Geothermal, one loop field, two air handlers
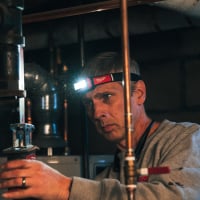
I’ve never done two systems off of one loop field.
How does my sketch look? I was going to switch to 1 1/4” type L, make myself a small loop against the wall, then head off to each heat pump.
The little circle under the loop pump is going to be a pressure gauge. Maybe I’ll put it on top, not the bottom.
I could flip the orientation of the supply and returns , but I think that’s smaller detail
Alpha2 29-99 circulator for loop and Bluetooth Alphas for the heat pumps.
I’ll have to figure out a way to get the primary pump to kick when one of the two system pumps energized.. zone control relay? RIBs?
I’ll probably need to fiddle with converting the 230 down to 115. But I’m trying not to build a weird Frankenstein.
I can add or subtract, I packed budget money.
Comments
-
I think you want sone hydraulic separation if those circles are zone pumps? Think of the loop field as the "boiler" same piping.
I would add checks and balance valves for some fine tuning.
I believe the Alphas and Magnas are available in 230V. I know Magnas are 230V and they seem to cross the 26-99 pretty close.
I have seen GEO versions of the Magna on some flow centers.
Here are some options, loop field squiggle lines :) With two zones, maybe some buffer tank capacity, unless the HP modulates?
Bob "hot rod" Rohr
trainer for Caleffi NA
Living the hydronic dream0 -
Nice, I like the 3rd, I would need to 90 up to fit in the purge cart apparatus, then hit the tees
But, making a circle isn't good? I have more than enough pump. With a boiler, i though the main concern was keeping flow from migrating. With this set up, I can care if some migration creeps around. How might that affect me?
Maybe option 3 is neater and cleaner
0 -
I can probably switch from 230 down to 115 right at the HP with a RIB(s). I just need to kich the loop pump when one or two of the HPs get cranked up
GEO versions of the Magna on some flow centers. Yes, the costs are high—-I guess it's all relative!
0 -
these are two stage heat pumps. But I was going to send the same GPM, not worry about stepping the pump speed down
I just need to draw in the purge cart hook ups onto the two different circuits
0 -
-
-
I'm a bit puzzled, @GW , about "switching" from 230 to 115? If you have a neutral available, you have 115 between either hot and that neutral anyway? And if you have a switch of any kind on one hot, you really have to have one on the other…
What am I missing?
Br. Jamie, osb
Building superintendent/caretaker, 7200 sq. ft. historic house museum with dependencies in New England0 -
Jamie, the geo HP's have a 230v pump output. Sure, i could grab a leg and steal a neutral, but that's a little yukky.
As HotRod mentioned, I could locate 230v circs, but I still need to get the two HP circs to 'talk' to the loop pump. No matter what, I have control stuff to deal with.
0 -
I take it that the HP pump pump output is 240 volt and not a dry set of contacts. I would put a relay with a 240 coil on the HP and a new 120 volt circuit to start the pumps through the relay contacts.
0 -
As far as the pipe connections to the ground loop I would tee both supplies to both HP together and tee both HP returns together to make sure both HPs get the same water temp. I would then tie the common supply and return to the heat pumps in on the same side of the GW loop pump. If you have supplies on one side of the pump and returns on the other the GW pump will try and push water through the HPs
0 -
Ed yes is there a sketch that doesn’t show both HPs getting the same temperature?
0 -
Probably not.
I did only a few WSHP, most of what i did were multiple boilers or multiple chillers. Because chillers only work (usually) with a 10-12TD they are very sensitive to different water temps. Because of that I always made sure to tee all returns together and all supplies together especially with P/S. I would always come off the loop with 1 return tee then tee again and go to each chiller if there were two of them and I would do the same with the two supply pipes. I wouldn't come off the loop with two return tees and two supply tees for two units. But that's just me. I always wanted to know that both units were getting the same return temp and that the supply temps were mixing.
If you have any variable speed circs and you get in a situation where the water can "back up" across the bridge" and you have multiple return tees one unit could get different return water temp that the other one
0 -
today’s riddle, why am I taping cardboard to the wall?
0 -
-
it’s fusion- I would have needed a 3rd arm
to hold a level.
