Welcome! Here are the website rules, as well as some tips for using this forum.
Need to contact us? Visit https://heatinghelp.com/contact-us/.
Click here to Find a Contractor in your area.
System piping and bypass question

tropostudio
Member Posts: 31
I've installed a Westinghouse WBRUNG080 modcon system, using 3x 5-loop Uponor manifolds and Myson T6 radiators. It is a home-run system, with each emitter having its own TRV, except for a couple locations where I installed 2 emitters in series, using a Myson bypass valve at both units in the pair. My understanding is the WBRU080 needs to maintain minimum flow of 1 gpm across the heat exchanger, although that is not explicitly stated in the boiler manual. Pressure drop curve for boiler below:
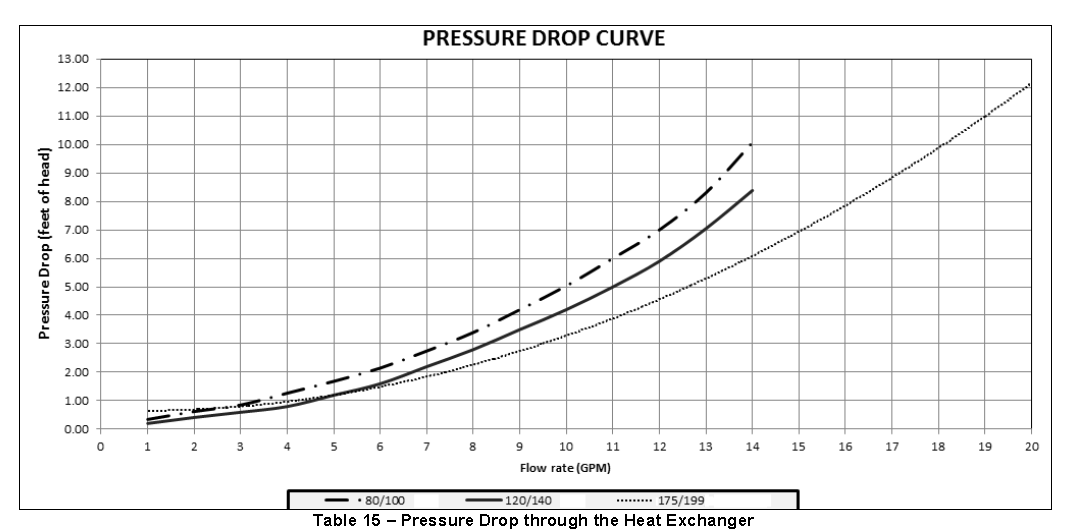
The sketch below labeled 'Current Emitter Piping' shows how it's set up. The sketch explains issues with the system, and need to have a minimum 1 gpm for the boiler even if all loops closed down.
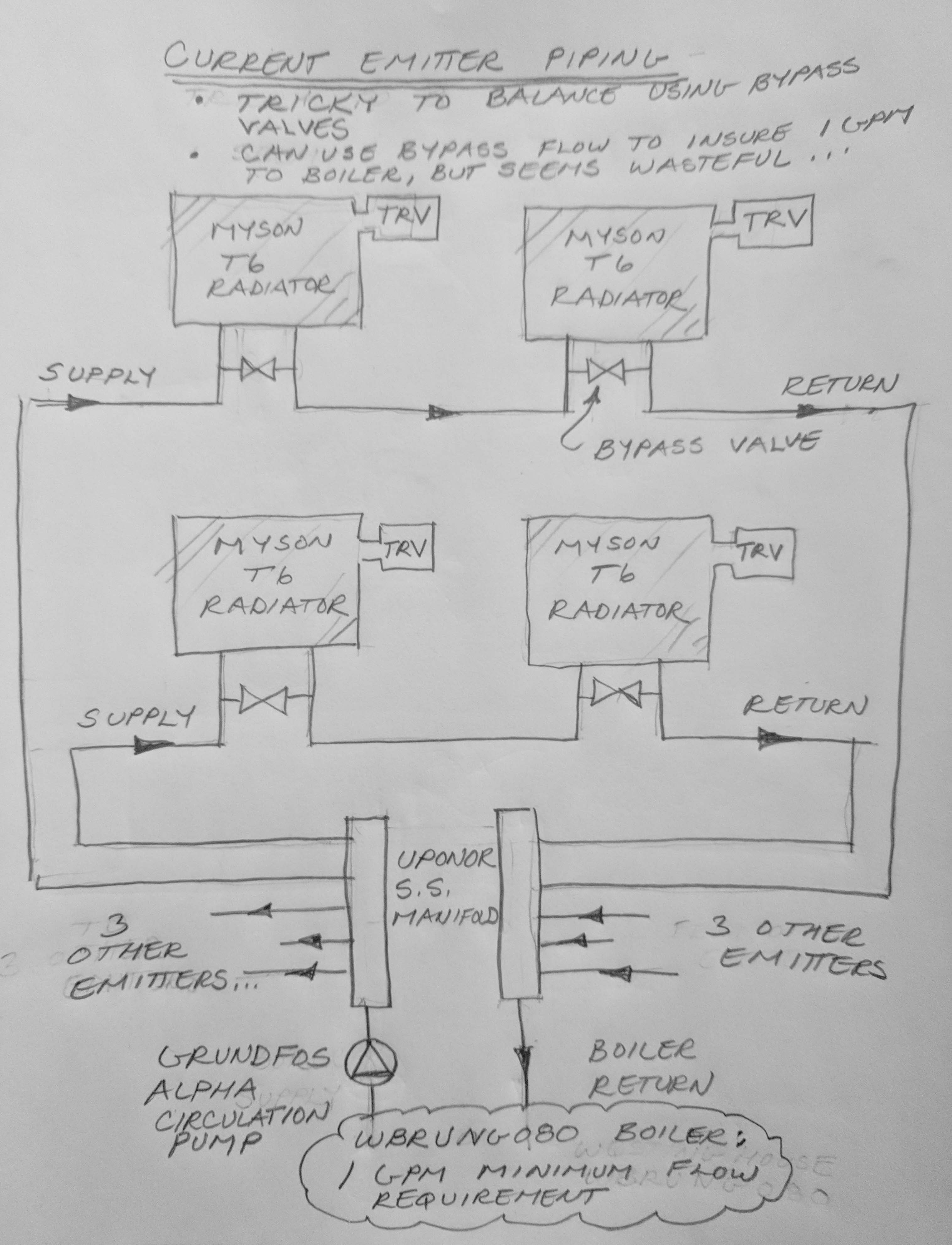
CH is a single pump system, using a Grundfos Alpha. No primary-secondary. I currently have that running in constant pressure mode on low, which indicates 1 gpm even if emitters are closed (because of effective bypass at the paired emitters). Running the Alpha in AutoAdapt mode brought the flows below 1 gpm, so I went to CP Low. DHW is provided through an Amtrol Boilermate 41 gallon tank with Grundfos 3-speed circulation pump, set on medium speed.There is a basic Tstat wired to TT at boiler, set at 80F, while all TRV's are set at 68F. This maintains a constant call for heat at TT. Outdoor re-set is used, although not optimally programmed yet. There are 3 manifolds, each with 5 loops, to cover basement, first, and second floors. The other 2 manifolds are in parallel with that shown in the sketch. Emitters are sized for 140F supply and 25F DT at -8F DD. Total Q at -8F DD is 59kBtuh, with f of 4.7 gpm.
My concern is with making the system easier to balance, and to insure a minimum flow across boiler HX if all emitters are closed. Sketch labeled 'Modify Emitter Piping System?' shows my proposed solution.
