Welcome! Here are the website rules, as well as some tips for using this forum.
Need to contact us? Visit https://heatinghelp.com/contact-us/.
Click here to Find a Contractor in your area.
By-passing the "Dole" Regulator?
RickDelta
Member Posts: 621
Hi Heating Help Community!
In my fluidized resin reactor tank (see attached pic) this is to be the only water flow (1 to 30 gpm max.) path out to the rest of the building.
The reactor tank will NOT function if the water flow thru it is allowed to exceed 30 gpm. Over 30 gpm the fluidized resin beads would all collect at the top of the tank and plug the water flow exit port.
There are peak water flow demands, at times during the day, where I need to, lets say, a total system water flow of 100 gpm.
To achieve this, the reactor tank will contribute its limited 30 gpm of filtered water and a by-pass device would contribute the 70 gpm of un-filtered water flow.
Will a "Back Pressure" regulator do this function for me?
Thanks!
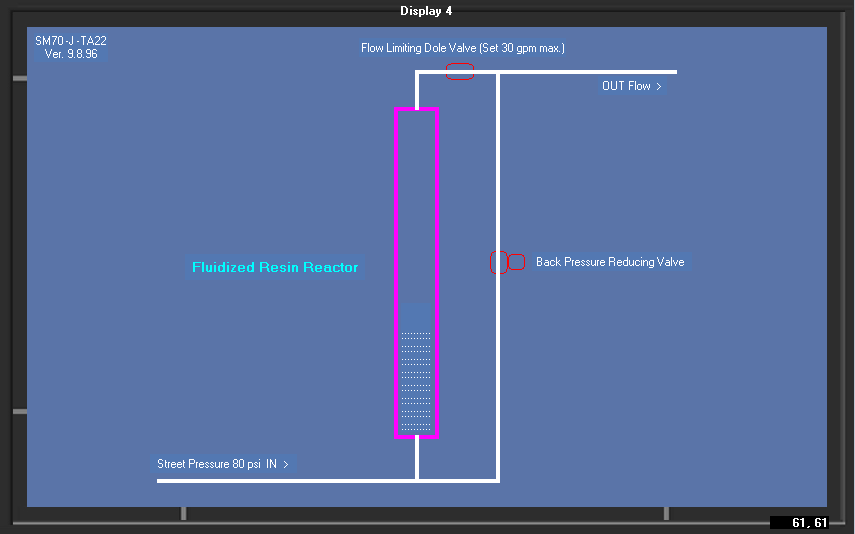
In my fluidized resin reactor tank (see attached pic) this is to be the only water flow (1 to 30 gpm max.) path out to the rest of the building.
The reactor tank will NOT function if the water flow thru it is allowed to exceed 30 gpm. Over 30 gpm the fluidized resin beads would all collect at the top of the tank and plug the water flow exit port.
There are peak water flow demands, at times during the day, where I need to, lets say, a total system water flow of 100 gpm.
To achieve this, the reactor tank will contribute its limited 30 gpm of filtered water and a by-pass device would contribute the 70 gpm of un-filtered water flow.
Will a "Back Pressure" regulator do this function for me?
Thanks!
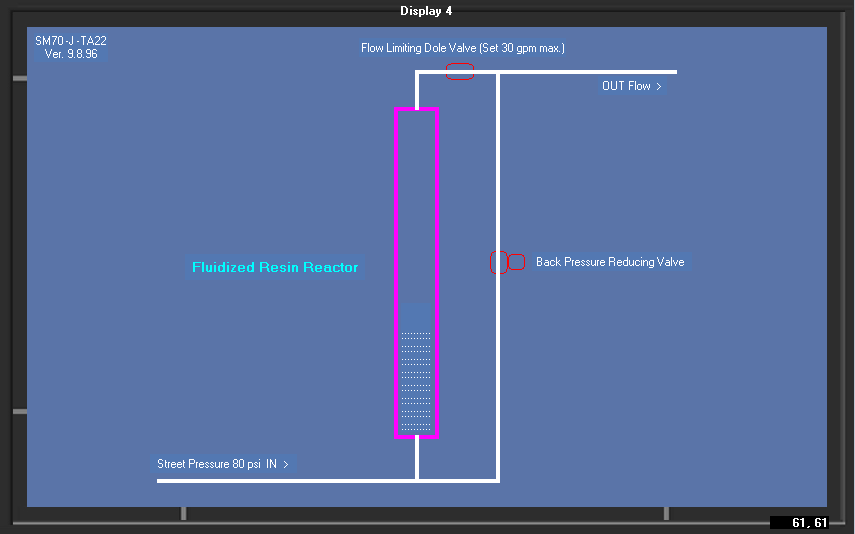
0
Comments
-
I won't even ask.
