Welcome! Here are the website rules, as well as some tips for using this forum.
Need to contact us? Visit https://heatinghelp.com/contact-us/.
Click here to Find a Contractor in your area.
Constant Air in System
Options

Matt328
Member Posts: 7
I have a combination oil/hand fired coal boiler, and for the 6 years we've lived here, I always have had air in the 2nd floor zone. I've purged the system by isolating one zone at a time, hooking a garden hose and bucket up to the drain valve and opening the flow reducer. Always there were bubbles in at least one of the zones, and they always eventually stopped, leaving me to think I'd been successful, but then about a day an a half later we get woken up in the night sounding like Niagara Falls. With the system up to temperature, between 160 and 180, the pressure gauge on the boiler shows around 20 psi.
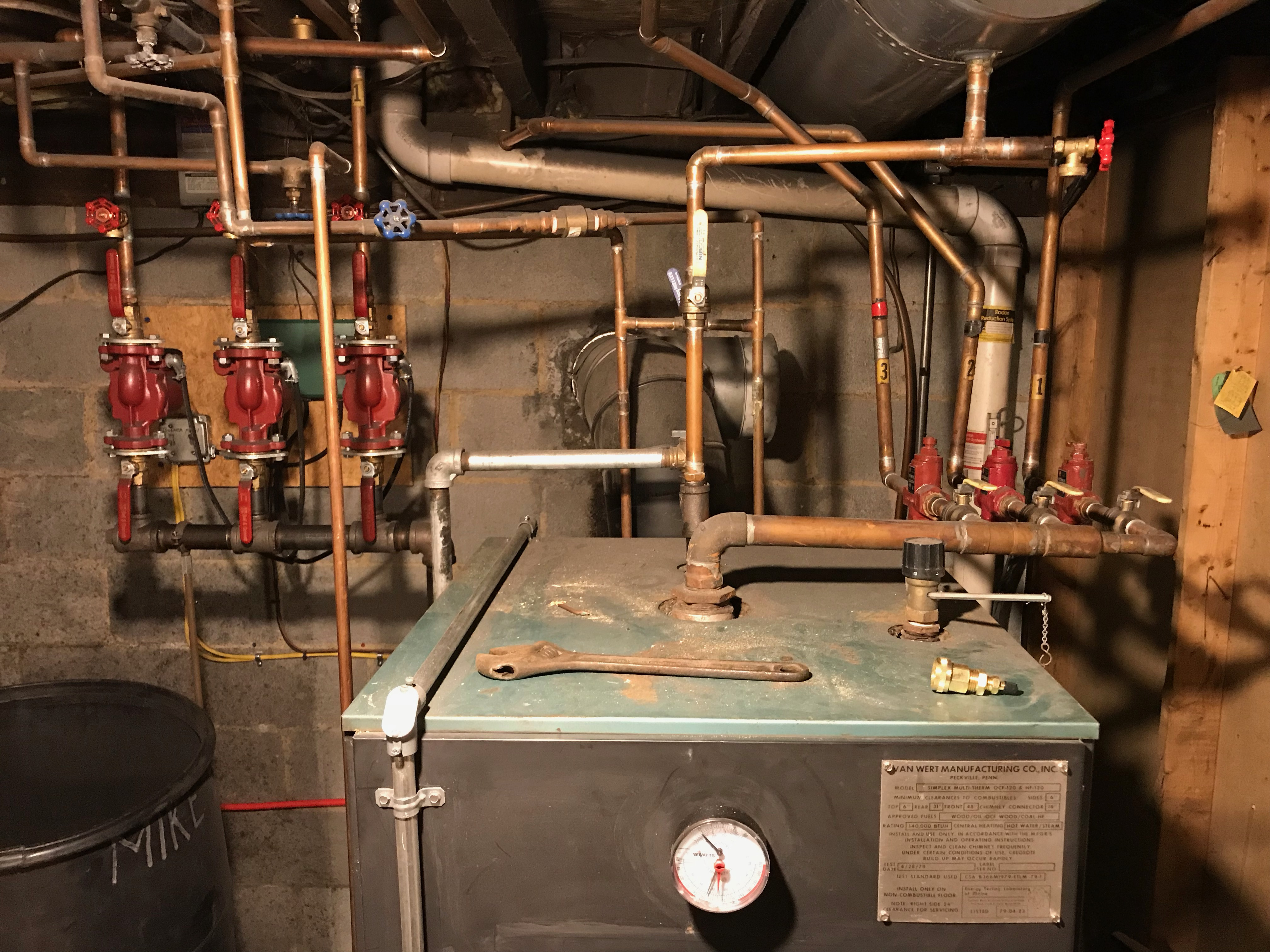
Originally there was a single circulator pump, it was on the left, and on the right were 3 zone valves, where the flow control valves are now. We had a leaking valve and hired a plumber to fix it, and he recommended and installed the system as it is in the picture.
