What adapter and thread to use? Boiler Line Tee

The Tee is a 3/4"x3/4"x1/2" Bell and Gossett Tee as pictured below.
There is a chance I can cut the copper right above the existing adapter and sweat on a coupling, but the existing copper piece is vertical and has lots of deposits from the slow drip over the years so I may not be able to clean it up well enough to get a coupling on reliably so I'm considering changing out the threaded adapter too.
Will this copper adapter be compatible and ideal? Or is some type of black steel required that will then transition to the copper?
https://www.supplyhouse.com/Elkhart-30436-1-2-FTG-x-Male-Street-Adapter
No clue if I'll be able to get the old threaded adapter out of the Tee, any tips? Use penetrating oil and heat?
Tips appreciated, thanks.
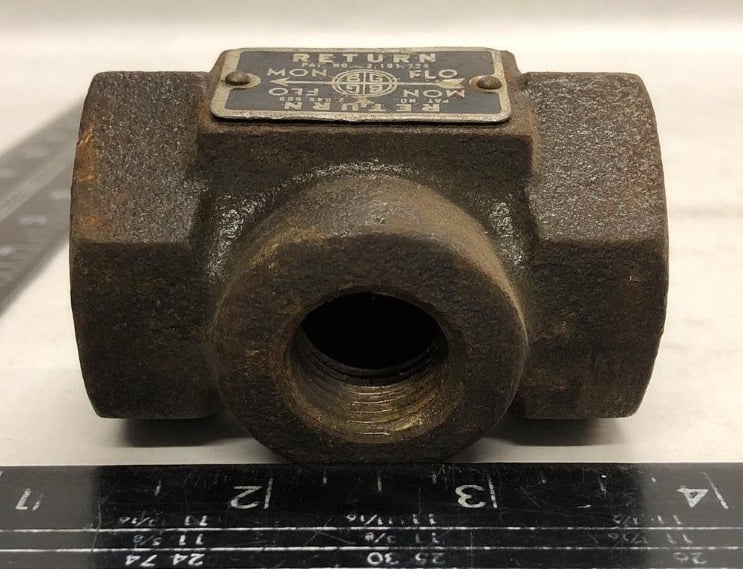
Comments
-
The threaded side will thread into the 1/2" thread on your tee. The copper end of the fitting you shared is a "street" which means the copper side will not slide over copper tube, it will go into a copper coupling.
this one is the standard male adapter that will sweat over copper pipe
https://www.supplyhouse.com/Elkhart-30310-ELKHART-1-2-Copper-x-Male-Adapter-1 -
Thanks for that! Didn't realize that part was a street off hand but I had the right idea, I was so caught up in thinking about the threads. Thanks for that link with the proper part.GGross said:The threaded side will thread into the 1/2" thread on your tee. The copper end of the fitting you shared is a "street" which means the copper side will not slide over copper tube, it will go into a copper coupling.
this one is the standard male adapter that will sweat over copper pipe
https://www.supplyhouse.com/Elkhart-30310-ELKHART-1-2-Copper-x-Male-Adapter
Any thoughts on getting the old one out? Think back then (late 1940's, or early 1950's) that threaded piece is steel like the Tee was and then transitioned to copper? Unsure if they were using copper threaded adapters back then. Any tips on getting that one one out safely?0 -
That’s a Monoflo tee which diverts some of the flow to the radiator. It has to remain in the system.
Getting the old male adapter out may be difficult. Is it actually leaking from the adapter or above it?
