Welcome! Here are the website rules, as well as some tips for using this forum.
Need to contact us? Visit https://heatinghelp.com/contact-us/.
Click here to Find a Contractor in your area.
Piping pressure gauges and pressure switches
Options
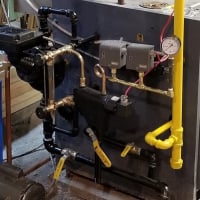
Powe
Member Posts: 35
First post here. I've been the owner of a 110 y.o. house for a year and a half now and I've done some work on the boiler this summer to clean it out and fix some leaks in the plumbing around the boiler. I have some questions at the end, as I am not a boiler technician. And no, I've never worked on a boiler before, but I do have experience in plumbing and electrical. I'm posting a really condensed story of my experience in case it may be useful for other to see it's not that scary of a process.
This was the state of the boiler last summer (2020) ...
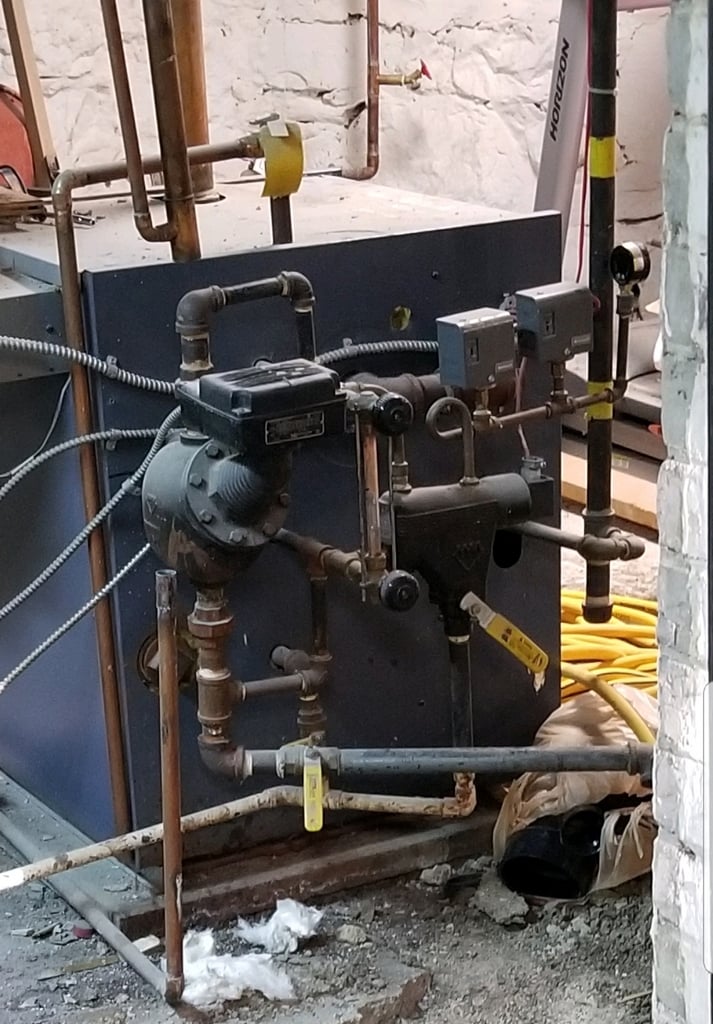
The condensate tank you see in the later pics had been removed temporarily to work on other stuff, but I reinstalled it and "nursed" the boiler through a Canadian winter praying it wouldn't quit on me. It suffered from a continually leaking condensate tank, non-functioning auto-fill solenoid, etc.
Well, it made it through the winter, and this summer I basically took it apart, cleaned everything up and rebuilt it the way it was, but in the process I have learned that some of it is wrong. Namely, the pigtail loop is upside down, and despite being all cleaned up and a new pressure gauge, I am not getting any readings on the gauge, (Note: I replaced the 30PSI gauge with a 3PSI gauge and I still need to get a couple of fittings to install the 30PSI gauge in parallel.
Here's the boiler mid-rebuild with everything taken apart ...
