Welcome! Here are the website rules, as well as some tips for using this forum.
Need to contact us? Visit https://heatinghelp.com/contact-us/.
Click here to Find a Contractor in your area.
Finding the right settings
Options
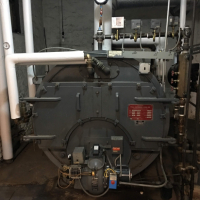
eappleton
Member Posts: 111
Hi all,
I'm trying to adjust our boiler to stable settings after we replaced insulation, installed main venting and repaired a leak in a buried condensate return.
Our system:
Federal FST-40 Scotch Marine, Heat Timer EPU-CH, Carlin 701CRD, Single-pipe steam, 24 apartments
Low-fire/high-fire pressuretrol (set between .5 and 2)
Cut-in pressuretrol (set between 2 and 3)
Outside temp sensor, heat system sensor on basement return, no thermostats
I have had trouble finding settings that keep the building at a comfortable temperature, not too hot, not too cold.
Problem #1:
Our system heat sensor is located on a return pipe in the basement. The pipe it is attached to was well insulated a month ago. Since then, it seemed that lockout period after a heat cycle was much longer than it had been in the past. My theory is that the sensor is kept warmer longer and delays the next heat cycle from starting. I response, I turned up the system sensor knob on the Heat Timer. This increased the length of the cycle since the timer started later, after the system was up to pressure, and shortened the time between cycles. I know that the heat system sensor should be set by timing how long it takes to heat up the farthest radiator from a cold start. However, we did this before the new insulation and I don't think the result would change. So we would end up with a much lower heat system sensor setting and the too-long lockout period problem.
Current thinking: Keep the system sensor high and find the right spot through trial and error. I'm worried that the cycles are still delayed, but I haven't timed them yet or measured temperature swings.
Problem #2:
I turned up the boiler yesterday but it didn't improve the heat. When I sat with the boiler for a while this morning, I noticed that the boiler shuts off and restarts during the heating cycle.
I watched the pressure climb up to about 1.5psi and then switch into low fire. In low fire, it continues to climb and got to 2psi after about 5 minutes, then shut off. The burner restarted a few minutes later and repeated the process.
It seems to me that the burner is restarting over and over, and losing pressure in between. Maybe this is why we're not getting better heat? I was also wondering if the system is locked out from restarting by the return sensor, so that it doesn't finish its timed hear cycle.
My current solution: 1) lower the low/high pressuretrol (.5?) so that it climbs more slowly to the cut out pressure. 2) raise the cut out pressure (2.5?) so that it shuts off on pressure later.
Questions:
Is it preferable that the boiler runs continuously through its heating cycle (approximately 34 minutes today)?
It would be nice to have a steady pressure after switching to hi fire so that it doesn't .cut off on pressure. Is there a way to accomplish this? Smaller fuel nozzle for low fire? Lower initial low fire setting?
Any advice would be appreciated.
Eric
I'm trying to adjust our boiler to stable settings after we replaced insulation, installed main venting and repaired a leak in a buried condensate return.
Our system:
Federal FST-40 Scotch Marine, Heat Timer EPU-CH, Carlin 701CRD, Single-pipe steam, 24 apartments
Low-fire/high-fire pressuretrol (set between .5 and 2)
Cut-in pressuretrol (set between 2 and 3)
Outside temp sensor, heat system sensor on basement return, no thermostats
I have had trouble finding settings that keep the building at a comfortable temperature, not too hot, not too cold.
Problem #1:
Our system heat sensor is located on a return pipe in the basement. The pipe it is attached to was well insulated a month ago. Since then, it seemed that lockout period after a heat cycle was much longer than it had been in the past. My theory is that the sensor is kept warmer longer and delays the next heat cycle from starting. I response, I turned up the system sensor knob on the Heat Timer. This increased the length of the cycle since the timer started later, after the system was up to pressure, and shortened the time between cycles. I know that the heat system sensor should be set by timing how long it takes to heat up the farthest radiator from a cold start. However, we did this before the new insulation and I don't think the result would change. So we would end up with a much lower heat system sensor setting and the too-long lockout period problem.
Current thinking: Keep the system sensor high and find the right spot through trial and error. I'm worried that the cycles are still delayed, but I haven't timed them yet or measured temperature swings.
Problem #2:
I turned up the boiler yesterday but it didn't improve the heat. When I sat with the boiler for a while this morning, I noticed that the boiler shuts off and restarts during the heating cycle.
I watched the pressure climb up to about 1.5psi and then switch into low fire. In low fire, it continues to climb and got to 2psi after about 5 minutes, then shut off. The burner restarted a few minutes later and repeated the process.
It seems to me that the burner is restarting over and over, and losing pressure in between. Maybe this is why we're not getting better heat? I was also wondering if the system is locked out from restarting by the return sensor, so that it doesn't finish its timed hear cycle.