Pics would help.Bob Boan
You can choose to do what you want, but you cannot choose the consequences.0 -
-
You will get that out, no problem. Just use a small pipe wrench, like an 8" or a 12". Whatever fits to give you leverage. its only a 1/2" c x m adapter. You can even go smaller and add a longer nipple at the end of pipe wrench handle to increase your leverage if needed. Really depends on how much room you have to play with.2
-
I want to keep the Tee in place, but change the 1/2" adapter where it pipes off to copper to the radiator. Here is a photo below. There is a pinhole leak right below the 90 joint where it bends off causing the water to drip downward onto the tee. If I could cut the copper and clean it up and just use a coupling I would go that route, but the mineral deposits on that copper may not clean up well enough. I do know this copper is old copper and the walls are extremely thick compared to today's copper tubing but I'd still rather change out the entire pipe that adapts into the Tee, unless it makes sense to just try to cut and clean up that copper and use a coupling and not touch the threaded adapter. It looks rough but the threaded adapter is holding water ok, the pinhole weep that's causing this chaos.Ironman said:That’s a Monoflo tee which diverts some of the flow to the radiator. It has to remain in the system.
Getting the old male adapter out may be difficult. Is it actually leaking from the adapter or above it?
Pics would help.
0 -
After getting the old adapter out i would chase those threads into the cast iron to clean them off so you can get the new adapter in a little deeper. You don't want to bottom out on the corrosion in the fitting.0
-
So you think that will come out ok? I shared a picture above of it. This gives me lots of hope. Agreed, I will plan to chase the threads and clean them up a bit. Is pipe dope ideal on this joint?pedmec said:After getting the old adapter out i would chase those threads into the cast iron to clean them off so you can get the new adapter in a little deeper. You don't want to bottom out on the corrosion in the fitting.
0 -
Sure do. steady pressure on the wrench. Its a small fitting. Generally the smaller the fitting the easier it should come out. But having said that there are times when things don't go as planned but you should be OK. i would worry more about the threads on the cast iron monoflo. If the threads suffered any electrolysis between the cast iron and copper. That's why i suggested chasing the threads on the cast iron so you can get the new adapter fitted snuggly into the tee. Use teflon tape and dope on the male adapter threads.0
-
Thanks for the extra tips, I'll keep you all posted how I make out.pedmec said:Sure do. steady pressure on the wrench. Its a small fitting. Generally the smaller the fitting the easier it should come out. But having said that there are times when things don't go as planned but you should be OK. i would worry more about the threads on the cast iron monoflo. If the threads suffered any electrolysis between the cast iron and copper. That's why i suggested chasing the threads on the cast iron so you can get the new adapter fitted snuggly into the tee. Use teflon tape and dope on the male adapter threads.
Thinking ahead if I have issues with getting it out, or with thread issues, if I had to cut out that monoflo and replace it, what is todays available part equivalent? Also, with the black pipe (2" I think) for the main boiler supply lines, what is common when replacing something like this? Assuming the black pipe would be cut out and then some type of union would be used vs. trying to deal with unthreading-rethreading these old pipes.0 -
That copper will clean up fine so that you can sweat to it. Just use a strip of emery cloth like you're shining a shoe, be sure to rotate your hands around it as you buff so you get all sides. Clean it before you cut it so it is held in place by the existing fitting. If I were a beginner I would wrap a wet rag around the male adapter because that 50/50 solder will melt at a lot lower temp than the lead free solder you'll be using on the new fittings, unless you're careful about where you put the heat or you put a heat sink on that fitting you will re-melt the solder in that adapter(which shouldn't be a problem but it could be).0
-
Thanks for the tips. I may try to do as you said and see how much it cleans up. The pin hole is hard to pinpoint if its on the joint of the 90 or in the pipe itself, but I know the walls on this old copper is extremely thick so it may be salvageable. Lets see how far the emery cloth gets me and if it cleans up, I may give this a go before I tackle replacing the entire adapter. My luck lately and I will probably be going the harder routemattmia2 said:That copper will clean up fine so that you can sweat to it. Just use a strip of emery cloth like you're shining a shoe, be sure to rotate your hands around it as you buff so you get all sides. Clean it before you cut it so it is held in place by the existing fitting. If I were a beginner I would wrap a wet rag around the male adapter because that 50/50 solder will melt at a lot lower temp than the lead free solder you'll be using on the new fittings, unless you're careful about where you put the heat or you put a heat sink on that fitting you will re-melt the solder in that adapter(which shouldn't be a problem but it could be).
0 -
I’d clean the cu nipple up, cut the ell off right at the socket, and sweat or press another ell on. You’ll probably need a coupling on the other side.
