Welcome! Here are the website rules, as well as some tips for using this forum.
Need to contact us? Visit https://heatinghelp.com/contact-us/.
Click here to Find a Contractor in your area.
off set nipple

cutter
Member Posts: 312
in Gas Heating
Last winter I lost a Wilo pump. I changed it out with another Wilo pump that was on the other boiler and not being used. All the piping is 1" 1/4 black pipe. It was a bear to get the second gasket in the pump flange. The piping would not budge so I could slip in the gasket. To get the second rubber gasket in I tightened up the first one to give me the room I needed.
I changed the pump from a Wilo to a Grundfos. There is a 3/8" difference in the distance from pump flange to flange. The Grundfos being longer. In order to install the Grundfos it would take a major piping change. P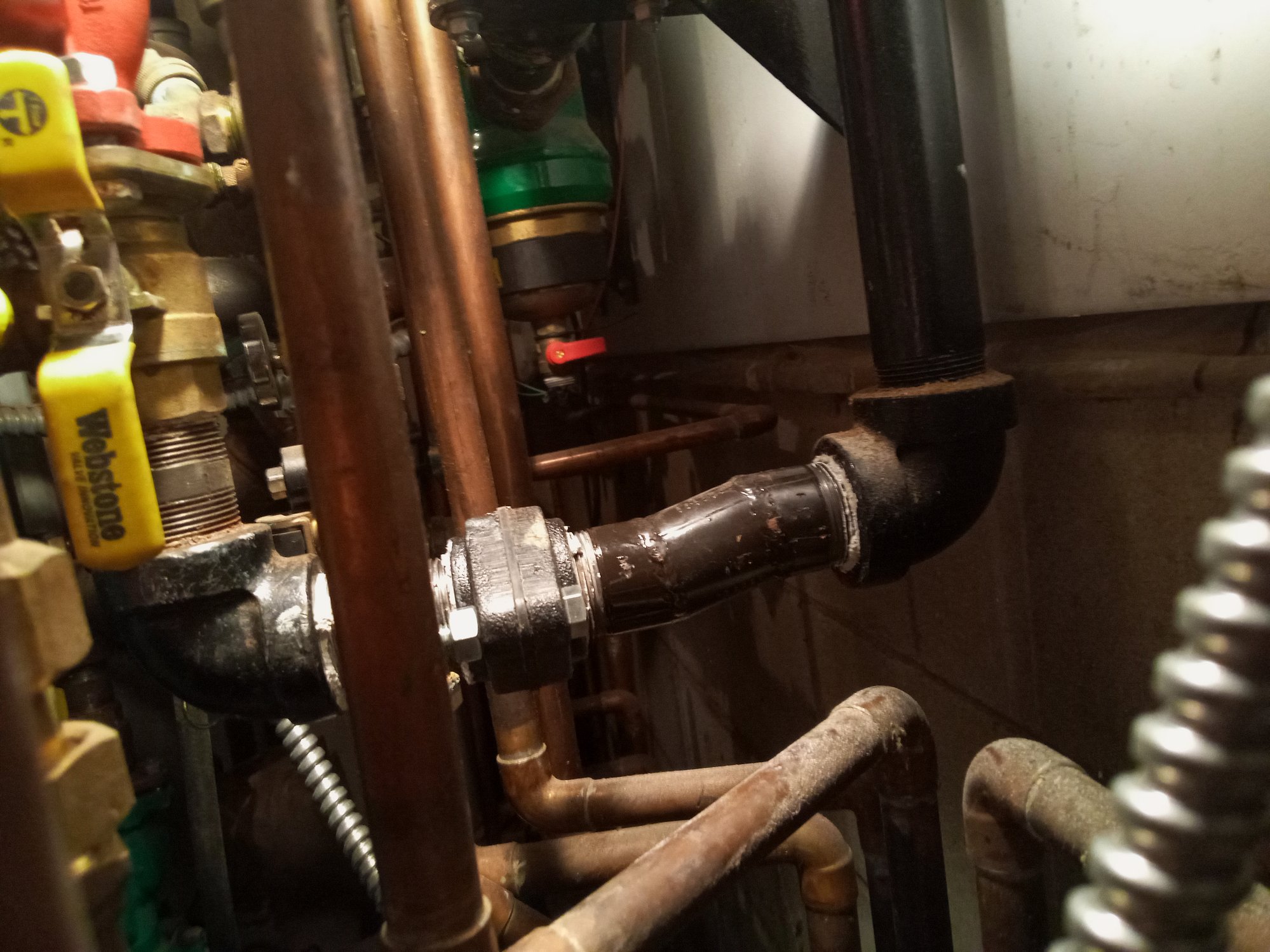
ipe can only be bought in 1/2" increments, unless it is over about 5 1/2"s. I had 2 options, take 3/8" out of a nipple and weld it back together or use an off set nipple. I chose the off set nipple. A longer nipple had the ends cut off at 12 degrees. The nipple was first tightened into the 90 where it was to go and marked for the top of the off set. The ends were put in a jig to the correct length, the center piece was cut to the correct length at 90 degrees and tig welded together. To change that pump without difficulty I added the flange down stream from a 90 degree bend. I don't know how in the world that picture got where it is.