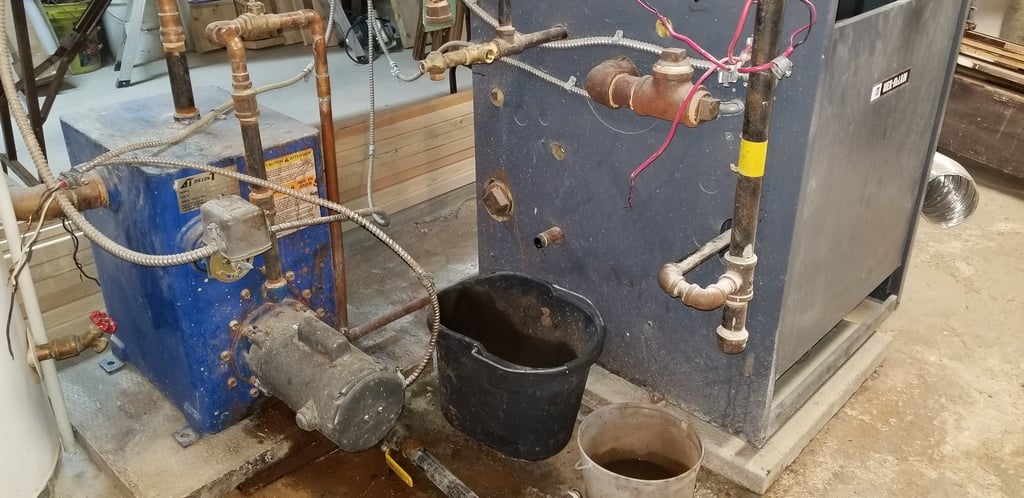
Several of the pipes into the boiler were rotten and basically just pulled out. The blue condensate tank was leaking and the seals on the pump were shot. I rebuilt the condensate tank and replaced the impeller (rotten - probably from too low PH), motor and pump seals and bearings, and cleaned out the tank. The boiler drain was clogged so I flushed that out well and used some boiler cleaner, and then flushed it again. Then I reassembled everything the way it was, and fired it up for the first time. No leaks!!!! Here's a pic when I was almost finished reassembly, with a few connections yet to make.
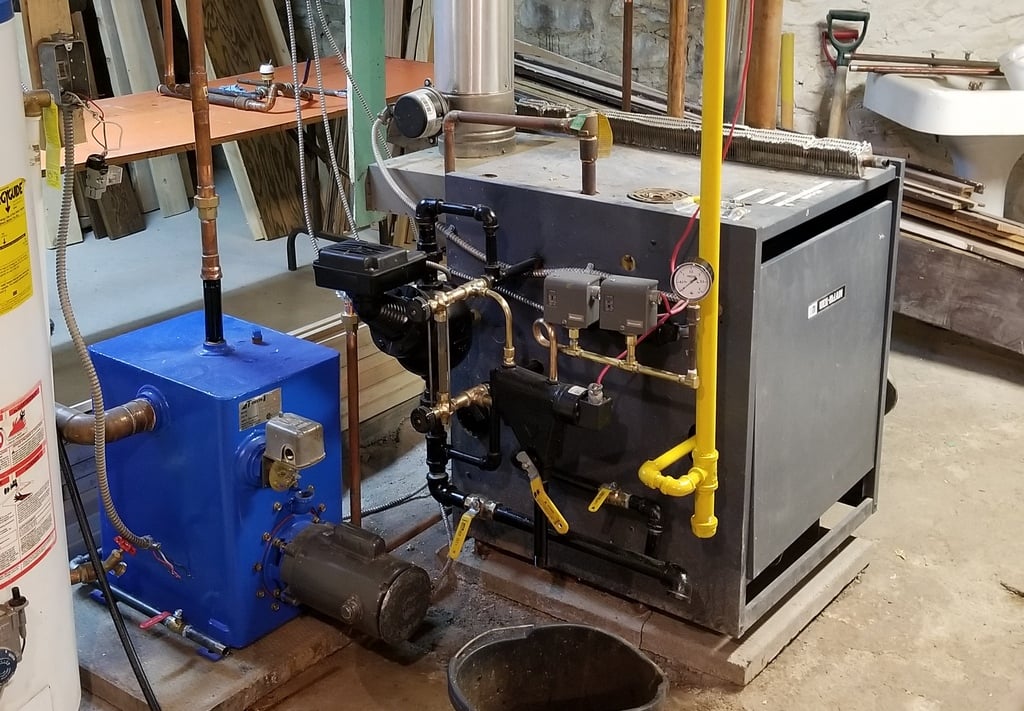
This is the point when I was still cleaning and flushing the boiler. The condensate tank is not connected as I didn't want dirty condensate getting into my clean tank. I had installed a drain valve on the condensate return line and I was just discarding the condensate and manually filling the boiler, while it was firing to run a few cycles of clean water through it.
