Why is 1 zone Supply side cooler than Return

Return on this side is heavily restricted in order to balance the house heat.
Edit: it might be relevant that the expansion (or compression? i don’t know which) is the vertices pipe coming off the cold supply line.
EDIT: additionally, supply-side water temp goes UP when circ turns on (prior to boiler firing), even after a period of inactivity.
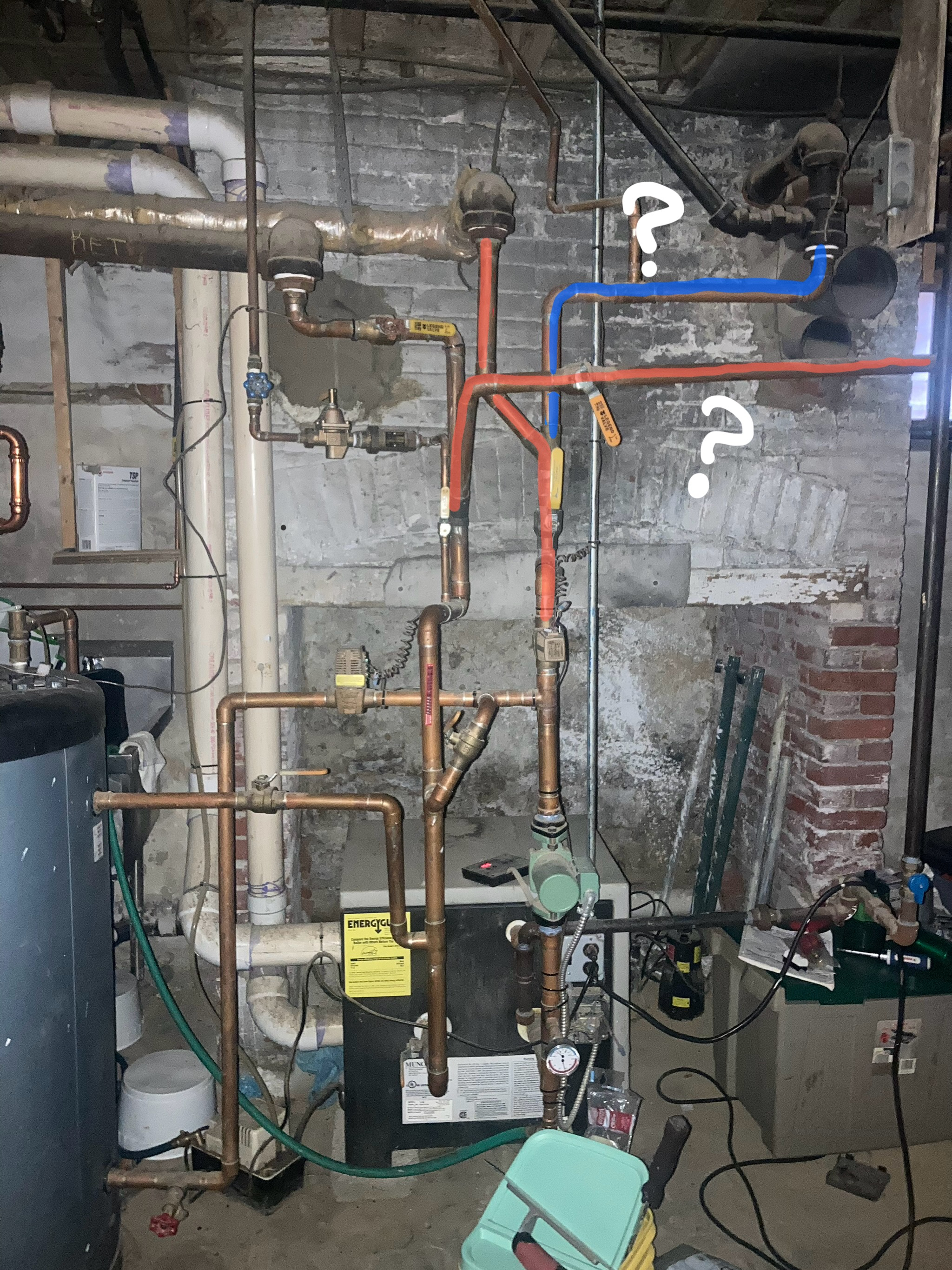
Comments
-
Most probably because you don't have flow thru that zone and you have thermo siphon in the return line.
