Radiant overpour over existing slab and stained concrete finish
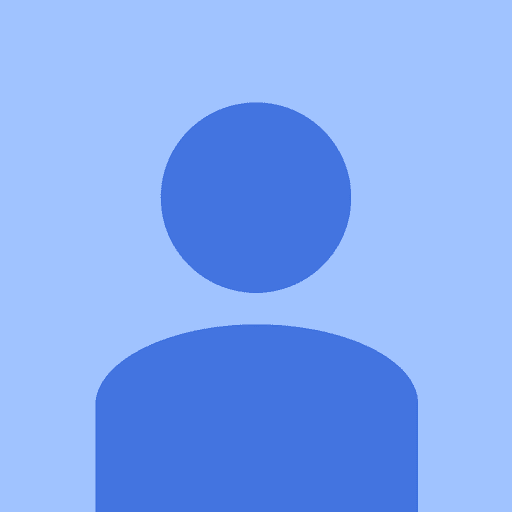
I've done radiant heating on several other projects, but they were all new construction or the slab was entirely new. Other than watching a bunch of videos, this is my first time attempting installation by overpour
The home's style is modern and I figured a stained concrete finish on the lower floor makes the most economical sense and fits the grand scheme of things
I have some room to work with in terms of how thick the overpour could be, the videos I've seen and the stuff I've read it seems like a lot of people are saying gypcrete. My experience with gypcrete isn't a great one, I had a property where we uncovered gypcrete and it was practically dust after we ripped out the tiles. Also doesn't help I don't really want to try someone new for this project...or having to find someone. Every sub I've worked with or site I've visited don't seem to have a good recommendation for gypcrete contractors in my area, a lot of "have you tried craigslist/yellow pages/yelp?" The other thing is I've never really seen microtopped gypcrete, so the end result might not be what I'm looking for.
What I'm thinking of is zip tie 1/2" pex at 8" oc on 6x6 wire mesh on top of the existing slab and doing a 2" lightweight concrete overpour, and acid stain. Cracking is my biggest concern here and I don't think a microtopping would help. Other concern is even though I have room, raising the finish floor by 2" seems a bit undesirable.
Another option is to just knockout the slab. The plan calls for new footing over around 10% of the existing slab. I'll need to knock out another 10% for new plumbing. So at that rate it might be more economical to just knock it out entirely and just re-pour. The entire lower floor is about 1.6k sq ft, addition pushes it to 2.2k so there would be 600 sq ft of new slab anyways.
I was hoping to see if anyone's done something similar, what they did, what products were used and recommendation. I didn't think the thought process would be this tedious. I've Google searched a bunch of thread and found a few videos doing something similar, but their end goals were tile or hardwood floors and about all of them were gypcrete.
Project's still a few months away so I'm hoping I still have time to think it out, and I'm hoping to gather a bit more info before that.
Comments
-
Always the height issue.
But more importantly, for performance, you've got to create a thermal break either from the existing slab or to ground if you bust up the existing slab. How's the water table? Within 6' to grade?
The best option is to start over with a new slab, and do the prep under it properly - 2" foam board insulation on compacted gravel, with perimeter around the footings, 6 mil vapor barrier over that, 6" mesh sheets over that, and then your tubing. Would be nice to bury a 3/8 copper tube, straight as possible, less than 6 feet or so to an accessible location for a sleeve for slab temp sensing if you wish.
If you bite the bullet and do it this way, the height issue is moot, and it's done to best practices.
If that's not possible, then looking at an overpour, you still need a thermal break to cut downward heat loss. I have on occasion, used (gasp) bubble foil in extreme cases where height was critical, or thinner high R foam board. Over that, either a rail product power nailed to the old slab, and tubing snapped into the rails or the plastic "honeycomb" panels that you walk the tubing into whatever configuration needed. Then a minimum of 1.5" concrete overpour. Not a fan of gypcrete.
Roth and others make a foam panel with tube grooves in them, as another overpour option, just watch the elevations. If it's going to be tile or stone finish floor or a floating hardwood composite, maybe no overpour and just that panel product with Hardibacker over it to create the subfloor.0 -
RADIANT CEILINGS or WALLS . Either of those an option ?You didn't get what you didn't pay for and it will never be what you thought it would .
Langans Plumbing & Heating LLC
732-751-1560
Serving most of New Jersey, Eastern Pa .
Consultation, Design & Installation anywhere
Rich McGrath 732-581-38333 -
Yeah, I forgot to mention it in the original post. If I did the overpour method I'd have the bubble foil beneath the overpour.Bob Bona said:Always the height issue.
But more importantly, for performance, you've got to create a thermal break either from the existing slab or to ground if you bust up the existing slab. How's the water table? Within 6' to grade?
The best option is to start over with a new slab, and do the prep under it properly - 2" foam board insulation on compacted gravel, with perimeter around the footings, 6 mil vapor barrier over that, 6" mesh sheets over that, and then your tubing. Would be nice to bury a 3/8 copper tube, straight as possible, less than 6 feet or so to an accessible location for a sleeve for slab temp sensing if you wish.
If you bite the bullet and do it this way, the height issue is moot, and it's done to best practices.
If that's not possible, then looking at an overpour, you still need a thermal break to cut downward heat loss. I have on occasion, used (gasp) bubble foil in extreme cases where height was critical, or thinner high R foam board. Over that, either a rail product power nailed to the old slab, and tubing snapped into the rails or the plastic "honeycomb" panels that you walk the tubing into whatever configuration needed. Then a minimum of 1.5" concrete overpour. Not a fan of gypcrete.
