Welcome! Here are the website rules, as well as some tips for using this forum.
Need to contact us? Visit https://heatinghelp.com/contact-us/.
Click here to Find a Contractor in your area.
Radiant: Between Joist - Are my Joists and subfloors drying out and twisting/slight movement?
Options

cloudd
Member Posts: 49
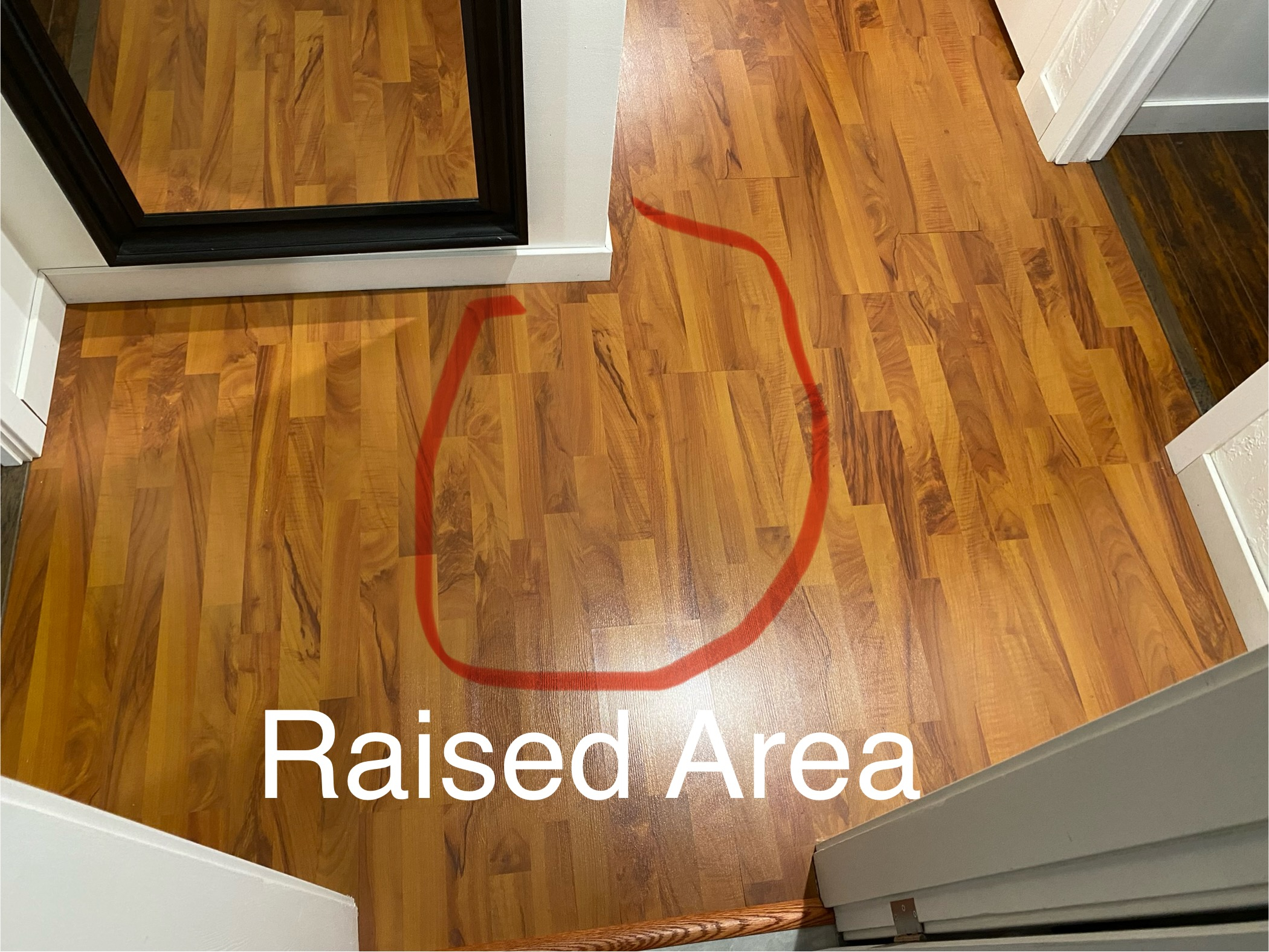
My house was built in 1970 so I think it is good to say it has settled.
Problem:
At one end of my house I have a crack that appeared on my wall (drywall) in the past few weeks. Could be a coincidence.
