Welcome! Here are the website rules, as well as some tips for using this forum.
Need to contact us? Visit https://heatinghelp.com/contact-us/.
Click here to Find a Contractor in your area.
Converting two pipe steam system into mechanical vacuum system

AMservices
Member Posts: 611
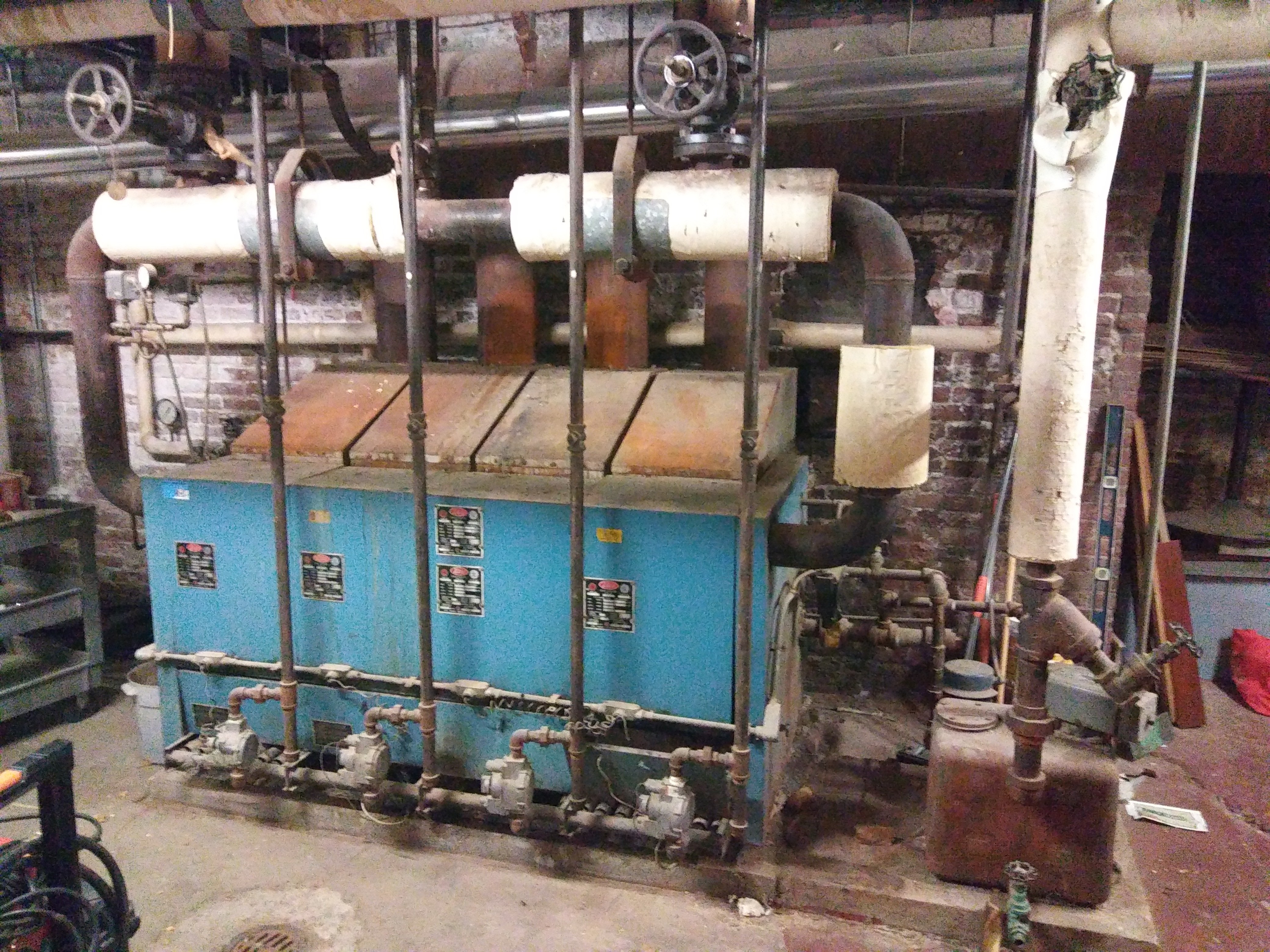
This week I'm going to be replacing a boiler in a commercial property that has cut the system size down by 80% from what it was when the current boiler was installed.
The boiler that's there now was once a 1.6 million btu boiler, (4) 400000 BTU Utica boilers pinned together. As of now only 1 of the 4 boilers is working.