I changed the pump from a Wilo to a Grundfos. There is a 3/8" difference in the distance from pump flange to flange. The Grundfos being longer. In order to install the Grundfos it would take a major piping change. P
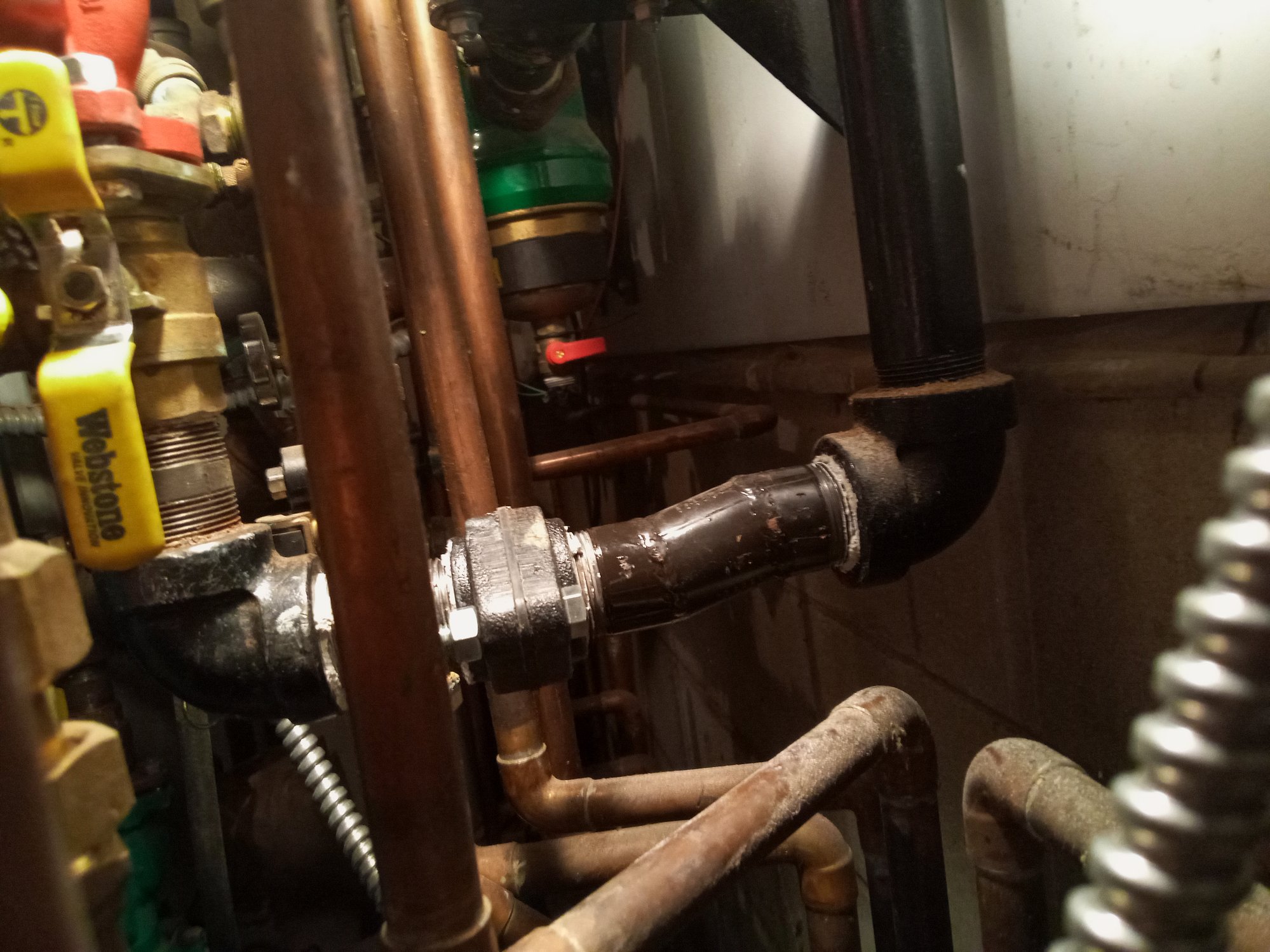
ipe can only be bought in 1/2" increments, unless it is over about 5 1/2"s. I had 2 options, take 3/8" out of a nipple and weld it back together or use an off set nipple. I chose the off set nipple. A longer nipple had the ends cut off at 12 degrees. The nipple was first tightened into the 90 where it was to go and marked for the top of the off set. The ends were put in a jig to the correct length, the center piece was cut to the correct length at 90 degrees and tig welded together. To change that pump without difficulty I added the flange down stream from a 90 degree bend. I don't know how in the world that picture got where it is.