Earlier today I drained and properly recharged the expansion tank, which was completely waterlogged, but that didn't seem to make any difference whatsoever.
I'm guessing what happens is air originates from somewhere in the system, but always makes its way to the 2nd floor zone, since it is the first one to come off the output side of the boiler, it's the pipe with the #3 label on it.
So problem 1, i'm not sure why the air isn't going to the expansion tank instead. I guess the boiler output is higher, so it goes there. I'm about ready to put an air separator right after the elbow on the output pipe.
Problem 2, the root cause, is where is all this air coming from? When I override the thermostat, I can sit and listen to the pump sound like it's pumping soda. It might quiet down for a minute or so, but then I hear a release of bubbles all at once, and about 45 seconds later the pump is making noise again.
There are air separators right before the downward elbows into the pumps, you can see one in the top right of the picture, but a) at that point, the air has already been through the house and woken everyone up, and b) they don't seem to be doing a damn thing anyway as I sat earlier today and listened to it pump air around and around for over an hour.
Any help and suggestions would be appreciated.
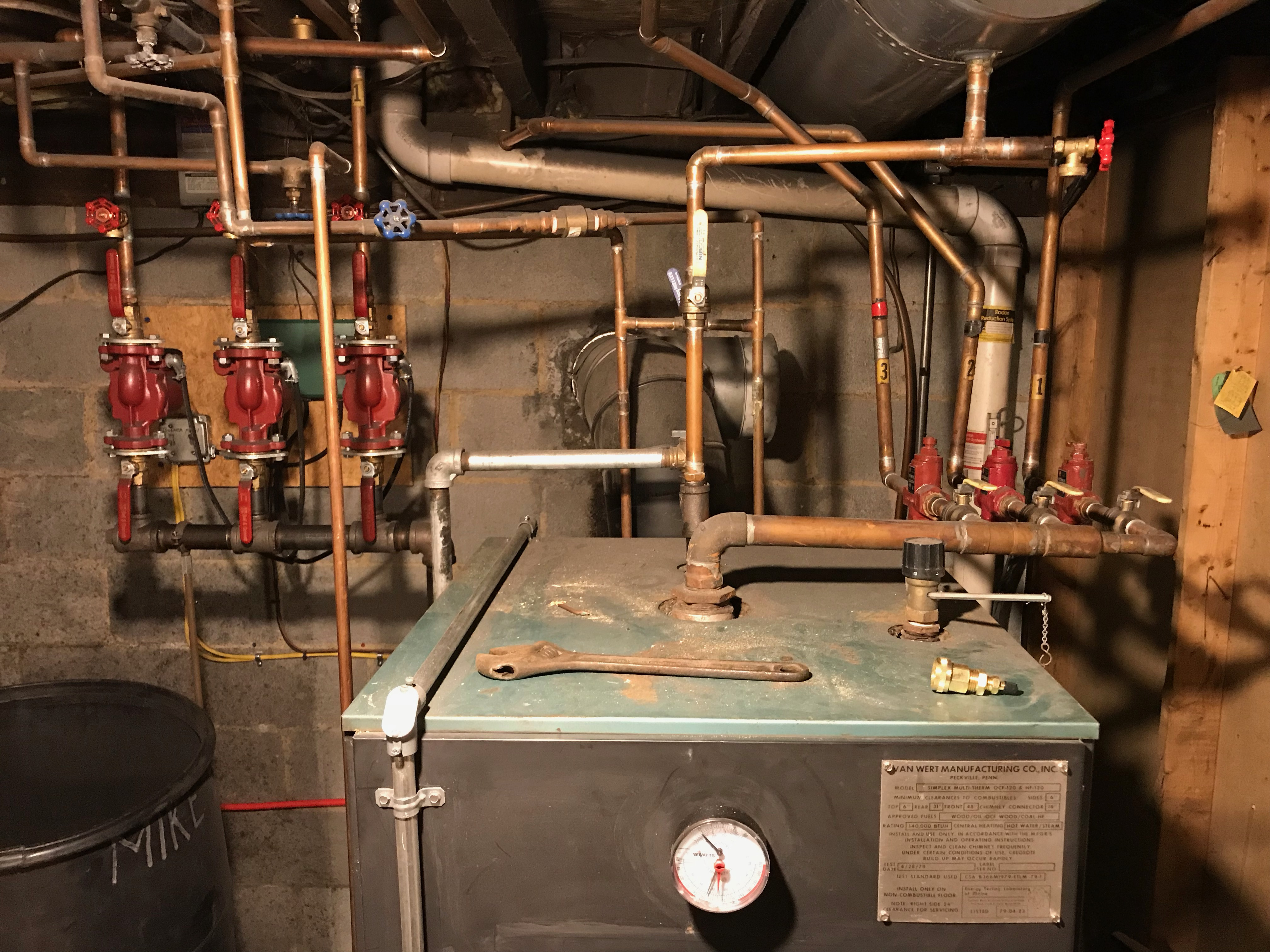
Originally there was a single circulator pump, it was on the left, and on the right were 3 zone valves, where the flow control valves are now. We had a leaking valve and hired a plumber to fix it, and he recommended and installed the system as it is in the picture.
