Hydraulic Separator - how to ensure proper flow?
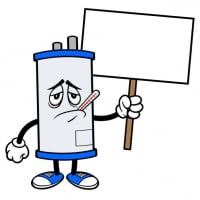
The primary 'loop' in my initial design enters and exits a hydraulic separator with a supply and return header on one side. The supply header branches to 2 zones (each with a mixing valve) and then returns to the return header.
My concern is that once the boiler primary loop temp is satisfied, the boiler will stop firing and turn off the boiler pump... however, the zone circulator pump continues to run (on a call for heat). In this case, wouldn't the return header flow enter the hydraulic separator and travel up the common section and into the hot supply header? It seems to me that the circulator pump will create a lower pressure area in the supply header with the main boiler pump off. So the return flow would not enter the primary loop, it would just go from the return header to the supply header.
The problem if that happens (it seems) is that the primary loop will stay hot while the zone supply temp will cool quickly as it would be using the cooler return water rather than hot boiler water. The control would be compromised because the zone supply temp will only be maintained when the boiler was firing and the boiler pump was operating. I thought about running the boiler pump even when the boiler wasn't firing when either zone circulator was running but i am not sure that is a good idea?
Comments
-
The most common control logic with seps is the boiler control sensor in or after the sep on the distribution supply.
I prefer downstream a few inches on the supply to get an accurate "blended" temperature.
As far as flow rates, those will vary on the distribution side as zones open and close. On the boiler side, if you have a variable speed circulator, as some mod cons do now, that flow rate changes also.
So the sensor on the distribution supply assures you get the temperature you want into the system.
Still open for debate which side is primary and which is secondary. The gentleman that wrote the book on primary secondary piping suggests whichever side you connect the expansion tank to, becomes the primary.
To me, with a properly engineered separator, near zero pressure drop in the vessel, the tank at either return connection establishes that entire sep as the PONPC.
So maybe the "vessel" becomes the primary and both boiler and distribution are secondaries???Bob "hot rod" Rohr
trainer for Caleffi NA
Living the hydronic dream0 -
The actual flow in an hydraulic separator is horribly complex-- but your description is fine for all practical purposes.
The trick is in the control. you may find you need an aquastat on the output from the separator to the system which will turn the boiler -- and its feed pump -- on when the system needs warmer water.Br. Jamie, osb
Building superintendent/caretaker, 7200 sq. ft. historic house museum with dependencies in New England0 -
Interesting and helpful comments, thank you.
Hot_Rod, very good screenshots, thanks for sharing those. The sep graphic especially, nice to see a well annotated graphic showing detailed functions.
One piece of additional info - I have a 2005 Carrier hot water basic (85%) boiler, so when the min boiler limit temp is reached, it fires the boiler and turns on the constant speed circulator pump. No variable control. Also, the expansion tank is currently mounted on the hot (supply) side of the boiler.... is it better to have that mounted on the cold (return) side?
Jamie_Hall, had not thought of putting an aquastat on the supply header. Currently there is an aquastat mounted on the hot (supply) side of the boiler. I have a Tekmar 256 that has the 'boiler' out contacts wired to the thermostat contacts on the aquastat. The 'circulator' contacts on the aquastat are wired directly to the boiler pump... thinking I can rewire that using a relay so that the boiler pump remains on even if the boiler is not firing as long as there is a call for heat from one of the zones.
Plus .... since I am repiping anyway, I could move the aquastat from the boiler outlet to the supply header... would that make a difference?
Just thinking out loud here, any more thoughts?0 -
If you are going to use a sep with that basic cast iron boiler you need to add a system temperature control. I like these Ranco or equal, lots of adjustability and a nice display to see what temperature is actually being supplied.
Probably a TT connection on the boiler that turns it on from a thermostat?
So I would have the heat call go through the Ranco. The boiler will run based on what the Ranco wants or tells it to go to, whenever there is any heat call.
All the other limits and safeties stay in the circuit, of course.
If you are kind, maybe @EdTheHeaterMan will do one of his custom wiring schematicsBob "hot rod" Rohr
trainer for Caleffi NA
Living the hydronic dream0 -
Be glad to work something up for you. I need to know all the components and what functions are necessary.hot_rod said:If you are going to use a sep with that basic cast iron boiler you need to add a system temperature control. I like these Ranco or equal, lots of adjustability and a nice display to see what temperature is actually being supplied.
Probably a TT connection on the boiler that turns it on from a thermostat?
So I would have the heat call go through the Ranco. The boiler will run based on what the Ranco wants or tells it to go to, whenever there is any heat call.