But no. What you need in that application is a valve which will open to maintain downstream pressure. A backpressure maintaining valve is designed to close to maintain upstream pressure. The latter configuration is common. The former -- the one you want -- is not at all common.
Now, that said, Zurn makes a pilot controlled pressure (or flow) control valve which can be configured in quite a variety of ways -- at least one of which will do what you need. I suggest you contact them directly (www.Zurn.com)Br. Jamie, osb
Building superintendent/caretaker, 7200 sq. ft. historic house museum with dependencies in New England0 -
"@ Jamie Hall"
What you need in that application is a valve which will open to maintain downstream pressure.
Hi Jamie!
well then ....... wouldn't a regular pressure reducing valve work then? (setting the PRV to a down stream psi to contribute the additional water flow)
Ref:
Street water pipe into building is 2" I.D @ 80 psi0 -
That may work. Worth a try -- as the fancy maintaining valves are definitely NOT cheap. Depends somewhat on how the downstream pressures vary with demand. It almost certainly would work if you could establish a really good correlation between the flow exceeding your 30 gpm maximum and the downstream pressure, and it is quite likely that the flow limiting valve will do that.
Interesting application...Br. Jamie, osb
Building superintendent/caretaker, 7200 sq. ft. historic house museum with dependencies in New England0 -
....... mmmmmm : (
..... looks like the regular PRV would also be contributing un-filtered water when lets say the flow thru the reactor tank is anywhere between the normal 1 and 30 gpm. : (0 -
@ "Jamie Hall"
Its a Template Assisted Crystallization® (TAC®) water filter system.
Atomic level templates on the surface of small specially treated
polymer spheres transform dissolved CaCO3 to a
crystalline form. The crystals are relatively insoluble,
effectively isolating the CaCO3 from the water chemistry
and anything the water contacts. This crystal transformation will de-scale everything, ie: all the feed pipes, solenoid valves, boilers, hot water tanks, tankless units, shower heads, etc ........ 24/7 including the existing scale build up already there.
The current commercial design of all the TAC units are sized up to meet the "peak demand" loads as well ...... they have to!, they have no way to hand off the infrequent peak demand load. This results in a lot more very expensive reactor tanks basically just sitting there most of the day!
My contention is to filter only the 90% of the normal flow rate and by-pass the infrequent 10% peak load.
This paradigm reduces the tank requirements to around 1/4 to 1/2.
0 -
....... mmmmmm : (
..... looks like the regular PRV would also be contributing un-filtered water when lets say the flow thru the reactor tank is anywhere between the normal 1 and 30 gpm. : (
Maybe. As I noted, it's a little complicated, since you really need to know what the pressure is downstream of the reactor under various operating conditions. If, for instance, the flow control valve and the demand interacted in such a way that the downstream pressure going through the reactor was always above a certain value, and only started really drooping when the flow control started restricting, you could probably get away with it.
The real question, I think, is whether the downstream pressure is some reliable function of flow.
I presume for the flow control valve you are using one of these: https://www.rcworst.com/Shared/content/mfr/eaton_corp/docs/dolevalve_specifications.pdf
They have a rather interesting property in that they have a well defined pressure drop across them at which they start restricting. This pressure drop could be transmitted to one of the Zurn pilot controlled valves which I mentioned earlier to control that valve. Adjustment would be a bit finicky, but could be done...Br. Jamie, osb
Building superintendent/caretaker, 7200 sq. ft. historic house museum with dependencies in New England0 -
@""Jamie Hall"
I presume for the flow control valve you are using one of these: https://www.rcworst.com/Shared/content/mfr/eaton_corp/docs/dolevalve_specifications.pdf
Yes! : )
I could do all the flow control with a PLC controller with flow/PSI sensors, but the "nature of the beast" doesn't required such high precision.