That's why we use check valves.0 -
-
There, there, be kind. Most home owners don't have a clue about boilers or how they work and depend upon technicians to build and service their heating plants. Many plumbers and hydronic specialists tell a good story and the homeowner has no way of judging the quality of what they are being told.
Thank God for Heating Help.com.
As my Dad use to say, "People who think they know it all are particularly annoying to those of us that do." He said that with a smile on his face.0 -
previous owner was actually my landlord. a nice enough guy, if a bit too frugal (pot calling the kettle there).
I just find it frustrating that they put this incredibly efficient and capable boiler in, and then undersized the indirect and didn’t pay for piping that takes advantage of it.
Pretty sure this things been running at 180 for 20 yrs (until I bumped it down to 160 last winter).
Why even buy a condensing boiler if you’re going to do that (I don’t know, maybe the mod and the con always come together)1 -
As a side note, the boiler supply water to the indirect tank heat exchanger may be incorrect as the hot water supply should, I think, go into the top port, not at the bottom of the tank, in a counter flow. That would take advantage of stratification.0
-
@HomerJSmith , yes, I’ve been told that in other threads.0
-
It looks like a split loop. Do all the radiators get hot? Assuming not.
What's the pressure on the boiler?
There's no way to purge from the boiler. Each radiator must be bled individually. That looks to be a high water volume system so it might take a while.
IDK if lack of check valves is the issue since there's zone valves.
IDK if the 007 circulator is correct for the system.0 -
When I looked at the piping and saw the Taco 571 zone valve, I thought to my self "SELF, that guy has insufficient hot water" but decided that was not the reason for this post and ignored my first impression... Then I read this:and then undersized the indirect and didn’t pay for piping that takes advantage of it.
So here is the sequence of operation for your (what looks like a 40 gallon tank) indirect.
1. Turn on the shower and get the water temperature to the shower, just right. (1 to 2 minutes)
2. Get in the shower and start to use the hot water for several minutes. (3 to 8 minutes)
3. The cold water in the tank has now been detected by the water heater thermostat. The zone valve gets power to open and start the boiler. (This can take as long as 90 seconds on the Taco 571) (8 to 9.5 minutes)
4. The zone valve end switch now closes and the burner goes into the start up cycle. Pre purge, then trial for ignition, then ignition then pilot flame is proven then main burner valve is opened and there is a full burner operation (9.5 to 11 minutes)
5. Circulator starts to pump cold boiler water into the tank during the start-up sequence of operation. (9.5 to 11 minutes)
6. The burner starts to heat the water in the boiler that is circulating through the indirect. (11 to 13 minutes)
7. Now the hot water is running for almost 13 minutes and the water heater is just starting to recover from putting cold water into that tank for all that time.
With a 2 GPM shower head, you have used 26 gallons of the 32 gallons of available hot water in the 40 gallon tank. If your shower head is a 3 GPM, then you used up all of the hot water in the tank and now the boiler is playing catch up to get the job done. Not the best zone valve for this situation. By increasing the temperature in the tank, and adding a mixing valve, then using a fast acting zone valve, you will find that the indirect is more than big enough.
Edward Young Retired
After you make that expensive repair and you still have the same problem, What will you check next?
0 -
You are possibly running out of heat. All of those BTUs have jumped off the track and now have cooled.
Those pipes are BIG and could be expelling the heat.
Tough to tell from here. Just my guess.0 -
@HomerJSmith and general update. (others have mentions where I'm specifically addressing what they brought up)
Ok, after a lot of running around taking temps and playing with valves and too many edits for this to be coherent. In short, neither I nor previous owner know of this happening prior to this.
So here's what the past few days have been like for my boiler and my hope as to why this is happening:
I never noticed this behavior before I blew a transformer. While waiting for a transformer, I was manually going down and turning on the thermostat every so often, and occassionally the hot water, until I realized that I could just wire the house T-stat straight to the boiler and manually open zone valves.
