Finishing room near boiler flue
I'm trying to determine the best way to maximize my room space while not creating a safety hazard.
The wall in question will be just to the right of the cinderblock/concrete line, and the finished portion will be to the left of that. I'll need to have a block bumped into the room to keep this on the unfinished side.
It's an oil boiler and hidden by that elbow is a barometric damper that opens to the right.
Clearance to the joists is about 9", which seems too little to me. I wonder if the flue used to go to that bricked up opening and why it was moved.
Aside from soliciting general opinions on how to best work around this, I'm also curious if it can be redone in double wall to reduce clearances to the wall, and if the barometric damper could be moved closer to the boiler for the same reason.
Thanks!
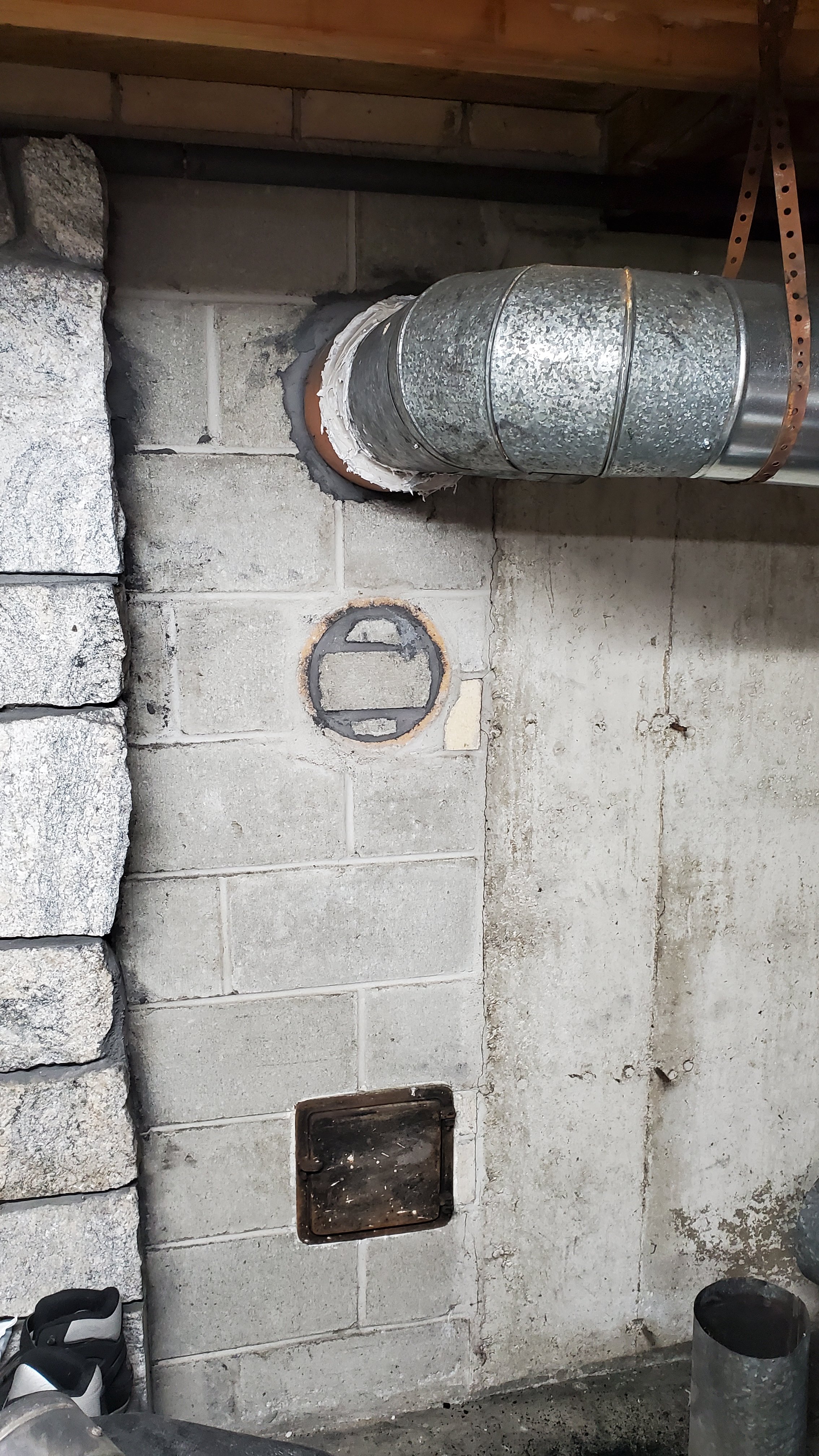
Comments
-
Codes vary somewhat, so your best bet to avoid problems is to consult with your authority (ies) having jurisdiction in your area -- your building inspector and your fire marshal. In my humble (?) both the clearance to the joists is too small -- and the clearance to your proposed wall, unless that wall is to be of fireproof (not resistant) material, such as block or brick. But that's just one man's opinion.Br. Jamie, osb
Building superintendent/caretaker, 7200 sq. ft. historic house museum with dependencies in New England0 -
The approved double wall vent for Oil Fired equipment has the L-Vent classification. That is not easy to find at most plumbing supply co. You may need to order online.