I'm hoping for a simple mechanical solution.0 -
Fair enough. How about this. What is the minimum pressure you need to maintain at the junction between the reactor and the bypass? Is this reasonably above the pressure which the flow control valve will drop the pressure at that point to? If so, you could use a simple pressure regulating valve on the bypass, set to that minimum pressure -- or slightly above, to allow for variations.
Suppose, for example, that you have say 60 psi going into the flow regulator, having lost 20 in the reactor -- and the regulator is dropping that to, say, 20 psi. Then your pressure reducing valve could be set for say 18 psi, and would start flowing to maintain that 18 psi. You would still be getting all the flow your reactor was capable of since it would be outputting a slightly higher pressure, and the makeup would come from the bypass.
As I say -- it would be a bit raggedy, but simple. But it all depends on what pressures you need -- or can tolerate -- under what flow conditions.Br. Jamie, osb
Building superintendent/caretaker, 7200 sq. ft. historic house museum with dependencies in New England0 -
@Jamie Hall
Your questions are over my head currently : (
(I'm just now reading up on the relationships between water pressure (psi), flow (gpm), pipe diameter and its lengths).
How they all interact at varying demands in practice is not yet clear to me.
Tidbits I kind of know about this systems environment:
Commercial 100 guest room motel (two Jaccuzi, two washers)
2" copper pipe into building @ 80 psi (max. flow capacity @12 ft/sec is 127 gpm .....??)
Thinking:
In the 100 guest rooms, 15 guests are currently using the shower, at a 2 gpm consumption rate (total 30 gpm flow rate demand).
These 15 open shower valves must equate to some definitive (known) pressure drop from the 80 psi street supply.
For simplicity, lets say the pressure drop per shower valve is 2 psi (total 30 psi)
If any additional shower valves are opened the Dole valve will NOT pass any additional flow capacity beyond its max. 30 gpm design.
All the open shower valves at that time will be flow reduced by this additional load demand.
At the known Dole valve pressure drop at 30 gpm .... I need to on an incremental basis add un-filtered water pipe pressure to the OUT feed piping.
....... do I understand this correctly?
0 -
...... now thinking:
If I install a 2" port sized standard pressure regulator paralleled to my reactor tank, set at 30 psi, it should now function as a high capacity "auto-fill valve" with a 127 gpm flow capacity.
think: The flow restricted reactor tank is actually keeping the 2" pressure regulator from any un-filtered water flow contribution until the OUT pressure drops below 30 gpm.
...... is this correct?
0 -
Good grief. Go big or go home! Pressure drop in a pipe is related to flow quantity. Roughly, the pressure drop per foot of pipe is a constant for a given pipe size and type times the square of the flow quantity. There really is no maximum velocity -- or flow -- in terms of the physics, but one tries to size the pipe so that the flow velocity stays not much over 10 feet per second. Hence your figure of 127 gpm at 12 feet per second as a design point.
But that's for a pipe. Elbows and such can be treated as so and so many feet of straight pipe for head loss -- pressure drop -- calculations. For valves the situation is somewhat different, and the pressure drop across a valve is related to the valve size and geometry (that's where the "CV" value for some valves -- it's the flow, in gallons per minute, which will have a 1 psi drop through the valve. Sort of. It's only good over a pretty limited range). Your flow restrictor is a valve -- of sorts -- but has a widely variable resistance to flow such that its pressure drop varies with flow in such a way as to hold the flow constant. Your reactor will also have a pressure drop in it -- and you'd have to consult the manufacturer's technical literature for that.
If those shower valves were in series -- one after the other rather than side by side -- the pressure drops would add -- but they aren't, and so while the flows will add (15 showers going at once at 2 gpm will take your 30 gpm) the pressure drops don't.
Now on the output side of all this, however, there is a certain minimum pressure which your motel can tolerate -- and in this particular application, I'm going to venture that it is the washers, and that they will want to see a minimum of 20 psi to operate properly. Their documentation will have the figure -- and it's worth checking.