My current solution: 1) lower the low/high pressuretrol (.5?) so that it climbs more slowly to the cut out pressure. 2) raise the cut out pressure (2.5?) so that it shuts off on pressure later.
Questions:
Is it preferable that the boiler runs continuously through its heating cycle (approximately 34 minutes today)?
It would be nice to have a steady pressure after switching to hi fire so that it doesn't .cut off on pressure. Is there a way to accomplish this? Smaller fuel nozzle for low fire? Lower initial low fire setting?
Any advice would be appreciated.
Eric
Single-pipe steam | 24 apartment, self-managed coop | Federal FST-40 Scotch Marine boiler | Carlin 701CRD burner | Heat Timer EPU-CH | Honeywell pressuretrols | Heating oil #2 (20% bio)
0
Comments
-
Unless your system has something other than radiators on it, it certainly doesn't need to raise the pressure beyond 2 psi -- in fact it will probably operate well at 1.7 psi. So raising the pressure setting on the low fire cutout won't do anything for you except burn more fuel for nothing. I would quite seriously, though, try it switching to low fire at 0.5 to 0.7 psi, with high fire cutting back in (if needed) at around 0.2 psi. That's a pretty close differential for the high fire, and the pressure control may not be able to do it -- but see what it can do. See if you can also reset the controls so that the low fire will start on its own at a pressure slightly above the high fire cutting back in. This depends on your controls --but a good place to start would be on initial fire and rising pressure -- high fire initially, high fire to low fire at about 0.7 psi, low fire off at 1.7 psi. On falling pressure, low fire back on at 0.7 psi, high fire back on at 0.2 psi.
It is certainly preferable that a boiler run continuously throughout a heating cycle. Lowering the change to low fire may help in that. If it still continues to rise to the low fire cut out, it is possible that a good technician could reduce the low fire firing rate, but that depends on the burner and the boiler. Otherwise, what you are seeing is actually kind of normal, if not ideal -- your boiler, on low fire, produces more steam than your radiation can condense, and it needs to take that time out for the radiators to catch up.
Be sure that you have ample venting on the mains -- and if this is more than three stories and upfeed, consider installing additional main vents at the tops of the risers.Br. Jamie, osb
Building superintendent/caretaker, 7200 sq. ft. historic house museum with dependencies in New England0 -
Heat timer sensor on the return line isn't great. I would relocate it to the farthest radiator steam supply if you can or as close to that location if possible. We have been replacing Heat Timers with Tekmar controller and getting better results easier set up for less $$ but the HT should work. Make sure your venting is up to par or you will just keep chasing your tail on heat timer adjustments.
Once that is done, a far as the pressure control settings the trick is to keep the burner from short cycling while keeping the pressure low. That is difficult especially in the spring and fall. The high limit I would set a cut out of 3psi, differential 2.75 (if possible that will cut in at .25psi
Hi/lo fire control cut out at 2 diff1.75 cut in at .25
If you know your edr load convert it to BTU/hr add 30% for boiler loss and pick up load.....that's a starting point and see if you can down fire the boiler to that BTU by changing nozzles You may not be able to go that low. You need a burner guy that knows his stuff and will do a combustion test.
Then you can start adjusting the heat timer
But the real question is what pressure do you need to run to heat the building? All the old buildings were designed to run 2 psi max.
If you need more pressure than that you could have venting or steam trap problems and no control adjustments will fix that very well0 -
Thank you for the detailed response and sorry for the delay in responding. I have been chasing my tail on the heat timer for sure.
Pressure settings: I took your advice and turned the low fire cutoff back down. It is currently at about 2 psi. I would like to turn it down lower, but it seems that this would shorten the heat cycle a lot (or at least create low pressure dips that would complicate the settings). I also turned down the hi/lo control to .5psi (at least that's what the pressuretrol says; our gauge makes it difficult to see anything under 1 lb of pressure). Both of these adjustments help. The cycle time before the low-fire cuts off is longer (though it still shuts off on pressure after about 15 minutes) and the radiators aren't screaming as much with pressure.
I'm currently trying to understand what more I can do with the controls I currently have. I also want to know what fixes I can make now and plan for soon. (I'm slowed down a bit in making fixes because I probably don't have the skill or confidence to do things myself, and have to get approval from the board to pay for repairs.)
I'm trying to understand the following advice.@EBEBRATT-Ed: The high limit I would set a cut out of 3psi, differential 2.75 (if possible that will cut in at .25psi. Hi/lo fire control cut out at 2 diff1.75 cut in at .25@Jamie Hall: a good place to start would be on initial fire and rising pressure -- high fire initially, high fire to low fire at about 0.7 psi, low fire off at 1.7 psi. On falling pressure, low fire back on at 0.7 psi, high fire back on at 0.2 psi.
