Welcome! Here are the website rules, as well as some tips for using this forum.
Need to contact us? Visit https://heatinghelp.com/contact-us/.
Click here to Find a Contractor in your area.
Multiple Parallel Injection Circulator Control help please...
Options

kuribo
Member Posts: 16
Hello-
I would like to use parallel injection mixing circulators per a J. Siegenthaler article:
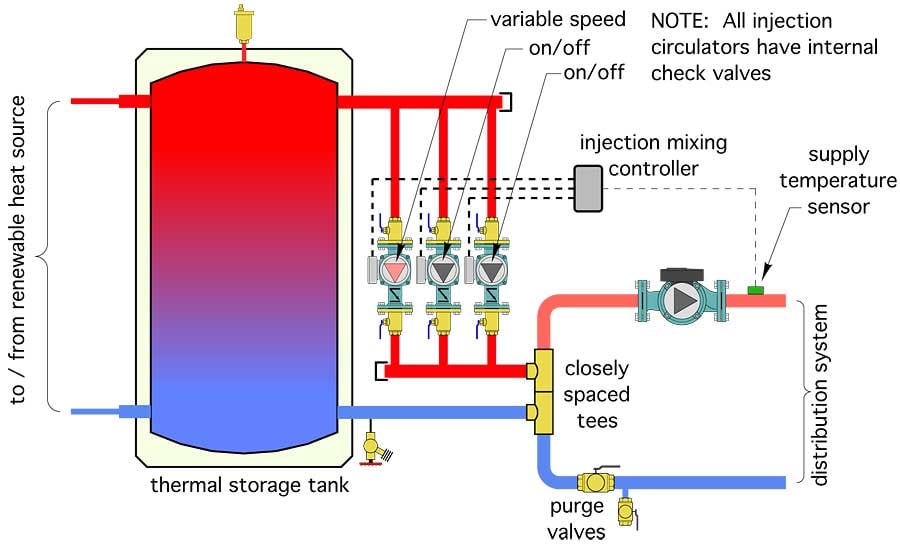
"Gang tactics
It’s also possible to use multiple (and identical) injection circulators in parallel, as shown in Figure 5.
When multiple and identical injection pumps are configured as shown in Figure 5, only one needs to be speed-controlled. The others can be controlled as on/off. This array of circulators would operate like a multiple boiler system having one fully modulating boiler in combination with additional on/off boilers. The variable-speed circulator would ramp up as the load begins to increase.
Once the load increases beyond what can be supplied through the variable-speed injection pump at full speed, one of the on/off injection pumps would turn on and the variable-speed circulator would drop back to a low speed.
Assuming the load continues to increase, the variable-speed circulator ramps up again until two of the on/off pumps can be on and the variable-speed circulator drops back down to low speed. In theory, this control action could be used with any number of identical circulators, only one of which is speed controlled. This technique allows smaller wet-rotor circulators to be used to meet the design-load injection flow rates that are beyond the range of a single small circulator. It also may reduce cost relative to a single larger injection pump with a VFD control. It also can provide injection flow rates lower than what a single larger circulator may be able to achieve based on a typical VFD that only reduces motor speed into the range of 20-30% of full speed."
The reason being I will be using a wood gasification boiler plumbed to storage. When the water in the tanks is at 180F, I only need a small gpm to meet my in floor loads. As the temp in the tank drops, I will need more and more gpm from the tanks. I would like to be able to use the tanks down to perhaps 100F supply temp. On a design day, that would mean 12gpm. When the water in the tanks is at 180F, I might only need 1 gpm or less. By using two pumps, I can use a small pump and smaller supply line (allowing me to operate within a 2ft/sec~4ft/sec window) for low flows, then use the larger or both pumps when the temps in the tank drop and injection flows reach 12gpm (again, keeping flow velocities within the recommended range. If I use one pump and size for the max flow, I will not meet the recommended flow velocities at low flow rates....
My question is, how would I control these two pumps (with outdoor reset) so that the smaller pump runs at a variable speed until it is maxed out, then the larger pump turns on until maxed out, then the smaller pump turns on, and with both running, I can reach the max flow required? Mr. Siegenthaler doesn't spec the control mechanism to accomplish this, he just describes how it works...Any suggestions appreciated....
