Bladder vs bladderless tank questions
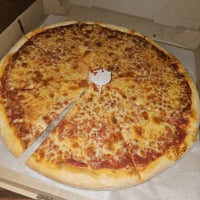
I've also learned that there shouldn't be any type of auto air vent on this system.
Can someone please shed some light on this subject? I'd like to learn how to properly set this up. How would I purge air from this type of system?
Am I better off just putting on a new bladder tank and using the air eliminator?
After learning this, I closed the vent of the air eliminator and purge some water from the tank.
System usually runs between 10-20 psi 180 degrees for a moderate sized home with hot water baseboard. 2 zones.
All help is appreciate as usual!
See pics attached.
Thanks in advance

(System is an old Weil McLain natural gas boiler. Oldest service tag is from 1977)
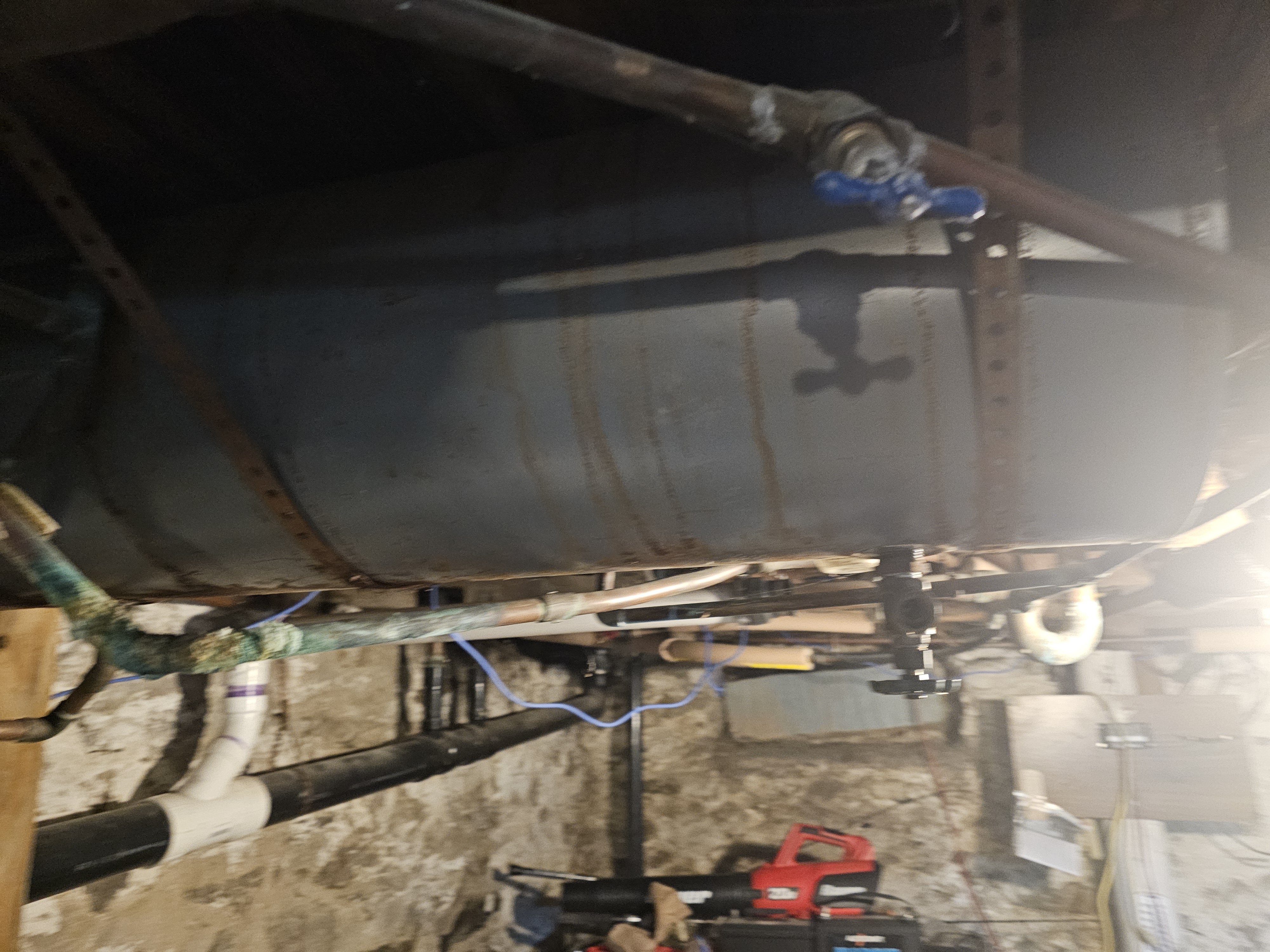
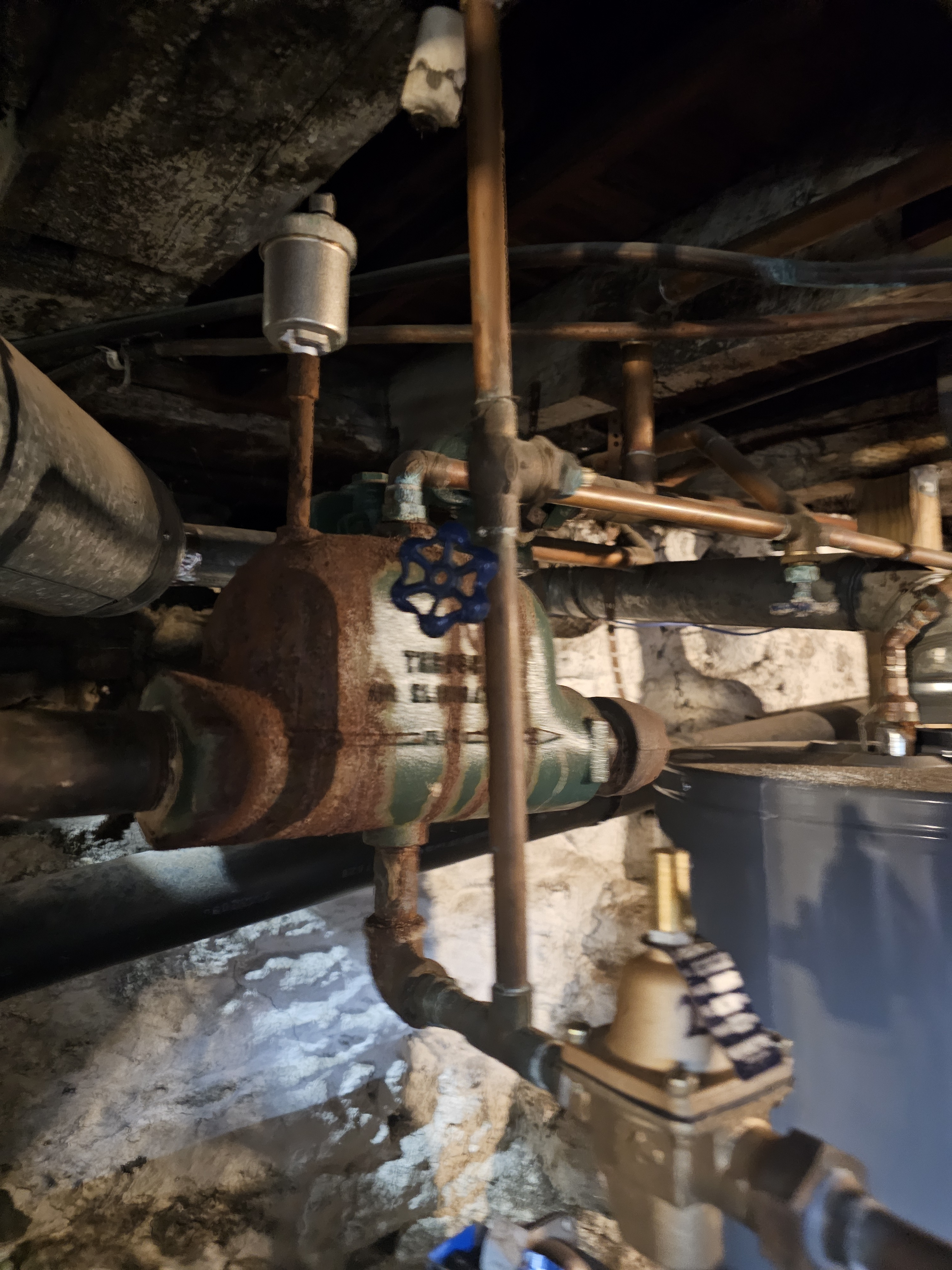
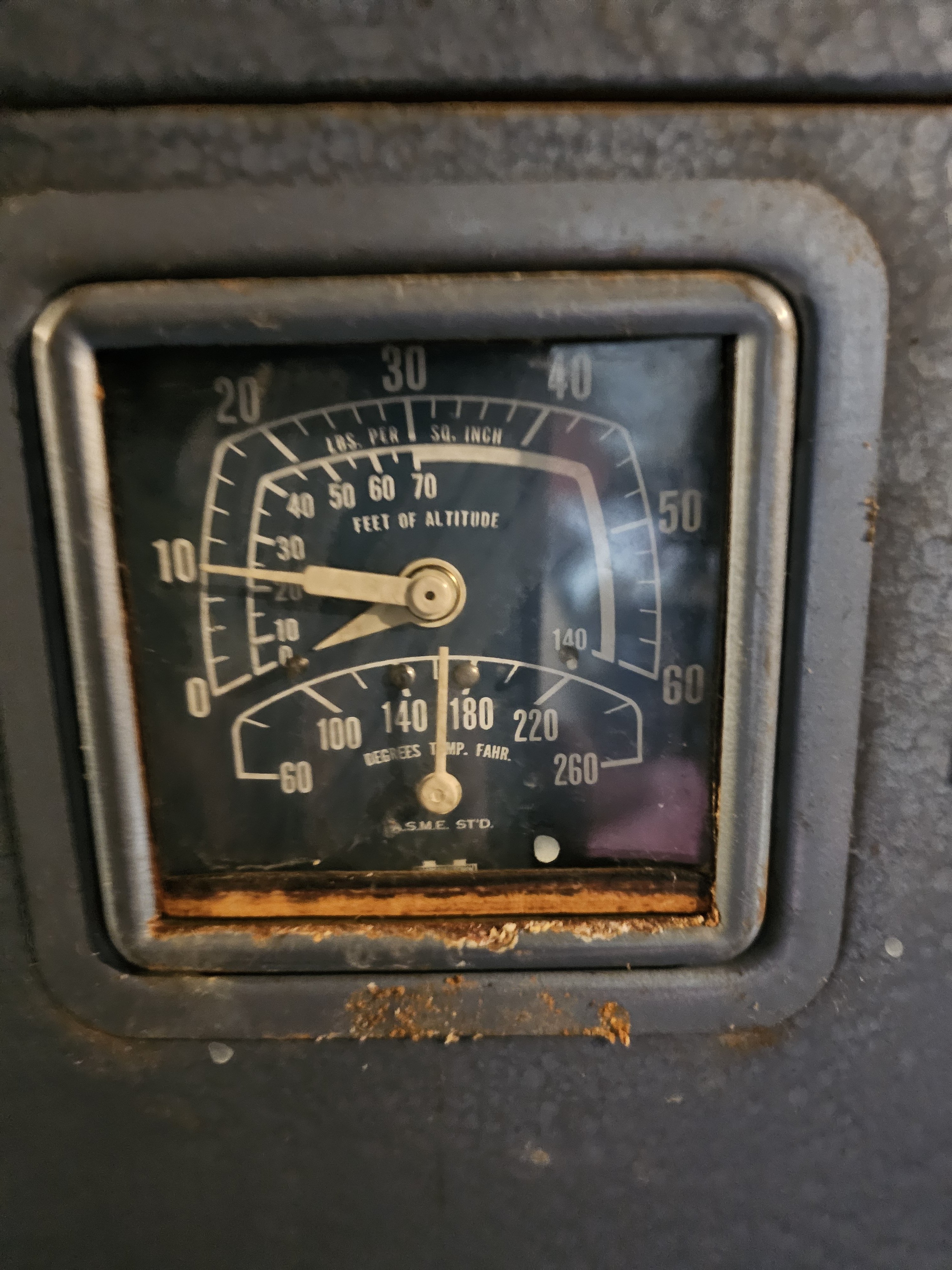
Comments
-
Also, the original setup kept blowing the pressure relief valves and auto air vent.
It's been notoriously difficult to purge air from the zones of this system.
0 -
That's a compression tank. Very simple. No bladder. No diaphragm. Works splendidly -- provided you know what you are dealing with.
Step 1. Lose the air eliminator vent. It almost looks as though the air removal fitting might just be properly connected to the compression tank. Is it?
What happens with these things is that all the air is directed to the compression tank, and forms an air cushion at the top of the tank. The bottom half of the tank -- more or less -- has water in it. But... it's that all the air goes there, as what causes problems with a compression tank is when that air cushion is lost and the tank becomes "waterlogged". You can still purge the system normally (and need to, if it's drained).