The hi/lo pressuretrol is set to cut-in at .5psi. That means low-fire turns on. The differential is currently set at 1.5, I think. That would mean the low-fire would shut off at 2psi? If I understand EBEBratt-ED, you're recommending I change the cut-in to .25psi and the differential to 1.75. Does this pressuretrol go as low as .25? My 0-30lb pressure gauge won't help me here.
If I understand Jamie, you're recommending I change the hi/lo cut-in to .7psi and the differential to 1.
In the course of a heating cycle, I see this pattern: hi fire until .5psi, lo fire until 2 psi, boiler shuts off, hi fire after a while... I haven't seen come back on with lo fire alone. This would be nice. I'm not understanding how the lo fire comes back on after the boiler turns off on pressure.
The other pressuretrol (labeled OPEN) is set to to 2 psi. I know this controls when the boiler shuts off completely, but the cut-in at 2 psi means that it shuts off? I thought cut-in opens the circuit. Cut-in on this pressuretrol turns off the circuit and cut-in on the other pressuretrol turns on the circuit? Or does the cut-in on the hi/low pressuretrol turn off the hi-fire and cut-out turns the hi-fire back on?
I'm trying to make sense of the pressuretrols with this diagram. I have the additive kind, right?
Regarding the sensor, I recognize that we need to move the sensor. The current situation is a mess. It takes forever for the boiler to leave the lockout mode and be ready for a new cycle. It's too hot if I turn up the heat system sensor, even at the lowest heat settings. And it's too cold if I turn down the heat system sensor, even at high settings, since the periods in between heat are too long. I'm getting complaints and crankiness from both ends of the spectrum.
Here's a dumb question: It's not all that easy to wire directly through the building from the boiler to a radiator on the 4th floor. We should send it out the window and then in a resident's window to attach to their radiator, right? Does anyone have an example of how this wire should go through a window frame, sealed nicely, and not annoying the person who has to let it be installed?
Thanks all!Single-pipe steam | 24 apartment, self-managed coop | Federal FST-40 Scotch Marine boiler | Carlin 701CRD burner | Heat Timer EPU-CH | Honeywell pressuretrols | Heating oil #2 (20% bio)0 -
Don't worry about the differences in pressure setting between what I said and what @EBEBRATT-Ed suggested -- we are both looking at the same principle, just slightly different numbers. The idea is this: starting cold (or cool!), the boiler should run on high fire up to a certain low pressure -- a few ounces -- and then should switch to low fire. Low fire should run up to a higher pressure (I'd never go over 2 psi for this type of system) and then shut off. When the pressure drops somewhat, low fire -- not high fire -- should come back on and the cycle should repeat. If the pressure continues to drop, however, then -- and only then -- should high fire come back on.
Without being there to fiddle (I'm a hands-on type of person) it's a little hard to say what's happening or why. One thing you might try, however, is setting the differential for the control which turns low fire off and on to as small a value as you can, and the differential for the high fire as large as possible (keeping the cut in above zero, of course!). It is possible, if there are post purge and pre purge delays in the system, that the system pressure drops low enough once low fire shuts off that the high fire cuts back in before the burner fires -- even though the low fire cut in has already tripped.
Might it be possible for you to make a complete circuit diagram of the pressure controls and burner connections, including the settings on each? I might be able to make more sense out of it then...Br. Jamie, osb
Building superintendent/caretaker, 7200 sq. ft. historic house museum with dependencies in New England0 -
@eappleton
I would suggest that if running at a lower pressure is helping as you seemed to indicate I would bring in a good burner tech to see if the burner boiler can be downfired. This will give you a longer run time.
This is a common issue with older steam systems. Originally with coal you shoveled in what you needed to heat the building with a continuous small coal fire.
The boiler and radiation was always oversized.
Now, converted to oil the burner has to be sized to heat the building on the coldest day....no more shovel....so that means the burner is oversized for most of the year....hence the hi/lo fire burner but that will only do so much.
Basically downfire the burner as much as possible, fix traps and air vents and check pitch and fix piping problems. Skim the boiler if need be.
Then the pressure should be set to run as low as possible TRYING to keep the burner from short cycling.0
Categories
- All Categories
- 87K THE MAIN WALL
- 3.2K A-C, Heat Pumps & Refrigeration
- 58 Biomass
- 426 Carbon Monoxide Awareness
- 116 Chimneys & Flues
- 2.1K Domestic Hot Water
- 5.7K Gas Heating
- 109 Geothermal
- 160 Indoor-Air Quality
- 3.6K Oil Heating
- 70 Pipe Deterioration
- 994 Plumbing
- 6.3K Radiant Heating
- 389 Solar
- 15.4K Strictly Steam
- 3.4K Thermostats and Controls
- 54 Water Quality
- 44 Industry Classes
- 48 Job Opportunities
- 18 Recall Announcements