All the other limits and safeties stay in the circuit, of course.
If you are kind, maybe @EdTheHeaterMan will do one of his custom wiring schematics
So far there is a Carrier Gas Boiler that has a control that operates the burner thru a limit and a circulator from some control connected to T T terminals Then there is a system pump and the suggestion of the electronic temperature control. Is there a need for minimum water temperature returning to the cast iron boiler? How will the system circulator operate? A thermostat by way of a switching relay? Is there outdoor reset involved?
The logic diagram needs to be made, then the controls can be added to make that happen.
Edward Young Retired
After you make that expensive repair and you still have the same problem, What will you check next?
1 -
@hot_rod Thank you! Yesterday was my anniversary, so the wife had other ideas of what I should be spending my time on. I appreciate the inputs! I actually found a similar product to your Ranco suggestion, see screenshot. I think they both would work, will read up and see which will work better.
@EdTheHeaterMan, VERY kind of you to offer up the help. Let me do my best to lay it out below.
- check the rough (initial) sketch for the control layout I just did (attached), It is not complete as the 2 Taco I-Series mix valves are not shown. The mix valves will be new and will replace the variable speed injection pump. I was planning on providing power (24vac) to each mixing valve when the zone pump turns on through a relay.
- I have Boiler Boss (2 zone model) that does a fine job of turning on the zone pumps when there is a call for heat. It also closes a contact that I had planned on using to allow the boiler controls to be enabled so the boiler will fire. See that rough sketch to get a better idea of my control logic.
- I planned on using the White Rodgers to enable/disable the TT switch on the boiler based on a 170 degree setpoint for the boiler supply. The white rodgers allows up to a 30 degree deadband... any suggestions on the temp and deadband values are appreciated! 140 to 170 seems like a good starting point though.
- Background - current piping does not use a hydraulic separator - it uses closely spaced "T's" and has a pump that acts as a mix pump controlled by a Tekmar 256. The mix water is then supplied to both zones... It works very well but my 2 zones need different supply temps, one is a concrete slab and the other is a staple up... was thinking 90 degrees for the slab and 120 for the staple up. So the mix pump has to go.
Thanks again!0 -
This will take some time to figure out. I'm not a fan of maintaining boiler temperature at 140 to 170. You don't need that in the fringe seasons. Cold start boilers have worked fine for years. we just need to maintain short warm up times so the return water can reach the 140° minimum during the fringe season and still accept the low temperature return water from the two radiant systems. That's the job of the Hydraulic separator. The temperature mixing will be done by the new Taco valves on the system side.
Now my brain is hurting from all this thinkingEdward Young Retired
After you make that expensive repair and you still have the same problem, What will you check next?
0 -
running across a system now designed by others
primary loop has a Bosch mod/con with onboard circ and LLH
the primary loop has an additional 15-58 circ. With Bosch LLH implemented on boiler
system side and boiler side separated by a caleffi hydro sep.
System side feeds manifolds to sun board and panel rad. Fed by 15-55
other manifolds fed to concrete slabs by 26-99
both have taco 3 way taco i valves with ODR feature as there is an OWB plumbed for future tie in to system.
Circs all auto adapt as manifolds loops have actuators.Blending in the sep is a float as system side requires 8.1 gpm if everything is calling for heat. Concrete Slab temps are 100 at design sunboard is 120 at design. So a happy medium needs to find its way to the 3 way mix valves out of sep.
130 makes everything happy to mix down at 3 ways and keep things cool as can be enough to the mod/con for efficiency sake.This yet has to be super tuned as it was just commissioned.
3 conveyor belts of btus. Boiler with onboard circ. Primary (boiler loop ) with its own circ decoupled with boilers onboard LLH. Then the secondary loop decoupled with the hydro sep.
@hot_rod I like the idea of the boiler supply sensor on the secondary supply. Have to see how it performs in a primary/sub primary setup.I don’t know if this helps OP or not.
as always the sep basics are0 -
I understand! My brain has been hurting for for a week now! Good news is that I am waiting until June/July to rebuild the boiler piping and controls. So lots of time to fine tune the design. More background - we have a geothermal unit that heats most of the house, i only kick on the boiler for Dec thru Feb.EdTheHeaterMan said:This will take some time to figure out. I'm not a fan of maintaining boiler temperature at 140 to 170. You don't need that in the fringe seasons. Cold start boilers have worked fine for years. we just need to maintain short warm up times so the return water can reach the 140° minimum during the fringe season and still accept the low temperature return water from the two radiant systems. That's the job of the Hydraulic separator. The temperature mixing will be done by the new Taco valves on the system side.