At the other end of my house in the hall I started to notice the floor has risen possibly risen 3/8" over 3' to 3-1/2' at the end of my hall by the support wall.
*I checked to see if my floors are level around this area of the main floor of the house and they appear pretty level, even really close to it. Roughly 3' away from it the slightly raised area at the end of the hall.*
*I say possibly because the end of the hall may not have been 100% level before. I did not measure the height difference before I turned the radiant system on, but the floor is noticeably higher within the last 1-1/2 months and is causing it to squeak where is has risen.*
I have been running this system for 4 Months now without any heating problems. This is the first winter using it.
Installation:
-Joists are all Douglas fir
-The shiplap 3/4" subfloor might be douglas fir as well
-Below subfloor between joists w/ Uponor aluminum plates
-Water temperature (130°F Supply Oct, Nov, Dec, Feb, Now) , (140°F Supply Jan)
-I have a relatively thick subfloor (3/4 shiplap, 5/8 plywood, foam layer, 12mm laminate)
-R22 Rockwool below the radiant pushing the heat up through the subfloor/floor
My floors do not appear really hot anywhere. I'd say sometimes the odd warm where the manifold is below ( that's not anywhere near the raised area) and other days not truly noticeable on the feet at all. I keep the rooms between 67-69F. I do not have any floor temperature sensors.
Here is a picture of how thick my flooring is that the radiant is below.
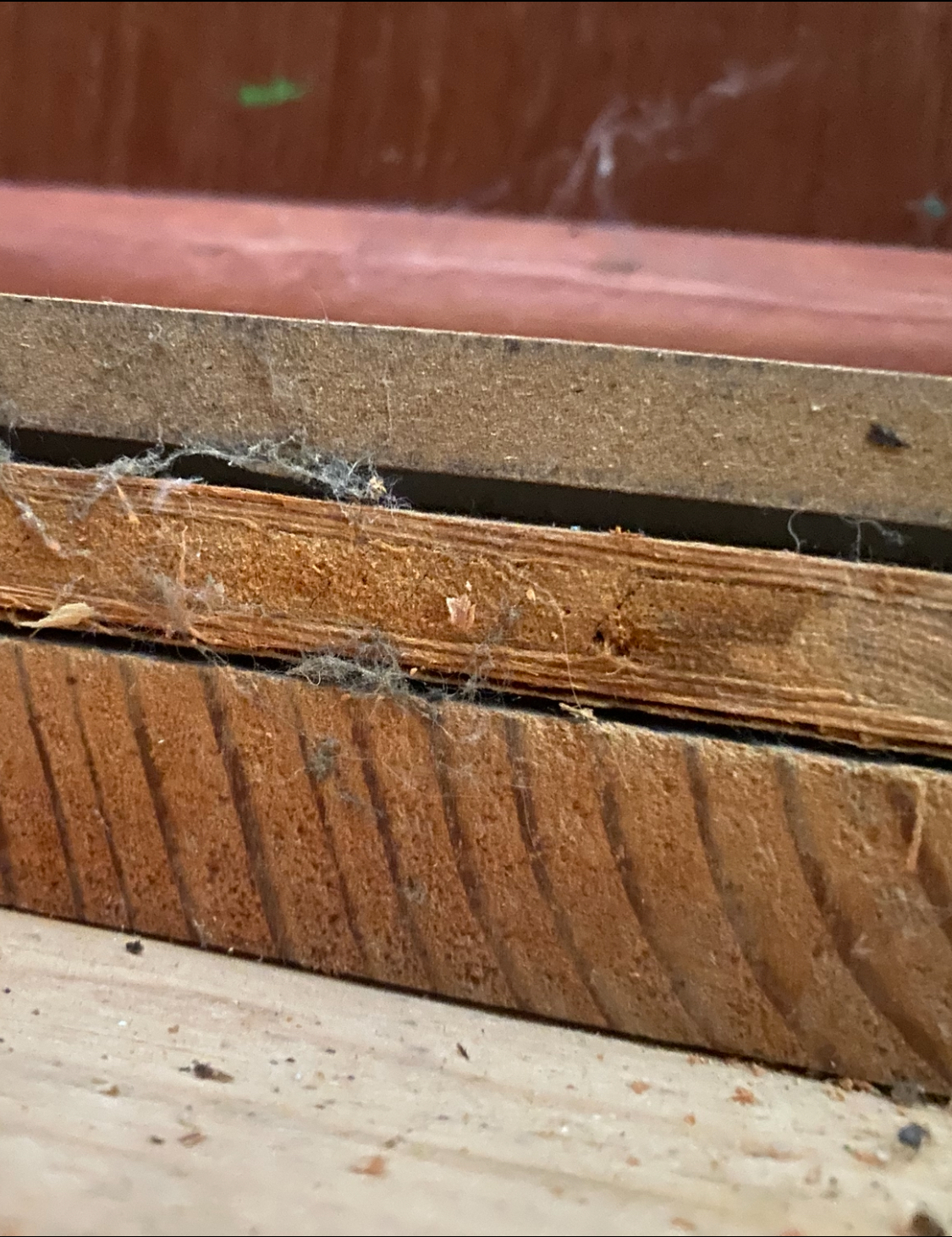
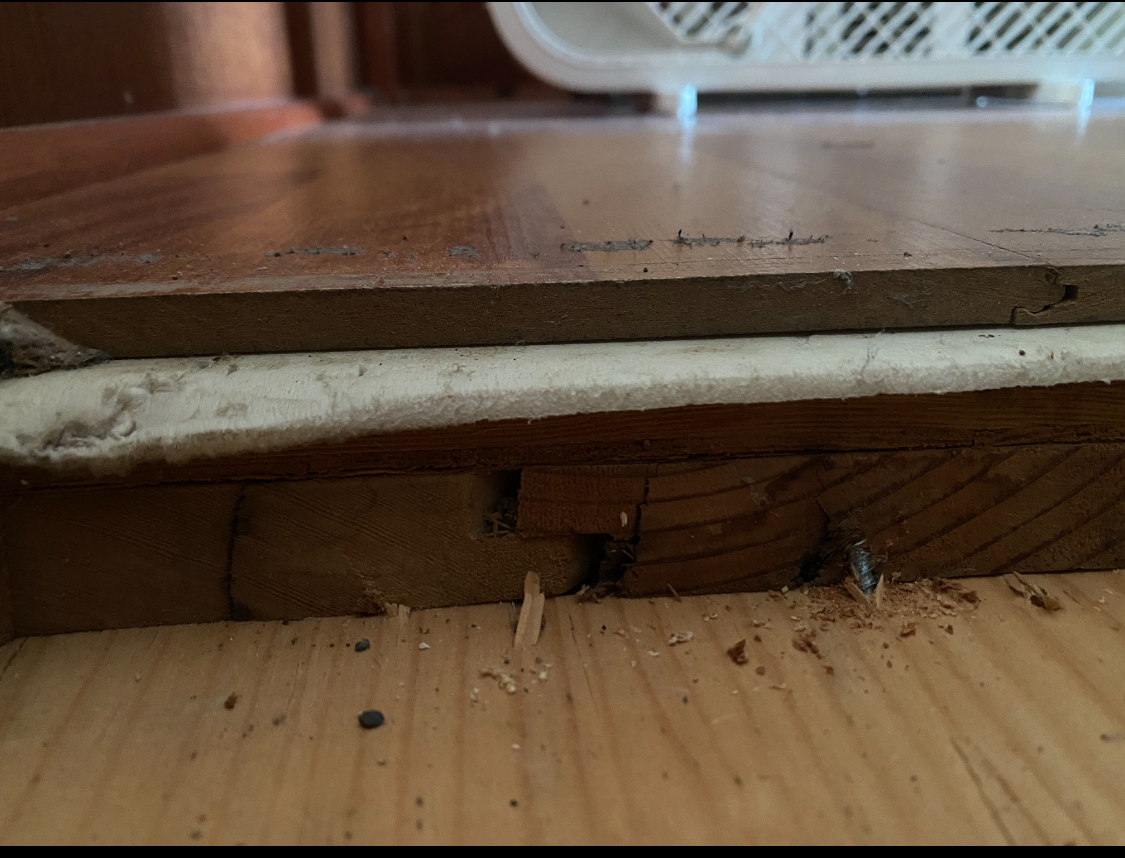
Could this be caused by shiplap subfloor and plywood drying out/twisting/warping in the one area of my hall causing the floor to raise slightly? Does this happen sometimes?