Look at this: https://forum.heatinghelp.com/discussion/117948/what-is-l-vent
here is a specification sheet of one brand:v https://www.mtlfab.com/media/L-Vent_Installation_Instructions-L2147.pdf
Edward Young Retired
After you make that expensive repair and you still have the same problem, What will you check next?
0 -
Thanks, I may try the fire marshal on this one. I'm very leery on bringing building inspectors in as they love to use any new construction as an excuse to force you to update old systems that have been safely operating for decades. I want everything to be safe, but at the same time I am doing little more than putting up simple non-loadbearing stud walls to add a storage area.Jamie Hall said:Codes vary somewhat, so your best bet to avoid problems is to consult with your authority (ies) having jurisdiction in your area -- your building inspector and your fire marshal. In my humble (?) both the clearance to the joists is too small -- and the clearance to your proposed wall, unless that wall is to be of fireproof (not resistant) material, such as block or brick. But that's just one man's opinion.
0 -
This is one of the reasons that the codes and standards were written. The administrative authority requires permits to be obtained, and the work conform to the standards, to protect the health and safety of not only the current occupants, but also future occupants.
It appears that you do not know the requirements. Also, there is more to it than just clearance to combustibles.
You really should determine all of the requirements, and obtain a permit if it is required in your area. What you are attempting involves life safety, and should not be taken lightly.
Most municipalities have rules in place governing the updating of "old systems" and the requirements. I would investigate those if you are worried.
Additionally, we now get several requests a week, due to real estate transactions, to obtain permits for projects that were completed with out them. Home inspectors and municipal housing inspectors are checking to see if permits were obtained for jobs just like what you are attempting. The majority of the time there are many, many code violations that need to be corrected, and many, many transactions have been cancelled or delayed because of them. So, they'll catch up with you sooner or later. And the fines are eye watering.
Then what happens when the fire marshal has lunch with the building inspector. "Hey, what did you tell hillridge about that new room in the basement.......?"
And, if something did happen, such as a fire, even if it was not directly related to what you are attempting, your insurance company would be looking for any way to not pay the claim. Unpermitted construction? Good luck with that.
Ultimately, the inspectors are looking out for your [the resident of the property] interests, and safety.
0 -
I don't disagree at all, and after spending some time this morning looking into my town's process, I think I will go pull the permits and roll the dice on the inspector. For a project this small, the permits are ~$100, and like you said, it can bite you later to skip that step.realliveplumber said:This is one of the reasons that the codes and standards were written. The administrative authority requires permits to be obtained, and the work conform to the standards, to protect the health and safety of not only the current occupants, but also future occupants.
It appears that you do not know the requirements. Also, there is more to it than just clearance to combustibles.
You really should determine all of the requirements, and obtain a permit if it is required in your area. What you are attempting involves life safety, and should not be taken lightly.
Most municipalities have rules in place governing the updating of "old systems" and the requirements. I would investigate those if you are worried.
