line back to the regulator.0 -
Double D said that without air the system overheated....fail safe.
Owners may have turned the HW round tstat down to keep boiler off most of the over night time.
If all of the leaks were repaired and the storage pressure pushed higher, the AC would not cycle much.0 -
The attached garage is right next to the boiler room. Good idea. So which is it, are they open or closed when the air is off. I can say I wasn't able to run the compressor very long due to all of the major leaks which I took care of while the boiler was cycling off the wall thermostat. The owner came to the boiler room and mentioned all of the radiators were hot with the exception of a couple that had their manual valves off. (2 in the garage and one in a hallway)0
-
Most likely they open with out air pressure. Simply leave the AC off and empty and turn tstat up, if everything heats up hot they are "fail open". As Ratio said most generally that way.
Iso pads under the compressor and larger air inlet filters may quiet things down.0 -
With the air pressure down, turn on the boiler. If you get heat at most/all radiators they're normally open, pressure to 15# to close. If you can get air up, you might be able to watch a valve perform while you turn the stat above & below the room temp.
It sounds like you've effectively done this already.0 -
I haven't been able to check the operation of the actuators due to the issues with leaks but it will be the first thing I do once all the air leaks are fixed. System issues may have to be another thread.0
-
Keep in mind that all it takes is 15# of air ...or dry nitrogen... Depending on where the leaks are, you could separate the system from the compressor/filter/regulator & supply dry N2 via a carefully!!! adjusted regulator. IDK how long a bottle would last, but I'd imagine you could get some diags done while you're waiting on the air compressor to be repaired.0
-
I did keep track of the fittings that were leaking. I could start with those without having the compressor up and running. Also I would like to disconnect the old compressor from the system piping. That alone takes care of 9 leaks.0
-
If you could get that AC relief valve to seat, it is probably most of the lost air. Air leaks sound worse than they usually are.0
-
I soaped every fitting in the boiler room, most are tiny leaks but there is a large leak on the 5/8" copper connection entering the tank and I've had no luck stopping any of the 3 valve stems from leaking. There's even a tiny sand hole in the middle of new tee at the compressor outlet.0
-
Sounds like you've got a handle on things. Take it one step at a time, starting with the air supply. The old air compressor is not needed, but I didn't see an air tank in any of your pics? If that's the only tank in the system you'll have to repair it or replace it. You don't want the compressor trying to run without anywhere to put the air but the piping. Johnstone carries pneumatic parts, anyone that's strong in Honeywell should be able to source parts as well. After the leaks are fixed and you're working on correct operation of the controls, keep in mind that it's a live zero system—normal operating range is 3-15 lbs. Below that & you have a supply issue as everything should be "off" by the time you reach 3 lbs.-1
-
As @JUGHNE said you can easily figure this stuff out with a little work.
The only reason that this system is messed up is because they don't have anyone that knows how to work on pneumatics.
You can learn this stuff easily and have a good working system.
Check out National Energy Controls there in Philidelphia 1-800-227-9800
They have all the pneumatic controls, texbooks, 1 day pneumatic training classes etc. You can also get controls from Grainger.
You can run the boiler with the existing electric stat and fix up the pneumatics to prevent overheating.
In the old days they probably ran the boiler on pressure-1 -
-
Those sylphon actuators are normally open air pressure closes them . They are a very robust component as is most of the old pneumatics. If you need to have the thermostats serviced my I suggest Edgemont Precision Rebuilders, Inc. They service mine when needed and are familiar with those old Johnson controls. Unfortunately you will have a very hard time finding any valve parts for those Streamline globe valves. The Sylphon operators can likiely be soldered if the bellows inside fails. There is a gasket in there that can be copied.Miss Hall's School service mechanic, greenhouse manager,teacher and dog walker0
-
Thank you @Grallert for Edgemont Precision. That will be very helpful. I was able to take care of all of the leaks in the boiler room however the new compressor relief still leaks a little. The compressor installer just replaced it Monday. The system still has several leaks but at least the compressor stays off for 30min. I know I still have leaks that need to be addressed (you can hear air leaking from one of the thermostats) but is there someone who can give me an idea how often the compressor on this system needs to run assuming the system is leak free? There are 10 thermostats along with 10 actuators.0
-
For the system I maintain with comparable equipment, the compressor might run once an hour.