Two nights ago, when I first noticed the problem, I had left the hot water valve open all night long (we have tenants and I didn't want them to get a cold shower).
My hope is that this intermittent running, plus leaving the hot water on all night (plus the cooler night weather), screwed with the flow enough that the front zone cooled down enough to start a thermo syphon. Even after turning off the DHW zone valve in the morning, this persisted due to a vicious cycle.
The issue resolve when I open the ball valve completely. I'm hoping that, after running heat with the ball valve completely open and warming up that water, I have broken the vicious cycle and regular service will be restored.
A mini-test seems to suggest this is what happened: I turned my boiler off and shut the ball valve considerably. After a wait, I went down and measured temps with my IR; send was colder than return (thermo syphon had begun). After firing up the boiler, send warmed up, return cooled down.
Does this sound plausible, or am I misreading/misunderstanding things?
Other info that may be useful (this all assumes I need to keep the ball valve open):
With the ball valve open, my IR heat gun registers 140 degrees (at the threaded joint with the iron pipe) going into that loop (4 radiators, 1 quite small with a detla T of approx 20-30) and approx 90 degrees going into the other loop (7 radiators, delta-T 4 degrees).
So I'm pretty concerned that, if this change is needed, the majority of the house will be considerably colder.
As far as I can reason, it doesn't matter where I restrict flow in that circuit (ball valve or with individual radiator valve adjustments). If I restrict flow in a way that balances the whole house, I assume I'll get backflow.
EDIT: Opening the ball valve has flow going the correct direction. However, at some point after this, I partially closed the first radiator on the system (Ts off the iron pipe right at the threaded joint). Flow reversed. I'm not sure if it caused it or not. But boy is this a PIA.
It is worth noting that I installed a kitchen radiator on the other circuit (removed and never replaced until now) a few months ago. It basically gets no flow (it has a TRV and no lockshield, so should be quick to heat up, assuming that the reduction in supply pipe diameter isn't a massive deal), so I closed the ball valve a bit more this fall to push more heat towards that part of the house.
I'm quite concerned I'm going to have a very cold kitchen with the ball valve fully open.
Full disclosure: Yesterday I tried installing a ZVC, which worked, except I ended up deciding using it was a bad idea (other posts cover this). So I uninstalled it, but in the processes, blew a transformer (also in another post). I'm currently assuming that was due to shorting out the T-stat wire (wiring diagram w/short in other post) and am waiting for a new transformer to arrive. Right now, I just have the T-stat hooked right up to the boiler and the valve manually opened.
I occasionally switch this to the indirect T-stat and switch valves to keep hot water up to temp.
In my inexperience, I'm concerned at how long the boiler's been running since then (seems to have run constantly since this am, but the T-stat is in a room affected by reverse flow, and opening the ball valve further meant that a lot more cold water would be flowing and need to heat up), but trying to reassure myself by reminding myself that it's a lot of water to heat up (both in the radiators and in the hot water tank) and it's colder out than it was before. (the munchkin is also sometimes going over it's set point by about 5% with the boiler still firing, which I don't remember happening before. There's approx 15 degree delta T between supply and return side).
Prior to my messing around, the 4 radiators on this backflow circuit acted as follows: 2 got hot (1 & 3), 2 didn't get very hot (2 & 4. 2 has an incredibly old valve that I don't trust. 4 may be able to be opened more). I do not know if the circuit was backflowing or not.
In fact, it even seemed that at least radiator #1 was getting hot enough even with back flow.
Back to the issue at hand:
Thinking about it more, I think many valves on the larger loop are almost completely closed, so it would also be possible to open them (although I've read mostly closed valves are useful for these old cast iron radiators).
I talked to the previous owner, and he says he noticed this issue (and says he touched the pipes often).
I assume if I put a flow-check valve in there, I can restrict as much as I want and still get correct directional flow. Is that accurate?
Could it be a circulator issue? The furtherst non-backflow zones are getting heat, so I dunno... I'm so confused.
