A few questions re: main venting capacity, condensate return, etc.

1. Main Venting - I've attached a quick diagram of my system
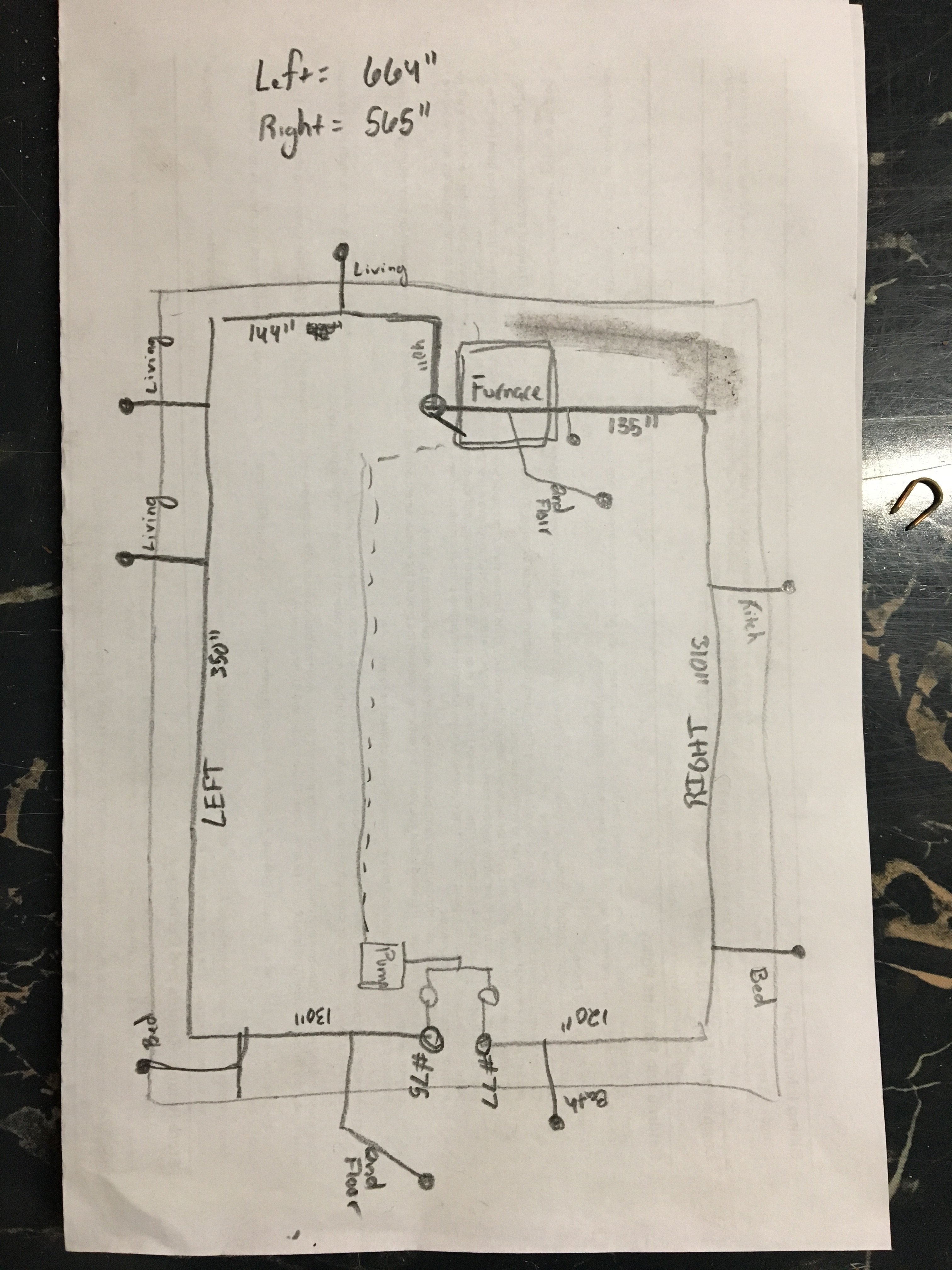
, but in short, my 2" main line is vented as follows: "Left Main" = 664" long, vented by a leaky Ventrite #75. "Right Main" = 565" long, vented by a Ventrite #77 (photo attached)
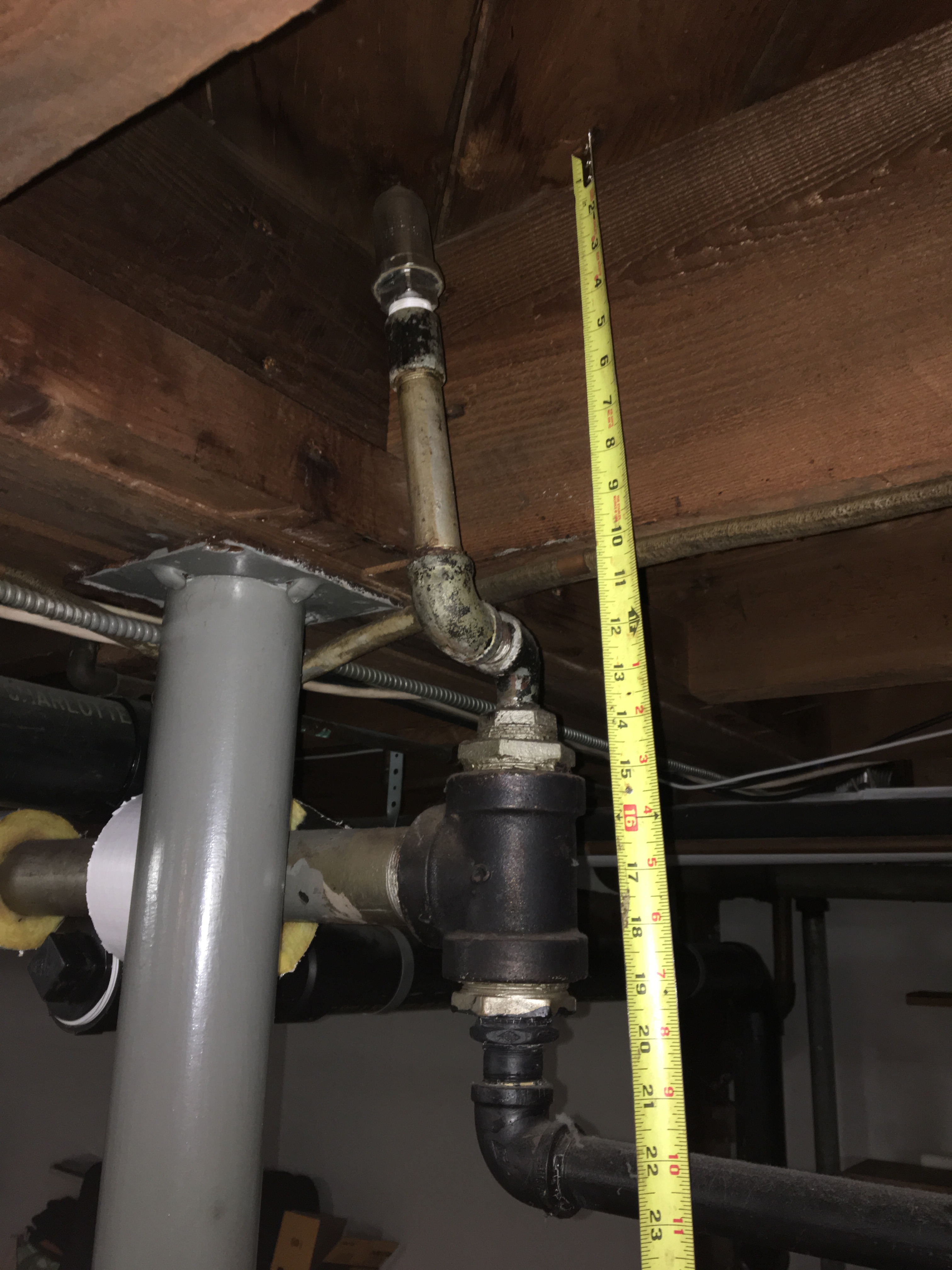
. The #75 has to be replaced because it's leaking steam, but I have a strong feeling that I need much more venting on my mains. The boiler cycles many times on a cold start before steam hits the radiators, and it can take upwards of 40 minutes of runtime before steam hits the radiators furthest from the boiler. I am going to go ahead and replace both main vents -- what would you all recommend I replace them with?