It use to serve the entire 5 story building, but now only heats (5)recess fan coil's, (6) 1-1/4" fin tube baseboard heaters and 2 air handlers with steam coils. The building went through major renovations Back in the early 90's,
When they cut the steam heat out of the top 4 floors to give the new office space A.C., they left the boiler to heat the stairwells, common areas and the restaurant that was not willing to pay to replace their heating equipment.
So now it's my job to make what's left of this system work right.
I could wright a long thread just talking about everything that's wrong with the system, but that would be a wast of time because its all getting replaced.
I'm going to install a EG-75 to cover the 900 EDR system size I calculated.
I want to stage the burner because there are motorized zone valves on the 2 air handlers and TRV's on all the baseboard heaters. With the zone valves closed, it reduces my EDR by 30%.
If I had more room in the budget, I would install 2 boilers and 4 stages.
You can't always get what you want.
What would be a good 2 stage gas valve for this boiler?
I'm planning on using a condensate pump to put the water back in the boiler. I want to use a boiler feed pump, only the smallest one I can find comes with a 50 gallon storage tank.
I think that's to big seeing how the EG-75 only holds 17 gallons in the block and the smallest condensate pump I could get has a 6 gallon tank. If the boiler is burning 300,000 BTU'S, it would be losing .60 gpm. To size a condensate pump tank, it's supposed to be 3 times the condensing rate of the boiler. The 6 gallon tank is oversized. I would much rather use a boiler feed pump to have the communication between the boiler and the pump. The 50 gallon tank would be cooling the condensate and dumping cold water into my boiler every time it came on.
This is my first pumped return so I'm unsure of all my options.
Are there smaller boiler feed systems that I'm not finding?
I'm making this into a mechanical vacuum system, so I know ill need a flow check and water seal on the condensate tank's open air vent. Also a vacuum equalizer between the supply and return to ensure that the vacuum level on the supply side is never greater than the vacuum in the return piping.
I'm going to replace the steam traps on all the radiators and the F&T'S on the 2 air handlers.
Building management told me they've never been serviced.
Currently there are (11) 1/2" sarco B25 steam traps and(4) sarco #15 F&T.
Are there better traps that I sould use in a vacuum system?
At the end of the steam mains they used #15 F&T'S. Look like they cut out loop seals and cheaply welded the traps in. Other then saving space, is there a benefit of using a F&T rather then a loop seal?
For a temperature control I'm going to be using a tekmar 279. system serves so many random places in the building. it's difficult to choose where I should place the indoor temperature sensor. I called tekmar text support to ask how I can wire the control to sense several readings. They told me by daisy chaining the resistors the control will average them out.
Not sure if maintaining an average in this manner is a good idea. I think that would make one area averagely overheated and another area averagely under heated. Thoughts?
As for the system sensors, my question for tekmar was " in a steam system where the steam mains will travel hundreds of feet in opposite directions, how do I decide which end of Main line gets the sensor? Do I put a sensor at the end of every Main?". He said nobody's ever asked them that before and it's never come up and any meeting he's attended. He did say that the control wood average those temperatures as well and I could adjust the parameters until I was happy with the results.
I figured I was going to be doing that anyways.
Here I think daisy chaining sensors to see an average won't hurt. If the sensors are placed on the return line of the farthest radiators and its purpose is to sense return condensate temperatures, then if one gets hot before the other the cold sensor should keep the control in check. Again thoughts, experience?
Thank you
A&M Services, bring steam back
0
Comments
-
I'm not the guy to answer most of your questions, only those about pumps.
Kind of confused about your use of condensate pumps, and boiler feed pumps. If you can have all of the returns come back by gravity to the boiler feed receiver, then you don't need a condensate pump too.
As far as sizing boiler feed pumps go, it's best to size based on the boiler's steaming capacity and time. I recommend sizing for 20 minutes steaming time, although you may be able to get by with as little as 10 minutes.
If you talk to the right people, you can get just about any size boiler feed system you like.
You don't say anything about vacuum pumps, only in your title. If you want a vacuum return, it is possible to get an all in one vacuum boiler feed unit, but a separate vacuum return pump set, feeding into a vented boiler feed tank is, IMO, an easier proposition to deal with in the long run. Easier to set up controls, and easier to service when needed.