Im not as optimistic about removing that adapter from the tee as some other folks may be. I work replacing old boilers, radiators and piping all the time and I’ve seen some like that that were ridiculous. Last week, I barely got a 1/2” adapter like that out of a black iron pipe using a 36” pipe wrench.
And good luck finding that black Monoflo tee: they haven’t made those for decades. Copper ones are still available, but probably only up to 1-1/4”.Bob Boan
You can choose to do what you want, but you cannot choose the consequences.0 -
Great insight and experience, I appreciate you sharing this. So in this case would you heat the adapter that is threaded into the tee and then get that piece of copper and elbow out, and then sweat a new piece in? I was thinking I may try to clean up the copper tube before the upper elbow with hopes that I can get it clean enough to put a coupling on and not have to mess around directly with the adapter that is threaded into the tee.Ironman said:I’d clean the cu nipple up, cut the ell off right at the socket, and sweat or press another ell on. You’ll probably need a coupling on the other side.
Im not as optimistic about removing that adapter from the tee as some other folks may be. I work replacing old boilers, radiators and piping all the time and I’ve seen some like that that were ridiculous. Last week, I barely got a 1/2” adapter like that out of a black iron pipe using a 36” pipe wrench.
And good luck finding that black Monoflo tee: they haven’t made those for decades. Copper ones are still available, but probably only up to 1-1/4”.
There is a used Tee on eBay right now if I needed to replace it, but it could sell at anytime and then I'd be stuck cutting out that entire length of main pipe and would need to adapt it with whatever is available in todays market. Hoping to not have to go this route.
Thinking this through after you've all shared so many great tips, I think i'll try the following:
-First I'll try to clean the existing copper and see if I can get a clean enough surface and check if the pin hole is high up on that piece of copper. if that works, I'll go ahead and cut it out at that spot and use a coupling. This scenario won't require me to touch the Tee, or the threaded adapter.
-If that doesn't clean up well, I will then try to get the small piece of vertical copper out of the threaded adapter that goes into the tee and hope to get it clean enough to then sweat in a new piece of copper. That hopefully lets me not have to deal with removing the adapter still
-If neither of the 2 above work or fail along the way, I'll have no choice but to try to get the old threaded adapter out of the tee, chase the threads, and put a new one back in
-If I fail at all 3 above, I'm guessing I'd then have to cut out the section of black pipe (2"?), get a new Tee, and then some type of union/adapters to go from the existing black pipe to patch in this middle piece where the new tee will sit.
I'm going to use all the knowledge you have all shared and keep my fingers crossed and start from the top. Any last minute tips are appreciated, I'll let you all know how I make out. Thanks again!0 -
No, leave the male adapter alone. Cut the ell off right where the copper nipple enters the bottom of the ell and work from there with a new ell.
It looks like someone used a Sharkbite fitting further up. I don’t care for them, but If your not very proficient sweating pipes, you might wanna consider using one their 90’s to replace the leaking one. Your very close to a PVC line which won’t like the heat from a torch.
The other thing would be using a press fitting. Most plumbing supplies will rent the tool.Bob Boan
You can choose to do what you want, but you cannot choose the consequences.0 -
Judging from there it is corroded , the leak has to be in the ell somewhere or maybe on the horizontal outlet of the ell. If you know someone with a 100w iron (not gun) you could just clean up where the pinhole is, drain the pipe, put some flux on the pipe and solder over the hole.
It looks like supplyhouse.com has 2" diverter tees in copper although they are pricey so you could cut out a section of the black iron and replace it with copper and adapters0 -
I don't like the SharkBite fitting in there.
If you need to use a solder free connection I would suggest a compression fitting. Adapters, ells, couplings are all available at plumbing or box stores. Compression fittings are common in Euro hydronic piping systems. Suited for pressure and temperature.