Roth and others make a foam panel with tube grooves in them, as another overpour option, just watch the elevations. If it's going to be tile or stone finish floor or a floating hardwood composite, maybe no overpour and just that panel product with Hardibacker over it to create the subfloor.
If I knock out the slab, I'd would be doing a 4" slab with #4 rebar @ 16 o.c. ew. And it seems like removing the old slab makes the most sense to meet my end goal of polished/stained concrete?
To Rich, ideally I'd like to just do the floors. The upper level will have pex between joist and no overpour there, hardwood floors nailed to 1 1/8" subfloor. That one's the easy one lol. The slab I definitely like to have heated just because my two options are tile or polished concrete.
The house is in California on an up slope, lowest elevation of the lot is 180', highest elevation is 196'. The existing grade I'll be building over is flat at 183'. So ground water's not a concern in this case.
Really appreciate the input.0 -
-
I took a rotary hammer and drilled a couple of holes to see if the slab and footing was a single pour, and it appears like it is. So it seems like this will prevent me from knocking out the entire slab without doing a large amount of work to it.
I suppose my biggest concern is cracking with a thin slab. Rebar is relatively cheap and I'm thinking instead of mesh I would do #3 12" o.c. and instead of doing a lightweight mix, doing a 6-6.5 sack mix maybe a 7 sack mix.
I've thought about doing fiber cement with the rebars, but I don't think the benefits and cost outweighs the imperfections and bumps the fiber creates.
I do have 10' ceilings so there's some room I can give up, but concerns definitely shifting towards cracking.0 -
A gas saw can cut your perimeters if that helps. A monolithic footing and slab pour is unusual in res though. If overpour, 1.5" minimum over the tube . How does your mason feel about the potential crack issue? Expect it, give it a place to crack..
My experience with fiber cement is that if it's not ccovered, over time traffic creates a fuzzy surface2 -
Only 2 kinds of slabs . Those that are cracked and those that have not cracked YET .You didn't get what you didn't pay for and it will never be what you thought it would .
Langans Plumbing & Heating LLC
732-751-1560
Serving most of New Jersey, Eastern Pa .
Consultation, Design & Installation anywhere
Rich McGrath 732-581-38333 -
null
The house is mines, but there's a good chance I will be selling it upon completion. All concrete cracks, I know, but I'd like to mitigate major cracking.
My first idea was to use a gas powered saw and cut around the perimeter. The existing footing was suppose to be only 18" width and about 24 depth. So far with my drilling, I'm getting up to 24" width. Sorta puts me in a possible, but not plausable situation. Definitely unusual, some of my commercial and multi family projects are less overkill than this.0 -
Familiar territory these last few days. Guys sawcut me a bunch of trenches thru old, leaking copper radiant sitting on the earth under a 5" slab. Ala Levittown LI. Ran 450 feet of 1/2" Fostapex home runs with Arma flex insulation today for a new cast iron radiator zone. Of course they severed the domestic piping going to a bath. Oops. But a blessing in disguise, those copper lines were a failure waiting to happen too. New pex there as well.2
-
Since you are already doing staple-up from below, since the ceiling is out, radiant ceiling will be the easiest and most cost effective solution. Once you take out the drywall you put up your tubing and (hopefully) plates, insulate the joist bay and fur down the ceiling and put up plates and tubing then re-drywall. With this method there are no issues with door frames and headers and all the other things that come with raising the floor. Make sure and do a heatloss to ensure the system will work without supplemental heat.1
-
-
If you do a concrete over pour, you MUST have a polyethylene bond breaking sheet to avoid the thermally active cement slab from getting bonded to the substrate or it WILL break up and look like a jig saw puzzle. Not a pretty picture.
You also must have expansion control joints in place to accommodate the expansion/contraction of the slab.
Honestly, I think I'd do a radiant ceiling, and NOT a radiant floor as my well known associate Mr. Tesmar has said.
I am of the opinion that if the edge of the slab is uninsulated, that it would be worth the time and money to dig up the exterior foundation to around 2' below grade and insulate it with EXP insulation. Extend the insulation outwards for a foot or two to give additional thermal shielding. Doing a radiant floor in a situation where the slab edge is not insulated may feel good on the feet, but it will waste a significant amount of energy from the slab edge losses. The Johnny Jumps ups that will be growing around the exterior of your home in January and the utility company will love you, but your checking account won't :-)
If you really want warm floors in the bathrooms, I'd recommend going with an thin set electric radiant floor grid in THOSE applications, and hydronic radiant ceilings in the balance of the home.
You won't regret doing radiant ceilings. I find mine just as comfortable as a radiant floors, and you can get more BTUH out of a wall or ceiling than you can a floor.
ME1
Categories
- All Categories
- 87K THE MAIN WALL
- 3.2K A-C, Heat Pumps & Refrigeration
- 58 Biomass
- 426 Carbon Monoxide Awareness
- 113 Chimneys & Flues
- 2.1K Domestic Hot Water
- 5.7K Gas Heating
- 109 Geothermal
- 161 Indoor-Air Quality
- 3.6K Oil Heating
- 70 Pipe Deterioration
- 994 Plumbing
- 6.3K Radiant Heating
- 391 Solar
- 15.4K Strictly Steam
- 3.4K Thermostats and Controls
- 55 Water Quality
- 44 Industry Classes
- 48 Job Opportunities
- 18 Recall Announcements