Now to the question. Obviously the pigtail is installed wrong - the loop needs to be down. The pressure gauge registered .5 PSI during the first firing of the boiler, and after that I get nothing.
I am thinking that the location where the pigtail is installed on the top of the LWCO switch, the entrance to the pigtail is under water, and I don't know if that is a problem? Can anyone answer that? It seems the pressure switches should be reading the pressure above the water level, which they are not doing the way this was originally built.
Since the last pic was taken, I have added another 2" riser between the LWCO and the pigtail to try to make sure the water level doesn't rise to the level of the bottom of the pressure switches (note: these are microswitch not mercury pressure switches). Even with the 2" riser, the pressure gauge still does not read any pressure.
I want to replace the 90 elbow at the top of the steel pipe that goes to the big boiler level switch, with a tee and install the pressure switches and gauges there instead of on the LWCO. Would like some input on whether that is a good place to install them?
Thanks and sorry for the long post here.
Powe
This was the state of the boiler last summer (2020) ...
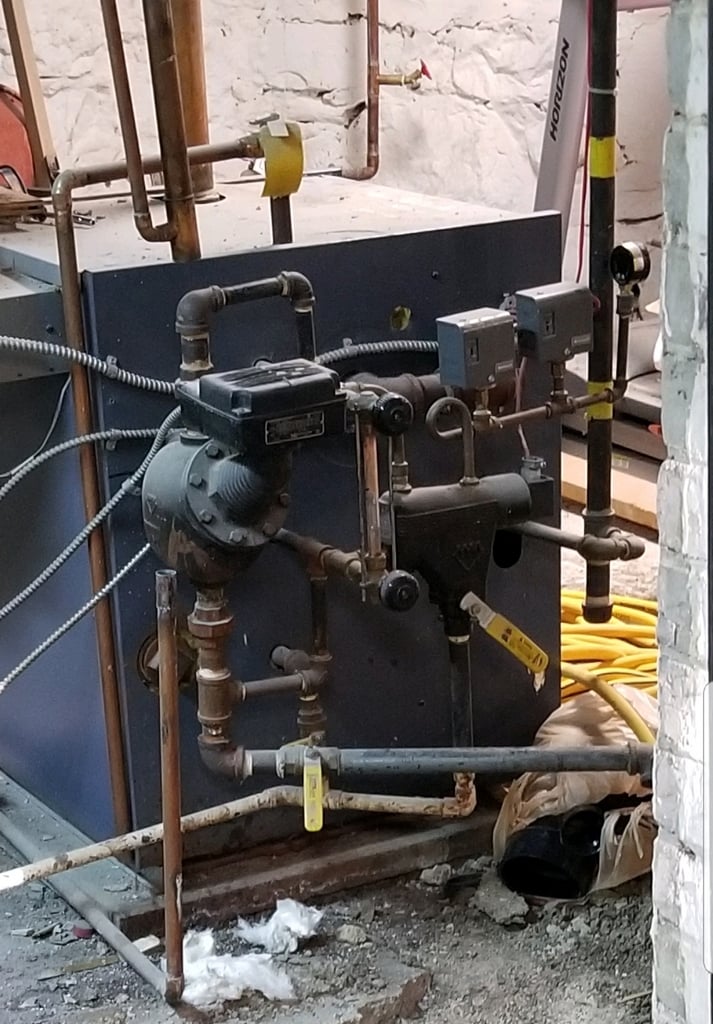
The condensate tank you see in the later pics had been removed temporarily to work on other stuff, but I reinstalled it and "nursed" the boiler through a Canadian winter praying it wouldn't quit on me. It suffered from a continually leaking condensate tank, non-functioning auto-fill solenoid, etc.