I'd start at the tee, also. Open mesh sand cloth cleans that green scale off quickly.Bob "hot rod" Rohr
trainer for Caleffi NA
Living the hydronic dream1 -
This strategy is what I'm hoping to try first. I cleaned up the pipe, have a look at the picture below and share any extra feedback. A friend I think has a lower end handheld propress crimper he bought off Amazon for a few joints that he said worked well, maybe I'll see if I can borrow that possibly if I can wait, otherwise I'll be taking a stab at sweating.Ironman said:No, leave the male adapter alone. Cut the ell off right where the copper nipple enters the bottom of the ell and work from there with a new ell.
It looks like someone used a Sharkbite fitting further up. I don’t care for them, but If your not very proficient sweating pipes, you might wanna consider using one their 90’s to replace the leaking one. Your very close to a PVC line which won’t like the heat from a torch.
The other thing would be using a press fitting. Most plumbing supplies will rent the tool.
Interesting, didn't think of that. I have a heavy duty soldering gun I could do that with. Now that I cleaned it up its hard to tell where it was leaking from. I drained the system since I'm changing circulator pumps and the system has minimal shut offs so the entire system is drained now while I do that. So I'd have to fill it back up to pinpoint it. Depending my progress on the circulator pumps and getting the boiler back up and running I'll be able to pinpoint it then, or just cut it out and start with a fresh joint.mattmia2 said:Judging from there it is corroded , the leak has to be in the ell somewhere or maybe on the horizontal outlet of the ell. If you know someone with a 100w iron (not gun) you could just clean up where the pinhole is, drain the pipe, put some flux on the pipe and solder over the hole.
It looks like supplyhouse.com has 2" diverter tees in copper although they are pricey so you could cut out a section of the black iron and replace it with copper and adapters
The sharkbite is only being used temporarily as a cap. The radiator on that feed is cracked so I cut the line and sharkbite capped it so I could let the rest of the system run. I really like using them in a pinch or for temporary work, but I can't believe some people use them and bury them behind walls. I know a friend who had a well respected plumber come over and do his new shower plumbing, I was shocked to see they ran all pex and used sharkbites, that was eye opening. I told him next time to find a new plumberhot_rod said:I don't like the SharkBite fitting in there.
If you need to use a solder free connection I would suggest a compression fitting. Adapters, ells, couplings are all available at plumbing or box stores. Compression fittings are common in Euro hydronic piping systems. Suited for pressure and temperature.
I'd start at the tee, also. Open mesh sand cloth cleans that green scale off quickly.
Is there a standard compression fitting that goes over 1/2" copper and has an adapting end? I checked Home Depot and the only compression 1/2 fittings they had didn't look like they would adapt as expected, can you share a photo of one?
This is absolutely very close to the PVC pipe beside it. I have one of those heat shield clothes I was planning to use to help minimize the heat exposure and I'll be trying to shoot the torch from the side so its not a direct hit against it. I like the suggestion to put a wet rag on the tee/adapter if I decide to leave that in place so the upper part of the copper takes the majority of the heat. If I can't get my hands on that propress hand crimp tool, I am going to get the torch out and give it a go starting at the top elbow, get a coupling on, and adapt from there.
Here is a picture of the pipe cleaned up.
0 -
You’re gonna need to clean that run of solder off before any type of new fitting will work.
Under those conditions, I’d really look at using a ProPress. You can rent one at most supply houses. Just make sure you prep the pipe properly (clean, round and smooth with no nicks, blobs of solder, gouges, etc.). Ream the pipe inside and out. Put a wad of tissue paper inside the pipe while reaming to catch the shavings. Then carefully remove it.
Copper pipe on a closed loop hydronic system should never develop pin holes. Was there a lot of flux left on it from when it was soldered? Are there leaks on the system elsewhere?Bob Boan
You can choose to do what you want, but you cannot choose the consequences.0 -
Thanks again for the tips. That handheld crimp propress tool is sounding better and better. I tried to call local supply houses and nobody has the tool available for rent, some have it but its rented and they have no expected return date. If I can't borrow my friends handheld crimper, I see a few crimpers on Amazon for around $150 that I may consider buying since I know I'll have more use-cases in the soon future. Not the most ideal tool, but the majority of reviews are good so I may go this route. Anyone ever use a handheld one with success?Ironman said:You’re gonna need to clean that run of solder off before any type of new fitting will work.