0
Comments
-
Radiant & wood is tricky. If this is just a recent phenomenon, it is likely the Radiant tubing is causing some realignment. What kind of temps through the tubing? Mas Dog 🐕0
-
It is the humidity change that can cause wood to move. Any way to measure or adjust the humidity
Always use the lowest swt to get adequate heat outputBob "hot rod" Rohr
trainer for Caleffi NA
Living the hydronic dream0 -
I'll go a little further out on the limb that @Mad Dog_2 is sawing away on, and say that almost certainly with those water temperatures the radiant is drying the wood subfloor in some areas more than it is in others -- and with modern wood (that subfloor looks more like southern pine plantation grown than douglas fir, but it doesn't really matter) you are going to get uneven warping and shrinkage. It may even out with time if you can keep the water temperature as low as possible and as constant as possible, depending on the moisture content of the wood when the floor was laid. May not, too. I might add that the forces involved are very large, and no reasonable amount of fastening is going to help.
I doubt that it is a problem with the joists -- they don't get hot enough -- but I'd be a bit concerned on other grounds about the dry wall crack..Br. Jamie, osb
Building superintendent/caretaker, 7200 sq. ft. historic house museum with dependencies in New England1 -
New Information:
I thought of something thismorning that may be the cause that I forgot about. Specifically in the wall directly where the floor is raising There was a leak in my chimney flashing that leaked into my attic > eventually the water made its way down that wall. It must have made its way to the bottom of the wall and into the subfloor. The radiant must have dried it up causing the plywood underlay and possibly the laminate to raise/warp. The laminate looks fine on the top but perhaps the plywood is warping or both. It seems a little ridiculous for the radiant to dry the wood out that much in and older house that has been heated and lived in for that long (1970 house).
I am going have to slide the floor a part and investigate more.2 -
This company has done a lot of testing with wood over radiant. typically winter humidity os lower and if anything you see shrinkage. certainly water would cause the floor to swell and pop up
https://launstein.wixsite.com/launsteinhardwoods/radiant-heatBob "hot rod" Rohr
trainer for Caleffi NA
Living the hydronic dream1 -
Well now. Yes, if water got into that plywood, it's going to swell and delmainate, unless it was marine grade which is unlikely... And it isn't shrinkage of the subfloor you need to think about it's warpage. Very different.Br. Jamie, osb
Building superintendent/caretaker, 7200 sq. ft. historic house museum with dependencies in New England0 -
when they laid the subfloor did they leave room for expansion? If it can't expand horizontally it will bow0
-
This is not radiant related anymore. Thank for the suggestions
(((((
I removed the vinyl flooring and foam pad. The plywood subfloor has taken on water from a leak that came from my roof chimney flashing in December > through the attic> down a wall and under the vinyl subfloor and foam pad. Trapping the water in the plywood subfloor because the radiant kept warming the water from below. Probably the water has been forced into the plywood because it had nowhere else to go. Up was the foam pad layer and down was the radiant heat between joist on the bottom of the shiplap then R22 rock wool and 2 layers of 5/8" drywall in the basement. The radiant have been on the entire time drying it from below. The plywood subfloor expanded on the seam where 2 pieces meet probably tongue and groove. It happens to be directly above my support wall which is causing all of the pressure from the expanded plywood seam to push up. My floors seem to be completely level everywhere eles / anywhere 3 feet away from this plywood seams. The board looks soaked in the picture but it seems just cooler to the touch along the high area. Perhaps some of this dark color is water stains?
OH JOY!
I have a dehumidifier and a fan blowing on it now. I will have to open the wall cavity that it came down and check for the beginning of any mould in the wall. If so I'll have to cut out and replace the drywall.
Hopefully the plywood drys out and shrinks back down to normal height!
If it does not I'll have to either do one of the following:
1. replace the plywood underlay and lay down a new layer with either 7/8" screws or nails
*I only have 1" of thickness before I am though the plywood & ship lap subfloor and then I'd hit a radiant aluminum joist plate or possibly radiant pex.*
2. Sand the warped underlay plywood down as flat as I can with a belt sander and re-lay my foam pad and vinyl flooring.
*This might be the less risky option if it comes down to it*
Does anyone know how long this might take to dry out to as good as it's going to get? 1 Week? 1 Month? I mean considering there is radiant below the subfloor running at 130F supply (not sure if this is the beginning or the end of the loop) and the dehumidifier/fan running. The humidity in the the hall area was just under 50 before I turned the dehumidifier on. I have never had to do this before.0 -
Give it a day or two before you pull out the power tools😏
Is you boiler on an outdoor reset control. Unless you have some high load rooms, you should not need 130 SWT all heating season.Bob "hot rod" Rohr
trainer for Caleffi NA
Living the hydronic dream0 -
Jamie Hall said:
....the forces involved are very large, and no reasonable amount of fastening is going to help.