Now my brain is hurting from all this thinking
Maybe 140 to 160 is a better boiler temp range?0 -
With a few numbers known, you can calculate the output side temperature..it will always be changing, so you need a mixing device if you want a set or predictable supply to heat emitters.
The math starts on page 39
https://www.caleffi.com/sites/default/files/file/idronics_15_na_2019.pdfBob "hot rod" Rohr
trainer for Caleffi NA
Living the hydronic dream0 -
hot_rod said:With a few numbers known, you can calculate the output side temperature..it will always be changing, so you need a mixing device if you want a set or predictable supply to heat emitters. The math starts on page 39 https://www.caleffi.com/sites/default/files/file/idronics_15_na_2019.pdf
Especially as actuators open and close in loops etc.
The most simple approach is insuring mixing devices get the temps they need on the secondary side. 3ways take it from there.
the other aspect IF dealing with a mod/con is insuring lowest return temps possible to boiler yes?0 -
Agreed. That’s great information. As you say it’s all dynamic until equilibrium is reached.Gordy said:hot_rod said:With a few numbers known, you can calculate the output side temperature..it will always be changing, so you need a mixing device if you want a set or predictable supply to heat emitters.
The math starts on page 39
https://www.caleffi.com/sites/default/files/file/idronics_15_na_2019.pdf
Especially as actuators open and close in loops etc.
The most simple approach is insuring mixing devices get the temps they need on the secondary side. 3ways take it from there.
the other aspect IF dealing with a mod/con is insuring lowest return temps possible to boiler yes?
Correct, in a perfect design the loads are met with the lowest possible supply temperature, the system has cruise control, ODR for example. Lastly the boiler runs good cycle lengths at condensing temperatures as much as possible
So the careful design steps give you the best shot of hitting all the goals. With radiant, the extra cost of tighter tube spacing, for example, give you the best shot at low SWT requirements. The heatload is very dynamic. The more dynamic your system, the better the match up.
So systems from mild to wild are possible, even Frankenstein hydronics if you are inclined.
Without saying, again, the structure dictates all of this. The more efficient the building shell the less btu to get er done
Bob "hot rod" Rohr
trainer for Caleffi NA
Living the hydronic dream1 -
This diagram assumes that there are no other zones or DHW tanks on this system. Also I was not sure of the Boiler Boss model number or the Carrier Boiler model number. The Boiler Boss I selected is Model SR201. The Carrier boiler I selected is equipped with Honeywell L8148J with B1 and B3 to power a 24VAC gas valve.
If any of these assumptions are incorrect, or if there are additional zones for heat or DHW, those additions or corrections are available on request.
The logic is set up for a cold start boiler. There is no control for minimum boiler return temperature, however the SEP should allow for a quick rise in boiler return temperature without additional control requirements.
If there is a need for additional controls or there is a flaw in this logic, please advise.
Edward Young Retired
After you make that expensive repair and you still have the same problem, What will you check next?
0 -
@EdTheHeaterMan, I am blown away, this is really nicely done, thank you.
I would like to pick your brain a little, couple questions and more background info below;
1. Yes, the Boiler Boss is the 2-zone, SR201
2. Carrier Boiler model is BW3AAN000075ABAA (Series XEB-3) 75k BTU at 85% efficiency
3. Honeywell Aquastat is L8148A (not the "J" model) see wiring layout image below for the control. Possibly the contractor installed the "A" by mistake? Maybe that is why the primary pump only runs when the boiler is firing? Pump should continue running after the boiler reaches temperature as long as there is a call for heat by the zones, correct? I planned on pulling the pump wires off the aquastat and controlling with a relay based on a call for heat, not the boiler firing. good/bad idea?
4. Layout you did was outstanding! Going to study it for a while so it can sink in, but a couple of initial questions.- You show 2 primary pumps, currently I only have one primary pump. I planned on a total of 15 feet of primary piping (1 1/4" black iron) - it doesn't seem like 2 pumps are needed?
- Rather than closing the primary loop by joining the supply to the return on the downstream side of the Sep, I had planned on capping the end of each run so that I had a supply 'header" and a return "header" that attached to the Sep. I have seen this piping recommended in a couple of articles. Would that work better? The Sep would account for any flow discrepancies I think.
- The Taco mixing valves allow for 3 sensors, you showed just the system supply sensor in your drawing. I planned to add a second sensor on each valve that sensed the boiler return temp. The valve is smart and will auto close off the valve supply flow to the system when low boiler return temp is sensed to protect the boiler. Not sure of the best placement for that sensor though.
