Welcome! Here are the website rules, as well as some tips for using this forum.
Need to contact us? Visit https://heatinghelp.com/contact-us/.
Click here to Find a Contractor in your area.
Reverse return with underfloor heating and supply air coil in parallel

Lasse
Member Posts: 4
Hello,
I have a customer that is having underfloor heating system and a supply air coil parallel. No balancing valves anywhere.
Few problems exists. When system is running from buffer tank, it does not get heating energy into the system. Only what is reserved in floor and buffer tank.
This is because system is serving two masters. Heating the floor and making hot tap water.
Supply air coil is the nearest from pump and underfloor heating manifold is further. Problem
1.) Is that the most of circulation goes through supply air coil and it cools down pretty quick when outside temperature is -27°C (-16.6°F).
2.) Pressure drop of the whole system is a bit too low. Below 10 kPa.
I am thinking of three options:
1.) Reverse returning the system. This is the easiest and low cost solution.
There are zone valves in the system, not in all branches. So underfloor manifold is not a constant flow system. Could this force circulation from floor and balance the system?
2.) Reverse return and a balancing valve after coil that is having “low” pressure drop.
This gives additional balancing help and makes flow control through coil easier.
3.) Reverse return, a balancing valve after coil and a balancing valve before under floor manifold. This gives UFH branch a bit more pressure drop.
I am not a battle hardened hydronics dude. So help is really appreciated.
Does reverse return give head aches to underfloor heating?
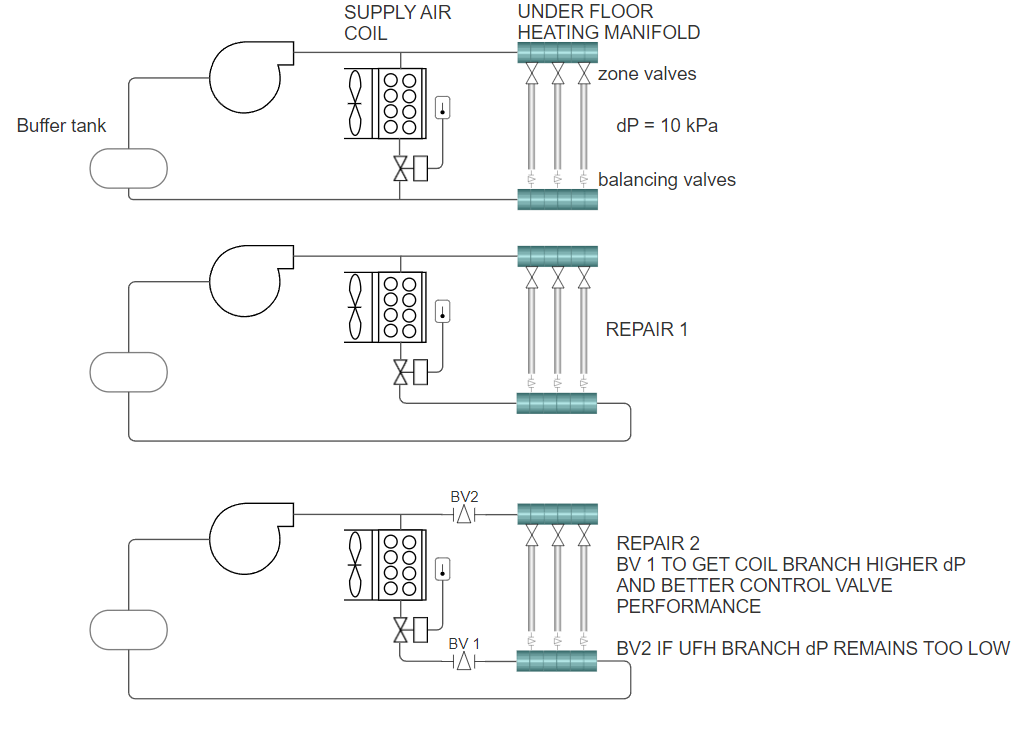
I have a customer that is having underfloor heating system and a supply air coil parallel. No balancing valves anywhere.