2. Condensate Return Pump - Below each main vent, the system is piped to a respective F&T trap, which both meet at a T and drain into a condensate return pump. See attached photos.
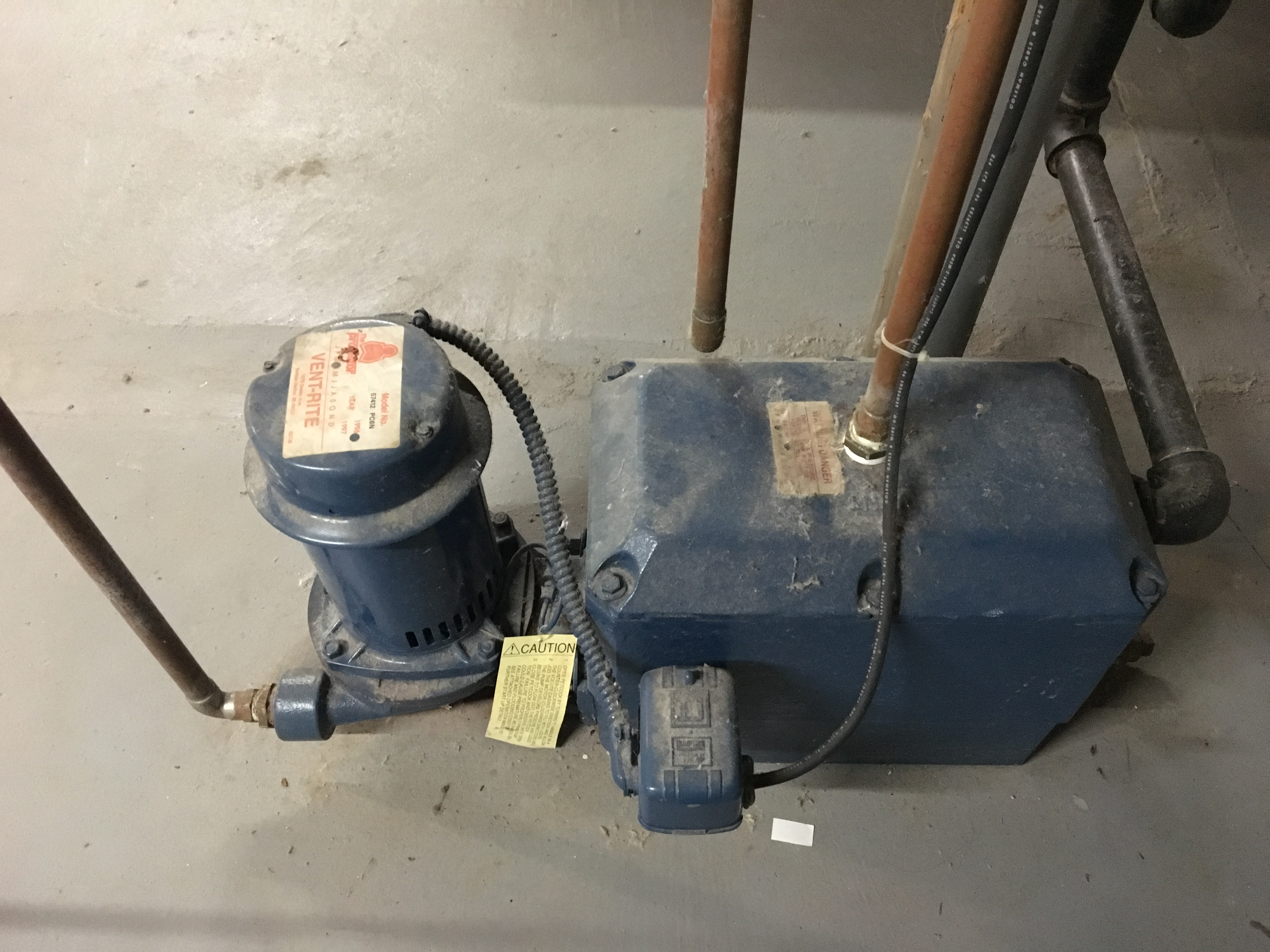
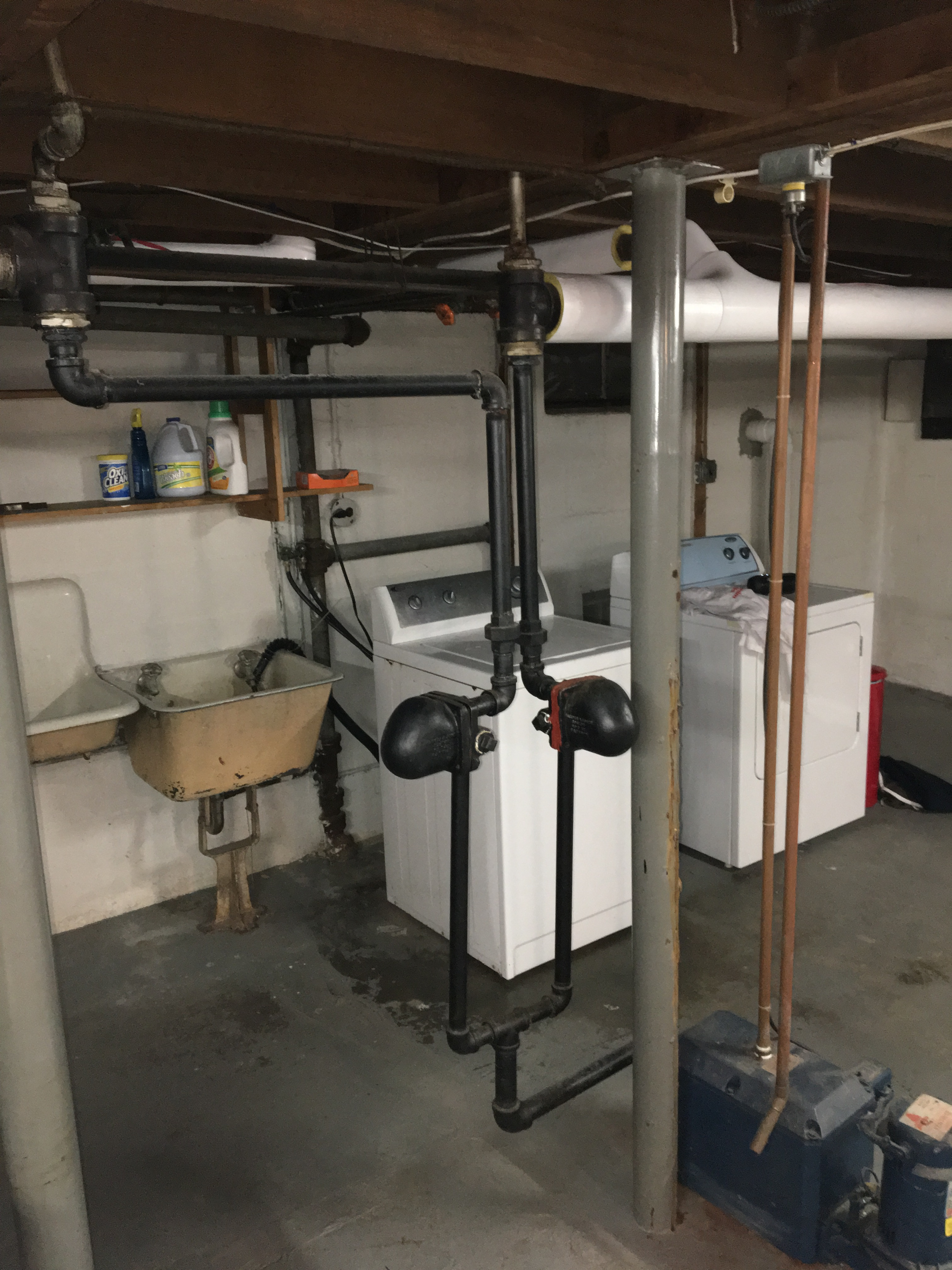
I believe a condensate return pump was used vs. gravity return because the lines for a gravity return would run right through the center of the basement, reducing the usable width in the basement. I'm having a problem with the return pump not triggering reliably to send water back to the boiler. Every so often, when the boiler has extended downtime, or when we set the thermostat low due to being away for some time, we'll come back to a very cold house and a boiler with the low water cutoff triggered. At first I thought I had a leak so I added water to the system, to come back later and notice it was now overfilled. I learned what is actually happening is water is collecting in the condensate pump, but not enough for the float to trigger the pump to send the water back to the boiler. If I lightly tap the float switch on the pump, sure enough it triggers, pumps its water, and my boiler water level goes back to normal. Do I need to service the pump? Adjust the float? Any pointers or instructions on how to do this?
