Welcome! Here are the website rules, as well as some tips for using this forum.
Need to contact us? Visit https://heatinghelp.com/contact-us/.
Click here to Find a Contractor in your area.
Setbacks and ODR in hot water systems
Options

SWEI
Member Posts: 7,348
Following up on an earlier comment I made, here is some data from a current project. The building is a 1949 church with uninsulated 12" CMU walls and a nearly uninsulated roof/ceiling (an inch or so of staple-up acoustic tile.) We have had it running on constant well-tuned ODR for about two months, with indoor temps varying only a degree or two and the control valves wide open. We agreed to try setbacks at the client's request after warning them that the results might not be what they imagine. In part, this was to help us understand when and how we might recommend setbacks for future projects with very intermittent occupancies. The chart plots several values: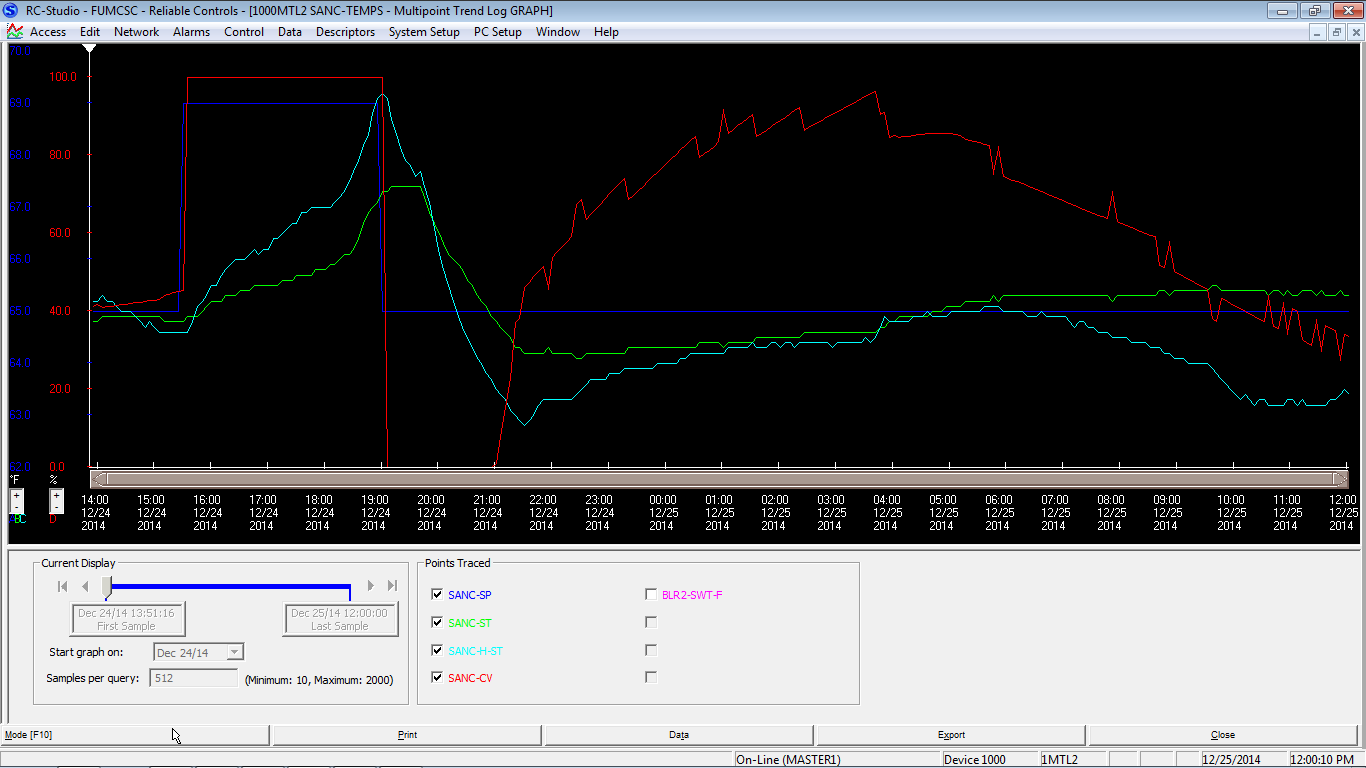
As you can see from the graph, it did not work out all that well. Next steps will be to turn on the ceiling fans whenever the upper temp exceeds the lower temp by 4˚F and to base the recovery start time on the outdoor temp averaged over the previous four hours (and perhaps the slope of the outdoor temp change, with negative slopes dictating a more aggressive recovery.) I think I'll start logging the firing rate of the cascaded boiler group as well, to see how well that correlates with the gas meter readings we plan to take.
- SANC-ST (green line) is a temperature sensor at the rear of the sanctuary, roughly four feet above the floor.
- SANC-H-ST (light blue line) is a temperature sensor mounted near the front of the sanctuary, roughly twelve feet above the floor.
- SANC-SP (blue line) is the setpoint (65˚F during unoccupied periods, 69˚F for occupied periods.)
- SANC-CV (red line) is the position of the control valve for that zone (percent open.)