Under those conditions, I’d really look at using a ProPress. You can rent one at most supply houses. Just make sure you prep the pipe properly (clean, round and smooth with no nicks, blobs of solder, gouges, etc.). Ream the pipe inside and out. Put a wad of tissue paper inside the pipe while reaming to catch the shavings. Then carefully remove it.
Copper pipe on a closed loop hydronic system should never develop pin holes. Was there a lot of flux left on it from when it was soldered? Are there leaks on the system elsewhere?
I don't see any other leaks currently and the system is holding pressure overall, but there is definitely some corrosion/bimetal looking growth on other joints. Whoever did the pipe work on that copper was a sloppy solderer, definitely lots of poured over copper so I'm guessing they left flux all over. I'm planning on updating more of this piping over time so I will expect to replace more and more in the off-season.
0 -
I doubt even the mini press jaws will fit against that PVC? And the hand press tool the handles need a lot of room to open.
I'd assemble the adapter and short copper stub first, thread into tee. Then sweat or press the ell and coupling where you have more clearance.
If you can protect the PVC to sweat find a long sweep 5/8 refrigeration ell so you could cut the existing ell too and use a long seep. press ells will be long sweep also.
1/2" copper tube that you have is 5/8" OD. So sometimes you need to look at 5/8" compression adapters and fittings.
Home Depot, Ace Hardware, plumbing wholesale, Amazon, SupplyHouse.com all have 5/8" compression fittings.
A number of ways to do this depending on what tools you have available. Soldering may or may not be the easiestBob "hot rod" Rohr
trainer for Caleffi NA
Living the hydronic dream0 -
Ironman said:You’re gonna need to clean that run of solder off before any type of new fitting will work.
Under those conditions, I’d really look at using a ProPress. You can rent one at most supply houses. Just make sure you prep the pipe properly (clean, round and smooth with no nicks, blobs of solder, gouges, etc.). Ream the pipe inside and out. Put a wad of tissue paper inside the pipe while reaming to catch the shavings. Then carefully remove it.
Copper pipe on a closed loop hydronic system should never develop pin holes. Was there a lot of flux left on it from when it was soldered? Are there leaks on the system elsewhere?
0 -
I agree about the hand press tool: you have to be able to get the handles 180* for most of them to fully open.
Cut the ell off right where the pipe enters the socket and the see if you can unscrew the male adapter from the tee without destroying it. If you can, then good; if you can’t, then try one of the mechanical joining methods suggested.
Dont booger the copper pipe while trying to unscrew the adapter.Bob Boan
You can choose to do what you want, but you cannot choose the consequences.0 -
A threaded steel nipple, threaded ell, another nipple, then transition to copper where it is easier to work onBob "hot rod" Rohr
trainer for Caleffi NA
Living the hydronic dream0 -
Another option, since you have to replace the runout to the radiator anyhow, would be to use oxygen barrier pex. Just use a compression to npt adapter or ell adapter and run pex to the new radiator.
You can get them with male or female thread depending on what adapter you want to connect to them
https://www.supplyhouse.com/Jones-Stephens-C74-090LF-69-108-5-8-OD-x-1-2-MIP-Brass-Compression-Elbow-Lead-Free
https://www.supplyhouse.com/Bluefin-BCM058-050-5-8-OD-x-1-2-MIP-Brass-Compression-Connector-Lead-Free
1/2" copper pipe is 5/8" outside diameter and compression fittings are usually spec'd as tub size which is measured by outside diameter.1 -
Thanks for explaining that about 5/8" being outside diameter, didn't realize that.mattmia2 said:Another option, since you have to replace the runout to the radiator anyhow, would be to use oxygen barrier pex. Just use a compression to npt adapter or ell adapter and run pex to the new radiator.