Few problems exists. When system is running from buffer tank, it does not get heating energy into the system. Only what is reserved in floor and buffer tank.
This is because system is serving two masters. Heating the floor and making hot tap water.
Supply air coil is the nearest from pump and underfloor heating manifold is further. Problem
1.) Is that the most of circulation goes through supply air coil and it cools down pretty quick when outside temperature is -27°C (-16.6°F).
2.) Pressure drop of the whole system is a bit too low. Below 10 kPa.
I am thinking of three options:
1.) Reverse returning the system. This is the easiest and low cost solution.
There are zone valves in the system, not in all branches. So underfloor manifold is not a constant flow system. Could this force circulation from floor and balance the system?
2.) Reverse return and a balancing valve after coil that is having “low” pressure drop.
This gives additional balancing help and makes flow control through coil easier.
3.) Reverse return, a balancing valve after coil and a balancing valve before under floor manifold. This gives UFH branch a bit more pressure drop.
I am not a battle hardened hydronics dude. So help is really appreciated.
Does reverse return give head aches to underfloor heating?
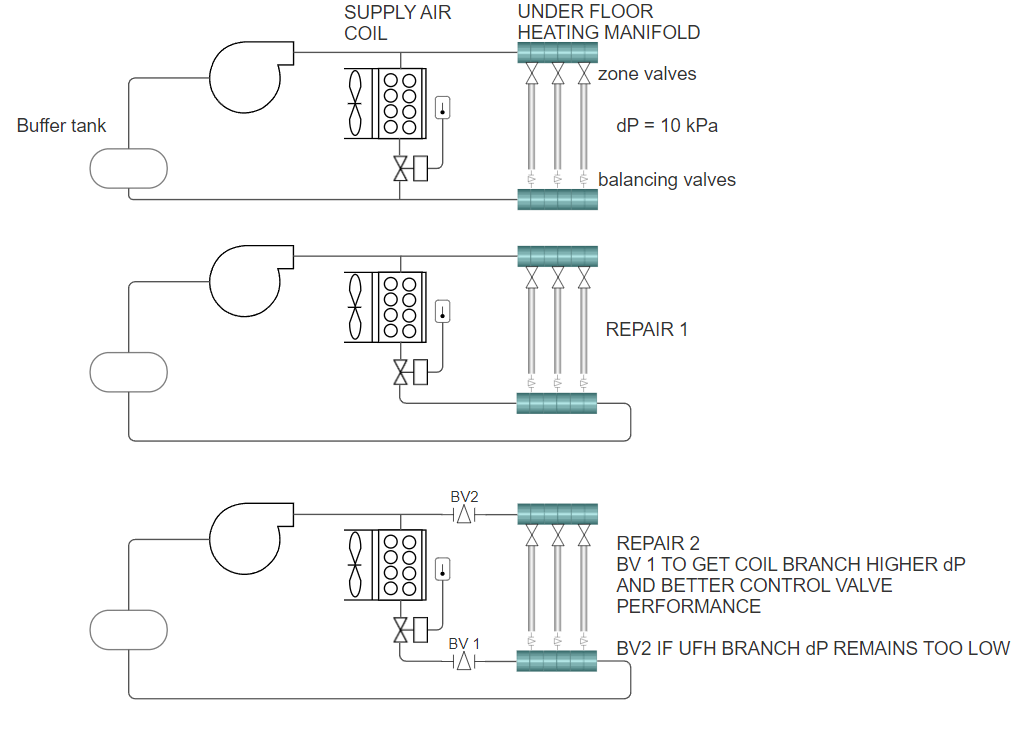
0
Comments
-
It seems to me you are actually talking about three end uses of the heat? The underfloor heating, the fan coil, and domestic hot water?
You have bigger problems than reverse return will help, never mind fix.
The biggest one is that you have three very different heating loads.
Let's take the first one first. Underfloor heating. That load will need a maximum water temperature of around 50 Celsius and ideally should be flowing at all times. Again ideally, the actual water temperature would be controlled by a mixing valve controlled by an outdoor reset, but you can also get adequate, if not really great results, with a floor or space thermostat and running a constant temperature of 50 supplied by a mixing valve but turning the pump for that use on and off. And yes, you need a separate pump for that use. You must NOT use any reset on a floor radiant system.