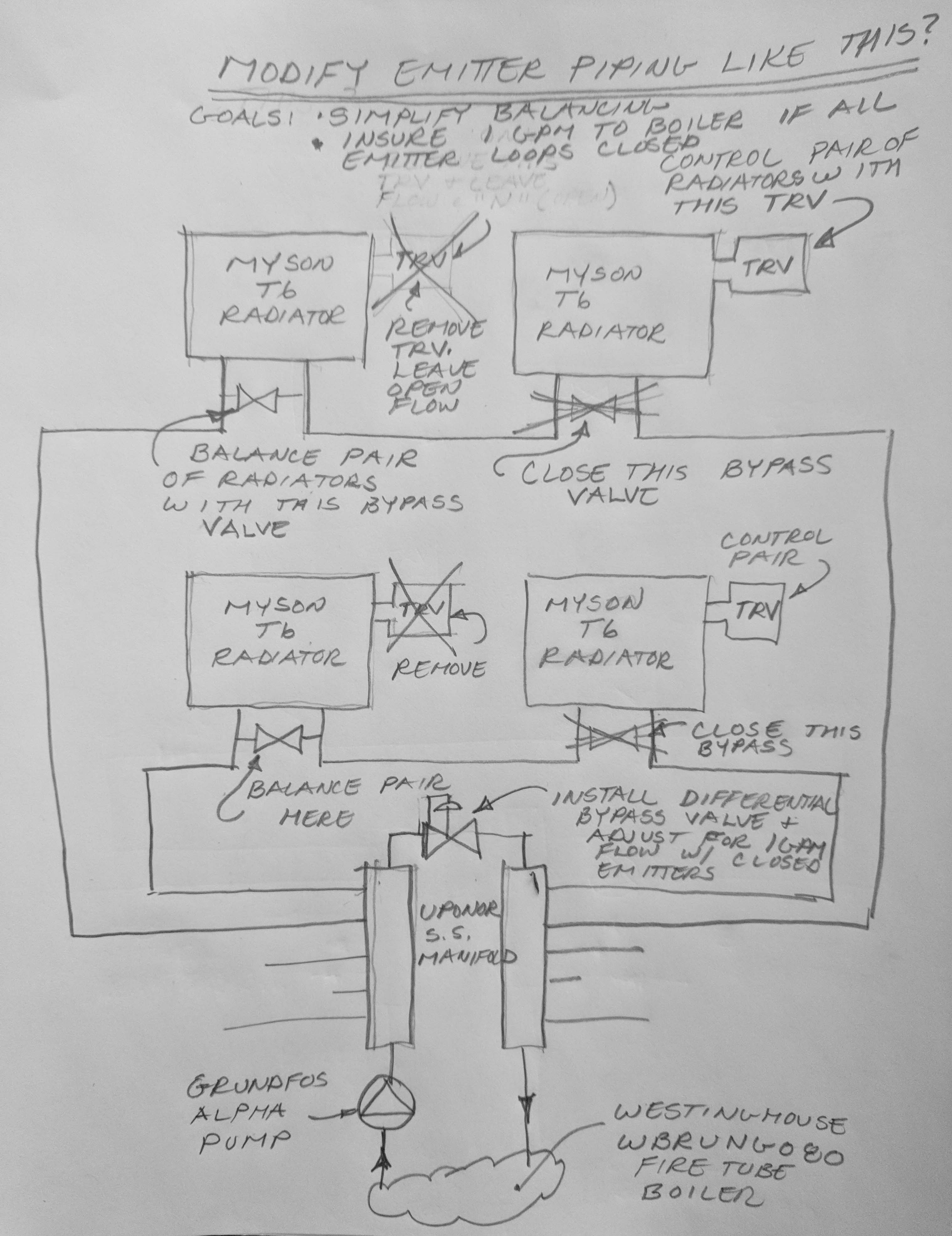
The Alpha will deal with a low or no-flow situation. Is the WBRU080 able to handle that, or will it burn it up? I welcome any critique, suggestions, or alternative solutions.
