Welcome! Here are the website rules, as well as some tips for using this forum.
Need to contact us? Visit https://heatinghelp.com/contact-us/.
Click here to Find a Contractor in your area.
Insulation help for staple-up w/sheet plates in heavily-insulated crawlspace vented to upstairs??

Steamback
Member Posts: 39
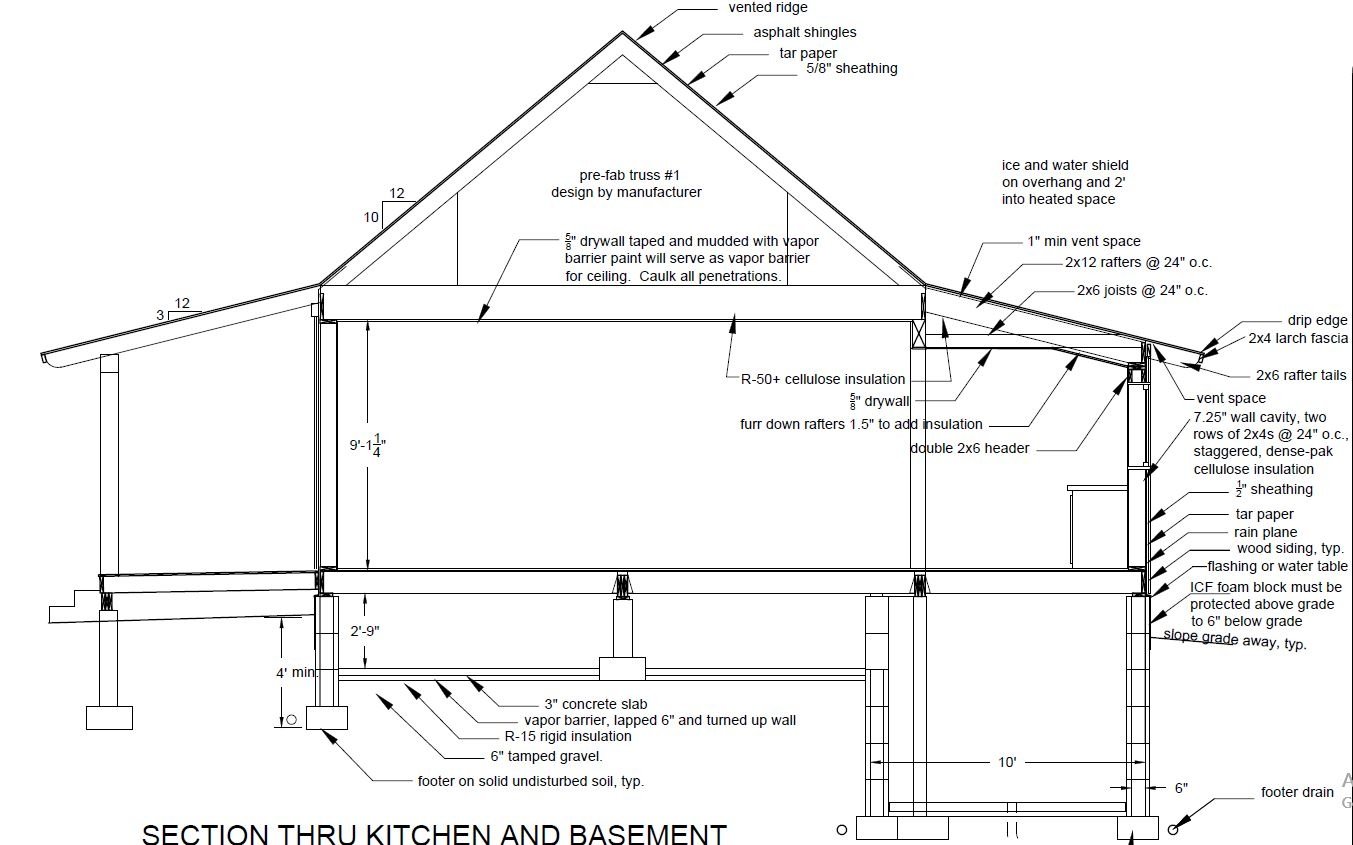
PHOTO Thanks to the Architect!
I have an interesting situation and would like to share for any feedback others may have?
I am installing radiant in a new home with a heavily-insulated, unvented to outside, low-height crawlspace. The builder says that by code he needs to cut openings in the floor system to the upstairs (about 1 small air grate per room) to facilitate ventilation to the upstairs, meaning between the enclosed crawlspace and the living space above. I was a bit surprised and not aware of such a code? It seems a little dumb to me but maybe I have not thought it through. Anyway…this seems to change a bit my insulation requirements for the radiant underfloor install if I am correct?
