PLC cold water "Rejection" mixer?
I'm pondering a solution to where I have two Rinnai CU199iN DUO storage tanks balanced piped together and one of the units shuts down (system detected fault).
This scenario immediately creates in effect an escalating and effective cold water mix into my working hot water supply piping as the failed heating has stopped, but its balanced water flow contribution has not.
I can easily program a PLC (Programable Logic Controller) to act as a cold water "rejection" mixer at the top of the storage tanks.
If at the time of failure, both tanks were up to set temperature, this rejection mixer would mix both tanks to hot out supply line.
As the failed tank starts to offer less and less of its set temperature, the rejection mixer starts to back off its allowed contribution from the failed tank.
This would eliminate waking up to a totally cold water system as the working side still remains heat producing.
..... should this be a competent solution, I would then venture into designing a PLC "cross mixer" by balance piping the side tank ports (hot & cold) so the working unit will start recovery of the non-working tank.
..... your thoughts on this would be appreciated!
Thanks!
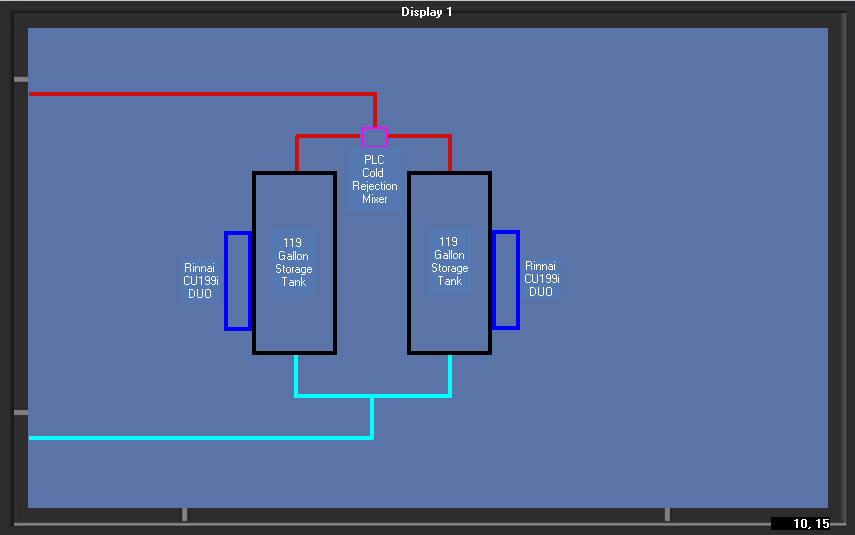
Comments
-
It seems like the main issue here is that your water heaters keep having system faults and breaking. That being said, what about a zone valve coming off each tank that is controlled by a temp probe in the tank? If the water gets too cold, it shuts off.0
-
Not a bad idea. But -- it is a bandaid. Your basic system is fine, except that for some reason your two heaters aren't always working. Might it not be much better to actually fix the problem than to mask it?Br. Jamie, osb
Building superintendent/caretaker, 7200 sq. ft. historic house museum with dependencies in New England0 -
It seems like the main issue here is that your water heaters keep having system faults and breaking.
No ....... not at all! : )
It just that these water heaters are in a more mission critical environment (80 guest room motel) and I wasn't happy with its terrible failure mode of operation when we do eventually get one.
This sparked my interest to design a PLC based critical failure/soft landing and recovery paradigm.
Your suggestion of using just zone valves is, well .... very "dinosauric" and limited in function : (
These are "state of the art" CPU based ultra efficient machines extracting every ounce of heat possible, wasting very little and transferring this generated heat to the water.
I wish to use this same level of technology in its critical failure mode for its recovery operation.
Its operational methodology may include:
current flow demand.
projected flow demand.
outdoor temperature.
number of guests in rooms.
Invoke max. system capable set temperatures (185 degrees F) to the down stream normal mixer (120 degrees F) to guest rooms
etc.
With this data the PLC would then allocate the best use of its available resources to mitigate the failure's effects.0 -
Not a bad idea. But -- it is a bandaid. Your basic system is fine, except that for some reason your two heaters aren't always working. Might it not be much better to actually fix the problem than to mask it?
You do understand this is just meant to be a hold over until service company arrives onsite? (that may be a few days sometimes over the weekend)
Its basically to minimize the failures impact on the paying guests.
0 -
The fundamental problem which I see with your scheme -- which will work -- is that you lose half of your storage capacity when one of the tankless heaters fails. Which leads me to wonder about the overall control and piping arrangements.
As I understand your arrangement at present, you have two tankless water heaters which feed individual large storage tanks.