Also related to above, the only water hammer I notice in my system is after the condensate return pump fires, particularly when the boiler hasn't been cycling much. I'll hear the pump trigger, and 1-2 seconds after it finishes pumping, there's a loud water hammer.
After I take care of these two main issues, I'll focus on balancing individual rooms on a radiator by radiator approach. Thanks for any help you all can provide. This website is an excellent resource.
Comments
-
On the vents. I'd replace them both with Barnes & Jones "BigMouth" vents. They're available both from the store on this website, or from Amazon. Inexpensive (definitely not cheap!) and very reliable.
The condensate return pump is going to be a headache. I can see why the folks who did it did it, but ... argh. The water hammer may be from the section of horizontal pipe in the drop which I see on the left in the picture showing the laundry machines. May not be, too, but I'm thinking water may lie in that bit of pipe and be inspired to move when the pump operates. Just a guess. As to the float control. You might just be able to get it to behave by checking to make sure the float moves freely, but in any case it would seem that the margin between your boiler's water capacity and the amount of water which gets out in the system before the float trips is probably pretty small. What is the low water cutoff on your boiler? If it's a McDonell Miller MM67 float type, by any chance? If it is, there's a workaround.Br. Jamie, osb
Building superintendent/caretaker, 7200 sq. ft. historic house museum with dependencies in New England-1 -
Thanks!Jamie Hall said:On the vents. I'd replace them both with Barnes & Jones "BigMouth" vents.
It's a Hydrolevel Company CycleGuard. When I get into the situation described above, the water level in the boiler is below 1/2 of the "water level" (line drawn on sight glass). Tripping the condensate pump brings it right back up to water level. Basically, 1/2 of the boilers capacity is stuck in the pump during that scenario.Jamie Hall said:What is the low water cutoff on your boiler? If it's a McDonell Miller MM67 float type, by any chance? If it is, there's a workaround.
0 -
Oh well. It was an idea. The MM67 has contacts which can be used to activate an automatic water feeder -- or a boiler feed pump. However..
You might try adjusting the float activation in the condensate return tank with the objective of getting it to turn on at a lower level.
Br. Jamie, osb
Building superintendent/caretaker, 7200 sq. ft. historic house museum with dependencies in New England0 -
I would suggest you set the float switch to the absolute minimum of it's range of travel.
If your unit has the float switch I think it has, the maximum range of level change is 5" and the minimum is 2".
