Welcome! Here are the website rules, as well as some tips for using this forum.
Need to contact us? Visit https://heatinghelp.com/contact-us/.
Click here to Find a Contractor in your area.
Evaluating Quotes/Plans for Oil to Gas Conversion
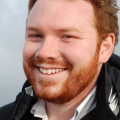
mjacksonw
Member Posts: 9
Hey folks,
This site has been an amazing resource to learn from over the last few weeks, so thanks for being awesome in general. It's probably taught me just enough to be dangerous so far, but still.
We moved into a ~1920 colonial in MA which had its fair share of heating/cooling challenges. There's approximately zero insulation (that's getting fixed, hopefully, starting tomorrow) across 2600sqft. The plumbing is a bit of a mess, exacerbated by a quickly corroding galvanized water supply pipe (hopefully fixed once the ground thaws out, but for now the house maxes out at about 3.5gpm). But most relevant is that the oil boiler is over sixty years old, and it managed to guzzle over 150 gallons of oil in a week when it was chilly earlier this month. So it seems worthwhile to start planning its replacement, and since we already have gas in the house, we've leaned toward saving the square footage of the tank and converting.
Other relevant details: we have hot water radiators in the old part of the house, and hot water baseboard in the three-story addition on the back of the house. The old part of the house is one zone, and the addition is divided into two. We have lots of large old double-hung windows, and a skylight in the finished attic. The unfinished basement is pretty warm itself, and the old carriage garage (a part of the basement) has an enormous ceiling radiator in it (which is good since we use it as a gym). Finally, we have DWH served by a relatively old (~15-20yrs) direct-fired gas 40gal tank – it's mostly fine, but there's a ~35' run from it at the perimeter of the basement to the plumbing core in the middle of the basement, and hot water takes a while (exacerbated by the low flow from the main).
I've been interested a combi unit. Obviously that would exacerbate the "hot water takes a while" problem without some sort of recirc solution, but the saved square footage would be great. I asked around the neighborhood, and a fair number of folks have some combination of combi (naviens and rennais seem popular) or modcon/indirect.
We've had three contractors come by for quotes, and each of them have been relatively dismissive of the combi concept.
Contractor 1 – This was a bit of a dud of a visit, from a pretty active company in an adjacent town. He seemed really annoyed that I was asking semi-researched questions, said he'd never touch a Navien and wouldn't trust anyone who ever did (Lochinvar was his go-to). Pretty dogmatic, which isn't my kind of guy. He never followed up with a quote, and didn't need to see anything other than the basement during his visit.
Contractor 2 – This was a large chain (multiple cities, etc), and the guy who came out was a sales guy rather than an installer or engineer. He did perform a Manual-J and came back with a quote based around a Bosch 151 combi unit, though there's a disclaimer that they can't guarantee the on-demand DWH will keep up. They also called out that they'd create an extra capped zone for future expansion, implement a "primary/secondary piping design with separate circulator pump," and use 3-speed Grundfos pumps. They'd be venting out the rear of the basement, which would be a pretty big run.
Contractor 3 – This was a smaller ~30-employee outfit mentioned by a neighbor, and the guy who came by is a technician who pitches in on sales stuff. I liked him. He performed a Manual-J as well, and his quote insisted on an indirect rather than a combi. The proposed system would be a Burnham K2 firetube at 110mbtu and a Heat-Flo 40gal indirect for DWH. The quote also includes lining our chimney and venting there. This quote was a couple grand less than contractor #2's quote, but same general neighborhood.
I feel like I need another quote or two, but I'm warming up to the indirect tank, especially since there's an option to position it directly below the plumbing core. It feels like having a 35' run from the boiler to the indirect would be better than having that length added to the distance between the tank and the fixtures.
Neither of the two relevant contractors provided the heat load they came up with, so I suppose the 110mbtu K2 could still be oversized, but it's not like he's throwing a 155 at me. Still, since the K2FT has a 5:1 TDR rather than 10:1, I guess it might end up mattering.
I'd love feedback and input about the general direction (combi/indirect, position of the indirect, etc), what to look for in another quote, and other questions I should be asking or answering along the way. My main priorities are that it 1) works well, 2) is efficient, and 3) saves space. I'd rather spend a little more on something that meets those priorities.
Thanks!
This site has been an amazing resource to learn from over the last few weeks, so thanks for being awesome in general. It's probably taught me just enough to be dangerous so far, but still.
We moved into a ~1920 colonial in MA which had its fair share of heating/cooling challenges. There's approximately zero insulation (that's getting fixed, hopefully, starting tomorrow) across 2600sqft. The plumbing is a bit of a mess, exacerbated by a quickly corroding galvanized water supply pipe (hopefully fixed once the ground thaws out, but for now the house maxes out at about 3.5gpm). But most relevant is that the oil boiler is over sixty years old, and it managed to guzzle over 150 gallons of oil in a week when it was chilly earlier this month. So it seems worthwhile to start planning its replacement, and since we already have gas in the house, we've leaned toward saving the square footage of the tank and converting.