First question: are these indirect type storage tanks, where the heater cicrculates water through a heat exchanger in the tank, thus heating the stored water, or is the tank water itself circulated through the tankless water heater? It is not clear from your description which arrangement -- both of which will work -- you have.
Second question: in either case above, is there a circulator on the heating side of the system? In the first case -- true indirects -- that would be circulating water through the tankless and then the heat exchanger. In the second case it would simply be circulating tank water through the tankless (not, frankly, totally unlike the old-time "sidearm" heaters we used to have, but with a pump rather than gravity flow!).
Now in either type of situation, provided there is some form of circulating pump, you can arrange things so that in the event one of the tankless heaters fails you will lose recovery capacity, but not storage for surge demands, which in your situation would appear to be required. Further, this can be done with a small amount of repiping, but perhaps no additional controls: the outputs from the two tankless heaters are run through check valves to a manifold, from which, in turn, the hot water inputs to the two storage tanks are taken. The returns to the tankless from the storage tanks are similarly manifolded, and the return lines to the tankless heaters are taken from the manifold. Note that the only pumps required are on the tankless circuits. The lines from the manifolds to the storage tanks must be carefully piped so as to be balanced in all respects (it is possible that balancing valves may be advisable). Now the control is this: if an aquastat on the system requests heat for the storage tanks, both tankless heaters are started. However, an additional aquastat is provided for each tankless on its output line and, if it senses low temperature (indicating failure of that tankless) it shuts off that tankless and its circulating pump.
It would be most advisable that that shutdown aquastat mentioned also activate an alarm in some monitored location, as otherwise a failure of one tankless probably would not be noticed -- which could lead to a latent failure condition which would appear only when the second tankless quit. This would not be good.
I realise that this arrangement would not have some of the more whizzy aspects of using a PLC. This is as much a matter of personal preference as anything. It would not, however, lose any of your storage -- only recovery -- and would be simple to understand and maintain; there is something to be said for that...Br. Jamie, osb
Building superintendent/caretaker, 7200 sq. ft. historic house museum with dependencies in New England0 -
@Jamie Hall
I hear ya! ...... and well said!
FYI ...... i'm not a heating guy : )
These are twin tankless units mounted to tanks (Rinnia DUO Hybrid Units)
199 K BTU attached to 119 gal storage tanks (direct tank water heating)
Self contained circulators for each tankless heater
No communication amongst the twins ....... none!
Taco 007 "Keep-alive" building return loop circulator (runs mostly 24/7)
The maintained equivalent water volume in feed and return loop is aprox. 130 gals storage capacity (ie:hot water held at 120 F temperature available over every guest room 24/7)
Rinnai configured this DUO Hybrid (tankless + tank) as generic replacement of the traditional bottom fired units.
Extended its capacity by a simple balanced parallel piping configuration with NO cooperation between the units (truly two stand alone units).
As this was their engineered design concept for this DUO Hybrid ..... they will not technically entertain my desire to enjoin them in a fault recovery mode of operation ...... but that would never stop me! : )0 -
speaking of best use of resources....
Should be held at far higher than 120 in a large system like that, especially with recirculation to prevent legionella.0 -
The efficiency of a condensing Rinnai tank-less water heater is standard: around 95-96% but only if it's in condensing mode (cold water entering) If you are producing tank water over 140F it is more like 85-86% most of the time. Rinnai uses no super high tech that negates the laws of physics. A ball valve might be simple but it's your best bet for low investment. Why would you not immediately isolate a down production unit? What will the PLC setup do better? Are you thinking your plc would change tank setpoint with some logic programing. If your DHW loop mixer is 120F fixed and your tank is 140F near fixed, what's the PLC doing?0
-
You can do it with two zone valves and two aquastats. Aquastat on each tank outlet, set to open on temperature fall, controlling zone valves BEYOND (in the flow direction) the aquastats. Zone valves open when aquastat is above say 120 or maybe even as low as 100. Then go to mixing valve to bring the temp to 120.
And as I said before, set it up with an alarm at some monitored location!Br. Jamie, osb
Building superintendent/caretaker, 7200 sq. ft. historic house museum with dependencies in New England0 -
Teemok said:
The efficiency of a condensing Rinnai tank-less water heater is standard: around 95-96% but only if it's in condensing mode (cold water entering) If you are producing tank water over 140F it is more like 85-86% most of the time. Rinnai uses no super high tech that negates the laws of physics. A ball valve might be simple but it's your best bet for low investment. Why would you not immediately isolate a down production unit? What will the PLC setup do better? Are you thinking your plc would change tank setpoint with some logic programing. If your DHW loop mixer is 120F fixed and your tank is 140F near fixed, what's the PLC doing?
Why would you not immediately isolate a down production unit?
Usually these things happen at 10:30 PM on a weekend and there is no maintenance person onsite and one person stuck at the front desk.