The house is respectable in terms of air-sealing and insulation. The slab in the crawlspace has R-15 under it. The perimeter walls of the crawlspace are ICF. The floor system rim board is spray-foamed.
The house is one story at about 1,100 SF. Exterior walls are double wall with offset studs and 7.25" of dense-pack cellulose (R-25+?). Ceiling is R-50 blown-in cellulose.
The house received a respectable blower-door test even with the heat recovery ventilation equipment installed, but the homeowner does plan to install a fireplace. I did in my heat loss calculations and radiant layout design confirm that most likely, even with the fireplace, the house should be able to be heated on coldest days with a radiant supply water temperature of about 130-135 and a floor temperature not exceeding 85F. Hopefully I am correct on that.
The radiant system I am installing is Wirsbo ½” hePex with dual-channel sheet aluminum at full coverage on the subfloor (1/4” gaps between plates with 14.5” width plates in 16” o.c. joist bays). I know there is debate to be had on whether I should have spent the money on heavier extrusion plates, but for various reasons that is what I doing.
I am running the PEX in ~250’ loop lengths. The final install looks to be 7 loops total all on one zone. I am thinking I will use a Grundfos Alpha as the primary circulator pump for the radiant and of course use a manifold with balancing valves.
Source heat is two 120 gallon water tanks each with one 4500W element. I’m going to use a boiler outdoor reset control in conjunction with Contactor-type relays to keep the water tank temps as low as possible.
The flooring is an Advantech OSB with ¾” reclaimed thin-strip flooring on top.
I guess my main question is this: with a well-insulated crawlspace and the house I outlined above, assuming someone with underfloor radiant is going to set the thermostat and forget it, combined with the fact that some code makes you vent the well-insulated crawlspace to the upstairs, what type and amount of insulation am I looking for between the joists? In this situation does it make more sense to skimp on insulation or skip it totally and rely on bringing all of the mass (including crawlspace, which is in the thermal envelope) up to temperature and leaving it there all winter?
I know this is debatable, but I’m thinking spraying at least 2 or 3 inches of open-cell foam over the sheet transfer plates. I know I need to check with Wirsbo first to see if they approve of foam, and what foam, in use with hePEX.
The situation is even a little more complex in that the home will not be finished soon and the homeowner will be away all winter, so we have a chance to do a study on heating performance before insulating the radiant underfloor and after . This of course means monitoring temperatures in the crawlspace and house in relation to the thermostat setting. The homeowner also asked me to hold-off on insulating the radiant this winter as long as I believe the house will not freeze, which I’m guessing it will not.
Anyway, to end, back to the original question at hand: when a well-insulated crawlspace hosts an underfloor staple-up radiant with full coverage sheet plates but is also vented to the upstairs, how much exactly do we still care about insulating the radiant system? And if we still do want to insulate it, is it bad to sprayfoam (the correct foam, whatever it is?) directly on to the sheet plates (assuming the PEX manufacturer is OK with it…).
0
Comments
-
you defiantly need to insulate under the tube, or you will have a warm crawlspace. The data T between the plates and the folly drives the transfer, with no insulation below the majority of that transfer will be down.
I have never heard of venting a crawlspace to the living space. It's rare to find a crawlspace that doesn't have some sort of smell, that now transfers upstairs?? Any Radon gas issues where you are?Bob "hot rod" Rohr
trainer for Caleffi NA
Living the hydronic dream0 -
Crawl spaces have to be ventilated or you get mold issues and other potentially devastating structural issues.
Sounds like a tight house. It might be a good candidate for an ERV. With a couple ducts in the crawlspace your issue would be resolved.0 -
You do NOT need to vent and Should Not vent the crawlspace to the outside. That is old wives tales stuff.
Any venting to the outside only brings in damp moist air to condense on the inside walls.
Building Science.com has LOTS of info on this.
Joe Lstiburek has done a ton of research on this.
Seal up the walls AND the floor you will be fine.
https://buildingscience.com/documents/insights/bsi-009-new-light-in-crawlspaces
1 -
If actually code, I would ventilate to adjacent full basement before upstairs to living space. I see its a block wall? Is the bearing wall next to the block wall in the full basement columns, and a beam?Not to difficult to cut openings in block. I have seen it done that way many times.0
-
Bob "hot rod" Rohr
trainer for Caleffi NA
Living the hydronic dream2 -
-
> @Harvey Ramer said:
> Sounds like I might be wrong about venting a crawlspace. However, I have seen an unvented crawlspace that turned into an absolute disaster. Perhaps some other detail was not right?
