Welcome! Here are the website rules, as well as some tips for using this forum.
Need to contact us? Visit https://heatinghelp.com/contact-us/.
Click here to Find a Contractor in your area.
Steam Pipe Corrosion

Dale_3
Member Posts: 58
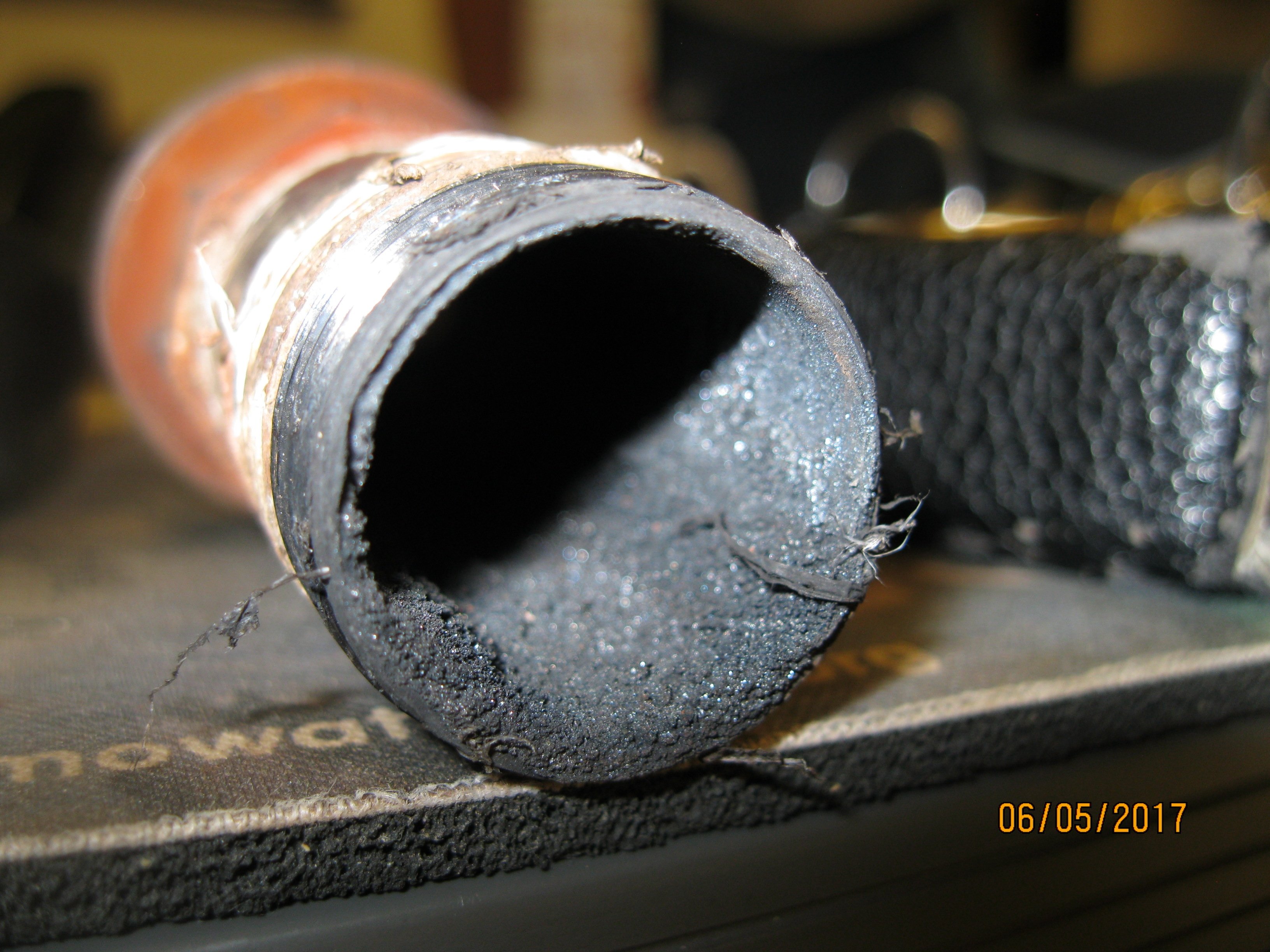
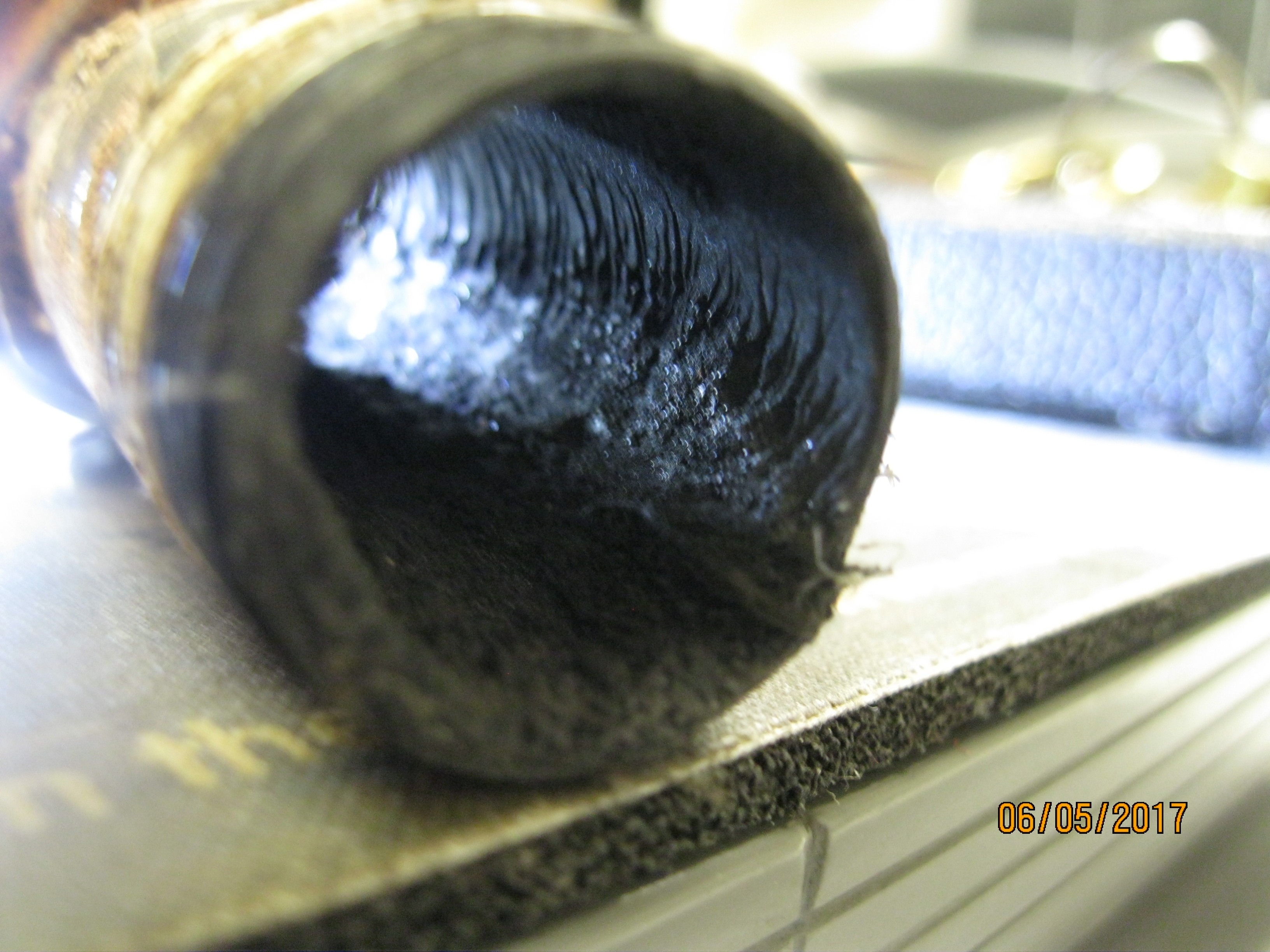
All - We have had severe pipe corrosion issues on a steam system over the last few years. I don't have all the chemical details but it is "monitored and treated". Would you say we need different monitoring and treating? Any thoughts or input is welcome. I've got to convince some people we have a problem and have yet to do so even though leaks have been continual issues. Do the weird markings inside the nipple mean anything to anyone? Thanks in advance.