Front desk person hears about the loss of hot water long after both tanks are stone cold : (
What will the PLC setup do better?
Intervene without human intervention!
Immediate evasive action to counter the faults effects (no hot water)
Are you thinking your plc would change tank setpoint with some logic programing
Yes! jump into its max. set point of 185 F
This should increase the available 120 F guest hot water capacity out of the last mixer before delivery.
If your DHW loop mixer is 120F fixed and your tank is 140F near fixed, what's the PLC doing?
Recovering the dead tank with the surplus heat from the working one by "cross mixing" the tanks.
0 -
...... other evasive actions may be to reduce pressure flow (like a brown out from the electric company does in over demand)0
-
OK, OK. Simple isn't popular. So I will make one other comment. Arrange your PLC and other controls, valves, sensors, and what have you so that the system fails operational when they fail -- particularly when the PLC fails. With a simple two aquastat/two zone valve system, a failure of one water heater reduces your reserve capacity, but nothing worse. A failure of one aquastat or one zone valve (fail closed) does the same -- but is a failure which even a moderately competent tech. should be able to fix in a few hours at most. If the more complex custom system fails, you are going to have to scramble to get it fixed... unless it is designed and installed to fail operational, in which case you are OK, sort of... but it may still take weeks to fix.
Just sayin'Br. Jamie, osb
Building superintendent/caretaker, 7200 sq. ft. historic house museum with dependencies in New England0 -
All this just to keep some useful hot water for the guests until help arrives.
As you know commercial size mixers are very expensive, I would be using three of them! This would normally be a cost prohibitive endeavor.
Only because I write the software and program the PLC myself does it make a project like this even affordable to the motel industry0 -
"@Jamie Hall"
a failure of one water heater reduces your reserve capacity, but nothing worse
Under a properly designed heat/loss system .... agreed!
..... but this building and hundreds more are now on there third or forth system now (older properties)
And as you may know the trend in these motels are to replace their systems with the magic "199K btu" and "119 gal" sized units, for that's the highest limit allowed before you are required to have mandatory state boiler inspections.
In their doing so, they knowingly or unknowingly scafriced the required heat load requirements for the building.
So basically,
Its my intention to temporally bridge this gap to minimize the complete loss of hot water until help comes.0 -
Quite agree with your primary objective. Just remember: KISS.Br. Jamie, osb
Building superintendent/caretaker, 7200 sq. ft. historic house museum with dependencies in New England0 -
I said "why would you not". I get it, you want to heat the down tank with the working unit. How will you raise the set point? Is there a 0-10 control option on the Rinnai?
0 -
The PLC must first take the heat exchanger off line, change setpoint (commercial temp. mode max. is 185 F) then bring system back on line.Teemok said:I said "why would you not". I get it, you want to heat the down tank with the working unit. How will you raise the set point? Is there a 0-10 control option on the Rinnai?
0 -
Zone valve isolates down tank. As the hot tank nears it's recovery set point the down tank recovery mode is activated. Link is apposing pumps, no checks, piped off the tank-less hot supply pipes, with a ball zone between them. Link the tank-less returns with ball zone valve between. Controller decides when to isolate outlet of the down tank and when to activate the correct cross tank circulator. Down tank recovers and outlet is opened till down tank temperature drops again.
It's a lot for not much added capacity.0 -
Extra CU199 installed and piped to replace either units failed heat source. 4 zone valves and a logic controller?0
-
Hi, I'd like to back up a bit and question some assumptions. You have two tanks in parallel, I must assume this is so you don't have any noticeable pressure drop through the tanks. Do you know what the maximum draw is? Might that draw flow adequately through the two tanks if they were hooked up in series? If the draw is too high for series plumbing now, have lower flow fixtures been considered? Have pressure compensating fixtures been considered? Think Neoperl.
All this is to get to the possibility of the tanks being piped in series, which would then allow recirculation to keep both tanks warm/hot even if one tankless unit failed. It would be simple rather than complex, and more likely to function reliably. I like @Jamie Hall 's affinity for simple!
Yours, Larry0 -
Thought of that as well. 3 way ball valve forces recirc. to down tank. Need a links from hot of down tank to cold of hot tank.0
-
"The PLC must first take the heat exchanger off line, change setpoint (commercial temp. mode max. is 185 F) then bring system back on line."
You doing it with a robot button pusher or you're hacking the control?
De-power and a dip switch throw?
0 -
Teemok said:
"The PLC must first take the heat exchanger off line, change setpoint (commercial temp. mode max. is 185 F) then bring system back on line."
You doing it with a robot button pusher or you're hacking the control?
De-power and a dip switch throw?