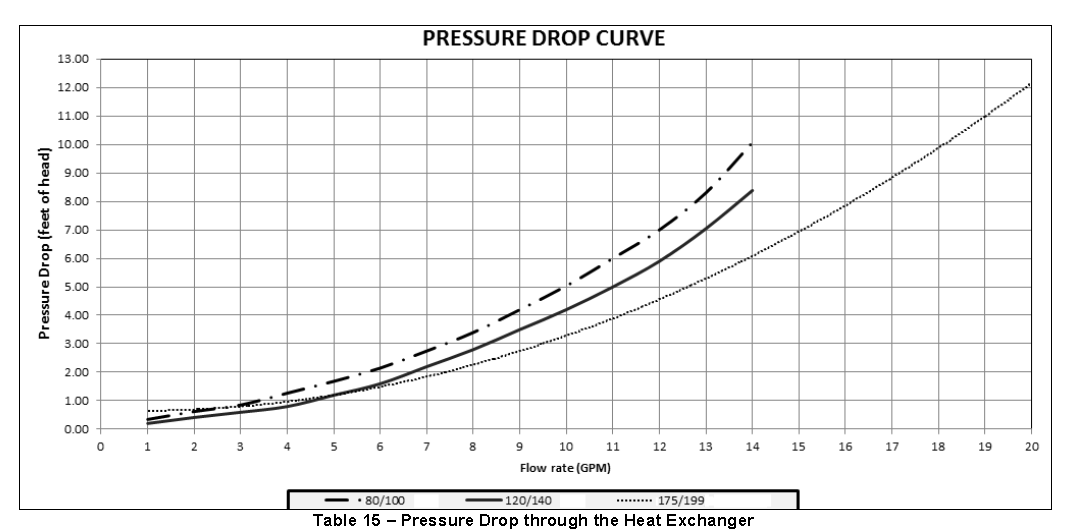
The sketch below labeled 'Current Emitter Piping' shows how it's set up. The sketch explains issues with the system, and need to have a minimum 1 gpm for the boiler even if all loops closed down.
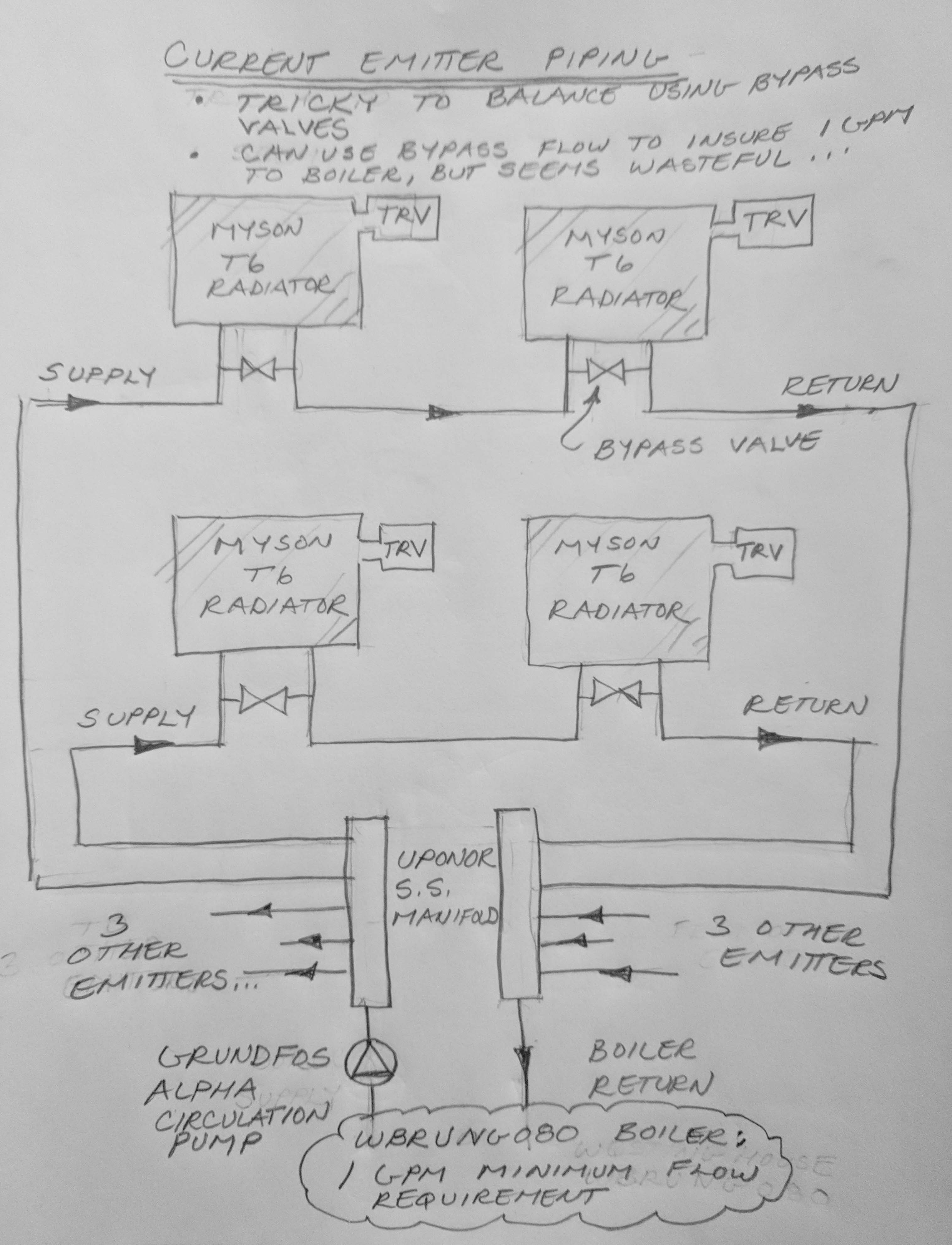
CH is a single pump system, using a Grundfos Alpha. No primary-secondary. I currently have that running in constant pressure mode on low, which indicates 1 gpm even if emitters are closed (because of effective bypass at the paired emitters). Running the Alpha in AutoAdapt mode brought the flows below 1 gpm, so I went to CP Low. DHW is provided through an Amtrol Boilermate 41 gallon tank with Grundfos 3-speed circulation pump, set on medium speed.There is a basic Tstat wired to TT at boiler, set at 80F, while all TRV's are set at 68F. This maintains a constant call for heat at TT. Outdoor re-set is used, although not optimally programmed yet. There are 3 manifolds, each with 5 loops, to cover basement, first, and second floors. The other 2 manifolds are in parallel with that shown in the sketch. Emitters are sized for 140F supply and 25F DT at -8F DD. Total Q at -8F DD is 59kBtuh, with f of 4.7 gpm.