Earlier today I drained and properly recharged the expansion tank, which was completely waterlogged, but that didn't seem to make any difference whatsoever.
I'm guessing what happens is air originates from somewhere in the system, but always makes its way to the 2nd floor zone, since it is the first one to come off the output side of the boiler, it's the pipe with the #3 label on it.
So problem 1, i'm not sure why the air isn't going to the expansion tank instead. I guess the boiler output is higher, so it goes there. I'm about ready to put an air separator right after the elbow on the output pipe.
Problem 2, the root cause, is where is all this air coming from? When I override the thermostat, I can sit and listen to the pump sound like it's pumping soda. It might quiet down for a minute or so, but then I hear a release of bubbles all at once, and about 45 seconds later the pump is making noise again.
There are air separators right before the downward elbows into the pumps, you can see one in the top right of the picture, but a) at that point, the air has already been through the house and woken everyone up, and b) they don't seem to be doing a damn thing anyway as I sat earlier today and listened to it pump air around and around for over an hour.
Any help and suggestions would be appreciated.
0
Comments
-
With the expansion tank you have (compression tank) air will migrate into the system via the water charge in the tank.
As water in the system is heated it makes its way up into the tank. The cooler water in the tank that has absorbed O2 in the tank migrates back down the same pipe out into the system. The flows happen with in the same pipe.
There is a airtrol tank fitting by bell, and gossett that helps to prevent this exchange.
With a compression tank you DO NOT want air removal devices in the system. You want the air to end up back in the tank to prevent water logging the tank.
Another thing is to pump away from the compression tank. This keeps the pumps differential (system psi) higher out in the system which helps move air along back to the tank.
Right now as set up you are pumping towards the compression tank. So the system pressure is lower out where the emitters are.
Lower system pressure allows air bubbles to enlarge, and come out of solution. This makes it harder for air bubbles to make it back to the boilers baffles to get the air back up into the tank.
2 -
Go to the library on this site, and research pumping away to better unspderstand how it works.0
-
It seems like this is put together completely backwards.
I didn't think I could be, but I am even less pleased with this plumber. Temperatures are starting to dip, and I'm probably at the point now where moving the pumps to the other side of the boiler might be something that will have to wait until spring. The 'pumping away' definitely seems like the way to go, but is spending a few bucks on a tank fitting worth trying first?
If so, the B&G Airtrol Fitting https://supplyhouse.com/Bell-Gossett-112010-1-2-ATF-12-Airtrol-Fitting-For-12-14-Compression-Tank-Dia-8624000-p says you also have to use an airtrol air separator https://supplyhouse.com/Webstone-75003-WEBSTONE-3-4-Air-Separator-Sweat Would you recommend that as well, or will the fitting get the job done.
Also, you said you do not want air removal devices in the system, each return line has an air separator, and they have ball valves to isolate them, should I close those ball valves, or leave them open?
Also do you have any insight on compression vs bladder type expansion tanks you'd be willing to share?0 -
With your present set up you don't want any air removal devices in the system. You need that air to go back to the compression tank.
So no you do not want the recommended air removal device for the airtrol fitting. That boiler has a built in baffle to get air up to the tank as is. The description of how it works is even wrong.
Some thoughts you can convert to a bladder tank which would then require an air removal device.
You should still pump away from its location.0 -
If the resistance of one of your piping loops is high you could be pulling air into one of the air vents. Shut the system down and bleed everything you can bleed. Then shut off the automatic air vents...can't use them with a compression tank.
Then start it up and See how this works.
If you still have problems I would install a bladder expansion tank with an air separator on it.
And lastly move the pumps to pump away.
Start with bleeding and isolate air vents and then move on to the other items if you need to.1 -
Gordy has this well diagnosed.
I will add that the 3 circulators look oversized. What model are they?