The second use is the fan coil. In general, to provide usable heat, they require a significantly higher water temperature -- typically between 60 and 80 Celsius. There are a number of ways to control fan coils, but often the most satisfactory is to control a pump or zone valve with a space thermostat, and the fan on the fan coil with an aquastat on the supply line so that it doesn't blow cold or cool air.
The third use, if I read correctly, would be the domestic hot water. Is that supplied by an indirect water heater? If so, that also needs water of at least 60 Celsius (the tank temperature should not be allowed to go below that, but the domestic output needs to be mixed down with cold supply water to about 43, to avoid scalding).
So to make the story short -- you are going to need at least one more pump and a couple of zone valves -- and best practice would be to pipe your boiler as an independent loop with its own controls and pump.Br. Jamie, osb
Building superintendent/caretaker, 7200 sq. ft. historic house museum with dependencies in New England0 -
The AH and radiant run together, on the same SWT?
Seems two or three separate zones would be better?Bob "hot rod" Rohr
trainer for Caleffi NA
Living the hydronic dream0 -
Here is a schema of the supplying system. It is an exhaust air heat pump that takes care of heating, supply air and hot tap water. Problem with this is that when supply air coil and UFH are not in balance the coil is in freezing risk.
Balancing and adequate pressure drop in UFH should have been done when commissioning the system. Instead balancing valves in manifold were all wide open. Coil is finned copper coil. 6 times 4 meters of copper between manifolds.
So it does not produce a lot of pressure drop when outside temperature is -27°C and control valve in series is wide open.
Supply temperature @ outside-27°C is around 38°C. Usually it is limited to 40°C.
When this condition is at hand and machine needs to switch from heating to hot water production and change over valves start turning, pressure drops below 2kPa, because valves are T-joins for a second. That pressure difference is not enough to push water fast enough through coil. Air flow through coil is 80 liters per second.
I am trying to fix the situation by balancing flows between UFH and SA coil and rising up the pressure difference level. Thought that reverse return in UFH manifold would force return water flow from both, UFH and coil. Thus improving balance.
I think that now the flow finds the easiest path through coil. Also balancing valve after coil and before UFH have to be installed.
Straight forward would be balancing valve in both, UFH and coil return.
But could there be extra benefit from reverse return?
It is easy to do and does not cost much hence coil and manifold are at 2 meter distance.
0 -
I don't see this as a pressure or flow problem. You have a temperature problem. Fundamentally, you cannot get satisfactory results from the fan coil unit and the underfloor heat with the same water temperature going to both. Changing flow volume is not going to alter that. Nor will the buffer tank, unless the buffer tank is run at a high enough temperature to satisfy the fan coil -- in which case you need a separate cirrcuit for the underfloor heat with a suitable mixing valve and circuit pump.
There is some doubt in my mind, as well, as to whether the heat pump can deliver the water temperature required for the fan coil or the domestic hot water, although perhaps the electric boost (resistance?) is to perform that function. What is the maximum output temperature from the heat pump?
Br. Jamie, osb
Building superintendent/caretaker, 7200 sq. ft. historic house museum with dependencies in New England0 -
Heat pump can deliver ~4kW. Required power for the house is 8kW. In hot water production heat pump gets tank temperarure to ~52°C in normal hot water demand. No electric heater needed during that.
Exhaust air coil needs to be defrosted hence evaporating temperature goes below -20°C. During that and when demand is high enough for heat pump to satisfy, electric heater after PUMP 1 is taken to production.
I am pretty sure that this is a flow and pressure problem.
This is what I think happened when the coil got destroyed.
Outside temperature was -27°C. All UFH manifold zone valves were open. Then fireplace was started. All zones (but few) were closed. UFH manifold flow reduced and manifold dP got up. Coil got the easiest path for water to flow and no mixing with water from UFH happened.
Outside air cooled the water in buffer tank (25 liters) quickly.