Solving a waterlogged compression tank is also easy. There should be a valve on the line from the air scoop to the tank. Close it. There is a drain on the bottom of the tank or at one end at the bottom. Open that. If there is another valve opening to the air near the top of the tank, open that, too -- otherwise you may have some difficulty in persuading the water to drain out of the tank -- which is what you want. One way or another get all the water -- all of it -- out of the tank. Then close the drain (and air inlet if it had one) and open the connection to the air scoop. Add enough water with your fill valve to reach the desired pressure, pick up you tools and that's it.
Edit: no need to replace anything. Just get rid of the air vent or close it off. The fact that it was blowing the pressure relief valve is a sure indication that the tank is waterlogged, and the auto air vent is the culprit. As I say, lose it.
Purging such a system of air only needs to be done if the system has been drained -- and it is done exactly as it would be with any hydronic system.Br. Jamie, osb
Building superintendent/caretaker, 7200 sq. ft. historic house museum with dependencies in New England3 -
Thank you so much! I appreciate that. Will do immediately.Jamie Hall said:That's a compression tank. Very simple. No bladder. No diaphragm. Works splendidly -- provided you know what you are dealing with.
Step 1. Lose the air eliminator vent. It almost looks as though the air removal fitting might just be properly connected to the compression tank. Is it?
What happens with these things is that all the air is directed to the compression tank, and forms an air cushion at the top of the tank. The bottom half of the tank -- more or less -- has water in it. But... it's that all the air goes there, as what causes problems with a compression tank is when that air cushion is lost and the tank becomes "waterlogged". You can still purge the system normally (and need to, if it's drained).
Solving a waterlogged compression tank is also easy. There should be a valve on the line from the air scoop to the tank. Close it. There is a drain on the bottom of the tank or at one end at the bottom. Open that. If there is another valve opening to the air near the top of the tank, open that, too -- otherwise you may have some difficulty in persuading the water to drain out of the tank -- which is what you want. One way or another get all the water -- all of it -- out of the tank. Then close the drain (and air inlet if it had one) and open the connection to the air scoop. Add enough water with your fill valve to reach the desired pressure, pick up you tools and that's it.
Edit: no need to replace anything. Just get rid of the air vent or close it off. The fact that it was blowing the pressure relief valve is a sure indication that the tank is waterlogged, and the auto air vent is the culprit. As I say, lose it.
Purging such a system of air only needs to be done if the system has been drained -- and it is done exactly as it would be with any hydronic system.0 -
Get rid of the auto vent on the cast purger, it will eventually eliminate the air in the tank. Or pipe the vent opening up to the compression tank.
A compression tank is an air management system. A bladder type expansion tank is an air elimination system.Bob "hot rod" Rohr
trainer for Caleffi NA
Living the hydronic dream1 -
I tried doing this last night. It ran okay for awhile.Jamie Hall said:That's a compression tank. Very simple. No bladder. No diaphragm. Works splendidly -- provided you know what you are dealing with.
Step 1. Lose the air eliminator vent. It almost looks as though the air removal fitting might just be properly connected to the compression tank. Is it?
What happens with these things is that all the air is directed to the compression tank, and forms an air cushion at the top of the tank. The bottom half of the tank -- more or less -- has water in it. But... it's that all the air goes there, as what causes problems with a compression tank is when that air cushion is lost and the tank becomes "waterlogged". You can still purge the system normally (and need to, if it's drained).
Solving a waterlogged compression tank is also easy. There should be a valve on the line from the air scoop to the tank. Close it. There is a drain on the bottom of the tank or at one end at the bottom. Open that. If there is another valve opening to the air near the top of the tank, open that, too -- otherwise you may have some difficulty in persuading the water to drain out of the tank -- which is what you want. One way or another get all the water -- all of it -- out of the tank. Then close the drain (and air inlet if it had one) and open the connection to the air scoop. Add enough water with your fill valve to reach the desired pressure, pick up you tools and that's it.
Edit: no need to replace anything. Just get rid of the air vent or close it off. The fact that it was blowing the pressure relief valve is a sure indication that the tank is waterlogged, and the auto air vent is the culprit. As I say, lose it.
Purging such a system of air only needs to be done if the system has been drained -- and it is done exactly as it would be with any hydronic system.
Then I see the pressure relief valve dripping again and water everything this morning.