If you have air eliminators upstream of a large circulator which is pumping into a compression tank, you likely have negative pressure at the circ inlet. Air eliminators turn into air adders when under negative pressure. Close the air eliminators..."If you can't explain it simply, you don't understand it well enough"
Albert Einstein2 -
The circulators are Grundfos UPS15-58FC.0
-
As a first step, try closing your air eliminators and setting the circs to speed 1."If you can't explain it simply, you don't understand it well enough"
Albert Einstein0 -
guys,
in a situation like this,
what would happen if the circs were just flipped to pump in the other direction?
specifically,
what happens if you pump from the low return on the boiler?
and then I guess the flow controls would need to be spun also,
and now you're really repiping.
but,
what happens if you pump from the low return of the boiler?known to beat dead horses0 -
You need a good central air purger, all those float vents do not equal a quality purger.
If you add a purger, the air discharge pipes up to the tank.
I have a 500 gallon buffer tank that I trap a bubble up top for a solar drainback, It has a Caleffi Discal with the vent piped to the air space, works great, excellent micro bubble removal and air remains in the upper part of the tank.
Better yet use the tank for a barbecue and add a diaphragm tank
Be nice to correct all the issues at once, move the circus to supply add air purger and expansion tank, if you are up for that much redo?Bob "hot rod" Rohr
trainer for Caleffi NA
Living the hydronic dream0 -
There have been at least 2 postings here where pumps accidently got flipped on the return side. Both cases had problems. The last one had his boiler overheating with air/steam on the top. It was pointed out that his pump was backwards, haven't heard from him since.
But pulling water down thru the boiler could cause overheating of the boiler. The one case pulled air into the boiler. Little heat delivery was achieved in either case.
If it were me I would close the air vents which are actually air inducers is this case. Be sure the old compression tank has an air charge and try the system out.0 -
There is nothing wrong with a compression tank other than size.
The difference between a diaphragm, or bladder type tank, and a compression tank is air management verses air elimination. Compression tanks manage air in the system getting it back to the tank through proper piping, and component location. The other type of x tank is air elimination. Which still requires proper piping, and component location practices.
Since you already have most of the components as is I was just trying to get you by as cheap as possible.
C
Well there is a reason the cooler return water comes in at the bottom of the boiler HX.neilc said:guys,
in a situation like this,
what would happen if the circs were just flipped to pump in the other direction?
specifically,
what happens if you pump from the low return on the boiler?
and then I guess the flow controls would need to be spun also,
and now you're really repiping.
but,
what happens if you pump from the low return of the boiler?
Among other things you have mentioned the air baffle chamber may not function as designed in the top of the HX.
0 -
Most All good advice? There are a whole bunch of right modern ways with more modern hardware to repipe to proven modern methods.
However many boilers out there with compression tanks that are going trouble free when piped correctly with minimal extra hardware. Diaphragm, and bladder tanks do fail probably more often than compression tanks in a compression tanks life span.
I merrily opted for a cheapest solution to get the air monkey off your back. For 75 bucks, and some minimal pipe work it will get you going, and you can decide on the ultimate plan come spring.
Compression tanks are air management systems, and diaphragm tanks are air removal systems.0 -
Fixing the compression tank to better capture air is a good first step, however you are still pumping towards the PONPC and I think air elimination will still be a challenge.
Pumping at the PONPC will cause low, sometimes sub atmospheric conditions in the systems, those air vents can become air intakes
More reading on expansion tank pro and cons.
https://www.google.com/search?client=safari&rls=en&q=Amtrol+handbook&ie=UTF-8&oe=UTF-8
Bob "hot rod" Rohr
trainer for Caleffi NA
Living the hydronic dream0 -
Right!0
-
Thanks everyone for the excellent discussion. Just by closing off the air separators this morning, my wife noticed today it’s been quieter than ever, knock on wood.
I’m ok with soldering copper and brass I’m just not very quick about it, so at this point if everything stays quiet I’ll probably tackle a re pipe in the spring. If today was a fluke and it gets noisy again I’ll go with the compression tank fitting and hope that gets by until spring.
Thanks again for the help, I wish I’d found this site about 5 years ago!0
Categories
- All Categories
- 87K THE MAIN WALL
- 3.2K A-C, Heat Pumps & Refrigeration
- 58 Biomass
- 427 Carbon Monoxide Awareness
- 113 Chimneys & Flues
- 2.1K Domestic Hot Water
- 5.7K Gas Heating
- 109 Geothermal
- 161 Indoor-Air Quality
- 3.6K Oil Heating
- 70 Pipe Deterioration
- 995 Plumbing
- 6.3K Radiant Heating
- 391 Solar
- 15.4K Strictly Steam
- 3.4K Thermostats and Controls
- 55 Water Quality
- 44 Industry Classes
- 48 Job Opportunities
- 18 Recall Announcements