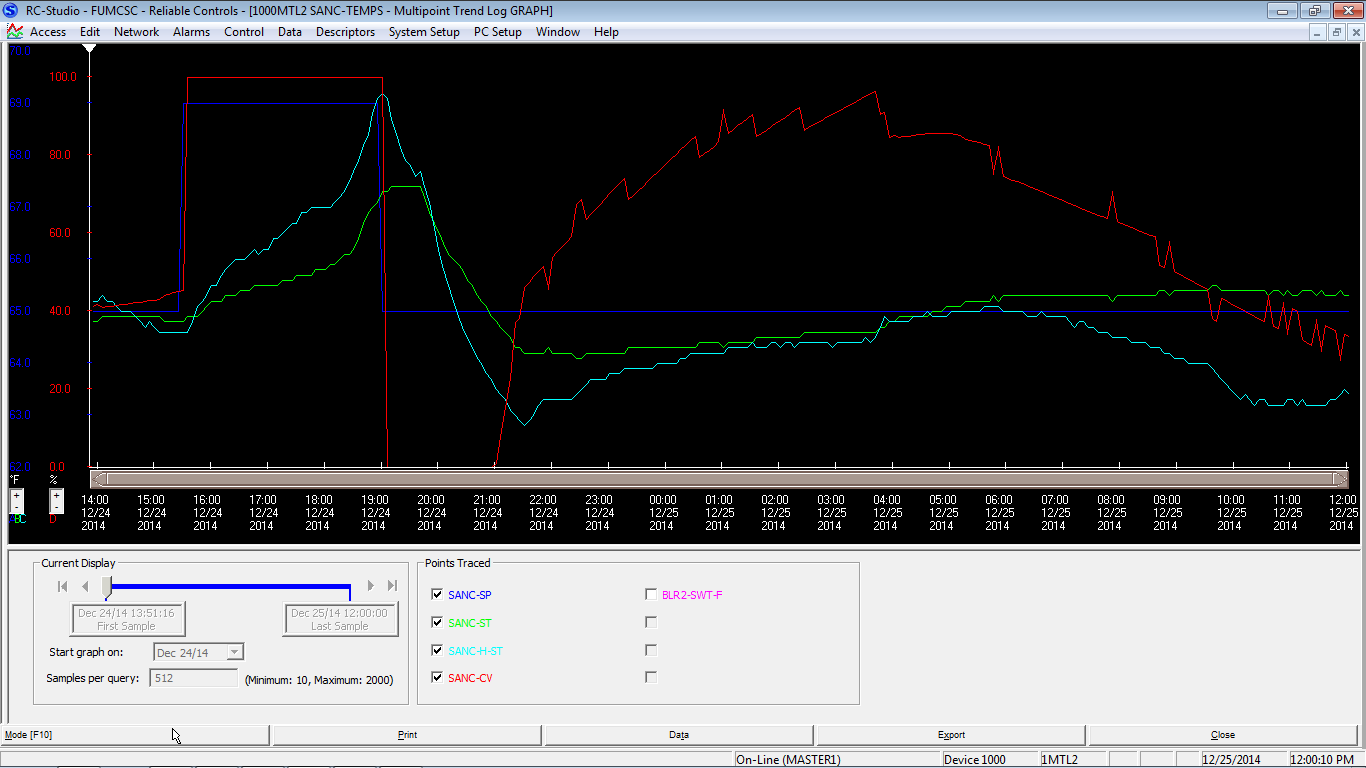
As you can see from the graph, it did not work out all that well. Next steps will be to turn on the ceiling fans whenever the upper temp exceeds the lower temp by 4˚F and to base the recovery start time on the outdoor temp averaged over the previous four hours (and perhaps the slope of the outdoor temp change, with negative slopes dictating a more aggressive recovery.) I think I'll start logging the firing rate of the cascaded boiler group as well, to see how well that correlates with the gas meter readings we plan to take.
0
Comments
-
The service was supposed to last about an hour. Previous experiments showed a longer "coasting time" from thermal mass, but we are now looking to adjust that based on outdoor air temp.Hatterasguy said:1) It appears that the system decided to go back to setback 30 minutes into the scheduled service (1900). Why?
2) The control valve remained closed until the exact point where the rear sensor crossed the setpoint (65°F).
Not quite sure what you are referring to -- roughly what timestamp?Is there any way to anticipate the setpoint or program it based upon the rate of temperature drop rather than actual temperature?
This is what the Integral component of a PID loop does (integrate over time.) The Derivative component has even more power, but is easy to destabilize things with -- sometimes into oscillation, which usually does not end well.Also, I consider what you have done as quite good. The largest deviation is 2°F. on the front sensor. This isn't exactly a temperature controlled room!!!
Thank you. The front sensor is not actually doing anything other than logging data at the moment. Next summer, it will tell us when to turn the fans on to destratify again, and help determine when to start the evaporative cooler -- and whether or not to wet the pads. The result should be a comfortable building, despite its being uninsulated and having no refrigerated air.0 -
We can minimize (damp) that with loop tuning. The Proportional band is tight on these, to allow for fast recovery. We will try updating the Integral a bit more frequently, but we have to watch for unintended consequences.Hatterasguy said:2) The control valve remained closed until the exact point where the rear sensor crossed the setpoint (65°F). With the natural hysteresis of the system, this would certainly result in a temperature drop below setpoint, as you have shown.
0 -
This shows how nicely proportional flow control and full ODR work together.0
Categories
- All Categories
- 87K THE MAIN WALL
- 3.2K A-C, Heat Pumps & Refrigeration
- 57 Biomass
- 425 Carbon Monoxide Awareness
- 115 Chimneys & Flues
- 2.1K Domestic Hot Water
- 5.7K Gas Heating
- 106 Geothermal
- 160 Indoor-Air Quality
- 3.6K Oil Heating
- 70 Pipe Deterioration
- 983 Plumbing
- 6.3K Radiant Heating
- 389 Solar
- 15.4K Strictly Steam
- 3.4K Thermostats and Controls
- 54 Water Quality
- 44 Industry Classes
- 48 Job Opportunities
- 18 Recall Announcements