My concern is with making the system easier to balance, and to insure a minimum flow across boiler HX if all emitters are closed. Sketch labeled 'Modify Emitter Piping System?' shows my proposed solution.
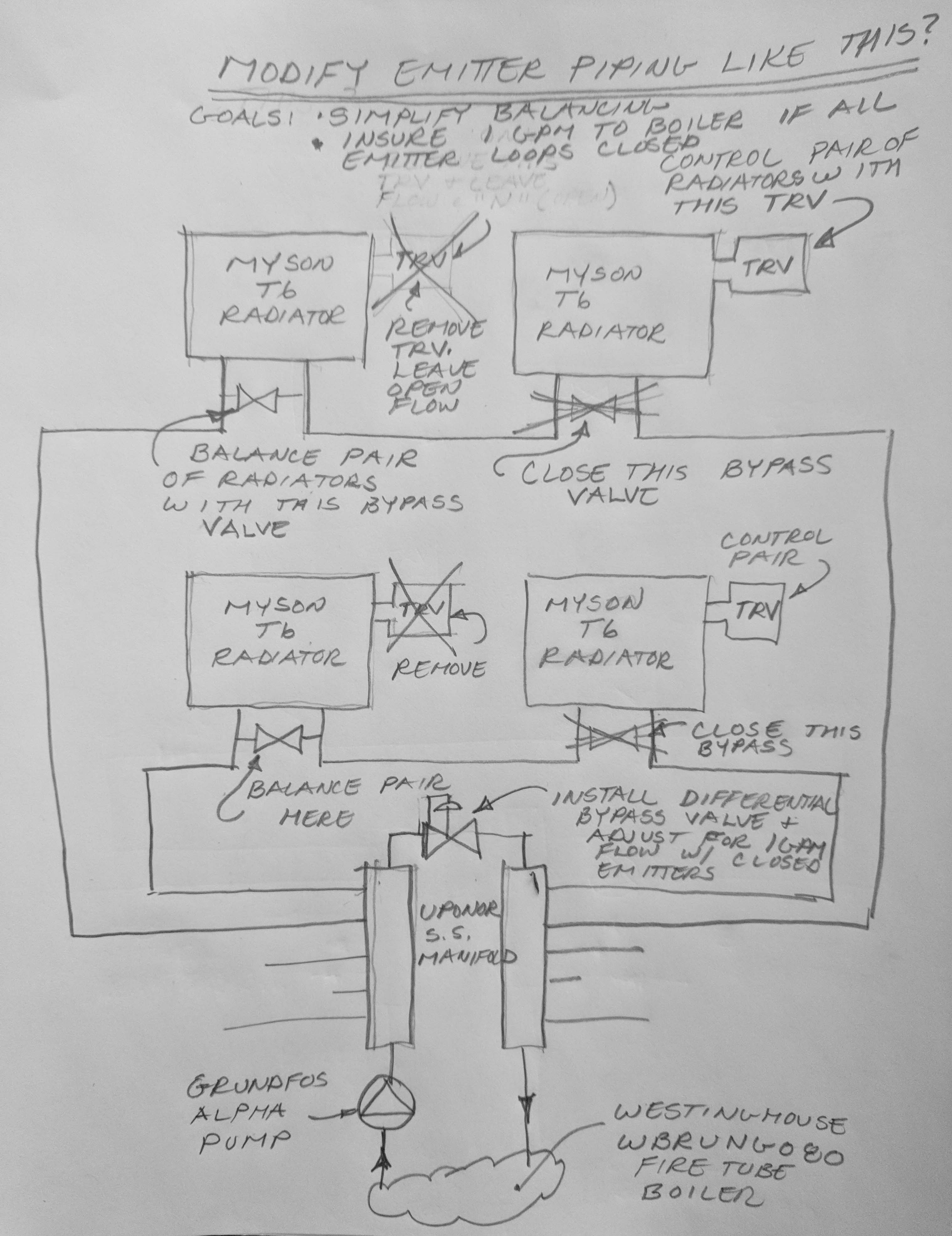
The Alpha will deal with a low or no-flow situation. Is the WBRU080 able to handle that, or will it burn it up? I welcome any critique, suggestions, or alternative solutions.
0
Comments
-
I would not trust the GPM readout on the circulator. Either add a good readable flow setter/ meter or measure the temperature across the boiler when in bypass mode.
The bypass on the radiator valves should allow sufficient flow.
If there is no load or heat call the boiler will shut down based on the operating stat setting.Bob "hot rod" Rohr
trainer for Caleffi NA
Living the hydronic dream0 -
You certainly can't trust the Grundfoss read out on their pumps.
I recently had one in a school where the pump showed 140 gpm @40 ft of head. I suspected the pump wasn't pumping. Putting an amprobe on it showed .4 amps. The pump was rated 5.5 amps.
The pump was air bound and wasn't pumping at all0 -
Thanks for the warning on Alpha pump flow readout.
hot rod - My current stat to TT is placed in the mechanical room, cranked up high, acting as a system-on switch. Every emitter has a TRV. Would you advise moving that stat to a room I want warmer than the others by a couple degrees (bathroom, maybe) and removing the TRV from the emitter in that room? Thinking it would cut out last after other TRV's are closed.
The modification sketch to the paired emitters is to make them into one big radiator, with balancing between units, and have TRV control of the pair at the downstream end. Right now balancing the pairs with individual TRV's and bypass valves is fiddly, and it feels like a lot of hot water is passing right back to the boiler via the return. Every other single emitter per loop has a cold return, and is really easy to adjust at the manifold. If I had a dedicated bypass loop across the end of one of the manifolds to insure flow across the HX, seems like that would be easier to manage.0 -
Is the balance vale simply an H valve with adjustment? that is typically all you need to dial in all the radiator outputs.