@HVACNUT
No, not all the rads get hot, but most do. The previous owner (I was a renter than) did complain often about how hard the house was to balance, though (he also refused to touch the old, stuck valves, despite having removing a radiator. so.... yeah. I take that with a grain of salt)
The ones that don't I was assuming were due to busted valves (I spent some time trying to loosen valves that literally had wooden handles... not too sure what exactly happened inside). I forget exact pressure; I think it was about 16-18 psi when I last looked (3 story).
I (amateur) think that the zone valves are irrelevant here, as they do not interfere with the reverse flow path in any way.
@EdTheHeaterMan
That's very useful, thanks. I've also been told that I should repipe so supply side goes into the top.
Previous owner did hotter storage and mixing valve. I installed low-flow showerheads and haven't had any complaints yet with the indirect T-stat at Max and boiler set-point at 160 (can't use the ODR here, but that's the subject of more than a few other posts and comments). (note: I had complaints when I was the upstairs tenant. Now that we own the place and I've installed the low-flow, I haven't had any complaints from my own tenants yet. But I do worry a bit as we go into the winter months).
@lntplm
I did a layman's manual J and it looks like the boiler is properly sized. My water temps are set a bit above what that manual J advised. I've read that the app I used often estimates BTU loss 25% higher than actual. And I've been told by others that my sq footage to EDR means that I could probably run much, much lower than that, even.
So I'm pretty sure that I'm good on BTUs. But let me know if there's something I'm missing or misunderstanding.0 -
If you look at the pipes in your mind's eye and think: “If I were heated water what would I do?”
You might come up with this:
Yellow is the hot water from the boiler and it is going through the zone valve then comes to a Y fitting. Now the water must make a decision because no one put the direction arrows on the inside of the pipes. The path of least resistance is to take the branch because that return pipe is almost fully closed (ball valves are not the best for balancing). Let's put numbers on the flow rate. Let's say that there are 15 units of water going out of the boiler through the pump. Yellow has 15 units of flow when it enters the Y fitting (think about the law of the tee. Because the Y is just a crooked Tee). When the water in the Y goes to the branch and leaves the Y at 15 units, that means the no water is going in or out of the run of the Y fitting.
Let that happen for an amount of time. Eventually that water returns a little cooler indicated by the purple arrow. BUT, compared to the other section of the system, the water is much warmer and therefore much lighter than the room temperature water in the problem Right Side of the system. So that water starts to move indicated by the green arrow that is flowing backwards at the supply Y fitting at a rate of 1 unit. So now apply the law of the Tee and you will get 15 units entering the Y from the bottom and 1 unit entering from the top so you get 16 units leaving the branch. Since the water on the right side is room temperature, that will feel much cooler to the touch than the water leaving the branch going to heat all those radiators on the left side.
Follow that all the way around to the return Y fitting and apply the law of the Tee and 16 units are returning from the left side of the system indicated in purple. Since the boiler pump is only moving 15 units, the Y fitting puts 15 units back into the boiler. The other 1 unit goes into the return of the right side. That water is warmer, so the return feels warmer to the touch at the Y fitting going to the right side radiators. Since the flow is so little, by the time that return temperature water reaches the first radiator on the right side of the system, all the heat is used up pretty quickly and only has room temperature water to put into the Y fitting on the supply side.
This is the only explanation that makes sense with the information you provided.
To fix this you need to open all the radiator valves and the 2 ball valves installed for balancing. Once you operate that system with all the valves open, you can see what rooms are too hot, then start to throttle those radiator valves a little at a time. Remember every time you adjust one radiator, the other radiators will feel the change and you may need to go back and adjust the ones you already got just right. Another fix is to install thermostatic radiator valves on all but the 2 coldest rooms in the system. (one on each side) then allow the TRVs to automatically adjust the flow as the room temperature requires.
The fact that there are copper Y fittings tells me that the original design was messed up when the original coal boiler was replaced with this or a previous replacement boiler. The original Coal boiler did not have Y fittings
Edward Young Retired
After you make that expensive repair and you still have the same problem, What will you check next?
0 -
Since the boiler is not piped primary secondary that bypass valve is to adjust and make sure the boiler gets adequate flow to not trip out on high limit.
However it also will blend the temperature and lower flow rate to the system.
