Welcome! Here are the website rules, as well as some tips for using this forum.
Need to contact us? Visit https://heatinghelp.com/contact-us/.
Click here to Find a Contractor in your area.
aluminum vs stainless steal HEX
Options
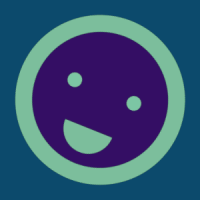
Snowmelt
Member Posts: 1,438
in Gas Heating
Navien vs Weil Mclain vs Triangle tube & so on..................
Just so I have a better understanding why aluminum vs stainless is better then the other can someone explain so I can explain to customers. Also do we want a boiler with a larger water content vs less water? I don't want to give wrong information to the customer. would you use a different boiler just on fact of hard well water vs nice clean proper ph water? as I said that past statement , are we as mechanical boiler guys treating water on every job? Did I miss anything ?
Just so I have a better understanding why aluminum vs stainless is better then the other can someone explain so I can explain to customers. Also do we want a boiler with a larger water content vs less water? I don't want to give wrong information to the customer. would you use a different boiler just on fact of hard well water vs nice clean proper ph water? as I said that past statement , are we as mechanical boiler guys treating water on every job? Did I miss anything ?
0
Comments
-
pros and cons to all the various metals used in boilers. Cost probably drives some of the choices. Of the various metals and alloys.. iron, SS, Al, and steel, copper by far is the best conductor.
As boilers moved to condensing operating conditions it became important to use metals that could deal with the low ph of the "fluids of condensation." Stainless boilers both water tube and fire tube use a much thiner wall material compared to cast or steel, so weight is also saved. Size and weight reduction leads to wall hung and small space applications.
Notice cast iron boilers are shrinking in size and water content, probably wall thickness alsoI'm not so sure 30 years is on the minds of manufacturers these days.
For systems with multiple and micro sized zones, having some volume can add some advantages. Tank type heaters and boilers are available for systems like that.
HydroPulse probably deserves credit for pioneering high efficiency and tank in one product. HTP and most of the water heater brands offer condensing tank style appliances.
Adding a buffer tank can also provide some nice benefit in addition to adding "capacitance" Storing energy is a super insulated, non flue tank is a nice option.
Three pipe buffer tanks give you the best of both worlds, direct to load, or load from tank, your choice of boiler(s).
aBob "hot rod" Rohr
trainer for Caleffi NA
Living the hydronic dream0 -
Hot rod, the hydropulse was an interesting duck, we worked on many of them. I think the pulse burner came from them when Lennox came out with their pulse furnace. If anyone ever needs parts for Hydropulse or for Heatmaker combi I have stock that I will never use so would be happy to off load. Don't know if their are many left although. The Hydropulse actually for a condensing boiler had quite a good lifetime. 20 + if taken care of.0
-
Aluminum is a bit more finicky as to system fluid composition, and fluid maintenance.
Stainless has always thought to have been bullet proof, however it is just more bullet proof than aluminum in my opinion. Depends on the quality of the stainless used, and it doesn't care much for chlorides.
Cast iron has a proven track record back when the hx was quite a bit heavier walled. Not so much anymore.
Mass is always a benefit when well managed. Boiler hx volumes are decreasing. Double edge sword. Lower volume, thinner walled hxers heat faster, and cool faster. Large volume thicker walled stay hotter longer, but also use more energy. So which is the pro, and which is the con? Is there one?
I like the tank style boilers that we dare say resemble a tank style water heater with modulating burner..........
1 -
With stainless there are so many choices and they all have different strong points. So far we have seen 304, 316, 409, some Ti stabilized grades as Viessmann prefers and AL grades. Some indirects use one grade for the tank, another for the coil inside.
Some alloys handle thermal stress better, some weld and form better, some handle aggressive fluids better.
A boiler presents unusual challenges with combustion and it's by products, multiple fuels with different and changing blends of fuels.
Extreme and often rapid temperature changes, pressure, contaminants on both sides of the tube. Intake air quality, the blending with multiple metals connected to them, and possible electrolysis.
Not to mention they need to being affordable
The small fluid capacity was the big selling feature with the original mod con designs like the Sermeta HXers. Why store any heat energy inside a vessel, especially one with a flue pipe connected?
The best way to store energy is in the fuel, un-combusted in the tank or piping. Transfer the energy from the fuel, stored in the gas to the load quickly, instantly, and only as needed.