It is also dependent upon the pressure settings for the air compressor system, (before your pressure regulator).
The higher the cut out pressure and lower the cut in you will have less cycling. You just have to keep maybe 25 PSI as a minimum to feed your 18 psi system.0 -
Could I set the on at 25psi and the off at 60psi? Right now the range is on at 40 and off at 60.0
-
Also, he has the compressor running on 115volt. There's plenty of room in the panel. Wouldn't it be better to run it on 220volt at 4.8amps instead of 9.6amps using 115volt?0
-
Look for a nameplate on that tank. I wouldn't want to run it over it's maximum pressure rating at all due to its age & construction method; I don't know enough about that style to know how reliable they are.
Check the relief pressure of the safety valve. I don't buy two defective new ones in a row.
0 -
I assume you got the bottom tank drain opened and cleared.
You can look at the old pressure switch to see the max they ran it at; although it could have been fiddled with.
Ratio is right that that is a pretty old tank and higher pressure may be the death of it.
There should be a relief valve on the compressor and also one on the tank. The old compressor may have a check valve right at the tank and if so then the old AC relief valve will not see the tank pressure.
There is probably an "unloader" valve on the existing pressure switch; that opens relieves air pressure from the cylinder heads whenever it switches off at the end of cycle. It would give you just about 1-2 seconds of air escaping. If more or constant air from that then the check valve on the new AC may not be sealing. Or if leaking during running then the unloader valve is not completely closed.
Play with it and you will see how it works.
The intent is to not have the AC start under any head pressure.
I would have thought the AC guy would have noticed this if the case.
Obviously a leak on the high side of the system will induce more run time than your low side leaks.0 -
The unloader seems to be working fine, I may have jumped the gun on calling it failed. Where is the best place to install the relief valves and where can I get the ones I need?
I repaired every leak I could without changing fittings. 2 of them will need new fittings. None of the thermostats are leaking however 4 of the actuators are. For the time being I'm going to cap the feed lines to them until the owner decides what he wants to do as far as repairing or replacing. One of the leakers is partially
buried in floor tile inside of a convector.
All of the actuators work off the thermostats, even the ones that are leaking.
In case anyone is wondering, the fail safe works. When there's no air the valve is wide open.
I turned the boiler on for the new owner last night. When I arrived this morning he let me know it hammered all night. The boiler has been running on a pressuretrol for the last 17yrs. The pic shows the pressure it shuts off at. As soon as the pressure was almost to 1-1/2lbs, the system hammered like crazy. Today I installed a vaporstat, the system has been silent.
0 -
Ah a riveted air tank. Seen plenty of old riveted boilers including high pressure steam but never a riveted air compressor tank. That's old.
How old, I don't know but although they were welding before 1930 (welding got started about WWI and developed slowly until about 1930 then started taking off) I can't imagine a riveted air tank0 -
A little of both on that tank. Some rivets and some welding.0
Categories
- All Categories
- 86.2K THE MAIN WALL
- 3.1K A-C, Heat Pumps & Refrigeration
- 52 Biomass
- 422 Carbon Monoxide Awareness
- 89 Chimneys & Flues
- 2K Domestic Hot Water
- 5.3K Gas Heating
- 99 Geothermal
- 156 Indoor-Air Quality
- 3.4K Oil Heating
- 63 Pipe Deterioration
- 910 Plumbing
- 6K Radiant Heating
- 380 Solar
- 14.8K Strictly Steam
- 3.3K Thermostats and Controls
- 53 Water Quality
- 41 Industry Classes
- 47 Job Opportunities
- 17 Recall Announcements