I would like to use parallel injection mixing circulators per a J. Siegenthaler article:
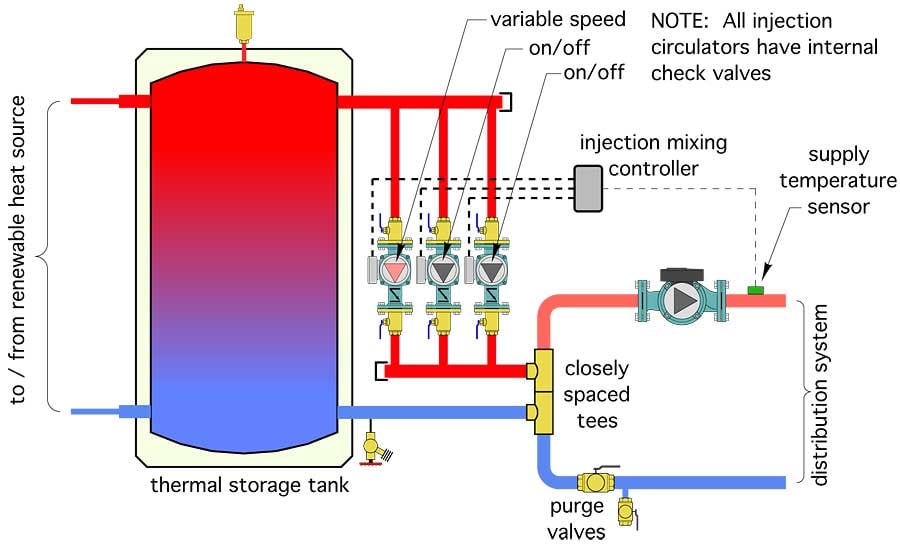
"Gang tactics
It’s also possible to use multiple (and identical) injection circulators in parallel, as shown in Figure 5.
When multiple and identical injection pumps are configured as shown in Figure 5, only one needs to be speed-controlled. The others can be controlled as on/off. This array of circulators would operate like a multiple boiler system having one fully modulating boiler in combination with additional on/off boilers. The variable-speed circulator would ramp up as the load begins to increase.
Once the load increases beyond what can be supplied through the variable-speed injection pump at full speed, one of the on/off injection pumps would turn on and the variable-speed circulator would drop back to a low speed.
Assuming the load continues to increase, the variable-speed circulator ramps up again until two of the on/off pumps can be on and the variable-speed circulator drops back down to low speed. In theory, this control action could be used with any number of identical circulators, only one of which is speed controlled. This technique allows smaller wet-rotor circulators to be used to meet the design-load injection flow rates that are beyond the range of a single small circulator. It also may reduce cost relative to a single larger injection pump with a VFD control. It also can provide injection flow rates lower than what a single larger circulator may be able to achieve based on a typical VFD that only reduces motor speed into the range of 20-30% of full speed."
The reason being I will be using a wood gasification boiler plumbed to storage. When the water in the tanks is at 180F, I only need a small gpm to meet my in floor loads. As the temp in the tank drops, I will need more and more gpm from the tanks. I would like to be able to use the tanks down to perhaps 100F supply temp. On a design day, that would mean 12gpm. When the water in the tanks is at 180F, I might only need 1 gpm or less. By using two pumps, I can use a small pump and smaller supply line (allowing me to operate within a 2ft/sec~4ft/sec window) for low flows, then use the larger or both pumps when the temps in the tank drop and injection flows reach 12gpm (again, keeping flow velocities within the recommended range. If I use one pump and size for the max flow, I will not meet the recommended flow velocities at low flow rates....
My question is, how would I control these two pumps (with outdoor reset) so that the smaller pump runs at a variable speed until it is maxed out, then the larger pump turns on until maxed out, then the smaller pump turns on, and with both running, I can reach the max flow required? Mr. Siegenthaler doesn't spec the control mechanism to accomplish this, he just describes how it works...Any suggestions appreciated....
0
Comments
-
I think you could cover that range with a single small wet rotor circ? You need gpm and fairly low head, a single control would do the trick then, also.
Or a motorized mixing valve.Bob "hot rod" Rohr
trainer for Caleffi NA
Living the hydronic dream0 -
Yes, without a doubt one pump would cover the gpm range, but the issue, as I mentioned, is that the pipe size to handle the gpm at 100F supply would need to be 1.25" , which is too large for the flow of around 1gpm at 180F supply to keep the flow velocity above 2ft/sec.
0 -
The 2 ft per second really only applies you have long runs of pipe with lots of ups and downs. Air tends to get trapped because the flow is too low in these cases. You also sometimes need the minimum flow to be insure turbulent flow in a heat exchanger or emitter in order to achieve good transfer.