I have seen many direct connected Munckins working, you might try closing the bypass valve and see how the boiler behaves.Bob "hot rod" Rohr
trainer for Caleffi NA
Living the hydronic dream0 -
The broken vents on the radiators need to be replaced. It's the only way to get the air out.0
-
@hot_rod what do i look for in behavior as I adjust that bypass valve? don’t want to screw up my boiler, obviously. (note: the bypass valve isn’t the problematic valve)
@HVACNUT it’s not bleed valves I refer to, but radiator valves.
@EdTheHeaterMan seems you’re right. everything flows right on startup, but after a while, it flips around.
At this point, I’m pretty sure something has changed in the system. Last week, before trying to add the ZVC, the system was fairly well balanced. That ball valve had been in a mostly-closed position for some time.
Now the system is struggling to satisfy a thermostat call (thermostat is in the reverse-flow loop zone, but that was never an issue before).
Things that changed:
- Maybe I broke something when trying to install the ZVC (but you said circ has no control over flow at Y, so I don’t think a damage circ would do it. And this seems like a circ issue. Or a clog somewhere? I don’t know)
- The CH Zone valve is staying open, even when there is no call for heat and no circ running. (don’t see why this would matter) during the wait to replace a blown transformer.
- I connected the circ’s ground wire to a proper ground; previously, it was only grounded through the MX (or whatever it is).
- i removed what I assumed was the thermostat-feeding resistor on the zone valve (might this be why my battery-powered t-stat continues to call for heat after it’s up to temp? this is pissing me off)
- I might’ve closed the bypass valve a bit, but I’m not sure.
- There’s an outside chance that the 3rd floor radiator valve is closed or almost closed (don’t remember if I changed it recently; tenants might’ve messed with it). However, I know it was almost or completely closed last winter and I don’t remember having this problem.
Any chance that restricting flow via the rad valves will be less likely to cause this issue? (vs balancing with the ball valve; why is one better than the together?)
I guess one way to test is to leave the ball valve completely open and see what happens. That’s for tomorrow.0 -
I have the same issue, although it only occurs once in awhile, usually on very cold days when the heater is going nonstop. The system was installed originally with the check valves removed although I don't know why.0
-
The way a Ball valve and a Globe valve and a Gate valve are designed make the flow thru the valve in the partial closed position act differently. It was explained to me once some time ago. But I forgot the details. (I file this under the phrase my son uses about me " My Dad forgot more about heaters than I'll ever know"). But the photos of a gate valve interior, the ball valve interior and the Globe valve interior will show that the globe valve has the most convoluted path when fully opened and that path is metered best with the valve seat and stem getting closed evenly all around the opening as the stem gets closer. The Gate valve is second best, and the Ball valve is the worst.SENorthEast1895er said:@EdTheHeaterMan seems you’re right. (I GET THAT A LOT) everything flows right on startup, but after a while, it flips around.
At this point, I’m pretty sure something has changed in the system. Last week, before trying to add the ZVC, the system was fairly well balanced. That ball valve had been in a mostly-closed position for some time.
Now the system is struggling to satisfy a thermostat call (thermostat is in the reverse-flow loop zone, but that was never an issue before).
Things that changed:
- Maybe I broke something when trying to install the ZVC (but you said circ has no control over flow at Y, so I don’t think a damage circ would do it. And this seems like a circ issue. Or a clog somewhere? I don’t know). This is unlikely. The electrical stuff that operates the pumps will have little to no effect on system flow. If the pump runs or does not run is based on electrical switching and will not change how the water flows inside the pipes. ...Unless you are loosing the pump operation when the hot side is still warm and the cold side is still cold
- The CH Zone valve is staying open, even when there is no call for heat and no circ running. (don’t see why this would matter) during the wait to replace a blown transformer. (an open valve can always be a big factor in changing how a system works when it valve is normally closed. Like when there is a call for DHW and no call for Heat.)
- I connected the circ’s ground wire to a proper ground; previously, it was only grounded through the MX (or whatever it is).
- i removed what I assumed was the thermostat-feeding resistor on the zone valve (might this be why my battery-powered t-stat continues to call for heat after it’s up to temp? this is pissing me off)
- I might’ve closed the bypass valve a bit, but I’m not sure.