Setting the float switch to the minimum range will decrease the cycle time and keep condensate moving to the boiler, not holding it up stored in the condensate pump's receiver tank.Dennis Pataki. Former Service Manager and Heating Pump Product Manager for Nash Engineering Company. Phone: 1-888 853 9963
Website: www.nashjenningspumps.com
The first step in solving any problem is TO IDENTIFY THE PROBLEM.0 -
The problem with a float operated condensate tank is the inability of the tank to know how much water the boiler needs.
Normally that type of tank would be used in a remote area far from from the boiler, and would pump back to a feed tank, next to the boiler, whose pump was triggered by the water level in the boiler, using the second contacts in the LWCO.
Luckily, you can pipe around the tank and pump, and convert to gravity. The old tank could be sold, or made into a flower box, by cutting the top off.
Yes, your main vents are much too small, and are running the boiler 40 minutes too long, several times a day! This lack of venting is compounded by the cycle guard LWCO, which constantly interrupts firing every few minutes. They waste so much fuel, that were they to be all outlawed, and replaced, we would not have to now drill for oil in the national parks, and the White House grounds.—NBC1 -
Exactly the solution I was hinting at. I hope @Pumpguy is right, for your sake!Pumpguy said:I would suggest you set the float switch to the absolute minimum of it's range of travel.
If your unit has the float switch I think it has, the maximum range of level change is 5" and the minimum is 2".
Setting the float switch to the minimum range will decrease the cycle time and keep condensate moving to the boiler, not holding it up stored in the condensate pump's receiver tank.Br. Jamie, osb
Building superintendent/caretaker, 7200 sq. ft. historic house museum with dependencies in New England0 -
Well, we can't see all the basement there could be other obstructions so maybe gravity cannot be used. Remove the float switch & float assembly and clean it up. They may have had wet returns under the basement floor originally.
Your water hammer is most likely happening in the pump discharge piping. You need to elbow up and then back down into the boiler with a vacuum breaker at the top of the rise. @Dan Holohan has posted how to pipe this (I think it's in LAOSH) as well
And install the big mouth vents as @Jamie Hall mentioned
Just 1 note of caution. Those F & T traps are carrying all the condensate load fro all your radiation + whatever condensate forms in the piping. They should also be sized at 2x the load for a safety factor. I would calculate your edr and check the traps sizes.
looking at the piping just seems like the condensate pump and traps are not from the original install but I could b e wrong0 -
@PumpguyPumpguy said:I would suggest you set the float switch to the absolute minimum of it's range of travel.
If your unit has the float switch I think it has, the maximum range of level change is 5" and the minimum is 2".
Setting the float switch to the minimum range will decrease the cycle time and keep condensate moving to the boiler, not holding it up stored in the condensate pump's receiver tank.
It's a Square D float switch. I believe it's a model #9037 but there are no markings on it. Here's a photo:
Would I set the float switch to the minimum range by adjusting the top screw in that photo?
Thanks for the insight - it's surely appreciated.
1 -
@EBEBRATT-Ed Original wet returns under the floor would make sense. There's disturbance to the concrete floor near the condensate pump and near the boiler. I'll do my best to remove and clean the float, perhaps it is sticking. Thanks. I can't think of a way to pipe gravity returns without really cutting down on the useable space in the basement. If I can adjust the float on the condensate pump and get it working reliably, this should work fine until the pump kicks the dust, then I'll think about gravity returns.EBEBRATT-Ed said:Well, we can't see all the basement there could be other obstructions so maybe gravity cannot be used. Remove the float switch & float assembly and clean it up. They may have had wet returns under the basement floor originally.