Well, it made it through the winter, and this summer I basically took it apart, cleaned everything up and rebuilt it the way it was, but in the process I have learned that some of it is wrong. Namely, the pigtail loop is upside down, and despite being all cleaned up and a new pressure gauge, I am not getting any readings on the gauge, (Note: I replaced the 30PSI gauge with a 3PSI gauge and I still need to get a couple of fittings to install the 30PSI gauge in parallel.
Here's the boiler mid-rebuild with everything taken apart ...
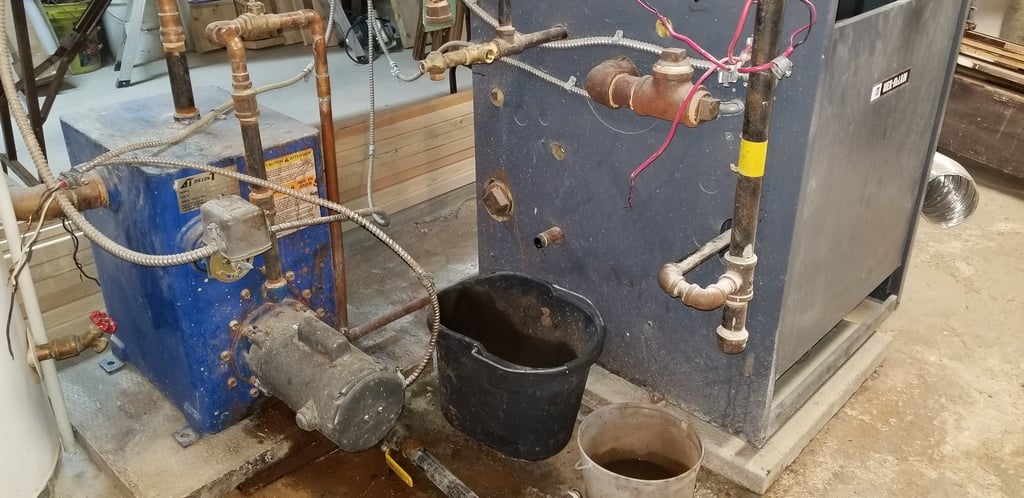
Several of the pipes into the boiler were rotten and basically just pulled out. The blue condensate tank was leaking and the seals on the pump were shot. I rebuilt the condensate tank and replaced the impeller (rotten - probably from too low PH), motor and pump seals and bearings, and cleaned out the tank. The boiler drain was clogged so I flushed that out well and used some boiler cleaner, and then flushed it again. Then I reassembled everything the way it was, and fired it up for the first time. No leaks!!!! Here's a pic when I was almost finished reassembly, with a few connections yet to make.
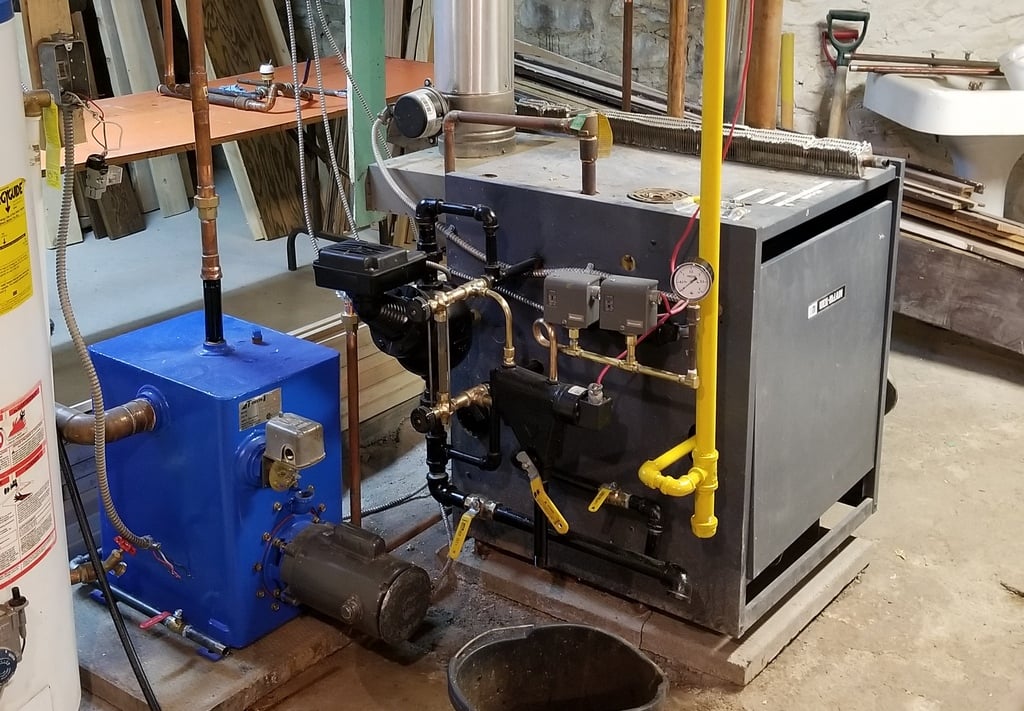
This is the point when I was still cleaning and flushing the boiler. The condensate tank is not connected as I didn't want dirty condensate getting into my clean tank. I had installed a drain valve on the condensate return line and I was just discarding the condensate and manually filling the boiler, while it was firing to run a few cycles of clean water through it.
Now to the question. Obviously the pigtail is installed wrong - the loop needs to be down. The pressure gauge registered .5 PSI during the first firing of the boiler, and after that I get nothing.
I am thinking that the location where the pigtail is installed on the top of the LWCO switch, the entrance to the pigtail is under water, and I don't know if that is a problem? Can anyone answer that? It seems the pressure switches should be reading the pressure above the water level, which they are not doing the way this was originally built.
Since the last pic was taken, I have added another 2" riser between the LWCO and the pigtail to try to make sure the water level doesn't rise to the level of the bottom of the pressure switches (note: these are microswitch not mercury pressure switches). Even with the 2" riser, the pressure gauge still does not read any pressure.