For near boiler piping, it is absolutely not necessary to keep flow at 2ft/sec. If it was, most zone manifolds would not work when only one zone is calling and all radiant loops would constantly air lock as they rarely achieve 2 ft/sec.
To answer your original question, you will not find an "out of the box" control for multiple injection circs. It would need to be a custom solution like DDC.
Tell us a little more about your system. Since the thermal tank provides hydronic separation, you could probably accomplish your goals with a Taco I-series valve or two and simplify the whole design."If you can't explain it simply, you don't understand it well enough"
Albert Einstein0 -
Is there a backup boiler involved? What type, how will you pipe that into the system?
Not as much injection mixing theses days, most boilers have outputs to run one or multiple mix valves, and it simplifies the piping and parts list.Bob "hot rod" Rohr
trainer for Caleffi NA
Living the hydronic dream0 -
I have a wood gasification boiler feeding 1000 gal stacked propane tank pressurized storage, plumbed in a two pipe configuration. I will have a mod/con boiler feeding an indirect DHW tank and through a buffer tank, my 2 infloor radiant loads, which are broken into 6 zones. The mod/con will provide backup to the radiant when we are away and unable to stoke the wood boiler. The supply and return injection flows from storage to the header on the input side of the buffer tank and will vary depending on heat load and storage tank temp from nil to 12 gpm at the design load of 120,000btu/hr. Crude schematic below....
I0 -
I don't see a boiler protection method or device? Here are some options.
How many temperatures do you need?
What are the load sizes on the heating, is the 2nd buffer needed?
Controls will be a challenge.
If you use a mixing valve for the tank, use one with ODR built in, that will simplify the control logic.
A differential control could call on the mod con when the big buffer drops to the lowest possible temperature.
A common relay panel could call on zones and the mod con as well as DHW if the boiler doesn't have that control onboard.Bob "hot rod" Rohr
trainer for Caleffi NA
Living the hydronic dream0 -
Pump to storage is a variable speed pump which is controlled to limit return temps to the boiler below a set point for boiler protection.
Only need one temp, which will be set by the odr running the injection pump.
Mod/con will not interact with the storage tanks, only the buffer tank. 8 zones, some small enough to require a buffer tank.
No mixing valves.
Will probably implement a diff to turn on the mod con automatically if storage temps drop below a useful temp.
Mod con has all the controls on board. Have a separate control system for the wood boiler/storage/injection pump.
Thanks for the replies. I think I will just size the injection plumbing for the design point and assume less than 2 ft//sec will not be an issue when the flows are small....
0 -
Make sure you are piping the VS return temperature protection pump properly.
This arrangement will not adequately protect the boiler, the one in the previous post will.
Here is another way to interface and leverage buffers.
With a two pipe buffer, if the load and boiler output are the same, including throughout the modulation range, all mod con output goes directly to loads. No interface needed with the buffer. As loads drop below boiler minimum modulation the tank will start charging. As loads drop off or satisfy THEN the buffer charges to set point, boiler drops off.
With a 4 pipe buffer there will always be flow thru the tank, and the tank needs to be hot before it can cover any load.
Wood buffer would behave the same, directly to load until it has more output than the load requires.
Anytime the wood buffer is hotter than the small buffer, it will add energy.
What temperature are you running the small buffer, ideally low enough to leverage the mod con.
You want the wood on priority, mod con only fires when wood cannot keep up.
indirect would also tie in so either or boiler could heat it.
Bob "hot rod" Rohr
trainer for Caleffi NA
Living the hydronic dream0 -
It has been a while since I have done injection mixing so some of the tech may have changed. Be sure to give yourself a means to add some resistance to the injection loop if needed. A balancing valve or globe valve would work.
The old Tekmar setups using conventional circs had a tendency to surge (seek) because they could not turn down low enough. Throttling the flow was the fix."If you can't explain it simply, you don't understand it well enough"
Albert Einstein1
Categories
- All Categories
- 87K THE MAIN WALL
- 3.2K A-C, Heat Pumps & Refrigeration
- 58 Biomass
- 427 Carbon Monoxide Awareness
- 113 Chimneys & Flues
- 2.1K Domestic Hot Water
- 5.7K Gas Heating
- 109 Geothermal
- 161 Indoor-Air Quality
- 3.6K Oil Heating
- 70 Pipe Deterioration
- 995 Plumbing
- 6.3K Radiant Heating
- 391 Solar
- 15.4K Strictly Steam
- 3.4K Thermostats and Controls
- 55 Water Quality
- 44 Industry Classes
- 48 Job Opportunities
- 18 Recall Announcements