Sure I could have eyeballed it, maybe it would be been close
0 -
Work looks great!
Assuming the rest of the piping looks like this?
If so the loads are parallel so they will receive the same SWT.
I imagine the loop pump is VS, driven by a control to maintain the ideal gpm at the desired ∆? The A2WHPs work that way varying the flow as the compressor modulates. Or vice versa.
One thought. The header at top should be sized for the flow of both loads with a low velocity, around 2 fps.
So if the zones are 6 gpm each, 12 gpm total that header should be 1-1/2" That section of piping is the low loss header, where all 3 flows need to get along. Bigger is better
If your loads are 9 gpm or less 1-1/4 will be ok.
If your 2 zones are more than 12 gpm, 2" may be better.
I'm not a fan of the valve between the close tees in that Webstone P/S assemble. Even a full port ball valve adds pressure drop, so the tees are a foot or two apart with that valve. If it is a reduced port ball valve between the tees the EL could be 6' or more!
Bob "hot rod" Rohr
trainer for Caleffi NA
Living the hydronic dream0 -
Hot Rod it’s a 3 ton and a 1 1/2, I’ll get back with the specific GMP and more pics. I had to scram after I took this pic today. My guy kept going after I left. Thanks
0 -
we’re picking away at this, I only got 3 1/2 hours on the job today. One of my guys did some of this manifold work as well. We also ran some 1” PE pipe through the basement. Back Monday to fire this puppy up. Maybe both puppies
yeah we slapped some vanes on that return
1 -
I’m a little bugged that the Alphas came “Rotated Flange”. I putty the dude that every tries to change a circ without a ratcheting box wrench
lol- Pitty
0 -
3 ton = 36,000 btu/hr maybe a bit less on the tag? So 3.6 gpm, well within the piping you have.
Bob "hot rod" Rohr
trainer for Caleffi NA
Living the hydronic dream0 -
laugh out loud, I jammed myself with the circulator bolts, had to twist 45°.
insulating pipes, not our thing. Some of it looks pretty good but getting this pump station to look nice was a bit of a battle. My guy did his best.
My next trip back I’m going to pull those brass pump cart connectors off, and I’m going to insulate that half inch. It’s sweating pretty good. I still need to pump in the methanol
I almost had a bird when the Electrician drilled those holes for the Romex and didn’t use a straight edge. But it’s all good. It matches our insulation job I guess.
0 -
One thing to watch when you set up your pumps is the primary flow always needs to be above the flow of the two heat pumps. If the flow rate is too low, the heat pumps will pull some of their own return water into the supply without going through the geo loop which will reduce COP.
If those Alphas have IFCs, I'm wondering if it might be better to leave the purge valve closed between the closed spaced Ts to avoid this issue.
P.S. How dare you install a heat pump water heater, it should be a dual tank with a desuperheater! The HPWHs are expensive, unreliable and maintaince nightmares :) On a serious note, do watch how you set up the recirc on it, uncontrolled recirc will wear them out.
1 -
Good points- I'll take a minute or two and look at the chart on the 2699 pump, convert the head loss to gpm and see how I fare. I'm on the middle speed on the loop pump. The lowest gpm I can get is 3, on the small 1 1/2 ton. At the moment, the 3 ton is working at 3.5 gpm.
No IFC, I don't care if there's some creepage.
Recirc pump - that wasn't my idea. It was there on the old wh and we just put it back where it was. It's actually unplugged. I'm a 'run a new recirc line' guy. I never liked these bypass thingies under the sink
0
Categories
- All Categories
- 87K THE MAIN WALL
- 3.2K A-C, Heat Pumps & Refrigeration
- 58 Biomass
- 427 Carbon Monoxide Awareness
- 113 Chimneys & Flues
- 2.1K Domestic Hot Water
- 5.7K Gas Heating
- 109 Geothermal
- 161 Indoor-Air Quality
- 3.6K Oil Heating
- 70 Pipe Deterioration
- 995 Plumbing
- 6.3K Radiant Heating
- 391 Solar
- 15.4K Strictly Steam
- 3.4K Thermostats and Controls
- 55 Water Quality
- 44 Industry Classes
- 48 Job Opportunities
- 18 Recall Announcements