I want to replace the 90 elbow at the top of the steel pipe that goes to the big boiler level switch, with a tee and install the pressure switches and gauges there instead of on the LWCO. Would like some input on whether that is a good place to install them?
Thanks and sorry for the long post here.
Powe
Single pipe steam
Weil-McLain EG/PEG -50
175K/145K in/out (454 sf)
Weil-McLain EG/PEG -50
175K/145K in/out (454 sf)
0
Comments
-
Not registering any pressure may or may not be a problem. The question is... where is the steam going? Presuming that steam is being made? If pressure is not being developed, it either has to be going into the atmosphere somewhere more or less nearby, or it has to be being condensed somewhere as fast as it is being produced. Which is a good thing, if that somewhere is where you want heat.
I can't see enough of the piping to comment on the riser(s) and header, or connections to the steam mains. Could we see more?
Quite correct that the pigtail should be the other way up. The connection to the top of the low water cutoff, though, is quite common. It isn't my preference -- it tends to clog there -- but it isn't much if any below the boiler water line, or at least it shouldn't be, assuming the low water cutoff is installed correctly.Br. Jamie, osb
Building superintendent/caretaker, 7200 sq. ft. historic house museum with dependencies in New England0 -
Why is that condensate tank and pump "needed"? Most are not. Does your system have zone valves?All Steamed Up, Inc.
Towson, MD, USA
Steam, Vapor & Hot-Water Heating Specialists
Oil & Gas Burner Service
Consulting1 -
Jaime, thanks for the reply. The rest of the system seems to be working fine. There are no other leaks or spitting vents anywhere. There's no hammering pipes. I was just thinking that the pressure is not getting to the gauge ... the pigtail is not blocked. I wasn't sure the gauge would be reading pressure with the inlet for the pigtail under water. When I have gotten a reading on the pressure gauge, the system seems to run at around 0.5 PSI which is great from what I understand.
Here's a pic of the header as you requested...
In the meantime today, I moved the pigtail and plugged the hole in the LWCO where it was mounted (see pic below) as I was thinking ...