You can get them with male or female thread depending on what adapter you want to connect to them
https://www.supplyhouse.com/Jones-Stephens-C74-090LF-69-108-5-8-OD-x-1-2-MIP-Brass-Compression-Elbow-Lead-Free
https://www.supplyhouse.com/Bluefin-BCM058-050-5-8-OD-x-1-2-MIP-Brass-Compression-Connector-Lead-Free
1/2" copper pipe is 5/8" outside diameter and compression fittings are usually spec'd as tub size which is measured by outside diameter.
Awesome recommendations, thanks to everyone for all this knowledge. Last night I went at it and managed to get that top elbow off and cleaned up the vertical piece of copper, leaving the threaded adapter into the tee in place. The copper still has some staining on it from the old solder/flux, but it is smooth so I think it will be workable when it comes time to adapt onto it (Sweat Elow, coupling, compression, etc). Great to know these compression fittings
I have LOTS of questions about changing over the old radiator feed/return lines over to pex but maybe I'll save the bulk of those questions for another post. Quick questions related, Is there anything special about the connections being used when it comes to radiator feed connections, or are common brass Pex adapters used in plumbing the same? Copper to Pex adapters ok, and then oxygen free pex for the new lines? I'll post more questions about this separately though so I can keep the topic in line.
Thanks again everyone!0 -
The fittings are the same, although if you are using plastic fittings you need to make sure they are rated for the temp involved.
The type of pex you need is "oxygen barrier". It has an extra layer on it that limits the amount of air that can migrate through the plastic.0 -
Two basic pex fittings. One uses an insert with a copper ring around the tube that gets crimped down.
Heating guys and gals like expansion type pex fittings. You expand the tube and slip the fitting in. So less flow restriction, pressure drop. Debatable which is the "better" fittingBob "hot rod" Rohr
trainer for Caleffi NA
Living the hydronic dream0 -
Great info, I did some looking around and see there are a lot of good options out there for oxygen barrier pex. I see some people talking about tubing size but the majority of this houses tubing stems off to 1/2" copper lines, or there is some black steel pipe that I'm uncertain of size but it looks closer to 3/4", at least its outer diameter does.mattmia2 said:The fittings are the same, although if you are using plastic fittings you need to make sure they are rated for the temp involved.
The type of pex you need is "oxygen barrier". It has an extra layer on it that limits the amount of air that can migrate through the plastic.
I mostly use cinch pex stainless clamps that I use for general plumbing updates. I see the benefit of the expansion type for sure, I could pick up a tool for $100-$150 if that is the preferred method and if 1/2 pex lines end up not being suitable. The house is pretty small overall so no extremely long runs so I may be ok with the cinch clamps, I'm going to create a new post soon asking some specifics on running pex lines.hot_rod said:Two basic pex fittings. One uses an insert with a copper ring around the tube that gets crimped down.
Heating guys and gals like expansion type pex fittings. You expand the tube and slip the fitting in. So less flow restriction, pressure drop. Debatable which is the "better" fitting
Update
On that original joint I posted about where I removed the upper elbow, I pressurized the system and had the circulation pumps running with a temporary sharkbite on the end of that joint and it held well.
Thanks again everyone!0 -
The Pex type A is the most flexible and easiest to use on retrofits. It accepts that expansion fitting or the crimp ring type.
Type b Pex is stiffer and it is debatable if it is a good match for expansion fittings.Bob "hot rod" Rohr
trainer for Caleffi NA
Living the hydronic dream0
Categories
- All Categories
- 87K THE MAIN WALL
- 3.2K A-C, Heat Pumps & Refrigeration
- 58 Biomass
- 427 Carbon Monoxide Awareness
- 113 Chimneys & Flues
- 2.1K Domestic Hot Water
- 5.7K Gas Heating
- 109 Geothermal
- 161 Indoor-Air Quality
- 3.6K Oil Heating
- 70 Pipe Deterioration
- 995 Plumbing
- 6.3K Radiant Heating
- 391 Solar
- 15.4K Strictly Steam
- 3.4K Thermostats and Controls
- 55 Water Quality
- 44 Industry Classes
- 48 Job Opportunities
- 18 Recall Announcements