0
Comments
-
Are these pictures of the wet return pipes? It is not unusual to have that kind of sledge build up over a few years, especially if the wet returns are rarely/never flushed out.I can't imagine you'd get that kind of build up on any steam carrying pipes.
Also, if these are, in fact wet returns and you are only replacing a section at a time, when it springs a leak, the other sections probably aren't far behind in terms of needing replacement, If these are relatively new pipes and they spring a leak, the water should be tested and a treatment based on that testing. The corrosive nature of the water (if that's what it is) will cause the boiler to rot through prematurely as well. Also be careful of storing chemicals, salts, bleach and other chemicals around the area of the boiler.0 -
If those lines are carrying dry steam -- or supposed to be -- you must have a terrific carryover problem. Dry steam just won't do that. On the other hand, if they are wet returns, they can sludge up and corrode -- but not, usually, as fast as you seem to suggest. What are you treating with, and why? What testing regime is being used to control the treatment? And is this a closed system or an open system?Br. Jamie, osb
Building superintendent/caretaker, 7200 sq. ft. historic house museum with dependencies in New England0 -
are you adding a lot of make-up water? Are you getting all the condensate back?0
-
This is a steam line and we add a lot of make up. We have a DA tank and everyone says it works but I really question how well it works given the amount of make up and the chemical dwell time with the water. I had them add a feed water meter a while back because no one could tell me how much we were making up or returning. We have a treatment company advising chemical treatment but I'm not real confident in their skills. I'm trying to convince the powers that be how big our problem is but since I don't have a PE at the end of my name I think I'm loosing the battle. "for now" Thanks again for all of the input.0
-
If those are steam carrying lines and not wet returns you have a major problem. Steam carrying lines for the sake of discussion shouldn't corrode...at all....ever. Wet returns can accumulate some sludge over time, but even the amount you are showing should take years...again on wet returns only. Steam lines should look virtually brand new after decades...even a century...if the system is operating properly.
How much make up water did the meter register in the past year? How big of a system are we talking about?0 -
Please tell us what chemicals they are using to treat this system. I can't imagine those are pictures of steam mains/lines. With that much crud in a steam main, I would think any and all vents would be clogged as well. Do the wet returns spring leaks too? Have you looked inside them to see how clogged they are? I'm having a hard time believing that steam can carry that much crud up into the mains like that. Can we also see pictures of the boiler and the piping above/around it?0
-
Is this a process steam system?You can have it good, fast or cheap. Pick two0
-
I would classify 90+% as process. I just found out the meter I asked to be installed had not yet been installed but as of a few hours ago it has.0
-
As I mentioned before, if those are steam lines as I think I understand, you have a real carryover problem. Dry steam -- regardless of how much feed water is involved -- should have nothing in it except ... steam.
Br. Jamie, osb
Building superintendent/caretaker, 7200 sq. ft. historic house museum with dependencies in New England0 -
Thanks for the input. I am now trying to become a carryover expertJamie Hall said:As I mentioned before, if those are steam lines as I think I understand, you have a real carryover problem. Dry steam -- regardless of how much feed water is involved -- should have nothing in it except ... steam.
Things are beginning to make sense.
0 -
One other comment I would like to through out there. If this is a carry over problem and it appears that the carryover is eating the iron pipe does (all debris appears to be magnetic and the pipe is thin) does that help in any way?0
-
I think you are making headway, @Dale , Two things to start looking at. First, what is the water treatment? It may not be helping any. Second, though, look very very carefully at all of your near boiler piping arrangements. It may even be necessary to put a really big drop header arrangement in -- in fact, what in the bad old days we'd have called a steam drum -- to separate any carryover from the boilers from the steam.Br. Jamie, osb
Building superintendent/caretaker, 7200 sq. ft. historic house museum with dependencies in New England0 -
Will try and get sight glass pics later. Here is an available pic of some of the DA tank piping.
Chemicals involved - Jaytech --- JT-4309, JT-4212, JT-4524 - Sorry but I don't know a lot of details yet on chemical levels and such. I'm being told the chemicals don't need to spend much time with the MU water in the DA tank to do their job.0 -
I think we need to see the steam distribution piping, to determine if its improper design and installation is contributing to excessive water carryover.