The various plumbing codes have in them tables which will give you the anticipated flow rate for applications such as this, where there are multiple bathroom groups or other fixtures (like those Jacuzzis!). They don't just simply add -- over the years engineers have studied usage, and have figured out just how likely it is to have a certain number of bathroom groups out of a certain other number all flowing at once. I have no idea where my copy of the code is at the moment -- but your plumbing contractor will have that.
This will also, on the way, give you the probably maximum flow you can expect to see at that junction point.
And then the fun begins. Someone -- and I suggest that if you either have a very good plumber or better a mechanical engineer -- needs to look at the plans and figure out what the various likely flows and pressure drops are in various bits of the plumbing -- and from that, working back, what the minimum pressure required is at the point where your reactor and flow restrictor join youe bypass. Then you can also work forward from the static pressure (you quote 80 psi) at the building intake and the assorted piping and valves on the way to the reactor and through the reactor to the junction.
Hopefully the resulting pressure from that calculation will be greater than the resulting pressure calculated from going backwards from the fixtures (if it's less, someone needs to redesign the plumbing...). If al goes well, though, you will end up with a pressure range at that junction. The pressure through the reactor train will, you hope, be the maximum that the reactor train, including the flow restrictor, will provide. The building calculation will give you the minimum. The pressure regulating valve in the bypass would be set for somewhere in that range.
Now how does this work? At low flows -- less than 30 gpm -- all the flow will go through the reactor and the pressure at the junction will be some probably fairly high number. Flow from there will go to the various using devices, which will have a higher pressure than they need -- but that's not a problem, as most of them have flow restrictors themselves, and the pressure drop through the fixture will handle the rest. As the flow demand from the users increases, at some point the flow restrictor will kick in, and any further pressure drop (as the flow demand increases) will happen in the flow restrictor -- until the pressure at the junction drops to the setting of the pressure regulating valve, at which point it will start to open and provide the additional flow required to hold that pressure.
Clear as mud? It's a lot easier to envision than it is to describe...Br. Jamie, osb
Building superintendent/caretaker, 7200 sq. ft. historic house museum with dependencies in New England0 -
"@Jamie Hall"
Got all that! Thank-you! : )
Suppose, for example, that you have say 60 psi going into the flow regulator, having lost 20 in the reactor
I don't know the the pressure drop across my reactor tank as of yet (I will be constructing my 1st prototype in about three weeks)
Commercially available reactor tanks have a large (12" to 24") resin bed tank diameters as compared to its small 2" IN/OUT ports.
These tanks also require an internal tank distribution manifold to evenly expose the water flow to the reactive poly resin filter beads.
Two special 2" O.D. stainless steel wire mesh (.2 mm) screens keeps the resin beads within the tank (one on the IN port and one on the OUT port).
....... all three of the above equate to the total FIXED reactor pressure drop introduced to the water supply line.
I by design, have eliminated the first two major restrictions altogether by limiting the reactor tank size to 4" dia x 5' tall (so, instead of lets say 2 large tanks .... I need 10 small ones on an exterior pipe manifold.
The 2" wire mesh screens (where all the total water system flow must pass) presents a large pressure drop to the system as well.
With multiple small screened tanks ...... I've decreased this tank pressure drop by at least a factor of 20 because of the very large increase in total screen flow area.
(think: of that 24" diameter tank having to pass all its rated flow thru just its 2" diameter (2mm mesh grid) resin screen. Now think: same 24" tank with a 24" resin screen to pass its flow!)
I expect my tanks FIXED pressure drop to be only 1/4 of the commercial versions.
The "fluidized" resin beads themselves offer very little flow restriction and can be ignored.
0 -
Interesting to see how the pressure drop varies with flow -- it will. Let me know.