Where are you located?Dennis Pataki. Former Service Manager and Heating Pump Product Manager for Nash Engineering Company. Phone: 1-888 853 9963
Website: www.nashjenningspumps.com
The first step in solving any problem is TO IDENTIFY THE PROBLEM.0 -
use a condensate pump as a boiler feed pump with a pump control mounted on the boiler. leave the float mounted switch on the condensate pump as a low water cut off for the pump.
pipe your make up water to the condensate pump.
the sequence would be like this:
On the boiler install a M/M #150 pump control.
as the water level drops the first switch (pump control switch) starts the condensate pump. The condensate pump will only run if there is sufficient water in the condensate tank as proven by the float control switch provided in the condensate pump. (both switches wired in series with the pump)
If the water level continues to drop
The second switch in the #150 pump control is (normally the low water cut off switch with an alarm contact) used to power a solenoid valve for the make-up water which is piped to the condensate tank. This will put water in the tank mixed with the condensate.
you would use the alarm contact to power the solenoid valve.1 -
WRT the Tekmar sensors, you want the steam-established (a.k.a. condensate) sensor as far away from the boiler as you can get it. At the very least, put it at the end of the longest main. The top of the furthest riser, right where it goes into a radiator, would be better. We've used both placements.
In order to avoid overheating, you want the sensor to tell the 279 that the steam is about to enter the radiator. The reason is, the sensor activation tells the 279 to check the outdoor temperature and decide how much longer the boiler needs to run to heat the building to the desired temperature. The 279 then counts down the calculated time and stops the burner. In milder weather, this will only heat the radiators part way, as it should.
It's a good idea to insulate over the sensor. Otherwise, the pipe and sensor may cool down too fast and start the next heating cycle too soon. This will make the building overheat.
If the building still overheats, you can increase the "lockout differential" so the sensor must cool down to a lower temperature before the next cycle will start. This setting is in the 279's menu.
The indoor sensor is there to prevent overheating- it's not a thermostat in the usual sense. I don't believe any of our buildings have indoor sensors- if the 279 is set up properly, the building will not overheat. If you're going to use one, it should be in a common area rather than in a tenant space.All Steamed Up, Inc.
Towson, MD, USA
Steam, Vapor & Hot-Water Heating Specialists
Oil & Gas Burner Service
Consulting0 -
EG75 does not have 1" tappings required for the typical McDonnel Miller float type lwco/boiler feed controls (#150, 157, etc). However, if you decide to go up one boiler size to a EGH85 they do come with the larger 1" control tappings.
As far as a two stage gas valve, I don't think W/M offers them in atmospheric boilers other than the LGB series. The LGB series does not offer two stage firing unless you go to at least a six section boiler. I suppose you could install an aftermarket gas valve, I'm not sure if this is a good idea with just one pilot assembly. I'm not certain, but I believe most atmospheric gas fired boilers with two stage firing have two pilot assemblies and/or two sensors.0 -
We repair a lot of Sarco traps with our cage units as we seal ours under vacuum, they function the same from vacuum to 25 PSIG. So no need to replace the entire trap, just more work. Pop off the cover, remove the various parts in there and drop in a cage unit. Screw on cover. Takes 2 minutes.
For the F&T same deal. Just repair with a face plate. Ours come with same cage unit element that works from vacuum to 25 PSIG.
For vacuum systems you want a balanced pressure thermostatic element. If you just get a regular it won't work as well. Depending on the level of vacuum of course.Peter Owens
SteamIQ0 -
> @EBEBRATT-Ed said:
> use a condensate pump as a boiler feed pump with a pump control mounted on the boiler. leave the float mounted switch on the condensate pump as a low water cut off for the pump.
>
> pipe your make up water to the condensate pump.
>
> the sequence would be like this:
>
> On the boiler install a M/M #150 pump control.
> as the water level drops the first switch (pump control switch) starts the condensate pump. The condensate pump will only run if there is sufficient water in the condensate tank as proven by the float control switch provided in the condensate pump. (both switches wired in series with the pump)
>
> If the water level continues to drop
>
> The second switch in the #150 pump control is (normally the low water cut off switch with an alarm contact) used to power a solenoid valve for the make-up water which is piped to the condensate tank. This will put water in the tank mixed with the condensate.
>
> you would use the alarm contact to power the solenoid valve.
Thank you. That's what I was thinking.
Didn't think of using the float to activate the auto feed. I was just going to use it as a safety to break power to the pump until water returned from the system.
@Pumpguy
Jobs in Boston
I work with @izhadano, using his concept and the same vac pump he uses. Its a 4 CFM, oil free vacuum pump.
@Steamhead
Much simpler then I was making it.
I have a condition called "engineering-itis"
It flares up when I'm being challenged by things I've only read about.
@ScottSecor
In this system, with motorized valves and TRV's all over the place, the system size can be different from time to time. One room is a daily rental space. The restaurant has 2 air handlers, one with a 5'x2' surface and another with a 30"x20" surface, both have motorized valves that when closed reduce my system size by half.