You say that 90% of the steam is used for process, so have you any idea how much makeup water is added per year?
What is the normal pressure of the system, and is there any venting?--NBC1 -
Normal operating pressure is 80 PSIG. Not sure I understand your venting question. Almost all of the 12# steam goes to humidification and the higher pressure stuff goes to cage washers. For reference, this is a 96 BHP Bryan flex tube boiler. Steam output is rated at 3299LBS/HR and I was told the DA needed 1066PPH. Working on finding recent MU quantities.0
-
I'm not really seeing any corrosion in the pictures - only a sludge deposit of some kind. If they are return lines, age and type of system have a lot to do with what might be in them.
Process steam can have lots of problems depending on what is being heated. Heating chemical tanks makes for the possibility of chemicals from the tanks making their way into the steam system through pin holes in the heating coils. This possibility obviously increases as the system ages. Heating acids as I do is something that needs to be monitored carefully as acid obviously can destroy boiler tubes quickly.
I run a 200Hp 12psi process steam system. The boiler is triple pass horizontal tube. I have had only 2 tubes fail in the 20 years I have run it so most of the tubes (I guess there are 30 or so) are original. The boiler itself is 45 years old. I don't meter it but there is significant makeup water daily (guessing 5-10 gallons per day). I meter in a chemical treatment with a pump which runs whenever the condensate return pump does. If anything I end up putting in more chemical than is required(the supplier doesn't mind that and neither apparently does the boiler). The chemical supplier samples the condensate once a month and gives me a report. I also run a water softener on the feed water line(per their instructions). The chemical supplier monitors: TDS, Hardness(CaCo3), Alkalinity, Sulfite(SO3), and Hydrate (OH). They don't check chlorides. I have never questioned their approach for to me the results speak for themselves. I just stay with their program. I can't say exactly what the chemical is as they regard it a proprietary brew. This is their business and I suspect I am not their only happy customer.1926 1000EDR Mouat 2 pipe vapor system,1957 Bryant Boiler 463,000 BTU input, Natural vacuum operation with single solenoid vent, Custom PLC control0 -
In one of the pictures, the inner surface of the pipe seems to have been etched above the layer of sludge.
I wonder if the continual addition of chemicals is causing an ongoing buildup of precipitate in the boiler, which with bad piping is blasted around the pipes. With bad venting, the boiled off oxygen, and carbonic acid can then do a number on the metals in the system.
There are other ways of handling the fresh water oxygen problem without, or with less chemicals.--NBC0 -
What about the velocity? Are there issues with steam as there is with hydronic piping at high flow conditions? It does look like erosion from scouring of the metal?Bob "hot rod" Rohr
trainer for Caleffi NA
Living the hydronic dream0 -
How about a simple sketch of the system which points out exactly where the pictured pipes are located?1926 1000EDR Mouat 2 pipe vapor system,1957 Bryant Boiler 463,000 BTU input, Natural vacuum operation with single solenoid vent, Custom PLC control0
-
A drawing. I don't have specifics right now but I hope this gives someone something to chew on. Thanks again. Dale
0 -
That is NOT the way to pipe steam boilers. Also, adding too much chemicals can cause foaming and carryover with the steam. Bryan boilers do not like to have too much chemicals as the tubes tend to block at the back of the boiler. Here is the^proper way to pipe two boilers:
bryanboilers.com/pdfs/EI-2/Pipe/Form_2275.pdf
0 -
Here is an example of a Bryan tube with too much chemicals. The chemicals would carryover and block the clean steam filters for the pasturisation process every week.
0 -
My boiler is fire tube so I know nothing about this type.Henry said:Here is an example of a Bryan tube with too much chemicals. The chemicals would carryover and block the clean steam filters for the pasturisation process every week.
Looks to me like it would take a crazy amount of solids in the water to do this. I see no evidence of any solids in any of my lines supply or return.