Was difficult getting the water out of tank, and I doubt I got all of it out.
Does it need to be completely empty?
Is there any benefit to switching to Bladder & Air Vent vs just capping the air vent and trying again with Compression tank?0 -
Currently I plan on just capping off the Air Vent and trying to empty tank again. I don't think I got it all out last time.hot_rod said:Get rid of the auto vent on the cast purger, it will eventually eliminate the air in the tank. Or pipe the vent opening up to the compression tank.
A compression tank is an air management system. A bladder type expansion tank is an air elimination system.
Also, when you say pipe the vent opening into tank, youre talking about the top of the air vent? Or top of Air Scoop. Currently there is a pipe from Air Scoop into one side of tank.0 -
hmm... first, yes -- you need to get all the water out of the tank before opening it back in to the system, and any drain valves you used to get the water out need to be closed tight before you do. The idea is to trap the air in there.
Now. How does the system and air scoop connect to the tank? You say there is a pipe from the air scoop into the side of the tank? Eh? Is there any pipe from the system into the bottom of the tank? A sketch of what connects to what might help...Br. Jamie, osb
Building superintendent/caretaker, 7200 sq. ft. historic house museum with dependencies in New England0 -
Jamie Hall said:hmm... first, yes -- you need to get all the water out of the tank before opening it back in to the system, and any drain valves you used to get the water out need to be closed tight before you do. The idea is to trap the air in there. Now. How does the system and air scoop connect to the tank? You say there is a pipe from the air scoop into the side of the tank? Eh? Is there any pipe from the system into the bottom of the tank? A sketch of what connects to what might help...
Maybe gatevalve is leaking by and letting water in while draining??
EDIT : sorry I forgot to include pic. Here it is!
Also, i shutoff the gate valve and tried to drain it, ended up draining the whole system. Im assuming that isolating valve is leaking past...I
0 -
Drained the whole system? That's a bore. Sorry about that... but otherwise you seem to be on the right track. And now that the system is empty, maybe the tank is, too! There is a drain valve on the tank, near the bottom, I hope?Br. Jamie, osb
Building superintendent/caretaker, 7200 sq. ft. historic house museum with dependencies in New England1 -
Yeah lmfao. I realized that the gate valve was leaking when I hit my third 5-gallon bucket... I just kinda visually compared the size of the tank vs 3 x 5gal buckets... lol. So I stopped halfway, just filled the system back up. I'm gonna come back to this another day. System is running okay from what I know. It's for close-family.Jamie Hall said:Drained the whole system? That's a bore. Sorry about that... but otherwise you seem to be on the right track. And now that the system is empty, maybe the tank is, too! There is a drain valve on the tank, near the bottom, I hope?
Yes, the drain valve is on opposite end from the copper pipe from Air Scoop.
The background light perfectly outshines it.0 -
Don't look at this process as draining the expansion tank. Look at this as filling the expansion tank with air. I have found a very easy way to accomplish this.
1. Close the automatic feed valve so no new water enters the boiler
2. Connect a hose to the lowest boiler drain in the system.
3. Open that boiler drain and let the water out at the bottom of the boiler ( if there is no floor drain then you will need a pump to remove the water from a basement below grade)
4. Eventually there will be zero pressure on the gauge and the water will stop flowing out of the hose.
Now here is the fun part. The water in the expansion tank is now under a negative pressure (similar to an inverted glass of water in the sink full of water. when you lift the inverted glass out of the water the glass stays full of water because there is no way to let the air in)
5. Open the drain valve at the bottom of the expansion tank and hear the air gurgle into the tank as the water leaves the boiler drain at the bottom.
6. Keep opening the valve until you get a drip of water out of the tank, then close is just a bit. This way the air will keep entering the tank as the water in the tank leaves thru the boiler drain at the bottom of the boiler.
7. Keep listening to the gurgle. As the tank has less and less water in it, it will become lighter and it will sound different.
8. Just as the tank is almost empty of water (Full of Air) close the tank drain valve, then close the boiler drain valve, and then open the water feed to get the boiler pressure back up to 12 PSI cold fill pressure.
EDIT added illustration.
Edward Young Retired
After you make that expensive repair and you still have the same problem, What will you check next?
4 -
-
With that boiler gauge and the compression tank, I'll bet you 2 to 1 that it had (or may still have) a B&G 100 or a Thrush vertical circulator on the return.hot_rod said:Were is the circulator on the system?