Additionally, we now get several requests a week, due to real estate transactions, to obtain permits for projects that were completed with out them. Home inspectors and municipal housing inspectors are checking to see if permits were obtained for jobs just like what you are attempting. The majority of the time there are many, many code violations that need to be corrected, and many, many transactions have been cancelled or delayed because of them. So, they'll catch up with you sooner or later. And the fines are eye watering.
Then what happens when the fire marshal has lunch with the building inspector. "Hey, what did you tell hillridge about that new room in the basement.......?"
And, if something did happen, such as a fire, even if it was not directly related to what you are attempting, your insurance company would be looking for any way to not pay the claim. Unpermitted construction? Good luck with that.
Ultimately, the inspectors are looking out for your [the resident of the property] interests, and safety.
I've had both extremely positive and negative experiences with inspectors in other towns. The last major project I did at my old house (a solar install), was all permitted and the only thing I had to change post-inspection was completely unrelated to the work I did and kind of a pain in the ****, but because I touched the electrical, it opened that door. Not sure if it's like this everywhere, but in another town I did work in the fire department has the final say on what they want, and can request things well in excess of actual code if they see fit, so it often comes down to whether or not the inspector is just looking out for your interests and safety, or on a power trip for no reason.0 -
Thats a wise decision. Around here, we submit the permit application with a detailed drawing, and the inspectors review it before issuing the permit. Its a plan review, and at no additional cost. if they see anything that isnt code compliant on the drawing, they will notify you to submit a plan that is. then complete the work to the plan.
We have verbiage in our rehabilitation sub code that helps with the power trip inspectors. All of that info is available on the State website. Also, the inspectors are required to cite a code section of the alleged violation, they can't simply say " do this or that".
0 -
First, refer to the rating plate on your boiler. It will state the clearance to combustibles from single walled chimney connector but some also state the reduced clearance for L vent. Next, check the listing of the L vent as stated in the installation instructions, which are available online.
In general, you do not want to pass through a wall then into any chimney. In the case of a combustible wall, you would need a listed 'pass-through' assembly/ firestop. However, start with the chimney- is it lined with a properly sized listed liner and inspected to be in serviceable condition? If not, reline. Next the connection from the chimney connector L vent must be accessible where it attaches to the chimney. You may have to move your wall. A masonry chimney requires a cleanout, which must be 'accessible'. Listed liners do not require cleanouts for oil though often recommended. The entire connector must be properly pitched, supported, connected and 'accessible' for inspection and replacement as needed.
The baro. damper should be close to the boiler but at least 1.5-2 duct diameters downstream of the appliance collar or any offsets such as ells or tees. The draft test port should be just downstream of the baro. while the combustion analysis port should be just upstream of the baro. Use a "draft hood connector" fitting to attach the L vent even though it's oil and doesn't have a hood. That's what they call the approved double wall to single wall adapter.
Last, with such as long connector, double check your total connector run length against allowables and derate all offsets. You may have to increase the size of the connector.
You can get 6" and 8" diameter listed L vent from chimney supply houses. They call it their double walled 'close clearance' smoke pipe for woodstoves and it's painted black, which is ok. It is, however, listed to UL 641 so it is suitable for use with oil. It has a stainless steel inner liner and carries a lifetime warranty usually. Note most clearances are higher off horizontal runs such as 6" off sides and 8" off top. Anything 45 degrees from level is considered vertical.
Calculate for makeup air and provide as needed. Enclosing a mechanical room usually makes it a 'confined space'.
HTH0 -
Well, should have gone with my gut on involving the building dept. They were no help in answering my question and actually told me at least 2 incorrect things. One was a different clearance issue. I looked that one up afterward and couldn't find the distance they were referring to in the code, so I called them and asked where it was. They couldn't find it either, and I was able to keep an existing clearance that complied with the actual, not made up, numbers. The other was about my actual question, which they said required 18". Turns out, as Bob said above, the real clearance is 6" as specified by the manufacturer. 18" is worst case with no manufacturer spec.