Keeping the flow even among the various tanks may take some creative piping. In fact, it may be almost impossible, even with large manifolds piped in a reverse return configuration. Is that 30 gpm restriction on flow the total for the 10 tanks? I know the dang things are expensive, but if the restriction is actually 3 gpm per tank, I'd be strongly inclined to place an appropriate flow restrictor on each tank outlet, rather than manifolding them together and then restricting the total. Otherwise you might get away with a very large diameter manifold on both inlet and outlet, piped reverse return (that is to say at let's say the left end of the manifold you feed the tanks in order from one to 10, with the main inlet on the left -- but on the back side the manifold has the main outlet on the right hand end, with tank 10 being closest to the outlet. I'd still be concerned, though, as I wouldn't want to guarantee that the flow match would be any better than 20 percent -- say plus or minus half a gpm on a 3 gpm flow -- and might be much greater at lower flows.
Also -- a filter before the tanks is going to be required. It need not be a really fine filter, but must be fine enough so that anything that gets through it -- anything -- can easily pass the stainless steel screens in the tanks.Br. Jamie, osb
Building superintendent/caretaker, 7200 sq. ft. historic house museum with dependencies in New England0 -
@Jamie Hall
Is that 30 gpm restriction on flow the total for the 10 tanks?
The flow and pressure numbers are just example numbers ..... I can make the total "bundled" tanks equate to max. street flow/pressure if desired.
yes! .... only one dole valve and one pressure reducing valve for the entire filter "bundled tank" system.0 -
"@Jamie Hall"
Also -- a filter before the tanks is going to be required. It need not be a really fine filter, but must be fine enough so that anything that gets through it
I'll have an activated charcoal filter before the TAC reactor.
(Here again, I'm pondering instead of a single large carbon filled tank with only one 2" IN/OUT port, to disperse the activated carbon within each bottom of the smaller reactor tanks , ..... a combo charcoal + TAC resin filter).0 -
The numbers aren't that important. What is is that with multiple tanks -- even two, never mind ten -- the odds on your getting flow balanced between them are pretty poor.Br. Jamie, osb
Building superintendent/caretaker, 7200 sq. ft. historic house museum with dependencies in New England0 -
"@ Jamie Hall"
The numbers aren't that important. What is is that with multiple tanks -- even two, never mind ten -- the odds on your getting flow balanced between them are pretty poor.
I've addressed that concern thru absolute symmetry of the manifolds construction ...... every connector and joining pipe nipple are identical in length (reversed piped IN/OUT).
The resin beads , un-like a salt brine system that requires a 45 secs exposure to the resin beads ..... the TAC resin beads only require 3 to 5 seconds! This allows for a much higher tolerance to any mismatch flows within the tanks required 200% "freeboard" area.
I don't think a reversed balanced (flow error canceling) piped tank will be significant here.
By design, after 8 years of the resins expiration, the entire multiple reactor tanks and pipe manifold is disposed of as one unit!0 -
Think:
Rem: .... each of my tanks are only carrying 1/10th the total flow rate thru them! (in a ten tank bundle)0 -
This is a pic of a High/Low flow water mixing valve assembly.
It uses a small capacity mixer valve along with a large capacity mixing valve.
Normally seen in commercial applications (ie: motels).
In a low flow demand, the small mixer is used for lets say 1 to 30 gpm flow demands.
They use the smaller mixer for this because the large mixer cant mix properly at such low flow rates.
Once the flow demands greater than 30 gpm the large pressure regulator (on left side of pic) allows the large mixer valve to take over the larger flow demands.
0 -
Every tank has a 2" O.D. stainless steel wire mesh screen filter
Tanks are reversed balanced piped.
The reverse-return system is nearly self-balancing because the hydraulic distance traveled by the fluid is close to the same regardless of which tank a given volume of fluid flows through; or said another way, reverse-return creates approximately equal hydraulic resistance through each flow path.
0
Categories
- All Categories
- 86.9K THE MAIN WALL
- 3.2K A-C, Heat Pumps & Refrigeration
- 57 Biomass
- 425 Carbon Monoxide Awareness
- 109 Chimneys & Flues
- 2.1K Domestic Hot Water
- 5.6K Gas Heating
- 105 Geothermal
- 160 Indoor-Air Quality
- 3.6K Oil Heating
- 70 Pipe Deterioration
- 967 Plumbing
- 6.3K Radiant Heating
- 385 Solar
- 15.3K Strictly Steam
- 3.4K Thermostats and Controls
- 54 Water Quality
- 44 Industry Classes
- 47 Job Opportunities
- 18 Recall Announcements