@Henry once a system was filled with this stuff how would you ever clean it out?1926 1000EDR Mouat 2 pipe vapor system,1957 Bryant Boiler 463,000 BTU input, Natural vacuum operation with single solenoid vent, Custom PLC control0 -
I have had some overenthusiastic chemical conditions. Normally, we drain the boiler, perform a wash and flush several times. It takes a whole day. They don't realise it much on heating boilers. They will usually spot on production boilers. Here is an example of a heating boiler where there is no need for any chemicals.
0 -
I get that you can clean the boiler. What if this stuff is all throughout the rest of the system?Henry said:I have had some overenthusiastic chemical conditions. Normally, we drain the boiler, perform a wash and flush several times. It takes a whole day. They don't realise it much on heating boilers. They will usually spot on production boilers. Here is an example of a heating boiler where there is no need for any chemicals.
1926 1000EDR Mouat 2 pipe vapor system,1957 Bryant Boiler 463,000 BTU input, Natural vacuum operation with single solenoid vent, Custom PLC control0 -
In a heating system, it usualy solidifies in the pipes as the steam velocity is low. In an industrial use where the velocity is much higher, it ends up after the control valves, Y strainers, steam traps or in the actual production.0
-
We replaced the boiler with a Smith. Notice the drop headder and two blowdowns.
0 -
I finally got some time to do further investigation. We have put about 4300 gallons of MU water in the system in about 9 days. After looking into things further I would say we are bringing back very little condensate. Some pics and chemical info.
0 -
Chemical data
0 -
Sulfite levels way over desired range. I can't really read the comment about that. Sulfite levels in my boiler always about 30. I really don't know what the effect of a high sulfite level would be. TDS looks reasonable.1926 1000EDR Mouat 2 pipe vapor system,1957 Bryant Boiler 463,000 BTU input, Natural vacuum operation with single solenoid vent, Custom PLC control0
-
What changed between April and May? Sulfites level jumped then. Should be in 50 ppm range. Also what psi is this running at?0
-
Not sure why the jump but am checking. We are running at about 80 psi.0
-
Above normal levels of sulfites will cause foaming.0
-
Sulfites in a heating boiler but the boiler was damaged by an incorrect piping setup that pulled the sections apart thus steam cuting the faces.
0 -
Let me guess- the header was welded?All Steamed Up, Inc.
Towson, MD, USA
Steam, Vapor & Hot-Water Heating Specialists
Oil & Gas Burner Service
Consulting0 -
I read in some paper that at ~490+*F sulfites will become corrosive. Let me see if I can dig it up... Ok, here it is:O. Sulfite Degradation
At temperatures as low as 490° F, sulfites begin to form corrosive gases. The extent reached is a function of boiler pressure and sulfite concentration, and is reflected in reduced pH values. The gases leave the boiler with the steam and the resulting acid condensate, unless neutralized, attacks turbine blades and other sections of the system.
Substantial generation of corrosive gases does not usually begin until 535° F but the range between desirable magnetite formation (428°F) and the start of degradation (490° F) is relatively narrow. In order to avoid excessive quantities of these gases, sulfite residuals should be carefully controlled.
Not sure if this applies - temps in the firebox and the boiler sections may as well be above the 490*F. This is above my level of knowledge. Someone else might chime in... fwiw.1 -
On all large jobs 3inch and over, it is all welded with swing joints as per manufacturer. This one had no swing joints. The three outlets went into a straigh pipe. Everytime it started up, it would pull the boiler apart. They changed the gaskets 3 times. It ended costing a new boiler and 150 feet S/S liner. BI & I inspected every year and saw nothing wrong with the install. Insurance would not pay saying it was corrosion. We won last year against the insurance company.0
Categories
- All Categories
- 86.8K THE MAIN WALL
- 3.1K A-C, Heat Pumps & Refrigeration
- 56 Biomass
- 425 Carbon Monoxide Awareness
- 108 Chimneys & Flues
- 2K Domestic Hot Water
- 5.6K Gas Heating
- 105 Geothermal
- 160 Indoor-Air Quality
- 3.6K Oil Heating
- 69 Pipe Deterioration
- 956 Plumbing
- 6.3K Radiant Heating
- 385 Solar
- 15.3K Strictly Steam
- 3.4K Thermostats and Controls
- 54 Water Quality
- 43 Industry Classes
- 47 Job Opportunities
- 18 Recall Announcements