>
It's quite possible @Harvey Ramer If they didn't pay enough attention to where moisture needed to be controlled, it would be a disaster. Do you remember any details about it?You can have it good, fast or cheap. Pick two0 -
I would share the above articles with the builder and ask for more info about the code. It is possible that it is a misguided local code, it is not in the IRC."If you can't explain it simply, you don't understand it well enough"
Albert Einstein0 -
Read this guys
https://buildingscience.com/documents/bareports/ba-0401-conditioned-crawlspace-construction-performance-and-codes/view
I'd point out that this was the perfect place for radiant ceilings and no insulation in the floor . ICF walls , especially those mostly below grade have little to no infiltration and a very respectable R Value , above what is conservatively listed . A radiant ceiling would excel here , moreso than our typical ceiling installYou didn't get what you didn't pay for and it will never be what you thought it would .
Langans Plumbing & Heating LLC
732-751-1560
Serving most of New Jersey, Eastern Pa .
Consultation, Design & Installation anywhere
Rich McGrath 732-581-38330 -
Older houses here (northern NE) with crawl spaces that were vented had humid soggy conditions in the summer and almost frozen water pipes in the winter and cold floors.
All the crawl spaces/unfinished basements I have done with forced air would get at least 2 supply air vents, one at each end. I have visited these 20 to 30 years after and they are dry and friendly.
But without some air moving I don't think they would have fared as well. Perhaps the vents thru the floor would convect enough air changes.
You would always want to insulate under the warm floor IMO.
A note on the plans, why not drop the crawl space floor down to sit on the (left side) footing? Minimal cost involved. The extra 8" would be welcome. Most architects have never worked in a crawl space and don't understand.0 -
Is the basement floor detail the same as the the crawl detail? If it is what is the difference between the crawl and basement other than height. That would make them both conditioned spaces. In my area NW Ohio we see a lot of partial conditioned basements connected and open to a conditioned crawl or a short basement. If the basement isn't vented to the upstairs directly with vents what makes the crawl any different other than the terminology of crawl space. I would open it up to the basement as Gordy said, gain 8" like Jughne said and make it some usable storage space. That is unless the powers to be insist on something else.0
-
Thanks everyone. So it's clear whether or not the vents in the floor are put in, I really should still insulate the radiant. That's pretty much what I thought, but I appreciate the backup.
I understand that as a rule I can indeed apply spray foam directly over my plates (which are almost 100% full coverage on the floor underside) but I'm struggling on using closed-cell or open-cell. And again, assuming the PEX manufacturer is OK with my foam choice...but anyway, I am pretty much set on open-cell unless people have good advice on why NOT to use open-cell?
I may be naive but I imagine open-cell as being good in the event a leak happens in the PEX someday. I imagine that with open-cell the water will fall from approximately the place the leak might happen, showing me where the leak is so I don't need to cut away a lot of foam to find any holes in the PEX. I can't imagine closed-cell can do that and if there is a leak with closed-cell, I might not know where the PEX is actually broken? Am I wrong on that? Add to that that closed-cell is a lot harder to dig out and remove...
Regarding all the responses, I maybe should not have used the term "crawlspace". In essence this house is a fully enclosed thermal envelope which happens to have a slab and also a floor system suspended a few feet above. The only water issues are probably going to be an accident...the ground-mount PV array wires to the house were done with underground unglued PVC joints and when it rains heavily a stream of water enters the basement area near the service panel. Not sure what logic ever leads an electrician to EVER bury PVC with unglued joints, but I'm all ears on why that might be a common practice...
0 -
-
-
Low bidder. If I was the homeowner that electrician would be digging it all back up because it was done incorrectly. I'm sure the inspector would be interested in hearing about it. No way that could possibly pass PROPER inspection.Steamback said:Not sure what logic ever leads an electrician to EVER bury PVC with unglued joints, but I'm all ears on why that might be a common practice...
As for the holes, I always thought that was a huge no no with respect to spread of fire. They don't even want the "holes" in the walls open from floor to floor.
0
Categories
- All Categories
- 87K THE MAIN WALL
- 3.2K A-C, Heat Pumps & Refrigeration
- 58 Biomass
- 427 Carbon Monoxide Awareness
- 113 Chimneys & Flues
- 2.1K Domestic Hot Water
- 5.7K Gas Heating
- 109 Geothermal
- 161 Indoor-Air Quality
- 3.6K Oil Heating
- 70 Pipe Deterioration
- 995 Plumbing
- 6.3K Radiant Heating
- 391 Solar
- 15.4K Strictly Steam
- 3.4K Thermostats and Controls
- 55 Water Quality
- 44 Industry Classes
- 48 Job Opportunities
- 18 Recall Announcements