The TRV does most of the work, it controls temperature at each unit. The balance just assures a portion of the flow is available for series rads.Bob "hot rod" Rohr
trainer for Caleffi NA
Living the hydronic dream0 -
Correct, just an H valve. One pair pair in particular seems to be really hard to get balanced, and there is no way of knowing the flow through the bypass portion vs what is going through the rads, as the entire loop flow is controlled and measured at a single valve and flow indicator at the manifold. Return temp on that manifold is high with respect to other manifolds, because of bypass flow.
Maybe I should fiddle with the bypass valves to try to get similar flows through each rad while also bringing down the return temp at the entire manifold? That would imply lower flow through the bypass portion, because more available heat is being given off at the rads rather than being returned?
0 -
Usually the instructions will tell you how the bypass was factory set. Here is how the Caleffi works and adjusts.
Bob "hot rod" Rohr
trainer for Caleffi NA
Living the hydronic dream0 -
It appears as though you have created the ultimate micro-zoned mod/con system. Provided the panel rads have been sized properly to heat loss.... why are you shutting them off at a temperature that your reset curve can maintain? Except for sleeping areas that might require tweaking for maximum comfort, it seems counter-productive to use a boiler designed to provide the bare minimum of heat, then try and trick it.0
-
Hot rod - Thanks! The Caleffi one pipe curve looks like the German language instructions with my Simplex bypass valves. I don't read German, but now I get it!
0 -
Paul48 -
I'm hoping my calcs for loop flows and panel radiator sizes are all correct, and that I'll get my rest curve dialed in. I'm not worried about the Alpha pump because it can work at no flow.
I currently keep keep the call for heat constant on the boiler with a single Tstat set at its upper limit. Jumpering the TT temrinals, essentially. It was suggested to me that that call for heat is constant and all my TRV's are closed, I could fry the heat exchanger on the WBRU080 modcon, and that it requires min 1 gpm flow across it Hence
0 -
Why not crank the TRV's up to max, and let the curve do the job?0
-
Paul48 - I think I get it .
If my Manual J, system design calcs, (loop flows, supply and return temps, emitter sizing, et al), and outdoor reset curve are correct, the flow never stops. If the flame is too low, house loses heat faster than it is produced and the boiler throttles up. If the flame is too high, return temp is closer to supply temp than optimal and boiler throttles down. TT is jumpered on and boiler is constantly modulating. Heat exchanger is happy because there is always flow and temp changes are gradual.
Is that essentially correct?0 -
If all the trv shut then won't the boiler still fire and shut off on high limit and sit and refire never circulating the water?0
-
@tropostudio
That's it..........Use the trv's if you want sleeping areas cooler. I'd give that a shot, first. Tweaking the reset curve and parameters can take a bit of time.0 -
@Leon82 - I think you are correct, but probably hard on the boiler and inefficient. My goal now is to get the the curve set so it's constantly running. NYRob suggested I set the max fire on the boiler to match expected load on DD, which is 75-80% of max output. He also suggested I use step modulation to force the boiler to increment from to a high-fire setting more slowly. I've done both, and made sure boost is off.
Thanks to all for your help - this is a great resource.0
Categories
- All Categories
- 87K THE MAIN WALL
- 3.2K A-C, Heat Pumps & Refrigeration
- 58 Biomass
- 427 Carbon Monoxide Awareness
- 113 Chimneys & Flues
- 2.1K Domestic Hot Water
- 5.7K Gas Heating
- 109 Geothermal
- 161 Indoor-Air Quality
- 3.6K Oil Heating
- 70 Pipe Deterioration
- 995 Plumbing
- 6.3K Radiant Heating
- 391 Solar
- 15.4K Strictly Steam
- 3.4K Thermostats and Controls
- 55 Water Quality
- 44 Industry Classes
- 48 Job Opportunities
- 18 Recall Announcements