(I installed the high pressure gauge as well but all I had was some steel parts to put it together for now. I'll replace that with brass on my next trip to the store.
I'm still not getting a reading on the pressure gauge unless I close the valve on the main steam header. Then the low pressure 0-3PSI gauge climbs easily. I get too nervous to keep the main valve closed long enough to see the 0-30PSI gauge even start to move. At 2.5PSI, I think I can just see the 0-30 gauge start to move.
Also, you may note that there is another tap into the boiler just below the right most pressure switch. I had considered using that for the pigtail loop and pressure switches but decided against it for two reasons. One is the access hole in the jacket is a bit off center and I would have to hack the hole a little bigger, and two, that plug has been in there since the boiler was installed ~ 25+ years ago. I don't feel like fighting with it and potentially damaging something. Lol!
The low pressure cut off was set at between .5 and 1 PSI with a 3 differential, so it was not cutting off when I let the pressure climb to 2.5. So I cranked that pressure switch as low as it would go which is marked as .5 on the front dial. Then I lowered the differential to 1 PSI. and I tried shutting the main steam valve off again and this time the LPCO shut the boiler off when the pressure reached between 2 and 2.5. So the front dial on the pressure switch is not accurate. (I've seen in other posts here that this type of switch is not accurate at the low end of the scale.)
Since I don't think the system runs a much above .5 PSI, I think I will leave the LPCO where I have it now.
I was a bit concerned that the pressure switches might not be working because of the way they were installed with the upside down pigtail, but they seem to be fine.
I still have some wiring to tidy up, and of course, now I also have to paint the new steel fittings. (lol).
Also, in case anyone is wondering why the pressure switches and the LWCO have that thin red red wiring is because they are all running on 24v.
Single pipe steam
Weil-McLain EG/PEG -50
175K/145K in/out (454 sf)0 -
@Powe
First off congratulations on doing a fine job...looks good especially for having not worked on boilers before.
@Jamie Hall is correct although many boiler MFGs send their boilers from the factory with the gauges and pressure controls mounted on top of the low water cutoff it's not the best spot due to potential plugging with sludge.
If it was me I would take the safety valve off the boiler and install a tee under the safety valve. Keep the safety valve upright as it now is and reinstall it on the tee. Come out of the branch of the tee with a 3/4 nipple. (larger pipe is less likely to plug) and put (4) 3/4" x 1/4" tees to make a control header. You will have a tee for each pressure control and 2 for your gauges. On he end of the last tee put a 1/4" pet cock or ball valve it's required in some locations and can be used to blow out the piping.
Use brass fittings for the 1/4" pigtails and fittings and black for the 3/4" stuff is ok
The fittings on your #150 pump control are supposed to be plugged crosses, not tees or elbows for future reference. I assume you have already cleaned out the piping on that so I would leave it alone as far as putting the crosses on now...you can do it in the future if you do any repairs
As far as what @Steamhead mentioned about needing or not needing the condensate tank we need to see pictures of the piping around the boile and the basement and a couple of radiatord to comment on that.
Good Job!!0 -
Thanks for your comment Steamhead. Short answer is I inherited it that way when I bought the house and I haven't learned enough about steam systems yet to confidently bypass it. And nope, no zone valves. But yeah I question why it was ever installed. I can think of only two reasons: 1) Whoever sold the previous owner the boiler didn't understand steam systems OR 2) It was an unnecessary UPsell to make more money.Steamhead said:Why is that condensate tank and pump "needed"? Most are not. Does your system have zone valves?
I think it's an energy waster because it holds about 10 gallons of water and every time the boiler needs water, this thing pumps in a gallon or so of cold water. The system has to be running quite a while for that condensate tank to have reasonably hot water in it to return to the boiler.
For now I'm going to leave it, but I may experiment some time in the future with taking it out of the system and/or insulating the tank and adjusting the float switch to reduce the amount of water it hold.
If you have a suggestion about how I would go about bypassing it, I would appreciate any input. My main concern is that without the tank, the wet return would not hold enough water as it is only a short run (about 10 feet) of 3/4 inch copper line right now. Would it be advisable to make the wet return a little bigger so it holds a bit more water?