Staging the boiler by letting the burner drop down 40% after 4 oz, then let the remaining 60% maintain and or build pressure to 8-12 oz before cutting out. If the demand is there the system will stay in high fire. From what the building manager told me, the restaurant air handlers almost never call for heat. The Heat pours out of the kitchen and when the restaurant is full the body heat raises the thermostat and the AC needs to kick on. If I can't stage the burner then the boiler will be short cycling 75% of the heating season at least.
Why is it okay to stage one steam boiler but not another?
@Sailah
I was hoping to hear from you.
I tried opening a couple of steam traps yesterday. The Caps wouldn't budge. I had it figured into the job cost to be replacing all of the traps and bodies. Me and my helper had them all removed within two hours.
Where do I go to buy your traps?
Igor wants me to try running the system without traps, so for my first test in going to leave the cartridges out.
The idea is if steam is always moving through the system as vapor being pulled by the vacuum and the vacuum level is equal throughout the system, the steam will favor the places that it can condense quicker, in other words where it's coldest.
I'm not promising any miracles on this one.
In a home with a radiator that I can always control the steam flow through that radiator with an orifice, in order to prevent short cycling back to the pump, that's a different story.
I have more control when I can arrange my own vacuum line system.
For the first test I will attempt running the system with everything wide open, no steam traps and if the pump short Cycles before everything is hot. Ill put the traps in.
But now if I have F&T'S at the ends of the steam mains and steam in the return, it's going to wreck the Trap element. That's way I ask if a water seal is any less affective then a F&T?
Thanks to everyone.
Big help0 -
You can purchase through any of my distributors in NE. Around Boston area your best bet is Met Pipe or FW Webb.
I didn't know you've already pulled the traps out.
I don't understand the statement you made so unsure how to advise.
But now if I have F&T'S at the ends of the steam mains and steam in the return, it's going to wreck the Trap element. That's way I ask if a water seal is any less affective then a F&T?
An F&T is essentially a water seal for the float mechanism. The air vent simply seals off when saturated steam temps have reach it. Therefore the only way anything can bypass an F&T trap is condensate raises the float which allows the condensate to drain through the (water sealed) orifice until the float drops and seals it off.
Sorry if I'm not understanding you I've been varnishing my boat and maybe sniffed a little too much paint fumes lolPeter Owens
SteamIQ0 -
I'm embarrassed to ask but, what model and brand traps do you make that would fit best where I took the Sarco traps out?
Igor doesn't want me to use steam traps at the radiators. I could have live steam in the returns.
If the float in water seal in the Trap is enough to protect the element, no worries.
I'll need replacements for the F&T'S as well.0 -
Why is it okay to stage one steam boiler but not another?
It's been a few years since I actually checked the input of a two stage W/M LGB, but I seem to recall the low fire rate was roughly 70% of the high fire rate. Even if you size the boiler tight as you mentioned above with a EG75, I think you will still be grossly over-fired most of the heating season due to the multiple zones. Imagine when just one zone is calling and roughly 210,000 BTU is firing, I suspect there will be water line issues and a lot of short cycling.
I was mistaken about the dual pilots on W/M LGB steam boilers, it's an insurance requirement for boilers over a certain BTU input. You could certainly add a second reverse acting pressure control and replace the factory supplied gas valve with a two stage gas valve. We have not done it (yet) due to insurance reasons and added cost, however I agree it would be great feature.0 -
@Sailah
Barnes and Jones, got it, wasn't thinking.
Your the guy with the Big Mouth. I mean.... Well you know what I mean.
Probably tired of that joke.
Ill be using your traps and I'm working with F.W. Webb.
The F&T are better then a loop seal because it will vent the mains and air won't vent through a water trap.
A Loop seal is better then a F&T because it has no moving to fail and easier to service. That is if the installer puts a drain at the bottom.
Think ill just use the F&T.0 -
What's the water volume of the condensate tank?
Just a heads up, if the boilers steam off all the available feed water before condensate returns, you will take on make up water from city supply, which will then cause overfilling when the boiler shuts down.
Should you find you need more water storage capacity, you can add another tank, piped in parallel with top and bottom balance pipes. Just be sure the extra tank is no taller than the existing one.Dennis Pataki. Former Service Manager and Heating Pump Product Manager for Nash Engineering Company. Phone: 1-888 853 9963
Website: www.nashjenningspumps.com
The first step in solving any problem is TO IDENTIFY THE PROBLEM.0 -
@Pumpguy
I need to correct myself, the Boiler holds 14 gallons. I said before it holds 17 gallons.