- No DHW or outdoor reset planned.
- What are your thoughts concerning placing the zone check valves on the return, rather than the supply, close to the return header, to prevent any back flow?
- One last request - any recommendations on where to place shutoff and purge valves for easy flushing and maintenance?
Greg0 -
@EdTheHeaterMan geez, forgot the aquastat image;
also, the carrier boiler wiring diagram if it is helpful;
0 -
The L8148A is for line voltage burner (like an oil burner) but the factory use this control to power a combustion air (or inducer) fan along with a 24 VAC step down transformer for the gas valve. (basically the same thing I did for the zone circulators and transformers to power the Taco Valves). So that control is probably OEM factory issue.Maybe that is why the primary pump only runs when the boiler is firing? Pump should continue running after the boiler reaches temperature as long as there is a call for heat by the zones, correct?. Not so. The L8148 control should operate the circulator when ever there is a call for heat. Can you photograph the inside wires of the L8148 from about 3 feet away so I can see where they go. Maybe 2 different angles in case some wires cover where other wires are connected.
On a call for heat (T T jumped) C1 and C2 get 120 VAC all the time. B1 and B2 get power thru the high limit. Here is the internal wiring of that control
Bottom of illustration is ladder diagram that is very basic. 24V transformer onboard the L8148 powers the 1K relay coil when the thermostat is calling. Contacts 1K1 power B1 thru the high limit and contacts 1K2 power C1 with no way to shut off the power. If the
factory installed jumper between L1 an 3 is removed, then what ever is connected to 3 is the reason the circulator is stopping.
1. Does your control have the Jumper between L1 an 3? If not,
2. What is connected to wire terminal 3 on the L8148?
3. Is the optional series 60 control used?
4. Does your boiler have a tankless coil for DHW?
Edward Young Retired
After you make that expensive repair and you still have the same problem, What will you check next?
0 -
Answers in Itilac1. You show 2 primary pumps, currently I only have one primary pump. I planned on a total of 15 feet of primary piping (1 1/4" black iron) - it doesn't seem like 2 pumps are needed? that is 2 pumps with different names system pump and boiler pump. The system pump moves the water thru the primary system that is hydraulically separated from the boiler loop. There are 2 pumps to keep the water moving in both system as needed . (Your idea may work though)
2. Rather than closing the primary loop by joining the supply to the return on the downstream side of the Sep, I had planned on capping the end of each run so that I had a supply 'header" and a return "header" that attached to the Sep. I have seen this piping recommended in a couple of articles. Would that work better? The Sep would account for any flow discrepancies I think. This causes the system pump to dead head against the closed zone valves... that you want to eliminate. (you may be able to eliminate the system pump with your idea)
3. The Taco mixing valves allow for 3 sensors, you showed just the system supply sensor in your drawing. I planned to add a second sensor on each valve that sensed the boiler return temp. The valve is smart and will auto close off the valve supply flow to the system when low boiler return temp is sensed to protect the boiler. Not sure of the best placement for that sensor though. I believe the SEP will take care of that but @hotrod Bob is better equipped to answer that
4. No DHW or outdoor reset planned.
5. What are your thoughts concerning placing the zone check valves on the return, rather than the supply, close to the return header, to prevent any back flow? The check valve location was selected by the taco diagram I pirated for the illustration
6. One last request - any recommendations on where to place shutoff and purge valves for easy flushing and maintenance? Everywhere. You can never have too many valves as long as they are full port valves
But placing purge or boiler drain valves at the bottom of things is always a good idea.Edward Young Retired
After you make that expensive repair and you still have the same problem, What will you check next?
0 -
@EdTheHeaterMan
answers in Bold, Italic
1. Does your control have the Jumper between L1 an 3? (yes, it is installed)
2. What is connected to wire terminal 3 on the L8148? (it is empty)
3. Is the optional series 60 control used? (no)
4. Does your boiler have a tankless coil for DHW? (no)
The aquastat is about 6 inches from the water heater... that will get moved when I repipe it. But for now very hard to get a picture with my phone. However, I think I figured out the issue causing the primary pump to shut off when the boiler stops firing, see below;
The room stats in each zone go back to the boiler boss. On a call for heat, the Boiler Boss closes the contact on terminals X1 and X2. These 2 terminals are connected to a Tekmar 356. The Tekmar then comes alive and heats up the T T terminals on the aquastat. The Tekmar has a boiler supply temp sensor and controls the T T output based on the boiler temp range programmed, not a call for heat.