ThanksSingle pipe steam
Weil-McLain EG/PEG -50
175K/145K in/out (454 sf)0 -
@Powe
we would need to see more of the system to decide about the condnsate tank.
You could leave the tank in place and pipe a bypass around it to the boiler to try it without the pump but this would require 3 valves and increasing the pipe size between the pump and the boiler0 -
@EBEBRATT-Ed
Thanks for the suggestion about mounting the pressure switches and gauges on the pressure relief riser. I just might do that. The current location seems to get a lot of pressure fluctuations from the water movement in the #150 pump control and piping. (ha! now I know what it's called - thanks EBERATT-Ed!) Which fittings are supposed to be plugged crosses, and can you enlighten me on why that's required? I simply rebuilt it the way it was - not knowing any better.
Your suggestion about running a bypass around the condensate tank is also a good idea that I didn't think of. It will allow me to quickly revert back to using the tank if it doesn't work as well. Hmmm... Is there some "rule of thumb" for how much capacity the wet return should have?
@Jamie Hall
You made a comment about the LWCO being mounted at the correct height. I believe it is, although until you mentioned that, and EBERATT-Ed mentioned the cross fittings for the #150 pump control, I never considered that any of that control piping could have been done wrong. (Gee, how can you tell I have limited boiler experience???) You guys that do this for a living must see some pretty weird setups!
In regard to the steam piping around the house, I have some notes on the lengths of pipes and radiator EDR specs which I'll try to post later in the week. (I'm tooo busy at my day job at the moment.)
Here's a reader's digest summary ... There are two main loops around the basement - you can see the two green branches off the main copper riser in one of the pics above. There are 14 radiators on 3 floors above the basement. No radiators in the basement. The main loops in the basement are not insulated and they provide sufficient heat in the basement - maybe a bit more than sufficient, and I should consider at least partially insulating them.
Thanks for all your help and comments. I'm learning as I go!
PoweSingle pipe steam
Weil-McLain EG/PEG -50
175K/145K in/out (454 sf)0 -
@Powe
The crosses on the 150 control are for cleaning out the piping every year. But if you cleaned everything I wouldn't bother until the 150 needs cleaning or replacement. Blowing down the 150 & the #67 occasionally will help keep the water connections clear. Their the ones that tend to plug up0 -
That's kind of what I was guessing. I try to flush a gallon or two of water out of the drain once a week or at least a couple times a month, and a gallon or less out of the #150 and #67. Last winter the drain was completely blocked so I knew I had to do something to clean it out this summer.EBEBRATT-Ed said:@Powe
The crosses on the 150 control are for cleaning out the piping every year. But if you cleaned everything I wouldn't bother until the 150 needs cleaning or replacement. Blowing down the 150 & the #67 occasionally will help keep the water connections clear. Their the ones that tend to plug up
How do you guys test the high limit pressure switch without taking it off the boiler. Is that even a thing that is done? I'm a bit nervous to just close the main steam valve and let the pressure build up to see if it shuts off. Obviously, I'd just open the valve again if the pressure went much above the setting of the switch but ... it just feels like testing fate or something??? This is an older boiler and I'm thinking it may not be a good idea to test it that way? Or is it best to bench test it?
Any input on this?Single pipe steam
Weil-McLain EG/PEG -50
175K/145K in/out (454 sf)0 -
Best way would be to make up a little manifold and test with air pressure0
Categories
- All Categories
- 87K THE MAIN WALL
- 3.2K A-C, Heat Pumps & Refrigeration
- 58 Biomass
- 427 Carbon Monoxide Awareness
- 113 Chimneys & Flues
- 2.1K Domestic Hot Water
- 5.7K Gas Heating
- 109 Geothermal
- 161 Indoor-Air Quality
- 3.6K Oil Heating
- 70 Pipe Deterioration
- 995 Plumbing
- 6.3K Radiant Heating
- 391 Solar
- 15.4K Strictly Steam
- 3.4K Thermostats and Controls
- 55 Water Quality
- 44 Industry Classes
- 48 Job Opportunities
- 18 Recall Announcements