On top of that, they require me to go up to R19 on the walls (easy enough to add some between studs), while also bringing it outside air for ventilation. Because it is now a living space, and there's no window, there's some fresh air requirement that's going to force me to add a mechanical system I'll never use.
At least it was under $100 for the permits, and everything will be unimpeachable when finished.
I had a local HVAC guy out today to figure out how to best do the ventilation requirement and advise on the boiler. He said much of the same. His advice was to come right off the wall with a 90 then a bit of straight, then the barometric damper, more straight, and 45/straight/45 back to the boiler. That would keep the flue tighter to the wall and give me max room on the finished side. He also said to check the boiler rating and that it should be 6" clearances, not 18. He seemed to think single wall was fine, just advised me that it needed to be at least 26 gauge. He also said to just stick some metal between the flue and the combustible material, with an air gap on the combustible side and the clearance could be even lower.Bob Harper said:First, refer to the rating plate on your boiler. It will state the clearance to combustibles from single walled chimney connector but some also state the reduced clearance for L vent. Next, check the listing of the L vent as stated in the installation instructions, which are available online.
In general, you do not want to pass through a wall then into any chimney. In the case of a combustible wall, you would need a listed 'pass-through' assembly/ firestop. However, start with the chimney- is it lined with a properly sized listed liner and inspected to be in serviceable condition? If not, reline. Next the connection from the chimney connector L vent must be accessible where it attaches to the chimney. You may have to move your wall. A masonry chimney requires a cleanout, which must be 'accessible'. Listed liners do not require cleanouts for oil though often recommended. The entire connector must be properly pitched, supported, connected and 'accessible' for inspection and replacement as needed.
The baro. damper should be close to the boiler but at least 1.5-2 duct diameters downstream of the appliance collar or any offsets such as ells or tees. The draft test port should be just downstream of the baro. while the combustion analysis port should be just upstream of the baro. Use a "draft hood connector" fitting to attach the L vent even though it's oil and doesn't have a hood. That's what they call the approved double wall to single wall adapter.
Last, with such as long connector, double check your total connector run length against allowables and derate all offsets. You may have to increase the size of the connector.
You can get 6" and 8" diameter listed L vent from chimney supply houses. They call it their double walled 'close clearance' smoke pipe for woodstoves and it's painted black, which is ok. It is, however, listed to UL 641 so it is suitable for use with oil. It has a stainless steel inner liner and carries a lifetime warranty usually. Note most clearances are higher off horizontal runs such as 6" off sides and 8" off top. Anything 45 degrees from level is considered vertical.
Calculate for makeup air and provide as needed. Enclosing a mechanical room usually makes it a 'confined space'.
HTH
I think I will take this opportunity to add test ports to the flue. Currently, the HVAC guys just use holes they poked in it and refill them with hi-temp RTV after testing.0 -
-
Yes, though neither of those apply here since the room being finished won't include any part of the boiler system. They are requiring me to have a "fresh air" ventilation system in place. Just got the quote back from the HVAC guys for $1200. That nearly doubles the project cost, all for a system I don't want and won't be using, but has to be there for "code".MikeL_2 said:Not meant to be a pita, but for clarification, there is a difference between make up air & air for combustion.
0 -
How is the overall humidity level in the basement? We satisfied the requirement by putting in a stand alone ventilating dehumidifier that for XX minutes per hour will also pull fresh air in and keep the basement at 55%. Made a world of difference in the overall air quality - we didn't know how bad it was until we experience how great it became.0
Categories
- All Categories
- 86.9K THE MAIN WALL
- 3.2K A-C, Heat Pumps & Refrigeration
- 57 Biomass
- 425 Carbon Monoxide Awareness
- 110 Chimneys & Flues
- 2.1K Domestic Hot Water
- 5.7K Gas Heating
- 105 Geothermal
- 160 Indoor-Air Quality
- 3.6K Oil Heating
- 70 Pipe Deterioration
- 978 Plumbing
- 6.3K Radiant Heating
- 387 Solar
- 15.4K Strictly Steam
- 3.4K Thermostats and Controls
- 54 Water Quality
- 44 Industry Classes
- 47 Job Opportunities
- 17 Recall Announcements