1
Comments
-
-
That is a rotating flange valve and I don't see how that would have helped. I would still have been 3/8" off in lining up the piping.EBEBRATT-Ed said:I would have put the ball valve on the 90 degree elbow on the drop and skipped the flanged valve. Then you would have had room to get it together without welding
0 -
I would never have thought of that, because I don't weld. I might have looked for a bracket or support that was able to be adjusted. Or I would purchase a longer nipple and cut off the exact amount needed to make it the right size then run it thru a pipe threading die to get the threads where they need to be.
If you are a hammer, every problem looks like a nail.
Prime example: A plumber friend called me with a "Zone Valve Wiring" problem. The answer was the thermostat wire from the T-stat to the Valve was OPEN (broken). The solution is a new wire but the existing wire can't be used to pull the new wire thru the wall because of difficult access and the house has Spray On Foam insulation everywhere.
I suggested relocating the thermostat to a place where the wire can be easily routed to the boiler room, like on a wall that has a closet behind it where the can be exposed until it gets to the floor and then drilled through the floor and insulation where it can be easily found and pulled to the boiler room. His comment: "I would have never thought of relocating the thermostat."
Changed the project from almost impossible to a 45 minute fix.
I applaud the out of the box thinking the OP used to solve this problem.Edward Young Retired
After you make that expensive repair and you still have the same problem, What will you check next?
0 -
tap and tap and dyes
cut Draper threads.0 -
I am not picking on the OP his fix is fine and shows a lot of ability. I wish I could tig weld.
My take is how I would have approached this without welding.
The riser pipe dropping down on the right I would leave the 90 degree elbow on there then put a nipple in the elbow and a threaded ball valve or put the thread x flange valve on there.
Then, half a flange on the pump and half a flange on the ball valve and then two nipples or two cut pieces of pipe and your done.
In fact if a shorter nipple was put between the valve (where it is now) and the 90 that probably would have worked.
Unless I am missing something
0 -
Awesome feat of engineering, i love seeing things like this from thinking outside the box. With that said, in instances like this, I'd simply tighten the long side until the 3/8" was made up or replace with copper.0
-
GroundUp said:
Awesome feat of engineering, i love seeing things like this from thinking outside the box. With that said, in instances like this, I'd simply tighten the long side until the 3/8" was made up or replace with copper.
You guys are the professionals and know all the tricks of the trade. This was a very small area with a lot of piping crammed into it. The Grundfos pump was 3/8 longer than the Wilo. the nipples above and below the pump were short 2 and1/2 inches. I could have lengthened the vertical pipe at the wall. In doing so I would have ran into trouble with the horizontal pipe running into zone piping in that area. I don't have you guys experience but I found it impossible to clamp and thread pipe shorter than 5 inches and maybe 6 inches. Even the local ACE hardware could not thread pipe that short. I felt I had two options take 3/8 inch out of a 2 and1/2 inch nipple or make the off set nipple. Taking 3/8 inch out of the 2 and 1/2 inch nipple would have pretty much made a close nipple, and been hard to weld straight. I also needed that flange on the horizontal pipe to making changing the pump easier. The pipe from the pump side of the flange is a standard pipe. The off set pipe measures 4 and 3/8 inches, plus what is in the fittings. Most likely could not have been bought if straight. It took me a little while to figure out how to do this job. The system is up and running.EBEBRATT-Ed said:I am not picking on the OP his fix is fine and shows a lot of ability. I wish I could tig weld.
My take is how I would have approached this without welding.1
Categories
- All Categories
- 87K THE MAIN WALL
- 3.2K A-C, Heat Pumps & Refrigeration
- 58 Biomass
- 427 Carbon Monoxide Awareness
- 113 Chimneys & Flues
- 2.1K Domestic Hot Water
- 5.7K Gas Heating
- 109 Geothermal
- 161 Indoor-Air Quality
- 3.6K Oil Heating
- 70 Pipe Deterioration
- 995 Plumbing
- 6.3K Radiant Heating
- 391 Solar
- 15.4K Strictly Steam
- 3.4K Thermostats and Controls
- 55 Water Quality
- 44 Industry Classes
- 48 Job Opportunities
- 18 Recall Announcements