I'll search around to see if I can find Dan's post on how to pipe the return correctly. Any keywords I should use?EBEBRATT-Ed said:Your water hammer is most likely happening in the pump discharge piping. You need to elbow up and then back down into the boiler with a vacuum breaker at the top of the rise. @Dan Holohan has posted how to pipe this (I think it's in LAOSH) as well
And install the big mouth vents as @Jamie Hall mentioned
Just 1 note of caution. Those F & T traps are carrying all the condensate load fro all your radiation + whatever condensate forms in the piping. They should also be sized at 2x the load for a safety factor. I would calculate your edr and check the traps sizes.
looking at the piping just seems like the condensate pump and traps are not from the original install but I could b e wrong
Here's a photo of one of the F&T traps:
Do two of those seem appropriate given the length & diameter of the main? ...or do you need more than that to calculate the EDR? (still learning). Thanks for chiming in -- I really appreciate your insight.0 -
@nicholas bonham-carter I appreciate your humor. I'll try to get the condensate return pump to function reliably, but if not, or when it kicks the dust, I'll start brainstorming about gravity returns. Regarding venting; I already have the Big Mouth vents on order.nicholas bonham-carter said:The problem with a float operated condensate tank is the inability of the tank to know how much water the boiler needs.
Normally that type of tank would be used in a remote area far from from the boiler, and would pump back to a feed tank, next to the boiler, whose pump was triggered by the water level in the boiler, using the second contacts in the LWCO.
Luckily, you can pipe around the tank and pump, and convert to gravity. The old tank could be sold, or made into a flower box, by cutting the top off.
Yes, your main vents are much too small, and are running the boiler 40 minutes too long, several times a day! This lack of venting is compounded by the cycle guard LWCO, which constantly interrupts firing every few minutes. They waste so much fuel, that were they to be all outlawed, and replaced, we would not have to now drill for oil in the national parks, and the White House grounds.—NBC
Now with the LWCO -- what's the solution here? Replace the Cycle Guard with a different LWCO that has a different behavior?0 -
@Jamie Hall , @EBEBRATT-Ed , are those traps ok at that height? Do they need to be some minimum height above the tank or the boiler water line?0
-
The trap height should be OK. But we should focus on eliminating the traps and pump.
I would look at running the mains full size over to the wall near the laundry sink, dropping them there and running a wet return along the wall back to the boiler, maybe a foot above the floor or so. This would eliminate a lot of moving parts and the time lag for the water to come back.All Steamed Up, Inc.
Towson, MD, USA
Steam, Vapor & Hot-Water Heating Specialists
Oil & Gas Burner Service
Consulting0 -
@entomodonata , Yes, all Square D 9037 screw-in type H float switches as shown in your picture can be set for a minimum 2" level change. This adjustment is made by moving the semi-circular stops so they are in contact with the pivot arm.
The actual position of these stops determines where the level change occurs.Dennis Pataki. Former Service Manager and Heating Pump Product Manager for Nash Engineering Company. Phone: 1-888 853 9963
Website: www.nashjenningspumps.com
The first step in solving any problem is TO IDENTIFY THE PROBLEM.-1 -
-
@Jamie Hall To update everyone on this -- I replaced the main vents with Big Mouths and my time for steam to get to the radiators on a cold start has been cut in half. The system overall is cycling much less, and my condensate return problem has been much less troublesome (also adjusted the float which likely helped).Jamie Hall said:On the vents. I'd replace them both with Barnes & Jones "BigMouth" vents. They're available both from the store on this website, or from Amazon. Inexpensive (definitely not cheap!) and very reliable.
Thanks again for all the great comments and advice.-1 -
Categories
- All Categories
- 87K THE MAIN WALL
- 3.2K A-C, Heat Pumps & Refrigeration
- 58 Biomass
- 426 Carbon Monoxide Awareness
- 113 Chimneys & Flues
- 2.1K Domestic Hot Water
- 5.7K Gas Heating
- 109 Geothermal
- 161 Indoor-Air Quality
- 3.6K Oil Heating
- 70 Pipe Deterioration
- 994 Plumbing
- 6.3K Radiant Heating
- 389 Solar
- 15.4K Strictly Steam
- 3.4K Thermostats and Controls
- 54 Water Quality
- 44 Industry Classes
- 48 Job Opportunities
- 18 Recall Announcements