I suppose an argument can be made for either design, an an application for both weather thy have 50 gallons or 1 gallon of fluid under the hood.Bob "hot rod" Rohr
trainer for Caleffi NA
Living the hydronic dream0 -
We have a service contract with a commercial and large condo building which has two De Dietrich C310-9 2 million BTU input condensing boiler. These have aluminium heat exchangers. We check them 3 times a year. Among other things, the plumber has to test the PH and TDS. We have an instrument that does that and more. The manufacturer suggest once a year test of the water in the system. No S/S boiler maker has this requirement.0
-
Aluminum conducts or transfers heat 12 times better than stainless. Cast iron 3 times greater than stainless. The question is wear and tear versus efficiency,0
-
Bear in mind that with those numbers for conduction hx wall thickness must be greatly considered. An aluminum, and cast iron hx is considerably thicker than a ss hx. With that in mind the flame to water transfer may be quite different
Longevity must be considered in the overall efficiency equation.1 -
-
Fluid quality is the big issue. When the HX metals are paper thin you need to be right on with water quality and ongoing yearly checks.
Properly applied hydronic conditioners protect any/all metal surfaces. Some aluminum brands ship with treatment now.
Conditioner chemicals really needs to be blended with good quality water also.Bob "hot rod" Rohr
trainer for Caleffi NA
Living the hydronic dream1 -
You are correct Gordy, wall thickness plays a big part. But who would have thought stainless is at the bottom of heat transfer.0
-
-
Hope you never see condensing temperature inside the aluminum... Have seen this too many times will not touch AL anymore.
IMO
D
0 -
Aluminum is much better overall at heat transfer but also for uniform, predictable heat transfer. SS is unpredictable. Corrosion resistance is a function of temperature as well as ph and overall reactivity. Metals do funky things at different temps. While ss is certainly indicated at temps above around 1,221°F at temps above around 1,050°F most alloys of ss are susceptible to sensitization and intergranular corrosion from chromium carbides forming at grain boundaries. This why welds are common failure points with ss. It's also why low carbon alloys are used for applications in these ranges. Where corrosion is more concern at lower temps then super ferritic alloys, such as AL29-4c (29% chromium, 4% molybdenum) perform well.
Many kitchen pot mfrs. use aluminum or an aluminum disc insert because of its heat transfer properties.
0 -
I have said before I like the Intergas boiler heat exchanger... Pretty unique. Aluminum block. Copper waterways. Less than ideal water chemistry has less of a chance to damage it. Great heat transfer and a compact footprint.
0 -
@Bob Harper my point is strictly the conduction process, and just because one metal is inherently more conductive than another one still has to make an assessment, and look at other variables in the conduction arena.
I’m quite sure this is considered when they decided to use Stainless as part of an HX design whether it’s water tube, or fire tube. The Wall is thinner than aluminum, or cast iron designs. The wall of either HX design in SS could have easily been made thicker. I’m sure it came down to heat transfer, and durability a fine line in the design.
0 -
This chart is interesting. It seems that 416 the better grade SS isn’t always a better choice than 316, or even 304 for a corrosion resistance grade with certain chemicals.
409 isn’t listed
https://www.engineeringtoolbox.com/metal-corrosion-resistance-d_491.html0 -
The thing with alloys is a trade off of properties. While 416 is the best machining ss, it is lousy for welding and sucks in chloride environments. It's a matter of what's most important and can you live with the short comings.0
-
"...are we as mechanical boiler guys treating water on every job?"
Ahhh! YES! The old days of hook'er up the main and as one shepherd says to another, "Lets get the flock out of here." are over.
Boiler manufacturers are becoming more concerned about the quality of water moving thru their boilers. Installers must heed these requirements for warranty protection and professional service to the customer demands it. As my dad said, "A jobs not done until it's done right."
0
Categories
- All Categories
- 87K THE MAIN WALL
- 3.2K A-C, Heat Pumps & Refrigeration
- 58 Biomass
- 427 Carbon Monoxide Awareness
- 113 Chimneys & Flues
- 2.1K Domestic Hot Water
- 5.7K Gas Heating
- 109 Geothermal
- 161 Indoor-Air Quality
- 3.6K Oil Heating
- 70 Pipe Deterioration
- 995 Plumbing
- 6.3K Radiant Heating
- 391 Solar
- 15.4K Strictly Steam
- 3.4K Thermostats and Controls
- 55 Water Quality
- 44 Industry Classes
- 48 Job Opportunities
- 18 Recall Announcements