Also when a circulator pump is delivering flow to 10 kPa and less, it’s NPSH required starts to rise up rapidly.
And this is the reason I would like to get pressure level a bit higher with balancing valves after coil and before UFH manifold.
For maximizing the flow from UFH manifold I was thinking if I could benefit from reverse return and could it cause any harm.0 -
Here is a piping design that may help. Since your floor needs lower water temperature It can be its own separate system off of the buffer tank. The other systems that need higher temperature will use the existing design, assuming that it works for the higher temperature needs.
Edward Young Retired
After you make that expensive repair and you still have the same problem, What will you check next?
0 -
This is definitely one thing to consider.
Trying to avoid extra pump, mixing valve and it's control versus two balancing valves and minor modifications to piping.
Should the blue pipe in picture go to COV2 vertical branch so that water goes to condenser instead of returning straight to tank without being heated?0 -
It could go the way. But since it is the lower temperature zone, I thought it would work without going that direction. That makes the Radiant floor a simpler project. That would also make the radiant floor zone dependent on at least one of the other zones calling for heat at some point. If you want to set it up as an independent zone that will cause the heating equipment(compressor or resistance) to operate regardless of a separate call for heat, then by all means connect return to COV2Lasse said:This is definitely one thing to consider.
Trying to avoid extra pump, mixing valve and it's control versus two balancing valves and minor modifications to piping.
Should the blue pipe in picture go to COV2 vertical branch so that water goes to condenser instead of returning straight to tank without being heated?
Edward Young Retired
After you make that expensive repair and you still have the same problem, What will you check next?
0 -
Trying to get back to a basic understanding of this system here so I can think about it some more.
As I understand it, you have some sort of forced air system in the building, or rather, perhaps, two of them.
System 1 has a fan coil unit powered by your heat source, and supplies space heating (perhaps in the makeup air to the building?).
System 2 has another fan assisted coil, but this one is actually the evaporator side of a heat pump system (this is, I presume the coil which freezes up?) and is located in the exhaust air flow from the building.
Then your primary heat source is a heat pump. The evaporator side is the coil mentioned as oart of system 2. The condensor side is the heat exchanger labelled as C1 in your diagram, which transfers heat to a circulating hot water system.
The circulating hot water powers three outputs: a domestic hot water tank, a radiant floor, and the fan coil which is part of System 1 above.
Is that a reasonable functional description of the system as installed?
A couple of other things. It is slightly unclear as to what the maximum temperature hot water the heat pump and heat exchanger combination can achieve. You mention that it can get the domestic hot water up to 52, (which is not hot enough for safe hot water storage), but in another place you mention that it is limited to 40. What is it, actually? Also, you mention that it has a power capability of 4 KW, but that the building load can be up to 8 KW. What other power source or sources do you have available for that full building load?
You mention that at least one of the problems you are trying to solve is that the evaporator (low temp) side of the heat pump coil freezes up and needs to be defrosted from time to time. That is completely normal and to be expected. More to the point, there is no way to prevent that.
OK. Is this a reasonable description of the system and its basic operation? Actually, I hope not, as if it is there is a fundamental flaw (a violation of the second law of thermodynamics) which no fiddling with pipes and pumps and valves and controls is going to fix. But let's cross that bridge when we get to it.Br. Jamie, osb
Building superintendent/caretaker, 7200 sq. ft. historic house museum with dependencies in New England0
Categories
- All Categories
- 87.1K THE MAIN WALL
- 3.2K A-C, Heat Pumps & Refrigeration
- 58 Biomass
- 427 Carbon Monoxide Awareness
- 113 Chimneys & Flues
- 2.1K Domestic Hot Water
- 5.7K Gas Heating
- 110 Geothermal
- 161 Indoor-Air Quality
- 3.6K Oil Heating
- 70 Pipe Deterioration
- 997 Plumbing
- 6.3K Radiant Heating
- 391 Solar
- 15.4K Strictly Steam
- 3.4K Thermostats and Controls
- 55 Water Quality
- 44 Industry Classes
- 48 Job Opportunities
- 18 Recall Announcements