- There’s an outside chance that the 3rd floor radiator valve is closed or almost closed (don’t remember if I changed it recently; tenants might’ve messed with it). However, I know it was almost or completely closed last winter and I don’t remember having this problem.
Any chance that restricting flow via the rad valves will be less likely to cause this issue? (vs balancing with the ball valve; why is one better than the together?)
I guess one way to test is to leave the ball valve completely open and see what happens. That’s for tomorrow.
The little I do remember is in this diagram that shows the partially closed ball valve has the most turbulent flow when partially open/closed. The other two have less turbulent flow. Now I may be incorrect on the details, I just remember that a ball valve is not the best for throttling flow.
I would start with all valves open full, then close any room you do not want heated at all (like that third floor) then start with any room that is too hot after 1 day of operation. Close that radiator valve to about 50% Then wait a day and go to the next room that is too hot and do the 50% thing then wait 24 hours. and so on... Once you have gone through the whole house or the half that is too warm, then see how each adjustment affects the first and second and so on. You may find that you need to open some back up or close some a little more... Once you get close to even, Lock the valves in place by tightening the packing nut and removing the handle. (on old valves be careful of tightening the packing nut). Also mark the positions of the final adjustment and record it somewhere for future reference when the other tenant(s) decide to change the adjustment to get more heat.
Edward Young Retired
After you make that expensive repair and you still have the same problem, What will you check next?
0 -
There is a description of how Radiator valves work. Steam radiator valves use a washer and seat like a globe valve while Hot Water radiator valves use a hollow gate that rotates until it is completely turned around to reveal a small orifice to allow a small amount of heated water to pass to prevent freeze-up
Look at this https://forum.heatinghelp.com/discussion/comment/1736251#Comment_1736251
Not every installer in the old days used the proper valve, some got it wrong. Some repair techs over the ages have used the wrong valve. So I can't tell if you have the hollow gate valve (180° turn) the ball valve type (90° turn) or the globe valve type (multiple turns). What ever valve you have, make sure you allow for a trickle of flow in the ones that you close 100% to prevent freezing.
Edward Young Retired
After you make that expensive repair and you still have the same problem, What will you check next?
0 -
@EdTheHeaterMan
cool, thanks. That’s very helpful.I haven’t completely thought through this, but I’m starting to wonder if closing the bypass valve is what did it. Boiler certainly seemed to be short-cycling; I remember being concerned before making any changes.Earlier today, I tested back-to-back. Bypass open: cycles on-off in less than a minute or so.Bypass closed: ran for ten minutes, then I had to go.My theory being that the short cycling never really allowed the temperate differential to reach a critical point to create back flow.In any case, the back flow prevents me from using my thermostat, so I figured I’d work around that by setting the boiler to run all night long at a temp that I thought would prevent me (and my family and tenants) from waking up freezing or roasting.My guesstimate was 110, and seemed to have worked well. I set it at 100 for most of the day and upped it to 105 towards afternoon. (Previous set point was 160).I haven’t caught it back flowing yet. Whole house is warm.The current plan is to use my ZVC to do the outdoor reset per the advice on this thread (was going to go your route, but I already have the ZVC) and wait to kick myself later (when it’s really cold) for not dealing with this now. With luck, I’ll get TRVs in before then.0 -
EdTheHeaterMan said:
@EdTheHeaterMan seems you’re right. (I GET THAT A LOT) everything flows right on startup, but after a while, it flips around. At this point, I’m pretty sure something has changed in the system. Last week, before trying to add the ZVC, the system was fairly well balanced. That ball valve had been in a mostly-closed position for some time. Now the system is struggling to satisfy a thermostat call (thermostat is in the reverse-flow loop zone, but that was never an issue before). Things that changed: - Maybe I broke something when trying to install the ZVC (but you said circ has no control over flow at Y, so I don’t think a damage circ would do it. And this seems like a circ issue. Or a clog somewhere? I don’t know). This is unlikely. The electrical stuff that operates the pumps will have little to no effect on system flow. If the pump runs or does not run is based on electrical switching and will not change how the water flows inside the pipes. ...Unless you are loosing the pump operation when the hot side is still warm and the cold side is still cold - The CH Zone valve is staying open, even when there is no call for heat and no circ running. (don’t see why this would matter) during the wait to replace a blown transformer. (an open valve can always be a big factor in changing how a system works when it valve is normally closed. Like when there is a call for DHW and no call for Heat.) - I connected the circ’s ground wire to a proper ground; previously, it was only grounded through the MX (or whatever it is). - i removed what I assumed was the thermostat-feeding resistor on the zone valve (might this be why my battery-powered t-stat continues to call for heat after it’s up to temp? this is pissing me off) - I might’ve closed the bypass valve a bit, but I’m not sure. - There’s an outside chance that the 3rd floor radiator valve is closed or almost closed (don’t remember if I changed it recently; tenants might’ve messed with it). However, I know it was almost or completely closed last winter and I don’t remember having this problem. Any chance that restricting flow via the rad valves will be less likely to cause this issue? (vs balancing with the ball valve; why is one better than the together?) I guess one way to test is to leave the ball valve completely open and see what happens. That’s for tomorrow.