Agree. 15+ years ago the prior owner's tenant part-flooded the place. Even after years of drying, it was a trip hazard. I used a very UN-reasonable number of extra-huge structural fasteners into strongbacks between the joists. Still a lump.ccloudd said:....water from a leak that came from my roof chimney flashing
0 -
I do not have an outdoor reset control (I could get one).hot_rod said:Give it a day or two before you pull out the power tools😏
Is you boiler on an outdoor reset control. Unless you have some high load rooms, you should not need 130 SWT all heating season.
I am using a Bosch Singular 5200 Combi which has an option for an outdoor reset control. I have tried setting the "Radiant Supply Temp" below 130F (120F, 112F...) and the radiant worked fine but then I experienced a problem with my DHW not reaching 140F (DHW has an independent Temperature setting in the combi and it was and is set to 140F). Once I set my Radiant Supply temperature below 130 it seems to have an impact on my DHW temperature reach 140F because the Bosch 5200 struggles to reach 140F for the DHW. It starting acting up (cycles, relights or something) and only is able to get the heat up to 120F-130F (DHW) it never gets up to 140F.
Based on what is going on if the radiant supply is set to 120 or under it acts like it is connected to the DHW temperature setting or is impacting it. This is wrong and should not be happening! It seems like the Bosch 5200 combi software/firmware has a fault in it or I had it configured wrong (there are only 2 independent temp settings "DHW Temperature" and "Radiant Supply Temp". I am puzzled and have read the manual thoroughly. I am pretty sure I had configured it correctly. It did not seem that hard to configure.
I did not call Bosch and ask them about this because it functioned fine at 130F. This was my first winter running the system at (130F most months -140F (1 month)) worked great. I think I should call Bosch support now and find out why I was experiencing this problem.
I do have a large living room 15'-30' and 12' cathedral ceiling (4 loops) one side of the room 30' long is all windows to the ceiling. It usually does not drip below -4C in the winter for 1-2 weeks. But it hit -9C for 4 days this winter...Condensation on the inside of my aluminum 2 pane windows was a big problem when it dropped below -2C. I had to whip the water up in the window sills (this was only for 2 weeks). I might add a baseboard to use in emergencies like this to keep condensation down for next year.
What temperature should I be ably to go down to on 7C days for supply do you think?
0 -
Your heating temperature setting has nothing to do with DHW mode. When in DHW the boiler should ramp up to 180 to give you adequate output.
If you are comfortable, go into the control settings to see how it is set up. Download a manual if you don’t have one. Probably find You Tube videos on how to adjust the control, maybe even at the Bosch website.
Typically the outdoor sensor ships with most all boilers now a days.
Reducing the supply temperature will also reduce the fuel costs a bit, prevent over heating and allow the system to run longer cycles. Instead of on and off cycling. Worth looking into.Bob "hot rod" Rohr
trainer for Caleffi NA
Living the hydronic dream0 -
Bad news. Once plywood has been soaked -- as yours has -- and started to delaminate -- as yours has -- it's not going to come back to the original thickness (not true of marine plywood -- which is why the stuff is kind of pricey). I'd suggest sanding...Br. Jamie, osb
Building superintendent/caretaker, 7200 sq. ft. historic house museum with dependencies in New England0 -
It depends on the type of sheathing plywood. Typically it is CDX which is and exterior glue and does get wet during new construction.
True underlayment plywood also has some water resistance.If it is plain 1/4” AC plywood as underlayment, all bets are off.
I suppose it depends on how wet and for how long.
You will know when it dries🧐Bob "hot rod" Rohr
trainer for Caleffi NA
Living the hydronic dream0
Categories
- All Categories
- 87.1K THE MAIN WALL
- 3.2K A-C, Heat Pumps & Refrigeration
- 58 Biomass
- 427 Carbon Monoxide Awareness
- 113 Chimneys & Flues
- 2.1K Domestic Hot Water
- 5.7K Gas Heating
- 110 Geothermal
- 161 Indoor-Air Quality
- 3.6K Oil Heating
- 70 Pipe Deterioration
- 997 Plumbing
- 6.3K Radiant Heating
- 391 Solar
- 15.4K Strictly Steam
- 3.4K Thermostats and Controls
- 55 Water Quality
- 44 Industry Classes
- 48 Job Opportunities
- 18 Recall Announcements