........ Its a simple keyboard matrix , discrete lines.Teemok said:"The PLC must first take the heat exchanger off line, change setpoint (commercial temp. mode max. is 185 F) then bring system back on line."
You doing it with a robot button pusher or you're hacking the control?
De-power and a dip switch throw?0 -
Larry Weingarten said:
Hi, I'd like to back up a bit and question some assumptions. You have two tanks in parallel, I must assume this is so you don't have any noticeable pressure drop through the tanks. Do you know what the maximum draw is? Might that draw flow adequately through the two tanks if they were hooked up in series? If the draw is too high for series plumbing now, have lower flow fixtures been considered? Have pressure compensating fixtures been considered? Think Neoperl.
All this is to get to the possibility of the tanks being piped in series, which would then allow recirculation to keep both tanks warm/hot even if one tankless unit failed. It would be simple rather than complex, and more likely to function reliably. I like @Jamie Hall 's affinity for simple!
Yours, Larry
Hi Larry!
Might that draw flow adequately through the two tanks if they were hooked up in series?
The draw would be fine I think ...... the problem would be the last in series tank's cold in will immediately shut down that tanks firing (the tank mounted controller has it temperature sensor sitting right there! .... thinking this tank has reached set point.)
0 -
Hi Teemok!Teemok said:Extra CU199 installed and piped to replace either units failed heat source. 4 zone valves and a logic controller?
I've been picking up all that you've been suggesting! Your not new to all this I see! : ) Thank you for the wider insite to all this!
Pulling everyone back, let me restate my intent and expectations thus far (if I'm wrong just let me know!) .... rem: I'm not a HAVC guy!
My intent was to basically leave everything as is .... no major re-work!
My thoughts were to at the hot out balanced "T" connection, replace "T" with my PLC "rejection" mixer.
My additional thought was instead of having my working heating unit go to sleep upon meeting its set point temperature, keep it running full blast but "cross connected" to the failed tank. (think: .... putting one tank on top of the other and series connect their side hot a cold ports)
Only if working tank is satisfied will the tank-less heating loop (side tank ports) be included in the failed tank.
0 -
Wow! ..... I think thru everyone's suggestions you've beaten some new sense into me! : )
How about this ......
Rejection mixer at the hot out "T".
Circulator in the bottom cold loop (only active on no-flow).
Working tank recovers failed tank only when it has nothing to do
Blocks the cold mix to hot water problem
Works for tank failure in either tank
..... that's it! so simple!1 -
RickDelta said:As this was their engineered design concept for this DUO Hybrid ..... they will not technically entertain my desire to enjoin them in a fault recovery mode of operation ...... but that would never stop me! : )Did you ask them? Tech support may already have an approved solution for this.You already have all the pieces now to do what you want, just not the right plumbing. Your Duo twins need to become Siamese Duo twins: conjoined at both the output of each pump and the output of each tankless. Then, it would work no differently than two separate tankless units working in unison and plumbed via manifolds to keep two separate tanks hot.
0 -
"....... Its a simple keyboard matrix, discrete lines." Easy for you to say
It is clear to me now, I should have asked for a definition of a cold rejection mixer set up. I see two inputs and and outlet. Is it less a mixer and more of a selector/ Isolater? I'm guessing there's a real temperature mixing valve set at 120F off the shared outlet post PLC CRM.
The 007's flow loop is through the plc rejection mixer valve? How? 007 in inlet might be restrictive. You would need a second 007 so flow is reversible. Hot water always flows out of the hot tank top too the top of the cold tank. Exchange flow would have to be slowed enough that the hot tank isn't chilled by the exchange.0 -
Any valve you use will need to be low lead NFS61. A zone valve will need to be a high pressure shut off. Probably a motorized type which may need to be powered open and closed
Belimo has some spring return ball valves, around 1500 bucks, probably not low lead though.
This seems like a complicated work around, certainly there is a way to make them work properly?Bob "hot rod" Rohr
trainer for Caleffi NA
Living the hydronic dream1 -
See new "PLC cold water "Rejection" mixer? (revised)" post on this guys Please!0
Categories
- All Categories
- 86.8K THE MAIN WALL
- 3.1K A-C, Heat Pumps & Refrigeration
- 56 Biomass
- 425 Carbon Monoxide Awareness
- 109 Chimneys & Flues
- 2.1K Domestic Hot Water
- 5.6K Gas Heating
- 105 Geothermal
- 160 Indoor-Air Quality
- 3.6K Oil Heating
- 70 Pipe Deterioration
- 966 Plumbing
- 6.3K Radiant Heating
- 385 Solar
- 15.3K Strictly Steam
- 3.4K Thermostats and Controls
- 54 Water Quality
- 44 Industry Classes
- 47 Job Opportunities
- 18 Recall Announcements