The way a Ball valve and a Globe valve and a Gate valve are designed make the flow thru the valve in the partial closed position act differently. It was explained to me once some time ago. But I forgot the details. (I file this under the phrase my son uses about me " My Dad forgot more about heaters than I'll ever know"). But the photos of a gate valve interior, the ball valve interior and the Globe valve interior will show that the globe valve has the most convoluted path when fully opened and that path is metered best with the valve seat and stem getting closed evenly all around the opening as the stem gets closer. The Gate valve is second best, and the Ball valve is the worst.The little I do remember is in this diagram that shows the partially closed ball valve has the most turbulent flow when partially open/closed. The other two have less turbulent flow. Now I may be incorrect on the details, I just remember that a ball valve is not the best for throttling flow. I would start with all valves open full, then close any room you do not want heated at all (like that third floor) then start with any room that is too hot after 1 day of operation. Close that radiator valve to about 50% Then wait a day and go to the next room that is too hot and do the 50% thing then wait 24 hours. and so on... Once you have gone through the whole house or the half that is too warm, then see how each adjustment affects the first and second and so on. You may find that you need to open some back up or close some a little more... Once you get close to even, Lock the valves in place by tightening the packing nut and removing the handle. (on old valves be careful of tightening the packing nut). Also mark the positions of the final adjustment and record it somewhere for future reference when the other tenant(s) decide to change the adjustment to get more heat.
Issue 8 of the Idronics library I sent you covers various valves used for balancingBob "hot rod" Rohr
trainer for Caleffi NA
Living the hydronic dream1 -
Thanks for the Directions Coach... Now I got more homework to do!hot_rod said:
A flat disc globe valve is not a very good balancing valve, not much better than a ball valve. A tapered seat globe is better, a valve with an engineered plug is best.
Issue 8 of the Idronics library I sent you covers various valves used for balancingEdward Young Retired
After you make that expensive repair and you still have the same problem, What will you check next?
0 -
EdTheHeaterMan said:
A flat disc globe valve is not a very good balancing valve, not much better than a ball valve. A tapered seat globe is better, a valve with an engineered plug is best.
Thanks for the Directions Coach... Now I got more homework to do!
Issue 8 of the Idronics library I sent you covers various valves used for balancing
Enjoy the retired life in the sunny south.Bob "hot rod" Rohr
trainer for Caleffi NA
Living the hydronic dream0
Categories
- All Categories
- 87K THE MAIN WALL
- 3.2K A-C, Heat Pumps & Refrigeration
- 58 Biomass
- 427 Carbon Monoxide Awareness
- 113 Chimneys & Flues
- 2.1K Domestic Hot Water
- 5.7K Gas Heating
- 109 Geothermal
- 161 Indoor-Air Quality
- 3.6K Oil Heating
- 70 Pipe Deterioration
- 994 Plumbing
- 6.3K Radiant Heating
- 391 Solar
- 15.4K Strictly Steam
- 3.4K Thermostats and Controls
- 55 Water Quality
- 44 Industry Classes
- 48 Job Opportunities
- 18 Recall Announcements