Edward Young Retired
After you make that expensive repair and you still have the same problem, What will you check next?
1 -
EdTheHeaterMan said:Don't look at this process as draining the expansion tank. Look at this as filling the expansion tank with air. I have found a very easy way to accomplish this. 1. Close the automatic feed valve so no new water enters the boiler 2. Connect a hose to the lowest boiler drain in the system. 3. Open that boiler drain and let the water out at the bottom of the boiler ( if there is no floor drain then you will need a pump to remove the water from a basement below grade) 4. Eventually there will be zero pressure on the gauge and the water will stop flowing out of the hose. Now here is the fun part. The water in the expansion tank is now under a negative pressure (similar to an inverted glass of water in the sink full of water. when you lift the inverted glass out of the water the glass stays full of water because there is no way to let the air in) 5. Open the drain valve at the bottom of the expansion tank and hear the air gurgle into the tank as the water leaves the boiler drain at the bottom. 6. Keep opening the valve until you get a drip of water out of the tank, then close is just a bit. This way the air will keep entering the tank as the water in the tank leaves thru the boiler drain at the bottom of the boiler. 7. Keep listening to the gurgle. As the tank has less and less water in it, it will become lighter and it will sound different. 8. Just as the tank is almost empty of water (Full of Air) close the tank drain valve, then close the boiler drain valve, and then open the water feed to get the boiler pressure back up to 12 PSI cold fill pressure. EDIT added illustration.0
-
EdTheHeaterMan said:
Were is the circulator on the system?
With that boiler gauge and the compression tank, I'll bet you 2 to 1 that it had (or may still have) a B&G 100 or a Thrush vertical circulator on the return.hot_rod said:Were is the circulator on the system?
I'll try to get a pic of the pumps.0 -
Brilliant!!! Very insightful, thank you Ed.Hot_n_Cold said:EdTheHeaterMan said:Don't look at this process as draining the expansion tank. Look at this as filling the expansion tank with air. I have found a very easy way to accomplish this.
1. Close the automatic feed valve so no new water enters the boiler
2. Connect a hose to the lowest boiler drain in the system.
3. Open that boiler drain and let the water out at the bottom of the boiler ( if there is no floor drain then you will need a pump to remove the water from a basement below grade)
4. Eventually there will be zero pressure on the gauge and the water will stop flowing out of the hose.
Now here is the fun part. The water in the expansion tank is now under a negative pressure (similar to an inverted glass of water in the sink full of water. when you lift the inverted glass out of the water the glass stays full of water because there is no way to let the air in)
5. Open the drain valve at the bottom of the expansion tank and hear the air gurgle into the tank as the water leaves the boiler drain at the bottom.
6. Keep opening the valve until you get a drip of water out of the tank, then close is just a bit. This way the air will keep entering the tank as the water in the tank leaves thru the boiler drain at the bottom of the boiler.
7. Keep listening to the gurgle. As the tank has less and less water in it, it will become lighter and it will sound different.
8. Just as the tank is almost empty of water (Full of Air) close the tank drain valve, then close the boiler drain valve, and then open the water feed to get the boiler pressure back up to 12 PSI cold fill pressure.
EDIT added illustration.
When I eventually fill the boiler again, should I open the drains at both pumps while filling to purge air out? Or should I literally just fill the system with water and not mess with air purging.0 -
-
Probably is. However, it's still going.mattmia2 said:That boiler looks to be from more like the 60's.
Anyone wanna place bets on how long it'll last? LOL0 -
Hot_n_Cold said:
That boiler looks to be from more like the 60's.
Probably is. However, it's still going. Anyone wanna place bets on how long it'll last? LOLBob "hot rod" Rohr
trainer for Caleffi NA
Living the hydronic dream0
Categories
- All Categories
- 87K THE MAIN WALL
- 3.2K A-C, Heat Pumps & Refrigeration
- 58 Biomass
- 426 Carbon Monoxide Awareness
- 117 Chimneys & Flues
- 2.1K Domestic Hot Water
- 5.7K Gas Heating
- 109 Geothermal
- 161 Indoor-Air Quality
- 3.6K Oil Heating
- 70 Pipe Deterioration
- 994 Plumbing
- 6.3K Radiant Heating
- 389 Solar
- 15.4K Strictly Steam
- 3.4K Thermostats and Controls
- 54 Water Quality
- 44 Industry Classes
- 48 Job Opportunities
- 18 Recall Announcements