Other relevant details: we have hot water radiators in the old part of the house, and hot water baseboard in the three-story addition on the back of the house. The old part of the house is one zone, and the addition is divided into two. We have lots of large old double-hung windows, and a skylight in the finished attic. The unfinished basement is pretty warm itself, and the old carriage garage (a part of the basement) has an enormous ceiling radiator in it (which is good since we use it as a gym). Finally, we have DWH served by a relatively old (~15-20yrs) direct-fired gas 40gal tank – it's mostly fine, but there's a ~35' run from it at the perimeter of the basement to the plumbing core in the middle of the basement, and hot water takes a while (exacerbated by the low flow from the main).
I've been interested a combi unit. Obviously that would exacerbate the "hot water takes a while" problem without some sort of recirc solution, but the saved square footage would be great. I asked around the neighborhood, and a fair number of folks have some combination of combi (naviens and rennais seem popular) or modcon/indirect.
We've had three contractors come by for quotes, and each of them have been relatively dismissive of the combi concept.
Contractor 1 – This was a bit of a dud of a visit, from a pretty active company in an adjacent town. He seemed really annoyed that I was asking semi-researched questions, said he'd never touch a Navien and wouldn't trust anyone who ever did (Lochinvar was his go-to). Pretty dogmatic, which isn't my kind of guy. He never followed up with a quote, and didn't need to see anything other than the basement during his visit.
Contractor 2 – This was a large chain (multiple cities, etc), and the guy who came out was a sales guy rather than an installer or engineer. He did perform a Manual-J and came back with a quote based around a Bosch 151 combi unit, though there's a disclaimer that they can't guarantee the on-demand DWH will keep up. They also called out that they'd create an extra capped zone for future expansion, implement a "primary/secondary piping design with separate circulator pump," and use 3-speed Grundfos pumps. They'd be venting out the rear of the basement, which would be a pretty big run.
Contractor 3 – This was a smaller ~30-employee outfit mentioned by a neighbor, and the guy who came by is a technician who pitches in on sales stuff. I liked him. He performed a Manual-J as well, and his quote insisted on an indirect rather than a combi. The proposed system would be a Burnham K2 firetube at 110mbtu and a Heat-Flo 40gal indirect for DWH. The quote also includes lining our chimney and venting there. This quote was a couple grand less than contractor #2's quote, but same general neighborhood.
I feel like I need another quote or two, but I'm warming up to the indirect tank, especially since there's an option to position it directly below the plumbing core. It feels like having a 35' run from the boiler to the indirect would be better than having that length added to the distance between the tank and the fixtures.
Neither of the two relevant contractors provided the heat load they came up with, so I suppose the 110mbtu K2 could still be oversized, but it's not like he's throwing a 155 at me. Still, since the K2FT has a 5:1 TDR rather than 10:1, I guess it might end up mattering.
I'd love feedback and input about the general direction (combi/indirect, position of the indirect, etc), what to look for in another quote, and other questions I should be asking or answering along the way. My main priorities are that it 1) works well, 2) is efficient, and 3) saves space. I'd rather spend a little more on something that meets those priorities.
Thanks!
0
Comments
-
Forget the first 2 contractors. You will probably not be happy with a combi in the DHW department. Indirects are a better fit.
If your insulating and doing windows for sure that should be included in the boiler sizing, it will reduce the size of the boiler and the cost of the job.
Where are you located in MA.? Try "find a contractor" on this site. @Charlie from wmass and others may respond0 -
Yes, @Charlie from wmass would be a good man to call. At least in central Mass. Gary Wilson is also excellent ( @GW ).
A thought on the windows: They undoubtedly need work -- but they need work, not replacement. You will get much better bang for your buck as well as retaining value if you find a good carpenter (or better yet, since you seem to like DIY, learn to do it yourself -- it's not hard) to repair them and tighten them up. Then you can use either inner or outer storm windows and the end result will be very nearly as good as the very top end replacement windows -- and last a lot longer.Br. Jamie, osb
Building superintendent/caretaker, 7200 sq. ft. historic house museum with dependencies in New England1 -
How do you know the K2FT is 5:1? I couldn't find it on US Boiler's website.0
-
Thanks for the early feedback! I'm in Newton, outside of Boston.
I'd mentioned the reinsulation work during the sizing, so I'm assuming that'd been taken into account. They didn't appear to directly assess the insulation anyway.
@Eastman: I saw it on the product spec PDF: https://file.ac/QjNiu2_qVgE/K2-FT Product Data Sheet.pdf0 -
There's apparently 3 different K2 models: the original K2 water tube, a K2 fire tube, and a newer K2 water tube B model that has 10:1. Then there's a whole bunch of other models with different names. I don't understand why they don't consolidate their product line.0
Categories
- All Categories
- 87K THE MAIN WALL
- 3.2K A-C, Heat Pumps & Refrigeration
- 58 Biomass
- 427 Carbon Monoxide Awareness
- 113 Chimneys & Flues
- 2.1K Domestic Hot Water
- 5.7K Gas Heating
- 109 Geothermal
- 161 Indoor-Air Quality
- 3.6K Oil Heating
- 70 Pipe Deterioration
- 995 Plumbing
- 6.3K Radiant Heating
- 391 Solar
- 15.4K Strictly Steam
- 3.4K Thermostats and Controls
- 55 Water Quality
- 44 Industry Classes
- 48 Job Opportunities
- 18 Recall Announcements