So in a nutshell, the aquastat loses the call for heat (TT energized from the Tekmar) when the boiler supply reaches the upper setpoint limit and does not get powered again (TT) until the boiler supply temp falls to the lower limit -- all this while there is a continuous call for heat! Without the TT energized the primary pump can't run... correct?
I am not a professional, but it sure sounds like this was installed with faulty control logic.
To fix this my plan is to come out of the main transformer, rout through the X1 and X2 contacts on the BBoss to the coil of a DPST 24vac relay. Then run the primary pump and the Tekmar heat input through the 2 poles on the relay. One pole will be 24vac while the other is 120vac, but they will be separate circuits. In my mind this makes sense, but let me know if I am missing anything.
This will be temporary to get me through the next couple of months, then I will start over and the Tekmar will not be used.
Let me address your second comment from above in another post.
Thanks again!
Greg1 -
-
@EdTheHeaterMan
Here is a link to a very good article, titled "Piping layouts to avoid in hydronic systems":
https://www.hpacmag.com/features/siegenthaler-hydronic-piping-layout/
John suggests, in the article, that "losing the loop", using a sep and generously sized supply/return headers that are kept short ... will result in almost no pressure loss along the header. So no need for the second system pump in your drawing - the individual zone pumps will be sufficient.
Here is the "no loop" drawing from his article. (it's a 5 to 10 minute read)
It shows 2 boilers, but the layout would be the same for a single boiler.
ALso, here is another diagram of that Taco I-series mix valve showing the 3 sensors.. seems like an easy way to accomplish boiler protection and outdoor reset!
0 -
I think I mentioned The Tekmar way up earlier, but didn't understand exactly how it was controlling the aquastat - also, I misspoke before, the Tekmar just closes the 2 "T" terminals which energizes the main control relay in the aquastat. The aquastat is dead until the TT terminals are shorted. I will order a DPST relay on Amazon right now and install it when it arrives. That should fix me up for now,EdTheHeaterMan said:Didn't know about the Tekmar.
But I think you are beginning to understand the logic of your system and that you may need a better design.
Any way I can talk you into updating that drawing of yours to show headers, no system pump, check valves on the return line and the boiler sensors for each mix valve? My pencil drawings are not very good. Are you using any special software or just a paint program?0 -
There is no "only one way" to do this. I think your idea has merit. "loosing the loop" will save on purchasing and installing the System Pump. The zone circs will do the job of taking the heat as needed from the SEP. I believe that operating the Taco valves and the zone pump from the Erie 201 will work well and avoid pumping against closed valves. If you look at the SEP there is a place to put the Boiler Sensor. but you will only fit one of the sensors. the other zone will need to strapped to the boiler return pipe and insulated. This will keep the SEP at the minimum temp to keep the boiler from receiving cold return water. The System sensor will be places on the loop to maintain the floor temperature.
The Taco I Series valves will eliminate the need for the Tekmar 365. So the injection pump and all the related piping is gone. All replaced with the SEP and the Taco valves That puts you back the my wiring diagram (with only a boiler pump ...no system pump)Edward Young Retired
After you make that expensive repair and you still have the same problem, What will you check next?
0 -
That is a different valve head. If you purchase that valve head then you can eliminate the Tekmar 365 because all the functions you want are in the Taco I-series valves. Good find!GregRem said:
...ALso, here is another diagram of that Taco I-series mix valve showing the 3 sensors.. seems like an easy way to accomplish boiler protection and outdoor reset!Edward Young Retired
After you make that expensive repair and you still have the same problem, What will you check next?
0 -
Well said. Good point about keeping the SEP from going below minimum boiler temp. The Tekmar is doing a terrible job now, I am hoping the new Taco valves are better. I am getting a lot of ... well, rust flecks? falling out of the boiler vent piping. Is that from the Tekmar not doing a good job of keeping the boiler above min temp?0
Categories
- All Categories
- 87K THE MAIN WALL
- 3.2K A-C, Heat Pumps & Refrigeration
- 58 Biomass
- 426 Carbon Monoxide Awareness
- 113 Chimneys & Flues
- 2.1K Domestic Hot Water
- 5.7K Gas Heating
- 109 Geothermal
- 161 Indoor-Air Quality
- 3.6K Oil Heating
- 70 Pipe Deterioration
- 994 Plumbing
- 6.3K Radiant Heating
- 389 Solar
- 15.4K Strictly Steam
- 3.4K Thermostats and Controls
- 54 Water Quality
- 44 Industry Classes
- 48 Job Opportunities
- 18 Recall Announcements