Con receiver holds 6 gallons.
Hope I don't have that problem. But that's a great sulotion. Thank you
First pumped return.
Live and learn.0 -
What is the recommended flow check I should use on the condensate pump receiver tank air vent line, in order to keep the air out and still keep the tank vented to the atmosphere? Looking at piping diagrams online and in the Lost Art, it shows a flow check and seal high above the tank. Is there a mechanical advantage to having the water seal that high? Would they fill the water seal with something thicker than water?
Also, how much psi does it take to get to the exploding point of a condensate pump? I asked mr. Owl, when he said "let's find out" I took my lollipop and left.
Why do condensate pumps explode?
Trying to figure out the safest way to keep an air vent open and closed at the same time has been the most complicated problem on this job for me.0 -
Is there a harder and more complicated way to do this? I can't think of one, off hand. That said, as a building super., I wouldn't want to have anything to do with this... or I'd surely want to be paid more!Br. Jamie, osb
Building superintendent/caretaker, 7200 sq. ft. historic house museum with dependencies in New England0 -
@Jamie Hall
I don't know why you feel like that. There's nothing crazy going on here that's never been done before. All that I'm doing is using a vacuum pump to remove the air, relieving the boiler from needing to build pressure in order to fill the system.
There is no extra service that needs to be done for the pump or the controls.
The only thing that's different is a vacuum pump turns on when there's a call for heat and turns off when the vacuum switch is satisfied.
The good thing about this system is it wasn't originally designed as a vacuum steam system. So even when the day comes that the pump sucks its last breath, the building won't be without heat. Simply disconnect the vacuum line from the solenoid valve and the valve will act as an automatic air vent.
The super won't ask for more money because he doesn't touch the boiler anyways1 -
Jamie Hall said:
Is there a harder and more complicated way to do this? I can't think of one, off hand. That said, as a building super., I wouldn't want to have anything to do with this... or I'd surely want to be paid more!
Single pipe 392sqft system with an EG-40 rated for 325sqft and it's silent and balanced at all times.
0 -
@AMservices -- I realise that there's nothing going that hasn't been done before. I just prefer to keep things as simple as possible. I suppose some supers don't touch the boiler; I do pay attention to them and while I don't baby them, I try to keep them running well. If only to avoid unexpected surprises at oh dark hundred in January at 20 below...Br. Jamie, osb
Building superintendent/caretaker, 7200 sq. ft. historic house museum with dependencies in New England0 -
Vacuum pump with zone valves?
A well thought out condensate handling facility is preferable to feed pump in my opinion.0 -
@AMservices, A common 1/2" brass swing check valve would be fine for a pressure vent for your size unit. Keep in mind that the air discharge line from the vacuum pump is different, and should not be asked to serve as a pressure vent from the condensate tank.
Is your condensate tank cast iron or welded steel? Typically, cast iron tanks are good for operating out to a 20" Hg. vacuum, or even more. I have even seen cast iron vessels used as air/water separators on liquid ring compressors discharging @ 80 to 100 PSI.
Might not hurt to take a light hammer and tap the sides and top to get an idea of tank's wall thickness. Depending on how the mold's interior core was set up at the foundry, you could have a thin section. I've seen this a few times in the past.
If your tank is welded carbon steel, typical wall thickness is only 3/16", and with longer unsupported sections, "oil can" flexing can occur with pressure changes. Your 6 gallon tank is one of the smallest, and least likely for this to occur due to small area of each section.
That said, I have seen weld failures due to pressure build up with no pressure vent line fitted. I never did find out what the actual pressure was on that job.Dennis Pataki. Former Service Manager and Heating Pump Product Manager for Nash Engineering Company. Phone: 1-888 853 9963
Website: www.nashjenningspumps.com
The first step in solving any problem is TO IDENTIFY THE PROBLEM.0
Categories
- All Categories
- 87K THE MAIN WALL
- 3.2K A-C, Heat Pumps & Refrigeration
- 58 Biomass
- 426 Carbon Monoxide Awareness
- 116 Chimneys & Flues
- 2.1K Domestic Hot Water
- 5.7K Gas Heating
- 109 Geothermal
- 161 Indoor-Air Quality
- 3.6K Oil Heating
- 70 Pipe Deterioration
- 994 Plumbing
- 6.3K Radiant Heating
- 389 Solar
- 15.4K Strictly Steam
- 3.4K Thermostats and Controls
- 54 Water Quality
- 44 Industry Classes
- 48 Job Opportunities
- 18 Recall Announcements